100mw汽轮发电机轴承座铸造工艺设计材料专业学位论文.docx
《100mw汽轮发电机轴承座铸造工艺设计材料专业学位论文.docx》由会员分享,可在线阅读,更多相关《100mw汽轮发电机轴承座铸造工艺设计材料专业学位论文.docx(40页珍藏版)》请在冰豆网上搜索。
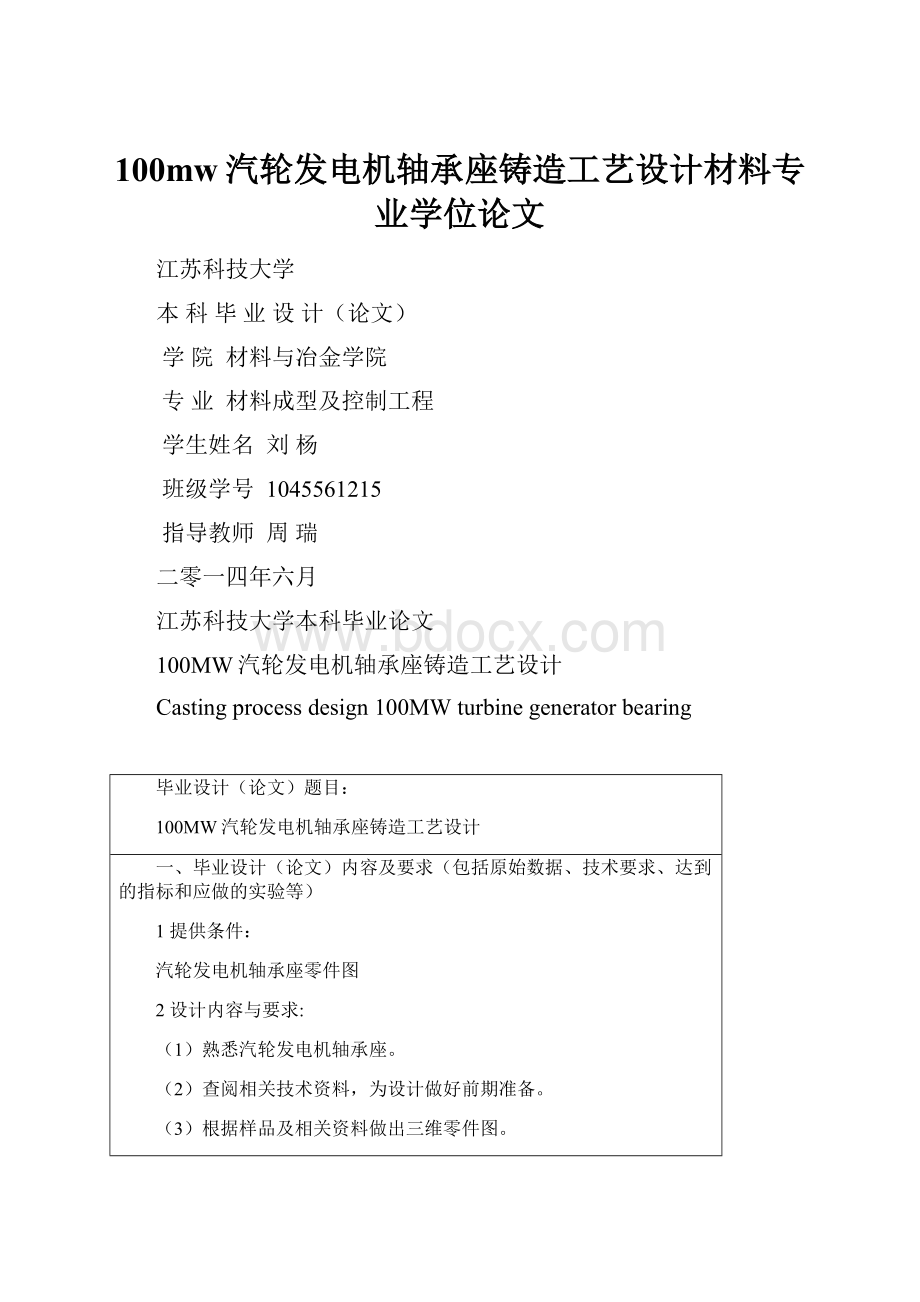
100mw汽轮发电机轴承座铸造工艺设计材料专业学位论文
江苏科技大学
本科毕业设计(论文)
学院材料与冶金学院
专业材料成型及控制工程
学生姓名刘杨
班级学号1045561215
指导教师周瑞
二零一四年六月
江苏科技大学本科毕业论文
100MW汽轮发电机轴承座铸造工艺设计
Castingprocessdesign100MWturbinegeneratorbearing
毕业设计(论文)题目:
100MW汽轮发电机轴承座铸造工艺设计
一、毕业设计(论文)内容及要求(包括原始数据、技术要求、达到的指标和应做的实验等)
1提供条件:
汽轮发电机轴承座零件图
2设计内容与要求:
(1)熟悉汽轮发电机轴承座。
(2)查阅相关技术资料,为设计做好前期准备。
(3)根据样品及相关资料做出三维零件图。
(4)提出工艺方案,并进行工艺设计。
3设计手段
设计手段:
查阅资料;设计二维零件图;提出并编写工艺方案;
二、完成后应交的作业(包括各种说明书、图纸等)
1.毕业设计论文一份(不少于1.5万字);
2.外文译文一篇(不少于5000英文单词,并附原文);
3.相关设计图纸。
三、完成日期及进度
自2014年3月5日起至2014年6月7日止进度安排:
3.5~3.16
文献检索与阅读;
3.16~5.23
设计与实验、提交开题报告和翻译文献;
5.23~6.04
撰写论文、提交论文;
6.04~6.06
论文评阅和修改;
