125MN油压双动铝挤压机设计.doc
《125MN油压双动铝挤压机设计.doc》由会员分享,可在线阅读,更多相关《125MN油压双动铝挤压机设计.doc(55页珍藏版)》请在冰豆网上搜索。
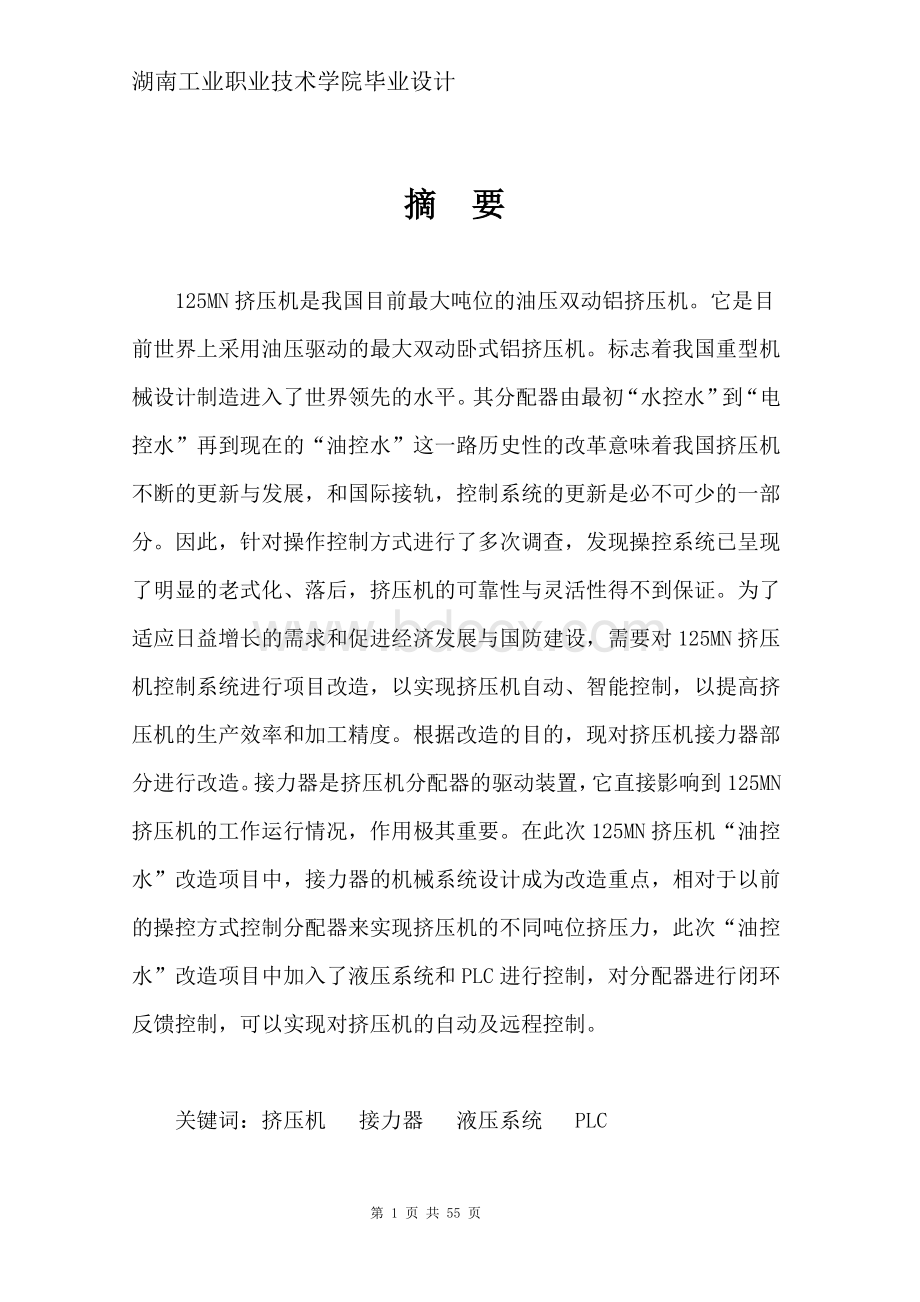
湖南工业职业技术学院毕业设计
摘要
125MN挤压机是我国目前最大吨位的油压双动铝挤压机。
它是目前世界上采用油压驱动的最大双动卧式铝挤压机。
标志着我国重型机械设计制造进入了世界领先的水平。
其分配器由最初“水控水”到“电控水”再到现在的“油控水”这一路历史性的改革意味着我国挤压机不断的更新与发展,和国际接轨,控制系统的更新是必不可少的一部分。
因此,针对操作控制方式进行了多次调查,发现操控系统已呈现了明显的老式化、落后,挤压机的可靠性与灵活性得不到保证。
为了适应日益增长的需求和促进经济发展与国防建设,需要对125MN挤压机控制系统进行项目改造,以实现挤压机自动、智能控制,以提高挤压机的生产效率和加工精度。
根据改造的目的,现对挤压机接力器部分进行改造。
接力器是挤压机分配器的驱动装置,它直接影响到125MN挤压机的工作运行情况,作用极其重要。
在此次125MN挤压机“油控水”改造项目中,接力器的机械系统设计成为改造重点,相对于以前的操控方式控制分配器来实现挤压机的不同吨位挤压力,此次“油控水”改造项目中加入了液压系统和PLC进行控制,对分配器进行闭环反馈控制,可以实现对挤压机的自动及远程控制。
关键词:
挤压机接力器液压系统PLC
ABSTRACT
125MNextrusionmachineisourcountryatpresentthebiggesttonnagedoublemotionandaluminumextrusionmachineoil.Itistheworld'slargesthydraulicdriveondoublemotionandhorizontalaluminumextrusionmachine.Markstheheavymechanicaldesign,manufacturinginChinaintotheworld'sleadinglevel.Thedistributorfromthefirst"waterwatercontrol"to"electricwater"andtothepresent"oilcontrolwater"theflightofthehistoricreformmeansourextrusionmachineconstantlyupdateanddevelopment,andtheinternationalcommunity,therenewalofthecontrolsystemisanessentialpart.Therefore,inviewoftheoperationcontrolmodehascarriedonmanytimesthesurveyandfoundthatcontrolsystemhaspresentedobviousofold,andbackward,andextrusionmachinereliabilityandflexibilitynotguarantee.Inordertomeetthegrowingneedsofandpromoteeconomicdevelopmentandnationaldefenseconstruction,needto125MNextrusionmachinecontrolsystemreconstructionproject,inordertorealizeautomaticextrusionmachines,intelligentcontrol,inordertoimprovetheproductionefficiencyandextrusionprocessingprecision.Accordingtothepurposeofthereform,isthepartofextrusionmachinesrelayfurnace.Therelayisthedrivingequipmentdistributorextrusionmachine,itdirectlyaffects125MNextrusionmachineworkingsituation,thefunctionisextremelyimportant.Inthe125MNextrusionmachine"oilwatercontrol"reconstructionproject,therelayofthemechanicalsystemdesignbecometransformationkey,relativetothepreviouscontrolmodecontroldistributortoachieveextrusionmachinedifferenttonnageextrusionpressure,the"oilwatercontrol"reconstructionprojectwiththehydraulicsystemandPLCcontrol,todistributorforclose-loopfeedbackcontrol,whichcanmaketheextrusionmachinesautomaticandremotecontrol.
