降低涂装生产线电能消耗.docx
《降低涂装生产线电能消耗.docx》由会员分享,可在线阅读,更多相关《降低涂装生产线电能消耗.docx(36页珍藏版)》请在冰豆网上搜索。
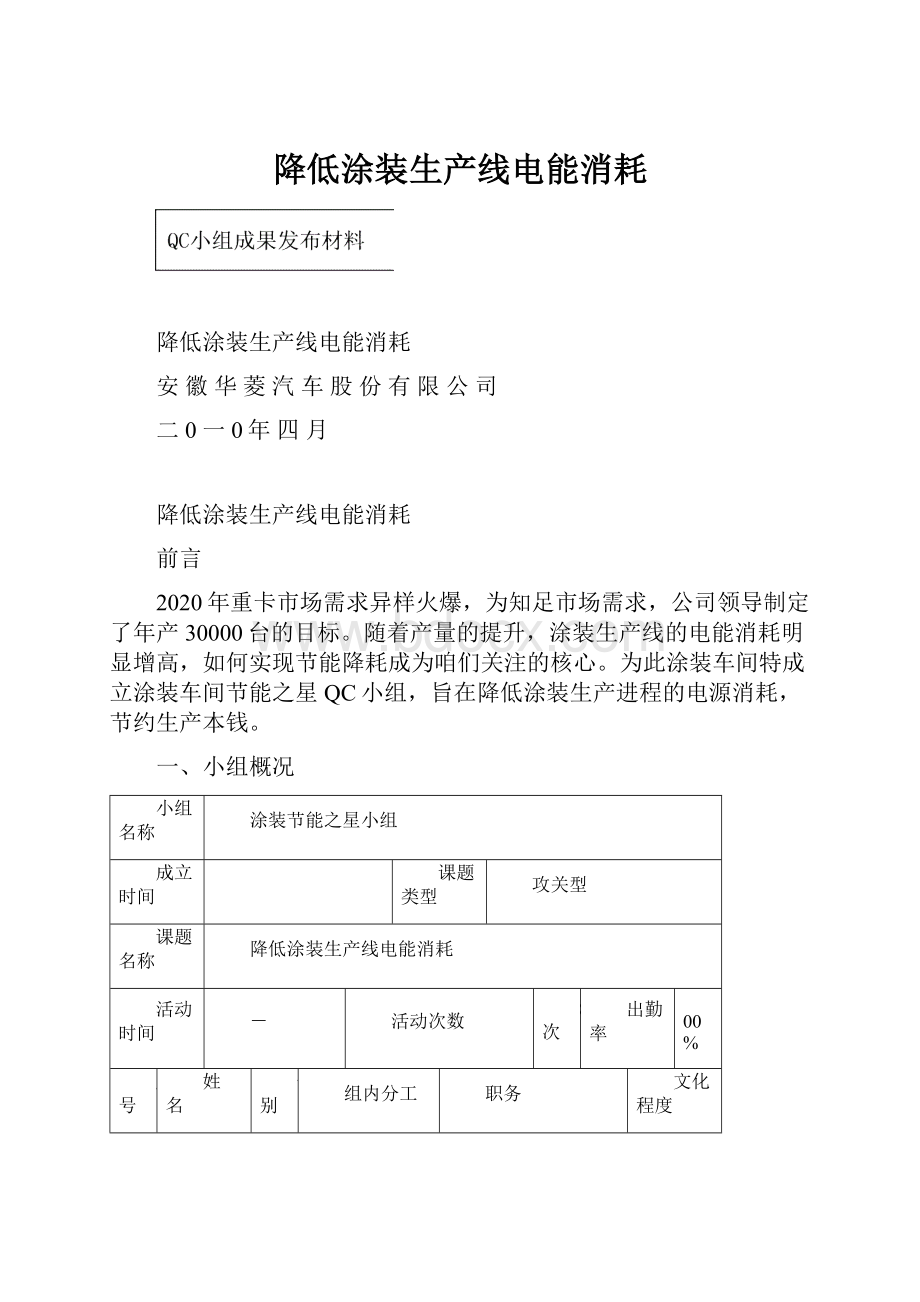
降低涂装生产线电能消耗
降低涂装生产线电能消耗
安徽华菱汽车股份有限公司
二0一0年四月
降低涂装生产线电能消耗
前言
2020年重卡市场需求异样火爆,为知足市场需求,公司领导制定了年产30000台的目标。
随着产量的提升,涂装生产线的电能消耗明显增高,如何实现节能降耗成为咱们关注的核心。
为此涂装车间特成立涂装车间节能之星QC小组,旨在降低涂装生产进程的电源消耗,节约生产本钱。
一、小组概况
小组名称
涂装节能之星小组
成立时间
课题类型
攻关型
课题名称
降低涂装生产线电能消耗
活动时间
-
活动次数
8次
出勤率
100%
序号
姓名
性别
组内分工
职务
文化程度
1
钟阿鹏
男
组长
副主任
中专
2
付贝贝
男
课题顾问
主任科员
大专
3
盛厚火
男
调查分析
主任科员
中专
4
袁佐明
男
调查分析
主任科员
中专
5
朱海峰
男
方案实施
维修班长
大专
6
管大林
男
数据收集
工段长
大专
7
赵刘峰
男
方案实施
班组长
中技
8
刘义娟
男
方案实施
班组长
大专
9
张荣明
男
方案实施
班组长
高中
10
王新刚
男
方案实施
班组长
中专
11
濮绪平
男
材料制作
班组长
中专
12
桂小坤
男
数据收集
工段长
中专
13
胡锡宽
男
方案实施
班组长
中专
14
王贤发
男
材料制作
班组长
中专
二、选题理由
三、现状调查
涂装车间涂装生产线分为驾驶室生产线和车架生产线,在09年6月1日—12月30日对两条生产线消耗电费调查如下:
项目
平均量
单台车身消耗电费
元
单台车架消耗电费
元
单台总消耗电费
元
四、活动的目标
项目
活动前
目标
单台车身消耗电费
元
元
单台车架消耗电费
元
元
单台总消耗电费
元
元
按2020年年产30000台产量消耗电费对照
活动前*30000=元
目标*30000=元
节约元-元=1887000元
小组讨论结果:
1、涂装生产线包括驾驶室、车架两条生产线,工艺、设备已经确信无法更改,无法从这方面入手。
二、天天8小时电费是固定的,只能在8小时生产进程中提高生产效率,提高两条生产线的产能,达到降低单台车身耗电量、单台车架耗电量的目标。
五、缘故分析
1.车身线缘故分析
通过车身工艺流程图每一个工位现场实际调查发觉以下问题
一、此刻车身生产全线的节拍为7台/小时。
二、实际面漆班组节拍能够达到台/小时、打磨打胶PVC班组节拍能够达到8台/小时、前处置电泳班组节拍能够达到台/小时。
3、前处置、中涂、面漆烘干室维修时刻太长
结论:
车身全线没有以最快的生产节拍生产,造成浪费。
2.车架线缘故分析
通过车架工艺流程图每一个工位现场实际调查发觉以下问题
一、此刻车架生产全线的节拍为6台/小时。
二、实际车架线节拍能够达到8台/小时
