换档机构分析报告最终版.docx
《换档机构分析报告最终版.docx》由会员分享,可在线阅读,更多相关《换档机构分析报告最终版.docx(34页珍藏版)》请在冰豆网上搜索。
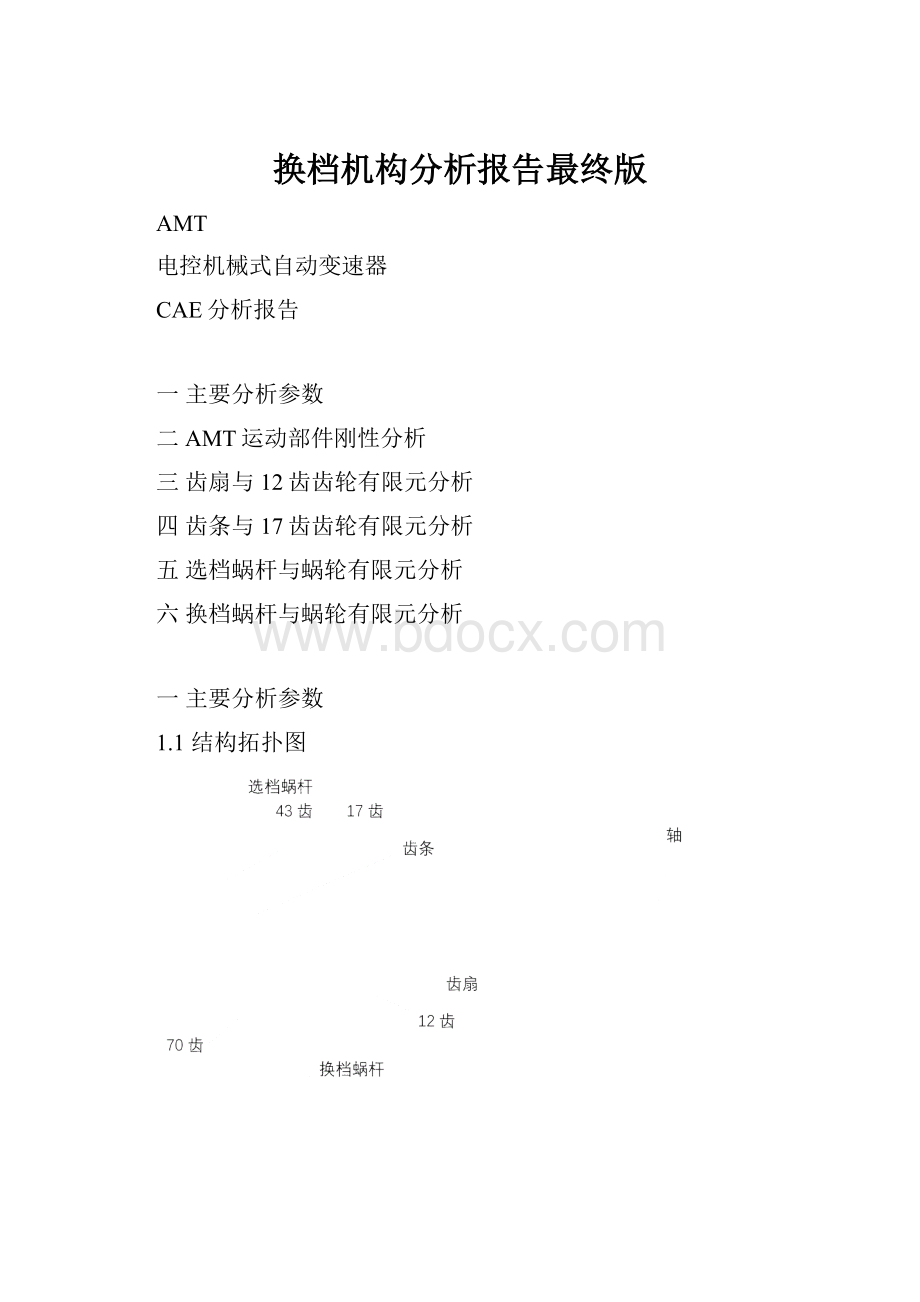
换档机构分析报告最终版
AMT
电控机械式自动变速器
CAE分析报告
一主要分析参数
二AMT运动部件刚性分析
三齿扇与12齿齿轮有限元分析
四齿条与17齿齿轮有限元分析
五选档蜗杆与蜗轮有限元分析
六换档蜗杆与蜗轮有限元分析
一主要分析参数
1.1结构拓扑图
图1刚性分析的总体结构模型
结构拓扑图
轴
齿扇
齿条
17齿齿轮
43齿齿轮
12齿齿轮
70齿齿轮
选档蜗杆
换档蜗杆
大地
轴
固定副fix2
旋转副revjoint4
齿扇
固定副fix2
接触contact1
齿条
接触contact3
移动副
17齿齿轮
接触contact3
接触contact4
旋转副revjoint1
43齿齿轮
接触contact4
接触contact5
旋转副revjoint2
12齿齿轮
接触contact1
固定副fix3
旋转副revjoint3
70齿齿轮
固定副fix3
接触contact2
选档蜗杆
接触contact5
旋转副revjoint5
换档蜗杆
接触contact2
旋转副revjoint6
1.2AMT零件的材料力学属性
轴
齿扇
齿条
17齿齿轮
43齿齿轮
12齿齿轮
70齿齿轮
选档蜗杆
换档蜗杆
材料
40Cr
40Cr
尼龙
40Cr
尼龙
40Cr
尼龙
40Cr
40Cr
弹性模量(MPa)
2.1e5
2.1e5
6e3
2.1e5
6e3
2.1e5
6e3
2.1e5
2.1e5
泊松比
0.287-0.3
0.287-0.3
0.4
0.287-0.3
0.4
0.287-0.3
0.4
0.287-0.3
0.287-0.3
密度kg/mm3
7.85e-6
7.85e-6
1.35e-6
7.85e-6
1.35e-6
7.85e-6
1.35e-6
7.85e-6
7.85e-6
屈服极限(MPa)
785
785
150
785
150
785
150
785
785
强度极限(MPa)
980
1.3分析方案及参数
采用N-1-2-3-4-5-4-3-2-1-N-R-N方案。
换挡间隔t=3s,仿真一个循环周期,即仿真时间为36s。
选档蜗杆和换档蜗杆为驱动件,转速为n=1000rpm,其中选档时间约为0.1468s,换档时间约为0.157s。
仿真模型中,换档的阻力等效为轴的阻力距。
选档的阻力为两个回位弹簧。
两个回位弹簧的动态阻尼系数为0.5。
选取刚体的接触刚度系数为10000。
1、2、3、4、5、倒档的换档和摘档的阻力分别为F1-F12。
选档行程h1和h2。
换档的行程l1-l6(参数均为汽车厂家提供)。
二AMT运动部件刚性分析
2.1选档蜗杆、换档蜗杆及轴的等效阻力矩
为了实现选档和换档的顺利进行,必须在规定时间周期内完成选档和换档。
