铅冶金.docx
《铅冶金.docx》由会员分享,可在线阅读,更多相关《铅冶金.docx(44页珍藏版)》请在冰豆网上搜索。
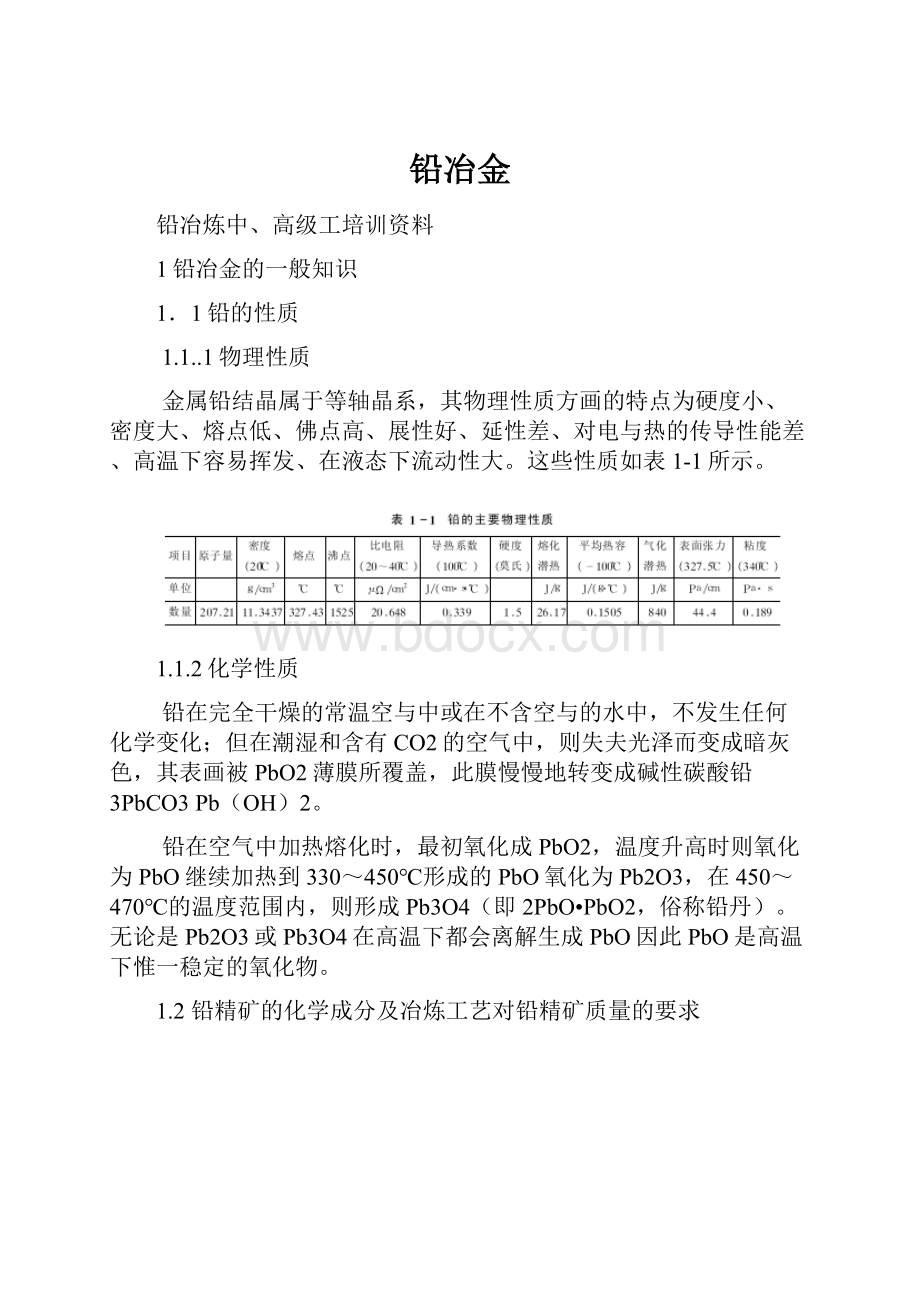
铅冶金
铅冶炼中、高级工培训资料
1铅冶金的一般知识
1.1铅的性质
1.1..1物理性质
金属铅结晶属于等轴晶系,其物理性质方画的特点为硬度小、密度大、熔点低、佛点高、展性好、延性差、对电与热的传导性能差、高温下容易挥发、在液态下流动性大。
这些性质如表1-1所示。
1.1.2化学性质
铅在完全干燥的常温空与中或在不含空与的水中,不发生任何化学变化;但在潮湿和含有CO2的空气中,则失夫光泽而变成暗灰色,其表画被PbO2薄膜所覆盖,此膜慢慢地转变成碱性碳酸铅3PbCO3Pb(OH)2。
铅在空气中加热熔化时,最初氧化成PbO2,温度升高时则氧化为PbO继续加热到330~450℃形成的PbO氧化为Pb2O3,在450~470℃的温度范围内,则形成Pb3O4(即2PbO•PbO2,俗称铅丹)。
无论是Pb2O3或Pb3O4在高温下都会离解生成PbO因此PbO是高温下惟一稳定的氧化物。
1.2铅精矿的化学成分及冶炼工艺对铅精矿质量的要求
铅精矿是由主金属铅(Pb)、硫(S)和伴生元素Zn、Cu、Fe、As、Sb、Bi、Sn、Au、Ag以及脉石氧化物SiO2、CaO、MgO、Al2O3等组成。
为了保证冶金产品质量和获得较高的生产效率,避免有害杂质的影响,使生产能够顺利进行,铅冶炼工艺对铅精矿成分有一定要求。
(1)主金属含量不宜过低,通常要求大于40%。
过低,对整个铅冶炼工艺来讲,单位物料产出的金属铅量减少,从而降低了生产效率。
(2)杂质铜含量不宜过高,通常要求小于1.5%。
铜过高,烧结块中铜含量会相应升高,在鼓风炉还原熔炼过程中,所产生的锍量增加:
一则使溶于锍中的主金属铅损失增加,二则易洗刷鼓风炉水套,缩短了水套使用寿命,并易造成冲炮等安全事故。
另外,含铜太高,也易造成粗铅和电铅中铜含量超标。
(3)锌的硫化物和氧化物均是熔点高、粘度大,特别是硫化锌。
如含锌过高,则在熔炼时,这些锌的化合物进入熔渣和铅锍,会使它们熔点升高,粘度增大,密度差变小,分离困难。
甚至因饱和在铅锍和熔渣之间析出形成横隔膜,严重影响鼓风炉炉况,妨碍熔体分离,故锌含量不宜过高,一般要小于5%。
(4)砷、锑等杂质含量也有严格的要求,通常要求AS+Sb小于1.2%,如过高,则经配料烧结后,在鼓风炉中形成黄渣的量会增加,而且金属铅的流失量会相应增大,更严重的是会造成粗铅、阳极铅含砷、锑过高;此外在电解精炼过程中,使铅溶解速度变慢,并且阳极泥难以洗刷干净。
这样既影响电流效率,又影响生产效率。
另外,MgO、Al2O3等杂质会影响鼓风炉渣型,故一般要求MgO<2%,Al2O3<4%。
1.3烧结焙烧—鼓风炉还原熔炼
近10年世界铅矿产量(指铅精矿含铅量)在300×104t/A左右徘徊,生产比较平衡,没有大的起落。
