机械加工通用技术要求规范教学文案.docx
《机械加工通用技术要求规范教学文案.docx》由会员分享,可在线阅读,更多相关《机械加工通用技术要求规范教学文案.docx(21页珍藏版)》请在冰豆网上搜索。
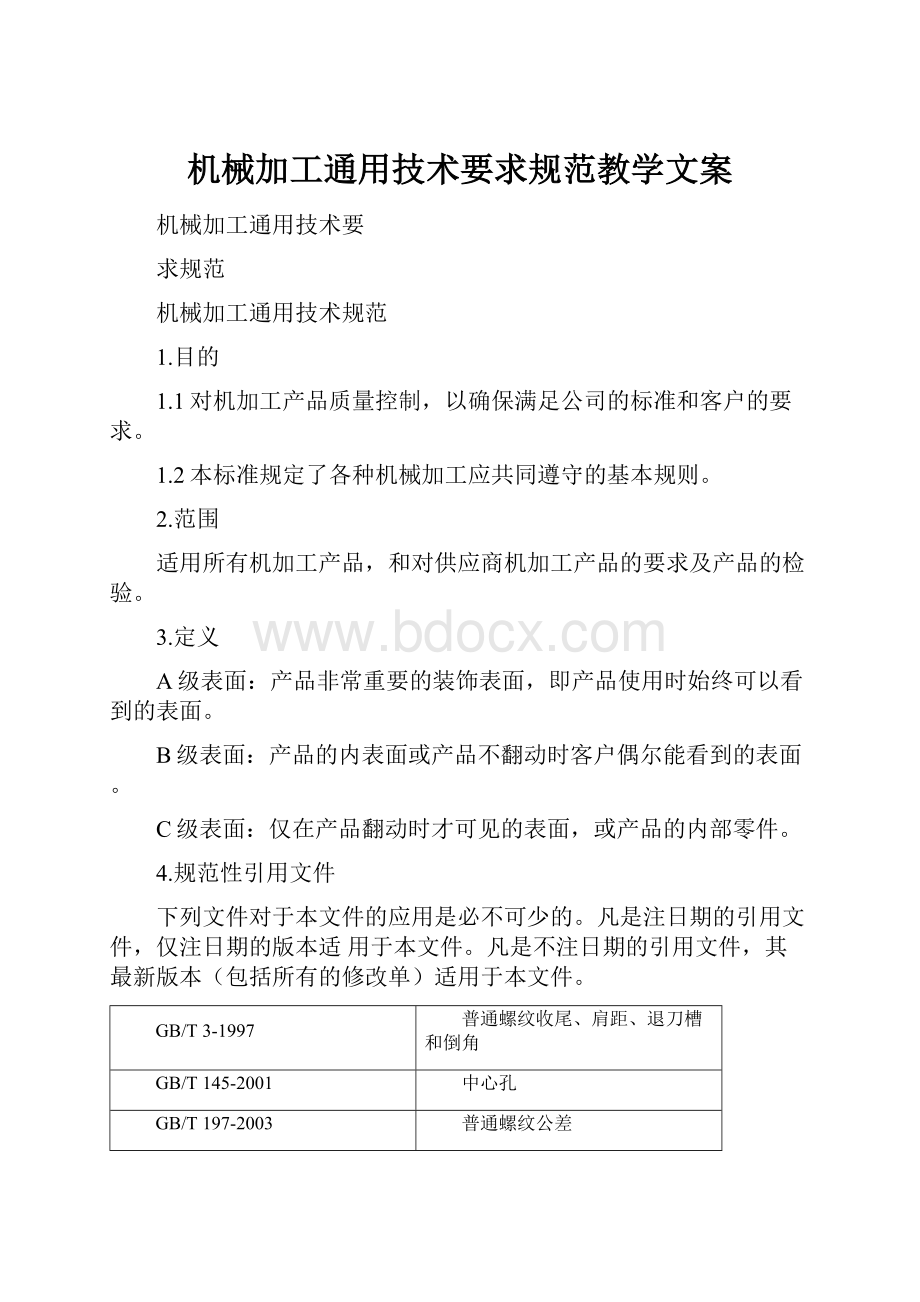
机械加工通用技术要求规范教学文案
机械加工通用技术要
求规范
机械加工通用技术规范
1.目的
1.1对机加工产品质量控制,以确保满足公司的标准和客户的要求。
1.2本标准规定了各种机械加工应共同遵守的基本规则。
2.范围
适用所有机加工产品,和对供应商机加工产品的要求及产品的检验。
3.定义
A级表面:
产品非常重要的装饰表面,即产品使用时始终可以看到的表面。
B级表面:
产品的内表面或产品不翻动时客户偶尔能看到的表面。
C级表面:
仅在产品翻动时才可见的表面,或产品的内部零件。
4.规范性引用文件
下列文件对于本文件的应用是必不可少的。
凡是注日期的引用文件,仅注日期的版本适用于本文件。
凡是不注日期的引用文件,其最新版本(包括所有的修改单)适用于本文件。
GB/T3-1997
普通螺纹收尾、肩距、退刀槽和倒角
GB/T145-2001
中心孔
GB/T197-2003
普通螺纹公差
GB/T1031-2009
产品几何技术规范(GPS)表面结构轮廓法表面粗糙度参数及其
数值
GB/T1182-2008
产品几何技术规范(GPS)几何公差形状、方向、位置和跳动公
差标注
GB/T1184-1996
形状和位置公差未注公差值
GB/T1568-2008
键技术条件
GB/T1804-2000
一般公差未注公差的线性和角度尺寸的公差
GB/T2828.1-2003
计数抽样检验程序第1部分:
按接收质量限(AQL检索的逐批
检验抽样计划
GB/T4249-2009
GB/T5796.4-2005
Q/JSJxx.xx-2012
Q/JSJxx.xx-2012
产品几何技术规范(GPS)公差原则
梯形螺纹第4部分:
公差
不合格品控制程序
机柜半成品钣金件下料技术要求
5.术语和定义
GB/T1182-2008给出的术语和定义及下列术语和定义适用于本文件。
5.1切削加工