此外轴上的等效阻力矩的大小必须和换档的时刻相对应。
在此,用if函数表达式来写驱动和阻力矩表达式。
图2选档蜗杆的转速
图2表示的是选档蜗杆的转速。
选档蜗杆处于反复旋转和静止的交替状态。
以下是实现选档蜗杆转速的表达式。
2*PI*n*(IF(TIME:
0,1,1)-IF(TIME-h1/a/n:
0,1,1)-IF(TIME-2*t-ATAN(l2/52)/b/n:
0,1,1)+IF(TIME-2*t-ATAN(l2/52)/b/n-h1/a/n:
0,1,1)-IF(TIME-4*t-ATAN(l4/52)/b/n:
0,1,1)+IF(TIME-4*t-ATAN(l4/52)/b/n-h2/a/n:
0,1,1)+IF(TIME-5*t-ATAN(l5/52)/b/n:
0,1,1)-IF(TIME-5*t-ATAN(l5/52)/b/n-h2/a/n:
0,1,1)+IF(TIME-7*t-ATAN(l3/52)/b/n:
0,1,1)-IF(TIME-7*t-ATAN(l3/52)/b/n-h1/a/n:
0,1,1)-IF(TIME-9*t-ATAN(l1/52)/b/n:
0,1,1)+IF(TIME-9*t-ATAN(l1/52)/b/n-h1/a/n:
0,1,1)-IF(TIME-10*t:
0,1,1)+IF(TIME-10*t-h2/a/n:
0,1,1)+IF(TIME-11*t-ATAN(l6/52)/b/n:
0,1,1)-IF(TIME-11*t-ATAN(l6/52)/b/n-h2/a/n:
0,1,1))
图3换档蜗杆的转速
图3显示的换档蜗杆的转速和图2显示的选档蜗杆的转速类似。
以下是实现换档蜗杆转速的表达式。
2*PI*n*(IF(TIME-h1/a/n:
0,1,1)-IF(TIME-h1/a/n-ATAN(l1/52)/b/n:
0,1,1)-IF(TIME-t:
0,1,1)+IF(TIME-t-ATAN(l1/52)/b/n-ATAN(l2/52)/b/n:
0,1,1)+IF(TIME-2*t:
0,1,1)-IF(TIME-2*t-ATAN(l2/52)/b/n:
0,1,1)+IF(TIME-2*t-ATAN(l2/52)/b/n-h1/a/n:
0,1,1)-IF(TIME-2*t-ATAN(l2/52)/b/n-h1/a/n-ATAN(l3/52)/b/n:
0,1,1)-IF(TIME-3*t:
0,1,1)+IF(TIME-3*t-ATAN(l3/52)/b/n-ATAN(l4/52)/b/n:
0,1,1)+IF(TIME-4*t:
0,1,1)-IF(TIME-4*t-ATAN(l4/52)/b/n:
0,1,1)+IF(TIME-4*t-ATAN(l4/52)/b/n-h2/a/n:
0,1,1)-IF(TIME-4*t-ATAN(l4/52)/b/n-h2/a/n-ATAN(l5/52)/b/n:
0,1,1)-IF(TIME-5*t:
0,1,1)+IF(TIME-5*t-ATAN(l5/52)/b/n:
