梯形盖注塑模具设计.docx
《梯形盖注塑模具设计.docx》由会员分享,可在线阅读,更多相关《梯形盖注塑模具设计.docx(49页珍藏版)》请在冰豆网上搜索。
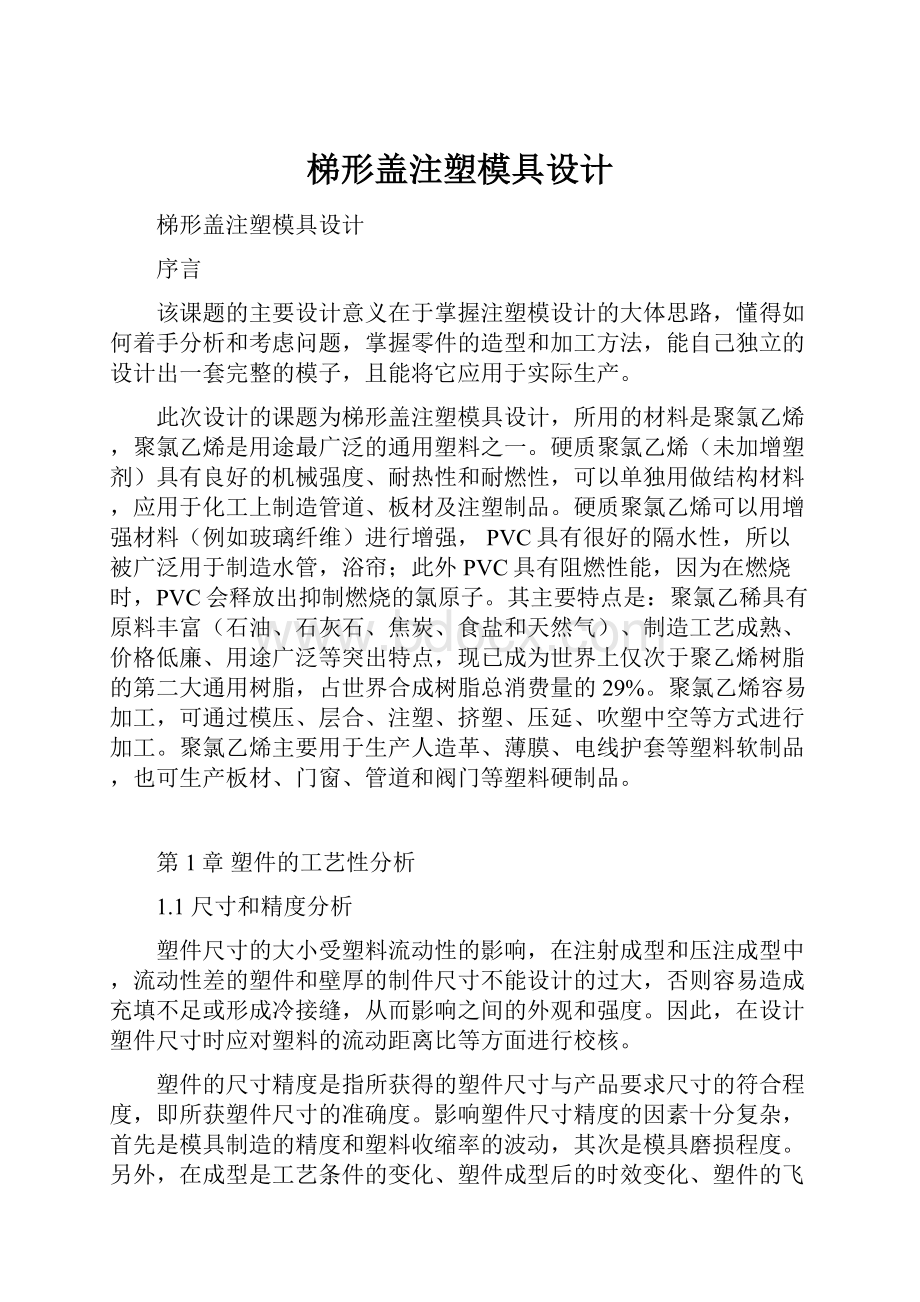
梯形盖注塑模具设计
梯形盖注塑模具设计
序言
该课题的主要设计意义在于掌握注塑模设计的大体思路,懂得如何着手分析和考虑问题,掌握零件的造型和加工方法,能自己独立的设计出一套完整的模子,且能将它应用于实际生产。
此次设计的课题为梯形盖注塑模具设计,所用的材料是聚氯乙烯,聚氯乙烯是用途最广泛的通用塑料之一。
硬质聚氯乙烯(未加增塑剂)具有良好的机械强度、耐热性和耐燃性,可以单独用做结构材料,应用于化工上制造管道、板材及注塑制品。
硬质聚氯乙烯可以用增强材料(例如玻璃纤维)进行增强,PVC具有很好的隔水性,所以被广泛用于制造水管,浴帘;此外PVC具有阻燃性能,因为在燃烧时,PVC会释放出抑制燃烧的氯原子。
其主要特点是:
聚氯乙稀具有原料丰富(石油、石灰石、焦炭、食盐和天然气)、制造工艺成熟、价格低廉、用途广泛等突出特点,现已成为世界上仅次于聚乙烯树脂的第二大通用树脂,占世界合成树脂总消费量的29%。
聚氯乙烯容易加工,可通过模压、层合、注塑、挤塑、压延、吹塑中空等方式进行加工。
聚氯乙烯主要用于生产人造革、薄膜、电线护套等塑料软制品,也可生产板材、门窗、管道和阀门等塑料硬制品。
第1章塑件的工艺性分析
1.1尺寸和精度分析
塑件尺寸的大小受塑料流动性的影响,在注射成型和压注成型中,流动性差的塑件和壁厚的制件尺寸不能设计的过大,否则容易造成充填不足或形成冷接缝,从而影响之间的外观和强度。
因此,在设计塑件尺寸时应对塑料的流动距离比等方面进行校核。
塑件的尺寸精度是指所获得的塑件尺寸与产品要求尺寸的符合程度,即所获塑件尺寸的准确度。
影响塑件尺寸精度的因素十分复杂,首先是模具制造的精度和塑料收缩率的波动,其次是模具磨损程度。
另外,在成型是工艺条件的变化、塑件成型后的时效变化、塑件的飞边等都会影响塑件的精度。
因此,塑件的尺寸精度的确定应该合理选择,尽可能选用低精度等级。
很多资料认为,在引起塑件尺寸的误差中,模具制造公差和成型收缩率波动引起的误差各占1/3。
实际上,对于小尺寸塑件,模具的制造公差对塑件尺寸精度影响相对要大一些,而对于大尺寸塑件,收缩率波动则是影响塑件尺寸精度的主要因素。
在本设计中,塑件的材料为软聚氯乙烯,标注公差尺寸高精度为MT5,未标注为MT7。
模塑件尺寸公差为MT,公差等级为7级,每一级又可分为A、B两部分,其中A为不受模具活动部分影响尺寸的公差,B受模具活动部分影响尺寸的公差,如塑件图:
图1—1塑件图
