组合机床动力滑台液压系统液压课程设计样本.docx
《组合机床动力滑台液压系统液压课程设计样本.docx》由会员分享,可在线阅读,更多相关《组合机床动力滑台液压系统液压课程设计样本.docx(19页珍藏版)》请在冰豆网上搜索。
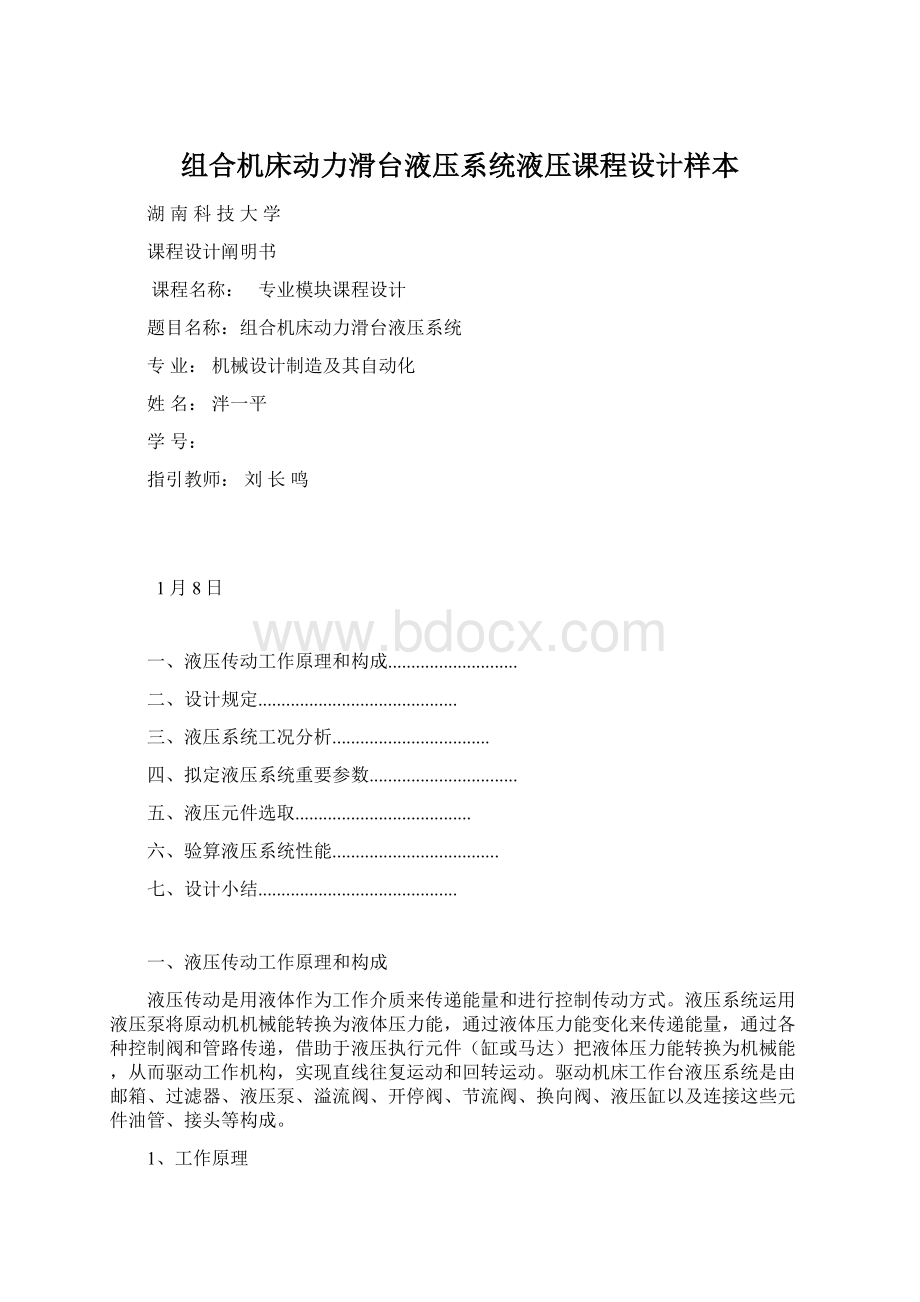
组合机床动力滑台液压系统液压课程设计样本
湖南科技大学
课程设计阐明书
课程名称:
专业模块课程设计
题目名称:
组合机床动力滑台液压系统
专业:
机械设计制造及其自动化
姓名:
泮一平
学号:
指引教师:
刘长鸣
1月8日
一、液压传动工作原理和构成............................
二、设计规定...........................................
三、液压系统工况分析..................................
四、拟定液压系统重要参数................................
五、液压元件选取......................................
六、验算液压系统性能....................................
七、设计小结...........................................