这就意味着目前世界原生铅(从矿石中提取的铅,又称矿产铅)的产量每年波动不大。
据不完全统计,世界上的矿产铅约75%是采用烧结焙烧—鼓风炉熔炼流程生产的,约10%是用铅锌密闭鼓风炉生产的,约15%是用直接熔炼的方法生产的。
该法属传统炼铅工艺。
硫化铅精矿经烧结焙烧后得到铅烧结块,在鼓风炉中进行还原熔炼,产出粗铅。
图1-1为鼓风炉熔炼工艺的原则流程。
用铅锌鼓风炉炼锌的同时产出粗铅也是采用烧结焙烧—(密闭)鼓风炉熔炼方法生产,其炼铅流程与图1-1所示方法基本相同。
烧结焙烧—鼓风炉熔炼法虽然工艺稳定、可靠,对原料适应性强,经济效果尚好。
但该工艺的缺点是烧结烟气SO2浓度低,采用常规制酸工艺难以实现SO2的利用,严重地污染了环境。
此外,烧结过程中产生的热量不能得到充分利用,在原料(制备返粉)多段破碎、筛分时,工艺流程长,物料量大,扬尘点分散,造成劳动作业条件恶劣。
为了改变传统炼铅工艺的这种状况,20世纪80年代以来,许多直接炼铅工艺被引起了广泛兴趣,近年已在工业生产上得到完善与发展。
传统工艺有被硫化铅精矿直接熔炼法完全取代的趋势。
图1-1 硫化铅精矿烧结焙烧一鼓风炉熔炼生产工艺流程
2 硫化铅精矿的烧结焙烧
2.1 硫化铅精矿烧结焙烧的目的
硫化铅精矿的粒度小,大都小于200目(0.074mm),其中除PbS外,还含有其他的金属硫化物和脉石。
在鼓风炉还原熔炼条件下,精矿中的PbS是不能被还原产出金属铅的,所以应预先进行氧化焙烧,使PbS变为PbO。
此外,精矿原料这种细粒物料进鼓风炉处理时,容易被鼓风吹出炉外,或者将炉料中的空隙堵死,使炉料透气性变坏,风难鼓入,熔炼过程难以进行。
所以硫化铅精矿的烧结焙烧是在有大量空气参与下的强氧化过程,其目的是:
①氧化脱硫,使金属硫化物变成氧化物,以便被碳还原,而硫以SO2逸出,以便制酸;②在高温下将粉料烧结成块,以适应鼓风熔炼作业的要求。
2.1.1 烧结焙烧的脱硫率
确定烧结块中残硫多少的原则是按精矿中铜、锌含量来加以控制。
如果铅精矿含Zn高,则焙烧时应尽量把硫除净,使Zn全部变为ZnO,这样可减少ZnS对还原熔炼时的危害。
如果精矿含铜较多(如Cu>1%),便希望焙烧时残余一部分硫在烧结块中,使铜在熔炼时以Cu2S形态进入铅锍,从而提高铜的回收率。
如果烧结块中残硫不够,则在还原熔炼时大部分铜会被还原为金属铜而入粗铅,少量以硅酸铜和亚铁酸铜形态进入炉渣,前者会导致鼓风炉操作上的困难,后者增加了铜的渣损失。
实践证明,当铅锍中含Cu10%~15%时,铜在铅锍中的回收率可达80%~90%。
如果精矿中含Cu、Zn都高,残硫问题只能根据各厂的具体情况而定。
有的工厂首先进行“死焙烧”,使铜和锌的硫化物都变成氧化物,而在鼓风炉熔炼时加入黄铁矿作硫化剂,将铜的氧化物再硫化成为Cu2S,使之进入铅锍,而锌以ZnO形态进入炉渣。
国内铅厂对含Cu、Zn都较高的精矿一般不造铅锍,而是采用“死焙烧”。