Keywords:
extrusionmachinerelayishydraulicsystemPLC
目录
第一章概述……………………………………………………………6
1.1课题背景……………………………………………6
1.2挤压机的技术现状及发展趋势……………………8
1.2.1技术现状……………………………………………8
1.2.2发展趋势…………………………………………14
1.3125MN挤压机原驱动方式分析…………………14
1.4本章小结…………………………………………18
第二章接力器设计方案确定……………………………19
2.1接力器和挤压机的关系……………………………19
2.2分配器驱动方式比较………………………………20
2.3接力器设计方案确定………………………………23
2.4本章小结……………………………………………24
第三章接力器控制系统设计……………………………25
3.1液压控制系统设计………………………………25
3.1.1液压系统设计总则………………………………25
3.1.2液压回路设计……………………………………26
3.1.3液压控制与分配器凸轮轴转角关系……………30
3.1.4液压系统元件的选用……………………………33
3.1.5液压系统安全性…………………………………36
3.1.6小结………………………………………………37
3.2电气控制系统设计………………………………38
3.2.1电气控制系统原则………………………………38
3.2.2电气控制系统设计………………………………39
3.2.3电器元件选择……………………………………45
3.3PLC系统硬件配置………………………………46
3.3.1软件设计…………………………………………49
3.4本章小结…………………………………………50
第四章总结与展望………………………………………51
4.1总结…………………………………………………51
4.2展望…………………………………………………52
结束语…………………………………………………………53
鸣谢……………………………………………………………54
参考文献………………………………………………………55
附录……………………………………………………………55
第一章概述
1.1课题背景
本论文“接力器控制系统设计”的背景是西南铝业集团有限公司“125MN挤压机现代化配套改造”项目。
该项目主要包括操纵系统改造、大小节流装置改造、进料机构重新设计制造、运垫机构改造、润滑系统改造等几大部分。
本论文主要研究工作为125MN挤压机操纵系统改造。
针对主分配器的驱动机构---接力器进行设计改造。
目的是设计一个液压驱动系统及控制系统,通过闭环反馈控制,启闭分配器,实现水压机的控制。
西南铝业集团有限责任公司锻造分厂的125MN挤压机(如图1)是我国目前最大的挤压机之一,是国防工业和基础建设的关键设备,在我国国防建设和经济发展中发挥着重要的作用。
该机由沈阳重型机器厂在20世纪60年代初期设计和制造,是我国自力更生生产的第一台这种大型的设备。
125MN挤压机为卧式四缸四柱带穿孔的系统结构,泵--蓄势器传动方式。
挤压力分55MN/7OMN/125MN三级,穿孔力为31.5MN。
主要用于生产大型的铝型材、铝棒材、铝管材等,例如波音飞机和直8的机翼。
其制品最大外接圆直径可达中600mm,最大宽度800mm,最大长度30m。
图1-1
但是由于该挤压机制造建成于上世纪六十年代末期,控制方式落后、自动化程度低、控制元器件老化,其控制系统控制精度不高、响应速度慢、可靠性低,已不能满足现代化生产的需要。
随着电子技术、液压控制技术以及液压元器件的进步和发展、控制学科发
展等,采用现代化的科学技术对挤压机进行改造,以提高设备的控制精度、加工精度以及生产效率,改善设备的操作方式,提升设备的自动化水平,是完全必要和迫切的。
此次挤压机接力器的设计和改造会加入一个液压系统,由以前“水控水”到“电控水”,现在将转变为“油控水”,并加入PLC进行闭环控制。
原有系统驱动方式为直流电机驱动,具体为通过交流电机带动直流发电机发电,发出的电能驱动直流电机运转,再通过蜗轮蜗杆减速器驱动各分配器凸轮轴的旋转。