一、液压传动工作原理和构成
液压传动是用液体作为工作介质来传递能量和进行控制传动方式。
液压系统运用液压泵将原动机机械能转换为液体压力能,通过液体压力能变化来传递能量,通过各种控制阀和管路传递,借助于液压执行元件(缸或马达)把液体压力能转换为机械能,从而驱动工作机构,实现直线往复运动和回转运动。
驱动机床工作台液压系统是由邮箱、过滤器、液压泵、溢流阀、开停阀、节流阀、换向阀、液压缸以及连接这些元件油管、接头等构成。
1、工作原理
(1)电动机驱动液压泵经滤油器从邮箱中吸油,油液被加压后,从泵输出口输入管路。
油液经开停阀、节流阀、换向阀进入液压缸,推动活塞而使工作台左右移动。
液压缸里油液经换向阀和回油管排回邮箱。
(2)工作台移动速度是通过节流阀来调节。
当节流阀开大时,进入液压缸油量增多,工作台移动速度增大;当节流阀关小时,进入液压缸油量减少,工作台移动速度减少。
由此可见,速度是油量决定。
2、液压系统基本构成
(1)能源装置——液压泵。
它将动力某些所输出机械能转换成液压能,给系统提供压力油液。
(2)执行装置——液压机。
通过它将液压能转换成机械能,推动负载做功。
(3)控制装置——液压阀。
通过它们控制调节,使液流压力、流速和方向得以变化,从而变化执行元件力、速度和方向。
(4)辅助装置——邮箱、管路、储能器、滤油器、管接头、压力表开关等。
通过这些元件把系统联接起来,以实现各种工作循环。
(5)工作介质——液压油。
绝大多数液压油采用矿物油,系统用它来传递能量和信息。
二、设计规定
设计一台组合机床动力滑台液压系统。
1.机床规定工作循环是:
规定实现工件快进、工进、快退等过程,最后自动停止;动力滑台采用平导轨,往复运动加速、减速时间
为0.2s。
2.机床其她工作参数如下:
参数三
运动部件总重力
G=30000N5000N
切削力
Ft=0N24000N
快进、快退速度
v1=v3=6m/min3.5m/min
最大行程
l=400mm300mm
工进速度
v2=20~120mm/min30~40mm/min=0.03m/min~
静摩擦系数
fs=0.2
动摩擦系数
fd=0.1
3.机床自动化规定:
规定系统采用电液结合,实现自动循环,速度换接无冲击,且速度要稳定,能承受一定量反向负荷。
由设计规定取工进速度为40mm/min,快进行程
为200mm,工进行程
为100mm
0.2s
三、液压系统工况分析
1.运动分析
绘制动力滑台工作循环图
2.负载分析
2.1负载计算
2.11工作阻力
工作阻力为已知
2.12摩擦阻力
已知采用平导轨,且静摩擦系数
,动摩擦系数
,正压力
,则:
静摩擦阻力
动摩擦阻力
2.13惯性力
2.2液压缸各运动阶段负载
如果忽视切削力引起颠覆力矩对导轨摩擦力影响,并设定液压缸机械效率
,则液压缸在各个工作阶段总接卸负载可以算出,见下表:
运动阶段
计算公式
总接卸负载F/N
起动
1052
加速
682
快进
526
工进
25789
快退
526
2.3绘制动力滑台负载循环图,速度循环图
三、液压系统方案设计
1.选取调速回路
这台机床液压系统功率较小,滑台运动速度低,工作负载为阻力负载且工作中变化小,故可选用进口节流调速回路。
为防止负载突变,在回油路上加背压阀。
由于系统选用节流调速方式,系统必然为开式循环系统。
2.选取油源形式
在工作循环内,液压缸规定油源提供快进、快退行程低压大流量和工进行程高压小流量油液。
在一种工作循环中大某些时间都处在高压小流量工作。
从提高系统效率、节约能量角度来看,选用单定量泵油源显然是不合理,为此可选用限压式变量泵或双联叶片泵作为油源。
考虑到前者流量突变时液压冲击较大,工作平稳性差,且后者可双泵同步向液压缸供油实现迅速运动,最后拟定选用双联叶片泵方案,如下图所示。
3.选取迅速运动和换向回路
本系统已选定液压缸差动连接和双泵供油两种迅速运动回路实现迅速运动。
考虑到从工进转快退时回油路流量较大,故选用换向时间可调电液换向阀式换向回路,以减小液压冲击。
由于要实现液压缸差动连接,因此选用三位五通电液换向阀,如下图所示。
4.选取速度换接回路
由于本系统滑台由快进转为工进时,速度变化大,为减少速度换接时液压冲击,选用行程阀控制换接回路,如图下图所示。
5.选取调压和卸荷回路
在双泵供油油源形式拟定后,调压和卸荷问题都已基本解决。
即滑台工进时,高压小流量泵出口压力由油源中溢流阀调定,无需另设调压回路。
在滑台工进和停止时,低压大流量泵通过液控顺序阀卸荷,高压小流量泵在滑台停止时虽未卸荷,但功率损失较小,故可不需再设卸荷回路。
6.构成液压系统
将上面选出液压基本回路组合在一起,并经修改和完善,就可得到完整液压系统工作原理图,如右图所示。
为理解决滑台工进时进、回油路串通使系统压力无法建立问题,增设了单向阀6。
