制药机械学讲义.doc
《制药机械学讲义.doc》由会员分享,可在线阅读,更多相关《制药机械学讲义.doc(61页珍藏版)》请在冰豆网上搜索。
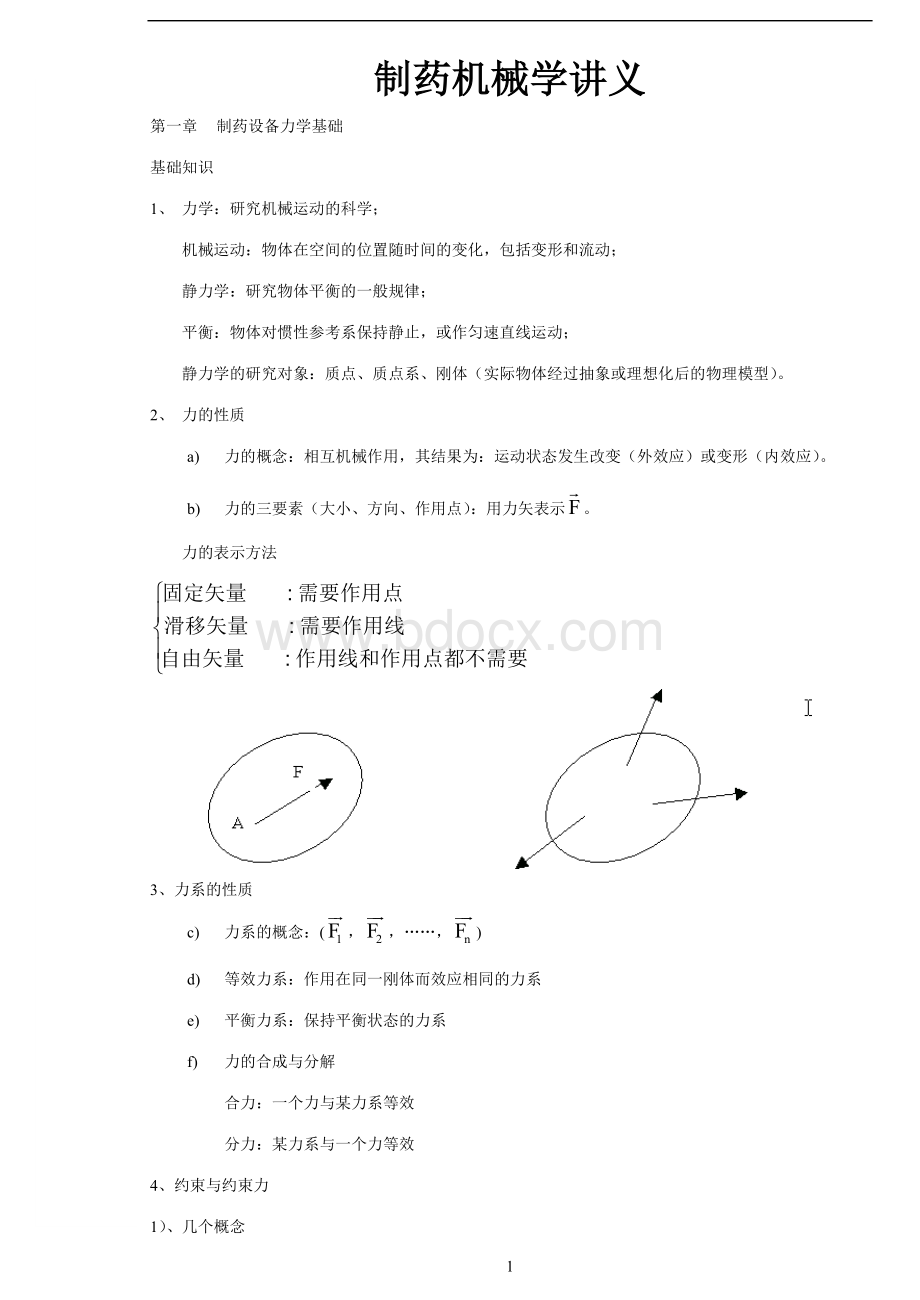
制药机械学讲义
第一章制药设备力学基础
基础知识
1、力学:
研究机械运动的科学;
机械运动:
物体在空间的位置随时间的变化,包括变形和流动;
静力学:
研究物体平衡的一般规律;
平衡:
物体对惯性参考系保持静止,或作匀速直线运动;
静力学的研究对象:
质点、质点系、刚体(实际物体经过抽象或理想化后的物理模型)。
2、力的性质
a)力的概念:
相互机械作用,其结果为:
运动状态发生改变(外效应)或变形(内效应)。
b)力的三要素(大小、方向、作用点):
用力矢表示。
力的表示方法
3、力系的性质
c)力系的概念:
(,,……,)
d)等效力系:
作用在同一刚体而效应相同的力系
e)平衡力系:
保持平衡状态的力系
f)力的合成与分解
合力:
一个力与某力系等效
分力:
某力系与一个力等效
4、约束与约束力
1)、几个概念
非自由体(受约束体)
约束:
限制条件
约束力:
与约束相关约束与非自由体接触,相互作用产生作用力。
2)、几种常见的约束
a)柔绳
只能承受拉力,注意约束力的特点
b)光滑支承面
约束力的方向:
沿接触点的公法线而指向被约束的物体,。
c)光滑圆柱铰链
i.固定铰链支座
ii.连接铰链
iii.径向轴承
iv.活动铰链支座
d)光滑球铰链
v.球铰
vi.止推轴承
e)二力构件
二力构件(二力杆)的概念;
二力构件平衡的条件:
刚体在二力作用下平衡的必要充分条件是此而力等值、反向、共线。
二力构件约束力的特点:
必定共线,方向可以任意假定。
