滚齿刀使用事项及对称.docx
《滚齿刀使用事项及对称.docx》由会员分享,可在线阅读,更多相关《滚齿刀使用事项及对称.docx(16页珍藏版)》请在冰豆网上搜索。
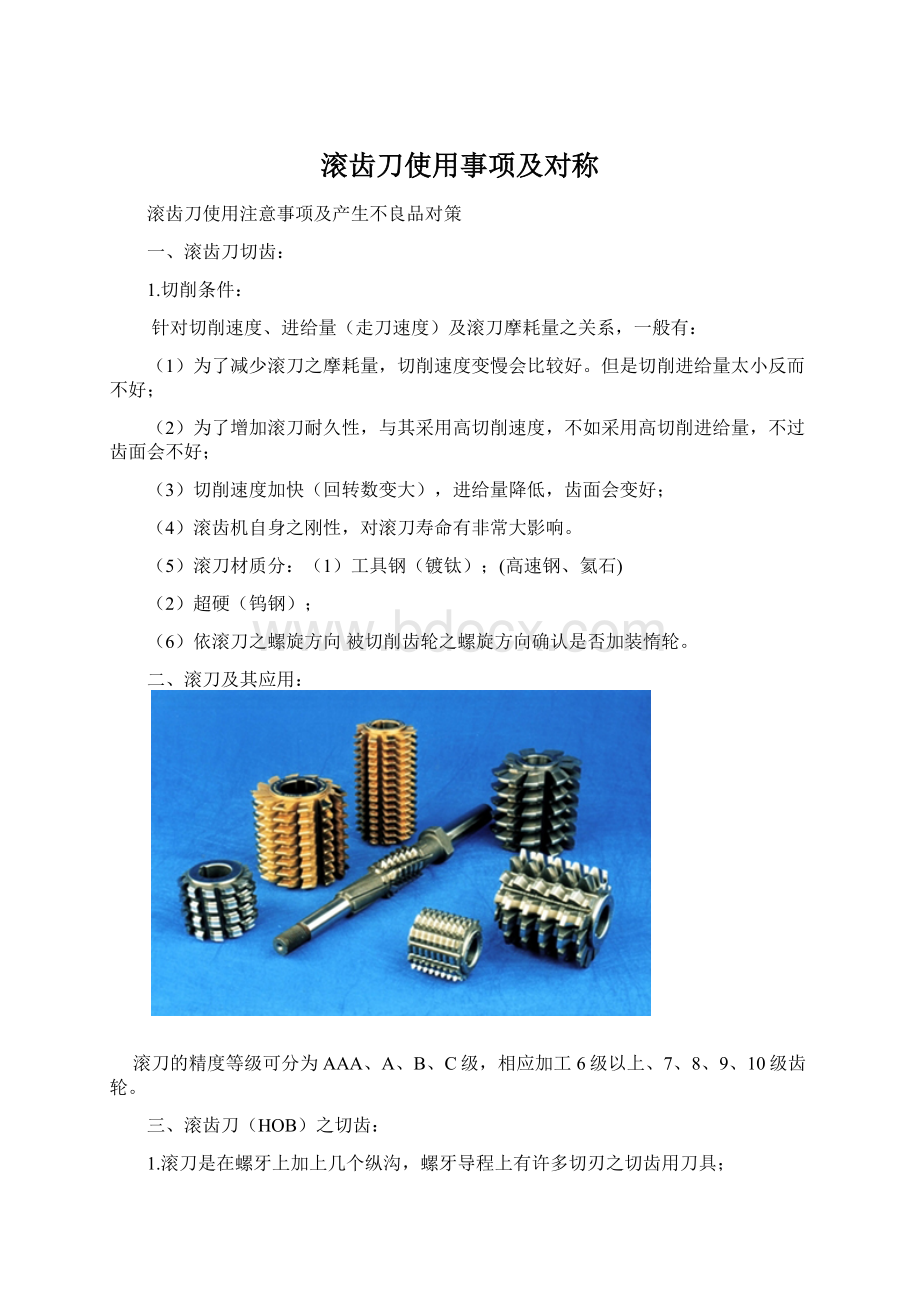
滚齿刀使用事项及对称
滚齿刀使用注意事项及产生不良品对策
一、滚齿刀切齿:
1.切削条件:
针对切削速度、进给量(走刀速度)及滚刀摩耗量之关系,一般有:
(1)为了减少滚刀之摩耗量,切削速度变慢会比较好。
但是切削进给量太小反而不好;
(2)为了增加滚刀耐久性,与其采用高切削速度,不如采用高切削进给量,不过齿面会不好;
(3)切削速度加快(回转数变大),进给量降低,齿面会变好;
(4)滚齿机自身之刚性,对滚刀寿命有非常大影响。
(5)滚刀材质分:
(1)工具钢(镀钛);(高速钢、氦石)
(2)超硬(钨钢);
(6)依滚刀之螺旋方向被切削齿轮之螺旋方向确认是否加装惰轮。
二、滚刀及其应用:
滚刀的精度等级可分为AAA、A、B、C级,相应加工6级以上、7、8、9、10级齿轮。
三、滚齿刀(HOB)之切齿:
1.滚刀是在螺牙上加上几个纵沟,螺牙导程上有许多切刃之切齿用刀具;
(1)一体型滚齿刀(本厂用之滚齿刀)
(2)组合型滚齿刀
2.滚刀和工件之关系:
(滚齿过程、成形方法)。
滚刀装设时,刀刃导程会对准齿轮之齿筋方向,此时滚刀之刀刃导程相当于假想之齿条,在渐开线齿轮场合,齿条刀刃形状是直线,滚刀只要有回转,接二连三的刀刃往工件里切入,切出齿。
因为刀刃是沿着螺纹分布,随着回转而切入之刀刃往左边移动,工件也配合此动作往左边移动。
只要回转齿轮工件就会从齿顶部逐渐往齿部切出齿形。
1条(单口,本厂均是)滚刀之场合,滚刀1回转,相当于假想齿条前进一个节距。
齿轮工件也只需运转1个节距即可。
即要切削Z齿数齿轮时,相对于齿轮工件之1回转、滚刀必须有Z回转才可。
四、滚刀精度误差对其生产中之影响:
1.因滚刀再研磨引起之齿形误差
(1)滚刀分割误差:
有分割误差发生时会反应在齿形误差上,影响非常大,压力角20º之滚刀在外周有0.1mm之分割误差时,会造成6um之齿形误差。
(2)倾斜角误差:
滚刀倾斜角误差会变成齿轮之压力角误差,滚刀之倾斜角误差1º时,压力角误差约为3´,并非大影响。
(3)切刃面之误差:
滚刀之切刃面并非直线,而是凹凸时,会造成齿形误差。
(4)刃沟之螺旋误差:
通常滚刀轴心和切刃沟是平行的,如果有此误差,会产生左右齿面非对称之压力角误差,1º约为10´之误差。
2.因滚刀之偏摆而造成之齿形误差。
(5)滚刀如果有偏摆,齿轮会产生很大弯曲误差,偏摆量0.03mm、压力角20º时的齿形误差约10um(该误差非常大)。
(6)滚刀偏心有下列现象:
a)切刃及孔之偏心(滚刀制作时产生)
b)滚刀装设时之偏心。
