齿轮加工.docx
《齿轮加工.docx》由会员分享,可在线阅读,更多相关《齿轮加工.docx(19页珍藏版)》请在冰豆网上搜索。
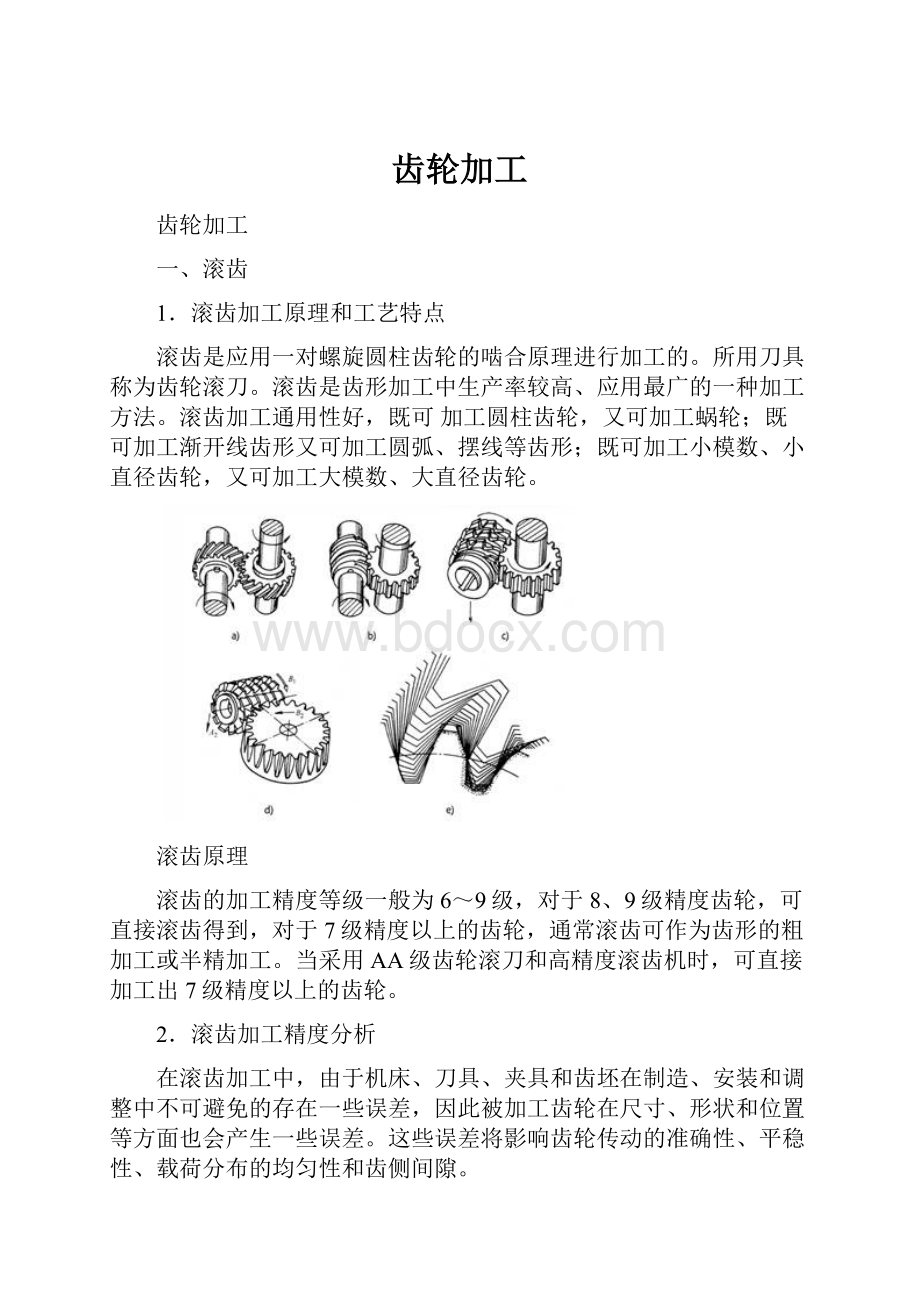
齿轮加工
齿轮加工
一、滚齿
1.滚齿加工原理和工艺特点
滚齿是应用一对螺旋圆柱齿轮的啮合原理进行加工的。
所用刀具称为齿轮滚刀。
滚齿是齿形加工中生产率较高、应用最广的一种加工方法。
滚齿加工通用性好,既可加工圆柱齿轮,又可加工蜗轮;既可加工渐开线齿形又可加工圆弧、摆线等齿形;既可加工小模数、小直径齿轮,又可加工大模数、大直径齿轮。
滚齿原理
滚齿的加工精度等级一般为6~9级,对于8、9级精度齿轮,可直接滚齿得到,对于7级精度以上的齿轮,通常滚齿可作为齿形的粗加工或半精加工。
当采用AA级齿轮滚刀和高精度滚齿机时,可直接加工出7级精度以上的齿轮。
2.滚齿加工精度分析
在滚齿加工中,由于机床、刀具、夹具和齿坯在制造、安装和调整中不可避免的存在一些误差,因此被加工齿轮在尺寸、形状和位置等方面也会产生一些误差。
这些误差将影响齿轮传动的准确性、平稳性、载荷分布的均匀性和齿侧间隙。
滚齿误差产生的主要原因和采取的相应措施见下表
影响
因素
滚齿误差
主要原因
采取的措施
影响传递运动准确性
齿距累积误差超差
齿圈径向圆跳动超差Fr
1.齿坯几何偏心或安装偏心造成
提高齿坯基准面精度要求
提高夹具定位面精度
提高调整技术水平
2.用顶尖定位时,顶尖与机床中心偏心
更换顶尖及提高中心孔制造质量,并在加
工过程中保护中心孔
3.用顶尖定位使,因顶尖或中心孔制造不良,使定位面接触不好造成偏心
提高顶尖及中心孔制造质量,并在加工过程
中保护中心孔
公法线长度变动量超差FW
滚齿机分度蜗轮精度过低
滚齿机工作台圆形导轨磨损
分度蜗轮与工作太圆形导轨不同轴
提高机床分度蜗轮精度
采用滚齿机校正机构
修刮导轨,并以其为基准精滚(或珩)分度蜗轮
影响传递运动的平稳、噪声、振动
齿形误差超差
齿形变肥或变瘦,且左右齿形对称
滚刀齿形角误差
前面刃磨产生较大的前角
更换滚刀或重磨前面
一边齿顶变肥,另一边齿顶边瘦,齿形不对称
刃磨时产生导程误差或直槽滚刀非轴向性误差
刀对中不好
误差较小时,重调刀架转角
重新调整滚刀刀齿,使它和齿坯中心对中
齿面上个别点凸出或凹进
滚刀容屑槽槽距误差
重磨滚刀前面
齿形面误差近似正弦分布的短周期误差
刀杆径向圆跳动太大
滚刀和刀轴间隙大
滚刀分度圆柱对内孔轴心线径向圆跳动误差
找正刀杆径向圆跳动
找正滚刀径向圆跳动
重磨滚刀前面
齿形一侧齿顶多切,另一侧齿根多切切呈正弦分布
滚刀轴向齿距误差
滚刀端面与孔轴线不垂直
垫圈两端面不平行
防止刀杆轴向窜动
找正滚刀偏摆,转动滚刀或刀杆加垫圈
重磨垫圈两端面
基圆齿距偏差超差fpb
滚刀轴向齿距误差
滚刀齿形角误差
机床蜗杆副齿距误差过大
提高滚刀铲磨精度(齿距齿形角)
更换滚刀或重磨前面
检修滚齿机或更换蜗杆副
载荷分布均匀性