二力构件的实际约束形势是多种多样的,注意区分。
第一节剪切与挤压
1、剪切概念
如上图所示的剪床剪裁钢板的情形:
剪床上的上下两个刀刃以大小相等、方向相反、作用线距离很近的两个P力作用于钢板上,迫使钢板在m—n截面的左右两部分沿m—n截面发生相对错动,直到钢板被剪断。
与此类似的还有:
传动轴与轮之间的键联接、螺栓联接、铆接等……
剪切的特点:
作用与构件两个侧面上且与构件轴线垂直的外力,可以简化成大小相等、方向相反、作用线相距很近的一对力,使构件两部分沿剪切面有发生相对错动的趋势。
2、挤压的概念
螺栓、销钉、键、铆钉等联接件,除了承受剪切以外,在联接件和被联接件的接触面上还相互压紧——这种现象称为挤压。
3、挤压的实用计算
在挤压面上,应力的分布比较复杂。
在实用计算时,假设挤压面上的应力均匀分布,有
相应的强度条件是
关于挤压面积的计算:
1、接触面为平面,如剪联接,其接触面积即为挤压面积;
2、接触面为圆柱面:
圆孔或圆钉的直径平面。
例题截面为正方形的两木杆的榫接头。
已知:
木材的顺纹许用挤压应力,顺纹许用剪应力,顺纹许用拉应力。
若P=40KN,试设计a、b、l。
解:
1、顺纹挤压条件为
(1)
2、顺纹剪切强度条件为
(2)
3、顺纹拉伸强度条件为
(3)
联立
(1)、
(2)、(3)式,解得
例题:
试导出圆墩的体积最小时决定其半径r的方程。
已知:
圆墩顶部承受压顶面的力P,加上自身的重量,墩身的密度为,容许压应力为。
解:
提示:
(1)
根据
(1)式有
两边积分得:
在四,面积,为顶面积,有
由此得
求半径:
求体积:
第二节扭转
一、扭转的概念
如丝锥、机床的光杆……等等
二、扭矩和扭矩图
1、外力偶的计算
⑴已知条件:
传动的功率P(KW),转速n(转/分、rpm、r/min)
外力偶m=?
