重庆大学数控加工实践报告.docx
《重庆大学数控加工实践报告.docx》由会员分享,可在线阅读,更多相关《重庆大学数控加工实践报告.docx(35页珍藏版)》请在冰豆网上搜索。
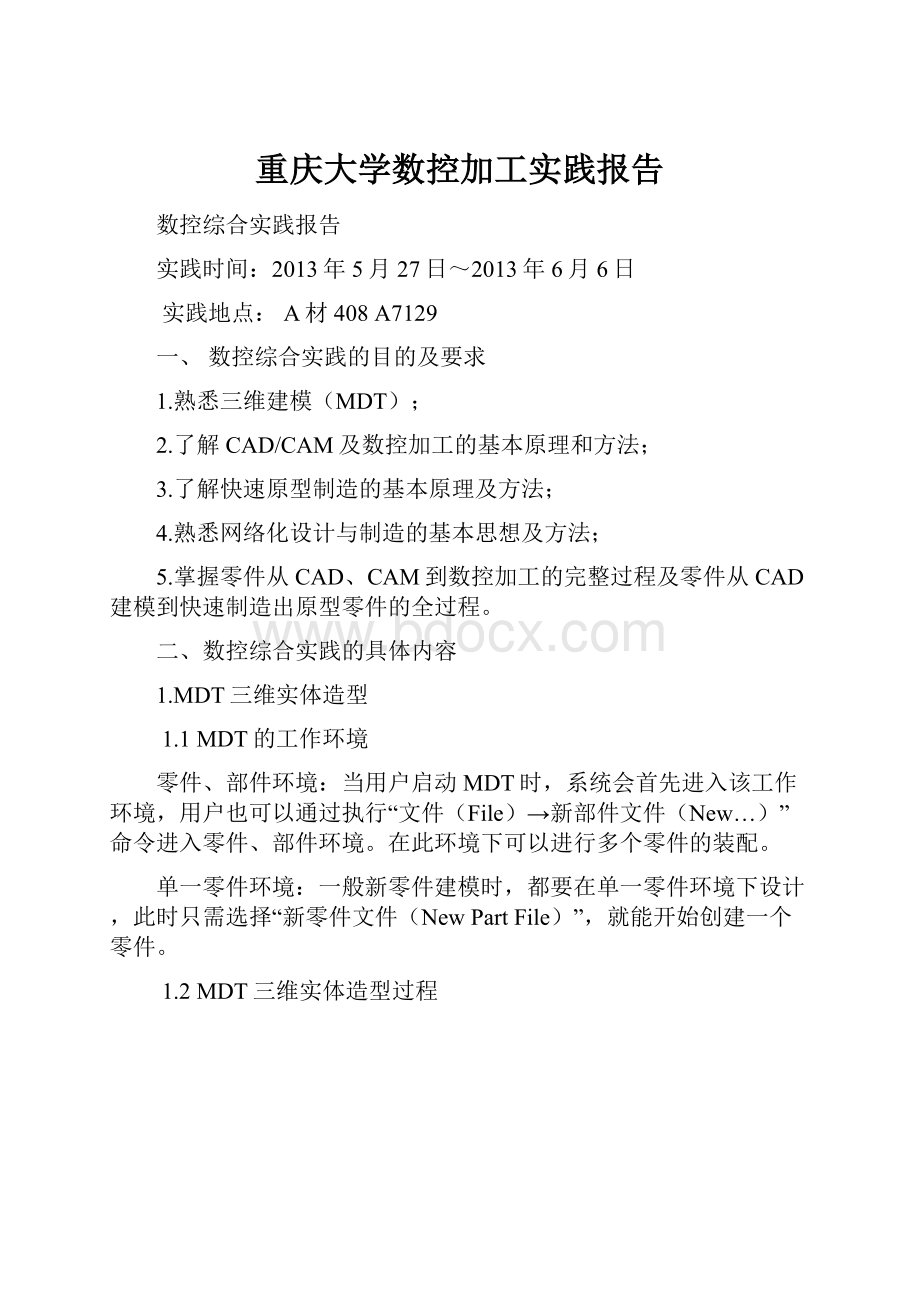
重庆大学数控加工实践报告
数控综合实践报告
实践时间:
2013年5月27日~2013年6月6日
实践地点:
A材408A7129
一、数控综合实践的目的及要求
1.熟悉三维建模(MDT);
2.了解CAD/CAM及数控加工的基本原理和方法;
3.了解快速原型制造的基本原理及方法;
4.熟悉网络化设计与制造的基本思想及方法;
5.掌握零件从CAD、CAM到数控加工的完整过程及零件从CAD建模到快速制造出原型零件的全过程。
二、数控综合实践的具体内容
1.MDT三维实体造型
1.1MDT的工作环境
零件、部件环境:
当用户启动MDT时,系统会首先进入该工作环境,用户也可以通过执行“文件(File)→新部件文件(New…)”命令进入零件、部件环境。
在此环境下可以进行多个零件的装配。
单一零件环境:
一般新零件建模时,都要在单一零件环境下设计,此时只需选择“新零件文件(NewPartFile)”,就能开始创建一个零件。
1.2MDT三维实体造型过程
(1)进入MDT的工作界面后,先建立西南等轴测视图XYZ,将工作平面XY设定为新的草图平面,并按照模型进行绘图。
(2)设定新的草图平面XY平面。
(3)在草图平面绘制直径为120mm的圆。
(4)将圆拉伸30mm后的到如下图形。
(5)再回到草图平面重新画完圆内的孔。
(6)将图形阵列以后。
(7)将草图拉伸后可得。
