碳化硅电子器件发展分析.docx
《碳化硅电子器件发展分析.docx》由会员分享,可在线阅读,更多相关《碳化硅电子器件发展分析.docx(9页珍藏版)》请在冰豆网上搜索。
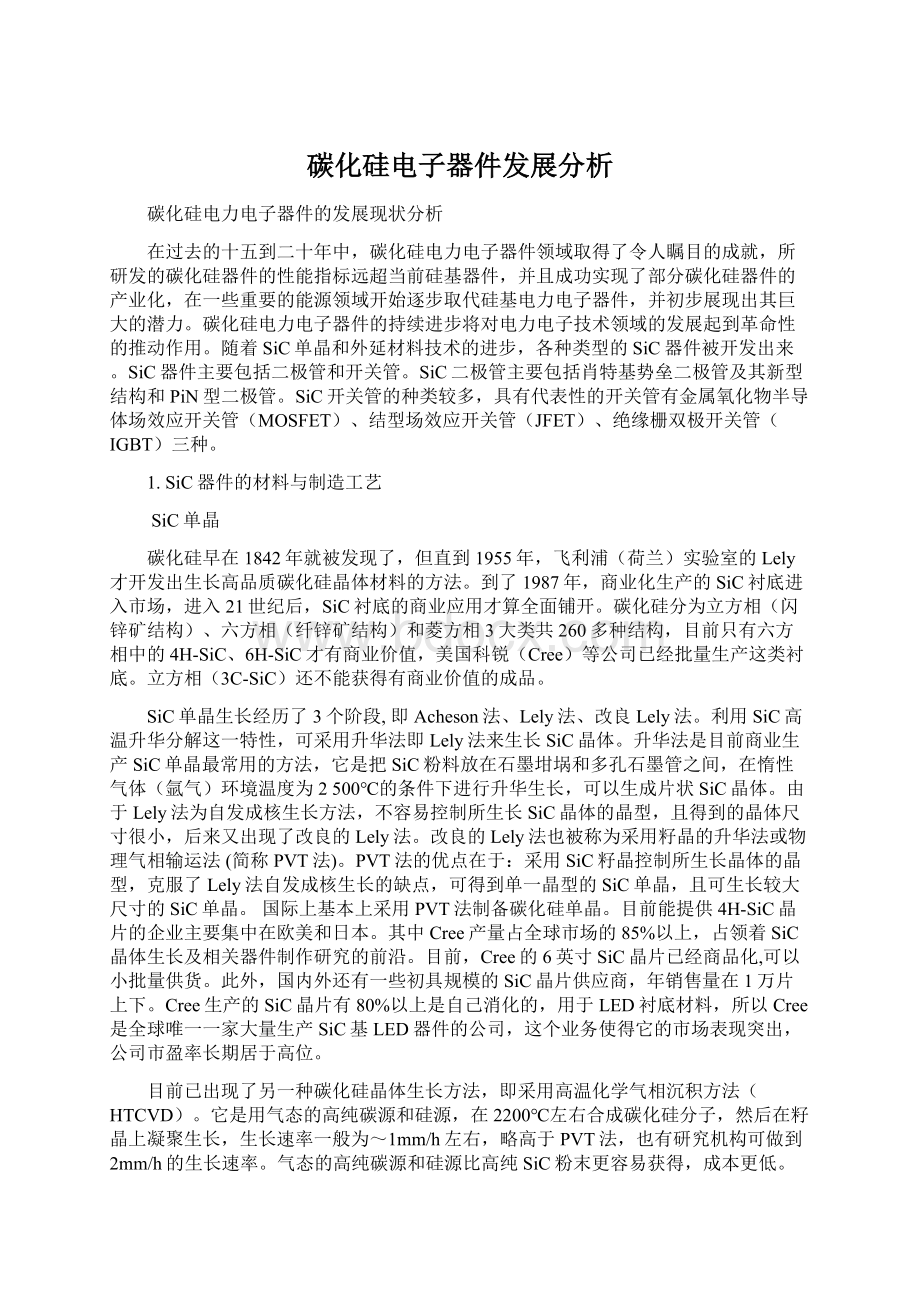
碳化硅电子器件发展分析
碳化硅电力电子器件的发展现状分析
在过去的十五到二十年中,碳化硅电力电子器件领域取得了令人瞩目的成就,所研发的碳化硅器件的性能指标远超当前硅基器件,并且成功实现了部分碳化硅器件的产业化,在一些重要的能源领域开始逐步取代硅基电力电子器件,并初步展现出其巨大的潜力。
碳化硅电力电子器件的持续进步将对电力电子技术领域的发展起到革命性的推动作用。
随着SiC单晶和外延材料技术的进步,各种类型的SiC器件被开发出来。
SiC器件主要包括二极管和开关管。
SiC二极管主要包括肖特基势垒二极管及其新型结构和PiN型二极管。
SiC开关管的种类较多,具有代表性的开关管有金属氧化物半导体场效应开关管(MOSFET)、结型场效应开关管(JFET)、绝缘栅双极开关管(IGBT)三种。
1.SiC器件的材料与制造工艺
SiC单晶
碳化硅早在1842年就被发现了,但直到1955年,飞利浦(荷兰)实验室的Lely才开发出生长高品质碳化硅晶体材料的方法。
到了1987年,商业化生产的SiC衬底进入市场,进入21世纪后,SiC衬底的商业应用才算全面铺开。
碳化硅分为立方相(闪锌矿结构)、六方相(纤锌矿结构)和菱方相3大类共260多种结构,目前只有六方相中的4H-SiC、6H-SiC才有商业价值,美国科锐(Cree)等公司已经批量生产这类衬底。
立方相(3C-SiC)还不能获得有商业价值的成品。
SiC单晶生长经历了3个阶段,即Acheson法、Lely法、改良Lely法。
利用SiC高温升华分解这一特性,可采用升华法即Lely法来生长SiC晶体。
升华法是目前商业生产SiC单晶最常用的方法,它是把SiC粉料放在石墨坩埚和多孔石墨管之间,在惰性气体(氩气)环境温度为2500℃的条件下进行升华生长,可以生成片状SiC晶体。
由于Lely法为自发成核生长方法,不容易控制所生长SiC晶体的晶型,且得到的晶体尺寸很小,后来又出现了改良的Lely法。
改良的Lely法也被称为采用籽晶的升华法或物理气相输运法(简称PVT法)。
PVT法的优点在于:
采用SiC籽晶控制所生长晶体的晶型,克服了Lely法自发成核生长的缺点,可得到单一晶型的SiC单晶,且可生长较大尺寸的SiC单晶。
国际上基本上采用PVT法制备碳化硅单晶。
目前能提供4H-SiC晶片的企业主要集中在欧美和日本。
其中Cree产量占全球市场的85%以上,占领着SiC晶体生长及相关器件制作研究的前沿。
目前,Cree的6英寸SiC晶片已经商品化,可以小批量供货。
此外,国内外还有一些初具规模的SiC晶片供应商,年销售量在1万片上下。
