Computeraided structural design of drawing dies中文翻译.docx
《Computeraided structural design of drawing dies中文翻译.docx》由会员分享,可在线阅读,更多相关《Computeraided structural design of drawing dies中文翻译.docx(17页珍藏版)》请在冰豆网上搜索。
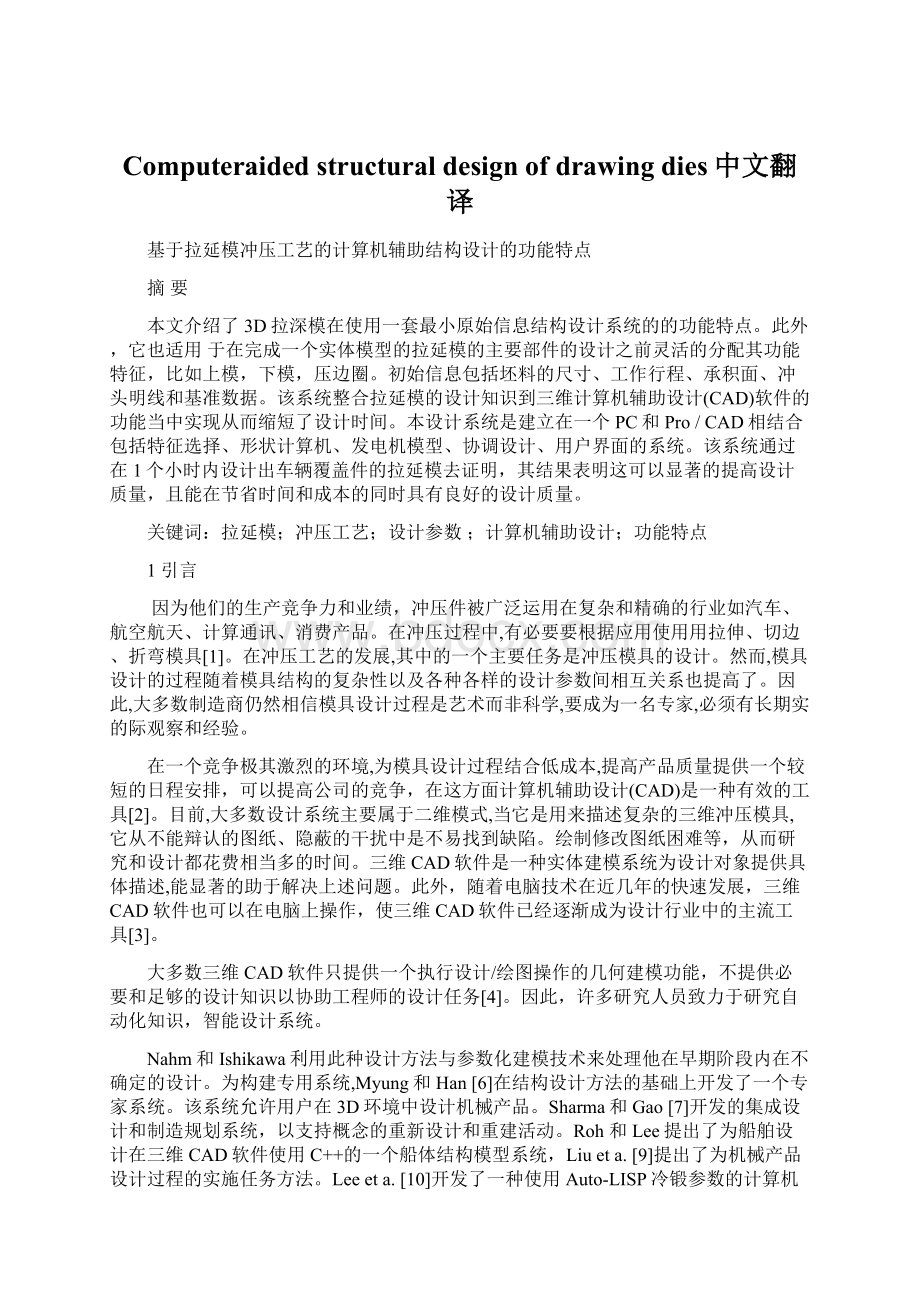
Computeraidedstructuraldesignofdrawingdies中文翻译
基于拉延模冲压工艺的计算机辅助结构设计的功能特点
摘要
本文介绍了3D拉深模在使用一套最小原始信息结构设计系统的的功能特点。
此外,它也适用于在完成一个实体模型的拉延模的主要部件的设计之前灵活的分配其功能特征,比如上模,下模,压边圈。
初始信息包括坯料的尺寸、工作行程、承积面、冲头明线和基准数据。
该系统整合拉延模的设计知识到三维计算机辅助设计(CAD)软件的功能当中实现从而缩短了设计时间。
本设计系统是建立在一个PC和Pro/CAD相结合包括特征选择、形状计算机、发电机模型、协调设计、用户界面的系统。
该系统通过在1个小时内设计出车辆覆盖件的拉延模去证明,其结果表明这可以显著的提高设计质量,且能在节省时间和成本的同时具有良好的设计质量。
关键词:
拉延模;冲压工艺;设计参数;计算机辅助设计;功能特点
1引言
因为他们的生产竞争力和业绩,冲压件被广泛运用在复杂和精确的行业如汽车、航空航天、计算通讯、消费产品。
在冲压过程中,有必要要根据应用使用用拉伸、切边、折弯模具[1]。
在冲压工艺的发展,其中的一个主要任务是冲压模具的设计。
然而,模具设计的过程随着模具结构的复杂性以及各种各样的设计参数间相互关系也提高了。
因此,大多数制造商仍然相信模具设计过程是艺术而非科学,要成为一名专家,必须有长期实的际观察和经验。
在一个竞争极其激烈的环境,为模具设计过程结合低成本,提高产品质量提供一个较短的日程安排,可以提高公司的竞争,在这方面计算机辅助设计(CAD)是一种有效的工具[2]。
目前,大多数设计系统主要属于二维模式,当它是用来描述复杂的三维冲压模具,它从不能辩认的图纸、隐蔽的干扰中是不易找到缺陷。
绘制修改图纸困难等,从而研究和设计都花费相当多的时间。