(8)将小孔打通并且将顶面的台阶拉伸出来.
(9)全部倒角。
(10)最后得到的MDT做出来的成型零件。
2.零件CAM及数控加工过程
2.1实践材料及设备
毛坯材料及尺寸:
长×宽×高=110mm×80mm×40mm;以毛坯顶面坐标点作为坐标系原点,高度方向最大切削深度不得超过30mm;
加工设备:
α-T10A钻削中心、TV5立式加工中心;
刀具:
φ10mm端铣刀(型号为G120221),R3mm球头铣刀(型号为Q121211)
刀具参数表
单位:
mm
刀具名称
刀具型号
刀具直径
夹持直径
刀刃长
刀具全长
二齿端铣刀
G120221
10
10
22
72
二齿球头铣刀
Q120211
6
6
13
57
铣削用量建议:
入刀速度为F100,正常走刀速度为F1000,φ10mm端铣刀的转速为1000rpm,R3mm球头铣刀转速为2000rpm,刀具切深和步距自定,注意切深不能一步到位,应采取分层加工,否则刀具会因切削用量过大而损坏。
2.1零件CAM及数控加工过程
(1)在MDT6.0环境下以“IGES”格式输出保存之前所做的实体造型;进入Mastercam9.0软件工作界面后,读取刚才所输出保存的“IGES“格式的文件,删除线条文件,得到实体文件。
(2)因为模型放入的方向和加工方向一致,座椅模型的方向不用旋转,将工件顶面中心点移动至坐标原点,首先移动XY向。
(3)调整Z方向的位置。
(4)坐标原点位置调整好后,进行模型的比例缩放,由于我建模尺寸为130*80*60,故将XY方向的比例增大到原来的1.5倍。
(5)调成俯视图状态,添加一个长×宽=120mm×90mm中心处于原点的方框作为粗加工。
(6)设定毛坯尺寸为120*90*40.