0,1,1)-IF(TIME-5*t-ATAN(l5/52)/b/n-h2/a/n:
0,1,1)+IF(TIME-5*t-ATAN(l5/52)/b/n-h2/a/n-ATAN(l4/52)/b/n:
0,1,1)+IF(TIME-6*t:
0,1,1)-IF(TIME-6*t-ATAN(l4/52)/b/n-ATAN(l3/52)/b/n:
0,1,1)-IF(TIME-7*t:
0,1,1)+IF(TIME-7*t-ATAN(l3/52)/b/n:
0,1,1)-IF(TIME-7*t-ATAN(l3/52)/b/n-h1/a/n:
0,1,1)+IF(TIME-7*t-ATAN(l3/52)/b/n-h1/a/n-ATAN(l2/52)/b/n:
0,1,1)+IF(TIME-8*t:
0,1,1)-IF(TIME-8*t-ATAN(l2/52)/b/n-ATAN(l1/52)/b/n:
0,1,1)-IF(TIME-9*t:
0,1,1)+IF(TIME-9*t-ATAN(l1/52)/b/n:
0,1,1)-IF(TIME-10*t-h2/a/n:
0,1,1)+IF(TIME-10*t-h2/a/n-ATAN(l6/52)/b/n:
0,1,1)+IF(TIME-11*t:
0,1,1)-IF(TIME-11*t-ATAN(l6/52)/b/n:
0,1,1))
图4轴上的等效阻力距
图4所示的轴上的等效阻力距和换档运动对应。
即在换档蜗杆运动时,轴上有相对应的阻力距,在换档蜗杆静止时,轴上的等效阻力距为零。
最大力矩可达9172.8Nmm。
其中阻力矩的等效计算为:
M=F*H
2.2后处理分析
主要包括动态接触力的分析、力矩的分析、接触力FFT频谱分析、力矩FFT频谱分析。
图5齿扇与12齿齿轮间接触力
图5显示了齿扇与12齿齿轮间接触力的变化规律。
其中最大接触力大约在30s的时候,即倒档的换档,接触力达317.321N,如图5所示。
另外可知,有接触力的时间段远小于接触力为零的时间段,齿扇与12齿齿轮的接触都是瞬时完成的。
图6齿扇与相应齿轮间接触力FFT频谱分析
通过对齿扇与齿轮间接触力FFT的变换,得到图6的结果,接触力的峰值出现在低频段,而且没有出现高频响应,就说明不存在高频振动问题。
图7换档蜗杆与蜗轮间接触力
对比图7与图5即可知,换档蜗杆与涡轮间接触力与齿扇与齿轮间接触力成一个比例关系。
接触力最大值为108.172N。
图8换档蜗杆与蜗轮间接触力FFT频谱分析
图8与图6的曲线变化规律一致,只是在幅度上有所差异。
图8的含义与图6相同。
图9齿条与齿轮间的接触力
图9为齿条与齿轮间的接触力,考虑了两个回位弹簧的动态阻尼系数之后,得到的接触力有很大的瞬时冲击,最大冲击力85.595N为平稳时的20N的4.2倍。
所以弹簧的瞬时压缩对接触力的影响很大,不能忽略。
图10选档蜗杆与蜗轮间的接触力
图10中,选档蜗杆与蜗轮间的接触力在平稳状态下的值为200N左右。
而由图9得到的齿条与齿轮间平稳时接触力的值为20N左右,两者相差10倍左右。
