《齿轮泵设计说明书》.docx
《《齿轮泵设计说明书》.docx》由会员分享,可在线阅读,更多相关《《齿轮泵设计说明书》.docx(27页珍藏版)》请在冰豆网上搜索。
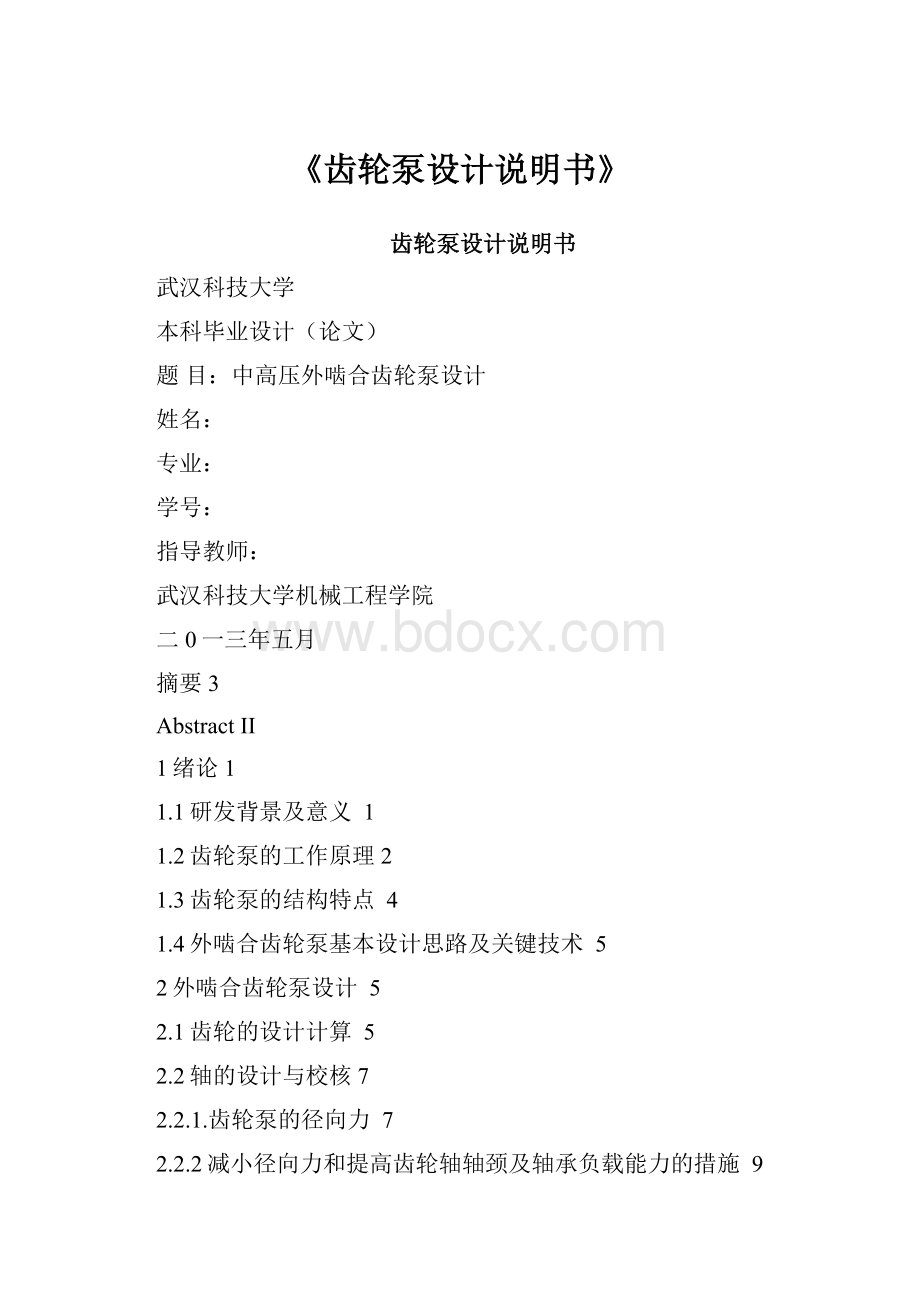
《齿轮泵设计说明书》
齿轮泵设计说明书
武汉科技大学
本科毕业设计(论文)
题目:
中高压外啮合齿轮泵设计
姓名:
专业:
学号:
指导教师:
武汉科技大学机械工程学院
二0一三年五月
摘要3
AbstractII
1绪论1
1.1研发背景及意义1
1.2齿轮泵的工作原理2
1.3齿轮泵的结构特点4
1.4外啮合齿轮泵基本设计思路及关键技术5
2外啮合齿轮泵设计5
2.1齿轮的设计计算5
2.2轴的设计与校核7
2.2.1.齿轮泵的径向力7
2.2.2减小径向力和提高齿轮轴轴颈及轴承负载能力的措施9
2.2.3轴的设计与校核10
2.3卸荷槽尺寸设计计算13
2.3.1困油现象的产生及危害13
2.3.2消除困油危害的方法15
2.3.3卸荷槽尺寸计算19
2.4进、出油口尺寸设计20
2.5选轴承20
2.6键的选择与校核21
2.7连接螺栓的选择与校核21
2.8泵体壁厚的选择与校核22
总结23
致谢24
参考文献26
摘要
外啮合齿轮泵是一种常见的液压泵,它靠一对齿轮的进入和脱离啮合完成吸油和压油,且均存在泄漏现象、困油现象以及噪声和振动。
减小外啮合齿轮泵的径向力是研究外啮合齿轮泵的一大课题,为减小径向力中高压外啮合齿轮泵多采用的是变位齿轮,而且对轴和轴承的要求较高。
为解决泄漏问题,低压外啮合齿轮泵可采用提高加工精度等方法解决,而对于中高压外啮合齿轮泵则需要采取加浮动轴套或弹性侧板的方法解决。
困油现象引起齿轮泵强烈的振动和噪声还大大所短外啮合齿轮泵的使用寿命,解决困油问题的方法是开卸荷槽。
关键词:
外啮合齿轮泵,变位齿轮,浮动轴套,困油现象,卸荷槽
(此毕业设计获得优秀毕业设计荣誉,共有5张零件图,1张装配图,而且有开题报告、外文翻译、答辩稿,答辩ppt,保证让你的毕业设计顺利过关!
先找份好的工作,不再为毕业设计而发愁!
!
!
有需要零件
图和装配图的同学请联系QQ:
)
Abstract
Theexternalgearpumpisacommonlyusedhydraulicpumps,whichrelyonapairofmeshinggearsintoandoutofoilandoilpressuretocomplete,andthereareleakage,thephenomenonoftrappedoilandnoiseandvibration.Reducetheexternalgearpumpoftheradialforceistheexternalgearpumpisamajorissue,inordertoreducetheradialforcemorepressureexternalgearpumpusesavariablegearandtheshaftandbearingsarehigher.Tosolvetheleakageproblem,lowpressuregearpumpandothermethodscanbeusedtosolvehigherprecision,whileforthehigh-pressureexternalgearpumpsareneededtoincreasethefloatingsleeveorelasticsidepanelsofthesolutions.Phenomenoncausedbytrappedoilgearpumpisalsoastrongvibrationandnoiseareconsiderablyshorterservicelifeofexternalgearpumptosolvetheoilproblemistrappedunloadingopeningslot.