Cree生产的SiC晶片有80%以上是自己消化的,用于LED衬底材料,所以Cree是全球唯一一家大量生产SiC基LED器件的公司,这个业务使得它的市场表现突出,公司市盈率长期居于高位。
目前已出现了另一种碳化硅晶体生长方法,即采用高温化学气相沉积方法(HTCVD)。
它是用气态的高纯碳源和硅源,在2200℃左右合成碳化硅分子,然后在籽晶上凝聚生长,生长速率一般为~1mm/h左右,略高于PVT法,也有研究机构可做到2mm/h的生长速率。
气态的高纯碳源和硅源比高纯SiC粉末更容易获得,成本更低。
由于气态源几乎没有杂质,因此,如果生长时不加入n型掺杂剂或p型掺杂剂,生长出的4H-SiC就是高纯半绝缘(HPSI)半导体。
HPSI与SI是有区别的,前者载流子浓度×1013~8×1015/cm3范围,具有较高的电子迁移率;后者同时进行n、p补偿,是高阻材料,电阻率很高,一般用于微波器件衬底,不导电。
如果要生长n型掺杂或p型掺杂的4H-SiC也非常好控制,只要分别通入氮或者硼的气态源就可以实现,而且通过控制通入的氮或者硼的流量,就可以控制碳化硅晶体的导电强弱。
目前瑞典的NorstelAB公司采用HTCVD商业化生产碳化硅衬底材料(n型、p型、HPSI型),目前已有4英寸HPSI型4H-SiC衬底出售。
SiC外延
为了制造碳化硅半导体器件,需要在碳化硅晶片表面生长1层或数层碳化硅薄膜。
这些薄膜具有不同的n、p导电类型,目前主流的方法是通过化学气相沉积方法进行同质外延生长。
碳化硅外延生长方案中,衬底起很大的支配作用,早期碳化硅是在无偏角衬底上外延生长的,即从晶锭上切割下来的晶片其外延表面法线与晶轴(c轴)夹角θ=0°,如碳化硅晶片的Si(0001)或C(000)面,外延表面几乎没有台阶,外延生长期望能够由理想的二维成核生长模型控制。
然而实际生长发现,外延结果远未如此理想。
由于碳化硅是一种多型体材料,外延层中容易产生多型体夹杂,比如4H-SiC外延层中存在3C-SiC夹杂,使外延层“不纯”,变成一种混合相结构,极大地影响碳化硅器件的性能,甚至不能用这样的外延材料制备器件。
另外,这样的外延层宏观外延缺陷密度很大,不能用常规的半导体工艺制备器件,即薄膜质量难于达到晶圆级外延水平。
后来发展了偏8°斜切碳化硅衬底,经过几十年的不断发展完善,现在己经成为碳化硅外延的主要技术方案。
与无偏角衬底比较起来,偏8°斜切衬底的外延表面有很高的台阶密度,且台面长度很短,一般为十几纳米,反应物容易从台面上迁移到台阶扭折处。
外延时,不必等着扭折沿台面运动到表面边缘,所有的扭折可以同时以相似类的速率运动,直至外延生长结束,这就是所谓的台阶流控制(step-flow)外延生长机制。
虽然在偏8°斜切衬底上外延时可以利用台阶流进行控制生长,较好地解决了多型体夹杂及相应的宏观缺陷等问题,但是它也有其固有劣势。
Cree在SiC衬底制备方面具有业内领先地位,它的产品是业界的风向标,代表了需求的发展方向。