齿向误差超差
机床几何精度低或使用磨损(立柱导轨、顶尖、工作台水平性等)
定期检修几何精度
夹具制造、安装、调整精度低
提高夹具的制造和安装精度
齿坯制造、安装、调整精度低
提高齿坯精度
表面粗糙度差
滚刀因素
滚刀刃磨质量差
滚刀径向圆跳动量大
滚刀磨损
滚刀未固紧而产生振动
辅助轴承支承不好
选用合格滚刀或重新刃磨
重新校正滚刀
刃磨滚刀
紧固滚刀
调整间隙
切削用量选择不当
合格选择切削用量
切削挤压引起
增加切削液的流量或采用顺铣加工
齿坯刚性不好或没有夹紧,加工时产生振动
选用小的切削用量,或夹紧齿坯,提高齿坯刚性
机床有间隙
工作台蜗杆副有间隙
滚刀轴向窜动和径向圆跳动大
刀架导轨与刀架间有间隙
进给丝杠有间隙
检修机床,消除间隙
3.齿轮滚刀
齿轮滚刀一般是指加工渐开线齿轮所用的滚刀。
它是按螺旋齿轮啮合原理加工齿轮的。
由于被加工齿轮是渐开线齿轮,所以它本身也应具有渐开线齿轮的几何特性。
齿轮滚刀从其外貌看并不象齿轮,实际上它仅有一个齿(或二个、三个齿),但齿很长而螺旋角又很大的斜齿圆柱齿轮,因为它的齿很长而螺旋角又很大,可以绕滚刀轴线转好几圈,因此,从外貌上看,它很象一个蜗杆。
如图所示。
为了使这个蜗杆能起切削作用,须沿其长度方向开出好多容屑槽,因此把蜗杆上的螺纹割成许多较短的刀齿,并产生了前刀面和切削刃。
每个刀齿有一个顶刃和两个侧刃。
为了使刀齿有后角,还要用铲齿方法铲出侧后面和顶后刀面。
但是各个刀齿的切削刃必须位于这个相当于斜齿圆柱齿轮的蜗杆的螺纹表面上,因此这个蜗杆就称为滚刀的基本蜗杆。
标准齿轮滚刀精度分为四级:
AA、A、B、C。
加工时按照齿轮精度的要求,选用相应的齿轮滚刀。
AA级滚刀可以加工6~7级齿轮;A级可以加工7~8级齿轮;B级可加工8~9级齿轮;C级可加工9~10级齿轮。
二、插齿
1.插齿原理及运动
插齿原理
(1)插齿原理从插齿原理上分析,插齿刀与工件相当于一对平行轴的圆柱直齿轮啮合。
(2)插齿的主要运动:
切削运动-即插齿刀的上下往复运动。
分齿展成运动-插齿刀与工件间应保证正确的啮合关系。
插齿刀每往复一次,工件相对刀具在分度圆上转过的弧长为加工时的圆周进给运动。
径向进给运动-插齿时,为逐步切至全齿深,插齿刀应该有径向进给运动。
让刀运动-插齿刀做上下往复运动时,向下是工作行程。
为了避免刀具檫伤已加工的齿面并减少刀齿的磨损,在插齿刀向上运动时,工作台带动工件退出切削区异端距离,插齿刀工作行程时,工件恢复原位。
2.插齿刀
插齿刀的形状很象齿轮:
直齿插齿刀象直齿齿轮,斜齿插齿刀象斜齿齿轮。
根据机械工业颁布的刀具标准JB2496-78规定,直齿插齿刀分为三种结构型式:
=1\*GB3①盘形直齿插齿刀,这是最常用的一种结构型式,用于加工直齿外齿轮和大直径的内齿轮。
不同规范的插齿机应选用不同分圆直径的插齿刀。
=2\*GB3②碗形直齿插齿刀它以内孔和端面定位,夹紧螺母可容纳在刀体内,主要用于加工多联齿轮和带凸肩的齿轮