3、车架线程控行车故障率较高
结论:
车架全线没有以最快的生产节拍生产,造成浪费。
六、要因确认
1.车身线要因确认
序号
末端因素
确认内容
确认方法
负责人
实施日期
1
人员技术培训不到位,技术水平差
生产线人员技术培训是否不到位
现场调查打磨、刮腻子、喷漆、修补人员技术水平实际情况
袁左明
1月3日-1月10日
2
生产组织优化
实际生产是否合理
现场调查生产实际情况
管大林
1月3日-1月10日
3
车身面漆返工率太高
是否需要返工、因为什么返工
现场调查车身面漆返工率实际情况
张荣明
1月3日-1月10日
4
喷漆前车身积放量太少
现场可以积放多少车身
现场调查是否积放量太少
王新刚
1月3日-1月10日
5
PVC烘干室节拍太慢
实际节拍是否合理
现场调查实际节拍是否太慢
刘义娟
1月10日-1月20日
6
PVC打胶工位节拍太慢
PVC打胶工位节拍太慢
实际节拍是否合理
刘义娟
1月10日-1月20日
7
前处理上料浪费时间
是否不适合生产线人员上料
现场调查前处理上料的实际情况
赵刘峰
1月10日-1月20日
8
烘干室维修时间太长
烘干室实际维修是否合理
现场调查烘干室实际维修情况
朱海峰
1月10日-1月20日
确认1:
人员技术培训不到位,技术水平差
a、各班组坚持每一个月进行一次技术培训,每周召开一次全班技术问答;
b、打磨、刮腻子、喷漆、修补人员都由师傅带徒弟培训合格上岗;(结论:
非要因)
确认2:
生产组织优化
a、自动喷涂机换色延误时刻
自动喷涂机每换一次颜色平均延误2台车身生产时刻,需要13分钟
实际统计驾驶室出天天要换色5次,延误65分钟
b、面漆生产线上驾驶室车距过大,驾驶室车距为1200mm
c、车身滑撬小车太少,只有90个,无法知足车身线流水线持续生产(结论:
要因)
确认3:
车身面漆返工率太高
a、车身整车返工2台车身
b、车身左右车门返工8个车门(结论:
要因)
确认4:
喷漆前车身积放量太少
喷漆前车身只能积放9台,当生产时积放的车身无法知足面漆班组台/小时的速度
(结论:
要因)
确认5:
PVC烘干室节拍太慢
a、3台车身进烘干室需要3分钟,节拍太慢。
烘干室前每次只能放2台车身,每次都等第3台车身,阻碍速度
b、3台车身在烘烤需要18分钟,烘烤时刻太长。
烘干室密封性不行。
c、3台车身出烘干室需要3分分钟,节拍太慢。
出车为人工拉车,效率很低
PVC烘干室一次性能够烘烤3台车身,3车身在那个工位需要24分钟
每台车身在pvc烘干室工位的时刻为:
24分钟/3=8分钟
每小时60分钟/8=台,无法知足面漆班组9台/小时的速度(结论:
要因)
确认6:
PVC打胶工位节拍太慢
PVC打胶工位前只能放2台车身,打胶工位前积放量太少,无法跟上PVC烘干室的生产节拍。
(结论:
要因)
确认7:
前处置上料浪费时刻
前处置班组天天必需安照工艺要求人工搬料到前处置槽体上,天天浪费30分钟搬料,费时费工。
(结论:
要因)
确认8:
烘干室维修时刻太长