而观察换档蜗杆与蜗轮间接触力、齿扇与齿轮间接触力时会发现,换档蜗杆与蜗轮间接触力比齿扇与齿轮间接触力小,两者相差3倍。
说明选档蜗杆承受的接触力较大,而换档蜗杆承受的接触力较小。
图11换档蜗杆驱动力矩
图11显示的是换档蜗杆的驱动力矩,这里显示的都是动载荷条件下的驱动力矩,其中最大的驱动力矩为1203Nmm。
最大的动载荷会用于后面的换档蜗杆的ansys静力学分析。
图12选档蜗杆驱动力矩
图12显示的是选档蜗杆的驱动力矩,这里显示的都是动载荷条件下的驱动力矩,其中最大的驱动力矩为736.06Nmm。
最大的动载荷会用于后面的选档蜗杆的ansys静力学分析。
图13一二档回位弹簧的力
图13表示的是一二档回位弹簧的力。
考虑动态阻尼系数时,最大弹簧力可达52N,为平稳时弹簧力的2倍左右。
图14五倒档回位弹簧的力
图14与图13类似,在平稳阶段弹簧力为17N左右。
考虑弹簧动态阻尼系数时,最大弹簧力可达50N左右。
图15轴的轴向线速度
从图15可看出,轴的线速度较大,最大值可达53mm/s。
三齿扇与12齿齿轮有限元分析
3.1分析目的
使用ansys分析软件,对齿轮与齿扇进行静态的接触分析,是非线性的求解。
齿轮的破坏一般是有接触疲劳破坏和弯曲疲劳破坏造成的。
在此分析齿面所受应力和应变的情况。
3.2分析过程
图16齿扇与12齿的三维几何模型图17齿扇与12齿的网格划分
由于齿扇与12齿齿轮的几何模型不规则,不利于网格的划分。
在此对三维几何模型进行适当的处理,处理后的三维模型有利于网格划分,且对应力应变的分析没有影响。
得到的网格如图17。
图18齿扇与12齿的有限元模型
在图18有限元模型中,边界条件为齿扇的圆弧部分施加全约束,在12齿齿轮上施加力矩317.321*12=3807.852Nmm,其中力矩为整个动力学分析过程中最大的转矩(考虑了惯性矩)。
在相互啮合的齿间添加了接触对。
节点数
单元数
单元类型
材料
屈服极限
泊松比
弹性模量
齿扇
22386
19200
Solid185
40Cr
785MPa
0.3
2.1e5
12齿
51127
43932
Solid185
40Cr
785MPa
0.3
2.1e5
图19齿扇与12齿齿轮的等效应力云图
从图19可看出,齿扇与12齿齿轮为双齿啮合,啮合区域位于齿扇齿顶和齿轮齿面中部时,应力最大。
图2012齿齿轮的等效应力云图
由图20的应力云图可测出12齿齿轮所受最大应力为22MPa。
应力集中在齿轮根部以及齿轮中部的接触位置。
图21齿扇的等效应力云图
由图21的应力云图可测出,齿扇所受最大应力为80Mpa,应力集中在齿顶的接触部位。
图22齿扇与12齿齿轮应变云图
图2312齿齿轮应变云图
由图23的应变云图可以看出,在啮合区的齿外侧,应变较大,最大应变为0.000748左右,相当小。
图24齿扇应变云图
从图24可看出,在两个啮合齿的部位应变较大,尤其在齿顶处应变最大,可达0.001123。
3.3结论
根据最大载荷的静力学分析可知齿扇和12齿齿轮所受最大应力均远小于40Cr材料齿轮的接触疲劳强度极限550MPa和弯曲疲劳强度极限450MPa。