根据公差尺寸精度查文献[10]得:
(1)总长:
500-0.80㎜A:
0.74㎜;
(2)总宽:
250-0.64㎜A:
0.50㎜;
(3)总高:
250-0.64㎜B:
0.70㎜;
(4)阶高:
130-0.48㎜B:
0.52㎜;
(5)锥底直径:
ф180-0.48㎜A:
0.44㎜;
(6)锥顶直径:
ф80-0.48㎜A:
0.28㎜。
1.2表面粗糙度分析
塑料制件的表面粗糙度,除了在成型时从工艺上尽可能避免冷疤、云纹等疵点外,主要取决于模具成型零件的表面粗糙度。
一般模具的表面粗糙度要比塑件的低1~2级,在本设计中,塑料制件的表面粗糙度Ra值一般为1.6~0.2μm,除了一些特别有粗糙度要求的。
如套筒表面粗糙度要求为0.8μm。
1.3形状分析
塑件的形状在满足使用要求的前提下,应使其有利于成型,特别是尽量不采用侧向抽芯机构,因此塑件设计时应可能避免侧向凹凸箱子和侧孔。
在本设计中就没采用侧向抽芯机构,因为,侧向分型与抽芯机构的模具机构不但提高了模具设计与制造成本,而且还会在分型面上留下飞边,增加后加工的工作量。
某些塑件只要适当地改变其形状,即能避免使用侧向抽芯机构,使其模具结构简化。
第2章分型面的选择
2.1分型面及其选择
分型面是决定模具结构形式的一个重要因素,分型面的类型、形状及位置与模具的整体结构、浇注系统的设计、塑件的脱模和模具的制造工艺等有关,不仅直接关系到模具结构的复杂程度,也关系到塑件的成型质量。
注射模有时为了结构的需要,在定模或动模部分增加辅助的分型面,此时,将脱模取出塑件的分型面称为主分型面。
2.1.1塑料制件在模具中的位置
1.型腔数目的确定
一次注射只能生产一件塑料产品的模具称为单型腔模具,如果一副模具一次注射能生产两件或两件以上的塑料产品,则这样的模具称为多型腔模具。
模具的型腔数一般由成型设备的技术参数限定,综合考虑生产效率及模具加工成本与难易,可选用一模一腔,一模两腔和一模多腔。
为满足生产效率,本设计采用普通浇注系统时,采用一模四腔。
2.塑件在模具的位置
由于型腔的排布与浇注系统布置密切相关,因此型腔的排布在多型腔模具设计中应加以综合考虑。
型腔的排布应使每个型腔都通过浇注系统从总压力中均等地分得所需的足够压力,以保证塑料熔体同时均匀地充满每个型腔多型腔模具型腔布局一般有平衡式和非平衡式。
对于本设计,根据浇注方式和制品几何形状,考虑模具型腔加工难易程度,可选用如下平衡式(图2-1)和非平衡式(图2-2)。
图2-1模具型腔布局
平衡式的特点是从主流道到各型腔浇口分流道的长度、截面形状和尺寸均对应相同,可实现各型腔均匀进料和同时充满型腔的目的,从而使所成型的塑件内在质量均一稳定,力学性能一致。
图2-2模具型腔布局