这样既免除ZnS的危害,又减少造锍的麻烦和锍处理的费用,同时铅的直收率也得到提高。
我国炼铅厂实践证明,粗铅含Cu2.5%左右时,操作中没有多大困难。
如某厂处理含锌和铜都比较高的精矿时,鼓风炉产出粗铅含Cu达3.5%~4.5%,只要采用高焦高钙炉渣进行熔炼,并维持较高的炉缸温度,操作无多大困难,但铜在粗铅中的回收率为70%~75%。
脱硫率是指焙烧时烧去的硫量与焙烧前炉料中总含硫量的百分比。
铅烧结焙烧的脱硫率一般为70%左右。
脱硫率可按下式计算:
脱硫率=[炉料含硫量-(烧结块残硫量+返粉含硫量)]/炉料含硫量×100%
2.1.2 烧结块的质量要求
烧结块的化学成分应满足还原反应与造渣过程的要求,同时应具有一定的机械强度,在鼓风炉还原熔炼时不致被一定高度的炉料层所压碎;烧结块应为多孔质结构并具有良好的透气性。
烧结块的质量,主要以强度、孔隙度和残硫率三个指标来衡量。
强度测定,通常作落下试验,将烧结块从1.5m的高处,自由落到水泥地面或钢板上,反复三次,一般视裂成少数几块而不全碎成粉为好;或将三次碎后物进行筛分,小于10mm的重量不超过15%~20%,则强度符合要求。
孔隙度在工厂很少测定,质量好的烧结块一般不小于50%~60%,通常凭肉眼判断。
残硫率则根据取样测定,一般要求在2%以下。
2.2 烧结焙烧炉料的准备
为了在生产实践中能顺利地对含铅炉料进行烧结焙烧,并能获得具有孔隙度大和足够强度的烧结块,又能满足鼓风炉熔炼对化学成分的要求,所以烧结焙烧炉料的准备,无论是对烧结焙烧本身,还是对鼓风炉熔炼,都具有很重要的意义。
2.2.1 对炉料化学成分的要求
烧结前进行配料,主要满足S、Pb和造渣组分的要求。
精矿中的硫化物就是焙烧过程的燃料,配料时硫的数量的确定是直接与过程的热平衡和烧结块残硫联系在一起的,过高与过低都会导致过程热制度的破坏以及残硫不符合要求。
烧结料适宜的硫量应当是:
脱硫率一般为60%~75%,欲得残硫1.0%~1.5%的烧结块,则料含S应为5%~7%。
如果S>7%时,则烧结块残硫必然升高而不合要求。
为了使鼓风炉熔炼获得高的生产率、金属回收率以及低的燃料和熔剂消耗,希望尽可能地提高烧结块的含Pb量,但太高会导致熔炼困难,因此,许多工厂将混合炉料中的铅含量提高到45%左右。
在日本有的工厂已将混合料含铅从48%提高到51%,最高达52%。
由于各铅厂原料成分和原料性质的不同,再加上冶炼技术水平的差异,各铅厂选配渣成分就不一样,且差别极大,一般范围(%)是:
SiO220~32,Fe22~30,CaO14~20,Zn8~15。
2.2.2 烧结配料原则及配料计算
烧结配料的一般原则:
(1)根据精矿的来源,确定各种精矿的配比,保证工厂生产在一定时间内能稳定进行,不致经常变动操作制度。
(2)仔细研究精矿的成分及当地熔剂来源,综合分析本厂及外厂的技术指标,选定适当的渣型,力求熔剂消耗最少。
(3)配好炉料的化学成分应能满足焙烧与熔炼的要求,不仅能保证生产过程能顺利进行,还要获得较好的技术经济指标。