Ø滚刀孔和滚刀轴有间隙;
Ø滚刀之螺帽上紧时之偏心:
螺帽、垫片、滚刀端面的平行度不良;切削时铁渣附着等造成滚刀轴弯曲,或不当上太紧造成滚刀轴弯曲;
(2)滚刀轴本身之偏心。
3.因滚刀之切刃沟引起多角形误差:
(7)多角形误差,可因切刃沟数多而变小;
(8)滚刀之条数愈多,误差愈大;
(9)齿数无法被滚刀条数整除时,误差变小;
(10)齿数可以被滚刀条数整除时,误差变大。
4.其它齿形误差原因:
(1)滚刀压力角误差,直接成为齿轮压力角误差;
(2)滚刀节距同样伸缩状态时会产生压力角误差;
(3)滚刀齿筋误差,会造成齿轮齿形误差。
以上均存在于滚刀制作精度。
(4)如果使用滚刀两端,就可能发生创成不完全而产生齿形误差;
(5)齿面出棱—修刀不等分;
(6)齿形不对称—滚刀安装不对中;
(7)齿形角误差—修刀不通过;
(8)齿形周期误差—安装刀具后径向、轴向跳动大;
(9)节距误差、累积节距误差—滚刀主轴轴向窜动大,滚刀径向跳动大(刀具精度不够);
(10)滚刀重新研磨后,请用黄铜刷子将切刃之棱线除去。
五、滚刀的选用:
可根据加工零件的精度要求来选用滚刀,通常加工5级精度(GB)的齿轮应采用“AAA”级的滚刀,加工6-7级精度的齿轮采用“AA”级的滚刀,加工8-9级精度的齿轮可采用“A”级或普通级的滚刀。
六、滚刀安装:
滚刀安装应根据压力角、模数、精度以及刀杆直径选择相应的滚刀,滚刀在刀杆安装夹紧后,应使用百分表,检查滚刀上两个凸台的径向跳动(有些滚刀只有一个凸台),两凸台的跳动方向和数值应尽可能一致,以避免滚滚刀安装的偏斜。
根据加工零件的不同精度等级,滚刀安装允许的径向跳动值为:
(依GB精度)
1.滚切5级精度齿轮,A、B处允许的径向跳动值为0.005-0.007mm;
2.滚切6级精度齿轮,A、B处允许的径向跳动值为0.007-0.009mm;
3.滚切7级精度齿轮,A、B处允许的径向跳动值为0.01mm。
当滚刀径向跳动超过允许值不大时,可以松开滚刀紧固螺冒,转动滚刀或垫圈,再重新夹紧进行检查。
反复多次直至到达滚刀的安装精度要求。
六、刀具使用上研磨后误差(精度):
刀具使用上的注意(再研磨、装取)
误
差
的
种
类
沟的分割误差
向心度误差
刀刃面的真直度误差
装设的震动
被
切
削
齿
轮
的
实
际
误
差
概
算
误
差
量
分割误差0.1mm以
齿形误差约6μmm
向心度误差1°以
压力角误差约3′
刀刃面的真直度误差
0.1mm以
齿形误差约6μmm
装取的震动
0.01mm以
齿形误差约3.5μmm
公法线齿厚容许差及齿顶圆直径容许差的关系
δda=δW/sinaδW=δda*sina
δW:
公法线齿厚容许差δda:
齿顶圆直径容许差
a=20°时(单位:
mm)
公法线齿厚公差
0.01
0.02
0.03
0.04
0.05
0.06
0.07
