年产15万吨合成氨变换工段.docx
《年产15万吨合成氨变换工段.docx》由会员分享,可在线阅读,更多相关《年产15万吨合成氨变换工段.docx(30页珍藏版)》请在冰豆网上搜索。
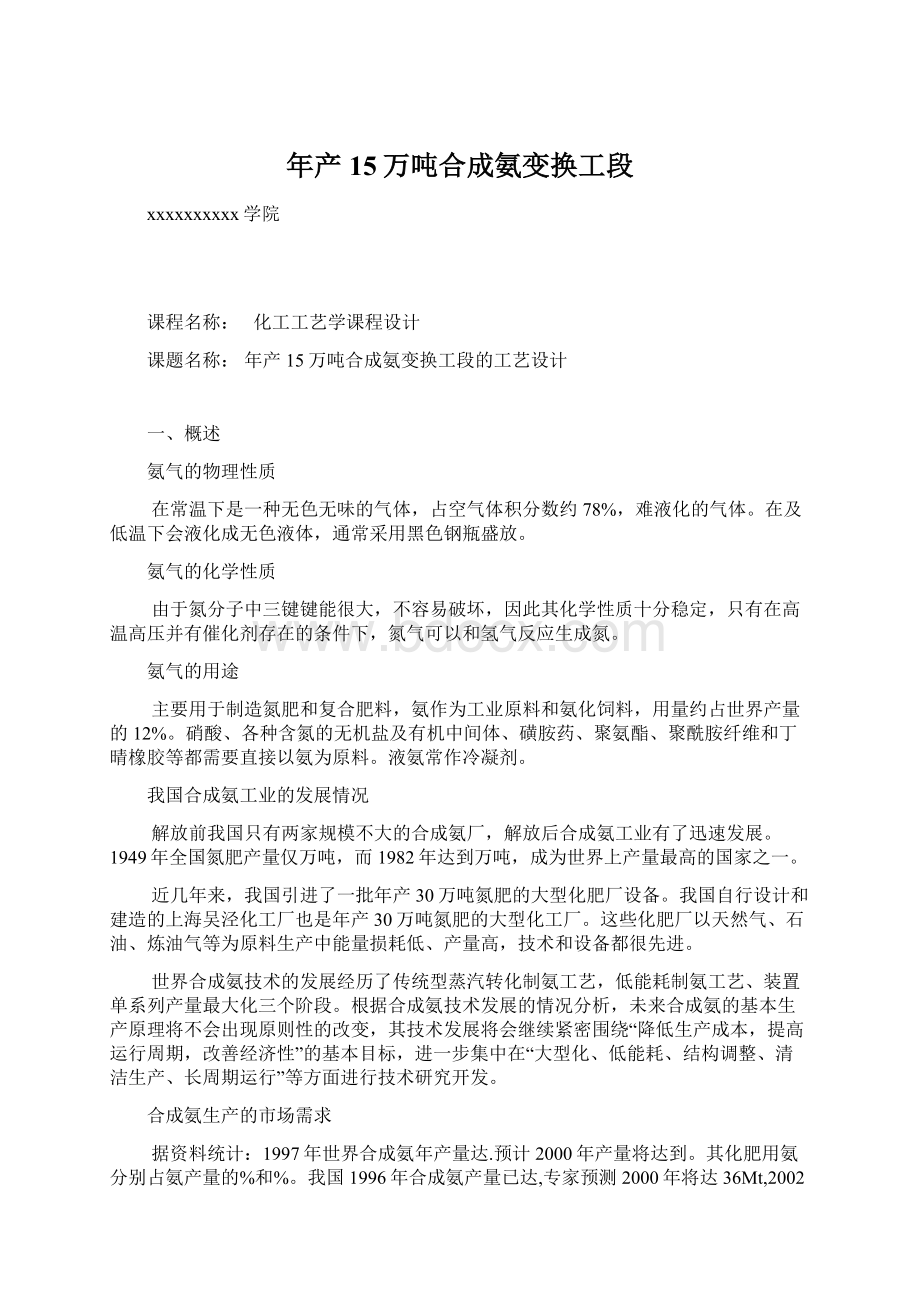
年产15万吨合成氨变换工段
xxxxxxxxxx学院
课程名称:
化工工艺学课程设计
课题名称:
年产15万吨合成氨变换工段的工艺设计
一、概述
氨气的物理性质
在常温下是一种无色无味的气体,占空气体积分数约78%,难液化的气体。
在及低温下会液化成无色液体,通常采用黑色钢瓶盛放。
氨气的化学性质
由于氮分子中三键键能很大,不容易破坏,因此其化学性质十分稳定,只有在高温高压并有催化剂存在的条件下,氮气可以和氢气反应生成氮。
氨气的用途
主要用于制造氮肥和复合肥料,氨作为工业原料和氨化饲料,用量约占世界产量的12%。
硝酸、各种含氮的无机盐及有机中间体、磺胺药、聚氨酯、聚酰胺纤维和丁晴橡胶等都需要直接以氨为原料。
液氨常作冷凝剂。
我国合成氨工业的发展情况
解放前我国只有两家规模不大的合成氨厂,解放后合成氨工业有了迅速发展。
1949年全国氮肥产量仅万吨,而1982年达到万吨,成为世界上产量最高的国家之一。
近几年来,我国引进了一批年产30万吨氮肥的大型化肥厂设备。
我国自行设计和建造的上海吴泾化工厂也是年产30万吨氮肥的大型化工厂。
这些化肥厂以天然气、石油、炼油气等为原料生产中能量损耗低、产量高,技术和设备都很先进。
世界合成氨技术的发展经历了传统型蒸汽转化制氨工艺,低能耗制氨工艺、装置单系列产量最大化三个阶段。
根据合成氨技术发展的情况分析,未来合成氨的基本生产原理将不会出现原则性的改变,其技术发展将会继续紧密围绕“降低生产成本,提高运行周期,改善经济性”的基本目标,进一步集中在“大型化、低能耗、结构调整、清洁生产、长周期运行”等方面进行技术研究开发。
合成氨生产的市场需求
据资料统计:
1997年世界合成氨年产量达.预计2000年产量将达到。
其化肥用氨分别占氨产量的%和%。
我国1996年合成氨产量已达,专家预测2000年将达36Mt,2002年将增加至45Mt。
即今后20年间将增加到现在的倍。
因而合成氨的持续健康发展还有相当长的路要走,未来我国合成氨氮肥的实物产量将会超过石油和钢铁。
合成氨工业在国民经济中举足轻重,农业生产“有收无收在水,收多收少在肥”。
所以,合成氨工业是农业的基础,它的发展将对国民经济的发展产生重大影响。
