工件的平面铣削与对刀及设置.docx
《工件的平面铣削与对刀及设置.docx》由会员分享,可在线阅读,更多相关《工件的平面铣削与对刀及设置.docx(23页珍藏版)》请在冰豆网上搜索。
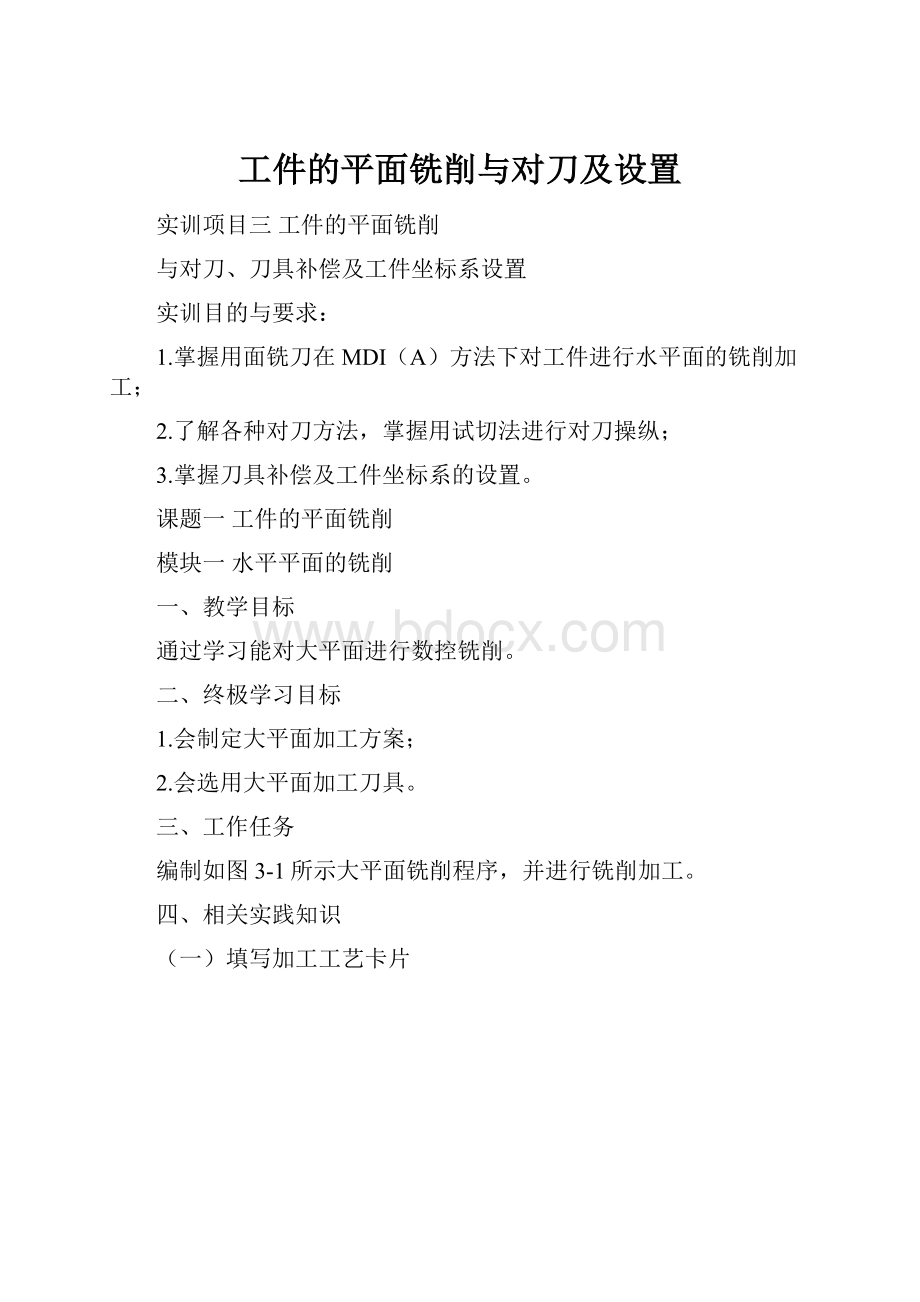
工件的平面铣削与对刀及设置
实训项目三工件的平面铣削
与对刀、刀具补偿及工件坐标系设置
实训目的与要求:
1.掌握用面铣刀在MDI(A)方法下对工件进行水平面的铣削加工;
2.了解各种对刀方法,掌握用试切法进行对刀操纵;
3.掌握刀具补偿及工件坐标系的设置。
课题一工件的平面铣削
模块一水平平面的铣削
一、教学目标
通过学习能对大平面进行数控铣削。
二、终极学习目标
1.会制定大平面加工方案;
2.会选用大平面加工刀具。
三、工作任务
编制如图3-1所示大平面铣削程序,并进行铣削加工。
四、相关实践知识
(一)填写加工工艺卡片
图3-1平面铣削练习
1.分析零件工艺性能
图3-1所示零件,外形尺寸长×宽×高=100×80×20,属于小零件。
高度尺寸为自由公差,大平面表面粗超度为Ra3.2。
2.选用毛坯或明确来料状况
所用材料:
45
半成品外形尺寸:
101×81×21,六面全部进行粗加工。
3.确定装夹方案
选用机用平口虎钳装夹工件。
底面朝下垫平,工件毛坯面高出钳口12mm,夹80两侧面;100任一侧面与虎钳侧面取平夹紧,实际上限制六个自由度,工件处于完全定位状态。
4.确定加工方案
由于该零件已进行粗加工,因此采用端面铣刀直接进行精加工。
加工方案及选用刀具见表3-1。
表3-1加工方案与刀具选择
序号
加工方案
刀具
刀具号
1
精铣平面
面铣刀
T1
5.填写工艺卡片
工艺卡片见表3-2。
表3-2凸块数控加工工序卡片
数控实训基地
数控加工工序卡片
产品名称或代号
零件名称
材料
零件图号
平板类零件
凸块
45
30-3001
工序号
程序编号
夹具名称
夹具编号
使用设备
车间
31
O0001
机用平口虎钳
200
VDF850
数控实训基地
工步号
工步内容
刀具号
刀具规格
主轴转速
(r/min)
进给速度
(mm/min)
背吃刀量
(mm)
量具
备注
1
精铣大平面
T1
面铣刀
600
120
0.5
游标卡尺
编制
审核
共页
第页
(二)选用刀具
高速钢面铣刀一般用于加工中等宽度的平面,标准铣刀直径范围为
,硬质合金面铣刀的切削效率及加工质量均比高速钢铣刀高,故目前广泛使用硬质合金面铣刀加工平面。
图3-2所示为整体焊接式面铣刀。
该刀结构紧凑,较易制造。
但刀齿磨损后整把刀将报废,故已较少使用。
图3-3为机夹焊接式面铣刀。
该铣刀是将硬质合金刀片焊接在小刀头上,再采用机械夹固的方法将刀装夹在刀体槽中。
刀头报废后可换上新刀头,因此延长了刀体的使用寿命。
图2-38a为可转位面铣刀。
该铣刀将刀片直接装夹在刀体槽中。
切削刃用钝后,将刀片转位或更换刀片即可继续使用。
可转位铣刀与可转位车刀一样且有效率高、寿命长、使用方便、加工质量稳定等优点。
这种铣刀是目前平面加工中应用最广泛的刀具之一。
可转位面铣刀已形成系列标准,可查阅刀具标准等有关资料。
图3-2整体焊接式面铣刀图3-3机夹焊接式面铣刀