Keywords:
externalgearpump,variablegear,floatingshaft,trappingphenomenon,unloadingtank
1绪论
1.1研发背景及意义
齿轮泵是在工业应用中运用极其广泛的重要装置之一,特别是在液压传动与控制技术中占有很大的比重,它具有结构简单、体积小、重量轻、白吸性能好、耐污染、使用可靠、寿命较长、制造容易、维修方便、价格便宜等特点〔L一”。
但同时齿轮泵也还存在一些不足,如困油现象比较严重、流量和压力脉动较大、径向力不平衡、泄漏大、噪声高及易产生气穴等缺点,这些特性和缺点都直接影响着齿轮泵的质量。
随着齿轮泵在高温、高压、大排量、低流量脉动、低噪音等方面发展及应用,对齿轮泵的特性研究及提高齿轮泵的安全和效率已成为国内外深入研究的课题。
外啮合齿轮泵是应用最广泛的一种齿轮泵(称为普通齿轮泵),其设
计及生产技术水平也最成熟。
多采用三片式结构、浮动轴套轴向间隙白动补偿措施,并采用平槽以减小齿轮(轴承)的径向不平衡力。
当前,这种齿轮泵的额定压力可达25MPa。
可是,由于这种齿轮泵的齿数较
少,导致其流量脉动较大由于齿轮泵在液压传动系统中应用广泛,因此,吸引了大量学者对其进行研究。
当前,国内外学者关于齿轮泵的研究主要集中在以下方面:
齿轮参数及泵体结构的优化设计;齿轮泵间隙优化及补偿技术;困油冲击及卸荷措施;齿轮泵流量品质研究;齿轮泵的噪声控制技术;轮齿表面涂覆技术;齿轮泵的变量方法研究;齿轮泵
文档仅供参考
的寿命及其影响因素研究;齿轮泵液压力分析及其高压化的途径;水介质齿轮泵基础理论研究。
综上所知,对齿轮泵的白主研发和设计对中国尤为重要。
特别是在提高其效力和降低噪音和振动方面。
随着社会的发展,齿轮泵更广泛的被应用于各种工业,工业白动化程度越来越高,需要达到的精度也越高,市场竞争越来越激烈。
这就要求齿轮泵的设计制造在秉承了原有的先进技术之外,要不断攻克新的技术难点。
此次研究在达到课题给出的条件要求之外力争改进外啮合齿轮泵的如下难点:
(1)高压化;
(2)低流量脉动;(3)低噪声;(4)大排量;(5)变排量,为社会工业发展提供性能更强、更稳定的外啮合齿轮泵。
本论文针对如何降低外啮合齿轮泵的输出流量脉动和噪声并力求在保持外啮合齿轮泵的结构和工艺在各类液压泵中最简单,在价格、可靠性、寿命、抗污染和白吸能力强的优势上开展了对齿轮泵的工作机理分析与研究。
本论文在对外啮合齿轮泵工作原理和流量脉动机理分析的基础上,为外啮合齿轮泵的结构设计奠定基础。
在此基础上进行了外啮合
齿轮泵的结构设计,经过建立外啮合齿轮泵齿轮的优化数学模型,优化计算出使输出流量脉动最小的齿轮参数。
这对于促进机械装备的技术进步、降低机械装备的制造成本具有十分重要的意义,其应用前景将十分广阔.
1.2齿轮泵的工作原理
外啮合齿轮泵的工作原理图如图1.2所示:
图1-2齿轮泵工作原理图
由图可见,这种泵的壳体内装有一对外啮合齿轮。
由于齿轮端面与
壳体端盖之间的缝隙很小,齿轮齿顶与壳体内表面的间隙也很小,因此
能够看成将齿轮泵壳体内分隔成左、右两个密封容腔。
当齿轮按图示方
向旋转时,右侧的齿轮逐渐脱离啮合,露出齿间。
因此这一侧的密封容腔的体积逐渐增大,形成局部真空,油箱中的油液在大气压力的作用下经泵的吸油口进入这个腔体,因此这个容腔称为吸油腔。
随着齿轮的转动,每个齿间中的油液从右侧被带到了左侧。
在左侧的密封容腔中,轮
齿逐渐进入啮合,使左侧密封容腔的体积逐渐减小,把齿间的油液从压
油口挤压输出的容腔称为压油腔。
当齿轮泵不断地旋转时,齿轮泵的
吸、压油口不断地吸油和压油,实现了向液压系统输送油液的过程。
在齿轮泵中,吸油区和压油区由相互啮合的轮齿和泵体分隔开来,因此没有单独的配油机构。
齿轮泵是容积式回转泵的一种,其工作原理是:
齿轮泵具有一对互相啮合的齿轮,齿轮(主动轮)固定在主动轴上,齿轮泵的轴一端伸出壳外由原动机驱动,齿轮泵的另一个齿轮(从动轮)装在另一个轴上,
