26000吨年PVC生产车间工艺流程设计.docx
《26000吨年PVC生产车间工艺流程设计.docx》由会员分享,可在线阅读,更多相关《26000吨年PVC生产车间工艺流程设计.docx(18页珍藏版)》请在冰豆网上搜索。
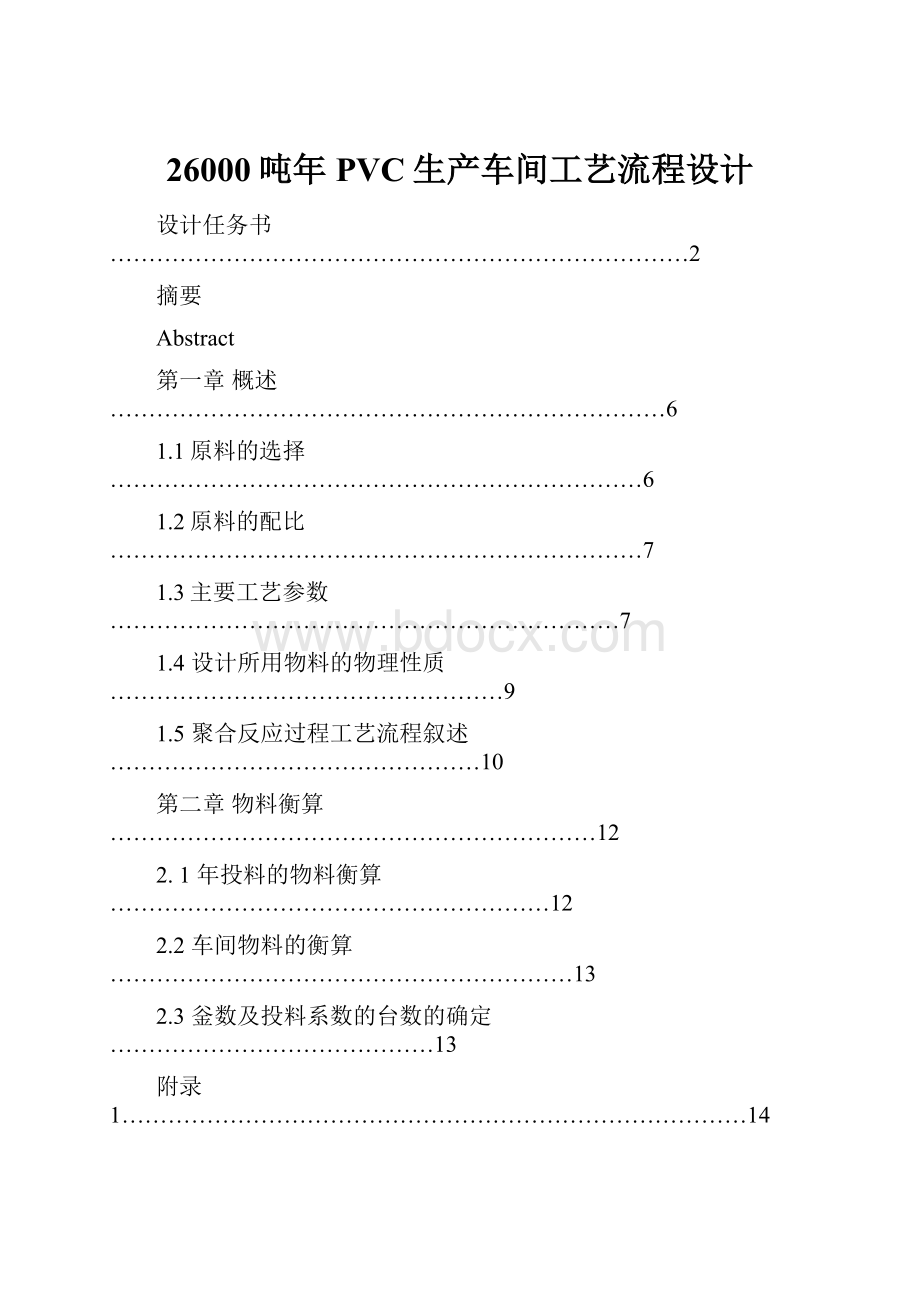
26000吨年PVC生产车间工艺流程设计
设计任务书…………………………………………………………………2
摘要
Abstract
第一章概述………………………………………………………………6
1.1原料的选择……………………………………………………………6
1.2原料的配比……………………………………………………………7
1.3主要工艺参数…………………………………………………………7
1.4设计所用物料的物理性质……………………………………………9
1.5聚合反应过程工艺流程叙述…………………………………………10
第二章物料衡算………………………………………………………12
2.1年投料的物料衡算…………………………………………………12
2.2车间物料的衡算……………………………………………………13
2.3釡数及投料系数的台数的确定……………………………………13
附录1………………………………………………………………………14
第三章热量衡算………………………………………………………15
附录2………………………………………………………………………15
第四章设备工艺设计…………………………………………………15
4.180m3不锈钢聚合釡………………………………………………15
4.2汽提塔………………………………………………………………16
4.3混料槽………………………………………………………………16
4.4离心机………………………………………………………………16
4.5干燥器………………………………………………………………17
附录3………………………………………………………………………17
参考文献……………………………………………………………………18
摘要Abstract(略)
第一章概述
1.1原料的选择
1、单体
表1.1单体指标
纯度,%
水,μg/g
铁,μg/g
醛,μg/g
低沸物,μg/g
高沸物,μg/g
≥99.98
≤100
≤0.5
≤3
≤10
≤50
2、去离子水
表1.2去离子水指标
控制项目
导电率
PH
二氧化硅
指标
<10μs/cm
5~8.5
<0.2mg/L
3、引发剂、分散剂
以EHP、CPN为引发剂;分散剂为450gVCM、315gPVA(平均聚合度2600,醇解度80%),225gPVA(平均聚合度300,醇解度45%),
4、链终止剂
选用HEO。
国内常用的终止剂ATSC终止效果优于双酚A,ATSC使产品分子量更均匀,白度也明显改善。
双酚A加入后仍有反应温度渐渐升高的过程,除此还在精馏系统中出现自聚现象,说明终止效果不彻底,尚有少部分引发剂未被破坏,反应继续进行。
而HEO与ATSC相比,由于HEO是复合配方,不仅终止效果好,而且其中有优良的热稳定配方,能大幅度提高产品白度。
试验表明,同样的配方和工艺条件,用ATSC最终产品白度在74%-76%,而用HEO产品白度可达85%。
5、分子量调节剂
最常见的调节剂是三氯乙烯,投加用量在较高范围(0.5%~1%,对单体),还对降低产品树脂分子量有显著效果。