(三)操作过程
在对水平面铣削前,一般还没有进行工件坐标系的设定(即还没有进行“对刀”),因此水平面的铣削加工在MDI(A)方式下进行。
其操作过程为:
1.工件装夹完毕后,把面铣刀刀柄装入数控机床主轴。
2.选择MDI(A)方式,进入图1-20、图1-51、图1-76操作界面,输入“M3S600”后,按“启动”。
3.转到手动方式,利用手持单元选择X、Y轴移动,使面铣刀处在图3-4中A上方的位置;选择Z轴使面铣刀下降(图3-5所示),当面铣刀接近工件表面时,把手持单元的进给倍率调到“×10”,然后继续下降,当进入切削后,根据工件上表面平整及粗糙度情况确定切深(背吃刀量
,一般取0.3~0.5mm)。
4.再次进入MDI(A)方式,输入加工程序后按“启动”进行切削加工。
图3-4铣平面刀具移动轨迹图3-5铣平面时的下刀与背吃刀量
(四)程序编制
G54G91M3S600;
G1X150F120;
Y40;
X-160
G0Z200;
M30;
说明:
在华中系统中,只能一段一段输入执行。
模块二侧平面的铣削
一、教学目标
通过学习能进行侧平面的数控铣削。
二、终极学习目标
1.会制定侧平面加工方案;
2.会选用侧平面加工刀具。
三、工作任务
编制如图3-1中100×80×8的侧平面铣削程序,并进行铣削加工。
四、相关实践知识
(一)填写数控工艺卡片
1.分析零件工艺性能
如图3-1中长度尺寸和宽度尺寸为自由公差,侧平面表面粗糙度为Ra3.2。
2.选用毛坯或明确来料状况
所用材料:
45
半成品外形尺寸:
101×81×21,六面全部已进行粗加工。
3.确定装夹方案
同上。
4.确定加工方案
由于单边的切削用量为0.5mm,所以直接采用立铣刀进行精加工。
加工方案及选用刀具见表3-3。
表3-3加工方案与刀具选择
序号
加工方案
刀具
刀具号
1
精铣侧平面
立铣刀
T2
5.填写工艺卡片
工艺卡片见表3-4。
表3-4凸块数控加工工序卡片
数控实训基地
数控加工工序卡片
产品名称或代号
零件名称
材料
零件图号
平板类零件
凸块
45
30-3001
工序号
程序编号
夹具名称
夹具编号
使用设备
车间
32
O0002
机用平口虎钳
200
VDF850
数控实训基地
工步号
工步内容
刀具号
刀具规格
主轴转速
(r/min)
进给速度
(mm/min)
背吃刀量
(mm)
侧吃刀量
(mm)
量具
备注
1
精铣侧平面
T2
立铣刀
400
100
0.5
2
游标卡尺
编制
审核
共页
第页
(二)选用刀具
立铣刀(图2-38b)主要用在立式数控机床上加工凹槽、阶台面。
立铣刀圆周上的切削刃是主切削刃,端面上的切削刃是副切削刃,故切削时一般不宜沿铣刀轴线方向进给。
(三)操作过程
对于侧平面的铣削加工,在进行“对刀”、刀具半径补偿和工件坐标系设置的情况下是很方便的。
我们这儿介绍的方法,是在没有任何设置的情况下所进行的操作,同样在MDI(A)方式下进行。
其操作过程为:
1.工件装夹完毕后,把
立铣刀刀柄装入数控机床主轴。
2.选择MDI(A)方式,输入“M3S400”后,按“启动”。