=3\*GB3③锥柄直齿插齿刀这种插齿刀的公称分圆直径有25毫米和38毫米两种。
因直径较小,不能做成套装式,所以做成带有锥柄的整体结构型式。
这种插齿刀主要用于加工内齿轮,
插齿刀有三个精度等级:
AA级适用于加工6级精度齿轮;A级适用于加工7级精度的齿轮;B级适用于加工8级精度的齿轮。
应该根据被加工齿轮的传动平稳性精度等级选取。
3.插齿加工质量分析
(1)传动准确性齿坯安装时的几何偏心使工件产生径向位移使得齿圈径向跳动;工作台分度蜗轮的运动偏心使工件产生切向位移,造成公法线长度变动;插齿刀的制造齿距累积误差和安装误差,也会造成插齿的公法线变动。
(2)传动平稳性插齿刀设计时没有近视误差,所以插齿的齿形误差比滚齿小。
(3)载荷均匀性机床刀架刀轨对工作台回转中心的平行度造成工件产生齿向误差;插齿刀的上下往复频繁运动使刀轨磨损,加上刀具刚性差,因此插齿的齿向误差比滚齿大。
(4)表面粗糙度插齿后的表面粗糙度比滚齿小,这是因为插齿过程中包络齿面的切削刃数教多。
4.提高插齿生产率的措施
(1)高速插齿为了缩短作业时间,可增加插齿刀没分钟的往复次数来谨慎性高速插齿。
现有高速插齿机的往复运动可以达到1000次/分钟,有的已经达到1800次。
(2)提高插齿刀耐用度改进刀具材料、刀具集合参数都能提高刀具耐用度。
(3)提高圆周进给量提高圆周进给量能减少作业时间,但齿面粗糙度增大,加上插齿回程时的让刀量增大,容易引起振动,因此应将粗精加工分开。
5.插齿的应用范围
插齿应用范围广泛,它能加工内外啮合齿轮、扇形齿轮齿条、斜齿轮等。
但是加工齿条需要附加齿条夹具,并在插齿机上开洞;加工斜齿轮需要螺旋刀轨。
所以插齿适合于加工模数教小、齿宽较小、工作平稳性要求较高、运动精度要求不高的齿轮。
三、剃齿
1.剃齿原理
剃齿是根据一对轴线交叉的斜齿轮啮合时,沿齿向有相对滑动而建立的一种加工方法。
剃齿刀与工件间有一夹角∑,∑=βg±βd,βg、βd
剃齿工作原理
分别为工件与刀具的分度圆螺旋角。
工件与刀具螺旋方向相同时为+,相反时为-。
为一把右旋剃齿刀剃削一左旋齿轮的情况,∑=βg-βd,剃齿时剃齿刀做高速回转并带动工件一起回转。
在啮合点P,剃齿刀圆周速度为V工件的圆周速度为V,它们都可以分解为垂直螺旋线齿面的法向分量和螺旋面的切向分量。
因为啮合点处的法向分量必须相等,而两个切向分量却不相等,因而产生相对滑动。
由于剃齿刀齿面少年宫开有小槽,就产生了切削作用,相对滑动速度就成了切削速度。
剃齿时剃齿刀和齿轮是无侧隙双面啮合,剃齿刀刀齿的两侧面都能进行切削。
当工件旋向不同或剃齿刀正反转时,刀齿两侧切削刃的切削速度是不同的。
为了使齿轮的两侧都能获得较好的剃削质量,剃齿刀在剃齿过程中应交替的进行正反转动。
2.剃齿质量分析
剃齿是一种利用剃齿刀与被剃齿轮做自由啮合进行展成加工的方法,。
剃齿刀与齿轮间没有强制性的啮合运动,所以对齿轮的传递运动准确性精度提高不大,但传动的平稳性和接触精度有较大的提高,齿轮表面粗糙度值明显减少。