a、车间电泳、中涂、面漆烘干室共有滑撬系统6台起落机的上升到位和减速耐高温开关,耐高温接近开关的安装位置不合理,离烘箱高温区域太近
b、一旦开关失灵需要维修改换,烘干室要先降温后,维修工进入烘干室维修,然后再升温到工艺要求的烘烤温度进行生产平均维修延误烘干室20分钟生产(结论:
要因)
2.车架线要因确认
末端因素
确认内容
确认方法
负责人
实施日期
1
人员成本意识不高
生产线人员成本意识是很低
现场观察生产线人员成本意识情况
桂小坤
1月3日-1月30日
2
生产组织优化
实际生产是否合理
现场调查生产实际情况
盛厚火
1月3日-1月30日
3
程控行车钢丝绳更换频繁
更换频繁是多少
现场调查程控行车钢丝绳更换频繁
朱海峰
1月3日-1月30日
4
程控行车故障比较频繁
故障停机多长时间
现场调查故障停机情况
胡锡宽
1月3日-1月30日
5
现场车架摆放杂乱
现场是否摆放杂乱
对车间现场进行5S考评
王贤发
1月3日-1月30日
6
焊装车架配送不及时
是否不及时
现场调查车架配送情况
桂小坤
1月3日-1月30日
确认1:
人员本钱意识不高
a、各班组坚持每周进行班组本钱学习讨论;
b、每位班组员工都超级重视本钱意识;(结论:
非要因)
确认2:
生产组织优化
车架线此刻是两个班次生产,天天晚上17:
30分交班,都得停线30分钟用饭。
(结论:
要因)
确认3:
程控行车钢丝绳改换频繁
程控行车有12根钢丝绳磨损严峻,1月3日-30日统计平均天天都要换1根钢丝绳,停线24分钟。
(结论:
要因)
确认4:
程控行车故障率较高
a、程控行车此刻超载运行,行车行走和卷扬轴承磨损严峻,改换十分困难。
2月1日-10日统计发觉,平均天天都要30分钟改换轴承
b、程控行车吊具掉落情形十分频繁,1月3日-30日统计平均天天都要40分钟来打捞吊具(结论:
要因)
确认五、现场车架摆放杂乱
生产现场整洁、有序,符合5S治理要求。
(结论:
非要因)
确认六、焊装车架配送不及时
焊装车间车架配送很及时,没有阻碍涂装车间生产。
(结论:
非要因)
六、制定计谋
1.车身线制定对策
要因
对策
目标
措施
地点
负责人
完成日期
1
生产优化
喷涂机换色要65分钟
降低换色时间
换色要13分钟
合理安排颜色顺序
面漆
王新刚
2月1日-10日
驾驶室车距1200mm
降低车距
车距1000mm
降至最小车距
面漆
张荣明
2月1日-10日
滑撬小车90个
增加滑撬小车
流水线连续生产
增加到110个
修补
管大林
2月1日-10日
2
返工率太高
返工2台车身
降低返工率
返工台车身
局部修补
修补
濮绪平
2月1日-20日
返工8台车门
降低返工率
返工1台车门
制作专门工装
面漆
管大林
2月1日-20日
3
喷漆前车身积放量少
喷漆前车身只能积放9台
增加积放量
积放量增加到15台
增加工位,加大喷漆前车身积放量
面漆
朱海峰
2月1日-20日
4
PVC烘干室节拍太慢
3台车身进烘干室要3分钟
积放3台车身
降低到进烘干室分钟
增加烘干室前的积放工位
PVC
朱海峰
