发酵工厂设计终极版.docx
《发酵工厂设计终极版.docx》由会员分享,可在线阅读,更多相关《发酵工厂设计终极版.docx(37页珍藏版)》请在冰豆网上搜索。
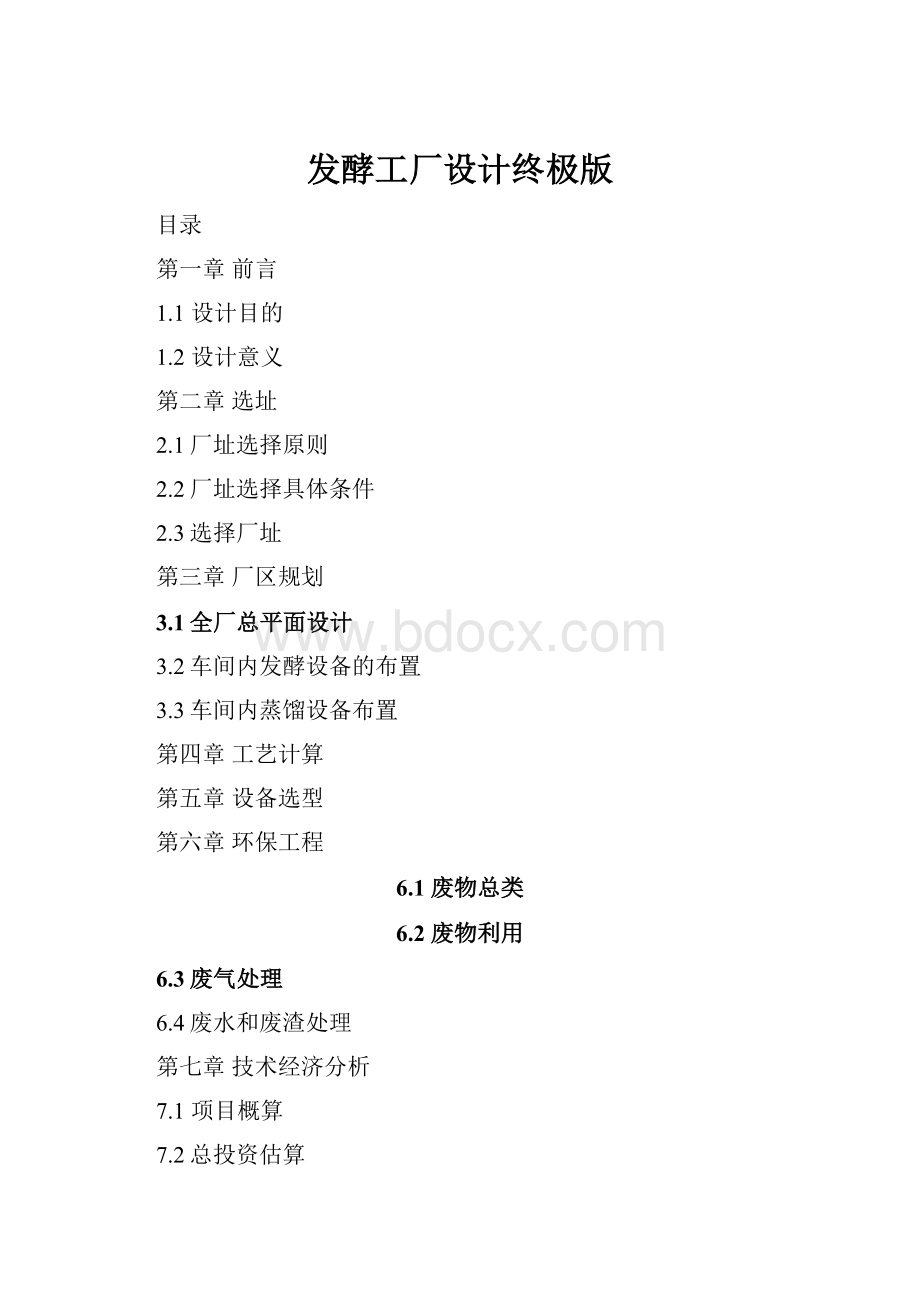
发酵工厂设计终极版
目录
第一章前言
1.1设计目的
1.2设计意义
第二章选址
2.1厂址选择原则
2.2厂址选择具体条件
2.3选择厂址
第三章厂区规划
3.1全厂总平面设计
3.2车间内发酵设备的布置
3.3车间内蒸馏设备布置
第四章工艺计算
第五章设备选型
第六章环保工程
6.1废物总类
6.2废物利用
6.3废气处理
6.4废水和废渣处理
第七章技术经济分析
7.1项目概算
7.2总投资估算
正文
第一章前言
1.2设计意义:
随着经济的发展,究竟这种重要的工业原料被广泛用于化工、塑料、橡胶、农药、化妆品及军工等工业部门。
且石油资源趋于缺乏、全球环境污染的日益加剧,各国纷纷开始开发新型能源。
燃料乙醇是目前为止最理想的石油替代能源,它的生产方法以发酵为主。
菌种的优劣对发酵效果的影响非常大,能够筛选出具有优良性状的菌株及对菌株进行改良,对于降低生产成本,乃至实现酒精的大规模工业化生产,解决能源危机都有着重大意义。
在我国石油年消费以13%的速度增长,2004年进口原油量超过1亿吨,是世界第二大的石油进口国。
我国燃料乙醇起步虽然较晚,但发展迅速,以成为继巴西美国之后世界第三大燃料乙醇生产国。
2001年4月,原国家计委发布了中国实施车用汽油添加燃料乙醇的相关办法,同时国家质量技术监督局颁布了“变性燃料乙醇”和“车用燃料乙醇汽油”2个国家标准。
作为试点,国家耗资50余亿元建立4个以消化“陈化粮”为主要目标的燃料乙醇生产企业。
2006年,我国燃料乙醇生产能力达到102万t,已实现年混配1020万t燃料乙醇汽油的能力。
2002年车用汽油消耗量占汽油产量的87.9%,如果按10%比例添加生产燃料酒精换算,需要燃料酒精381万吨,而全年酒精总产量仅为20.7万吨,如果在不久将来,能用燃料酒精替代500万吨等量的汽油,就可以为我国节省外汇15亿美元。
在目前中国人均石油开采储量仅为2.6吨的低水平条件下,开发新能源成为社会发展,推动经济增长的动力,燃料酒精作为国家战略部署的新型能源之一,在我国具有广阔的市场前景。
第二章选址
③交通运输条件:
交通便利
④协作条件
2.3选择厂址
根据以上原则及要求,我们选择浙江省衢州市龙游县
依据:
交通便利,空气清洁,无污染,水质好,水源丰富,原料(生产糖蜜的厂家)丰富
衢州市位于浙江省西部,钱塘江上游,东与金华、丽水、杭州三市相交,南接福建,西连江西,北邻安徽,是闽浙赣皖四省边际中心城市,公路、铁路交错纵横,水运、空运发达,交通便利,素有“四省通衢”之称。
同时衢州森林覆盖率达70%,环境优美,闲置土地资源丰富。
而且龙游县为了招商引资,提供了一系列优惠政策,工业用地价格为6万元/亩,工业用电价格平均0.76元/度,工业用水1.1元/吨,五年内企业所得税全额补贴,所以,该地适合建厂。
第三章厂区规划
3.1全厂总平面设计