此齿轮和齿扇的设计是安全的。
四齿条与17齿齿轮有限元分析
4.1分析目的
使用ansys分析软件,对齿条与齿轮进行静态的接触分析,是非线性的求解。
齿轮的破坏一般是有接触疲劳破坏和弯曲疲劳破坏造成的。
在此分析齿面所受应力和应变的情况。
4.2分析过程
图25齿轮与齿条的三维简化模型
为方便网格的划分,对模型进行简化,可将模型简化为图26所示,并进行有限元网格划分。
图26齿条和齿轮的有限元网格划分
图27齿轮齿条有限元模型
边界条件为齿条内径节点施加全约束,在齿轮上施加力矩85.595*10.625=909.447Nmm,其中力矩为整个动力学分析过程中最大的转矩(考虑了惯性矩,即为动态载荷)。
在相互啮合的齿间添加了接触对。
单元数
单元类型
材料
屈服极限
泊松比
弹性模量
齿条
44372
Solid185
尼龙
150MPa
0.4
6e3
17齿
11625
Solid187
40Cr
785MPa
0.3
2.1e5
图28齿条和齿轮的应力云图
图2917齿齿轮的应力云图及应力集中点
由图29可看出,应力最大处集中在齿根处,最大值达10.737MPa。
而在齿的接触面处应力则相对小一些。
图30齿条的应力云图及应力集中点
由图30的应力云图可测出齿条所受最大应力为13MPa。
应力集中在齿轮中部的接触位置,表现为接触应力。
图31应变云图
图32齿条应变云图
由图32的应变云图可以看出,在齿条齿顶处应变较大,最大应变为0.003132左右,相当小。
图33齿轮应变云图
从图33可看出,在17齿齿轮的轮齿齿顶部分(包括接触区域和非接触区域)应变较大,最大可达0.004597。
4.3结论
根据最大载荷的静力学分析可知齿条和17齿齿轮所受最大应力均远小于40Cr材料齿轮的接触疲劳强度极限550MPa和弯曲疲劳强度极限450MPa和PA66gf15材料的屈服极限。
此齿轮和齿条的设计是安全的。
五选档蜗杆与蜗轮有限元分析
5.1分析目的
使用ansys分析软件,对选档蜗杆和蜗轮进行静态的接触分析,是非线性的求解。
齿轮的破坏一般是有接触疲劳破坏和弯曲疲劳破坏造成的。
在此分析齿面所受应力和应变的情况。
5.2分析过程
图34选档蜗杆和蜗轮的三维几何模型
和此前类似,选档蜗杆和蜗轮的三维几何模型进行适当的简化,使得有利于网格的划分又不影响最终的结果。
对图34的几何模型简化并划分后得到图35所示的网格。
图35选档蜗杆和蜗轮的网格划分
图36选档蜗杆和蜗轮的有限元模型
图36所示的有限元模型的边界条件为蜗轮内径节点施加全约束,在蜗杆上施加力矩736Nmm,其中力矩为整个动力学分析过程中最大的转矩(考虑了惯性矩)。
在相互啮合的齿间添加了接触对。
单元数
单元类型
材料
屈服极限
泊松比
弹性模量
选档蜗轮
44372
Solid185
尼龙
150MPa
0.4
6e3
选档蜗杆
11625
Solid187
40Cr
785MPa
0.3
2.1e5
图37选档蜗杆和蜗轮的应力云图
图38选档蜗杆的应力云图