三维CAD软件是一种实体建模系统为设计对象提供具体描述,能显著的助于解决上述问题。
此外,随着电脑技术在近几年的快速发展,三维CAD软件也可以在电脑上操作,使三维CAD软件已经逐渐成为设计行业中的主流工具[3]。
大多数三维CAD软件只提供一个执行设计/绘图操作的几何建模功能,不提供必要和足够的设计知识以协助工程师的设计任务[4]。
因此,许多研究人员致力于研究自动化知识,智能设计系统。
Nahm和Ishikawa利用此种设计方法与参数化建模技术来处理他在早期阶段内在不确定的设计。
为构建专用系统,Myung和Han[6]在结构设计方法的基础上开发了一个专家系统。
该系统允许用户在3D环境中设计机械产品。
Sharma和Gao[7]开发的集成设计和制造规划系统,以支持概念的重新设计和重建活动。
Roh和Lee提出了为船舶设计在三维CAD软件使用C++的一个船体结构模型系统,Liueta.[9]提出了为机械产品设计过程的实施任务方法。
Leeeta.[10]开发了一种使用Auto-LISP冷锻参数的计算机辅助模具设计系统。
为了使建模过程更加高效,Kongeta[3]开发了基于使用VisuaC++的SoidWorks基础上的Windows原生3D塑料注塑模具设计系统。
Chueta.[11]为民航局在CATIA的轮胎模具生产中开发了计算机辅助的三维参数化设计系统。
模具设计是非常复杂的,尽管它是一个可以有科学方法的成熟的和常规的设计过程。
在冲压模具设计方面Cheok和Nee[12]在AutoCAD中开发了一个以知识为本条状布局设计系统。
基于钣金业务,Singh和Sekhon[13],开发了一种建立在AutoCAD使用AutoLISP语言的打卡机选择专家系统。
Choi et a[14]开发了计算机辅助设计和制造系统,为不规则形状的板材金属制品冲裁或冲孔和弯曲操作。
现在Tor等。
Toreta.[15]提出了一个以知识为基础的级进模冲压工艺规划黑板框架的设计。
Jiang et a.[16]介绍了这种基于CATIA使用插入内置模块的自动化设计知识的方法,Lin and Hsu[17]提出一种覆盖件拉延模具设计的自动化系统。
Tisza [18]在AutoCAD中制定一个详细的金属成形工艺规划专家系统。
Chang et a.[19]建立了解决连续模工作步骤排序的遗传算法问题。
Lin et a.[20] 开发了一种在Pro/E中绘制模具与一种特定类型的模具结构参数化设计系统。