厂区总平面的布置采用联合式布置形式。
生产车间集中建在厂区西南侧,属下风向,这样有利于物料的运输,节省管子材料。
锅炉房配电站在厂区中央,有利于向各个部门输配电及供热,但热电厂和锅炉间则建在厂区最西侧。
职工宿舍远离车间,在上风向。
厂区周围设有花草,美化环境。
3.2车间内发酵设备的布置
由于酒精发酵周期长,发酵罐数量较多,发酵罐间的距离为4.0m,离墙的距离应大于1m,每两列发酵罐间应留有足够的人行通道和操作面,距离为3.0m。
发酵罐用水泥支座落地安装,罐底有出料阀门,罐底离地面距离1.2m。
3.3车间内蒸馏设备布置
蒸馏设备为半露天布置。
车间为一层,把较低的塔设备置于车间内,基本上处于一条线,再沸器、分凝器、预热器、泵等小设备也放在车间内。
较高的塔露天布置,其中包括醪塔、精馏塔。
塔顶布置一组冷凝器,利用重力回流,节省能源消耗,同时也节约厂房造价。
塔与塔的间距为2m以上,塔距墙为1m以上。
塔的人孔尽可能朝同一方,人孔的中心高度距楼面为1m左右。
塔的视镜也尽可能朝同一方向。
。
车间或部门的组成
车间
内容
生产车间
发酵车间,蒸馏车间
动力车间
锅炉房、水泵房、变电房
辅助车间
机修、污水处理站
仓库
原料、成品
公共设备
食堂、宿舍、医务所、车库、门卫、办公室
第四章工艺计算
第二章生产流程的确定
2.1工艺指标和基础数据
1、生产规模:
50000t/a
2、生产方法:
单浓度连续发酵、差压式二塔蒸馏、吸附脱水技术
3、生产天数:
每年250天
4、酒精日产量:
200t
5、酒精年产量:
49998t
6、副产品年产量:
次级酒精占酒精总量的2%
7、杂醇油量:
为成品酒精量的0.3%
8、产品质量:
燃料酒精[乙醇含量为99.5%(v/v)]
9、糖蜜原料:
含可发酵性糖50﹪
10、发酵率:
90﹪
11、蒸馏率:
98﹪
12、发酵周期:
48小时
13、发酵温度:
28~34℃
14、硫酸铵用量:
1Kg/t糖蜜
15、硫酸用量:
5Kg/t糖蜜
16、酒精质量标准根据国家标准生产(见表1-1)
表1-1无水酒精质量标准GB678—90
检验项目
计量单位或符号
产品等级
优级
分析
化学
乙醇
%(V/V)≥
99.8
99.7
99.5
密度(20℃)
g/ml
0.789-
0.791
0.789-
0.791
0.789-
0.791
与水混合试验
合格
蒸发残渣
%
0.0005
0.001
0.001
水份
%(v/v)
0.2
0.3
0.5
酸度
mmol/100g
0.02
0.04
0.1
碱度(以OH计)
mmol/100g
0.005
0.01
0.03
甲醇
%
0.02
0.05
0.2
异丙醇
%
0.003
0.01
0.05
羰基化合物(以CO计)
%
0.003
0.003
0.005
还原高锰酸钾物质(以O计)
%
0.00025
0.00025
0.0006
外观
清澈透明
易碳化物质
合格
2.2工艺流程
1、原料的预处理包括添加絮凝剂、静止澄清、加酸等过程;
2、糖蜜稀释采用连续稀释;
3、酵母菌发酵
4、分离纯化本
5、生产工艺流程图(见图2-1)