剃齿是在滚齿之后,对未淬硬齿轮的齿形进行精加工的一种常用方法。
由于剃齿的质量较好、生产率高、所用机床简单、调整方便、剃齿刀耐用度高,所以汽车、拖拉机和机床中的齿轮,多用这种加工方法来进行精加工。
目前我国剃齿加工中最常用的方法是平行剃齿法,它最主要的缺点是刀具利用率不好,局部磨损使刀具利用率寿命低;另一缺点是剃前时间长,生产率低。
为此,大力发展了对角剃齿、横向剃齿、径向剃齿等方法。
近年来,由于含钴、钼成分较高的高性能高速钢刀具的应用,使剃齿也能进行硬齿面的齿轮精加工。
加工精度可达7级,齿面的表面粗糙度值Ra为0.8~1.6微米。
但淬硬前的精度应提高一级,留硬剃余量为0.01~0.03毫米。
3.剃齿工艺中的几个问题
(1)剃前齿轮的材料剃前齿轮硬度在22~32HRC范围时,剃齿刀校正误差能力最好,如果齿轮材质不均匀,含杂质过多或韧性过大会引起剃齿刀滑刀或啃刀,最终影响剃齿的齿形及表面粗糙度。
(2)剃前齿轮的精度剃齿是齿形的精加工方法,因此剃齿前的齿轮应有较高的精度,通常剃齿后的精度只能比剃齿前提高一级。
(3)剃齿余量剃齿余量的大小,对剃齿质量和生产率均有较大影响。
余量不足时,剃前误差及表面缺陷不能全部除去;余量过大,则剃齿效率低,刀具磨损快,剃齿质量反而下降。
(4)剃前齿形加工时的刀具剃齿时,为了减轻剃齿刀齿顶负荷,避免刀尖折断,剃前在齿跟处挖掉一块。
齿顶处希望能有一修缘,这不仅对工作平稳系性有利,而且可使剃齿后的工件沿外圆不产生毛刺。
此外,合理的确定切削用量和正确的操作也十分重要。
四、珩齿
1.珩齿原理及特点
珩齿是热处理后的一种光整加工方法。
珩齿的运动关系和所用机床与剃齿相似,珩轮与工件是一对斜齿轮副无侧隙的自由紧密啮合,所不同的是珩齿所用刀具是含有磨料、环氧树脂等原料混合后在铁心上浇铸而成的塑料齿轮。
切削是在珩轮与被加工齿轮的“自由啮合”过程中,靠齿面间的压力和相对滑动来进行的。
如下图所示。
珩磨轮于珩磨原理
1-珩磨轮 2-工件
珩齿的运动与剃齿基本相同,即珩轮带动工件高速正反转;工件沿轴向往复运动及工件的径向进给运动。
所不同的是其径向进给是在开车后一次进给到预定位置。
因此,珩齿开始时齿面压力较大,随后逐渐减少,直至压力消失时珩齿便结束。
珩齿的特点如下:
1)珩齿后表面质量较好珩齿速度一般是1~3m/s,比普通磨削速度低,磨粒粒度又小,结合几弹性较大,珩齿过程实际上是低速磨削、研磨和抛光的综合过程,齿面不会产生烧伤和裂纹,所以珩齿后齿的表面质量较好。
2)珩齿后的表面粗糙度值减少珩轮齿面上均匀密布着磨粒,珩齿后齿面切削痕迹很细,磨粒不仅在齿面产生滑动而切削,而且沿渐开线切线方向亦具有切削作用,从而在齿面上产生交叉网纹,使齿面的表面粗糙度值明显减少。
3)珩齿修正误差能力低珩齿与剃齿的运动关系基本相同,由于珩轮本身有一定的弹性,不会全部复映到齿轮上,所以珩轮本身精度一般都不高,但对珩前齿轮的精度则要求高。
2.珩齿方法
