陶瓷缺陷分析.docx
《陶瓷缺陷分析.docx》由会员分享,可在线阅读,更多相关《陶瓷缺陷分析.docx(19页珍藏版)》请在冰豆网上搜索。
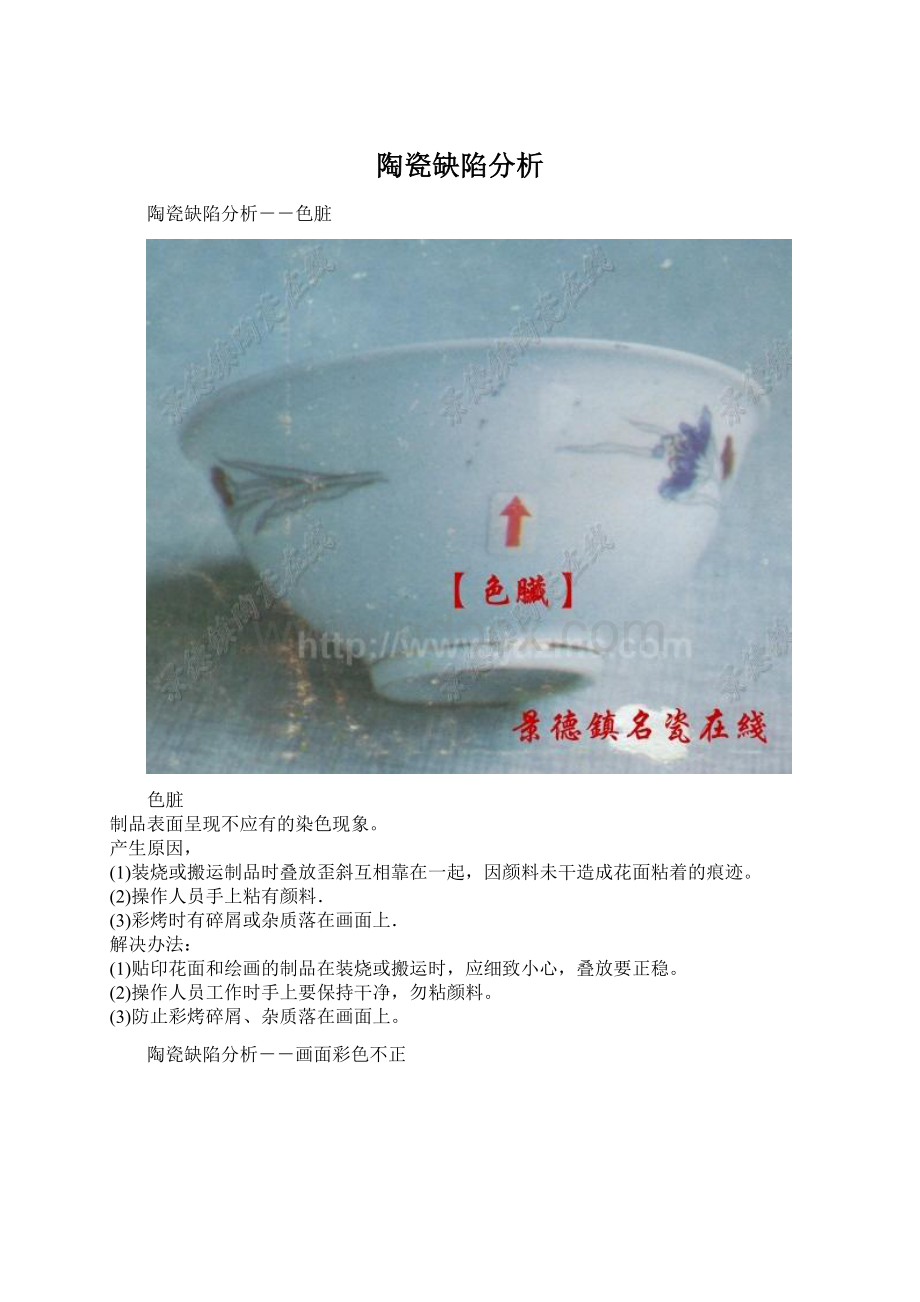
陶瓷缺陷分析
陶瓷缺陷分析--色脏
色脏
制品表面呈现不应有的染色现象。
产生原因,
(1)装烧或搬运制品时叠放歪斜互相靠在一起,因颜料未干造成花面粘着的痕迹。
(2)操作人员手上粘有颜料.
(3)彩烤时有碎屑或杂质落在画面上.
解决办法:
(1)贴印花面和绘画的制品在装烧或搬运时,应细致小心,叠放要正稳。
(2)操作人员工作时手上要保持干净,勿粘颜料。
(3)防止彩烤碎屑、杂质落在画面上。
陶瓷缺陷分析--画面彩色不正
画面彩色不正
(1)画面缺陷--面面残缺和色泽不正的现象.