非平衡式的特点是从主流道到各型腔浇口分流道的长度不相同,因而不利于均衡进料,但可以明显缩短分流道的长度,节约塑件的原材料。
为了使非平衡式布置的型腔也能达到同时充满的目的,往往各浇口的截面尺寸要制造得不相同。
在实际多型腔模具的设计与制造中,对于精度要求高、物理与力学性能要求均稳定的塑件制件,应尽量选择平衡式布置的形式。
本设计,一模出四个,浇口分流道的长度、截面形状和尺寸均对应相同,所以采用平衡式。
由于本设计采用一模四腔,型腔布局如图2-3:
图2-3型腔布局
2.1.2分型面的选择
分型面是决定模具结构形式的一个重要因素,它与模具的整体结构、浇注系统的设计、塑件的脱模和模具的制造工艺等有关,分型面的选择是注射模设计中的一个关键。
1.分型面的形式
注射模具有的只有一个分型面,有的有多个分型面。
在多个分型面的模具中,将脱模时取出塑件的那个分型面称为主分型面,其他的分型面称为辅助分型面,辅助分型面是为了达到某种目的而设计的。
分型面的形状有平直分型面、倾斜分型面、梯形分型面、曲面分型面、垂直分型面等等。
在本设计中分型面的形状是平直的,其形状如图2-4:
图2-4分型面的形状
2.分型面的设计原则
由于分型面受塑件在模具中的成型位置、浇注系统设计、塑件结构工艺性尺寸精度、嵌件的位置、塑件的推出、排气等多种因素的影响,因此在选择分型面时应综合分析比较,以选出较为合理的方案。
选择分型面时,应遵循几项基本原则:
分型面应选在塑件外形最大轮廓处、分型面的选择应有利于塑件顺利脱模、分型面的选择应保证塑件的尺寸精度和表面质量、分型面的选择应有利于模具的加工以及分型面的选择应有利于排气。
在实际设计中,应找住主要矛盾,从而合理地确定分型面。
第3章注射模结构设计与注射机选择
塑料注射成型模具主要用于热塑性塑料制件的成型。
注射成型的特点是生产率高,容易实现自动化生产。
由于注射成型的工艺优点显著,所以塑料注射成型的应用最为广泛。
近年来,随着成型技术的发展,热固性塑料的注射成型应用也日趋广泛。
3.1注射模的典型结构
注射模具有很多的分类方法。
按注射模具的典型结构特征可分为单分型面注射模具、双分型面注射模具、斜导柱(弯销、斜导槽、斜滑块、齿轮齿条)侧向分型与抽芯注射模具、带有活动镶件的注射模具、定模带有推出装置的注射模具和自动卸螺纹注射模具等;按浇注系统的结构形式分类,可分为普通流道注射模具、热流道注射模具;按注射模具所用注射机的类型可分为卧式注射机用模具、立式注射机用模具和角式注射机用模具;按塑料的性质分类,可分为热塑性塑料注射模具、热固性塑料注射模具;按注射成型技术可分为低发泡注射模、精密注射模、气体辅助注射成型注射模、双色注射模、多色注射模等。