3.转到手动方式,利用手持单元选择X、Y轴移动,使立铣刀处在图3-6中A上方的位置;选择Z轴使立铣刀下降到工件上表面以下约5mm处;选择Y轴,沿“-Y”移动刀具,使刀具逐渐靠近工件,当立铣刀接近工件侧面时把手持单元的进给倍率调到“×10”,然后继续移动,当出现微量切屑时停止移动;选择Z轴,沿“+Z”抬刀,并记下当前的Y轴机床坐标值。
4.选择X、Y轴移动,使立铣刀处在图3-6中B上方的位置;选择Z轴使立铣刀下降到工件上表面以下约5mm处;选择X轴,沿“+X”移动刀具,使刀具逐渐靠近工件,当立铣刀接近工件侧面时把手持单元的进给倍率调到“×10”,然后继续移动,当出现微量切屑时停止移动;并记下当前的X轴机床坐标值。
5.选择X、Y轴移动,使立铣刀处在图3-6中C上方的位置;选择Z轴使立铣刀下降,当立铣刀接近工件表面时,把手持单元的进给倍率调到“×10”,然后继续移动,当出现微量切屑时停止移动,并记下当前的Z轴机床坐标值。
6.选择Z轴,沿“+Z”抬刀后选择X、Y轴,使刀具移动到前面所记的X、Y轴机床坐标值位置(图3-6中D的上方);选择Z轴,同样使Z轴到前面所记的机床坐标位置。
7.再次进入MDI(A)方式,输入加工程序后按“启动”进行切削加工,其切削轨迹见图3-7。
图3-6侧平面铣削确定起刀位置图3-7侧平面铣削走刀轨迹
(四)程序编制
G54G91M3S400;
G00Z-8;
G1X0.5Y-0.5F100;
X116;
Y-96;
X-116;
Y110;
G0Z200;
M30;
说明:
在华中系统中,只能一段一段输入执行。
课题二对刀、刀具补偿及工件坐标系设置
模块一对刀操作
通过一定的方法把工件坐标系原点(实际上是工件坐标系原点所在的机床坐标值)体现出来,这个过程称为“对刀”。
在对刀前首先要把工件六个平面铣好(起码夹住的侧面应铣平);其次按工件定位基准面与机床运动方向一致的要求把工件定位装夹好;再次(如果工件表面没有精加工)用面铣刀把工件上表面铣平。
一、用铣刀直接对刀
用铣刀直接对刀,就是在工件已装夹完成并在主轴上装入刀具后,通过手持单元操作移动工作台及主轴,使旋转的刀具与工件的前(后)、左(右)侧面及工件的上表面(图308中1~5这五个位置)作极微量的接触切削(产生切削或摩擦声),分别记下刀具在作极微量切削时所处的机床坐标值,对这些坐标值作一定的数值处理后就可以设定工件坐标系了。
图3-8用铣刀直接对刀图3-9用铣刀直接对刀时的刀具移动图
操作过程为(针对图3-8中1的位置):
1.工件装夹并校正平行后夹紧。
2.在主轴上装入已装好刀具的刀柄。
3.在MDI(A)方式下,输入M3S300,按<循环启动>,使主轴的旋转。
4.换到手动方式,使主轴停转。
手持盒上选择Z轴(倍率可以选择×100),转动手摇脉冲发生器,使主轴上升的一定的位置(在水平面移动时不会与工件及夹具碰撞即可);分别选择X、Y轴,移动工作台使主轴处于工件上方适当的位置(如图3-9中A)。
5.手持盒上选择X轴,移动工作台(图3-9中①),使刀具处在工件的外侧(图3-9中B);手持盒上选择Z轴,使主轴下降(图3-9中②),刀具到达图3-9中C;手持盒上重新选择X轴,移动工作台(图3-9中③),当刀具接近工件侧面时用手转动主轴使刀具的刀刃与工件侧面相对,感觉刀刃很接近工件时,启动主轴使主轴转动,倍率选择×10或×1,此时应一格一格地转动手摇脉冲发生器,应注意观察有无切屑(一旦发现有切屑应马上停止脉冲进给)或注意听声(一般刀具与工件微量接触切削时会发出“嚓”、“嚓”、“嚓”…的响声,一旦听到声音应马上停止脉冲进给),即到达了图3-9中D的位置。