第三章工艺计算
3.1物料衡算
3.1.1原料消耗量计算(基准:
1吨无水乙醇)
1、糖蜜原料生产酒精的总化学反应式为:
C12H22O11+H2O→2C6H12O6→4C2H5OH+4CO2↑
342360184176
X1000
2、生产1000Kg无水酒精的理论蔗糖消耗量:
1000×(342÷184)﹦1858.7(㎏)
3、生产1000Kg燃料酒精(燃料酒精中的乙醇99.5%(V)以上,相当于99.18%(m))的理论蔗糖消耗量:
1858.7×99.18%﹦1843.5(㎏)
4、生产1000Kg燃料酒精实际蔗糖消耗量(生产过程中蒸馏率为98﹪,发酵率为90﹪):
1843.5÷98﹪÷90﹪﹦2090(㎏)
5、生产1000Kg燃料酒精糖蜜原料消耗量(糖蜜原料含可发酵性糖50%):
2090÷50﹪=4180(Kg)
6、生产1000Kg无水酒精量(扣除蒸馏损失生产1000kg无水酒精耗糖蜜量为):
1858.7÷90﹪÷50﹪=4130.4(kg)
3.1.2发酵醪量的计算:
酒母培养和发酵过程放出二氧化碳量为:
单浓度酒精连续发酵工艺,把含固形物88﹪的糖蜜稀释成浓度为25﹪的稀糖液经连续稀释器可得稀糖液量为:
4180×85﹪/25﹪=14212(kg)
即发酵醪量为:
14212kg
酒母繁殖和发酵过程中放出968Kg的二氧化碳,且酒精捕集器稀酒精为发酵醪量的6﹪,则蒸馏发酵醪的量为:
(14212-968)×(1.00+6﹪)=14039(kg)
蒸馏发酵成熟醪的酒精浓度为:
3.1.3成品与废醪量的计算
糖蜜原料杂醇油产量约为成品酒精的0.25~0.35﹪,以0.3﹪计,则杂醇油量为1000×0.3﹪=3(kg)
醪液进醪温度为t1=55℃,塔底排醪温度为t4=85℃,成熟醪酒精浓度为B1=7.14﹪,塔顶上升蒸汽的酒精浓度50﹪(v)即42.43﹪(w),生产1000Kg酒精则
醪塔上升蒸汽量为:
V1=14039×7.14﹪÷42.43﹪=2363(kg)
残留液量为:
WX=14039-2363=11676(kg)
成熟醪量比热容为:
C1=4.18×(1.019-0.95B1)
=4.18×(1.019-0.95×7.14﹪)
=3.98[KJ/(Kg·K)]
成熟醪带入塔的热量为:
Q1=F1C1t1=14039×3.98×55=3.08×106(KJ)
蒸馏残液内固形物浓度为:
蒸馏残留液的比热:
塔底残留液带出热量为:
查附录得42.43﹪酒精蒸汽焓为2045KJ/Kg。
故上升蒸汽带出的量为:
塔底真空度为-0.05MPa(表压),蒸汽加热焓为2644KJ/Kg,又蒸馏过程热损失Qn可取传递总热量的1﹪,根据热量衡算,可得消耗的蒸汽量为:
若采用直接蒸汽加热,则塔底排出废醪量为:
11676+2542=14218(kg)
3.1.4年产量为1万吨燃料酒精的总物料衡算
工厂年开工为250天。
日产产品酒精量:
10000/250﹦40(t)
每小时酒精量:
40×1000÷24=1667(Kg)=1.667(t)
实际年产量(次级酒精忽略不计):
1.667×24×250=10002(t/a)