6.07
答辩。
四、主要参考资料(包括书刊名称、出版年月等):
[1]蒋毓良.超超临界1000MW汽轮发电机轴承座的铸造质量控制[J].上海宏钢电站设备铸锻有限公司.2002:
[2]王秀瑾.百万千瓦级核电汽轮发电机轴承座刚度计算[J].上海发电设备成套设计研究院.2012
[3]南红艳.灰铸铁轴承座的两种铸造工艺方案数值模拟对比与选定[J].河南理工大学材料科学与工程学院.2012.11
[4]廖琼.轴承座铸造工艺方案研究及模拟[J].天津重型装备工程研究有限公司.2012
[5]王文清,李魁盛等.铸造工艺学(M).北京:
机械工业出版社.2002.10:
10-11
[6]李弘英.铸造工艺设计(M).北京:
机械工业出版社.2005.2:
1-3
[7]沈红卫.超临界900MW汽轮发电机轴承座铸件的铸造[J].上海汽轮机有限公司.2003.9
[8]许济群,蒋磊,叶青等.16V240ZB型柴油机铸钢主轴承座铸造工艺[J].1994
[9]冯景兰,付龙.大型铸钢件缩松改进实践[J].宁夏机械.2009,4:
91-94
[9]林工.树脂砂铸造工艺.树脂砂、V法、消失模造型线及单机[J].2011,10
[10]李日,刘百成,李文珍.温度梯度对致密厚壁铸钢件工艺设计的重要性[J].机械科学与技术.2004:
92-96
[11]杜西灵等.铸造技术与应用案例.机械工业出版社[M].2009:
1-5
[12]王文清等.铸造工艺学.机械工业出版社[M].2009:
83-90
[13]郭林.凝固模拟技术在轴承座铸造中的应用[J].济钢集团重工机械有限公司2011
[14]蒋志龙,李全勇,樊志勇.汽轮发电机轴瓦倾斜故障分析[J].中国设备工程.2013:
38-39.
[15]张建国.390MW燃汽轮发电机轴瓦制造工艺[J].上海大中型电机.2006.4:
9.