6.手持盒上选择Z轴(避免在后面的操作中不小心碰到脉冲发生器而出现意外)。
记下此时X轴的机床坐标或把X的相对坐标清零。
7.转动手摇脉冲发生器(倍率重新选择为×100),使主轴上升(图3-9中④);移动到一定高度后,选择X轴,作水平移动(图3-9中⑤),再停止主轴的转动。
图3-8中2、3、4三个位置的操作参考上面的方法进行。
在用刀具进行Z轴对刀时,刀具应处在今后切除部位的上方(如图3-9中A),转动手摇脉冲发生器,使主轴下降,待刀具比较接近工件表面时,启动主轴转动,倍率选小,一格一格地转动手摇脉冲发生器,当发现切屑或观察到工件表面切出一个圆圈时(也可以在刀具正下方的工件上贴一小片浸了切削液或油的薄纸片,纸片厚度可以用千分尺测量,当刀具把纸片转飞时)停止手摇脉冲发生器的进给,记下此时的Z轴机床坐标值(用薄纸片时应在此坐标值的基础上减去一个纸片厚度);反向转动手摇脉冲发生器,待确认主轴是上升的,把倍率选大,继续主轴上升。
用铣刀直接对刀时,由于每个操作者对微量切削的感觉程度不同,所以对刀精度并不高。
这种方法主要应用在要求不高或没有寻边器的场合。
图3-10光电式寻边器对刀图3-11偏心式寻边器对刀
二、用寻边器对刀
用寻边器(图1-113a、b)对刀只能确定X、Y方向的机床坐标值,而Z方向只能通过刀具或刀具与Z轴设定器(图1-113c)配合来确定。
图3-10为使用光电式寻边器在1~4这四个位置确定X、Y方向的机床坐标值;在5这个位置用刀具确定Z方向的机床坐标值。
图3-11为使用偏心式寻边器在1~4这四个位置确定X、Y方向的机床坐标值;在5这个位置用刀具确定Z方向的机床坐标值。
使用光电式寻边器时(主轴作50~100r/min的转动),当寻边器S
球头与工件侧面的距离较小时,手摇脉冲发生器的倍率旋钮应选择×10或×1,且一个脉冲、一个脉冲地移动;到出现发光或蜂鸣时应停止移动(此时光电寻边器与工件正好接触。
其移动顺序参见图3-9),且记录下当前位置的机床坐标值或相对坐标清零。
在退出时应注意其移动方向,如果移动方向发生错误会损坏寻边器,导致寻边器歪斜而无法继续准确使用。
一般可以先沿+Z移动退离工件,然后再作X、Y方向移动。
使用光电式寻边器对刀时,在装夹过程中就必须把工件的各个面擦干净,不能影响其导电性。
a)b)c)d)
图3-12偏心式寻边器对刀过程图3-13偏心式寻边器内部结构
使用偏心式寻边器的对刀过程见图3-12。
图3-12a为偏心式寻边器装入主轴没有旋转时;图3-12b为主轴旋转时(转速为200~300r/min。
转速不能超过350r/min以上,否则会在离心力的作用下把偏心式寻边器中的拉簧拉坏而引起偏心式寻边器损坏)寻边器的下半部分在内部拉簧(见图3-13)的带动下一起旋转,在没有到达准确位置时出现虚像;图3-12c为移动到准确位置后上下重合,此时应记录下当前位置的机床坐标值或相对坐标清零;图3-12d为移动过头后的情况,下半部分没有出现虚像。