(7)在“ToolParameters”粗加工参数界面空白处单击鼠标右键→“CreateNewTool”新建刀具,进入“ToolType”刀具选择界面,选择“EndMill”立铣刀,并按实际情况及相关要求调整相应参数,点击“OK”。
(8)在平铣刀数据修改界面点选“JobSetup”,进入工作范围调整界面,根据实际情况及相关要求调整相应参数。
(9)切换到“Surfaceparameters”页面,根据实际情况及相关要求调整相应参数。
(10)切换到“Roughpocketparameters”页面,根据实际情况及相关要求调整相应参数。
(11)在“Roughpocketparameters”页面点击“Cutdepths”,根据实际情况及相关要求调整相应参数,点击“OK”。
(12)点击“Gapsettings”,复选“Optimizecutorder”,点击“OK”。
(13)选取之前添加的粗加工边界,点击“Done”。
选择边界右侧靠近人的一角为粗加工入刀点,生成刀具曲线。
(14)进行一次仿真,看看自己的初步成果。
(15)进行精加工,进入精加工参数界面,选择刀具“SpherMill”球头铣刀,根据实际情况及相关要求调整相应参数。
(16)点击“OK”,回到精加工参数界面,根据实际情况及相关要求调整相应参数。
(17)切换到“Surfaceparameters”页面,根据实际情况及相关要求调整相应参数。
(18)切换到“Finishparallelparameters”页面,根据实际情况及相关要求调整相应参数。
(19)点击“Depthlimits”,根据实际情况及相关要求调整相应参数,点击“OK”。
(20)点击“Gapsettings”,复选“Optimizecutorder”,点击“OK”。
(21)点击“确定”,等待计算机计算。
(22)进行仿真,进入“OperationsManager”操作管理界面,点击“SelectAll”选择全部,并重新计算。
点击“Verify”进入仿真界面,点击播放键,开始仿真。
此为加工过程中。
(23)仿真结束后所得的加工零件图形。
(24)粗加工部分的NC代码。
%
O0001
(PROGRAMNAME-20102283-1)
(DATE=DD-MM-YY-01-06-13TIME=HH:
MM-20:
31)
N100G21
N102G0G17G40G49G80G90
(TOOL-9DIA.OFF.-9LEN.-9DIA.-10.)
N104T9M6
N106G0G90X65.Y-45.A0.S1500M3
N108G43H9Z20.
N110Z5.
N112G1Z2.F100.
N114X-64.Y-44.F1000.
………………………………….
N5236G0Z5.
N5238Z10.
N5240X-39.12Y-9.425
N5242Z5.
N5244G1Z-11.F100.
N5246Y-9.487Z-10.977F2000.
N5248Y-9.692Z-10.978
N5250Y-9.761Z-10.933
N5252Y-9.772Z-10.937
N5254Y-9.785Z-10.927
N5256Y-9.948Z-10.875
N5258Y-9.952Z-10.871
N5260Y-9.982Z-10.901
N5262Y-10.084Z-10.991
N5264Y-10.106Z-11.
N5266Z-25.895
N5268Y-10.211Z-26.
N5270G0Z5.
N5272Z20.
N5274M5
N5276G91G28Z0.
N5278G28X0.Y0.A0.
N5280M30
%
(25)精加工的部分NC代码。
%
O0001
(PROGRAMNAME-20102283-2)
(DATE=DD-MM-YY-01-06-13TIME=HH:
MM-20:
32)
N100G21
N102G0G17G40G49G80G90
(TOOL-10DIA.OFF.-10LEN.-10DIA.-6.)
N104T10M6
N106G0G90X-10.597Y-38.735A0.S2000M3
N108G43H10Z20.
N110Z5.
N112G1Z-11.F100.
……………………………………….
N5582G0Z5.
N5584Z10.
N5586X-39.12Y-9.425
N5588Z5.
N5590G1Z-11.F100.
N5592Y-9.487Z-10.977F2000.
N5594Y-9.692Z-10.978
N5596Y-9.761Z-10.933
N5598Y-9.772Z-10.937
N5600Y-9.785Z-10.927
N5602Y-9.948Z-10.875
N5604Y-9.952Z-10.871
N5606Y-9.982Z-10.901
N5608Y-10.084Z-10.991
N5610Y-10.106Z-11.
N5612Z-25.895
N5614Y-10.211Z-26.
N5616G0Z5.
N5618Z20.
N5620M5
N5622G91G28Z0.
N5624G28X0.Y0.A0.