系(教研室)主任:
(签章)年月日
学院主管领导:
(签章)年月日
摘要
全球经济在飞速发展的热潮中,现代对汽轮发电机的需求越来越高。
汽轮发电机是指用汽轮机驱动的发电的机器,是一种将机械能转化成电能的机器,这项工作由蒸汽投入机器中扩张做功,让叶片转动从而推动产生电。
汽轮发电机一般是由定子、转子及轴承座等部件构成,所以轴承座的铸造是制造汽轮发电机的重要工艺流程。
而合适的汽轮发电机轴承座的铸造工艺不仅能提高电机的性能,也能延长它的使用寿命。
本文完成了对ZG230-450铸钢件铸造工艺设计,首先要先确定轴承座尺寸2700×1345×945,浇注位置和分型面,采取一箱一件造型方式进行生产。
包括浇注系统、砂芯的设计、工艺参数的确定。
设计模样、芯盒和砂箱,设计砂芯的可行性方案,以及对浇注时候可能出现的缺陷进行分析,从而对铸件工艺进行优化。
关键词:
汽轮发电机轴承座;铸钢;铸造工艺设计
Abstract
Therapiddevelopmentoftheglobaleconomyintheboom,themodernincreasinglyhighdemandforsteamturbinegenerator.Turboreferstoaturbinedrivenpowergeneratingapparatus,amechanicalenergyintoelectricalenergymachine.Bythesteamintotheturbineexpansionwork,sothatthebladesrotatepromptinggenerators.Turbogeneratorgenerallystator,rotorandbearingcomponentssuchasconstitution,itisanimportantbearingcastingprocessmanufacturingturbinegenerator.Theturbo-generatorhousingssuitablecastingprocesscannotonlyimprovetheperformanceofthemotor,butalsotoextenditsservicelife.
Thispapercompletedthedeterminationof100MWturbinegeneratorbearingcastingprocessdesign,includingtheselectionofsub-surfacesystemsandpouringsandcoredesign,processparameters.Designlookslike,coreboxesandsandbox,revealingtheproducelooseshrink,shrinkagecausesthesiteandthusthecastingprocessoptimization.
Keywords:
turbinegeneratorbearing;caststeel;castingprocessdesign
第一章绪论
1.1本课题的研究背景
随着世界各国经济发展迅速的趋势,人类对于电能的运用和需求也就显得尤为重要。
电能是我们生活的必要资源,它其实是容易获得、干净和经济的动力是国民经济发扬的因素。
近几年,经济持续快速增长,与此同时,我国的经济发展与资源利用的矛盾日益突出。
而很多的城市持续加深发电高效行使和广泛管制。
1.2本课题研究发展现状
目前我国主要的发电方式是火力发电,火力发电按照它的作用可以分为两大类:
供电和供热。
顾名思义,原动机就是提供动力,汽轮机作为火力发电的三大重要的原动机之一,为我国的火电行业提供了有力地保障。
所以在我国庞大电力市场,发电技艺必须持续的提升,就能让相关设备更有效快速发展。