确定配料比,应根据精矿和熔剂的化学成分,进行冶金计算,这是一项复杂而又仔细的工作。
下面举例说明一般用代数法进行的冶金计算,比较适合工厂岗位人员。
配料计算的程序是:
(1)根据精矿及其他含铅二次物料(如锌浸出渣)的供应情况,确定各种原料的配用比例,然后根据这些原料的化学成分,计算出混合原料的成分。
(2)根据混合原料成分,选择适合鼓风炉熔炼的渣型,然后根据渣型计算所需熔剂的数量。
(3)根据加入熔剂后炉料的含硫量,计算所需返粉的数量;根据铅含量,计算检验是否还要配鼓风炉水淬渣(返渣)。
2.2.3 炉料组成及配料
烧结炉料主要是由铅精矿、返粉、熔剂(主要是石灰石、铁矿石、石英石等)、杂料(包括烟尘、含铅杂物如浸出渣等)等组成。
一些工厂铅烧结焙烧的炉料组成列于表2-6。
经过配料后的混合料的化学成分列于表2-7。
鼓风炉熔炼造渣所需要的熔剂,一般根据配料计算量全部混入烧结炉料中,这样的烧结块在鼓风炉熔炼时就可以大大提高生产率。
如果所需的熔剂在熔炼时才加入,由于熔剂与烧结块中造渣成分不能相互密切接触而使造渣过程缓慢,过程不均衡而引起熔炼速度下降。
因此,常把熔炼过程所需的熔剂预先与精矿一起配入烧结炉料进行烧结焙烧而产出的烧结块称为自熔烧结块。
在烧结焙烧时,为了稀释炉料中的硫,通常加入大量的返粉,其数量可达精矿数量的2~3倍。
所谓返粉,即为含硫低的烧结焙烧产品,经破碎后返回烧结配料的粉料。
为了稀释炉料中的硫和铅,有时还加入一定量的鼓风炉水淬渣,也有利于改善烧结块的质量。
炉料的含铅量不仅是影响烧结块质量的主要因素之一,也是影响烧结和熔炼技术经济指标的因素。
如果炉料含铅低,焙烧后形成的低熔点硅酸铅量少,则使炉料的结块不好;同时含铅低的烧结块使设备以铅计的生产率低,熔炼含铅低的烧结块时,因渣量增大,铅的损失也就增加,从而提高了产品成本。
为了提高铅精矿的处理量及减少过程中铅的损失,以及为了降低燃料及熔剂的消耗,要尽可能地提高烧结块的含铅量。
但是炉料含铅太高,则在烧结焙烧过程中,容易产生过早烧结,降低烧结块质量。
同时高铅炉料对于吸风烧结机来说,由于产生的易熔物多(如Pb、PbO等),当其流至炉篦时,便会冷却粘结在炉篦上,甚至流入风箱,把风箱堵塞,给生产造成困难;含铅高的烧结块在鼓风炉熔炼时,也会产生一些不利影响,如渣含铅升高,炉结形成机会增多等。
因此,各工厂并不极力追求把烧结炉料品位提得很高。
烧结炉料适宜的含铅量一般为40%~50%。
生产实践证明,在其他条件一定时,合理控制和调节炉料的含硫量与含铅量,是保证烧结块优质高产的途径。
适当配用焦粉是提高烧结块质量的有效方法。
如炉料含铅30%~40%和含硫3%~6%这种偏低的情况下,便会产出强度不高的烧结块,如果在这种炉料中加入焦粉(其量为配料量0.3%~3%),返粉率为60%~65%,便可提高烧结块质量。
当炉料含铅在40%以上,硫在6%以上就可不配焦粉,将返粉提高到70%,同样可以保证过程的热平衡条件和透气性,使烧结块质量提高。