近年来,已见有巯基乙醇作为分子量调节剂,当投加用量在100μg/g~200μg/g范围时,可降低反应温度2℃~3℃左右。
依据发展趋势,选用巯基乙醇作为分子量调节剂。
1.2原料的配比
表1.3原料配方
原料
VCM
水
引发剂
分散剂
其他助剂
重量,份
100
180
0.04
0.08
适量
1.3主要工艺参数
1、产品类型:
选用疏松型。
2、聚合反应时间:
5h
3、聚合温度:
57OC
4、操作周期:
9h
表1.4乙烯悬浮聚合操作周期
工序
设计值min
1、水相加料
30
2、抽真空
15
3、加VCM
15
4、加热到570C
30
5、恒温聚合时间
300
6、回收单体
60
7、出料
30
8、清釡
60
聚合周期
540(9h)
5、年平均操作时数:
8000小时
6、转化率:
90%。
根据要求生产的树脂牌号,氯乙烯单体的转化率选定在70%—95%范围。
工业上生产硬质PVC塑料制品用树脂,转化率要求大约为90%。
7、PVC粉体特性:
聚合度1000,表观密度0.55g/ml,平均粒径149μm,孔隙率0.185ml/g。
8、系统损失率
表3系统损失率
部位
损失率(kg/kg聚合物)
回收损失
0.25%
放空损失
0.51%
浆料损失
0.05%
气提损失
0.1%
离心、干燥损失
0.38%
精馏损失
3.5%
包装
0.21%
总计
5%
1.4设计所用物料的物理性质
表1.5水的物理性质
温度
℃
密度
kg/m3
比热容
KJ/(kg.℃)
导热系
λ×102w/(m.℃)
粘度
×105/Pa.s
普兰德数
Pr
10
999.7
4.191
57.45
130.77
9.52
30
995.7
4.174
61.76
80.07
40
992.2
4.174
63.38
65.60
4.32
57
986.6
4.175
65.13
49.3
表3.2VCM物理性质
温度℃
密度kg/m3
比热容KJ/(kg.℃)
20
1.352
50
1.53
57
837
1.57
70
1.63
表1.6PVC的物理性能
性能
指标
结晶数据/mm
工业PVC
单晶
结晶度/%
聚合后
熔体
密度(未复配)(g/㎝3)
总体
晶体
泊松比(硬PVC)
折射率
玻璃化温度/℃
线膨胀系数(未增塑)/℃-1
比热容/(J/g·℃)
硬PVC
23℃
50℃
80℃
120℃
增塑的PVC(50份DOP)
23℃
52℃
80℃
120℃
热导率(未增塑)/[J/(㎝·s·℃)]
介电强度/(kv/mm)
溶解度参数/(J/㎝3)0.5
正交晶系,每个晶胞两个单体
abc
1.060.540.51
1.0240.5240.508
1.9
4.9
1.39
1.53
0.41
1.54
83
7×10-3
0.92
1.05
1.45
1.63
1.88
1.54
1.67
1.75
1.88
17.5×10-4
20
40.7(平均)
1.5聚合反应过程工艺流程叙述:
工艺流程方框图:
工艺流程叙述
1、聚合单元
首先将加热到48℃左右的去离子水由泵计量后加入到聚合釜中,分散剂配成一定浓度溶液,在搅拌下由泵经计量后加入聚合釜内(也可由人孔直接投入),其他助剂配制成溶液通常由人孔投加,然后关闭人孔盖,通入氮气试压及排除系统中氧气,或借抽真空及充入氯乙烯方法。
最后将新鲜氯乙烯与回收后经处理的氯乙烯依一定比例(回收的VCM占总量的10%),送入计量槽内计量,再经单体过滤器过滤后加入釜内,开启多级往复泵将引发剂计量后加入釜中。
加料完毕后,于釜夹套内通入热水将釜内物料升温至规定的温度(57℃)。