⑵横截面上扭矩T的计算
利用截面法,可以方便求出各段的扭矩T。
扭矩T方向的规定:
一般按照右手螺旋法则,把T作为矢量对待,当矢量的方向与截面的外法线方向一致时为正,否则为负。
⑶扭矩和扭矩图
根据公式1和截面法可以直接计算传动轴各段的扭矩,并画出扭矩图。
例题如图所示为传动轴,有主动轮A输入功率,从动轮B、C、D输出功率分别为,,轴的转速为。
试作轴的扭力图。
三、纯剪切
1、薄壁圆筒扭转时的切应力
扭转时,力学模型的建立及结果的探讨:
…………结合图示,给同学们讲清楚。
2、切应力互等定律
单元体如上图所示,根据平衡条件,单元体的上、下,左、右都应该存在应力,且有
表明:
在垂直的两个面上,切应力成对出现,大小相等,方向则共同指向或背离交线。
四、切应变剪切的胡克定律
1、切应变
2、剪切的胡克定律
扭转的实验表明:
切应力低于材料的剪切比例极限时,扭转角与扭转力偶矩m成正比。
对照拉伸和压缩的,有
第三节弯曲
弯曲的概念和内力
一、梁的概念
杆件上的外力垂直于杆件的轴线,使原为直线的轴线变形后为曲线,这种变行为弯曲变形,以弯曲变形为主的杆件,以弯曲变形为主的杆件称为梁。
绝大多数受弯曲杆件的横截面都有一根对称轴,它与整个杆件轴线形成整个杆件的纵向对称面。
当作用于梁上的所有外力都在纵向对称面内时,变形后的轴线也将是位于这个对称面内的一条曲线对称弯曲
二、梁的支座和载荷的简化
1、支座的基本形式
固定铰支座。
可动铰支座。
固定端支座
2、载荷的简化
l集中力:
在什么情况下可以简化为集中力?
均布载荷的长度相对于杆件的长度很小。
l均布力
3、静定梁
分类
静定梁:
梁的支座反力都可以由静力平衡方程确定。
四、剪力和弯矩
沿截面mm假想地把梁分成两个部分,并以左段为研究对象,如图所示。
Q称为横截面mm上的剪力。
它是与横截面相切的分布力系的合力。
M称为横截面mm上的弯矩。
它是与横截面垂直的分布力系的合力偶。
对于右段也可以使用同样的方法求出Q、M,而且左、右两部分求出的值是相等的。
例题1:
如右图所示,求跨度中点E和截面C上的弯矩和剪力。
解:
1、以整体为研究对象,受力分析如图所示,由于整个构件和受力均为对称,可知
2、以AC为研究对象,受力分析如图所示,有
3、以AE为研究对象,受力分析如图所示,有
例题2:
简支梁受力如图所示,试求1-1、2-2截面上的剪力和弯矩。
解:
1、由静平衡条件计算支座反力
其余计算此处从略。
第二章制药设备常用材料
一、金属材料
钢
钢的热处理:
为了改变钢材内部的组织结构,以满足对零件的加工性能和使用性能的要求所施加的一种综合的热加工工艺过程。
它包括三个环节:
1.加热到预定的温度(加热);
2.在预定的温度下适当保温(保温),保温的时间与工件的尺寸和性能有关;
3.以预定的冷却速度冷却(冷却)。
如:
橡胶机械中的挤出机和注射机中的螺杆等轴类零件的常用材料40Cr(中碳、低合金结构钢),为满足不同的加工和使用性能的要求,须进行不同的热处理:
热处理工艺曲线的示意图
1.炉冷珠光体(片)
先共析FHB207易切削的硬度,满足了切削加工的性能的要求。
2.空冷细片状P720~740MN/m2
先共析FHB250Jb:
72~74Kg/mm2
3.油冷粒状F和σb>100Kg/mm2ak>(6kg/cm2)60J/cm2
回火粒状Fe3C组成
强韧性好,从而能够满足这类零件的耐磨损、耐冲击、耐疲劳等性能的要求。
可见,通过热处理可以改变钢的组织和性能,充分发挥材料的潜力,调整材料的机械性能,满足机械零件在加工和使用过程中对性能的要求。
所以,在实际生产中凡是重要的零部件都必须经过适当的热处理。
下面介绍两个热处理中常见的概念:
热处理工艺:
热处理时的加热温度、保温时间和冷却速度等工序的总和称为热处理工艺。
热处理工艺曲线:
将热处理工艺参数标示在温度——时间坐标图上,得到的曲线即为热处理工艺曲线。
常见的热处理方法
根据热处理时加热和冷却方法的不同,常用的热处理方法大致分类如下:
退火
正火
普通热处理淬火
热处理回火
表面热处理表面淬火火焰加热表面淬火
感应加热表面淬火
化学热处理渗碳渗氮
碳氮共渗
钢的化学成分
碳:
当钢中的碳以固溶态存在时,C↑,D↑,晶粒粗化,当钢中的碳以碳化物形成存在时,有阻碍晶粒长大的作用。
对于钢中的合金元素,碳化物形成元素能阻碍晶粒长大,非碳化物形成元素有的阻碍晶粒长大如:
Cu、Si、Ni等;有的促进晶粒长大,如PMn。
实际生产中因加热温度不当,使奥氏体晶粒长大粗化的现象叫“过热”,过热后将使钢的性能恶化,因此控制奥氏体晶粒大小,是热处理和热加工制定加热温度时必须考虑的重要问题。
冷处理:
对高碳钢或高碳合金钢,为了减少其淬火后残余奥氏体的量,常对其进行“冷处理”。
所谓的冷处理即淬火至室温后,立即将钢件放入干冰酒精等深冷剂中继续冷却到零下温度,使残余奥氏体继续转变为马氏体。
钢的普通热处理
普通热处理是将工件整体进行加热、保温和冷却,以使其获得均匀的组织和性能的一种操作。
它包括退火、正火、淬火和回火。
【钢的退火与正火】
实际生产中,各种工件在制造过程中有不同的工艺路线,如:
铸造(或锻造)→退火(正火)→切削加工→成品;或铸造(或锻造)→退火(正火)→粗加工→淬火→回火→精加工→成品。
可见,退火与正火是应用非常广泛的热处理。
为什么将其安排在铸造成锻造之后,切削加工之前呢?
原因如下:
①在铸造或锻造之后,钢件中不但残留有铸造或锻造应力,而且还往往存在着成分和组织上的不均匀性,因而机械性能较低,还会导致以后淬火时的变形和开裂。
经过退火和正火后,便可得到细而均匀的组织,并消除应力,改善钢件的机械性能并为随后的淬火作了准备。
②铸造或锻造后,钢件硬度经常偏高或偏低,严重影响切削加工。
经过退火与正火后,钢的组织接近于平衡组织,其硬度适中,有利于下一步的切削加工。
③如果工件的性能要求不高时,如铸件、锻件或焊接件等,退火或正火常作为最终热处理。
1.钢的退火
退火是将工件加热到临界点以上或在临界点以下某一温度保温一定时间后,以十分缓慢的冷却速度(炉冷、坑冷、灰冷)进行冷却的一种操作。
根据钢的成分、组织状态和退火目的不同,退火工艺可分为:
完全退火、等温退火、球化退火、去应力退火等。
(1)完全退火和等温退火
用于亚共析钢成分的碳钢和合金钢的铸件、锻件及热轧型材。
有时也用于焊接结构。
目的:
细化晶粒,降低硬度,改善切削加工性能。
(2)球化退火
主要用于共析或过共析成分的碳钢及合金钢。
目的:
在于降低硬度,改善切削加工性,并为以后淬火做准备。
实质:
通过球化退火,使层状渗碳体和网状渗碳体变为球状渗碳体,球化退火后的组织是由铁素体和球状渗碳体组成的球状珠光体。
(3)去应力退火(低温退火)
主要用于消除铸件、锻件、焊接件、冷冲压件(或冷拔件)及机加工的残余内应力。
这些应力若不消除会导致随后的切削加工或使用中的变形开裂。
降低机器的精度,甚至会发生事故。
2.钢的正火:
正火:
将工件加热到Ac3或Accm以上30~80℃,保温后从炉中取出在空气中冷却。
与退火的区别是冷速快,组织细,强度和硬度有所提高。
当钢件尺寸较小时,正火后组织:
S,而退火后组织:
P。
钢的退火与正火工艺参数见图5-15。
正火的应用:
(1)用于普通结构零件,作为最终热处理,细化晶粒提高机械性能。
(2)用于低、中碳钢作为预先热处理,得合适的硬度便于切削加工。
(3)用于过共析钢,消除网状Fe3CⅡ,有利于球化退火的进行。
3.退火和正火的选择
从前面的学习中知,退火与正火在某种程度上有相似之处,在实际生产中又可替代,那么,在设计时根据什么原则进行选择呢?