配料时也应考虑到其他杂质的含量:
例如炉料中的ZnO含量最好应使产出的鼓风炉渣含ZnO不超过15%~20%。
MgO含量也应控制在一定范围内。
如果粗铅采用电解精炼,则在配料时应考虑电解精炼时对阳极中锑含量的要求。
烧结炉料的配料方法常见有两种,即仓式配料(也称皮带配料或圆盘配料)法和堆式配料法。
也有联合使用的。
仓式配料法设备简单,占地面积小,便于机械化,我国普遍采用,其最大缺点是很难控制各组分的正确配料比例与数量。
堆式配料法的优点有:
配料比较容易控制,炉料成分均匀;可预先分析炉料成分,准确度高,可大量储存已配好的炉料,使烧结块成分长时间无波动。
缺点是需要在料堆的一端设有为临时改变炉料组成用的补充配料仓,并且占地面积大,使大量精矿不能得到迅速处理。
2.2.4 炉料的混合与制粒
为保证配料后的炉料在烧结前达到最佳湿度,并使其化学成分、粒度和水分的均匀一致,必须对炉料进行良好的混合与润湿。
所谓最佳湿度是指炉料润湿到最大毛细水含量时的湿度。
当炉料达到最佳湿度时其结团作用最大,此时的炉料容积最大,堆密度最小,见表2-8。
表2-8 某些物料的最佳湿度
一般来说,混合料的最佳湿度为5%~7%,如果小于5%,则烧结速度大大下降并得到不坚实的烧结块,若大于7%~8%时,则烧结块残硫增加,质量变坏。
必须指出,混合料的最佳湿度随返料的数量和粒度的增大而降低。
返粉的粒度组成是直接影响烧结炉料粒度及其透气性的重要因素,因此各个工厂根据各自具体条件通过生产实践来确定其粒度组成。
一般控制3~9mm占60%以上,小于3mm的不超过30%,大于9mm应在10%以下。
对熔剂和焦粉成分、粒度的要求见表2-9。
炉料的混合一般采用二次或三次混合,并且多半是混合与润湿同时进行。
在最后一次混合过程中具有制粒作用,从而防止了各组分因密度和粒度不同而发生的偏析现象。
这样就使炉料各组分分配均匀,并大大地改善了炉料的透气性。
生产上广泛采用的混合设备为鼠笼混合机和圆盘混合机,也有采用反螺旋的圆筒混合机。
混合料的制粒,常在圆筒制粒机和圆盘制粒机中进行,目的在于提高炉料的透气性,不论是圆筒还是圆盘制粒机,除将物料滚动成球外,还具有一定的混合作用。
所有不同性质、不同粒度、具有适当润湿程度的物料,都能制成球。
球的强度又由下列因素决定:
①物料的表面性质,一般炉料粒度愈小,则制成的球强度愈大;②炉料的化学及矿物成分:
多种粒级和多种物料制粒,得到的强度最大;③物料湿度,水分过多或过少都影响制粒强度。
根据铅烧结炉料组成的特性,以含水为5%~6%为宜,如果物料在制粒过程中不加水而加造纸废液或其他粘合剂,则可提高制粒强度;④制粒条件,如给料速度、制粒机转速等都直接影响制粒的强度。
实践证明,与不制粒相比制粒烧结焙烧的生产率和烧结块质量都获得很大提高,所以铅厂的炉料一般通过制粒后再进行烧结焙烧。
2.3铅烧结焙烧的生产实践
2.3.1 带式烧结机及其附属设备
烧结焙烧的主要设备是带式烧结机。