注射模具的结构由塑件的复杂程度及注射机的结构形式等因素决定。
注射模具可分为动模和定模两大部分,定模部分安装在注射机的固定模板上,动模部分安装在注射机的移动模板上,注射时动模与定模闭合构成浇注系统和型腔,开模时动模与定模分离,取出塑件。
根据模具上各个部分所起的作用,注射模具的总体结构组成如下图所示:
1.成型部分
成型部分是指与塑件直接接触、成型塑件内表面和外表面的模具部分,它由凸模(型芯)、凹模(型腔)以及嵌件和镶块等组成。
凸模(型芯)形成塑件的内表面形状,凹模形成塑件的外表面形状,合模后凸模和凹模便构成了模具模腔。
如下图所示的模具中,模腔由动模板9、定模板12、凸模18等组成。
图3-1注射模具的结构
1.推板垫板2.拉料杆3.推杆4.圆头螺钉5.内六角螺钉6.模脚7.动模垫板8.定距拉板9.动模板10.套筒11.脱模板12.定模板13.定模座板14.圆头螺钉15.圆柱销16.压缩弹簧17.限位导柱18.型芯19.浇口套20.导柱21.圆头螺钉22.推杆
2.浇注系统
浇注系统是熔融塑料在压力作用下充填模具型腔的通道(熔融塑料从注射机喷嘴进入模具型腔所流经的通道)。
浇注系统由主流道、分流道、浇口及冷料穴等组成。
浇注系统对塑料熔体在模内流动的方向与状态、排气溢流、模具的压力传递等起到重要的作用。
3.导向部分
为了保证动模、定模在合模是的准确定位,模具必须设计有导向机构。
导向机构分为导柱、导套导向结构与内外锥面定位导向机构两种形式。
上图中的导向机构由导柱20和导套10组成。
4.推出机构
推出机构是将成型后的塑件从模具中推出的装置。
推出机构有推板、推杆固定板、拉料杆、推板导柱、推板导套、推杆等零件组成。
5.温度调节系统
为了满足注射工艺对模具的温度要求,必须对模具的温度进行控制,模具结构中一般都设有对模具进行冷却或加热的温度调节系统。
如上图,模具的冷却方式是在模具上开设冷却通道。
本设计不需要加热装置。
6.排气系统
在注射成型过程中,为了将型腔内的气体排出模外,常常需要开设排气系统。
排气系统通常是在分型面上有目的地开设几条排气沟槽,如上图所示。
另外许多模具的推杆或活动型芯与模板之间的配合间隙可起排气作用。
7.支承零部件
用来安装固定或支承成型零部件以及前述各部分机构的零部件均称为支承零部件。
支承零部件组装在一起,构成注射模具的基本骨架。
如上图中的支承零部件有定模座板13、脱模板7和垫板1等。
根据注射模中各零件的作用,上述七大部分可以分为成型零部件和结构零部件两大类。
在结构零部件中,合模导向机构与支承零部件合称为基本机构零部件,因为二者组装起来可以构成注射模架(已标准化)。
任何注射模均可以以这种模架为基础再添加成型零部件和其他必要的功能结构来形成.