当氯乙烯开始聚合反应并释放出热量时,夹套内改通冷却水以及时移除反应热,并使反应温度控制在57±0.2℃,直至反应结束。
当釜内单体转化率达到85%以上,这时釜内聚合压力为0.5MPa,由计量泵向釜内加入一定量的终止剂,未反应的氯乙烯单体经自压回收后,当压力降至2.9Kpa时,将釜内浆料升温至70℃左右,进行真空回收,真空度为500mmHg~550mmHg,最后浆料中的氯乙烯含量在700μg/g。
然后进入放料操作。
2、汽提、干燥工序
由聚合釜排出的浆料,为降低残留在其中的氯乙烯和减少氯乙烯对环境的污染,用泵打入出料槽除去其中的大块物料,再将其送入汽提塔,在塔内与由塔底上升的蒸汽在塔板上进行逆流传质过程。
该塔为真空操作,用真空泵维持塔顶的真空度,并以此来保证塔顶的温度。
塔顶逸出的含氯乙烯气经冷凝,未凝的氯乙烯含氧量在1%以下时,经真空泵送至氯乙烯气柜备用。
塔釜之浆料含氯乙烯约400μg/g,经热交换器冷却后进入混料槽,再送往离心机进行离心分离。
离心分离后PVC滤饼含水量为23%~27%,经滤饼分散器机械分散并均匀地加入干燥器中进行干燥。
干燥器内带有内加热和内冷却。
第1~5室为干燥室,用热水盘管和热风干燥,第6室为冷却室。
干燥后的氯乙烯树脂含水量为0.3%~0.4%。
经过筛除去大颗粒,再由气流输送至贮料仓,最后由包装单元进行包装。
[12]
3、VC回收工序
VC回收工序包括VC气体回收至气柜、VC气体压缩、精馏等部分。
自压回收的氯乙烯,经VC气体洗涤塔以除去气体飞沫中夹带的PVC,然后经气体冷却器进入气柜,真空回收的VCM,用回收风机抽至气柜。
由气柜出来的VC气体送至脱湿塔,用5℃的冷冻盐水进一步冷凝,两个冷凝器所冷凝的VC送至精馏塔进行精馏,所得的精氯乙烯经过滤后,按比例送入氯乙烯计量槽与新鲜氯乙烯混合供聚合使用,未凝的气体送至焚烧炉处理,塔釜的高沸物排放至塔底液罐中,加热以进一步回收部分氯乙烯。
第二章物料衡算
2.1年投料的物料衡算
表3系统损失率
部位
损失率(kg/kg聚合物)
回收损失
0.25%
放空损失
0.51%
浆料损失
0.05%
气提损失
0.1%
离心、干燥损失
0.38%
精馏损失
3.5%
包装
0.21%
总计
5%
因为产品的最后产量为26000吨,由表3系统损失率可以计算出系统年初始投料量:
筛分损失率为0.21%则
筛分时产量为:
26000×(1+0.21%)=
吨
干燥时损失率为0.13%则
干燥时产量为:
×(1+0.13%)=
吨
离心时损失率为0.25%则
离心时产量为:
×(1+0.25%)=26153.7吨
混料时损失率为0.01%则
混料时产量为:
26153.7×(1+0.01%)=26156.3吨
汽提时损失率为0.1%则
汽提时产量为:
26156.3×(1+0.1%)=26182.5吨
出料时损失率为0.01%则
出料量的产量为:
26182.5×(1+0.01%)=26185.1吨
聚合时损失率为0.03%+0.25%+0.51%则
聚合时VCM投料量为:
26185.1×(1+0.03%+0.25%+0.51%)=26392..0吨
因为聚合时的转化率为90%则
聚合时共投料量为:
26392.0/90%=29324.4吨
2.2车间物料的衡算
投入单体的计算:
投料系数为0.82、釡的体积为100m3、在20摄氏度时,ρVCM=911kg/m3ρH2O=997.7kg/m3设每次投入单体的质量为X则X/911+1.8X/997.7=100×0.82