带式烧结机又称直线型烧结机,由许多个紧密挤在一起的小车组成。
小车用钢铸成,底部有炉篦,短边设有挡板(即为车帮),挡板的高矮确定料层的厚薄,而长边则彼此紧密相连,因此,由于小车的有效宽度,便形成一个有炉篦的大而长的浅槽,它类似于一条作环形运动的运输带。
烧结料层的厚薄,可通过点火炉前面的刮料板上下移动来调节。
为了补救刮料板将小车炉篦子上的混合料压紧的缺陷,有的把平口刮板改成耙齿形刮板,用来耙松炉料以改善透气性。
炉料的点火系采用悬吊在烧结机上方靠近头部的点火炉进行,点火炉的外壳用钢板制成,内衬耐火砖,燃料可用焦炭、重油和煤气,由于煤气点火炉具有所占面积小、产生的火焰均匀、点火温度容易控制等优点,故在有煤气供应的情况下,多采用煤气点火。
点火温度的高低应根据:
①对于含铅和二氧化硅较高的易熔炉料,点火温度应低;含钙高而含铅低的炉料,则要求点火温度提高;②炉料粒度小,着火容易,点火温度应低;粒度大,温度相应地要提高;③炉料水分多,点火温度要高,否则点不着火;④小车速度快,点火时间短,应提高点火温度。
实践要求点火时间不少于18s,点火温度为900~1000℃左右。
点燃火的炉料小车,不断地通过风箱向前移动,而整个风箱又分成若干个小室,与风机连接的总管串通。
由高速空气流带入的氧同炉料中的各种金属硫化物进行强烈的反应并伴随产生熔化、造渣、粘结和冷却等作用,使炉料氧化并结块,同时产生大量的含有二氧化硫及占炉料质量0.8%~1.5%的烟尘炉气,经单管或多管旋涡除去粗尘后送往收尘及制酸系统。
小车连续往前移动,然后达到烧结机的尾部卸料端。
卸料端的下面,用条钢或钢轨制成间距为40~60mm,倾斜角为35°~45°的条筛,条筛上部安装一台单轴破碎机,其上方设有与收尘装置相连的烟罩,以减少烧结物往下翻落破碎时产生的烟尘飞扬损失和改善现场劳动条件。
载有烧结物料的小车,借烧结机尾部半圆形固定支架或星轮,依次往下翻落,而自动将烧结物料倾出,空载小车则沿风箱下部的倾斜轨道重返烧结机头部大齿轮处,如此周而复始。
2.3.2 烧结机的正常操作及故障处理
2.3.2.1 烧结机的正常操作
烧结机作业包括点火操作、台车速度控制、鼓风制度和床层温度的合理控制等项内容。
(1)点火操作。
点火操作是烧结焙烧的关键操作之一。
点火主要是控制好点火温度和0号风箱负压。
点火温度太高,炉料表面会结壳;温度低,点火层厚度不够。
点火温度控制在900~1000℃比较适合。
0号风箱负压是点火层往下燃烧的动力,一般控制在800~1000Pa。
当点火料层通过点火炉以后,表面红层的厚度占整个点火料层厚度的2/3时,可认为点火效果最佳。
(2)台车速度。
台车的运行速度主要取决于炉料成分、炉料粒度、鼓风量、料层厚度等因素。
在烧结时,车速必须与料层厚度相适应,以保证小车达到最后的鼓风箱时烧结过程已进行完毕。
在生产过程中,一般很少将车速与料层厚度同时改变。
实际烧结过程有两种操作法,即厚料层慢车速与薄料层快车速操作法。