因此,我国现有众多的化肥生产装置应为改造扩建增产的基础。
我国七十至九十年代先后重复引进30多套大化肥装置,耗费巨额资金,在提高了化肥生产技术水平的同时,也受到国外的制约,今后应用国内开发和消化吸收引进的技术,自力更生,立足国内,走出一条具有中国特色的社会主义名族工业的道路,过去引进建设一套大型化肥装置,耗资数十亿元。
当今走老厂改造扩建的道路,可使投资节省1/2-2/3.节省的巨额资金用作农田水利建设和农产品深加工,将在加速农村经济发展,提高农民生活水平,缩小城乡差距起着重要作用。
二、工艺路线的选择
常用的变换工艺有:
中温变换工艺、中串低变换工艺、中低低变换工艺、全低变工艺。
中温变换工艺
中温变换工艺早期均采用常压,经节能改造,现在大都采用加压变换。
加压中温变换工艺主要特点是:
采用低温高活性的中变催化剂,降低了工艺上对过量蒸汽的要求;采用段间冷激降温,减少了系统的热负荷和阻力,减小外供蒸汽量;合成与变换,铜洗构成第二换热网络,合理利用热能。
中串低变换工艺
所谓中温变换串低温变换流程,就是在B107等Fe-Cr系催化剂之后串入Co-Mo系宽温变换催化剂。
与中变流程相比,中串低工艺蒸汽消耗下降,饱和塔负荷减轻。
中低低变换工艺
中低低流程是在一段铁铬系中温变换催化剂后直接串二段钴钼系耐硫变换催化剂,利用中温变换的高温来提高反应速率,利用两段低温变换提高变换率,实现节能降耗。
这样充分发挥了中变催化剂和低变催化剂的特点,实现了最佳组合,达到了能耗低、阻力小、操作方便的理想效果。
全低变工艺
全低变工艺是全部采用低温活性钴钼系变换催化剂进行一氧化碳变换的工艺过程,作为一种节能新工艺,节能降耗的效果显著。
此工艺中蒸汽消耗较低,在几种变换流程中蒸汽消耗最低。
三、工艺流程的设计
.压力:
压力对变换反应的平衡几乎没有影响。
但是提高压力将使析炭和生成甲烷等副反应易于进行。
单就平衡而言,加压并无好处。
但从动力学角度,加压可提高反应速率。
从能量消耗上看,加压也是有利。
由于干原料气摩尔数小于干变换气的摩尔数,所以,先压缩原料气后再进行变换的能耗,比常压变换再进行压缩的能耗底。
具体操作压力的数值,应根据中小型氨厂的特点,特别是工艺蒸汽的压力及压缩机投各段压力的合理配置而定。
一般小型氨厂操作压力为中型氨厂为~。
本设计的原料气由小型合成氨厂天然气蒸汽转化而来,故压力可取.
.温度:
变化反应是可逆放热反应。