铸造工艺生产出的零件毛坯已经大致的成性,只需进行简单的精加工即可,从而简化了工序,价格也降低了。
所以说汽轮发电机轴承座的各种性能与铸造工艺密不可分。
1.3本课题的研究目的与意义
轴承座目的是能让它的外圈固定,只使内圈旋转,一直与传输方向一样,并且还能够保持平衡状态。
这就表明轴承座是机器正常工作的重要影响因素。
轴承座的主要应用于工农业,另外也应用于交通业、航空航天业等,足以证明轴承座在现代各行各业中的重要作用。
轴承座的概念就是轴承与箱体的集合体,方便运用,这样的好处是可以有更好的配合,更便捷有效,减少企业的使用成本。
至于轴承座外形,大多数有一个箱体,轴承就是安装在里面,但是本课题设计的是多箱体。
轴承主要分为:
分离轴承、外球面轴承、法兰轴承、滑动轴承、滚动轴承等,他们也都有其相应的轴承座。
本毕业设计的题目是:
100MW汽轮发电机轴承座的铸造工艺设计。
可以通过阅读书籍资料,依据轴承使用机能剖析决定浇注位置、分型面的选取要领、工艺参数、砂芯设计等进行研究。
1.4铸造概述
铸造工艺是机器生产的根蒂而且很紧要的的方式。
铸造的工艺方法有着悠久的历史,其中我国就有很丰富的铸造经验。
随着现代工业的规模不断扩大,大型铸件的铸造质量很大程度上影响着出厂产品内部的核心质量,因此,铸造在工业制造中占起着举足轻重的地位。
由于现代工业对铸造质量、精确度、成本和自动化要求的提高,铸造工艺正在向着精确化、质量体系化、自动化和环保化的方向迈进。
铸造是将通过熔化的金属液体浇注入型腔内,然后冷却凝固后达到预定的形状和性能产品的制作过程。
它是很实用的生产方式,在低价格、方法比较灵便的特征下,可以获得各类繁杂外形或者大型铸件,所以这样有有优势的特性,较为准确的优点,美观的外表已经成为成为铸件的发展趋势。
所以,目前多数轴承座就是运用铸造方式获得。
1.5铸造的特点
铸造生产是将液态金属注入型腔中,经降温、固态成型,这类生产金属方法叫做铸造。
铸造生产具有以下特点:
(1)适用性强:
铸造工艺一般对零件的大尺寸、重量、材料型号(厚度)、和复杂性没有太多要求,所以说它的适用性强。
很复杂的铸件都可以铸造出来。
(2)适用的范围广:
像铸铁、铸钢还有很多种类的材料都可以使用铸造进行生产。
(3)铸件的尺寸精度高:
铸件的尺寸一般要比锻件、焊接件的更加精确,这样产生的废料就会很少,可以有效地节约金属材料和机械加工的时间。
1.6铸造方法的分类
(1)砂型铸造
砂型铸造是一种很普遍的铸造方法。
铸钢件、铸铁件等都可以通过这种方法生产。
砂型铸造能够适应大、中、小批量的生产特点,而且操作简单。
因此,砂型铸造一直是铸造生产中的主要铸造方法。
所以砂型铸造可以作为本课题轴承座设计的备选铸造方法。
(2)金属型铸造
金属型不仅能采取重力铸造,还能利用压力铸造。
金属型的铸型模具能够循环使用,使用寿命长,生产效率很高。
金属型的铸件优点是不仅尺寸精度高。
但是,金属型铸造也是有缺陷的:
因为此铸件材料的熔点很高,所以一般不被选用。
对于小批量生产加工的话,金属型的模具价格很高;而且金属型铸造的模具受材料尺寸等条件的限制,对于大的铸件无法加工。
几乎不用金属型铸造生产大量同批产品。
所以本课题研究的轴承座不会采用这种方式。
(3)压力铸造
压铸是当今效能最高的铸造方法。
它有热室和冷室的两种。
长处:
(1)它的自动化水准较高,原料损耗少。
(2)它的机器加工余量放的小一点,0.5毫米上下就行,一方面可以减少生产成本,也可以避免破坏表面致密层。
弊端:
(1)受到加工工具耐热性的影响,现在唯独可在熔点低一点的原料上生产。
(2)铸造熔融金属在高速灌装的状态下,在一个很大压力下成型,所以腔中的气体容易涂抹在铸件的内部出现孔隙。
基于以上分析压力铸造不能用于生产本课题设计的轴承座铸造方法。
(4)熔模铸造