注射模的典型结构主要有单分型面注射模、双分型面注射模、斜导柱侧向分型与抽芯注射模、斜滑块侧向分型与抽芯注射模、带有活动镶件的注射模等等。
由于本设计选择双分型面注射模,下面着重谈谈双分型注射模。
双分型面注射模具的结构特征是有两个分型面,常常用于点浇口浇注系统的模具,也叫三板式(动模板、中间板、定模座板)注射模具,如上图3-1所示,在定模部分增加一个分型面(A分型面),分型的目的是为取出浇注系统凝料,便于下一次注射成型;B分型面为主分型面,分型的目的是开模推出塑件。
双分型面注射模具与单分型面注射模具比较,结构较复杂。
其工作原理为:
开模时,动模部分向后移动,由于弹簧16的作用,使定模板12与定模座板13首先沿A-A分型面定距分型,其分型距离由定距拉板8控制,以便取出这两块模板之间的浇注系统凝料。
继续开模时,沿B-B面分型,然后在注射机推出机构作用下推杆22推动脱模板11,使之沿C-C面分离,塑件即脱离型芯,完成一次注射过程。
3.2注射模与注射机
注射机是注射成型的设备,注射模是安装在注射机上生产的。
注射机选用得是否合理,直接影响模具的结构设计,因此,在进行模具设计时,必须对所选用活动注射机的相关技术参数有全面的了解。
注射机发展很快,类型不断增加,注射机的分类方法较多,通常按注射机外形特征分类,这种分类法主要根据注射装置和合模装置的排列方式进行分类,可以分为卧式注射成型机、立式注射成型机、角式注射成型机和多模成型机等几种。
本设计中采用卧式注射成型机。
卧式注射成型机是使用最广泛的注射成型设备,它的注射装置和合模装置的轴线呈一线并水平排列,它的优点是便于操纵和维修,机器重心低,比较稳定,成型后的塑件推出后可利用其自重自动落下,容易实现全自动操作等。
常用的卧式注射机型号有:
XS-ZY30、XS-ZY60、XS-ZY125、XS-ZY500、XS-ZY1000等。
其中XS表示塑料成型机械;Z表示注射成型;Y表示螺杆式(预塑式);500、125等表示注射机的最大注射量(㎝3或g)。
3.2.1注射机有关工艺参数的校核
模具设计时,必须根据塑件的机构特点、塑件的技术要求确定模具机构,模具的结构与注射机之间有着必然的联系,模具定位圈尺寸、模板的外围尺寸、注射量的大小、推出机构的设置及锁模力的大小等必须参照注射机的类型及相关尺寸进行设计,否则,模具就无法与注射机合理匹配,注射过程也就无法进行。
1.最大注射量的校核
最大注射量是指注射机对空注射的条件下,注射螺杆或柱塞作一次最大注射行程时,注射装置所能达到的最大注射量。
设计模具时,应满足注射成型塑件所需的总注射量小于所选注射机的最大注射量,当注射机选XS-ZY125时,即:
nm+mj≤kmn(3-1)
式中n——型腔数目;
M——单个塑件的体积或质量,㎝3或g;
mj——浇注系统凝量,㎝3或g;
mn——注射机最大注射量,㎝3或g;查文献[7]mn为125;
k——注射机最大注射量利用系数,一般取0.8。
柱塞式注射机的允许最大注射量是以一次注射聚苯乙烯的最大克数(g)为标准的;螺杆式注射机是以体积(㎝3)表示最大注射量。
根据上式,可以校核出:
4×19+2.3≤0.8×125
78.3≤100
根据上式的校核,注射机的选择符合要求。
2.型腔数量的确定和校核
型腔数量的确定是模具设计的第一步,型腔数量与注射机的塑化速率、最大注射量及锁模力等参数有关,另外,型腔数量还直接影响塑件的精度和生产的经济性。
型腔数量的确定方法有很多种。
下面按注射机的额定塑化速率确定型腔的数量n:
nm1+m2≤KMT/3600(3-2)
式中n——型腔数量;
m1——单个塑件的质量或体积。
㎝3或g;
m2——浇注系统凝料的塑料质量或体积,g或㎝3;
K——注射机最大注射量的利用系数,一般取0.8左右,视设备的新旧而取值;
M——注射机的额定塑化量,(g/h)或(㎝3/h);查文献[7]M为13;
T——成型周期,s。
查文献[7]T为3600。
根据上式,可以计算校核出:
19n+2.3≤0.8×13×3600×60/3600
n≤31.6
n取4符合要求。
上述方法是确定或校核型腔数量的基本方法。
具体设计时,还需考虑成型塑件的尺寸精度、生产的经济性及注射机安装模板尺寸的大小。
3.锁模力的校核
注射时塑料熔体进入型腔内仍然存在较大的压力,它会使模具从分型面涨开。
为了平衡塑料熔体的压力,锁紧模具保证塑件的质量,注射机必须保证足够的锁模力。
它用注射量一样,也反应了注射机的加工能力,是一个重要参数。
涨模力等于塑件和浇注系统在分型面上不重合的投影面积之和乘以型腔的压力,它应小于注射机的额定锁模力Fn,才能使注射时不发生溢料和涨模现象,即满足下式:
(nA1+Aj)p≤Fn(3-3)
式中Fn——注射机的额定锁模力。
查文献[7]Fn为900。
根据上式,可以校核出:
(4×1250+76.28)×0.8×120≤900×1000
487322.88≤900000
符合要求。
4.注射压力的校核
塑料成型时所需要的注射压力是由塑料品种、注射机类型、喷嘴形式、塑件形状以及浇注系统的压力损失等因素决定的。
注射压力的校核是核定注射机的额定注射压力是否大于成型时所需的注射压力。
根据查表可知:
p0≥p(3-4)
式中p0——注射机最大压力;查文献[8]p0为120;
P——塑件成型所需的注射压力。
查文献[8]P为120。
根据上式,
120≥60
符合要求。
5.模具与注射机安装部分相关尺寸的校核
注射模具是安装在注射机上生产的,在设计模具时,必须使模具的有关尺寸与注射机相匹配。
与模具安装的有关尺寸包括喷嘴尺寸、定位圈尺寸、模具的最大和最小厚度以及模板上的安装螺孔尺寸等。
(1)浇口套球面尺寸设计模具时,浇口套内主流道始端的球面必须比注射机喷嘴头部球面半径略大一些。
如图3-2:
图3-2浇口套
(2)定位圈尺寸为了使模具在注射机上的安装准确、可靠,定位圈的设计很关键。
模具定位圈的外径尺寸必须与注射机的定位孔尺寸相匹配。
通常采用间隙配合,以保证模具主流道的中心线与注射机喷嘴的中心线重合,一般模具的定位圈外径尺寸应比注射机固定模板上的定位孔尺寸小0.2㎜以下。
(3)模具的最大、最小厚度模具的总高度必须位于注射机可安装模具的最大模厚与最小模厚之间,同时应校核模具的外形尺寸,使模具能从注射机的拉杆之间装入。