为了避免机床停止工作时回路中油液流回油箱,导致空气进入系统,影响滑台运动平稳性,图中添置了一种单向阀13。
考虑到这台机床用于钻孔(通孔与不通孔)加工,对位置定位精度规定较高,图中增设了一种压力继电器14。
当滑台碰上死挡块后,系统压力升高,它发出快退信号,操纵电液换向阀换向。
四、拟定液压系统重要参数
1.初选液压缸工作压力
所设计动力滑台在工进时负载最大,在其他工况负载都不太高,参照表1和表2,初选液压缸工作压力p1=5MPa。
2.计算液压缸重要尺寸
鉴于动力滑台快进和快退速度相等,这里液压缸可选用单活塞杆式差动液压缸(A1=2A2),快进时液压缸差动连接。
工进时为防止负载突变采用背压,参照表4选此背压为pb=0.8MPa。
表1按负载选取工作压力
负载/KN
<5
5~10
10~20
20~30
30~50
>50
工作压力/MPa
<0.8~1
1.5~2
2.5~3
3~4
4~5
≥5
表2各种机械惯用系统工作压力
机械类型
机床
农业机械
小型工程机械
建筑机械
液压凿岩机
液压机
大中型挖掘机
重型机械
起重运送机械
磨床
组合机床
龙门刨床
拉床
工作压力/MPa
0.8~2
3~5
2~8
8~10
10~18
20~32
表3执行元件背压力
系统类型
背压力/MPa
简朴系统或轻载节流调速系统
0.2~0.5
回油路带调速阀系统
0.4~0.6
回油路设立有背压阀系统
0.5~1.5
用补油泵闭式回路
0.8~1.5
回油路较复杂工程机械
1.2~3
回油路较短且直接回油
可忽视不计
表4按工作压力选用d/D
工作压力/MPa
≤5.0
5.0~7.0
≥7.0
d/D
0.5~0.55
0.62~0.70
0.7
表5按速比规定拟定d/D
2/
1
1.15
1.25
1.33
1.46
1.61
2
d/D
0.3
0.4
0.5
0.55
0.62
0.71
注:
1—无杆腔进油时活塞运动速度;
2—有杆腔进油时活塞运动速度。
液压缸活塞杆外径尺寸系列
——————摘自GB/T2348—1993(mm)
4
20
56
160
5
22
63
180
6
25
70
200
8
28
80
220
10
32
90
250
12
36
100
280
14
40
110
320
16
45
125
360
18
50
140
由公式
可得:
则活塞直径
参照表4及表5,得d
0.71D=60mm,圆整后取原则数值得
D=84mm,d=60mm。
由此求得液压缸两腔实际有效面积为
依照计算出液压缸尺寸,可估算出液压缸在工作循环中各阶段压力、流量和功率,如下表所列。
表6液压缸所需实际流量、压力和功率
工作循环
计算公式
负载F
进油压力
回油压力
所需流量
输入功率P
N
pj
pb
L/min
KW
差动快进
526
18.66
0.48
工进
25789
0.51
0.036
快退
526
19.44
0.63
注:
---------
1.Δp为液压缸差动连接时,回油口到进油口之间压力损失,取Δp=0.5MPa。
2.快退时,液压缸有杆腔进油,压力为pj,无杆腔回油,压力为pb=pj+Δp。
3.计算工进是背压按pb=0.8Mpa代入。
4.快退时背压按pb=0.5Mpa代入。
3.液压泵参数计算
小流量泵在快进和工进时都向液压缸供油,由表6可知,液压缸在工进时工作压力最大,最大工作压力为p1=4.22MPa,如在调速阀进口节流调速回路中,选用进油路上总压力损失∑∆p=0.6MPa,考虑到压力继电器可靠动作规定压差∆p=0.5MPa,则小流量泵最高工作压力估算为
大流量泵只在快进和快退时向液压缸供油,由表6可见,快退时液压缸工作压力为p1=1.95MPa,比快进时大。
考虑到快退时进油不通过调速阀,故其进油路压力损失比前者小,现取进油路上总压力损失∑∆p=0.3MPa,则大流量泵最高工作压力估算为
因而泵额定压力可取
(2)计算液压泵流量
由表6可知,油源向液压缸输入最大流量为19.44L/min,若取回路泄漏系数K=1.1,则两个泵总流量为
考虑到溢流阀最小稳定流量为2.5L/min,工进时流量为0.51L/min则小流量泵流量
小流量泵流量至少应为3.1L/min。
因此大流量泵流量
(3)拟定液压泵规格和电动机功率
依照以上压力和流量数值查阅产品样本,并考虑液压泵存在容积损失,最后拟定选用PV2R12-6/26型双联叶片泵。
其小流量泵和大流量泵排量分别为6mL/min和26mL/min,当液压泵转速np=960r/min时,其理论流量
分别为5.6L/min和24.3L/min,若取液压泵容积效率ηv=0.9,则液压泵实际输出流量为
由于液压缸在快退时输入功率最大,若取液压泵总效率ηp=0.8,这时液压泵驱动电动机功率为
依照此数值查阅产品样本,选用规格相近Y100L—6型电动机,其额定