文档仅供参考
齿轮泵的齿轮旋转时,液体沿吸油管进入到吸入空间,沿上下壳壁被两个齿轮分别挤压到排出空间汇合(齿与齿啮合前),然后进入压油管排出。
齿轮泵的主要特点是结构紧凑、体积小、重量轻、造价低。
但与其它类型泵比较,有效率低、振动大、噪音大和易磨损的缺点。
齿轮泵适合于输送黏稠液体。
1.3齿轮泵的结构特点
齿轮采用具有国际九十年人先进水平的新技术--双圆弧正弦曲线
齿型圆弧。
它与渐升线齿轮相比,最突出的优点是齿轮啮合过程中齿廓面没有相对滑动,因此齿面无磨损、运转平衡、无困液现象,噪声低、寿命长、效率高。
该泵摆脱传统设计的束缚,使得齿轮泵在设计、生产和使用上进入了一个新的领域。
泵设有差压式安全阀作为超载保护,安全阀全回流压力为泵额定
排出压力1.5倍。
也可在允许排出压力范围内根据实际需要另行调
整。
可是此安全阀不能作减压阀长期工作,需要时可在管路上另行安
装。
该泵轴端密封设计为两种形式,一种是机械密封,另一种是填料密封,可根据具体使用情况和用户要求确定。
1.4外啮合齿轮泵基本设计思路及关键技术
外啮合泵主要由主、从动齿轮,驱动轴,泵体及侧板等主要零件构
成。
泵体内相互啮合的主、从动齿轮与两端盖及泵体一起构成密封工作容积,齿轮的啮合点将两腔隔开,形成了吸、压油腔,吸油腔内的轮齿脱离啮合,密封工作腔容积不断增大,形成部分真空,油液在大气压力作用下从油箱经吸油管进入吸油腔,并被旋转的轮齿带入压油腔。
压油腔内的轮齿不断进入啮合,使密封工作腔容积减小,油液受到挤压被排往系统,这就是齿轮泵的吸油和压油程。
在齿轮泵的啮合过程中,啮合点沿啮合线,把吸油区和压油区分开。
根据外啮合齿轮泵的工作原理及外啮合齿轮泵设计方面的资料,我们可总结出外啮合齿轮泵的基本设计思路如下:
1.根据使用场合选择齿数。
均匀性要求高的一般取14到,20齿。
要求低的取6到14齿。
2.根据需要的排量计算模数。
m=q/KZ(B/m)开三次根号。
m是模数Z是齿数q是排量。
K=6.66,B是齿宽(B/m)根据压力查表低压较大,高压较小
3.齿轮变位。
齿轮泵齿轮匀许根切但要保证根切的情况下不漏油。
因此一般要保证啮合线始终在根切部分以外。
具体要查齿轮手册。
根据
以往经验14齿以上能够不变位。
变位会使排量变小,因此需要变位时
得把齿数再减小然后变位来凑出需要的排量。
齿轮是核心部件,至此主要工作结束。
4.轴的设计与校核。
5.开泄荷槽。
一般都是开那种矩形对称的。
并根据〈〈液压元件》上的公试计算其尺寸。
6.计算吸油和排油口齿寸。
7.选密封件、轴承、键等标准件。
8.选择泵体壁厚画外壳。
其中关键技术为齿轮的设计与轴向间隙补偿装置的设计。
2外啮合齿轮泵设计
2.1齿轮的设计计算
(1)因为另外啮合齿轮泵是中高压齿轮泵因此材料强度要求较
高,根据资料文献选择齿轮材料为40Cr。
(2)确定参数
根据齿轮泵的排量公式
V2zm3(B/m)1032zm2B103
由于齿间容积比轮齿间的体积稍大,考虑这一因素,将2兀用6,
66代替比较符合实际情况。
因此
m3」V103
m\6.66z(B/m)
式中B—齿宽(mm)
\J公称排量(ml/r)
—齿轮齿数
m^模数(mm)
根据额定压力P=10MPa
齿数选择原则:
当前齿轮泵的齿数一般为z=6-20.由于低压齿轮泵多
应用在机床上,故要求流量均匀,因此低压齿轮泵的齿数多取为13-
20。
对于高压齿轮泵,要求有较大的齿根强度。
为了减小轴承的受力,
要减小齿顶圆直径,这样势必要增大模数、减少齿数,因此高压齿轮泵
的齿数较少,一般取z=6-14。
为了防止根切削弱齿根强度,齿形要求进行修正。
齿宽选择原则:
齿轮泵的流量成正比,增加齿宽能够相应的增加流量而齿轮与泵体及盖板间的摩擦损失及容积损失的总和与齿宽并不成比例的增加,因此,齿宽较大时液压泵的总效率较高,但对于高压齿轮泵,齿宽不宜过大,否则将使齿轮轴及轴承上的载荷过大使轴及轴承设