齿顶圆直径公差
0.029
0.058
0.088
0.117
0.146
0.175
0.205
0.08
0.09
0.10
0.20
0.30
0.40
0.50
0.234
0.263
0.292
0.585
0.877
1.170
1.462
1.新滚刀切出的正确的渐形线齿形
2.滚刀重磨后切出的齿形
图1
阿基米德滚刀
关于切削
一、切削方法:
1.滚刀进给(移位)方向:
(1)面向主轴(夹头);
(2)面向尾座(顶针)。
2.滚刀回转方向:
(1)上切(UPCUT)(逆铣):
切削时振动小,切削平稳,当机床走刀机构存在间隙时,刀齿也不会断裂或崩刀,但刀具易磨钝;刀齿切出时毛刺较大。
(2)下切(DOWNCUT)(顺铣)
刀具寿命长,消耗功率小,但机床的走刀机构必须要有消除走刀丝杆与螺母间隙的装置,否则易使滚刀产生断裂或崩刃,同时要求机床的刚性较高。
3.切削方法选定:
(1)标准切削方法,上切(普通);
(2)切削抵抗大造成主轴侧负担大,采用面向主轴下切或面向尾座上切;
(3)上切比下切更能获得较好的精度;
(4)下切比上切更能获得好齿面;
(5)必须考虑毛边(披锋)出现的方向。
(6)通常滚切直齿时推荐采用逆铣的方法加工;滚切斜齿轮时可根据需要进行选择,也常采用逆铣的方法;
二、工件装设要点及对精度的影响:
1.偏心误差:
工件装设时偏摆或弯曲会造成偏心误差。
2.齿筋误差:
(1)工件弯曲装设时会造成齿筋误差;
(2)工件没有确实装设在主轴和尾座顶心间时会造成斜坡及齿筋误差。
三、选定切削用量:
1滚刀进给量
1)欧洲工具厂的推荐值
德国saacke,Fette和sazzor齿轮滚刀厂均推荐以齿轮滚刀顶刃的最大许可切屑厚度(h1max)来确定滚刀进给量。
a.硬质合金滚刀的h1max规定按国际标准(ISO)对硬质合金的分类:
P类硬质合金滚刀h1max为0.18mm;K类硬质合金滚刀h1max为0.12~0.15mm。
P类硬质合金常用牌号为P25~P40。
这类整体硬质合金滚刀在新刀时要进行TiN表面涂层处理,但刃磨后一般不再进行涂层。
K类硬质合金滚刀常用于对淬硬钢齿轮的齿形精加工,牌号多为K10,对较小模数的滚刀要用细颗粒硬质合金。
在精滚齿时,新刀及每次刃磨后均进行TiN涂层处理。
轿车方向盘转向器上的小齿轮淬硬后采用硬质合金滚刀精滚工艺。
b.高速钢滚刀的h1max规定对中小模数的轿车齿轮(m=1.4~2.8mm),一般选用h1max为0.2~0.25mm。
对模数大的齿轮,可选用较大值为0.25~0.3mm。
上述欧洲工具厂的高速钢滚刀材料常用含钴5%的钴高速钢S6-5-2-5(S后的数字依次为钨-钼-钒-钴的百分数),淬火硬度为65~66HRC。
2)美国star工具厂的推荐值
美国star工具厂是美国主要的齿轮滚刀生产厂之一。