首先,衬底斜切,在增加外延台阶的同时,也引入了基平面位错,其次,衬底斜切,衬底产率降低,造成了很大的原材料浪费,增加了衬底制备的成本。
当晶圆直径增大时,这个问题变得更加突出。
Cree现在供应的主流衬底片主要是4英寸和6英寸大尺寸晶片,其中4英寸片提供斜切偏角为4°以及无偏角的,8°的可以定制;6英寸片只提供无偏角的,对于相同规格(产品等级、掺杂类型、微管密度等)的衬底片,偏8°的比偏4°的贵约1000美元,偏4°的比无偏角的贵约1200美元,当衬底片用量很大时,这是一个很可观的数目。
因此,从以上分析并结合目前发展趋势来看,大偏角斜切衬底必然是一个过渡方案,在世界各国科技人员的努力下,外延要回归到小偏角斜切衬底方向上来。
现在Cree主推偏角为4°衬底。
SiC器件工艺
虽然碳化硅器件工艺和设备都与硅器件有很强的兼容性,但也远不是可以原封不动地照搬。
与硅相比,碳化硅器件工艺的温度一般要高得多。
碳化硅晶片较小、易碎、透明、难适应,倒是一些大学实验室比较灵活,而且价格昂贵,大公司的生产线较成为开发碳化硅器件工艺的主力。
掺杂是最基本的器件工艺。
由于一般杂质在碳化硅中的扩散系数跟在Si02中一样低,在适合于对碳化硅进行有效杂质扩散的温度下,Si02已失去了对杂质的掩蔽作用,而且碳化硅本身在这样的高温下也不稳定,因此不宜采用扩散掺杂,而主要靠离子注入和材料制各过程中的伴随掺杂来满足制造碳化硅器件的需要。
在碳化硅材料的气相生长过程中,n型掺杂一般用电子级纯度的氮做掺杂剂,P型掺杂一般使用三甲基铝。
n型离子注入的杂质一般也是氮。
氮离子注入对晶格的损伤比较容易用退火的方式消除。
P型离子注入的杂质一般也是铝。
由于铝原子比碳原子大得多,注入对晶格的损伤和杂质处于未激活状态的情况都比较严重,往往要在相当高的衬底温度下进行,并在更高的温度下退火。
这样就带来了晶片表面碳化硅分解、硅原子升华的问题。
残留碳如果能形成石墨态碳膜,会对阻止表面继续分解起一定作用。
于是,尺寸与碳比较相当的硼也成为常用的p型注入杂质。
目前,P型离子注入的问题还比较多,从杂质选择到退火温度的一系列工艺参数都还需要优化,而P型离子注入对提高功率MOS的沟道迁移率又十分重要。
栅氧化物与碳化硅之间的界面缺陷对功率MOS的沟道迁移率也有十分重要的影晌,因而栅氛化物的生长或淀积十分关键。
除类似于硅的热氧化之外,碳化硅还可用燃烧法生长栅氧化物,而且这种方法产生的界面态密度较低。
用热氧化法在NO中生长栅氧化物也能降低界面态的密度。
就同样的栅氧化物生长方法而言,6H-SiC比4H-SiC的沟道迁移率要高一些;而就体材料中的载流子迁移率而言,是4H-SiC比6H-SiC高。
这说明4H-SiC的氧化物界面缺陷问题比较严重。
使用1400℃高温快速退火法,n型和P型4H-SiC的欧姆接触都可以做到单位面积接触电阻低达10-5?