N5626M30
%
3.快速原型制造的实践过程。
3.1快速原型制造的原理
快速原型制造是综合利用CAD技术、数控技术、激光加工技术和材料技术实现从零件设计到三维实体原型制造一体化的系统技术。
它采用软件离散—材料堆积的原理实现零件的成形。
快速制造的原理如下:
首先利用高性能的CAD软件设计出零件的三维曲面或实体模型;再根据工艺要求,按照一定的厚度在Z向(或其他方向)对生成的CAD模型进行切面分层,生成各个截面的二维平面信息;并对层面信息进行工艺处理,选择加工参数,系统自动生成刀具移动轨迹和数控加工代码。
之后对加工过程进行仿真,确认数控代码的正确性;接着利用数控装置精确控制激光束或其他工具的运动,在当前工作层(二维)上采用轮廓扫描,加工出适当的截面形状;然后铺上一层新的成形材料,进行下一次的加工,直至整个零件加工完毕。
可以看出,快速原型制造技术是一个由三维换成二维(软件离散化),再由二维到三维(材料堆积)的工作过程。
3.2快速原型制造技术的特点及适用范围
快速制造技术具有下列特点和优点:
——更适合于形状复杂的、规则零件的加工;
——减少了对熟练技术工人的需求;
——没有或减少下脚料,是一种环保型制造技术;
——成功解决了计算机辅助设计中三维造型“看得见,摸不着”的问题;
——系统柔性高,只需修改CAD模型就可生成各种不同形状的零件;
——技术集成。
设计制造一体化;
——具有广泛的材料适应性;
——不需要专门的工装夹具,大大缩短新产品试制时间;
——零件的复杂程度与制造成本关系不大。
以上特点决定了快速原型制造技术主要适合于新产品开发、快速单件及小批量零件的制造,复杂形状零件的制造、模具设计与制造等,也适合于难加工材料的制造、外形设计检查、装配检验和快速反求工程等。
3.3快速原型制造基本过程
(1)启动“RPProgram”软件后,加载模型。
(2)调整模型的比例,使其适中。
(3)对模型进行当前模型分层。
(4)进入轮廓编辑器。
(5)检查所有层的轮廓线形态。
(6)对异常的轮廓线进行处理。
(7)再次检查轮廓线的完整性。
(8)进行基础支撑设置。
(9)进入人工支撑编辑器,根据模型的形状及要求,对模型添加人工支撑。
(10)添加完成了辅助支撑。
(11)保存文件。
关闭“RPProgram”软件,打开“RPBuild”并加载先前保存的模型。
(12)对模型进行仿真。
3.4原型零件的上级制造过程。
(1)制作的原理
本实践采用的CPS25OB紫外光快速成型机。
紫外光束在计算机控制下,根据分层工艺数据连续扫描液态光敏树脂表面,利用液态光敏树脂紫外光照射凝固的原理,层层固化光敏树脂,一层固化后,工作台移一个精确距离,扫描下一层,并且保证相邻层可靠粘结,如此反复,直到成型出一个完整的零件。
(2)原型零件的制作过程
数据准备:
包括CAD三维模型的设计、STL数据的转换、制作方向的选择、分层切片以及支撑等几个过程,完成制作数据的准备。
快速成型制作:
快速成型制作过程就是将制作数据传输到成型机中,然后快速成型出原型零件的过程,他是快速成型技术的核心。
后期处理:
是指将整个零件成型完后进行的辅助处理工艺,包括零件的清洗、支撑去除、后固化、修补、打磨、表面喷漆等,目的是活的一个表面质量与机械性能更优的零件。
(3)原型零件的实践步骤
1.打开总电源开关;按下加热健;
2.打开工控开关,启动WINDOWS98/WINDOWS2000/WINDOWSNT;
3.按下伺服键;在工控机中打开RPBuild控制程序,加载加工零件的*.pmr文件;
4.加载托板位置,使之略高于液面;点击开始,重新制作,制作完成后,将托板升出液面,取出制件,将托板清洗干净。
3.5利用TV立式加工中心加工木块
TV立式加工中心操作步骤:
1.闭合车间电源总开关;开空气压缩机;
2.闭合加工中心配电空气开关;
3.闭合加工中心总开关,松“急停”按钮牛,按系统“POWERON”,加工中心启动;
4.确认压缩空气压力、液压系统压力和自动润滑系统工作正常;
5.选HANDLE方式调整X、Y、Z轴离各自的机械零点至少50mm以上,调A轴的机械坐标为300°左右;
6.按Z、X、Y、A轴顺序回机械零点;安装毛坯,调用所需的刀柄;
7.安装Ф10mm端铣刀,用MDI方式按500rpm的转速启动主轴,检查刀具安装是否良好;
8.选HANDLE方式用“试切法”找到毛坯顶面中心店,将机床坐标系的X和Y坐标记录到工件坐标G59中,而工件坐标系G59的Z值为0;
9.选HANDLE方式移动Z轴直到铣刀切削到毛坯顶面以下约1~2mm,将机床坐标系的Z坐标值记录到刀补号H32中;
10.提升主轴,停转主轴;通过现场总线网络向DNC主控计算机中请粗加工NC程序,以DNC方式实现零件的粗加工;
11.用对刀块检测并记录刀具的长度,更换刀具为R3球头铣刀,再次检测并记录刀具的长度,计算刀长的变化,根据差值修正刀补号H32中的刀补值;
12.再次通过现场总线网络向DNC主控计算机申请0度平行精加工NC程序,以DNC方式实现零件的精加工;
13.为了提高零件的表面质量,再一次通过现场总线网络向DNC主控计算机申请90度平行精加工NC程序,最终完成零件加工;
14.从虎钳上卸下工件;关机。
数控技术的前景
数控技术是一门集计算机技术、自动化控制技术、测量技术、现代机械制造技术、微电子技术、信息处理技术等多学科交叉的综合技术,是近年来应用领域中发展十分迅速的一项综合性的高新技术。
它是为适应高精度、高速度、复杂零件的加工而出现的,是实现自动化、数字化、柔性化、信息化、集成化、网络化的基础,是现代机床装备的灵魂和核心,有着广泛的应用领域和广阔的应用前景。
随着计算机技术的高速发展,传统的制造业开始了根本性变革,各工业发达国家投入巨资,对现代制造技术进行研究开发,提出了全新的制造模式。
在现代制造系统中,数控技术是关键技术,它集微电子、计算机、信息处理、自动检测、自动控制等高新技术于一体,具有高精度、高效率、柔性自动化等特点,对制造业实现柔性自动化、集成化、智能化起着举足轻重的作用。
目前,数控技术正在发生根本性变革,由专用型封闭式开环控制模式向通用型开放式实时动态全闭环控制模式发展。
在集成化基础上,数控系统实现了超薄型、超小型化;在智能化基础上,综合了计算机、多媒体、模糊控制、神经网络等多学科技术,数控系统实现了高速、高精、高效控制,加工过程中可以自动修正、调节与补偿各项参数,实现了在线诊断和智能化故障处理。
长期以来,我国的数控系统为传统的封闭式体系结构,CNC只能作为非智能的机床运动控制器。
加工过程变量根据经验以固定参数形式事先设定,加工程序在实际加工前用手工方式或通过CAD/CAM及自动编程系统进行编制。
CAD/CAM和CNC之间没有反馈控制环节,整个制造过程中CNC只是一个封闭式的开环执行机构。
在复杂环境以及多变条件下,加工过程中的刀具组合、工件材料、主轴转速、进给速率、刀具轨迹、切削深度、步长、加工余量等加工参数,无法在现场环境下根据外部干扰和随机因素实时动态调整,更无法通过反馈控制环节随机修正CAD/CAM中的设定量,因而影响CNC的工作效率和产品加工质量。
由此可见,传统CNC系统的这种固定程序控制模式和封闭式体系结构,限制了CNC向多变量智能化控制发展,己不适应日益复杂的制造过程,因此,大力发展以数控技术为核心的先进制造技术已成为我们国家加速经济发展、提高综合国力和国家地位的重要途径。
数控技术的应用不但给传统制造业带来了革命性的变化,使制造业为工业化的象征,而且随着数控技术的不断发展和应用领域的扩大,他对国计民生的一些重要行业的发展起着越来越重要的作用。