对于初学者最好使用偏心式寻边器对刀,因为移动方向发生错误不会损坏寻边器。
另外在观察偏心式寻边器的影像时,不能只在一个方向观察,应在互相垂直的两个方向进行。
三、用芯棒和塞尺对刀
使用芯棒和塞尺(图1-104)对刀同样只能确定X、Y方向的机床坐标值,而Z方向只能通过刀具或刀具与Z轴设定器配合来确定。
操作过程为(针对图3-14中1这个位置):
1.工件装夹并校正平行后夹紧;上表面铣平。
2.在手动方式下,把已装好芯棒的刀柄装入机床主轴。
3.通过手持盒,使芯棒到达工件的上方后,像图3-9中①、②、③这样的移动步骤,移动到1所在位置,当芯棒接近到工件侧面时,选择某一尺寸规格的塞尺(如0.02mm)放在芯棒与工件侧面之间,把倍率换到“×10”这一档,边使芯棒向工件移动边抽动塞尺,当塞尺无法抽动后停止芯棒的移动并记下此时X轴的机床坐标或把X轴的相对坐标清零。
图3-14用芯棒和塞尺对刀
图3-14中2、3、4三个位置的操作参考上面的方法进行。
模块二工件坐标系与刀具补偿的设置
一、对刀后的数值处理和工件坐标系G54~G59等的设置
通过对刀所得到的5个机床坐标值(在实际应用时有时可能只要3~4个),必须通过一定的数值处理才能确定工件坐标系原点的机床坐标值。
代表性的情况有以下几种:
图3-15对刀后数值处理关系图一图3-16对刀后数值处理关系图二
1.工件坐标系的原点与工件坯料的对称中心重合(图3-8)
在这种情况下,其工件坐标系原点的机床坐标值按以下计算式计算。
2.工件坐标系的原点与工件坯料的对称中心不重合(见图3-15)
在这种情况下,其工件坐标系原点的机床坐标值按以下计算式计算。
上式中a、b前的正、负号的选取参见表3-5。
表3-5不同位置a、b符号的选取
工件坐标系原点在以工件坯料对称中心所划区域中的象限
第一象限
第二象限
第三象限
第四象限
a取号
+
-
-
+
b取号
+
+
-
-
3.工件坯料只有两个垂直侧面是加工过的,其它两侧面因要铣掉而不加工(见图3-16)
在这种情况下,其工件坐标系原点的机床坐标值按以下计算式计算。
本组计算式只针对图3-16的情况,对其它侧面情况的计算可参考进行。
上面的数值处理结束后,进入图1-30、图1-63、图1-94的界面,分别在G54(或G55~G59)中X、Y的位置输入上面处理后的X工机和Y工机。
二、利用相对坐标清零功能进行工件坐标系G54~G59等的设置
1.FANUC0i-MC系统的操作
图3-17相对坐标显示界面图3-18工件坐标系测量界面
在图3-9、图3-10、图3-11、图3-14中,我们把在1号位时的X相对坐标清零(图1-19),到达2号位时我们可以从相对坐标的显示页面(图3-17)上知道其相对坐标值。
如果X轴的工件坐标系原点设在工件坯料的中心,我们只需按页面上X的相对坐标值去除2(完全可以心算),然后移动到这个相对坐标位置,我们进入图1-30所示页面,只需输入“X0”(图3-18),然后按[测量],系统会自动把当前所设置的X方向工件坐标系原点的机床坐标值输入到G54中X的位置。