以100m3釡为例,每次投入单体28473.8kg。
因转化率为90%,则反应得到树脂G1=28473.8×90%=25626.4kg,回收时损失的VCM为0.25%
则G2=25626.4×0.25%=64.1kg
放空时损失为0.51%,则G3=28473.8×0.51%=145.2kg
浆料损失为0.05%,则G4=28473.8×0.05%=14.2kg
汽提损失为0.1%,则G5=28473.8×0.1%=28.5kg
离心干燥损失为0.38%,则G6=28473.8×0.38%=108.2kg
精馏时损失为3.5%,则G7=28473.8×3.5%=996.6kg
包装时损失为0.21%,则G8=28473.8×0.21%=59.8kg
未测定其损失为G9=1322.9kg
反应前物料G=
kg,根据物料平衡原理:
G=G1+G2+···+G9
=25626.4+64.1+
+28.5+
+108.2+996.6+59.8+1322.9=
kg
2.3釡数及投料系数的台数的确定
因为每台釡年平均要工作9000小时,而每生产一次的周期为9小时,年投料量(VCM)为29324.4吨,每釡的出料量为
吨,选择投料系数为0.8,先用100m3的标准釡,VVCM=29324.4×1000/837=35035.1m3
V水=1.8×
×1000/997.7=63063.2m3
所需要釡的台数为(35035.1+63063.2)/(80×0.8×(9000/9))=1.53台,取整数为2台。
调整后的投料系数为0.76
实际的投料系数计算:
(35035.1+63063.2)/(80×2×1000)=0.76可取0.68
每个釡所需的VCM的体积为:
35035.1/(2×(9000/9))=21.7m3
每釡所需的水的体积为:
63063.2/(2×(9000/9))=31.5m3
根据表1.3原料的配方得:
表2.1
原料
VCM
水
引发剂
分散剂
其他助剂
重量,kg
8.8
17.6
适量
以100m3釡生产为例,分述如下:
(1)投料投料温度为20℃,单体21.7m3,水31.5m3,
投料体积21.7+31.5=53.2m3;
空余(气相)体积=80-53.2=26.8m3
(2)升温升温到期60℃,单体重度d依温度t变化
d=0.9471-0.001746t-0.00000324t2
得:
20℃时d=0.910;57℃时d=0.83
单体在57℃时体积增加到:
21.7×0.91/0.83=23.8m3
物料总体积:
23.8+31.5=55.3m3
空余(气相)体积:
80-55.3=24.7m3
(3)反应结束:
转化率为90%,树脂真实密度为1.4kg/m3
则此时树脂体积:
21.7×90%×0.83/1.4=11.6m3
未聚合单体体积:
21.7×0.1=2.17m3
物料总体积:
31.5+11.6+2.17=45.27m3
空余(气相)体积:
80-45.27=34.73m3
表2.2物料衡算汇总表
损失
损失率/%
损失前的重量/t
筛分
0.21
26054.6
干燥
0.13
26088.5
离心
0.25
26153.7
混料
0.01
26156.3
汽提
0.1
26182.5
出料
0.001
26185.1
聚合
0.79
26392.4
第三章热量衡算
3.1热量衡算
设夹套热水温度为62℃将聚合釜加热至50℃;其热损失为5%
平均每小时进入聚合釜的VCM量W