用切削工具(包括刀具、磨具和磨料)把坯料或工件上多余的材料层切去成为切屑,使
工件获得规定的几何形状、尺寸和表面质量的加工方法。
包括车削、铣削、刨削、磨削、拉削、钻孔、扩孔、铰孔、研磨、珩磨、抛光、超精加工及由它们组成的自动技术、数控技术、成组技术、组合机床、流水线、自动线。
5.2特种加工
特种加工亦称“非传统加工”或“现代加工方法”,泛指用电能、热能、光能、电化学能、化学能、声能及特殊机械能等能量达到去除或增加材料的加工方法,从而实现材料被去除、变形、改变性能或被镀覆等。
公司现有的特殊加工方法有线切割加工、激光加工、水切割加工。
5.3公差带
有一个或几个理想的几何线或面所限定的、由线性公差值表示其大小的区域。
6.技术要求6.1加工原则
1)“基准先行”原则
基准表面先加工,为后续工序作可靠的定位。
如轴类零件第一道工序一般为铣端面钻中心孔,然后以中心孔定位加工其它表面。
2)“先面后孔”原则
当零件上有较大的平面可以用来作为定位基准时,总是先加工平面,再以平面定位加工孔,保证孔和平面之间的位置精度,这样定位比较稳定,装夹也方便,并可避免粗糙面钻孔引起的偏斜。
3)“先主后次”原则
先加工主要表面(位置精度要求较高的基准面和工作表面)后加工次要表面(如键槽、螺孔、紧固小孔等)。
次要表面一般在主要表面达到一定精度后,最终精加工之前。
4)“先粗后精”原则
对于精度要求较高的零件,按由粗到精的顺序依次进行,逐步提高加工精度。
这一点对于刚性较差的零件,尤其不能忽视。
6.2—般要求
621机械加工件的切削加工和必须符合产品图样,工艺规程和本标准规定。
6.2.2机械加工件的已加工表面,不得有锈蚀及影响性能,寿命和外观的磕碰、戈M伤等缺陷。
6.2.3除了特殊要求外,加工后的零部件不得有尖锐的棱角和毛刺。
6.2.4精加工后的配合面,摩擦面和定位面等工作表面,不得打有损于表面质量的印记。
6.2.5经热处理后的零件,精加工时不得产生退火、烧伤及裂纹等现象。
6.2.6经加工后的零件在搬运、存放时,必须防止受到损伤、腐蚀及变形。
627图样上未注明的倒角应符合表1的规定
表1mm
D(d或
I)
>5〜
510
>10〜30
>30〜
100
>100〜
250
>250〜
500
>500〜
1000
C
0.