前者的目的是使点火时间延长,又由于料层较厚,热的利用率较好,从而可提高烧结反应带的温度使焙烧及烧结效果好,有利于提高烟气二氧化硫浓度。
后者是为了减少料层的阻力,使空气容易鼓入,有利于防止炉料过早结块,从而提高过程的脱硫率和改善烧结块质量。
在生产实践中,为了提高烧结机的利用率,车速应与垂直烧结速度相适应,避免烧结过早或欠烧,最简单的调节方法是根据烧穿点来调节车速。
在给定的料层厚度情况下,若要保持烧结机上的烧穿点不变,即在保证完全脱硫的前提下垂直烧结速度越快,车速也要加快。
一般小车运行速度控制在1.2~1.5m/min。
(3)垂直烧结速度。
所谓垂直烧结速度,是指烧结焙烧时间除料层厚度之商(V1=h/t)。
而烧结时间又是小车运行速度除从点火到烧穿点的有效长度之商(t=L/V),故垂直烧结速度可以从下式求出:
V1=(h×V)/(L×1000) (mm/min)
式中:
V1为垂直烧结速度(mm/min);V为小车运行速度(mm/min);h为主料层厚度(mm);L为从点火到烧穿点的有效长度(m)。
生产实践中,通常是根据炉料的透气性来选择适当的料层厚度,再根据垂直烧结速度的大小来确定小车的速度。
垂直烧结速度与炉料的物理性质、化学成分、点火温度、进风量以及气体成分等因素有关,其波动范围很大。
反映料层垂直烧透了的位置即为烧穿点(也叫烧透点),它与床层最高烧结温度相对应(一般烧穿点温度在600~800℃,仅测出料面上空温度,并非实际的料层烧穿点温度)。
烧穿点位置的确定,就以烧结床层温度最高点为依据。
在生产实践中,垂直烧结速度一般为10~30mm/min。
(4)鼓风制度。
烧结过程是强氧化过程,需要大量的空气和返回烟气参与反应。
生产实践中,实际空气的消耗量大于理论量,要有一定过量的空气才能使料烧透。
目前,标准的铅烧结的单位鼓风量约为425Nm3/t料。
最适宜的鼓风强度取决于采用哪种烧结混合料,并且要能保证炉料充分脱硫,提高烟气二氧化硫浓度和满足制酸烟气量要求。
鼓风强度小时,透过料层的空气少,烧结速度减慢,同时由于料层的温度不能达到烧结温度,脱硫率也低。
但是,鼓风强度的提高受到额定的风压所限制,风量大则风压增加,风压过大容易造成料层穿孔而跑空风,使烧结过程变坏。
另外,风压过大,小车与风箱滑动轨道之间漏风增大;加大风量,势必造成烟气量膨胀,从而降低烟气二氧化硫浓度,不利于制酸。
料层厚度为330~360mm时,一般控制风箱的风压为4~5.5KPa。
(5)床层温度。
床层温度是指烧结机料层中的实际温度(也称料层温度)。
床层温度在烧结机的不同位置及料层的不同高度均不相同。
在烧结过程中,锌和铁的硫化物容易氧化,但硫化铅的氧化则需要较高的氧势,因此,控制较高的床层温度对烧结过程的脱硫和提高烧结块强度是很必要的。
床层温度通常是难测定的,一般通过床层阻力和烟气温度来判断。
床层温度高,熔融液相层厚,床层阻力相应增加。
2.3.2.2 非正常操作的控制与调整