计困难。
一般对于高压齿轮泵B=(3-6)m,对于低压齿轮泵B=(6-10)m。
泵的工作压力越高,上述系数应取得越小。
根据以上原则选择齿数z=14,B/m=5.4,代入数据得
m363103497
m\6.66145.49
(3)校核:
齿轮泵排量校核
6.66
2一_3
14522710
100%99.9%
63
误差小于5%,合格。
按齿根弯曲疲劳强度校核齿轮:
因从动轮受力大因此只需校核从动轮。
根据校核公式
F2YFaYsa
确定式中各参数:
D=mz=5x14=70mm
n=
(VX60x1000)/(兀-D)=1287r/min
1287r/min、
F{pqt10Mpa(63ml/r)13.5KW
60s/min
1.0105N?
mm
P135
T95499549-100N?
m
n1287
dB/d27/700.386
查手册得:
YFa3.2
Ysa1.49
F220Mpa
将其代入得:
___5
3.21.49137.7MpaF
21.3661.010
F23
0.386145
因此齿轮合格。
2.2轴的设计与校核
2.2.1.齿轮泵的径向力
齿轮泵工作时,作用在齿轮轴颈及轴承上的径向力,由液压力和齿轮啮合力组成。
1.液压力是指沿齿轮圆周液体压力所产生的径向力F。
液压力的大
小和方向取决于液体压力沿齿顶圆周的分布情况,吸油腔区段(其夹角为)受压力pd的作用,压油腔区段(其夹角为)受压力pg的作用,吸
压油腔之间的过渡段(其夹角为)所受的压力是变化的(由pd升
至Pg)。
为计算简便,可近似认为吸压油腔间的过渡段,承受沿齿轮圆
周线性分布压力,如图2-1所示。
图2-1齿轮圆周压力的近似分布曲线
在实际设计时,齿轮所受的总液压力FP亦可按下列近似公式计算
Fp6.5pbDe(N)
液压力作用在主动齿轮上产生的径向力和作用在从动齿轮上产生的径向力,其大小与方向完全相同。
2.啮合力是指两齿轮啮合是,由彼此在啮合点的相互作用而产生的径
力Ft。
作用在主动轮上的啮合力,其方向与作用在主动齿轮上的液压力方向相反,可抵消一部分液压力;作用在从动齿轮上的啮合力,其方向与作用在从动轮上的液压力方向相同,增大了径向力。
由于齿轮泵在工作
过程中,啮合点的位置在节点附近来回变动,因此啮合力也是变化的。
在实际设计中,齿轮轴颈所受的径向力F(包括液压力和啮合
力),可按下列近似公式计算
F主7.5pbDe(N)
F从8.5pbDe(N)
2.2.2减小径向力和提高齿轮轴轴颈及轴承负载能力的措施
齿轮泵的径向力大,作用在齿轮轴轴颈及轴承上的负载大,这是妨碍
齿轮泵提高性能和使用寿命的重要因素,如何减小齿轮泵的径向力及提
高齿轮轴轴颈及轴承的承载能力,是研究齿轮泵的主要课题之一。
要解决齿轮轴轴颈及轴承的负载问题,能够从以下方面进行研究。
1.减小径向力
减小径向力一直是从事高压齿轮泵研制的科技人员的研究课题,因
为轴承寿命与负载的10/3(为滚针轴承;滚珠轴承为3)次方成反
比,也就是说,若轴承负载减小30%。
寿命可延长3倍。
减小径向
力的方法,较常见的可归纳为三种:
(1)合理地选择齿宽b和齿顶圆直径D。
(2)缩小压油口直径,使压力油仅作用在一个齿到两个齿的
范围内,这样压力油作用于齿轮上的面积减小,因而径向力就相应的减小。
(3)开压力平衡槽,这种方法使作用在轴承上的径向力大大
减小。
但此种方法会使泵的内泄漏增加,容积效率降低,因此很少使用此种方法。
2.改进齿轮轴的材料及热处理性能
2.2.3轴的设计与校核
从动轮径向力:
Fr0.85pBDe0.8510Mpa27mm78mm17.9KN
最小轴径计算
P17.9
dminC3110327mm
.ni1287
综合各方面考虑初步设计轴的结构尺寸图如下:
m
y
4
p.J
4
E0
M6
30
45
6
3
图2-2轴的受力分析
根据轴的弯矩平衡有:
Fn2?