我国将熔模铸造应用于工农业生产,取得极大的发展。
熔模铸造是一种几乎没有切削加工余量的铸造方法,甚至有时一些铸件只需要留有很少的打磨、抛光余量,不需要再进行机械加工,因而得到了非常广泛的应用。
优点在于它不仅能够适用于各种材料的铸造,而且生产出的铸件尺寸精度比其它铸造方法都要高,甚至可以生产很多结构非常复杂的和耐热性强的铸件。
熔模铸造铸件粗糙度至少有Ra0.63~1.25um,比其他1-3点方法的高。
可是因为它的工艺进程繁杂,很多情况破坏铸件尺寸精度。
比如收缩性、变形等原因。
汽轮发电机轴承座的精度要求高,铸造过程中不允许有变形,所以不采用熔模铸造方法。
所以选用砂型铸造设计此轴承座。
1.7铸造工艺设计的原则
随着科技进步,我们对铸件的质量也在提高:
(1)表面粗糙度要低,性能要好;
(2)还要拥有一些特殊的机能,像耐腐、耐热性;
(3)铸件要有合适的厚度,这样可以防止浇不到、冷隔等缺陷,但也不能设计的太厚;
(4)设计时注意铸件的结构特点,不能造成较大的收缩阻碍,多用一些圆角来解决此问题;
(5)铸件的内壁要比外壁薄一些,目的就是都能均匀的冷却;
(6)避免各种情况的变形;
(7)设计注意达到按顺序凝固;
(8)要求生产工时少,成本也不能很高。
因此,铸件在生产之前,铸造工艺设计很有必要。
此次设计便是凭借此轴承座图纸的规格尺寸特征,以及工艺流程规定,采取有优势的方案,进而确定一些参数,制作工艺等技术文件的过程。
1.8确定浇注位置的一般原则
(1)铸造时下面和侧面一般放置零件工作面,避免各种缺陷;
(2)浇注位置应有利于所确定的凝固顺序,对于凝固体收缩率较大的铸造合金,应尽量满足顺序凝固原则,铸件厚实部分应尽可能至于上方,利于设置冒口补缩;
(3)浇注位置应有利于砂芯的定位、固定和排气;
(4)平面要放在下部或倾斜位置,用来避免各种缺陷。
有时为了方便造型,可采用“横做立浇”、“平做立浇”的方法;
(5)铸件的薄壁部分应置于铸件的底部或侧面,以防浇不到、冷隔等缺陷;
(6)大批量生产时尽量减少飞翅和毛刺;
(7)要避免厚实铸件冒口下面的受力面产生偏析;
(8)尽量使冒口置于加工面上,以减少铸件清理工作量。
1.9分型面的选择原则
铸件分型面的选择一般要遵循以下原则:
(1)尽量将铸件的全部或大部分放在同一箱内,以减少错型和不便于验型而造成的尺寸偏差;
(2)尽量将加工定位面和主要加工面放在同一箱内,以减少加工定位的尺寸偏差;
(3)尽量减少分型面数量,在机器造型中一般采用一个分型面;
(4)在机器造型中,应尽量不使用活块,必要时用砂芯取代模样拆活;
(5)尽量减少砂芯数量;
(6)尽量使分型面为平面,必要时也可不做成平面;
(7)为了方便起模,分型面应在铸件的最大截面处,对于较高的铸件,尽量使铸件在一箱内不过高;
(8)在大量生产时,分型面的选择应有利于铸件的清除;
(9)选择分型面应考虑到造型方法的不同。
1.10铸造工艺设计的内容和步骤
1.10.1本课题研究的内容
(1)绘制100MW汽轮发电机轴承座铸件零件图。
(2)设计确定铸造工艺方案。
(3)了解轴承座的铸件结构和技术特点;
(4)CAD和SolidWorks绘图。
(5)浇注系统,分型面选择工艺参数,分析设计过程;
(6)改善产品缺陷,达到优化设计的目的;
(7)根据铸造工艺方案作出设计说明。
1.10.2本课题设计的步骤
(1)确定合理的铸造工艺
顾名思义,一个好的铸造工艺方案不仅提高生产效率,而且很大程度上提高产品质量。
有许多铸造型,选取合理的工艺是产品质量的前提;主要依据有轴承座材料的选择、结构的设计与技术要求也很重要。
以及生产批量的大小,在现有的条件下生产的铸造工艺条件的选择,最主要的设计就是这种浇注位置、分型面选择等适不适合100MW汽轮发电机轴承座的生产,从而确定铸造工艺方案。