2月10日-20日
3台车身烘烤需要18分钟
减少升温时间
降低到烘烤要16分钟
增加烘干室密封性
PVC
刘义娟
2月10日-20日
3台车身出烘干室要3分钟
改变出口方式
降低到出烘干室要分钟
改变PVC烘干室出口电器控制
PVC
朱海峰
2月10日-20日
5
PVC打胶节拍太慢
打胶工位前积放量2台车身
增加积放量
积放量增加到4台
停止器前移2个工位,并改变停止器控制程序
PVC
刘义娟
2月20日-30日
要因
对策
目标
措施
地点
负责人
完成日期
6
前处理上料慢
前处理30分钟人工搬料
改变上料方式
人工搬料时间降低到5分钟
增加上料吊具,自动上料
修补
赵刘峰
2月20日-30日
7
烘干室维修时间太长
维修耽误烘干室20分钟生产
降低维修时间
维修不耽误生产时间
改变开关位置,便于维修
维修
朱海峰
2月20日-30日
2.车架线制定对策
小组针对每一个要因各提出了两种方案并进行评判选择。
序号
评价内容
◎
○
△
1
可实施性
小组能自行解决
需要其他部门协助
难度大
2
有效性
预计很有效
会有一定效果
把握不大
3
可靠性
彻底改造
较彻底改造
临时措施
4
经济性
费用低
需要一定费用但尚能承担
费用很高很难承受
表中:
◎5分○3分△1分
序号
要因
方案
评价
得分
实施性
有效性
可靠性
经济性
1
生产组织优化
两班次合为一个班次
△
○
○
△
8
×
对两个班次的吃饭时间调整
◎
◎
◎
◎
20
√
2
钢丝绳更换频繁
改变行车东侧钢丝绳卷扬导绳槽的旋向
◎
◎
○
◎
18
√
更换粗的钢丝绳
○
○
△
○
10
×
3
程控行车故障比较频繁
行车轴承磨损严重
更换好的轴承
◎
△
△
○
10
×
安排外协人员晚上进行维保更换轴承
◎
◎
◎
○
18
√
行车吊具掉落频繁
制作专门的工具打捞掉落的吊具
○
△
△
△
6
×
更改吊具减少吊具的掉落频次
◎
◎
○
◎
18
√
八、计谋实施
1.车身线计谋实施
实施1:
生产组织优化
a.喷涂机换色要70分钟
现场调查发觉天天的换色是因为焊装车间驾驶室顺序无法统一颜色生产,和焊装车间协商后,天天由涂装车间给焊装车间安排驾驶室生产顺序
通过2月20日—3月20日统计发觉,天天平均换色为1次,延误2台车身生产时刻,天天可多生产8台驾驶室
b、驾驶室车距1200mm
现场调查发觉驾驶室车距为1200mm,可降至1000mm,每台车节约200mm.通过2月20日—3月20日,天天可多生产3台驾驶室
c、车身滑撬小车90个
现场调查发觉滑撬小车加到110个后,面漆班组能够不断线生产。
通过2月20日—3月20日,天天多生产8台车身
实施前面漆天天生产:
8﹡7=56台
实施后面漆天天生产:
56+8+3+8=75台-2(换色)=73台(合格)
实施2:
面漆返工率太高
a、车身平均天天返工2台车身,依如实际调查返工车身都能够进行局部修理
局部手工喷漆实施后
实施后2月20日-3月20日统计得出天天平均返工车身
b、车门返工率8%