(2)彩色不正--同一花纹色彩浓淡不匀或由于欠火而产生不光亮的现象。
产生原因:
I.釉下装饰
(1)分水时,水色、浓淡、厚薄不统一。
(2)施釉时,釉层厚薄不一或画面不干净.
(3)花纸上的料没有全部贴坯上,或使用了不符合要求的花纸,以及纸上料色有浓淡不匀的现象。
(4)烧成温度低或烧成气氛不当,使釉面没有充分玻化,花纹色彩不易进出.
(5)烧成时由于吸烟或者是欠釉影响产品的呈色效果.
2.釉上装饰
(1)花纸质量不好或存放时间过长而变质.
(2)操作技术不熟练,贴花时未贴妥,而鼓有空气,随着彩烤时温度上升,气泡胀破,导致爆花,或花纸正反面贴错,会造成严重爆花.
(3)贴薄膜花纸时,所用酒精配制不当.
(4)彩烤时,从色料中或花纸中所产生的气体会对其它产品上的色料发生反应,从而出现呈色不良.
(5)所使用的燃料其含硫量过高,使气氛中的二氧化硫与釉料或色料中氧化钙及其它化合物生成硫酸盐,从而使彩色失去光泽。
(6)装烤方式或装载量不当。
(7)彩烤温度过高或过低,使彩色不正。
解决办法:
1。
釉下装饰
(1)熟悉釉下贴花的操作技术,以及手工工艺,掌握釉下花面的色彩浓淡要求,调好料浆水份.
(2)保管好花纸,防止受潮或过干,产生贴花的问题。
(3)掌握釉下贴花产品的施釉厚度,防止过厚或过薄。
(4)制定合理的烧成制度,防止吸烟和烧成气氛不良的现象。
2.釉上装饰
(1)妥善保管好花纸,勿使其受潮变质,注意先进厂的先用,保管时间不超过两年,若时间过久将会自然老化变质。
(2)根据不同季节,气候和薄膜厚薄,配制适宜的酒精溶液.
(3)操作要细心熟练,一次不宜贴粘过多的产品,贴一批及时将气泡、皱纹用纯酒精刮干,然后再继续进行彩贴。
(4)根据花纸型号,所贴彩件品种,选择适当的空位,适合的彩烤温度,并注意通风。
’
(5)不使用含硫量过高的燃料。
陶瓷坯体开裂成因及克服方法
从材料的力学性质可知,只有当外力大于材料原子间的结合力时,材料才能断裂。
不同的材料,因组成不同,晶体结构不同,以及键合方式不同,其原子间的结合力也就不同。
关于材料的微观机理的研究,已发展出一门新的学科——断裂力学。
本书仅简要介绍陶瓷生产过程中,造成超过原子间结合力的因素。
格里菲思(Griffith)认为:
“实际材料中总是存在许多细小的裂纹或缺陷,在外力作用下,这些裂纹和缺陷附近易产生应力集中现象,当应力达到一定程度时,裂纹就开始扩展而导致断裂”。
形成这些裂纹或缺陷的原因主要是晶体微观结构中存在裂隙或坯体在干燥中由于热应力而形成裂纹及坯体成形、干燥运输过程中因操作不慎而造成的机械损伤。
总之,裂纹缺陷的成因很多,根据开裂的特征,分别介绍如下。
一、坯裂
特征是裂纹向内纵深发展;裂透、坯釉同时开裂;或坯裂釉不裂,裂口面粗糙,不锋利。
造成坯裂的因素有:
1、制品在成形、干燥、精坯、釉坯、挖取釉、运输、吊钵、装窑、装车过程中,已因收缩不均匀、机械碰撞等原因,形成细小裂纹,在加工过程中未发现剔除,高温时应力释放,则暴露出开裂,具有大同小异的特征。
2、供成形的泥料或泥浆,未经充分捏练和排泡、排气、含有空气和硬泥籽等,影响产品组织的均一性,形成薄弱环节。
这种坯在干燥收缩和烧成收缩中,因收缩应力加大,超过坯体的结合力而撕裂。
3、塑性成形的产品,打泥饼入模过重,使泥料粒子排列改变,鼓入空气于底部或投模入泥过早,构成水分差等,都将造成底部泥料组织不均一。
滚头中心夹角不对或不对中心、尖部磨损等,会导致压力不均匀;滚头润滑不好、坯泥粘性强等,会产生轻微卷泥,使坯体受伤。
4、需刀修的产品,特别是湿修产品,因泥料是半干的,刚性不够,结合力差,修边、挖沟、剐底时,因刀子过钝、用力过大、切削刀的前角过大、修削面过宽、吃刀过深,都将使坯体表现爱到机械损伤而产生微裂纹,于烧成收缩时扩大成开裂。