cm2量级的水平,所用的电极材料分别是Ni和A1。
不过这种接触在400℃C以上的热稳定性较差。
对P型4H-SiC采用Al/Ni/W/Au复合电极可以把热稳定性提高到600℃100小时,不过其接触比电阻高达10-3?
cm2。
采用TaC和AlSi合金电极也可获得类似效果。
6H-SiC比4H-SiC容易获得低阻欧姆接触,其接触比电阻可低达10-6?
cm2。
在高压硅器件中采用的多数终端技术和钝化技术,比如场板、场环和结终端等也适用与碳化硅器件。
除此而外,在结终端注入大剂量Ar或B,借损伤晶格形成高阻区,起类似于硅功率器件中半绝缘多晶硅(SIPOS)的作用,也有明显效果。
若在Ar、B离子注入后再在600℃退火,器件的反向特性还会进一步改善。
目前SiC功率器件封装工艺及方法通常借鉴SiIGBT封装技术,在DBC布局、芯片键合、高温焊料、硅凝胶填充、密封材料等方面还存在一些问题,针对SiC器件封装特殊要求,三菱、塞米控、富士等公司在封装材料及结构方面提出了新的思路,如三菱公司铜针布线技术,塞米控公司低温纳米银烧结技术,富士公司低电感和优化的DBC布局设计。
2.SiC二极管实现产业化
SiC电力电子器件中,SiC二极管最先实现产业化。
一般可分为肖特基二极管(Schottky?
barrier?
diode,?
SBD)、PiN二极管和结势垒控制肖特基二极管(junction?
barrier?
Schottky,?
JBS)三种。
在5kV阻断电压以下的范围,碳化硅SBD具有一定的优势,而对于PiN结二极管,由于其内部的电导调制作用而呈现出较低的导通电阻,使得它更适合制备4~5kV或者以上电压等级的器件。
JBS?
二极管则结合了肖特基二极管所拥有的出色的开关特性和PiN结二极管所拥有的低漏电流的特点。
另外,把JBS二极管结构参数和制造工艺稍作调整就可以形成混合PiN-肖特基结二极管(merged?
PiN?
Schottky,?
MPS)。
2001年德国Infineon公司率先推出SiC二极管产品,美国Cree和意法半导体等厂商也紧随其后推出了SiC二极管产品。
在日本,罗姆、新日本无线及瑞萨电子等投产了SiC二极管。
很多企业在开发肖特基势垒二极管(SBD)和JBS结构二极管。
目前,SiC二极管已经存在600V~1700V电压等级和50A电流等级的产品。
SiC肖特基二极管能提供近乎理想的动态性能。
做为单子器件,它的工作过程中没有电荷储存,因此它的反向恢复电流仅由它的耗尽层结电容造成,其反向恢复电荷以及其反向恢复损耗比Si超快恢复二极管要低一到两个数量级。
更重要的是,和它匹配的开关管的开通损耗也可以得到大幅度减少,因此提高电路的开关频率。
另外,它几乎没有正向恢复电压,因而能够立即导通,不存在双极型器件的开通延时现象。
在常温下,其正态导通压降和Si超快恢复器件基本相同,但是由于SiC肖特基二极管的导通电阻具有正温度系数,这将有利于将多个SiC肖特基二极管并联。
在二极管单芯片面积和电流受限的情况下,这可以大幅度提高SiC肖特基二极管的容量,使它在较大容量中的应用成为可能。
目前实验室报道的最大容量的SiC二极管已经达到了6500V/1000A的水平。
由于SiC开关管的发展相对二极管滞后,当前更普遍的做法是将SiC二极管和SiIGBT和MOSFET器件封装在一个模块中以形成大功率开关组合。
目前Cree公司、Microsemi公司、Infineon公司