然而,这些建议不能满足冲压模具设计行业的不同要求。
在系统设计中,组件只考虑将影响输入/输出参数功能作为一个整体的系统的首次合成系统[21]。
因此,设计师可以认真对待作为设计单位每一个功能特征。
然后,为了模具设计的一套功能特点被选中,以满足模具的需求,然后决定被选中功能特性每一个位置和尺寸。
每个功能特性的位置和尺寸必须遵循它的设计规范和标准,且不能与其他的功能特性和模具的需求发生冲突。
最后,模具的设计稿进行编辑和输出。
为了使模具设计在质量更高的同时更加灵活和高效率,本文提出了一种用于冲压工艺功能特性的拉延模具计算机辅助结构设计系统。
用户只需要输入一个初始信息的最小集合分配所选的功能特点,该系统将自动完成剩下的设计。
本研究整合Pro/ENGINEER模块和拉延模具设计的知识以构建设计系统。
Pro/ENGINEER的模块,包括草图,零件设计,装配,程序,和工具箱。
拉延模具设计的知识拉延模的设计步骤,草图的功能特点,设计准则和各功能特性的标准。
本文的其余部分安排如下:
第2节描述的拉延模具的主要部分的布局和设计过程。
第3节解释的结构设计系统的体系结构。
第4节逐步处理构建结构设计系统的过程。
第5节论证了采用该系统的顶盖拉延模具的设计。
总结在第6节给出。
2拉延模设计
冲压件通常借助适当的模具用一块金属平板在室温条件下使用。
冲压件的形状通常与模具的形状相适应。
所有金属板料的冲压工艺可以分为切割和塑性变形过程。
切割工艺中切割材料受到凸、凹模或者剪切片之间的切应力,其工艺包括剪切,落料,冲压。
塑性变形过程涉及工作材料的部分或全部材料塑性变形,包括弯曲,冲压和其他各种成型过程[1]。
冲压是一个通过凸模使钣金流入凹模型腔以形成一个无缝空心容器的过程。
在冲压期间,钣金以一块平板开始奠定了模具的开始。
为了限制金属流动时防止其起皱,必须对平板施力。
根据该部分的形状,这种类型的冲压在要求更多的发展的同时也需要尝试与错误。
一旦接到一个冲压件的表面模型,模具制造商模具开发过程中的初始化包括模面设计,平面布置图设计,模具设计,以及其他各种非设计流程。
模面设计是设计冲压件表面周围的各种配套表面的过程。
模面设计将是模具设计的首要信息。
这一进程的目的是为了提高冲压零件表面的成形性和避免冲压缺陷。
布局图设计是为了规划和确定冲压工艺标准和程序(拉延,落料和/或翻边),作为冲压模具设计的基础。
冲压模具是在他们的功能基础上构建冲压模具的结构[24].