从反应动力学的角度来看,温度升高,反应速率常数增大对反应速率有利,但平衡常数随温度的升高而变小,即CO平衡含量增大,反应推动力变小,对反应速率不利,可见温度对两者的影响是相反的。
因而存在着最佳反应温对一定催化剂及气相组成,从动力学角度推导的计算式为
Tm=
式中Tm、Te—分别为最佳反应温度及平衡温度,最佳反应温度随系统组成和催化剂的不同而变化。
.汽气比:
水蒸汽比例一般指H2O/CO比值或水蒸汽/干原料气.改变水蒸汽比例是工业变换反应中最主要的调节手段。
增加水蒸汽用量,提高了CO的平衡变换率,从而有利于降低CO残余含量,加速变换反应的进行。
由于过量水蒸汽的存在,保证催化剂中活性组分Fe3O4的稳定而不被还原,并使析炭及生成甲烷等副反应不易发生。
但是,水蒸气用量是变换过程中最主要消耗指标,尽量减少其用量对过程的经济性具有重要的意义,蒸汽比例如果过高,将造成催化剂床层阻力增加;CO停留时间缩短,余热回收设备附和加重等,所以,中(高)变换时适宜的水蒸气比例一般为:
H2O/CO=3~5,经反应后,中变气中H2O/CO可达15以上,不必再添加蒸汽即可满足低温变换的要求。
.流程图
原料气体→脱硫→一段转化→二段转换→变换
↓
脱硫
↓
合成气
.工艺选择
目前的变化工艺有:
中温变换,中串低,全低及中低低4种工艺。
选用中串低工艺。
转化气从转化炉进入废热锅炉,在废热锅炉中变换气从920℃降到330℃,在废热锅炉出口加入水蒸汽使汽气比达到3到5之间,以后再进入中变炉将转换气中一氧化碳含量降到3%以下。
再通过换热器将转换气的温度降到180℃左右,进入低变炉将转换气中一氧化碳含量降到%以下,再进入甲烷化工段。
中低变串联流程中,主要设备有中变炉、低变炉、废热锅炉、换热器等。
四、工艺计算
中温变换物料衡算及热量衡算
.1.确定转化气组成:
已知条件中变炉进口气体组成:
表4-1进口气体组成表
组分
CO2
CO
H2
N2
CH4
O2
合计
%
100
计算基准:
1吨氨
计算生产1吨氨需要的变化气量:
(1000/17)×(2×)=M3(标)
因为在生产过程中物量可能会有消耗,因此变化气量取M3(标)
年产15万吨合成氨生产能力:
日生产量:
150000/330=d=h
要求出中变炉的变换气干组分中CO%小于2%
进中变炉的变换气干组分:
表4-2进中变炉的变换气干组分表
组分
CO2
CO
H2
N2
O2
CH4
合计
含量,%
100
M3(标)
474
假设入中变炉气体温度为335摄氏度,取出炉与入炉的温差为30摄氏度,则出炉温度为365摄氏度。
进中变炉干气压力
=.