(2)铸造工艺参数的设计计算
铸造工艺参数有着很重要的功用,这个步骤主要包括
(1)铸件最小铸出壁厚;
(2)铸件最小铸出孔与槽;(3)铸件尺寸公差;(4)机械加工余量;(5)铸造收缩率;(6)起模斜度;(7)浇注系统的形式和位置;(8)工艺补正量及反变形量;(9)浇冒口的切割余量等。
(3)砂芯的设计
砂芯设计满足强度高,铸件形成可以及时的排出气体,铸件的收缩性的要求是足够小,易于清洗。
任务主要是砂芯尺寸、定位个数、芯头大小、砂芯排气系统等。
(4)浇注系统设计
浇注系统是熔融金属填充到型腔模具的路径。
由浇口杯、直浇道、横浇道和内浇道组成的它。
虽然类型很多,不过设计它们的目的和依据都一样:
保证熔融金属能够均匀、连续的、稳定的进入型腔,并能够有效地阻止熔渣和气体进入。
要求说明浇道类型及其各种参数。
(5)出气孔设计
排气通常是放在浇注位置法兰或简单的空气阻力对表面的最高点。
它按照能否与空气接触,可以分成明和暗出。
(6)补缩系统设计
铸件从液态变为固态时候,会发生收缩。
导致容易在铸件的内部产生缩孔等缺陷。
补缩系统就是可以在金属液凝固前给其填补液体,这需要冒口合理。
(7)铸造工艺装备设计
铸造工装就是在做合箱时要用到的所有工具的总称。
要求造价不高、容易获得。
第二章轴承座工艺性分析
2.1汽轮发电机轴承座
图2-1发电机轴承座立体图
2.2轴承座铸造方法的选定
轴承座生产特点是大批量生产,材料选取ZG230-450,汽轮发电机轴承座主要生产要求比较高,不能受到铸造中经常出现的各类缺陷的影响,并且要能符合ZG230-450的材料规定。
现代经常利用而且很容易操作的方法就是砂型铸造。
它可以用于生产尺寸相对大一些的零件,而且生产必备的砂子等其他用料价格便宜。
另外,生产操作的方式比其它几种铸造方法简便点,能够适应批量生产的能力。
100MW汽轮发电机轴承座的质量约为7吨,尺寸较为庞大,基于以上观点,我选用砂型铸造。
此轴承座尺寸为:
是大型铸钢件,且是关键性零部件,要求高标准的尺寸精度,所以铸造过程中必须排除一切变形因素,例如砂芯的变形、膨胀变形、碰伤等。
呋喃树脂砂强度很高,热稳定性好;无需烘干节约了能源成本;而且砂芯固化后就起模,减少振动和碰伤,恰恰可以排除上述的各种变形因素;另外呋喃树脂砂生产的产品规格精确度要有所改善;呋喃树脂砂的流动性很好,无需再去紧实,所以说它的造型效率较高;故我选用砂型铸造,呋喃树脂砂。
2.3轴承座铸造材料
本课题所给的零件是100MW汽轮发电机轴承座部分。
轴承是它与外壳的集合,为了方便操作,优点是便捷,是轴承座达到作用的重要部分。
轴承座能够保持平衡状态依靠固定的轴承,轴承的外环不能动达到此目的。
所以我们一般考虑的是轴承座的抗振动与抗冲击能力、导热系数、耐磨损能力、耐热与防腐能力等。
基于轴承座以上的性能要求,我们通常选择铸造方法生产轴承座,材料一般从铸钢、铸铁、不锈钢等材料中选择。
一般普通的轴承座选用的是铸铁材料,虽然铸铁的价格相对要低一些,但是它生产出铸件的各种性能和耐用性不是很高;不锈钢轴承座一般用于酸碱度较强的海水里,不易失灵。
而铸钢的力学、化学性能更好,因此使用寿命更长,耐用性能好,铸钢的优点:
设计具有灵活性,节约时间;拥有比较好的实用性和灵活性;可以适应大批量大型生产。
综上所述,以及查资料知道:
铸钢件的综合力学性能都胜过其他任何铸造合金,其中ZG230-450对夹杂物的限制要求较为严格,230指的是这种铸钢件的屈服强度为230MPa,450指的是这种材质的抗拉强度为450MPa。
化学成分:
0.20%~0.30%C;0.20%~0.50%Si;0.50%~0.90%Mn;≤0.04%P、S;≤0.03%Cu。
表2-1ZG230-450疲劳值
σ-1/MPa
σ-Jav/MPa
σ-1rms/MPa