(1)烧结过程的判断。
影响烧结过程的因素是多方面的,在生产实践中可以根据测量仪表指示、分析化验结果和观察烧结机尾卸料端的现象来判断烧结过程的好坏。
当烧结块成块率高、粉料少或从尾部观察到烧结块垂直断面只有1/3的红层,表明小车到达最末一个风箱时,烧结过程恰好结束,进程控制良好。
反之,如看到烧结块红层厚,烟尘大,或烧结块冷却过快,没什么红尘,或倒出的烧结块块度小,粉料多,都说明作业不正常。
烧穿点也是判断烧结程度正常与否的一个标志,从安装在烟罩内的热电偶测到的温度观察,烧穿点稳定或波动不大,并且烧穿点温度较高,在500~600℃以上,则表明烧结焙烧状况良好;若烧穿点温度过高或过低,烧穿点前移或后移严重,则说明烧结情况不正常。
风箱内的风压是判断作业是否正常、炉料制粒好坏、炉床布料是否均匀的依据。
若风压高,可能是烧结混合料的细颗粒太多或混合料含水分过高或过低。
在生产中,每隔2h取样分析一次返粉含硫,并根据返粉含硫量指导配料。
(2)烧结过程中的工艺故障处理。
烧结焙烧作业不正常往往影响烧结块的质量(如烧结块残硫高,强度低)、烟气二氧化硫浓度和烧结机单位生产率低。
因此应仔细查明原因,及时处理。
结块好而焙烧不好表现为烧结块块度大,但残硫高。
造成原因是炉料含SiO2和铅高,形成大量的易熔相,结果使烧结块强度大,过早烧结而脱硫不好。
焙烧好,结块差,表现为结块块度小,强度低,但残硫不高。
原因是由于炉料中二氧化硅和铅含量低,因而缺少粘结相(硅酸铅)或是点火温度太低,以致过程进行比较缓慢,氧化反应产生的温度不够,使结块不好。
烧结和焙烧都不好,表现为结块不仅块度小,强度低,而且残硫高,其原因是配料不准确,粒度过细,床层阻力大,风量控制不合理,炉料水分控制不当。
水分过湿点不着火,料层厚度和车速配合不当。
烧结机生产率低,造成原因是配料成分控制不当,风机运转不正常,风压太低,风量不足,影响烧结焙烧过程进行的速度,漏风严重,使透过料层的空气量少,小车速度和料层厚度与焙烧速度不相适应。
烧结烟气二氧化硫浓度低,原因是炉料配硫偏低,炉料过干或过湿,或细粒物料太多,床层阻力升高,料层没辅到料,造成跑空车,烟罩控制负压过大,鼓风量太大。
恶性烧结现象表现为烟气二氧化硫浓度低,烧穿点温度低,结块率低并夹有生料、块残硫及返粉含硫高,造成原因是由于配料事故,如主成分严重偏离控制值,点火效果不好,炉料水分过干或过湿,炉篦大面积堵塞,风量控制失调。
2.3.3 烧结机的供风排气
硫化精矿的烧结焙烧是强氧化过程,需要大量空气参与反应,所需理论空气量可通过冶金计算确定。
根据气流透过料层的方式可分为吸风烧结与鼓风烧结。
自1955年澳大利亚皮里港炼铅厂的鼓风烧结投产后,其他厂相继将原吸风烧结焙烧改为鼓风烧结焙烧,并逐步大型化。
在生产实践中,烧结机的鼓风压力为3~6KPa,鼓风强度为15~30m3/(m2·min)。
现代炼铅厂大都采用返烟烧结,即将烧结产出的低浓度SO2烟气返回重用,以提高烟气中SO2浓度。