珩齿方法有外啮合珩齿、内啮合珩齿和蜗杆状珩磨轮珩齿三种。
3.珩齿的应用
因为珩齿修正误差能力差,因而珩齿主要用于去除热处理后齿面上的氧化皮及毛刺,可使表面粗糙度Ra值从1.6um左右降到0.4um以下,为了保证齿轮的精度要求,必须提高珩前的加工精度和减少热处理变形。
因此,珩前加工多采用剃齿。
如磨齿后需要进一步降低表面粗糙度值,也可以采用珩齿使齿面的表面粗糙度值R值达到0.1um.
珩齿的轴交角常取15度。
珩齿余量很小,一般珩前为剃齿时,常取0.01~0.02mm;珩前为磨齿时,取0.003~0.005mm。
由于珩齿具有齿面的表面粗糙度值小、效率高、成本低、设备简单、操作方便等优点,故是一种很好的齿轮光整加工方法,一般可取加工6~8级精度的齿轮。
五、磨齿
1.磨齿原理
磨齿是齿形加工中加工精度最高的一种方法。
对于淬硬的齿面,要纠正热处理变形。
获得高精度齿廓。
磨齿是目前最常用的加工方法。
磨齿是用强制性的传动链,因此它的加工精度不直接决定于毛坯精度。
磨齿可使齿轮精度最高达到3级,表面粗糙度Ra值可以达到0.8~0.2微米,但加工成本高、生产率较低。
2.磨齿方法
磨齿方法很多,根据磨齿原理的不同可以分成形法和展成法两类。
成形法是一种用成形砂轮磨齿的方法,目前生产中应用较少,但它已经成为磨削内齿轮和特殊齿轮时必须采用的方法。
展成法主要是利用齿轮与齿条啮合原理进行加工的方法,这种方法是将砂轮的工作面构成假象齿条的单侧或双侧齿面,在砂轮与工件的啮合运动中,砂轮的磨削平面包络出渐开线齿面。
六、典型齿轮加工工艺分析
1.圆柱齿轮加工工艺程的内容和要求
圆柱齿轮的加工工艺程一般应包括以下内容:
齿轮毛坯加工、齿面加工、热处理工艺及齿面的的精加工。
在编制工艺过程中,常因齿轮结构、精度等级、生产批量和生产环境的不同,而采取各种不同的工艺方案。
下图为一直齿圆柱齿轮的简图
下表出了该齿轮机械加工工艺过程。
序号
工序内容及要求
定位基准
设备
1
锻造
2
正火
3
粗车各部,均放余量1.5mm
外圆、端面
转塔车床
4
精车各部,内孔至锥孔塞规刻线外露6~8mm,其余达图样要求
外圆、内孔、端面
C616车床
5
滚齿Fw=0.036mmFi″=0.10mm
fi″=0.022mmFβ=0.011mm
W=
mm,齿面Ra2.5μm
内孔、B端面
Y38滚齿机
6
倒角
内孔、B端面
倒角机
7
插键槽达图样要求
内孔、B端面
插床
8
去毛刺
9
剃齿
内孔、B端面
Y5714
10
热处理,齿部5132
11
磨内锥孔,磨至锥孔塞规小端平
外圆、B端面
M220
12
珩齿达图样要求
内孔、B端面
Y5714
13
终结检验
从中可以看出,编制齿轮加工工艺过程大致可以划分如下几个阶段:
1)齿轮毛坯的形成:
锻件、棒料或铸件;
2)粗加工:
切除较多的余量;
3)半精加工:
车、滚、插齿;
4)热处理:
调质、渗碳淬火、齿面高频感应加热淬火等
5)精加工:
精修基准、精加工齿形