从以下三方面予以考虑:
(1)从切削加工性上考虑
切削加工性又包括硬度,切削脆性,表面粗糙度及对刀具的磨损等。
一般金属的硬度在HB170~230范围内,切削性能较好。
高于它过硬,难以加工,且刀具磨损快;过低则切屑不易断,造成刀具发热和磨损,加工后的零件表面粗糙度很大。
对于低、中碳结构钢以正火作为预先热处理比较合适,高碳结构钢和工具钢则以退火为宜。
至于合金钢,由于合金元素的加入,使钢的硬度有所提高,故中碳以上的合金钢一般都采用退火以改善切削性。
(2)从使用性能上考虑
如工件性能要求不太高,随后不再进行淬火和回火,那么往往用正火来提高其机械性能,但若零件的形状比较复杂,正火的冷却速度有形成裂纹的危险,应采用退火。
(3)从经济上考虑
正火比退火的生产周期短,耗能少,且操作简便,故在可能的条件下,应优先考虑以正火代替退火。
【钢的淬火】
淬火的目的
淬火就是将钢件加热到Ac3或Ac1以上30~50℃,保温一定时间,然后快速冷却(一般为油冷或水冷),从而得马氏体的一种操作。
因此淬火的目的就是获得马氏体。
但淬火必须和回火相配合,否则淬火后得到了高硬度,高强度,但韧性,塑性低,不能得到优良的综合机械性能。
淬火方法
为了使工件淬火成马氏体并防止变形和开裂,单纯依靠选择淬火介质是不行的,还必须采取正确的淬火方法。
最常用的淬火方法有如下四种:
①单液淬火法
将加热的工件放入一种淬火介质中一直冷到室温。
这种方法操作简单,容易实现机械化,自动化,如碳钢在水中淬火,合金钢在油中淬火。
但其缺点是不符合理想淬火冷却速度的要求,水淬容易产生变形和裂纹,油淬容易产生硬度不足或硬度不均匀等现象。
②双液淬火法
将加热的工件先在快速冷却的介质中冷却到300℃左右,立即转入另一种缓慢冷却的介质中冷却至室温,以降低马氏体转变时的应力,防止变形开裂。
如形状复杂的碳钢工件常采用水淬油冷的方法,即先在水中冷却到300℃后在油中冷却;而合金钢则采用油淬空冷,即先在油中冷却后在空气中冷却。
③分级淬火法
将加热的工件先放入温度稍高于Ms的硝盐浴或碱浴中,保温2~5min,使零件内外的温度均匀后,立即取出在空气中冷却。
这种方法可以减少工件内外的温差和减慢马氏体转变时的冷却速度,从而有效地减少内应力,防止产生变形和开裂。
但由于硝盐浴或碱浴的冷却能力低,只能适用于零件尺寸较小,要求变形小,尺寸精度高的工件,如模具、刀具等。
④等温淬火法
将加热的工件放入温度稍高于Ms的硝盐浴或碱浴中,保温足够长的时间使其完成B转变。
等温淬火后获得B下组织。
钢的淬透性:
(1)淬透性的概念
所谓淬透性是指钢在淬火时获得淬硬层的能力。
淬硬层一般规定为工件表面至半马氏体(马氏体量占50%)之间的区域,它的深度叫淬硬层深度。
不同的钢在同样的条件下淬硬层深度不同,说明不同的钢淬透性不同,淬硬层较深的钢淬透性较好。
淬硬性:
是指钢以大于临界冷却速度冷却时,获得的马氏体组织所能达到的最高硬度。
钢的淬硬性主要决定于马氏体的含碳量,即取决于淬火前奥氏体的含碳量。
(2)影响淬透性的因素
①化学成分
C曲线距纵坐标愈远,淬火的临界冷却速度愈小,则钢的淬透性愈好。
对于碳钢,钢中含碳量愈接近共析成分,其C曲线愈靠右,临界冷却速度愈小,则淬透性愈好,即亚共析钢的淬透性随含碳量增加而增大,过共析钢的淬透性随含碳量增加而减小。
除Co和Al(>2.5%)以外的大多数合金元素都使C曲线右移,使钢的淬透性增加,因此合金钢的淬透性比碳钢好。
②奥氏体化温度
温度愈高,晶粒愈粗,未溶第二相愈少,淬透性愈好。