2.1拉延模具布局
拉延模通过使材料受到严重塑性变形转化平板金属成杯,框架,或其他拉延形状[25]。
对于拉延模具设计总的设计布局可以总结为两部分。
第一部分是标准件,其中包括穿板,气弹簧,瓶塞,螺丝。
这些部件可以根据标准尺寸标准化。
另一部分是主要部分,其中包括上模、下模,和压边圈,如图1中所示。
这些部件根据冲压件,冲压工艺要求和客户要求而变化。
本文着重对主要部件的设计。
图1顶板拉延模主要部件的结构
2.2拉延模设计的主要部分
拉延模具结构设计的主要部分的结构是非常复杂的,因此,它的设计过程比一般的相比要复杂的多。
一般来说,冲模主要零件的设计过程包括两个阶段:
信息初始化和功能结构的设计。
2.2.1信息初始化
每个拉延模具设计的初始信息包括毛坯尺寸,模具型面,凸模开行,工作行程和冲压数据。
毛坯尺寸:
毛坯尺寸是金属板材的尺寸,虽然通常根据模面形状是不规则形状,但一般是一般长方形的。
在大多数模具的设计,这种模具的长度和宽度都可以根据板料的尺寸决定。
模具型面和凸模开行线:
如图2所示,模具型面包括产品形式,齿顶,拉深筋和粘合面。
模具型面是冲压后的最后所需形状而变位数,拉深筋和粘合面是拉延过程中的辅助形式。
模具型面可以作为上模的表面;此外,冲孔开行线可以作为将模具型面分割为下模和压边圈两个表面的便面形式。
一些研究者[26-28]用有限元法预测和/或优化冲压模具的模具型面和板料的成性参数,那些超出了本文的范围。
a模具型面b冲孔开行线
图2顶盖拉延模的模具型面和冲孔开行线
工作行程:
行程从上模与压边圈的接触点开始到底部结束;一般来说,其值得大小是模面最高点和最低点之间的高度差加上10mm。
压机数据:
这对于拉延模具设计的压机是必要的相关数据,包括压机规格和与压机以及拉延模具相关的数据。
压机规格涵盖压机工作行程,滑块的底部上方,模座的高度和尺寸以及T型槽和缓冲空的位置和尺寸。
与机器和模具有关的数据包括模具高度,料位,缓冲行程,加工中心和模具中心。
2.2.2功能结构设计
Pratt和Wison[29]首次提出产品特点设计理念。
功能特点意味着工程师可以将一个产品的通用形状或者特征与其某些用处和知识用于与该产品的推理。
通过它们的组成特点,可以模拟出特定产品,比单纯的几何模型与设计师互动能提供更自然的基础。
可以通过访问记录在最终产品模型的功能获得其一般知识[21]。
Wang和Nnaji[30]提出了在基于特征的参数化建模中用于代表和有关特征设计的一种基于几何语义的方法。
Ismaieta.[31]开发了一种以特征为基础的使用不昂贵CAD软件的级进模。
Rantaeta.[32]提出了一种整合产品建模的功能和特征的智能制造系统。
以功能为基础的设计不同于基于特征的设计,基于特征的设计是基于功能形式,如垫,凹坑,孔等设计方法。
这些功能在一个特定的部分被用于制造特殊形状。
如套筒,肋板,钩等的设计方法。
从设计师的角度来看,装配是一个在不同层面上反映了一定的关系结构模型,为表征组装属性组织部分交配信息是在产品装配建模的主要问题之一。
装配操作设计采用了多项设计和分析工具以帮助设计师在组装待选件之前计划和分析零件的几何形状的详细知识[33]。
其他也尝试了不同的方法,例如,Zha et a.[34]开发了以知识为基础的方法和系统面向装配设计,Armiotta et a.[35]提出了一种基于CAD的方法从他们的设计信息来生成拉延模具和落料模具的装配计划。
功能结构设计是是用功能特点设计一个模具的组装结构的过程,包括尺寸(长度,宽度和高度)上模,下模,压边,模面的厚度,孔的间隙,排料,肋板厚度,导料板的厚度和尺寸,辅助结构,快速定位器,缓冲销,止阀座,插销,U型槽,耐磨板,钩和压力表。
用导柱式指导设计作为一个例子,其设计标准如下:
在无侧向力以及考虑节约成本的因素的情况下,导套类型可以使用。
如果有侧向力,那么就有必要使用导柱的类型。
对于模具长或宽超过4米,为避免不稳定,有必要使用一个由导柱和导套导向共同的机制,该导向机构应周边对称,且导柱外缘和这种模具外援的距离应大于30mm。