该厂也是推荐滚刀顶刃的最大许可切屑厚度h1max来确定滚刀进给量。
a.对于P类硬质合金滚刀的h1max规定为0.15mm。
b.对高速钢滚刀的h1max规定为0.2~0.25mm。
该厂与德国Liebherr滚齿机厂交换过意见,两厂分别导出的滚齿切屑最大厚度公式,得到的h1max值很相近。
2滚刀顶刃的h1max与滚刀轴向进给量fa的关系
根据滚刀顶刃最大切屑厚度h1max值换算成滚刀轴向进给量fa值才能在滚削加工中应用。
德国人Dr.B.Hoffmeister博士于1979年在阿亨大学发表的论文中研究了滚齿中的顶刃最大切屑厚度,并建立了计算用数学公式,用它可以从顶刃切屑厚度计算工件每转的轴向进给量。
此公式在顶刃切屑厚度h1max=0.35mm对m=1的滚刀和h1max=0.1mm对m=32的滚刀皆得到验证。
德国的滚刀厂皆用Hoffmeister博士的公式从h1max值计算fa值。
计算式为fa=Fh1·Fm·Fz2·Fd·F(N/z0)·Fa
(1)式中,
Fh1、Fm、Fz2、Fd、F(N/z0)、Fa为6个影响因子,各有其计算式。
由于各因子的计算方程式较为复杂,考虑工业应用,近年有人将其简化列于表1。
表1fa的各影响因子计算方程式(简化式)
影响因子名称计算方程式顶刃切屑厚度h1因子Fh1Fh1=h1max1.9569齿轮法向模数m因子FmFm=0.0446m-0.7730齿轮齿数z2因子Fz2对z2≤120Fz2=z21.0607滚刀外径d(mm)因子FdFd=(d/2)1.6145×10-2×0.4403
Fd=(d/2)0.4403(=0°)滚刀刃齿数N和滚刀头数z0因子FN/z0F(N/z0)=(N/z0)1.7162滚刀切入深度a(mm)和齿轮齿形位移修正系数p因子FaFa=a-0.6243
p影响极微,皆以p=0计算表1中h1max——滚刀顶刃的最大切屑厚度,mm
fa——滚刀轴向进给量/工件每转,mm/r
——齿轮分圆螺旋角,公式中为弧度值(以度数为单位的角,要乘/180)
3h1max或fa的选取
滚削实例的原始数据及按公式
(1)计算所得的fa或h1max均列于表2,说明如下。
1)表2中1号滚刀
这是德国saacke厂在1997年国际展览会上作为新产品宣传的TiALN涂层硬质合金整体滚刀加长结构。
Ø60(D)mm×150(刃长)mmר27(孔)mm,体现了小直径,加长,多刃齿,多头的现代滚刀,它代表了现代硬质合金滚刀滚齿的最高水平。
用来加工20MnCrS5含硫易切渗碳钢齿轮(含硫0.03%),滚齿速度Vc=395m/min(2095r/min),采用fa=1.8mm/r(188mm/min),用公式
(1)计算,可得h1max=0.14mm,此值与该厂推荐的不超过0.18mm最大许可切屑厚度相符。
刀具寿命为32m/刃齿,全刀可加工