水汽比的确定:
考虑到是天然气蒸汽转化来的原料气,所以取
故V(水)=(标)n(水)=
因此进中变炉的变换气湿组分:
表4-3进中变炉的变换气湿组分表
组分
CO
合计
含量%
100
M3(标)
474
koml
中变炉CO的实际变换率的求取:
假定湿转化气为100mol,其中CO基含量为%,要求变换气中CO含量为
2%,故根据变换反应:
CO+H2O=H2+CO2,则CO的实际变换率为:
%=
×100=74%
式中Ya、
分别为原料及变换气中CO的摩尔分率(湿基)
则反应掉的CO的量为:
×74%=
则反应后的各组分的量分别为:
H2O%=%%+%=23%
CO%=%%=%
H2%=%+%%=%
CO2%=%+%=%
中变炉出口的平衡常数:
K=(H2%×CO2%)/(H2O%×CO%)=12
查《小合成氨厂工艺技术与设计手册》可知K=12时温度为397℃。
中变的平均温距为397℃-365℃=32℃
中变的平均温距合理,故取的H2O/CO可用。
中变炉一段催化床层的物料衡算
假设CO在一段催化床层的实际变换率为60%。
因为进中变炉一段催化床层的变换气湿组分:
表4-4催化床层的变换气湿组分表
组分
CO2
CO
H2
N2
O2
CH4
H2O
合计
含量,%
100
M3(标)
474
koml
假使O2与H2完全反应,O2完全反应掉
故在一段催化床层反应掉的CO的量为:
60%×=(标)=
出一段催化床层的CO的量为:
M3(标)=
故在一段催化床层反应后剩余的H2的量为:
+×=M3(标)=
故在一段催化床层反应后剩余的CO2的量为:
474+=M3(标)=
出中变炉一段催化床层的变换气干组分:
表4-5变换气干组分表
组分
CO2
CO
H2
N2
CH4
合计
含量%
100
M3(标)
koml
剩余的H2O的量为:
标)=
所以出中变炉一段催化床层的变换气湿组分:
表4-6一段催化床层的变换气湿组分表
组分
CO2
CO
H2
N2
CH4
H2O
合计
含量%
100
M3(标)
koml
对出中变炉一段催化床层的变换气的温度进行计算:
已知出中变炉一段催化床层的变换气湿组分的含量(%):
表4-7变换气湿组分的含量(%)表
组分
CO2
CO
H2
N2
CH4
H2O
合计
含量%
100
M3(标)
koml
对出变炉一段催化床层的变换气温度进行估算:
根据:
K=(H2%×CO2%)/(H2O%×CO%)计算得K=
查《小合成氨厂工艺技术与设计手册》知当K=时t=445℃
设平均温距为30℃,则出变炉一段催化床层的变换气温度为:
445℃-30℃=415℃
中变炉一段催化床层的热量衡算
以知条件:
进中变炉温度:
335℃
出变炉一段催化床层的变换气温度为:
415℃
反应放热Q:
在变化气中含有CO,H2O,O2,H2这4种物质会发生以下2种反应:
CO+H2O=CO2+H2(1-1)
O2+2H2=2H2O(1-2)
这2个反应都是放热反应。
为简化计算,拟采用统一基准焓(或称生成焓)计算。
以P=1atm,t=25℃为基准的气体的统一基准焓