0.5
2
1
2
3
4
6
注:
非圆柱面倒角参照选用,其中I为与倒角处有关的尺寸中最小的一个尺寸
628图样上未注注明的倒圆尺寸,如无倾角要求时,应符合表2的规定。
表2mm
D-d
<4
>4〜12
>12〜
30
>12〜
80
>80〜
140
>140〜
200
>200
>10〜
>30〜
>80〜
>260〜
>630〜
D(L)
3〜10
30
80
260
630
1000
>1000
R
0.5
1
2
4
8
12
20
注1:
D值用于盲孔和外端面倒圆。
注2:
非圆柱面倒圆参照选用,其中L为与倒圆处有关的尺寸中最小的一个尺寸。
629图样上未注明倒角,过度圆角的表面粗糙度,应以相连两表中Ra值较大的选取,如
有一面不进行加工时,则应取加工面的Rd值。
6.2.10在成对成组加工的零部件(如滑动轴承的上、下轴瓦,齿轮箱的上下盖等)上,应做出标记.
6.3未注尺寸公差
631未注公差尺寸(不包括倒角和倒圆半径)的极限偏差数值按GB/T1804-2000-m级取
值。
数值见表3的规定。
表3未注公差尺寸的极限偏差数值mm
公差
等级
基本长度范围
0.5〜
3
>3〜
6
>6〜
30
>30〜
120
>120〜
400
>400〜
1000
>1000〜
2000
f
±0.05
±0.05
±0.1
±0.15
±0.2
±0.3
±0.5
m
±0.1
±0.1
±0.2
±0.3
±0.5
±0.8
±1.2
c
±0.2
±0.3
±0.5
±0.8
±1.2
+2
±3
v
—
±0.5
±1
±1.5
±2.5
±4
±6
6.3.2倒角尺寸和倒圆半径的极限偏差数值按GB/T1804-2000-m级取值。
数值见表4的规
表4倒角尺寸和倒圆半径的极限偏差数值mm
公差等级
基本长度范围
0.5〜3
>3〜6
>6〜30
>30
f
±0.2
±0.5
±1
+2
m
c
+0.4
±1
±2
±4
v
633盲孔的钻孔深度,其允许偏差规定如下:
1)孔深不大于50mm的为0〜+3mm
2)孔深大于50mm的为0〜+5mm
6.3.4凡锪平处以最低点测量,锪平深度的极限偏差为0〜+5mm
6.3.5一面为加工面,一面为非加工面的未注尺寸公差的极限偏差应符合下列规定:
仅供学习与交流,如有侵权请联系网站删除谢谢6
1)铸件、锻件及焊接件按相应的非加工未注尺寸公差的极限偏差的70驱土值
2)铸件、锻件的突缘或壁厚允许减薄,当壁厚w10mm寸,其减薄量不得大于壁厚的
20%当壁厚>10mm寸,其减薄量不得大于壁厚的15%.