分配器控制最主要的系统为直流电机控制的位置随动系统,这种驱动方式中间环节多,故障率高,维修繁琐。
现拟采用油缸+齿轮齿条+凸轮装置的驱动方式,通过油缸驱动齿轮齿条装置,带动分配器的凸轮轴旋转,通过编码器检测到的凸轮转角模拟信号反馈给PLC,再调整液压系统进行控制。
从而能较精确的调节分配器阀的开启和开启高度。
也实现了自动及远程的控制要求。
设计后的接力器将实现125MN挤压机的自动及远程控制,控制精度和效率都将得到提高。
改造完成后的125MN挤压机继续为我国国防建设和经济发展做出贡献
1.2挤压机的技术现状及发展趋势
1.2.1技术现状
我们一般称挤压力大于50MN的为大型挤压机,挤压力大于80MN的为特大型挤压机。
据不完全统计,目前全世界已投产的挤压力大于80MN的铝型材挤压机约有65台左右。
美国拥有大型挤压机最多,达20台,超过10OMN的有4台。
俄罗斯有10台,大部分是80年代以前投产的,泵--蓄势器传动方式居多,其中前苏联古比雪夫铝加工厂的2OOMN挤压机是世界上最大的挤压机。
日本有4台,挤压力最大的为95MN。
德国有5台,德国VAW波恩工厂1999年投产了一台10OMN的双动油压挤压机。
韩国、波兰、瑞士、挪威、瑞典各有l台大型挤压机,挤压力在65MN-90MN之间。
意大利有3台大型挤压机,2000年建成投产了一台130MN的铜、铝油压挤压机。
我国拥有大型、特大型挤压机数量大约是20台。
在挤压机本体方面,近年来国外发展了钢板组合框架和预应力“T”型头板柱结构机架及预应力混凝土机架,大量采用扁挤压筒、固定挤压垫片、活动模架和内置式独立穿孔系统。
在传动形式方面发展了自给油机传动系统,甚至在10OMN-150MN挤压机上也采用了油泵直接传动装置。
现代挤压机及其辅助系统的工作都采用了PLC(程序逻辑控制)系统和CADEX等控制系统,即实现了速度自动控制和等温--等速挤压、工模具自动快速装卸,乃至全机自动化控制。
挤压机的机前设备(如长坯料自控加热炉,坯料热切装置和坯锭运送装置等)和机后设备(如牵引装置,精密水、雾、气在线淬火装置,活动工作台,冷床和横向运输装置,拉伸矫直机,成品锯,人工时效炉等)已经实现了自动化和连续化运行。
美国通用合金(UniversalAlloy)公司对其购进的二手二战时期德国杜依斯堡(Drisburg)液压公司制造的125MN挤压机进行了技术改造。
主要改造内容:
一是挤压力由125MN提高至145MN;二是由原来的正向挤压改为正、反向两用挤压机;三是由泵--蓄势站传动改为油泵直接传动。
改造的目标是为波音公司生产7E7型飞机、欧洲空中客车公司生产的A380飞机从机身到机翼的各种特大型材,如纵梁、板条、一体化带筋壁板等。
可生产长32m,最宽壁板1016mm、单位质量134Kg/m的铝型材。
改造完成后,该挤压机将是北美最大铝型材挤压机,世界上最大的泵直接传动的挤压机,世界第三大铝型材挤压机。
近年来,我国改造或者新建的大型挤压机主要有:
1、1999年我国太原重型机械集团有限公司设计、制造出了75MN泵直接传动铝挤压机。
2、西南铝业集团有限责任公司95/80MN挤压机现代化配套改造;3、2002年山东丛林集团投资,西安重型机械研究所设计、上海重型机器厂制造的世界第一条1OOMN油压双动铝挤压机。
4、2005年,辽宁忠旺集团投资,西安重型机械研究所设计、上海重型机器厂有限公司制造的125MN油压双动铝挤压机。
它是目前世界上采用油压驱动的最大的双动卧式铝挤压机,标志着我国重型机械设计制造进入了世界领先的水平。
(1)液压系统
95/80MN挤压机在改造中,由泵--蓄势器传动方式改造为油泵直接传动。
用5台PVV-540大流量伺服变量轴向柱塞泵给主系统供油,泵的额定工作压力为31.5MPa,最高压力可达4OMPa。
控制阀选用集成式插装阀,各控制回路阀块除有特定控制功能外,还具有超压保护功能。
主缸控制回路阀采用先进的差动式比例锥阀。
通过计算机设置回路压力或流量大小,实现主缸准确的无级卸压及回程调速控制,使挤压机能够快速、无冲击的平稳工作。
控制回路中利用位移传感器将变量缸位移信号反馈给伺服放大器前端,从而实现高精度的远程可变流量控制。
利用压力传感器将压力反馈信号与预置压力信号进行比较,实现泵的压力控制。