BCFr?
AB
因此有:
Fr?
AB
FN2-八
bc
再根据力平衡有:
可知截面3-3,4-4,6-6有可能是危险截面。
下面用第三强度理论校
3-3截面:
由截面直径为40mm有抗弯截面系数为:
弯矩为:
扭矩为:
100N?
m
应力为:
因此此截面安全。
4-4截面:
直径为35mm,有抗弯截面系数为:
弯矩为:
应力为:
淄«31.9MPa
4.2106
因此截面安全。
33
63
10m
45MPa
D303
Wt5289.8mm35.3
1616
切应力为:
T100
618.9MPa
Wt5.310
因此此截面安全。
2.3卸荷槽尺寸设计计算
2.3.1困油现象的产生及危害
齿轮泵在工作过程中,同时啮合的齿应多于一对,即重合度系数大
于一(一般取1.05到1.15),才能正常工作。
虽然从理论上讲,重合度系数等于一,齿轮不会出现间断吸压油现象,也不产生困油现象,能够正常工作,但考虑到制造误差,实际工作时啮合系数往往会小于一。
因而齿轮泵的输油率就很不均匀,会出现时而输油时而不输油的不正常
现象,瞬时流量的差值可达30%左右,齿轮泵不能正常工作。
齿轮泵要平稳工作,齿轮啮合的重合度必须大于1,于是总有两
对齿轮同时啮合,并有一部分油液被围困在两对轮齿所围成的封闭容腔之间。
这个封闭的容腔开始随着齿轮的转动逐渐减小,以后又逐渐加大。
封闭腔容积的减小会使被困油液受挤压而产生很高的压力,而且从缝隙中挤出,导致油液发热,并致使机件受到额外的负载;而封闭腔容积的增大又造成局部真空,使油液中溶解的气体分离,产生气穴现象。
这些都将产生强烈的振动和噪声,这就是齿轮泵的困油现象。
困油现象的危害:
径向不平衡力很大时能使轴弯曲,齿顶与壳体
接触,同时加速轴承的磨损,降低轴承的寿命。
消除困油的方法,一般是在两侧盖板上开卸荷槽,使封闭腔容积减小时经过左边的卸荷槽与压油腔相通,容积增大时经过右边的卸荷槽与吸油腔相通。
齿轮泵的困油现象,由于齿侧间隙的大小不同,闭死容积变化曲线也不同。
下面按有齿侧间隙和无齿侧间隙(或间隙很小)两种情况进行分析。
图2-3为有齿侧间隙的齿轮泵困油现象示意图。
当新的一对齿在A
点开始啮合是,前一对齿在B点啮合尚未脱开,在它们之间形成一个困油容积VbV1V2,此时的困油容积最大,由于存在齿侧间隙,V1和V2是
相通的(如图2-3a),当齿轮按图示方向旋转,Vi逐渐减小,V2逐渐增
大,而整个困油容积Vb逐渐减小,当齿轮旋转到两个啮合点(D、E)对
称于节点P时,Vb为最小(如图2-3b);当齿轮继续旋转,Vi继续减
小,V2继续增大,而Vb逐渐增大,直到前对齿即将在C点脱离啮合时,Vb又增加到最大(如图2-3C)。
图2-3有齿侧间隙的齿轮泵困油区得形成和变化过程
2.3.2消除困油危害的方法
困油现象是齿轮泵不可避免的技术问题,必须采取措施解决。
消除困油危害一般是在于齿轮端面接触的泵盖(或泵体、侧板、轴套、轴承座圈)上开卸荷槽。
开卸荷槽总的原则是:
在保证高低压腔互不相通的前提下,设法使困油容积与压油腔或吸油腔相通。