根据压力机类型,相应的导柱的直径和数目,如表1所示。
设计标准如表2所示。
表1导向用导柱导向类型时的设计表格
冲压类型
A
B
C
E
G
导柱(mm)
φ100
φ80
φ60
50×200L
38×200L
32×130L
25×130L
数量
4
4
4
1
1
表2导向用导柱导向类型时的设计标准
a)支座衬套;b)支座杆
单位:
mm
3系统构架
除了根据规范和标准实施模具设计任务,该系统还允许用户分配的功能特点的类型以取代现有的功能特点设计。
该系统的构架如图3所示,包括如下:
拉延模设计基础知识、功能选择,形状计算器,模型生成,协调设计和用户界面。
各部分在下面的小节详述。
图3系统结构
3.1拉延模设计基础知识
对于用3D标准化构建拉延模具设计,有必要分析模具结构以及将该模具的子部分构造和功能特点进行分类。
这样,设计师可以将模具结构系统分类,理解在建模过程中各项功能特点必要地几何操作。
这些数据以一个三维实体模型模板的格式存储,在现有的基础知识中有27种(总)功能特性,此外还有每个功能特点的二维图的设计参数与相应的设计准则和标准,每个不同功能特性的设计参数之间的关系都储存在一个标签的格式接口。
在这里,他们可用于培训新设计师,访问模具信息,以及编译,修改和调试程序。
3.2功能选择
该选择器提供数据的类型、数量、位置和与功能特点有关的尺寸。
因此,当系统正在设计功能特性,该选择器会根据从最初的信息和设计标准转化的约束和公式中选择类型、数量、位置和与功能特点。
拉延模具分为三个主要部分:
15个模块和27种类型的功能特点,如图6所示。
以导柱的导向设计为例,在第2.2节中介绍的三个设计准则衍生出三个公式。
因此,在我们系统中的这27个功能特点总共有302个公式。
当根据初步信息、约束和计算公式不能找到合适的结果时选择器会发送一个警告。
3.3形状计算器
这个计算器可以根据设计功能特点的固定的类型和规模(即独立设计参数),提供功能特性的形状参数。
该计算器将根据功能特性的设计标准对每个形状参数计算设计值。
以导柱的导向设计为例,根据设计标准有14个设计参数,如表2所示,27功能特点,有435的设计参数。
3.4模型生成器
模型生成器可以用功能特点进行三维实体造型工艺。
它可以在建模过程中根据待选的功能特征如数量,位置和尺寸参数结合各功能特点的几何类型用来建造功能特征的几何模型。
由于实体模型的参数是电脑系统自动生成,而不是与用户的互动的结果,这个实体模型的建模过程是三维CAD系统自动完成的。
在建模过程中,如果存在任何错误,设计协调员会发送一个错误信息给向用户,导致错误命令和环境。
3.5协调设计
这种协调的功能用于缓和该系统的不同任务,从用户界面的输入的初始信息开,协调器将根据拉延模具的三维设计工艺设计各功能特点如图5所示。
当设计各功能特点时,,首先用特征选择器计算种类,数量,位置,功能特点的尺寸,然后用形状计算器获取那些功能特征的形状参数,同时激活模型生成器构建功能特征的实体模型。
此外,如果用户界面的输入值是指定的功能特征,则将把这种功能特征的位置出入到拉延模具的3维设计工艺中,且持续的覆盖指定功能特征执行上述工艺。
3.6用户界面
用户界面负责责任设计者与系统之间的交流。
该系统的用户界面包括初始信息的输入,比如说:
毛坯尺寸、工作行程和冲压数据以及分配功能特征的类型。
用户界面也负责检测不正确的数据输入和对特殊事件的管理。
4构建以知识为基础的工艺
本研究建立在Pro/ENGINEER三维CAD系统和其“附加”的Pro/PROGRAM和Pro/TOOLKIT模块基础上。
它用于构建在初始信息基础上和符合设计准则和设计标准条件下拉延模具的主要部件的实体模型。
因此,可以实现更快速地设计。
用这种方式功能特性的类型可进行分配,该部分设计任务的灵活性和范围可以增强。
该系统的构建过程如图4所示,每一个过程的简要阐述将在下面部分说明:
4.1模具结构规划
由于拉延模具结构相当大且复杂,有必要为模具的整体结构布局做一个全面和系统的计划。
因此,模具设计规划不仅可以为CAD系统开发构建逻辑,而且防止在模具设计中任何可能的错误。