依如实际调查7%的返工车门,原有固定方式为铁丝钩固定,车门在行进进程中,铁丝易松开,门自动打开,油漆刮坏
铁丝扣门油漆刮坏
依照现场需求,绘制车门卡专用工装图
工装图工装扣门图
实施前:
天天返工2台车身+8个车门
实施后2月20日-3月20日统计得出:
天天平均返工台车身+1个车门
实施3:
喷漆前车身积放量少
依如实际现场调查发觉喷漆前能够通过增加储蓄链来达到增加车身的目的
实施前喷漆前车身积放:
9台
实施后喷漆前车身:
9+新增6台=15台
2月20日-3月20日现场实际调查发觉,喷漆前车身积放15台能够知足面漆的生产速度
实施4:
PVC烘干室节拍太慢
a.3台车身进烘干室需要3分钟
依如实际现场调查发觉PVC烘干室每次能够烘烤3台车身,而PVC烘干室前只能积放2台车身,每次都等第3台车身,浪费时刻
对现场实际测量发觉,PVC烘干室前通过工位调整能够积放3台车身,能够知足烘干室一次烘烤3台车身的生产节拍
实施后3台车身一次性持续不断进入烘干室,2月20日-3月20日
现场测量统计出3台车身一次性进入烘干室平均要分钟,缩短分钟
台车身在烘干室中烘烤需要18分钟
对现场实际测量发觉3台车身在烘干室烘烤到工艺要求要18钟,因为烘干室门关不紧密封不行,温度流失严峻,阻碍升温时刻。
维修班组对PVC大门研究后发觉,门关不紧和门上方的2台开关门的传动电机的速比选择不妥,将速比调整后,门已能全数关紧。
2月20日-3月20日现场测量统计出3台在烘干室里面烘烤平均要16分钟,缩短2分钟。
C.3台车身出烘干室需要3分钟
对现场实际测量发觉3台车身出烘干室要3分钟,为人工拉车,速度超级慢,且劳动强度专门大。
通过与设备部工程师一路商量讨论,改变PVC烘干室出口电器操纵,从而改变烘干室出口的出车方式,由手动人工拉车变成自动出车。
极大的降低了劳动量,缩短了出车时刻。
实施后3台车身自动出烘干室,极大的降低劳动量,缩短出车时刻。
2月20日-3月20日现场测量统计3台车身出烘干室平均要分钟,缩短分钟。
实施前:
PVC工位节拍时刻:
3分钟(进车)+18分钟(烘烤)+3分钟(出车)=24分钟
每台车身在pvc烘干室工位的时刻为:
24分钟/3=8分钟
每小时生产节拍:
60分钟/8=台8小时能够生产60台
实施后:
PVC工位节拍时刻:
分钟(进车)+16分钟(烘烤)+分钟(出车)=19分钟
每台车身在pvc烘干室工位的时刻为:
19分钟/3=分钟
每小时生产节拍:
60分钟/=台8小时能够生产76台
实施后能够知足面漆班组8小时75台车身的生产速度。
实施5:
PVC打胶节拍太慢
PVC打胶工位前只能积放2台车身,阻碍整个PVC打胶工位的生产节拍。
停止器操纵旧程序
维修工对现场实际调查发觉,可将PVC打胶工位前的GG4停止器前移两个工位,并更改原有的操纵程序。
从而使PVC打胶工位前的车身积放量达到4台,知足了后续工位的生产节拍。
停止器操纵新程序
实施前:
积放2台车
实施后:
积放4台车
3月1日-3月30日现场测量统计发觉PVC打胶工位前积放4台车能够知足后绪工位的节拍速度。