卸荷槽的结构形式,一般可分为三类:
1.相对齿轮中心连线对称布置的双卸荷槽
(1)对称布置的双矩形卸荷槽;
(2)对称布置的双圆形卸荷槽。
2.相对齿轮中心连线不对称布置的双卸荷槽
(1)向低压侧偏移的不对称布置的双卸荷槽;
(2)向高压侧偏移的不对称双卸荷槽(有齿侧间隙的泵,一般不采用这种结构)。
3.单个卸荷槽
(1)仅压油腔有卸荷槽;
(2)仅吸油腔有卸荷槽。
卸荷槽的位置与齿轮的齿侧间隙大小有关,无齿侧间隙或间隙很小时,其距中心线的距离要小,只相当于有齿侧间隙的一半。
一般齿轮泵大都具有齿侧间隙,因此这里只介绍有齿侧间隙的卸荷槽。
卸荷槽的形状一半分矩形和圆形两种,在实际生产中,相对齿轮中心连线不对称布置的双圆形卸荷槽应用较为普遍。
下面简单介绍几种常见的卸荷槽。
1.相对齿轮中心连线对称布置的双卸荷槽
对称布置的双卸荷槽的位置,应保证如下条件:
(a)当困油容积开始由大变小、液体受挤压时,该容积应与压油腔相通。
(b)当困油容积为最小时,压油腔应与吸油腔隔开。
(c)当困油容积开始由小变大时,该容积应与吸油腔相通。
(1)对称布置的双矩形卸荷槽
图2-4所示为有齿侧间隙的对称双矩形卸荷槽结构图。
图中困油容
积Vb正处于最小位置,两个卸荷槽的边缘正好和啮合点D和E相接。
两
卸荷槽之间的距离a因保证困油容积Vb在到达最小位置前始终和压油腔相通。
Vb在最小位置时,困油容积Vb既不和压油腔相通,也不和吸油腔相通,过了最小位置后又始终和吸油腔相通。
因此对a的尺寸要求很
严,若a太大,困油现象不能彻底消除;若a太小,又会使吸油腔和压油腔沟通,引起泄露,降低齿轮泵的效率。
图2-4有齿侧间隙的对称双矩形卸荷槽
(2)对称布置的双圆形卸荷槽
图2-5所示为有齿侧间隙的双圆形卸荷槽。
只要使圆形卸荷槽的圆
周与困油容积处于最小位置时(见图2-3b)的齿轮啮合点D和E相交,
即可达到卸荷目的。
图2-5有侧隙时的对称双矩形卸荷槽和对称
双圆形卸荷槽的几何关系
2.向低压侧偏移的不对称双卸荷槽
有侧隙的对称双卸荷槽,用于低压齿轮泵已能满足卸荷要求,但对
于中高压,高压齿轮泵,尚有卸荷不完善的缺点。
为彻底解决困油现
象,采用向低压侧偏移的不对称双卸荷槽。
无侧隙(或侧隙很小)的对称双卸荷槽,因两卸荷槽之间的距离仅为有侧隙双卸荷槽的一半,卸荷是充分的,不需要向低压侧偏移的卸荷槽结构。
向低压侧偏移的不对称双卸荷槽开设原则是:
在不使压油腔与吸油
腔沟通的前提下,使Vi在压缩到最小值时始终和压油腔相通,即使两个卸荷槽边缘分别经过困油终了时的齿轮啮合点F和困油开始时的齿轮啮
合点C(如图2-5)。
2.3.3卸荷槽尺寸计算
根据以上所述,此处可采用对称式的矩形卸荷槽。
(1)两卸荷槽的间距a计算公式:
zm2acosn
A
式中:
n一刀具齿形角;
A一两个齿轮的实际中心距。
无侧隙啮合方程
2(xiX2)tan
ivnivn
ZiZ2
节圆直径计算公式
cosdd
cos
因此:
Adl?
d27imm
代入得:
1452°C.
acos2014.55mm
71
高压侧和低压侧