6.4未注形状公差
641直线度和平面度
图样上未标注的直线度和平面度的公差值按GB/T1184-1996-H级取值,具体公差值见表5
表5mm
基本长度范围
公差等级
w10
>10〜
>30〜
>100〜
>300〜
>1000〜
30
100
300
1000
3000
H
0.02
0.05
0.1
0.2
0.3
0.4
6.4.2圆度、圆柱度的未注公差值
圆度、圆柱度的未注公差值要求见GB/T1184-1996中相关规定6.5未注位置公差
6.5.1平行度
平行度的未注公差值等于给出的尺寸公差值,或是直线度和平面度未注公差值中的相应公差值取较大者。
应取两要素中较长者作为基准,若两要素的长度相等则可选取一要素为基准。
6.5.2垂直度
取形成直角的两边中较长的一边作为基准,较短的一边作为被测要素,若两边的长度相
等则可取其中任意一边作为基准,按GB/T1184-1996-H级取值,垂直度的未注公差值见表6.
表6
mm
公差等级
基本长度范围
<100
>100〜300
>300〜
1000
>1000〜3000
H
0.2
0.3
0.4
0.5
6.5.3对称度
应取两要素中较长的一边作为基准,较短的一边作为被测要素,若两要素的长度相等则
可取其中任意一要素作为基准,按GB/T1184-1996-H级取值,对称度的未注公差值见表7.
注:
对称度的未注公差值用于至少两个要素中的一个是中心平面,或两个要素的轴
线相互垂直。
表7mm
公差等级
基本长度范围
<100
>100〜300
>300〜
1000
>1000〜3000
H
0.5
K
0.6
0.8
1.0
L
0.6
1.0
1.5
2.0
6.5.4同轴度
同轴度的未注公差值未作规定。
在几极限情况下,同轴度的未注公差值可以和表8中规定的径向圆跳动的未注公差值相
等,应取两要素中较长的一边作为基准,若两要素的长度相等则可取其中任意一要素作为基准。
6.5.5圆跳动
对于圆跳动的未注公差值,应以设计或工艺给出的支撑面作为基准,否则应取两要素中
较长的一边作为基准,若两要素的长度相等则可取其中任意一要素作为基准。
按GB/T1184-
1996-H级取值,圆跳动的未注公差值见表8.
表8mm
公差等级
圆跳动公差值
H
0.1
K
0.2
L
0.5
6.5.6垂直要素、倾斜要素由角度公差和直线度或平面度未注公差值分别控制。
6.5.7圆跳动和全跳动的公差值不应大于该要素的形状和位置的未注公差的综合值。
6.5.8任意两螺钉、螺栓孔中心距的极限偏差当图样上未注明时,按表9的规定
表9mm
螺钉或螺
栓中心
距
3〜6
>6〜10
>10〜
18
>18〜
30
>30〜
100
>100〜
200
>200
任意两螺
钉中心
距极限
偏差
±0.12
±0.25
±0.30
±0.50
±0.75
±1.25
±1.50
任意两螺
±0.25
±0.50
±0.75
±1.00
±1.50
±2.50
±3.00
栓中心距
极限偏差
6.6未注公差角度的极限偏差
角度尺寸的极限偏差数值按角度短边长度确定,对圆锥角按圆锥素线长度确定。
角度尺寸的极限偏差数值按GB/T1804-2000-m级取值。
角度尺寸的极限偏差数值见表10.