5、接斗产品,因互相粘接的两个部件及粘接泥的配方不同、成形方法不同、部件水分不同及坯料的密度、泥料粒子排列不同,特别是在粘接、加工、干燥过程中受应力,烧成中因收缩不同,应力释放而开裂。
二、惊裂
俗称冷炸,裂口光亮、锋利,有坯、釉皆裂和釉裂坯不裂两种(斑纹裂是特殊艺术效果)。
1、坯釉皆裂。
一般说,坯、釉皆裂者主要是冷却制度不当,尤其是隧道窑快速冷却,控制不当最容易出现惊裂缺陷。
通常因高温冷却过快造成的裂纹,裂口较大;因中温冷却过快形成的裂纹,裂口较小,如发丝状。
其影响因素有:
①隧道窑零压位置前移,窑头温度偏低,冷却带温度普遍降低或气压高、气温低和烟囱抽力大,使高温冷却的速度超过允许急冷温度范围的规定。
②高火炉最后一对炉温偏低,使冷却带的蓄热少,从而造成制品冷却速度过快。
③隧道窑的急冷风,风压高、风量大,冷风侵袭产品。
④中温阶段(700~450℃)冷却过快,特别是含游离石英多的坯体,由于石英晶型的急速转化,产生体积变化,因体积变化的应力差而惊裂。
⑤装窑过密,气流不畅通,尤其大型、厚胎产品,因上下、内外温差而产生应力。
⑥产品过烧,脆性加大,耐应变能力差,冷却稍有不当,就产生开裂。
2、釉裂。
釉面惊裂而坯不裂的原因是釉料膨胀系数大于坯料膨胀系数,使釉层受到拉应力,当应力超过釉层的允许强度和弹性限度时,釉层龟裂。
影响釉惊裂的因素有:
①原料配方或原料性质、原料成分变动,使釉的膨胀系数增高。
如釉中碱土金属氧化物组分提高,釉层中玻璃与晶体混合物的结构网格的键强会降低甚至断裂。
它除导致膨胀系数提高外,还能提高釉的弹性模数,使其弹性变小,这使得补偿坯釉之间接触层中所产生的应力以及对于机械作用所产生应力的应变能力也变小,这种釉就容易产生釉裂。
②釉层过厚,加大了釉层的膨胀率,中间层就相对减小,不足以缓和坯釉之间因膨胀系数差异而出现的应力,易出现釉裂。
当然,过薄的釉层,对釉的光泽和光滑会产生不利的影响。
③釉料的粉碎程度过细、釉烧温度过高、高温时间过长,都将改变釉层的玻璃相和结晶微粒的组成,从而影响釉的膨胀系数和弹性模数。
④坯的膨胀系数和坯的吸水率大小,将直接影响釉的开裂。
如生烧坯,在吸水、干燥的往复过程中,体积膨胀、收缩,造成和加速釉的龟裂,甚至坯釉均裂。
⑤釉的陈腐时间、悬浮性能;施釉时搅拌均匀与否;烧成时的气氛浓度等工艺参数变化,都将或多或少影响釉的龟裂。
日用瓷的斑点成因及克服方法
斑点是日用瓷长期以来难以彻底解决的主要缺陷之一,它直接影响产品的外观质量,是国际市场最忌讳的,尤其在美国市场,对斑点要求极其严格。
斑点是陶瓷制品最容易产生的一种常见缺陷,虽不妨碍日用瓷的使用性能,但却严重影响了它的美观,给人一种不清洁的感觉。
造成斑点的原因比较复杂,因素众多,归纳起来,主要有以下几点原因:
1、产生斑点的机理
①着色杂质颗粒较粗的坯料,在各种烧成条件下都呈现斑点,不过斑点的大小,呈色深浅因烧成条件不同而异。
比如,在1330℃氧化气氛下因坯料已发泡,斑点扩大的倍数大,故呈现大斑点。
②着色杂质颗粒较细的坯料在氧分焰烧成下,无釉素坯上肉眼观察只有很认真才能见到小斑点;在还原焰烧成下,若烧成条件适合坯、釉配方,不显现斑点;若烧成温度较低,显“阴斑点”;若还原气氛欠佳,稍显“阴斑点”。
③反应速度与组分数量、温度、加热时间成正比例,也与颗粒大小成正比例,即参加反应物质的颗粒愈小时,其比表面积愈大,反应速度也越快。
金属铁、铁锈和其他着色杂质在日用瓷中经高温煅烧后“熔融扩散”形成斑点。
据资料介绍,他们在坯中扩散2—3倍,在釉中扩散2—5倍。