主要原料糖蜜用量:
日耗量:
4180×40==167200(kg)=167.2(t)
年耗量:
167.2×250=41800(t)
每小时产次级酒精:
1667×(2÷98)=34.02(kg)
实际年产次级酒精:
34.02×24×250=204120(Kg)=204.12(t/a)
表3-1200000t/a糖蜜原料酒精厂物料衡算表
物料衡算
生产1000Kg99.5%酒精物料量
每小时
(Kg)
每天
(t)
每年
(t)
燃料酒精
1000
1667
40
10002
糖蜜原料
4180
6967
167.2
41800
次级酒精
20
33.34
0.8
200
发酵醪
14212
23687.8
568.48
142120
蒸馏发酵醪
14039
23399.45
561.56
140390
杂醇油
3
5
0.12
30
二氧化碳
968
1613.4
38.72
96800
醪塔废醪量
14218
23701.4
568.7
142178.6
3.1.5稀释工段的物料衡算物料衡算
糖蜜稀释用水量(以每生产1000kg酒精计算)
稀释成25﹪稀糖液用水量为:
W1=14212-4180=10032(kg)
则生产1万吨酒精每小时需要稀释用水量:
10032×1677÷1000=16723.4(kg/h)
生产1万吨酒精一年需要的稀释用水量:
10032×10000=1.0032×108(t/a)
营养盐添加量:
选用氮量21﹪的硫酸铵作为氮源,每吨糖蜜添加1Kg,则每生产1000kg酒精:
硫酸铵年耗量为:
41800×1=41800(kg/a)=41.8(t/a)4.18t4.18kg
41800t
日耗量:
41800÷250=167.2(kg/d)
每小时耗量:
167.2÷24=7(kg/h)
则生产1万吨酒精一年需要硫酸铵用量:
41.8×10000=4.18×105(t/a)
3、硫酸用量]
稀释酒母稀糖液用酸5Kg/t糖蜜:
年用量:
41800×5=20900(kg/a)=20.9(t/a)
日用量:
20900÷250=83.6(kg)
每小时用量:
83.6÷24=3.5(kg/h)
则生产1万吨酒精硫酸铵一年用量:
20.9×10000=2.09×105
表3-2稀释工段各物料用量(5万吨产量计算)
物料
用量(t/a)
糖蜜稀释用水量
1.0032×108
营养盐添加量
4.18×105
硫酸用量
2.09×105
3.2热量衡算
3.2.1发酵工段
现生产10000t/a,要每小时投入糖蜜量6967kg/h,则无水酒精量为:
6867×1000÷4130.4=1686.76(kg/h)
以葡萄糖为碳源,酒母发酵每生成1kg酒精放出的热量约为1170KJ左右,则发酵和培养酒母每小时放出的热量为:
Q=1170×1667=1.97×106(KJ/h)
发酵酒母冷却水初
=20℃,终温
=27℃,平均耗水量为:
酒母酒精捕集用水为:
(待蒸馏发酵醪液量为F=23399.45kg/h)
5﹪F÷1.06=5﹪×23399.45÷1.06=1103.7(kg/h)
发酵洗罐用水为:
(每15天洗一次)
2﹪F÷1.06=2﹪×23399.45÷1.06=441.5(kg/15天)
则在发酵工段总用水量W发酵工段=1103.7+441.5+67327.4=68872.6(kg/h)
3.2.2蒸馏工段
按采用差压蒸馏两塔流程计算,进醪塔浓度为7.14﹪,出醪塔酒精蒸汽浓度为50﹪.
1、醪塔
图2-1醪塔的物料和热量平衡图
醪液预热至55℃,进入醪塔蒸馏,酒精质量分数为7.14﹪,沸点92.4℃,取上升蒸汽浓度为50﹪(v),即42.43﹪(w)。
塔顶温度75℃,塔底温度85℃。
则塔顶上升蒸汽热焓量i1=2045kJ/kg。
加热蒸汽取0.05MPa绝对压力,则其热焓量I1=2644KJ/kg。
总物料衡算:
即
2-1
酒精衡算式:
2-2
式中:
xF1—成熟发酵醪内酒精含量[﹪(W)],xF1=7.14﹪。
y1—塔顶上升蒸汽中酒精浓度[﹪(W)],y1=42.43﹪。
XW1—塔底排出废糟内的酒精浓度[﹪(W)],塔底允许逃酒在0.04﹪以下,取xW1=0.04﹪。
热量衡算式:
2-3
设CF1=3.98KJ/(kg·h),CW=4.04KJ/(kg·k),Ce=4.18KJ/(kg·k),并取热损失Qn1=1﹪D1I1,tF1=55℃,tW1=85℃,F1=23399.45(kg/h)
联解2-1、2-2、2-3求得
V1=3914.45(kg/h),Wx=19485(kg/h),D1=5063(kg/h)
一般醪塔采用直接蒸汽加热,塔底醪排出量为:
G1=WX+D1=19485+5063=24548(kg/h)
表3-3年产1万吨酒精厂蒸馏工段醪塔物料热量汇总表
进入系统
离开系统
项目
物料(kg/h)
热量(kJ/h)
项目
物料(kg/h)
热量(kj/h)
成熟醪
F1
23399.45
F1CF1tF1
3.05×107
蒸馏残液
WX
19485
WXCWtW1
2.8×107
加热蒸汽
D1
5063
D1I1
1.34×107
上升蒸汽
V1
3914.45
V1i1
8×106
加热蒸汽
D1
5063
D1tW1Ce
7.57×106
热损失
Qn1
1.34×105
累计
28462.45
4.39×107
累计
28462.45
4.37×107
2、精馏塔
塔顶温度105℃,塔底130℃,进汽温度130℃,出塔浓度为96﹪(v),即93.84﹪(w)。
出塔酒精量为:
P=1667×99.18/93.84=1761.9(kg/h)
每小时醛酒量因为醛酒占出塔酒精的2﹪,则每小时的醛酒量为:
A=2﹪×1761.9=35.24(kg/h)
(3)P′=P–A=1761.9-35.24=1726.66(kg/h)
图2-2精馏塔的物料和热量衡算图
在精馏塔中,塔顶酒精蒸汽经粗馏塔底再沸器冷凝后,除回流外,还将少量酒精送到洗涤塔再次提净。
据经验值,此少量酒精约为精馏塔馏出塔酒精的2%左右,则其量为:
Pe=P,×2%=1726.66×2%=34.5(kg/h)