实施6:
前处置上料慢
对现场实际调查发觉前处置的工艺要求确信,节拍无法改变,每小时只能生产台,平均天天上料要30分钟。
上料方式为人工搬料,劳动强度专门大。
通过和维修工一路现场调查发觉,能够在前处置电泳槽体上增加一个电动葫芦上料,
极大的节省劳动力,节约了生产时刻。
现场实际测量实施后天天上料只要2分钟。
实施前上料30分钟
实施后上料2分钟节约:
30分钟-2分钟=28分钟
实施前8小时生产:
(480分钟-30分钟)/=60台
实施后8小时生产:
(480分钟-2分钟)/=64台
因为前处置电泳班组受工艺要求不得改变节拍速度,只能提早90分钟上班。
来完成天天75台的产量,以保证后继工位能够持续不中断生产。
实施7:
烘干室维修时刻太长
对现场实际调查发觉电泳、中涂、面漆烘干室共有滑撬系统6台起落机,共有12个感应开关在高温区域。
每次维修时烘干室要先降温后,维修工爬到起落机高处维修,维修作业完成后再升温到工艺要求的烘烤温度进行生产,平均维修延误烘干室20分钟生产
维修工将烘干室感应开关下移至低温区
3月1日-30日现场跟踪统计维修班班改换感应开关,都没有延误烘干室20分钟生产
实施前改换需要时刻:
20分钟
实施后改换需要时刻:
0分钟
节约需要时刻:
20分钟
2.车架线计谋实施
实施一:
对两个班次的用饭时刻调整
各班组内部开会讨论,后决定白班往后延迟20分钟下班到17:
50分下班,晚班17:
55分上班。
节约25分钟时刻。
实施前:
浪费30分钟
实施后:
30分钟-25分钟=5分钟
2月1日-28日统计后发觉平均天天都节约25分钟后,天天能够多干3台车架
实施二:
改变行车钢丝绳卷扬方向
车间维修工和设备部工程师对程控行车东侧钢丝绳卷扬机的研究发觉车间东面的行车卷扬滚筒导绳槽设计旋向错误,造成钢丝绳在导绳槽外运行,致使钢丝绳磨损严峻,改换频繁,1月3日-15日统计平均天天都要换1根钢丝绳,停线24分钟。
2月1日-30日对改造后的程控行车卷扬钢丝绳磨损情形,统计平均得出改换了一根钢丝绳。
实施前:
24分钟(平均天天改换花费时刻)
实施后:
1分钟(平均天天改换花费时刻)
实施后天天能够多生产3台车架
实施三:
程控行车故障比较频繁
a、行车轴承磨损严峻
程控行车此刻超载运行,行车轴承磨损严峻,改换十分困难。
1月1日-15日统计发觉,平均天天都要32分钟改换轴承。
现场班组和维修班组讨论研究得出,此刻维修班组只有白班有人维修,而此刻车架线两个班次生产,只能在凌晨2点到7点有4个小时的停线时刻。
只能安排外协人员在凌晨时刻进行行车轴承保养、改换。
实施前:
32分钟
实施后:
0分钟节约:
32分钟
实施后天天能够多生产4台车架
b、行车吊具掉落频繁
程控行车吊具掉落情形十分频繁,2月1日-10日统计发觉,平均天天都要40分钟来打捞吊具。
车间维修班组和现场员工一路研究讨论发觉程控行车吊具,吊具两边的吊耳太短,致使容易掉落。
决定加长吊具两边的吊耳,来减少程控行车吊具掉落情形。
实施前:
48分钟