如金属铁粒径在0.55—0.61mm时,形成斑点最多;铁锈粒径在0.076—0.10mm时,也形成斑点最多;黑云母粒径在0.154—0.315mm时,烧成后则扩大为0.5—1.5mm的斑点。
④“阴斑点”产生的根本原因与“明斑点”大致一样。
但“明斑点”多系坯、釉中混入较大颗粒的金属铁、铁锈,渗透釉层在釉面呈色;“阴斑点”则多偏重于坯胎表层夹杂稍小的着色矿物和锈泥在釉下透过釉层显色。
例如,某厂产品出现“阴斑点”,就是由于坯料中含云母(铁含量2.61%)呈粗粒存在于坯料内,烧成时不能全部熔融所致。
⑤着色杂质是否呈现斑点和斑点颜色的深浅,主要决定于在高温下形成着色剂化合物的颜色和某些无色化合物(如Al2O3、ZnO、CaCO3等)对色调的改变作用。
而这些与烧成温度的高低,特别是气氛的影响关系极大。
经分解后的氧化铁很不稳定,生成不同形态铁的化合物,显示出不同的颜色;而且原料中含铁矿物的生成条件不同,化学成分也不一样,其呈色随铁含量所占比重的增大,着色增强,颜色加深。
如在氧化焰烧成下,以三价铁存在时,正三价铁离子(Fe3+)产生的颜色范围为红褐色到褐色;而在还原气氛下烧成时,Fe3+被还原成正二价铁离子(Fe2+),呈灰绿色,易溶解在坯釉液相中组成复合硅酸盐,此时呈青菜色,但若正二价铁离子(Fe+2)和正三价铁离子(FeO•Fe2O3)的结晶则呈黑色。
2、斑点产生的原因
引起斑点的原因很多。
一般来说,主要是管理不善使坯、釉中混入的铁锈所致。
原料本身含有一定量的铁,且多为铁的化合物。
还原焰烧成时生成氧化亚铁,当颗粒很细时影响产品色调,不产生斑点。
但云母、黄铁矿(FeS)、鞭铁矿(FeSO3)等若检选不净,则可能产生斑点。
原料加工过程中易混入铁(管道生锈及设备磨损而带入铁锈)。
泥浆输送或贮浆桶的铁件年久氧化或脱落生锈,滤泥机和磨泥机有磨损或锈蚀现象。
过筛粗,吸铁器磁场强度低,一定粒径的杂质才会形成斑点。
泥料若通过220目筛就不会形成0.3mm以上粒径的斑点。
泥料陈腐练制中带入铁锈,工作场地环境不好及风沙带入铁锈,晾泥和供泥过程中混入铁锈,成型设备磨损带入的铁锈,成形过程中带入铁锈,通过多次试烧与摸索,发现成形中产生的斑点缺陷比原料工序严重的多。
采用D250滚压成形机与D254滚压成形机,其中托盘与转盘的磨擦形成的铁锈,以及铸铁滚压头耐磨性不好(1个月内磨损3—5g)形成的铁锈全部带入坯体内,烧成后即达数万个斑点(<0.5mm)。
链式干燥器内链条与框架的磨擦及风盒氧化生锈,烘箱内金属架氧化,链板生锈都能带入铁锈。
锉锈。
泥料未加盖塑料布而落上杂质、灰尘,屋面铁架、工作台不干净等也能带入铁锈。
还有其他因素,如各种运输工具锈蚀,釉料、泥料保管不妥,装窑不扫灰等都能带入铁杂质而产生斑点。
3、克服斑点的办法
(1)加强对吸铁过筛(180—200目)泥浆的稀释,容重在1.2—1.4kg/m3之间。
要多层过筛,后过细筛;专人除渣,防止泥浆溢流;贮泥室每天清扫擦洗,每周一大扫;泥浆运输要遮盖,原料车间不准存放铁器用具;铁屋梁、器具设备要定期用防锈漆涂刷,练泥场地进出换鞋;成型工地要保持干净,坯架要用塑料盖顶包围,釉缸加盖,送釉必须吸铁过100—120目筛;链式烘房金属架要定期刷防锈漆,链板也要定期涂刷,每周彻底清扫设备与干燥箱一次;成型车间泥料不落地,工具尽量做到非铁化,在远离工作地处定点锉刀;装窑须三净,匣钵工序也应加强除铁;所有生产车间做到洒水扫地,减少二次扬尘,有条件的要定期冲洗地面。
一般从原料带入的着色杂质多半为含铁矿物,如钛铁矿、磁铁矿、黄铁矿、褐铁矿、菱铁矿。
一般白瓷(特别是高白瓷)所用陶瓷原料中着色杂质含量本来就很少,经过细磨其分散度高,如果过筛细致,再经过除铁处理,只能影响产