Emax/MPa
202.47,198.97,208.70
210.59,203.21,208.52
207.50,212.24
206.52
4.5266
0.4772
铸钢的铸态组织如图2-2所示
图2-2铸钢铸态组织
碳钢的铸态组织:
(1)细等轴晶区
(2)柱状晶区(3)粗晶区
液态钢在凝固的时候,在其断面上的奥氏体会沿着这个断面温度方向长成不同形状的晶粒。
这三个晶区的厚度将会随着材料的不同及冷却的条件不同而发生改变。
铸件的降温速度随着厚度的增大而减小,所以其柱状、粗晶区就更发达。
ZG230-450的塑性不错,有高熔点,被切削性也不错,可以直接在机器上生产不需要热处理。
2.4轴承座工艺分析
该零件外形规格是1345×2700毫米。
外观上它是对称排布。
零件的底部有空腔,中间位置是肋。
另外两侧2个对称的190毫米凸台,前侧有一个高25毫米凸台,凸台两侧对称分布着2个宽度是100毫米筋。
工艺分析:
(1)此轴承座各部分的尺寸相对较大,因此不存在低于最小壁厚的问题;
(2)很多壁厚的地方都有不同大小的圆角避免掉应力集中导致的裂纹;(3)轴承座底部比较厚,而且尺寸大,存在热节,要考虑到补缩问题,避免变形。
2.5加工面选择
因为我们都知道铸件做容易出现缺陷的地方就是朝上的面,四周和下表面就比较平整,所以我选择的加工面就是朝上的面,这样还一个好处就是避免凹陷。
如图2-3
图2-3加工面
第三章工艺方案的确定
3.1浇注位置的选择
首先,此轴承座规格很大,精确度必须提高。
其次,要避免各种缺陷,得到高质量铸件,而且浇注的位置要能够达到顺序凝固。
因此,设计在底座比较厚的位置。
底座在上的浇注方法。
从底到上凝固,让工作面处得以充分补缩。
综上考虑,浇注位置选取如图3-1所示。
图3-1浇注位置选择
3.2分型面选择
方案如图3-2所示。
图3-2分型面选择
方案分析:
采取此方案,铸件在箱里就不会太高。
底部较厚的位置,浇注时间比较长,为了有助补缩,采取顶注式浇注。
另外,该轴承座尺寸较大:
2700mm×1345mm×945mm,质量也很大,将近7吨,内部结构也很复杂,所以采用一箱一件。
3.3砂箱尺寸确定
砂箱长度和宽度应该是50或100mm的倍数,高度应该是20或50mm的倍数。
图3-3模样平均轮廓吃砂量
表3-1模样平均轮廓吃砂量
模样平均轮廓尺寸
a
b和c
d
滑脱砂箱≤400
≥20
30~50
1/2模样高度
30~50
40~70
400~700
50~70
70~90
1/2-3/2模样高度
701~1000
71~100
91~120
1001~2000
101~150
121~150
2001~3000
151~200
151~200
3001~4000
201~250
201~250
>4000
251~500
>250
选取砂箱尺寸为:
上箱3200×1800×650mm;下箱:
3200×1800×1000mm。
第四章轴承座铸造工艺参数
工艺参数的定义是拟定基本规格索引在生产之前,获得的所有数据对生产做出明确限制,达到按照指导标准生产的效果。
4.1铸件的尺寸公差
就是说的2组可变动的公称数值的最大和最小差值。
如果产品的最后实际尺寸位于2个差值之间,那么就可以获得满足机械化、使用性能的零件。
现有CT1~16级的尺寸公差,如表4-1及4-2所示。
表4-1公差等级
造型方式
公差的等级
铸件材料
灰铸铁
铸钢
球墨铸铁
铜合金
砂型铸造手工造型
11~14
11~14
10~13
10~13
砂型铸造机械造型
8~12
8~12
8~12
8~10
选用机械造型,铸钢材料,8-12级,故选用CT12。
表4-2铸件尺寸公差数值
铸件基本尺寸
公差等级CT
8
9
10
11
12
>1000~1600
3.2
4.6
7
9
1