酒精被加热蒸汽汽化逐板增浓,在塔板液相浓度55﹪(v)出汽相抽取部分冷凝去杂醇油分离器,这部分冷凝液称杂醇油酒精,数量为塔顶馏出塔酒精的2﹪左右,其中包括杂醇油m0=0.3﹪(P′+A)=5.3(kg/h),故H=(P′+Pe)×2﹪=(1726.66+34.5)×2﹪=35(kg/h)
在杂醇油分离器内约加入4倍水稀释,分油后的稀酒精用塔底的蒸馏废水经预热到tH=80℃,仍回入精馏塔,这部分稀酒精量为:
H′=(1+4)H–m0=5H–m0=5×35-5.3=169.7(kg/h)
(6)物料平衡:
F2+D2+H′=P′+Pe+H+D3+W’x
则:
W’x=F2+H′-P′-Pe-H
=3914.45+169.7-1726.66-34.5-35
=2287.99(kg/h)
(7)热量平衡:
=
式中R—精馏塔回流比一般为3~4,取3
I2—精馏塔加热蒸汽热含量,0.6Mpa绝对压力,I2=2652(kJ/h)
tH—为回流稀酒精进塔温度tH=80℃
CH—为杂醇油分离器稀酒精比热,稀酒精浓度为:
,
查得起比热为CH=4.43KJ/(kg·k),75.2﹪—为杂醇油酒精的重量百分浓度,与液相浓度55﹪(v)相平衡。
tP—出塔酒精的饱和温度(78.3℃)
CP—出塔酒精的比热,应为2.80[kJ/(kg.K)]
i2—塔顶上升蒸汽热含量,i2=1163.2(kJ/kg)
iH—杂醇油酒精蒸汽热含量,应为iH=1496(kJ/kg)
tw2—精馏塔塔底温度,取130℃
Cw取4.04KJ/(kg·k)
Qn2—精馏塔热损失,Qn3=2%D2I2
CF2—进塔酒精的比热,取CF3=4.16(kJ/kg)
tF2—进料温度,取90℃
W’x上面算得2287.99kg/h
计算可得:
D2=2243(kg/h)
塔底排出的废水:
G=D2+W,x=2243+2287.99=4530.99(kg/h)
计算蒸馏工段的蒸馏效率:
表2-4年产1万吨酒精工厂蒸馏工段精馏塔物料热量衡算汇总表
进入系统
离开系统
项目
物料(kg/h)
热量(kJ/h)
项目
物料(kg/h)
热量(kj/h)
脱醛液
F2
3914.45
F2CF2tF2
5.9×106
96﹪酒精
P′
1726.66
P′CPtP
1.69×106
加热蒸汽
D2
2243
D2I2
5.9×106
次级酒精
Pe
34.5
—
—
稀酒精
169.7
CHtH
2.65×105
杂醇油酒精蒸汽
H
35
HiH
0.52×105
回流液
—
—
R(Pe+P`)Cptp
5.2×106
蒸馏废水
Wx+D2
4530.99
(Wx+D2)tW2Cw
7.37×106
上升蒸汽
—
—
(R+1)
(Pe+P`)i2
8.2×106
热损失
—
—
Qn2
0.12×106
累计
6327.15
1.72×107
累计
6327.15
1.74×107
3.3供水衡算
利用酒母发酵的冷却废水进行冷却,这样可以节省冷凝水用量。
3.3.1精馏塔分凝器冷却用水
精馏塔分凝器热量衡算有:
(R2+1)(P′+Pe)i2=W精馏CW(
-tH3)
W精馏分凝
精馏塔回流比R为3
塔顶上升蒸汽热焓i2=1163.2KJ/kg
冷却水进出口温度tH3、