(4)安装螺孔尺寸
注射模具在注射机上的安装方法有两种,一种是用螺钉直接固定;另一种是用螺钉、压板固定。
当用螺钉直接固定时,模具动、定座板与注射机模板上的螺孔应完全吻合;本设计中用压板固定,只要在模具固定板需安放压板的外侧附近有螺孔就能紧固,因此,压板固定具有较大的灵活性。
6.开模行程的校核
注射机的开模行程是受合模机构限制的,注射机的最大开模距离必须大于脱模距离,否则塑件无法从模具中取出。
由于注射机的合模机构不同,开模行程有三种校核:
注射机的最大开模行程与模具厚度无关的校核、注射机的最大开模行程与模具厚度有关的校核、具有侧向抽芯机构时的校核。
在本设计中,计算注射机的最大开模行程与模具厚度有关的校核。
如图3-3所示,对于双分型面。
此时最大开模行程等于注射机移动模板与固定板之间的最大距离s减去模具厚度Hm;
图3-3双分型面注射模开模行程
对于双分型面注射模具,校核公式为:
s≥Hm+H1+H2+a+(5~10)㎜(3-5)
式中s——注射机最大开模行程,㎜;
H1——推出距离(脱模距离),㎜;
H2——包括浇注系统在内的塑件高度,㎜。
根据上式,
580≥170+55+62+70+8
580≥365
符合要求。
7.推出装置的校核
各种型号注射机的推出装置和最大推出距离不尽相同,设计时,应使模具的推出机构与注射机相适应。
通常是根据开合模系统推出装置的推出形式(中心推出还是两侧推出)、注射机的顶杆直径、顶杆间距和顶出距离等校核模具推出机构是否合理、推杆推出距离能否达到使塑件顺利脱模的目的。
第4章成型零部件设计
模具合模后,在动模板和定模板之间的某些零部件组成一个能充填塑料熔体的模具型腔,模具型腔的形状和尺寸就决定了塑料制件的形状与尺寸。
构成模具型腔的所有零部件称为成型零部件。
成型零件工作时直接与塑料熔体接触,要承受熔融塑料流的高压冲刷、脱模摩擦等。
因此,成型零件不仅要求有正确的几何形状、较高的尺寸精度和较低的表面粗糙度值,而且还要求有合理的结构和较高的强度、刚度及较好的耐磨性。
设计注射模的成型零件时,应根据成型塑件的塑料性能、使用要求、几何形状,并集合分型面和浇口位置的选择、脱模方式和排气位置的考虑来确定型腔的总体结构;根据塑件的尺寸计算成型零件型腔的尺寸;确定成型零件的机械加工、热处理、装配等要求;对关键的部位要进行强度和刚度校核。
由此可见,注射模的成型零部件设计是注射模设计的一个重要部分。
4.1成型零部件的结构设计
成型零部件是决定塑件几何形状和尺寸的零件。
它是模具的主要部分,主要包括凹模、凸模及镶件、成型杆和成型环等。
由于塑料成型的特殊性,塑料成型零件的设计与冷冲模的凹、凸模设计有所不同。
4.1.1凹模和凸模的结构设计
凹模也称型腔,是成型塑件外表面的主要零件,其中成型塑件上外螺纹的称螺纹型环;凸模也称型芯,是成型塑件内表面的零件,成型其主体部分内表面的零件称主型芯或凸模,而成型其他小孔的型芯称为小型芯或称型杆,成型塑件上内螺纹的称螺纹型芯。
凹、凸模按结构不同主要可分为整体式和组合式两种形式。