为了设计模具结构,首先有必要收集各式车辆的各种结构模具有关的信息,然后分析各拉延模具的所有主要部件。
比如上模、下模、压边。
也有必要将这些主要部件的各功能特点分区,根据它们与各功能特点的设计位置和尺寸的关系考虑设计准则和设计标准。
然后,可以开发拉延模的设计流程图,如图5所示。
因此,它对于做出结构和初始尺寸以及为主要部件中的各功能特征的位置和初始尺寸均是有用。
图4提议系统构建过程的流程图
图5拉延模主要部件的设计步骤
4.2设置功能模块
参数化模具设计以多变的模具结构尺寸作为参数,然后通过改变模具结构尺寸参数的关系式以满足设计目标。
但是在模具设计过程中,一些模具的部分可能很不相同,例如导向装置,U型槽、耐磨板、安全装置、压边圈等,因此仅通过单独改变结构尺寸是不可能满足设计要求的。
因此,在本文中,一个拉延模具的主要部分的不同结构被分到不同的功能特征,相同的功能被分在一个相同功能模块。
最终的冲模功能模块结构图如图6所示。
以导向模块为例被分为了三个类型:
完全导柱,导套,导柱和导套结合型。
此外,在设计过程中,有必要按照设计准则和设计标准设计合适的导向类型。
在可接受的范围内按设计规范和标准在模块中分配导向类型是可能得。
图6拉延模功能模块的结构图
4.3构建平面框架
在模具结构规划实施后,工艺特征层树根据模具设计构建,如图7所示。
下一步要构建的是冲模的平面框架,这将作为实体模型拉深厚度的基础以及连接下面的操作的公式。
冲模的平面框架模型如图8所示。
对于一个冲模,这个框架模型是最初结构。
为了使平面结构模型化,本文提出,对于平面框架模型提前为每种结构功能类型预构建是必要的。
例如,在平板框架模型中有两种类型的耐磨板—环状耐磨板和坡口状耐磨板,如图9所示。
他们作为建设基线预先在框架模型中建立。
当构建一个模具的实体模型时,只有选定的功能特性应该被激活。
所有未选中的功能应停止。
另外,在构建框架模型之后,有必要应用各种因素分别去限制其维度。
约束是不可变尺寸的参考,且约束的数量与模具设计过程中的灵活性程度有关。
由于使用约束可以减少参数的数量和简化编程工作,设计师在规划和使用约束是应非常谨慎。
图7拉延模的功能树
在下列程序,每个维度将被定义为设计参数。
在这个程序中,当定义各个维度时应该考虑每个情况,因为维度的值不能为空或者负。
此外,考虑一些功能特点的参数和其它功能特点的功能参数的因果关系是非常重要的,因此,要规划公式关系和阻止程序出现错误。
4.4定义参数
在平板框架模型构建后,为了改变平板框架模型的维度以符合该模具的设计信息、准则和标准,给一个可变维度指定参数名称时必要的。
然后可以根据它与设计条件的关系定义参数关系式,且其将作为改变尺寸的依据。
此外,与冲模现有系统有关的参数有数百个,为参数名定义应该体系化及合适的进行分类以便于理解和管理参数以及便于以后的编程工作和调试。
在本文中使用的参数名称由两部分组成—功能名称是参数名的属性,各功能特点的维度名如图表所示。
至于参数的分类,由于各功能将有一个子程序组成,相关参数可以被分类成局部和全局参数。
全局参数与其它特征的尺寸有关,同时他们要求与由参数的应用范围决定的子程序相关。
相反,局部参数仅能用于一个子程序。
此外,基于
图8拉延模主要部件的平面框架
参数的功能,参数可分为位置参数和形状参数。
此外,形状参数又可分为独立参数和从属参数。
在这里,独立参数是一些有不同尺寸值的参数,根据设计条件以及设计准则决定。
相反,从属参数是那些有不同维度值的参数,根据从属参数以及设计标准构成。
以表2中的导柱为例,导柱的直径D是一个独立参数,而其他尺寸,比如说 D1,D2,H, H1,和N是从属参数。
4.5编程
编程意味着为每个参数找到为该设计基于输入信息设置合适的关系,同时与设计准则设计标准和建模过程相一致。
然后Pro/PROGRAM的功能是在Pro/ENGINEER构建的程序用来将参数关系转换成相关程序。
图9垫板的平面框架和实体模型
为了方便设计过程,该方案被列为分为三个级别。