由图38的应力云图可测出选档蜗杆所受最大应力为224.855MPa。
最大应力出现在蜗杆齿根位置。
图39齿蜗轮的应力云图
由图39的应力云图可测出换挡蜗轮所受最大应力为194.276MPa。
最大应力出现在蜗轮齿根位置。
图40选档蜗杆和蜗轮的应变云图
图41选档蜗杆的应变云图
由图41的应变云图可以看出,在选档蜗轮的齿顶处,应变较大,最大应变为0.482102。
图42齿蜗轮的应变云图
从图42可看出,在选档蜗轮和蜗杆接触的位置应变较大,在齿顶处最大应变为0.064741。
5.3结论
根据最大载荷的静力学分析可知选档蜗杆所受的最大应力远小于40Cr材料蜗杆的接触疲劳强度极限550MPa和弯曲疲劳强度极限450MPa。
换挡蜗轮所受的最大应力超过了尼龙材料的接触疲劳强度极限150MPa,最大应力出现在蜗轮齿根易出现应力集中处,所以在蜗轮齿根处应该采用圆角过渡。
建议设计者在保证选挡蜗杆与蜗轮几何尺寸不干涉的前提下,增大蜗轮齿根的过度圆弧半径(建议半径为0.1mm)。
六换档蜗杆与蜗轮有限元分析
6.1分析目的
使用ansys分析软件,对换挡蜗杆与蜗轮进行静态的接触分析,是非线性的求解。
蜗轮蜗杆传动的破坏一般是由接触疲劳破坏和弯曲疲劳破坏造成的。
在此分析蜗轮蜗杆齿面所受应力和应变的情况。
6.2分析过程
图43换档蜗轮蜗杆模型图44换挡蜗轮蜗杆模型的有限元网格划分
由于换挡蜗轮蜗杆的几何模型不规则,不利于网格的划分。
在此对三维几何模型进行适当的处理,处理后的三维模型有利于网格划分,且对应力应变的分析影响很小。
得到的网格如图44。
图45换档蜗轮蜗杆有限元模型
边界条件为换挡蜗轮内径节点施加全约束,在蜗杆上施加力矩359.104*3.35=1203Nmm(动载荷),其中力矩为整个动力学分析过程中最大的转矩(考虑了惯性矩)。
在相互啮合的齿间添加了接触对。
单元数
单元类型
材料
屈服极限
泊松比
弹性模量
换挡蜗轮
67848
Solid185
尼龙
150MPa
0.4
6e3
蜗杆
25747
Solid187
40Cr
785MPa
0.3
2.1e5
图46换挡蜗轮和蜗杆的应力云图
图47换挡蜗杆的应力云图
由图47的应力云图可测出换挡蜗杆所受最大应力为190.343MPa。
最大应力出现在蜗杆齿顶的接触位置。
图48换挡蜗轮的应力云图
由图48的应力云图可测出换挡蜗轮所受最大应力为147.035MPa。
最大应力出现在蜗轮根部以及中部的接触位置。
图49换挡蜗轮和蜗杆的应变云图
图50换挡蜗杆的应变云图
由图50的应变云图可以看出,在换挡蜗轮的齿顶处,应变较大,最大应变为0.533757。
图51换挡蜗轮的应变云图
从图51可看出,在换挡蜗轮和蜗杆的啮合处应变较大,在齿顶处应变最大为0.077013。
6.3结论
根据最大动载荷条件下的静力学分析可知,换挡蜗杆所受的最大应力远小于40Cr材料蜗杆的接触疲劳强度极限550MPa和弯曲疲劳强度极限450MPa。
换挡蜗轮所受的最大应力小于尼龙材料的接触疲劳强度极限150MPa。
因此,换挡蜗轮蜗杆传动的设计是安全的。