实施后:
0分钟
节约:
48分钟
天天多生产6台车架
实施前8小时车架生产台数:
6台*8=48台
实施后:
48台+3台+3台+4台+6台=64台
九、成效验证
1.车身线成效验证
天天工作8个小时车身产量
实施前:
56台车身
实施后:
73台车身
实施前:
单台车身电费:
元
8小时车身电费:
56台×=元
实施后:
单台车身电费:
元/73台=元
单台车身节约电费:
元-元=元
单台车身电费对照
2.车架线成效验证
天天工作8个小时车架产量
实施前:
48台车架
实施后:
64台车架
实施前
单台车架消耗电费:
元
8小时车架消耗电费:
48台×=7560元
实施后
单台车架消耗电费:
元/64台=元
单台车架节约电费:
元元=元
单台车架消耗电费对照
九、效益分析
1.车身线效益分析
2020年产30000台车身消耗电费
实施前:
元×30000=7848000元
实施后:
元×30000=6021000元
节约:
7848000元-6021000元=1827000元
1.车架线效益分析
2020年产30000台车架消耗电费
实施前:
元×300000=4725000元
实施后:
元×30000=3543750元
节约:
4725000元-3543750元=1181250元
3.涂装生产线电能消耗分析
活动后单台车身消耗电费:
元
单台车架消耗电费:
元
车间消耗总电费=单台车身消耗电费+单台车架消耗电费=元+元=元
项目
活动前
目标
活动后
单台车身消耗电费
元
元
元
单台车架消耗电费
元
元
元
单台总消耗电费
元
元
元
2020年产30000台消耗电费
效益分析
实施前:
元*30000=元
实施后:
元*30000=9564750元
节约:
元-9564750元=3008250元
2020年产30000台车计算可节约电费3008250元
无形效益
a.通过本次活动,进一步提高了成员的质量意识、问题意识和改良意识,大大增强了团队凝聚力,锻炼了成员协作和集体攻关的能力。
b.增强了员工的效率意识,提高了员工本钱观念。
c.为公司QC活动的普及和推行起到了专门好的示范作用,吸引更多职工参加QC小组活动。
十、巩固方法
1.为维持成效,车间将对新的改造项目进行重点节拍观注,并对各操作人员进行相关培训,使活动功效标准化。
二、对车间员工进行本钱意识常常性培训。
3、制定优化生产治理相关的制度,增强制度的宣传及监控,使得改造后的生产节拍及生产动作制度化、标准化。
十二、活动体会
1.通过本次活动,小组成员分工协作,各展所长,充分发挥了各自的主观能动性,提高了团队成员协同作战的能力,为尔后咱们更好的开展QC活动打下了良好的基础。
2.本次活动解决了涂装车间用电量本钱太高的问题,带来了超级大的经济效益。
3.本次活动增强了小组成员的质量意识,提高了大伙儿解决实际问题的信心。
4.通过本次活动咱们学到了解决实际问题的方式。
5.为尔后咱们更好的开展QC活动打下了良好的基础。
十三、下一步打算
本次活动取得了专门大的经济效益。
针