为了导向的设计,例如,特征选择器程序是在第一级,该级通过转换设计准则到公式中来负责识别类型、数量、位置和功能特征的尺寸,如图10a所示。
第二个级别,形状计算器程序,用于计算功能特性的形状尺寸。
在这个级别的程序为根据第一级别的程序分配的功能特征的独立参数和类型决定的功能特征分配因变量。
这些程序也符合设计标准,比如导柱,如图10b所示。
第三个级别,称为模型生成程序,用来构建功能特征。
在这个级别的程序纬功能特征建模过程中的几何操作,由此,为根据由上述程序决定的功能特征的类型和尺寸的功能特征的实体模型构建了,比如10c图中所示的导柱。
图10导柱导向编程范例
a特征选择器编程;b形状计算器编程;c模型生成器编程
4.6构建用户界面
用户界面允许用户在一个用户友好的界面用该系统设计冲模。
此外,为了有一个更灵活的设计过程,该系统不仅可以从设计准则中选择合适的功能特征类型,而且额外的手动选择功能可以安装在该程序以设置这种类型的功能特征。
用这种方法,该系统通过提供一个更友好的用户环境将能够满足用户的要求。
用户界面是利用包含在Pro/ENGINEER中的Pro/TOOLKIT模块来构建的。
用于该系统的用户界面根据其功能将其命名分类为两部分。
第1部分为初始信息(毛坯尺寸、工作行程和冲压数据)组成输入界面,如图11a所示。
对于毛坯尺寸输入区域,用户要求输入毛坯4个顶点的x和y的坐标。
对于冲压数据,由于压力机的规格已经储存在我们的系统中,故可充分使用压线。
此外,其他数据包括模具高度、进刀距离、缓冲行程以及压力及中心和模具中心的距离。
第2部分包含所有功能模块的种类,例如图11b所示的导向机构,在该部分除了线框模型所有类型的导向装置都给了个功能特征名称。
然而使用这个系统时,仅仅选择功能特征的类型是必要的。
然后通过简单的按“确认”键,预期具有所有功能特征的模具设计产品将能顺利产出。
图11用户界面标签
a初始信息b导向模块
5例证
该开发系统用汽车顶盖的冲压模设计为说明。
首先,毛坯尺寸、工作行程和冲压数据输入到用户界面菜单的系统中。
然后冲孔模的模具型面和冲孔开行嵌入到特征树种,如图12a所示。
模具型面和冲孔开行先是挤压和切边工序的边缘,当挤压平面框架模型为固体模型。
毛坯尺寸、工作行程和冲压数据是用于平板框架和实体模型中位置和尺寸公式中的参数。
在这上,系统开始完成余下的设计。
设计协调员开始设计基于在图5中描述的设计程序的各个功能特征和模具的主要部件。
当设计各个功能特征时,系统首先要求特征选择器决定基于初始信息和设计准则上的各功能特征的类型,数量和位置。
然后,形状计算器将会为基于功能特征以及来自设计标准的程序的形状和尺寸的选订的功能特征决定形状参数,然后选定的功能特征的模型生成器被激活,构建基于其类型、数量、位置和尺寸基础上的实体模型。
在以合适的秩序构建各个选择功能特征的模型之后,为顶板的冲模设计就完成了,如图12b所示。
另外,这个模具的导向结构类型是导柱导向。
如果一个用户更倾向于为冲模使用特殊功能特征类型,例如导向装置用导套导向和用导柱导向类型。
设计者可以使用用户界面菜单挑选导向模块。
这里导套导向和导柱导向也可以被选择,如图12c所示,按下“确认”键之后,该系统的导柱导向和导套导向自动的构建冲压模的主要部件。
如图12d所示,与设计准则和设计标准符合。
图12顶板拉延模的设计步骤
a输入的初始信息;b输出拉延模的自动设计;
c选择导套和导柱导向类型;d输出拉延模的指定设计
6结论和未来工作
本文提出了用于建立在电脑和整合了Pro/ENGINEER和CAD系统上的功能特征基础上的三维模具结构设计系统,该系统使用初始信息,可设计拉延模的主要部分。
必要时,可以灵活选择功能特征的类型。
该系统摄入初始信息和选择出功能特征。
然后将他们转换成设计参数,使建模过程成为几何操作,最后输出冲模的主要实体模型。
为车顶盖的冲模设计作为演示该系统的应用实
例,该系统能够在1个小时内成功的设计出冲模模具,而一个三维CAD系统完成同样的工作将耗费许多天。
因此,它能够显著的为冲压模具的设计节省时间和花费也能够提供优良的质量。
该系统仅应用于冲压模具的设计,但是