因为奥氏体晶粒粗大使晶界减少,不利珠光体的形核,从而避免淬火时发生珠光体转变。
【钢的回火】
回火是将淬火钢重新加热到A1点以下的某一温度,保温一定时间后,冷却到室温的一种操作。
由于淬火钢硬度高,脆性大,存在着淬火内应力,且淬火后的组织M和A’都处于非平衡态,是一种不稳定的组织,在一定条件下,经过一定的时间后,组织会向平衡组织转变,导致工件的尺寸形状改变,性能发生变化,为克服淬火组织的这些弱点而采取回火处理。
回火的目的:
降低淬火钢的脆性,减少或消除内应力,使组织趋于稳定并获得所需要的性能。
回火的方法及应用
钢的回火按回火温度范围可分为以下三种:
(1)低温回火
回火温度范围150~250℃。
得到的组织:
回火马氏体。
内应力和脆性降低,保持了高硬度和高耐磨性。
这种回火主要应用于高碳钢或高碳合金钢制造的工、模具、滚动轴承及渗碳和表面淬火的零件,回火后的硬度一般为HRC58-64。
(2)中温回火
回火温度范围为350~500℃,回火后的组织为回火屈氏体,硬度HRC35-45,具有一定的韧性和高的弹性极限及屈服极限。
这种回火主要应用于含碳0.5-0.7%的碳钢和合金钢制造的各类弹簧。
(3)高温回火
回火温度范围为500~650℃,回火后的组织为回火索氏体,其硬度HRC25-35,具有适当的强度和足够的塑性和韧性。
这种回火主要应用于含碳0.3-0.5%的碳钢和合金钢制造的各类连接和传动的结构零件,如轴、连杆、螺栓等。
通常在生产上将淬火加高温回火的处理称为“调质处理”。
对于在交变载荷下工作的重要零件,要求其整个截面得到均匀的回火索氏体组织,首先必须使零件淬透,因此,随着调质零件尺寸不同,要求钢的淬透性也不同,大零件要求选用高淬透性的钢,小零件则可以选用淬透性较低的钢。
钢的表面热处理
一些在弯曲、扭转、冲击载荷、磨擦条件区工作的齿轮等机器零件,它们要求具有表面硬、耐磨,而心部韧,能抗冲击的特性,仅从选材方面去考虑是很难达到此要求的。
如用高碳钢,虽然硬度高,但心部韧性不足,若用低碳钢,虽然心部韧性好,但表面硬度低,不耐磨,所以工业上广泛采用表面热处理来满足上述要求。
【钢的表面淬火】
表面淬火是将工件的表面层淬硬到一定深度,而心部仍保持未淬火状态的一种局部淬火法。
它是利用快速加热使钢件表面奥氏体化,而中心尚处于较低温度即迅速予以冷却,表层被淬硬为马氏体,而中心仍保持原来的退火、正火或调质状态的组织。
表面淬火一般适用于中碳钢(0.4~0.5%C)和中碳低合金钢(40Cr、40MnB等),也可用于高碳工具钢,低合金工具钢(如T8、9Mn2V、GCr15等)。
以及球墨铸铁等。
目前应用最多的是感应加热和火焰加热表面淬火。
【钢的化学热处理】
化学热处理是将工件置于活性介质中加热和保温,使介质中活性原子渗入工件表层,以改变其表面层的化学成分、组织结构和性能的热处理工艺。
根据渗入元素的类别,化学热处理可分为渗碳、氮化、碳氮共渗等。
化学热处理的主要目的:
除提高钢件表面硬度,耐磨性以及疲劳极限外,也用于提高零件的抗腐蚀性、抗氧化性,以代替昂贵的合金钢。
化学热处理的一般过程:
任何化学热处理方法的物理化学过程基本相同,都要经过分解、吸收和扩散三个过程。
(1)介质分解:
分解出活性的[N][C]原子
(2)吸收:
活性原子被工件表面吸收、先固溶于基体金属,当超过固溶度后,使可能形成化合物。
(3)原子向内扩散:
形成具有一定厚度的渗层。
1.钢的渗碳