由于控制回路采用了先进的流量、压力双指令控制,可实现主油泵的稳定变量控制,进而准确稳定的控制挤压、剪切等运动部件的速度。
1OOMN挤压机在挤压速度为0.2mm/s专门配置了小流量高压变量泵和高频响应的电磁比例阀联合调速的闭环回路,通过PID调节器使挤压轴按挤压工艺要求的速度-行程曲线来调整,使重达180t的活动部分在0.2mm/s低速工作下不爬行,调速响应频率不超过50ms,达到较高的调速精度。
挤压速度大于5mm/s时,直接用变量泵加定量泵进行开环容积调节,为挤压机创造了可实现等温挤压工艺的变速条件。
针对挤压机挤压力大于100MN时,主缸内油液压缩量达184L,按35卸压时间计算,瞬时排出的流量高达3600L/min,相当于7台500L/min流量的大泵在同时排放,容易产生大的振动,给系统造成大的危害的情况,应用了西安重型机械所的专利技术“带阻尼卸压、排液用三级插装阀”,使系统能按理想卸压曲线进行快速卸压、振动小、挤压机工作平稳。
主机液压控制系统集中在油箱顶部,采用新一代的二通插装阀集成式分配器,该阀具有开启行程小、过油量大、动作响应快等特点。
对几只流量特大的主阀采用西安重型机械所的专利技术“用于高压大流量进、排液控制的三级插装阀”,在先导控制阀和大通径插装锥阀之间增加一套中间插装阀,并通过功能元件控制三级阀的启闭速度构成理想的液压控制回路,减少了系统冲击,加快了阀的启闭速度。
中间主缸的柱塞直径达2m,为确保高速空程前进的缸内充液和回程时大流量的排液,要避免主缸吸空,西安重型机械所自行开发设计了国内卧式液压机最大口径DN400的充液阀,在主缸后部三只并联使用。
125MN挤压机选用预卸压阀和比例溢流阀两种卸压元件来实现挤压机的卸压。
通过电控系统控制的比例溢流阀在卸压初始阶段有良好的卸压性能,但当压力减小到3MPa左右时,其卸压速度急剧减慢,此时启用预卸压阀,使工作缸的压力快速卸掉。
比例溢流阀可根据不同的挤压工艺及挤压工具,设定挤压机最高工作压力,从而对挤压工具起到有效保护作用。
125MN挤压机采用了与100MN挤压机类似的充液系统,并自行开发研制了相应规格为DN450的充液阀。
主控液压系统采用带外控功能的两级控制插装阀,通过调整先导控制阀下叠加的双作用单向节流阀,实现对主阀启闭速度的有效控制,所带外控功能可以有效改善大型两级插装阀动作响应慢的缺点。
辅控系统的油源是由定量泵与蓄能器构成的恒压传动系统,用带叠加式高开启压力液压锁的J型中位机能比例或普通电磁滑阀作为控制阀,确保在阀断电状态时辅机装置的位置固定,为挤压机的自动化提供保障。
125MN挤压机在液压系统设计时分析了引起油温升高的原因,采用变量泵或变量泵与定量泵组合的形式通过容积调速的方法来实现工作缸工作速度的调整,尽可能少用节流阀和减压阀,使系统溢流尤其是高压溢流情况的出现减少到最低程度。
挤压筒锁紧保压系统、主泵外控系统、阀外控系统均采用恒压变量泵与蓄能器组合而成的恒压传动系统,保证了微量溢流情况下的恒定控制压力输出,既节能又降低了发热。
(2)电控系统
75MN铝挤压机的机后区分成三个相对独立的控制区,采用三台PLC对其进行控制,可独立工作,互不依赖,同时应用网络技术将PLC联网,实现集中监督、管理。
PLC选用高可靠性的SIMATICS7系列产品,配置为l套S7-400PLC、2套S7-300PLC以及分布式I/O和人机界面TD17、OP27,通过PROFIBUS-DP网络连接起来,实现联网控制。
为了实现生产车辆用大型铝合金型材所要求的铸锭加热温度准确、挤压速度稳定可控、牵引与热锯同步、成品精密锯切等性能,95/80MN挤压机电控系统选用西门子公司的S7-400PLC作为主控组件和PROFIBUS网络,组成全机列的控制系统。
1OOMN挤压机电气控制系统由独立的三部分组成:
主机、活动出料台以及后部出料系统,它们通过MPI网络相互通讯,对挤压生产线进行联网控制。
主机控制系统采用西门子S7-400系列PLC,CPU为416-2,通过PROFIBUS-DP与分布式1/0模块ETZOOM进行通讯,共同担负主机的数据采集、处理、挤压工作程序的执行。
操作台上两台SIMATICTP37-10触摸屏与主机、活动出料台以及后部出料系统的PLC通过MPI构成网络,来完成下列主要操作功能:
泵的启动停止;联机设定挤压机参数;图形显示挤压速度、压力、位置的实际值;故障显示与报警等。
1.2.2发展趋势
1高速化,高效化,低能耗。
提高挤压机的工作效率,降低生产成本。
在大型型材、壁板的生产方面,产品规格品种增加,难度加大,其特征是宽高比大、壁厚薄。
挤压工艺技术也将会有大改进和发展。
高效反挤压、扁挤压、宽展挤压、组合模挤压、穿孔挤压、静液挤压、连续挤压、快速挤压等新工艺技术将得到更广泛的应用和推广。
2机电一体化。
充分合理利用机械和电子方面的先进技术促进整个液压系统的完善。
电子技术的发展、计算机的应用和普及,促进了挤压设备控制系统的高度自动化,提高了挤压机速度闭环控制的精度,进一步满足了挤压工艺的要求
3自动化、智能化。
微电子技术的高速发展为挤压机的自动化和智能化提供了充分的条件,自动化不仅仅体现在加工,应能够实现对系统的自动诊断和调整,具有故障预处理的功能。
4各元件集成化,标准化,特别是集成的液压系统减少了管路连接,有效地防止了泄漏和污染。
标准化元件为机器维修带来了方便。
未来十年,我国的挤压加工技术以及制品在高、新、精方面将会有突破性进展。
1.3125MN挤压机原驱动方式分析
125MN挤压机采用泵--蓄势站传动方式,使用32MPa的高压水乳液和0.7-1.2MPa的低压水乳液。
高压水用于挤压机前后主工作缸、穿孔工作缸、挤压容室工作缸、剪刀工作缸的工作行程。
低压水用于挤压机前、后主工作缸,穿孔工作缸,挤压容室工作缸,剪刀工作缸的空行程或空试车。
125MN挤压机操纵系统中一个重要部分就是分配器,它是高压液体进入工作缸的必经之路,通过控制分配器上锥阀的开启以及开启高度来控制工作柱(活)塞的方向和移动速度。
125MN挤压机有7个分配器,即主分配器、穿孔分配器、容室分配器、大剪刀分配器、移动工作台分配器、锁键分配器、分离机分配器,分别对应控制挤压机的活动横梁、穿孔小动梁、挤压容室、大剪刀、移动工作台、锁键以及分离机的动作。
下面以主分配器为例说明分配器的工作原理。
主分配器的阀配置如图2-1所示,阀开启图如图2-2所示。
(l)当凸轮轴角度在-11°—11°之间时,锥阀1、2、3、4都关闭,主分配器处于停止状态,相应的活动横梁无动作;
(2)随着凸轮轴向加压方向旋转,锥阀3慢慢打开,前后活动横梁回程缸的水回低压罐,活动横梁空程前进;(3)凸轮轴旋转到106°时,锥阀2、3完全打开,来自高压水泵站的高压水进入后主缸,推动活动横梁以5500T压力向前;(4)凸轮轴旋转到2000时,锥阀1、3打开,高压水进入前主缸,活动横梁以7000T压力向前;(5)凸轮轴旋转到253°时,锥阀1、2、3打开,高压水进入前、后主缸,活动横梁以12500T压力向前;(6)凸轮轴回程方向旋转到-53°时,锥阀4打开,高压水进入回程缸,推动活动横梁向后。
图2-1主分配器阀配置图图2-2主分配器阀开启图
图2-3交流电机控制的分配
125MN挤压机分配器原来的驱动方式为“电控水”,具体可分为两
种:
1、移动工作台分配器、锁键分配器、分离机分配器是以交流电机经蜗轮减速器驱动分配器的凸轮轴,在凸轮轴端装有终端开关,用于控制凸轮轴转动的角度,其驱动方式如图2-3所示。
2、主分配器、穿孔分配器、容室分配器、大剪刀分配器是以直流电机经蜗轮减速器驱动分配器的凸轮轴,其电气控制原理如图2-4所示。
ZF是装在操作台手柄上的自整角机,而自整角接收机ZJ装在分配器的转轴上。
当操作台的手柄使ZF转过一个角时,就会与ZJ出现角度差,而使ZJ的激励绕组出现感应电动势。
这个电势经过相敏整流器输入电机放大机的激磁绕组,从而控制传动分配器转轴(经蜗轮蜗杆减速)的直流电动机。
随着转轴的转动,自整角机ZJ、ZF的差角减小,直至为零,电子相敏整流器无输出,直流电动机也随之停止转动。
这种驱动方式电路比较复杂,中间环节多,故障率高,维修繁琐。
图2-4直流电机控制分配器的电气原理
125MN挤压机电气控制系统为传统的继电器--接触器控制方式,人工操作启动按钮(开关),经中间执行元件(各种继电器、行程开关、热元件、接触器等),直至执行机构,都必须靠硬连接。
而挤压机本体庞大,机构众多,联锁关系复杂,使接线繁多,维护量大,可靠性差。
1.4本章小结
对125MN挤压机的了解和分析,125MN挤压机(如图1-1)是我国目前最大的挤压机之一,该机