W=每个釡所需的VCM的体积×57℃下的VCM的密度
=21.7×837kg=18162.9kg
VCW比热容Cp20℃=1.352J/(g.K)
Cp50℃=1.53J/(g.K)Cp57℃=1.57J/(g.K)Cp70℃=1.63J/(g.K)
VCM聚合热1540KJ/kg
聚合搅拌功率163KW
转化率90%
设VCM进料温度20℃
聚合温度57℃
基准温度0℃
1、进入聚合釜的热量Q入
A、物料带入热量Q1=WCp20℃.t1=18162.9×1.352×20=4.91×105KJ/h
B、聚合热Q2=W.90%.1540=18162.9×0.9×1540=2.51×107KJ/h
C、搅拌热:
H=163KW=163×3600KJ/h=586800KJ/h
D、物料升温吸热
Q3=W.CpΔt=18162.9×(1.352+1.57)/2×(57-20)=9.71×105KJ/h
2、从釜带走的热量Q出
A、物料带出热Q4=WCpt
=18162.9×1.57×57=1.46×106KJ/h
B、釜表面散热Q5=5%Q2=5%×2.51×107=0.126×107KJ/h
C、冷却水带走热由Q入=Q出得Q6=Q1+Q2+H-Q3-Q4-Q5=
4.91×105+2.51×107+586800-9.71×105-1.46×106-0.126×107
=2.24×107
3.3.2循环水用量
设循环水从10℃升到40℃
10℃时Cp水=4.194KJ/(kg.℃)
40℃时Cp水=4.174KJ/(kg.℃)
Cpm=4.183KJ/(kg.℃)
W水=Q6/(Cpt)=2.24×107/(4.183×30)=1.8×105KJ/h
3.3.3传热面积
①最高热负荷Qmax
Qmax=330GR/t
57℃时T1/2(EHP)=2h查表得热负荷分布指数R=1.4
Qmax=330×52.5×1000×1.05×1.4/4.5=7835.7KW
②平均温差Δt
Δt=(47-17)/In(47/17)=30℃
③总传热面积F
F=Q/KΔt=7835.7×1000/(200×30)=1305.95m2
表3.-1热量衡算汇总表
物料带入热量Q1/(KJ/h)
1×105
聚合热Q2水/(KJ/h)
2.51×107
搅拌热△H/(KJ/h)
586800
物料升温吸热Q3/(KJ/h)
9.71×105
物料带出热Q4/(KJ/h)
1.46×106
釜表面散热Q5/(KJ/h)
0.126×107
冷却水带走热Q6/(KJ/h)
2.24×107
循环水用量W/(KJ/h)
1.8×105
第四章设备工艺设计
4.180m3不锈钢聚合釡
80m3的聚合釡主要工艺参数如下:
体积:
80m3直筒长:
5000mm
内径:
4000mm长径比:
1.25
电机功率:
22~28kW搅拌转速:
197~250r/min
传热面积:
1305.95m2加VCM:
1470.33kg/min
加水:
1323.30kg/min
因为釡比传热面积大,不设内冷管和釡顶冷凝器。
设备由于属瘦长釡型,为加强上下层物料均匀混合,安装有6层搅拌叶浆,采用推进式浆叶型,这有利于加强沿搅拌轴上下的循环混合作用。
搅拌轴与釡底轴瓦的安装间隙要求在0.90mm,使用一段时间后因机械磨损逐渐变大,一般当间隙达2mm左右更换新轴瓦。
4.2汽提塔
选用穿流式(无溢流管)的筛板的汽提塔。
这种处理浆料的筛板塔,采用无溢流管式大孔径筛板,筛孔直径选用20mm,筛板有效开孔率选用11%。