表10
公差等级
基本长度范围(mr)i
<10
>10〜50
>50〜
120
>120〜
400
>400
f
±1°
±30'
+20'
±10'
+5'
m
c
±1°30'
±1°
±30'
±15'
±10'
v
±3°
+2°
±1°
±30'
+20'
6.7螺纹6.7.1加工的螺纹表面不允许有黑皮、磕碰、乱扣和毛刺等缺陷。
6.7.2螺纹的加工精度和表面粗糙度,当图样上未注明时应按下列规定:
1)普通螺纹精度应按GB/T197-2003规定的6H、6g级。
内螺纹表面粗糙度值为
12.5卩®外螺纹表面粗糙度值为6.3ym
2)梯形螺纹精度应按GB/T5796.4-2005的规定。
内螺纹表面粗糙度值为6.3ym外螺纹表面粗糙度值为3.2ym
6.7.3外螺纹轴线对杆部轴线及内螺纹轴线对孔部轴线的同轴度,分别不大于外螺纹大径及内螺纹大径的尺寸公差1/2.
6.7.4螺纹收尾、肩距、退刀槽和倒角应符合GB/T3-1997的规定。
6.7.5攻制螺孔的轴线对端面的垂直度应按表11的规定。
表11mm
螺纹长度
<10
>10〜
>16〜
>25〜
>40〜
>63〜
16
25
40
63
100
公差值
手攻
0.12
0.15
0.20
0.25
0.30
0.40
机攻
0.08
0.10
0.12
0.15
0.20
0.25
6.8螺纹、孔的检验:
6.8.1采用牙规、塞规检验或用螺钉检验,螺纹的底孔不大于标准底孔的0.1mm
6.8.2图样上未注精度等级的普通螺均按GB197规定:
内螺纹按7H;外螺纹7g加工和
检验;未注明粗糙度的螺纹的粗糙度均为Ra6.3
6.8.3螺纹部分的长度公差按+1.5倍螺距执行
6.8.4螺孔对端平面、螺栓外螺纹对支承平面垂直度匀差按1.2/100加工和检验
6.8.5内螺纹孔口按90°120°倒角,倒角外圆应大于螺纹直径;外螺纹端部按45°倒角,倒角后小径应小于螺纹小径。
6.8.6中心孔
1.中心孔是否保留应在图样上注明,若未注明则认为有无均可,或按工艺规定。
2.中心孔的规格图样上如未注明时按A型(不带护锥)加工和检验。
尺寸见表七。
夷七
料端部昴小百徑
10
12
15
20
25
30
料最大直径
1>10
>1S
>30
>50
>80
>120「
>1SO
最大IS量
120
200
500
SCO
1000
1500
2000
中赴孔賣径
2
2.5
3
4j
5
6
S
6.9零件的检验要全面到位防止不良的产品流入公司造成不必要的损失。
6.8键和键槽
6.8.1键必须符合GB/T1568-2008的规定
6.8.2当键长与键宽之比》8时,键工作面在长度方向的平面度应符合下列规定
1)当键宽w6mm寸,公差等级按7级;
2)当键宽》8〜36mm寸,公差等级按6级;
3)当键宽》40mm寸,公差等级按5级;
4)具体公差数值见表12。
表12mm
键、
键槽长
w10
>10〜
>
>25〜
>40〜
>63〜
>100〜
>160〜
度
16
16
40
63
100
160
250
25
公差
5
公
0.005
0.006
0.008
0.010
0.012
0.015
0.020
0.025
等级
6
差
0.008
0.010
0.012
0.015
0.020
0.025
0.030
0.040
7
值
0.012
0.015
0.020
0.025
0.030
0.040
0.050
0.060
6.8.3未注键槽两工作面平行度的公差应按表12中公差等级7级取值
6.8.4未注键槽的对称度按GB/T1184-1996附录B中表B4中9级取值6.9中心孔