也可以在2号位不动,同样把相对坐标值去除2,然后在图3-18中输入“X50.32”(假定计算出的值为50.32,即刀具中心当前位置在X轴的正方向,距离原点50.32),按[测量],系统会自动把偏离当前点50.32的工件坐标系原点所处的机床坐标值输入到G54中X的设置位置。
如果X轴的工件坐标系原点不在工件坯料的中心,我们仍可以移动到上面除2的位置,在图3-18页面中我们输入坯料中心在工件坐标系中的坐标值(如O在图3-15中的第一象限,a为30mm,那么我们应输入“X-30”);或在2号位直接计算出工件坐标系原点O与现在位置之间的距离,如为20.32,则输入“X20.32”,按[测量]后系统会自动计算出工件坐标系原点的机床坐标值并输入到G54等相应的设置位置。
Y轴的设置方法与上面相同。
在其它位置(如图3-9、图3-10、图3-11、图3-14中1号、3号、4号位)进行相对坐标值的直接设置时,应注意是X轴还是Y轴、在原点的哪个方向,即输入时是“+”还是“-”。
2.华中HNC-22M系统
在图3-9、图3-10、图3-11、图3-14中,我们把在1号位时的X相对坐标清零(图1-49),到达2号位时我们可以从相对坐标的显示页面上知道其相对坐标值;根据工件坐标系原点在工件上的位置算出相对坐标,再移动到这个相对坐标位置。
由于华中系统没有[测量]这一功能,所以只能在到达上面这个位置后,根据图1-63页面右侧的“机床实际坐标”的X值,输入到此界面的G54中。
Y方向的处理方法相同。
3.SINUMERIK802D系统
图3-19测量工件在左侧图3-20测量工件在右侧
对于SINUMERIK802D系统,在图3-9、图3-10、图3-11、图3-14中1号位时,进入如图1-92所示窗口,利用光标键选择
,按
使其变成
;继续利用光标键选择
,按
使其变成
,按
把X相对坐标清零,则图1-92变成图3-19;当到图3-9、图3-10、图3-11、图3-14中2号位时,利用光标键选择
,按
使其变回
,此时图3-19变成图3-20;假定工件坐标系原点设在工件的上表面中点,则在图3-20中,利用光标键选择
,然后输入X相对坐标的一半值“50.32”(在图3-20中,X的相对坐标值为100.64。
此时刀具在工件的右侧,相对工件坐标系原点来说是在X轴的正方向,所以输入“+”值。
其它位置请根据相对坐标清零及刀具位置的不同而定),按
后系统会自动计算出工件坐标系原点的机床坐标值并输入到G54等相应的设置位置(图1-94)。
Y方向的设置方法是在图3-19中按
,其它相同。
三、工件坐标系原点Z0的设定、刀具长度补偿量的设置
1.工件坐标系原点Z0的设定
在编程时,工件坐标系原点Z0一般取在工件的上表面。
但在设置时,工件坐标系原点Z0的设定一般采用以下两种方法:
方法一:
工件坐标系原点Z0设定在工件的上表面;
方法二:
工件坐标系原点Z0设定在机床坐标系的Z0处,图3-21所示。
在设置G54等时,Z后面为0。
对于第一种方法,必须选择一把刀具为基准刀具(通常选择在加工Z轴方向尺寸要求比较高的刀具为基准刀具),其它刀具通过与基准刀具的比较确定其长度补偿值。
这种方法在基准刀具和其它刀具都出现断刀的情况下,较难重新确定长度补偿值,因此对这种方法不推荐使用。
图3-21Z轴工件坐标系与长度补偿值的关系图3-22确定长度补偿值