整体式的凹模和凸模是指直接在整块模板上分别加工出凹、凸形状的结构形式。
其特点是牢固、不容易变形,不会使塑件产生拼接线痕迹。
但加工困难,热处理不方便,整体式凸模还有消耗模具钢多、浪费材料等特点。
所以整体式凹、凸模结构常用于形状简单的单个型腔中、小型模具或工艺试验模具。
组合式凹模、凸模结构是指由两个或两个以上的零件组合而上的凹模和凸模,按组合方式不同,可分为整体嵌入式、局部镶嵌式和四壁拼合式等形式。
在本设计中,采用整体嵌入式,如图4-1所示,因为在小型塑件采用多型腔模具成型时,各单个型腔和型芯采用单独加工(机械加工、冷挤压、电加工等方法)的方法加工制成,然后采用H7/m6过渡配合压入模板中。
这种结构加工效率高,装拆方便,容易保证形状和尺寸精度。
图4-1整体嵌入式凹、凸模结构形式
4.2成型零部件的工作尺寸计算
成型零件的工作尺寸是指凹模和型芯直接构成塑件的尺寸。
例如型芯和型腔的径向尺寸、高度和高度尺寸、孔间距尺寸、孔或凸台至某成型表面的尺寸、螺纹成型零件的径向尺寸和螺距尺寸。
4.2.1影响成型零件工作尺寸的因素
影响成型零件工作尺寸的因素很多,概括地说,有塑料原材料、塑件结构和成型工艺、模具结构、模具制造和装配、模具使用过程中的磨损等因素。
塑料原材料方面的因素主要是指收缩率的影响。
由于影响塑件尺寸的因素很多,特别是由于塑料收缩率的影响,所以使其计算过程比冷冲模要复杂。
(1)塑件的收缩率波动塑件成型后的收缩率变化与塑料的品种,塑件的形状、尺寸、壁厚、成型工艺条件,模具的结构等因素有关。
确定准确的收缩率是很困难的,由于工艺条件、塑料批号发生的变化会造成塑件收缩率的波动,其塑料收缩率波动误差为
δ=(Smax~Smin)Ls(4-1)
式中δ——塑料收缩率波动误差;
Smax——塑料的最大收缩率;查文献[8]可知。
Smin——塑料的最小收缩率;查文献[8]可知。
在0.5范围内。
Ls——塑件的基本尺寸。
根据上面的公式,在本设计中:
δ=(Smax~Smin)Ls=0.5×50=25
因而实际收缩率与计算收缩率有差异。
按照一般的要求,塑料收缩率波动所引起的误差应小于塑件公差的1/3。
(2)模具成型零件的制造误差模具成型零件的制造精度是影响塑件尺寸精度的重要因素之一。
模具成型零件的制造精度愈低,塑件尺寸精度也愈低。
一般成型零件工作尺寸的制造公差值取塑件公差值的1/3~1/4或取IT7~8级作为制造公差。
组合式型芯和型腔应根据尺寸链来确定。
(3)模具成型零件的磨损模具在使用过程中,由于塑料熔体流动的冲刷、成型过程中可能产生的腐蚀性气体的锈蚀、脱模时塑件与模具的摩擦,以及由于上述原因造成的成型零件表面粗糙度提高而重新打磨抛光等原因,均造成成型零件尺寸变化。
这种变化称为成型零件的磨损。
其中脱模摩擦磨损是主要因素。
磨损的结果是使型腔尺寸变大,型芯尺寸变小。
磨损大小与塑料的品种和模具材料及热处理有关。
为简化计算,凡与脱模方向垂直的表面因磨损小而不考虑,与脱模方向平行的表面应考虑磨损。
磨损量应根据塑件的产量、塑件的品种、模具的材料等因素来确定。
对于中小型塑件,最大磨损量可取塑件公差的1