为使浆料经处理后,残留单体降到400ppm以下,汽提塔内设置20块筛板保持板间距离300mm。
为保证气液接触时筛板上泡沫高度的均匀,空塔气速在1m/s,筛板孔速10m/s,物料停留时间表4~8分钟。
4.3混料槽
采用搅拌型式的混料槽,耙齿与压缩空气组合由于转速很低,底轴瓦内采用连续式注水结构。
底部的出料小罐中,设置相对直径较大的平浆式搅拌叶,使搅拌速度达到较高值,以防止出料区因树脂沉积而堵塞。
该混合槽的主要技术参数:
转速:
8~12r/min
电机功率:
7.5~10kW
4.4离心机
采用三足式离心机,主要特点是对各种产品适应性较强。
即悬浮液料进入转鼓后,在离心力的作用下固液分离,是依靠多孔转鼓上的滤网滤布来实现。
采用最简单的“SS”型号的足式上部卸料离心机其特点是结构简单,电机通过三角皮带直接带动转鼓轴上的皮带轮驱动转鼓旋转,完成固液分离后停机铲出。
4.5干燥器
选用气流干燥器,它的特点是:
1、工艺流程与设备简单,投资少。
2、生产能力连续化,干燥均匀,操作控制方便。
3、干燥速度快,能力大,很适合热敏感性的物料干燥。
气流干燥器是一根管线,聚氯乙烯生产的气流干燥速度,一般设计在14~21m/s之间,停留时间2秒左右。
热风可高达160℃,热交换效率高。
采用螺旋输送器将湿物料加入气流干燥管内。
附录3
表4.1聚合釜及设备设计参数汇总表
实际容积/V,m3
80
直筒长/H,mm
5000
筒内径/D,mm
4000
长径比/H/D
1.25
电机功率/P,kW
22~28
搅拌转速/n,r/min
197~250
夹套传热面积/m2
1305.95
加VCM/kg/min
1470.33
加水/kg/min
1323.30
搅拌叶浆/层
1
筛孔/mm
20
有效开孔率/%
11
筛板数/层
20
筛板间距/mm
300
筛板孔速/m/s
10
物料停留时间/min
4~8
混料槽转速/r/min
8~12
混料槽电机功率/kW
7.5~10
干燥器气流速度/m/s
14~21
干燥停留时间/t
2
热风温度/℃,
160
参考文献
[1]张洋主编.高聚物合成工艺设计基础.北京:
化学工业出版社,1981
[2]严福英.聚氯乙烯工艺学.化学工业出版社,1996
[3]赵德仁、张慰盛主编.高聚物合成工艺学[M].华东理工大学:
化学工业出版社,2003
[4]史子瑾主编.聚合反应工程基础[M].化学工业出版社,2004
Forpersonaluseonlyinstudyandresearch;notforcommercialuse
[5]化工部设备设计技术中心站主编.搅拌设备设计.上海:
上海科学技术出版社,1988
仅供个人用于学习、研究;不得用于商业用途。
Forpersonaluseonlyinstudyandresearch;notforcommercialuse.
NurfürdenpersönlichenfürStudien,Forschung,zukommerziellenZweckenverwendetwerden.
Pourl'étudeetlarechercheuniquementàdesfinspersonnelles;pasàdesfinscommerciales.
толькодлялюдей,которыеиспользуютсядляобучения,исследованийинедолжныиспользоватьсявкоммерческихцелях.
以下无正文