将工件放在渗碳性介质中,使其表面层渗入碳原子的一种化学热处理工艺称为渗碳。
渗碳钢都是含0.15~0.25%的低碳钢和低碳合金钢,如20、20Cr、20CrMnTi、20SiMnVB等。
渗碳层深度一般都在0.5~2.5mm。
钢渗碳后表面层的含碳量可达到0.8~1.1%C范围。
渗碳件渗碳后缓冷到室温的组织接近于铁碳相图所反映的平衡组织,从表层到心部依次是过共析组织,共析组织,亚共析过渡层,心部原始组织。
渗碳主要用于表面受严重磨损,并在较大的冲击载荷下工作的零件(受较大接触应力)如齿轮、轴类、套角等。
渗碳方法有气体渗碳、液体渗碳、固体渗碳,目前常用的就是气体渗碳。
(1)气体渗碳
将工件放在900~950℃,密封的渗碳炉中,向炉内滴入易分解的有机液体(如媒油、丙酮、甲醇等)或直接通入渗碳总体(如煤气、石油液化气等),经裂解后得到含H2、CO和CH4的渗碳气体与钢中表面接触后产生活性原子[C]。
发生的反应:
产生的活性碳原子溶入钢中,使工件表面渗碳。
气体渗碳的设备见P92-图3-45。
气体渗碳的优点是生产率高,劳动条件较好,渗碳气氛易控制,渗碳层均匀,易实现机械化和自动化。
(2)固体渗碳
将工件埋入填满固体渗碳剂的渗碳箱中,用盖和耐火封泥密封后,放入900~950℃加热炉中保温一定时间后,得到一定厚度的渗碳层。
固体渗碳的优点是设备简单,适应性大,在单件、小批量生产的情况下,具有一定的优越性,但劳动效率低,生产条件差,质量不易控制。
不论是气体渗碳还是固体渗碳,渗碳后的零件都要进行淬火和低温回火处理,才能达到所要求的使用性能。
2.钢的氮化
向钢件表面渗入氮,形成含氮硬化层的化学热处理过程称为氮化。
氮化实质就是利用含氮的物质分解产生活性[N]原子,渗入工件的表层。
应用较广泛的是气体氮化法,即把工件放入密封箱式(或中式)炉内加热(温度500~580℃),并通入氨气,使其分解:
分解出的活性氮原子被工件表面吸收,通过扩散传质,得到一定深度的渗氮层。
N位于铁素体形成含氮铁素体(即α相),当含氮量超过饱和溶解度时,就会形成γ’(Fe4N)和ε(Fe2N)两种氮化物。
此外,N还可与钢中合金元素Cr、Mo、Al形成CrN、MoN、AlN氮化物,这些氮化物具有高硬度,高耐磨度,高的耐蚀性。
氮化缓冷后渗层组织从表面到心部按Fe-N相图依次是ε→→γ’→→心部原始组织。
氮化用钢通常是含Al、Cr、Mo等合金元素的钢,如38CrMoAlA是一种比较典型的氮化钢,此外还有35CrMo、18CrNiW等也经常作为氮化钢。
合金元素Al、Cr、Mo、V、Ti极易与氮元素形成颗粒细密,分布均匀,硬度高且稳定的各种氮化物如AlN、CrN、MoN、TiN、VN等,这些氮化物的存在对氮化钢的性能起着主要的作用。
与渗碳相比、氮化工件具有以下特点:
1)氮化前需经调质处理,以便使心部组织具有较高的强度和韧性。
2)表面硬度可达HRC65~72,具有较高的耐磨性。
3)氮化表面形成致密氮化物组成的连续薄膜,具有一定的耐腐蚀性。
4)氮化处理温度低,渗氮后不需再进行其它热处理。
氮化处理适用于耐磨性和精度都要求较高的零件或要求抗热、抗蚀的耐磨件。
如:
发动机的汽缸、排气阀、高精度传动齿轮等。
3.碳氮共渗
碳氮共渗是向钢的表面同时渗入碳和氮的过程。
习惯上又称氮化,目前以中温气体碳氮共渗和低温气体碳氮共渗(即气体软氧化)应用较为广泛。
中温气体碳氮共渗的主要目的是提高钢的硬度、耐磨性和疲劳强度。
低温气体碳氮共渗以渗氮为主,其主要目的是提高钢的耐磨性和抗咬合性。
【钢的