,取tH3=20℃,
=85℃
Cw取4.04kj/kg
则精馏塔冷凝器冷却用水为:
W精馏分凝=31204.59kg/h
3.3.2成品酒精冷却和杂醇油分离器稀释用水
成品酒精冷却使用20℃的河水,根据热量衡算,耗水量为:
CP为成品酒精比热容为2.90KJ/(kg·K)
、
为成品酒精冷却前后的温度,分别为78.3℃、30℃
、
为冷却水进出口温度,分别为20℃、40℃
Cw=4.04KJ/(kg·K)
则成品酒精冷却水用量为:
W成品=2993.23kg/h
在杂醇油分离器内加入4倍的水稀释,则稀释用水量为:
W杂醇油分离=4H=4×35=140kg/h
3.3.3总用水量
蒸馏车间总用水量为:
W蒸馏工段=W精馏分凝+W成品+W杂醇油分离=34337.82(kg/h)
表3-1各工段用水量及总用水量
工段
稀释工段
发酵工段
蒸馏工段
用水量(kg/h)
16723.4
68872.6
34337.82
总计(kg/h)
119933.82
3.4其他衡算
3.4.1供气衡算
由前面计算所得数据可知蒸馏工段蒸汽消耗:
D=D1+D2
=5063+2243=7306(kg/h)
年耗蒸汽量为:
7306×24×250=43836(t)
酒精厂平均蒸汽用量:
酒精厂每小时平均蒸汽消耗量主要供给蒸馏工段,因此其消耗量由蒸馏量和损失组成,蒸汽总损失取蒸馏工段蒸汽消耗量的4%,则锅炉需要蒸发量为:
7306×(100﹪+4%)=7598.24kg/h
使用热值为4000大卡的煤,假设锅炉效率为80%,则每吨煤能供生产使用50t新鲜蒸汽,则连续蒸馏煤消耗量为:
7598.24÷50000÷80﹪=0.189(t/h)
本设计选用的锅炉为工业中压(1.47—5.88Mp)中型(20—75t)的煤粉锅炉型号为YG80/3.82—M7蒸发量为80t/h,额定温度为450℃
3.4.2供电衡算
根据我国糖蜜酒精连续发酵工艺技术指标[9],设生产每吨酒精耗电40度,可估算酒精厂的用电:
40×10000=4×105(度/年)=1600(度/日)
考虑到此值为估算值,所以乘以一个富裕系数为120﹪:
1600×120﹪=1920(度/日)=4.8×105(度/年)
第六章设备计算
4.1发酵设备设计
采用连续发酵方式,根据物料衡算结果可知,每小时进入发酵罐的醪液体积流量为:
23687.8kg/h,密度为1200kg/m3[14]。
进入种子罐和1号发酵罐的醪液体积流量为W:
23687.8/1200=19.7=20m3/h
4.1.1发酵罐容积和个数的确定
(1)种子罐个数的确定:
为保证种子罐有足够种子,种子罐内醪液停留时间应在12h左右,则种子罐有效容积为:
V=20×12=240(m3)
取种子罐装料经验系数为80﹪,则种子罐全容积为:
V全=V/u=240/80%=300m3取300m3
每个罐的容积为150m3,则种子罐个数为:
300/150=2(个)
(2)发酵罐体积。
根据发酵罐现在的设备情况,从100m3到500m3,现在酒精厂一般采用300m3,按照有关情况和指导老师建议,我采用300m3,取H=2D,h1=h2=0.