2.齿轮加工工艺过程分析
1)基准的选择
对于齿轮加工基准的选择常因齿轮的结构形状不同而有所差异。
带轴齿轮主要采用顶点孔定位;对于空心轴,则在中心内孔钻出后,用两端孔口的斜面定位;孔径大时则采用锥堵。
顶点定位的精度高,且能作到基准重合和统一。
对带孔齿轮在齿面加工时常采用以下两种定位、夹紧方式。
=1\*GB3①以内孔和端面定位这种定位方式是以工件内孔定位,确定定位位置,再以端面作为轴向定位基准,并对着端面夹紧。
这样可使定位基准、设计基准、装配基准和测量基准重合,定位精度高,适合于批量生产。
但对于夹具的制造精度要求较高。
=2\*GB3②以外圆和端面定位当工件和加剧心轴的配合间隙较大时,采用千分表校正外圆以确定中心的位置,并以端面进行轴向定位,从另一端面夹紧。
这种定位方式因每个工件都要校正,故生产率低;同时对齿坯的内、外圆同轴要求高,而对夹具精度要求不高,故适用于单件、小批生产。
综上所述,为了减少定位误差,提高齿轮加工精度,在加工时应满足以下要求:
=1\*GB3①应选择基准重合、统一的定位方式;
=2\*GB3②内孔定位时,配合间隙应近可能减少;
=3\*GB3③定位端面与定位孔或外圆应在一次装夹中加工出来,以保证垂直度要求。
2)齿轮毛坯的加工
齿面加工前的齿轮毛坯加工,在整个齿轮加工过程中占有很重要的地位。
因为齿面加工和检测所用的基准必须在此阶段加工出来,同时齿坯加工所占工时的比例较大,无论从提高生产率,还是从保证齿轮的加工质量,都必须重视齿轮毛坯的加工。
在齿轮图样的技术部要求中,如果规定以分度圆选齿厚的减薄量来测定齿侧间隙时,应注意齿顶圆的精度要求,因为齿厚的检测是以齿顶圆为测量基准的。
齿顶圆精度太低,必然使测量出的齿厚无法正确反映出齿侧间隙的大小,所以,在这一加工过程中应注意以下三个问题:
=1\*GB3①当以齿顶圆作为测量基准时,应严格控制齿顶圆的尺寸精度;
=2\*GB3②保证定位端面和定位孔或外圆间的垂直度;
=3\*GB3③提高齿轮内孔的制造精度,减少与夹具心轴的配合间隙;
3)、齿形及齿端加工
齿形加工是齿轮加工的关键,其方案的选择取决于多方面的因素,如设备条件、齿轮精度等级、表面粗糙度、硬度等。
常用的齿形加工方案在上节已有讲解,在此不再叙述。
齿轮的齿端加工有倒圆、倒尖、倒棱和去毛刺等方式。
如下图所示。
齿端加工方式
a)倒圆b)倒尖c)倒棱
经倒圆、倒尖后的齿轮在换档时容易进入啮合状态,减少撞击现象。
倒棱可除去齿端尖角和毛刺。
图9-14是用指状铣刀对齿端进行倒圆的加工示意图。
齿端倒圆
倒圆时,铣刀告诉旋转,并沿圆弧作摆动,加工完一个齿后,工件退离铣刀,经分度再快速向铣刀靠近加工下一个齿的齿端。
齿端加工必须在淬火之前进行,通常都在滚(插)齿之后,剃齿之前安排齿端加工。
4)、轮加工过程中的热处理要求
在齿轮加工工艺过程中,热处理工序的位置安排十分重要,它直接影响齿轮的力学性能及切削加工性。
一般在齿轮加工中进行两种热处理工序,即毛坯热处理和齿形热处理