6.9.1图样中未注明、加工中又需要中心孔的零件,在不影响使用和外观的情况下,加工后中心孔可以保留。
6.9.2中心孔应符合GB/T145-2001的规定。
6.10表面粗糙度
图样中未注明表面粗糙度应符合GB/T1031-2009的规定。
4.机加工的要求
4.1机加工件材料要符合图纸,选用的材料符合国家标准
4.2机加工件图纸未注尺寸公差参考国家标准线性尺寸的未注公差GB/T1804-f要求进
行检验。
4.3机加工件图纸未注角度公差参考国家标准角度的未注公差GB/T11335-m要求进行检。
4.4机加工件图纸未注形位公差参考国家标准形位的未注公差GB/T1184-H要求进行检验。
4.5图纸中尺寸标注为配合形式加工的,采用间隙配合,具体要求为:
外配合为配
合为配作对象最大尺寸+0.01~+0.10mm内配合为配作对象最小尺寸-0.10~-0.01。
5.机加工质量的控制
5.1零件加工按照图纸加工,对图纸有标示不清、模糊、错误和对图纸产生疑问的与公司工艺人员联系。
5.2零件加工按照工艺流程去做。
5.3零件加工过程中遇到加工错误或尺寸超出公差范围要与公司工艺人员联系,公司工艺人员将会确认零件可以采用或不可采用。
5.4需要划线加工的零件,加工后不允许有划线的痕迹。
5.5所有机加工的零件要去毛刺、钻孔后要倒角、棱角要倒钝(特殊要求除外)。
5.6两加工面间过度圆角或倒角的粗糙度,按其中较低的执行。
5.7两加工面间的根部,
未要求清根的,其圆角半径均不大于0.5。
5.8零件的配合表面上,除图样及技术文件有规定外,不得刻打印记或作其它不易清除的标记。
5.9图样上未注明锪平深度的,其深度尺寸不作检查,以锪平为限。
5.10碰到零件加工错误不应该擅做主张对零件进行修改,应与公司工艺人员联系获得技术支持。
6.机加工外观的控制
6.1机加工中由于控制不力和操作不当造成机械碰伤、表面划伤的不允许存在A级表
面,允许存在B,C级表面.。
6.2变形、裂纹不允许存在A,B,C级表面。
6.3需要表面处理的零件表面不允许有氧化层、铁锈、凹凸不平的缺陷。
7•机加工质量检验
7.1外观检验:
不允许有翘曲、变形、裂纹、划伤、碰伤、凹凸不平及表面粗糙度符合要求。
7.2材料的检验:
材料厚度符合国家标准。
7.3尺寸及公差的检验:
零件的尺寸和公差符合图纸的要求。
7.4.键槽对称度的检测方法按国家标准GB1958有关规定
检测装蛊示意圏
A.检测方法说明:
基准轴线由V型块摸拟,被测中心平面由定位块模拟,分两步测量。
(1).截面测量,调整被测件使定位块沿径向与平板平行,测量定位块与平板的距离。
再将被测件旋转180度后,重复上述测量,得到该截面上下两对应点的读数差a,则该截面的对
称度误差
f截=ah/(2-h)
(2).长向测量,沿键槽长度方向测量,长向两点的最大读数差即该键槽的斜度。
取以
上两个方向误差的最大值作为该零件的对称度误差。
B.按本规定键槽轴线偏移量换算成对
称度误差并载于表八。
表八
轴或孔的
直径
键槽|
允许偏移
截面检测误差
相当于
GB1134
£md
深h
£
amax=2e
计章值f
W彷
^20
0.12
0.24
^0.053
8—10级
0,027〜
0.053
>75—1^0
WM6
O_1B
0.36
8〜9细
0.031〜
0.040
>150〜
26C
5
0J5
0_50
0_044
$〜9级
0.03〜0.06
7.5检验要求7.5.1凡经机械加工件,由质管部按图样、有关技术文件和本标准进行检验和验收。
零件按工序检查合格后,方可转入下道工序。