对于第二种方法,不设定基准刀具,每把刀具都以机床坐标原点为基准(此基准对某一台数控机床而言,从出厂后是固定不变的)。
通过刀具在机床坐标原点所在位置到工件上表面位置之间的距离,来确定其长度补偿值(图3-21中的Z机,由于为“-Z”方向移动,所以补偿值一般为负),通过长度补偿后使其仍以工件上表面为编程时的工件坐标系原点。
确定长度补偿值的具体操作方法为:
(1)用Z轴设定器
①把Z轴设定器(图1-114c)放置在工件的水平表面上,主轴上装入已装夹好刀具的各个刀柄刀具(图3-22),移动X、Y轴,使刀具尽可能处在Z轴设定器中心的上方;
②移动Z轴,用刀具(主轴禁止转动)压下Z轴设定器圆柱台,使指针指到调整好的“0”位;
③记录每把刀具当前的Z轴机床坐标值(应该为当前机床坐标读数值减去Z轴设定器的标准高)。
如图3-22中T1刀,其记录的Z轴机床坐标值应为:
-175.12-50=-225.12;T2刀为:
-159.377-50=-209.377;T3刀为:
-210.407-50=-260.407。
(2)直接用刀具
①见前面“用铣刀直接对刀”中所述(图3-8中5)。
②刀具禁止转动,移动Z轴,当刀具接近工件上表面时,在刀具与工件之间放入塞尺(如0.02mm塞尺),边使刀具向下移动边抽动塞尺,当塞尺无法抽动后停止刀具的下降,并记下此时Z轴的机床坐标(应在此坐标值的基础上减去一个塞尺厚度)。
2.刀具长度补偿的设置
把上面所得到的每把刀具的Z轴机床坐标值,根据数控系统的不同,可分别输入到图1-29、图1-62、图1-87所示的界面中。
四、刀具半径补偿量及磨损量的设置
由于数控系统具有刀具半径自动补偿的功能,因此我们在编程时只需按照工件的实际轮廓尺寸编制即可,刀具半径补偿量设置在数控系统中相对应的位置。
刀具在切削过程中,刀刃会出现磨损(刀具直径变小),最后会出现外轮廓尺寸偏大、内轮廓尺寸偏小(反之,则所加工的工件已报废),此时可通过对刀具磨损量的设置,然后再精铣轮廓,一般就能达到所需的加工尺寸。
举例:
磨损量设置值
测量要素
要求尺寸
测量尺寸
磨损量设置值
A
100.12
-0.06~-0.087
B
55.86
-0.07~-0.085
注:
如果在磨损量设置处已有数值(对操作者来说,由于加工工件及使用刀具的不同,开机后一般需把磨损量清零),则需在原数值的基础上进行叠加。
例:
原有值为-0.07,现尺寸偏大0.1(单边0.05),则重新设置的值为:
-0.07-0.05=-0.12
如果精加工结束后,发现工件的表面粗糙度很差、且刀具磨损较严重,通过测量尺寸有偏差,此时必须更换铣刀重新精铣,此时磨损量先不要重设,等铣完后通过对尺寸的测量,再作是否补偿的决定,预防产生“过切”。
刀具半径及磨损量的设置操作:
1.对FANUC0i-MC系统,进入图1-29的界面,在每把刀具对应的“外形(D)”下,输入刀具的半径补偿量;在“磨损(D)”下,输入刀具的磨损量。
2.对华中HNC-22M系统,进入图1-62的界面,在每把刀具对应的“半径”下,输入刀具半径与磨损量的叠加值。
3.对SINUMERIK802D系统,进入图1-87的窗口,在每把刀具对应的“几何/半径”下,输