7.5.2批量生产或用工装加工的零件必须进行首件检查,主要零件应逐件检查几何形状与尺寸精度。
7.5.3机械加工件的外观按要求进行检验。
7.5.4机械加工件的未注尺寸公差和角度公差要求进行检验。
7.5.5机械加工件的未注形状和位置公差的要求进行检验。
7.5.6机械加工件螺纹的外观、尺寸精度、形位公差、表面粗糙度按要求进行检验。
7.5.7键和键槽的尺寸精度、形位公差按要求进行检验。
7.5.8机械加工件成品经检查合格后,应在明显位置标出质管部的检收标记。
7.5.9械加工件检验合格后才能入库。
8.外协件的一般要求
8.1外协零件毛坯须经检验合格后方可投于加工,在加工过程中如发现有经修补后可以使用的沙眼、缩松、裂纹等缺陷件,应报设计部门同意后再处理。
8.2零件热处理后不再进行加工的表面应清理干净,表面处理后的加工件光泽应均匀一致
9.零件加工时的操作要求
9.1.下料
9.1.1看清下料单上的材质、规格、尺寸及数量等。
9.1.2核对材质、规格与下料单要求是否相符。
材料代用必须严格履行代用手续。
9.1.3查看材料外观质量(疤痕、夹层、变形、锈蚀等)是否符合有关质量规定。
9.1.4将不同工件所用相同材质、规格的料单集中,考虑能否套料。
9.1.5号料
1.端面不规则的型钢、钢板、管材等材料号料时必须将不规则部分让出。
钢材表面上如有不平、弯曲、扭曲、波浪等缺陷,在下料切割和成形加工之前,必须对有缺陷的钢材进行矫正。
2.号料时,应考虑下料方法,留出切口余量。
3.有下料定尺挡板的设备,下料前要按尺寸要求调准定尺挡板,并保证工作可靠,下料时材料靠实挡板。
9.2加工前的准备
9.2.1操作者接到加工任务后,应借领加工所需的产品图样。
922根据产品图样及技术要求,有工艺规程的应看清、看懂,无工艺规程的按通用工艺制定自己的加工工步。
有疑问之处找有关技术人员问清后再进行加工。
9.2.3按产品图样及工艺要求复核工件毛坯或半成品是否符合要求,有问题应找有关人员反
映,待处理后方能进行加工。
9.2.4根据图样中的尺寸以及工艺要求,准备好所需的工、卡、量具以及工艺装备。
对新工
艺装备要熟悉其使用要求,操作方法,且不可随意拆卸或更换零件。
9.2.5加工所需的一切工、卡、量具均放在规定的位置,不得随意乱放,更不能放在机床导轨上。
9.2.6使用设备均应有该类机床的操作合格证才能操作。
9.3刀具与工件的装夹
9.3.1刀具的装夹
1.在装夹各种刀具前,一定要把刀柄、刀杆、导套等擦拭干净。
2.刀具装夹后,应用对刀
装置或试切等方法检查是否正确。
9.3.2工件的装夹
1.在机床工作中上安装夹具时,要擦净其定位基准面,并要找正其与刀具的相对位置。
2.
工件装夹前应将其定位面、夹紧面、垫铁和夹具的定位、夹紧面擦拭干净,且去毛刺3.要
按规定的定位其准装夹工件,若工艺中未规定装夹方法,可自行选择定位基准和装夹方法,选择定位基准应按以下原则:
A)尽可能使定位基准与设计基准重合;
B)尽可能使各加工面采用同一定位基准;
C)粗加工定位基准应昼选择不加工或加工余量比较小的平整平面,而且只能使用一次
D)精加工序的定位基装应是已加工表面;
4.对无专用夹具的工件,装夹时应按以下原则进行校正。
A)对划线工件应按线进行找正;
B)对不划线工件,在本工序后尚需继续加工的表面(二次加工),找正精度应保证下工序有足够的加工余量;
C)对在本工序加工到成品尺寸的表面,其找正精度应小于尺寸公差和形位公差的
1/3;D)对在本工序加工到成品尺寸的未注尺寸公差(俗称自由公差),应按照
GB/T1804-92,IT12标准执行。
5.夹紧工件时,夹紧力的作用点应通过支承点或支承面,对刚性较