从目前世界上数控技术发展的趋势来看,主要有如下几个方面:
1.高精度,高速度的发展趋势。
尽管十多年前就出现高精度高速度的趋势,但是科学技术的发展是没有止境的,高精度、高速度的内涵也在不断变化,目前正在向着精度和速度的极限发展。
效率、质量是先进制造技术的主体。
高速、高精加工技术可极大地提高效率,提高产品的质量和档次,缩短生产周期和提高市场竞争能力。
为此日本先端技术研究会将其列为5大现代制造技术之一,国际生产工程学会将其确定为21世纪的中心研究方向之一。
在轿车工业领域,年产30万辆的生产节拍是40秒/辆,而且多品种加工是轿车装备必须解决的重点问题之一;在航空和宇航工业领域,其加工的零部件多为薄壁和薄筋,刚度很差,材料为铝或铝合金,只有在高切削速度和切削力很小的情况下,才能对这些筋、壁进行加工。
近来采用大型整体铝合金坯料"掏空"的方法来制造机翼、机身等大型零件来替代多个零件通过众多的铆钉、螺钉和其他联结方式拼装,使构件的强度、刚度和可靠性得到提高。
这些都对加工装备提出了高速、高精和高柔性的要求。
2.智能化、开放式、网络化成为当代数控发展的主要趋势。
21世纪的数控装备将是具有一定智能化的系统,智能化的内容包括在数控系统中的各个方面:
为追求加工效率和加工质量方面的智能化,如加工过程的自适应控制,工艺参数自动生成;为提高驱动性能及使用连接方便的智能化,如前馈控制、电机参数的自适应运算、自动识别负自动选定模型、自整定等;简化编程、简化操作方面的智能化,如智能化的自动编程、智能化的人机界面等;还有智能诊断、智能监控方面的内容、方便系统的诊断及维修等。
为解决传统的数控系统封闭性和数控应用软件的产业化生产存在的问题。
目前许多国家对开放式数控系统进行研究,数控系统开放化已经成为数控系统的未来之路。
所谓开放式数控系统就是数控系统的开发可以在统一的运行平台上,面向机床厂家和最终用户,通过改变、增加或剪裁结构对象(数控功能),形成系列化,并可方便地将用户的特殊应用和技术诀窍集成到控制系统中,快速实现不同品种、不同档次的开放式数控系统,形成具有鲜明个性的名牌产品。
目前开放式数控系统的体系结构规范、通信规范、配置规范、运行平台、数控系统功能库以及数控系统功能软件开发工具等是当前研究的核心。
网络化数控装备是近两年国际著名机床博览会的一个新亮点。
数控装备的网络化将极大地满足生产线、制造系统、制造企业对信息集成的需求,也是实现新的制造模式如敏捷制造、虚拟企业、全球制造的基础单元。
国内外一些著名数控机床和数控系统制造公司都在近两年推出了相关的新概念和样机,反映了数控机床加工向网络化方向发展的趋势。
数控加工技术的飞速发展必将成为以后加工技术的主要发展趋势,主要的研究对像,数控技术必将飞速的发展。
心得与体会
为期一周的数控综合实践结束了,在这一周的实践中,感觉过的很充实,也觉得时间过的太快了,还没有更加深入的学习和了解数控加工的知识,觉得课时有点少。
在这一周的学习中,第一次上机实践,我学会的三维CAD建模,学会使用了MDT三维建模软件,在老师的耐心教导下,开始使用MDT进行三维建模,在第一次的建模过程中,遇到了许许多多的问题,主要是我以前的CAD的知识忘记了,不知道该去那里找自己需要的功能,不过好在有老师和同学的帮助下,很快熟悉的MDT的运用,还是很快地完成了我所学到的槽轮的建模。
第二次的上级实践中,我了解了零件CAM及数控加工的过程,学会了使用Mastercam9.0进行数控加工的模拟,在上机的实践过程中,由于需要修改的参数过多,在老师的讲解过程中,没有完全的记住的这些参数的设定,导致后面的参数设定中,没有方向,不知道自己该如何确定参数,还有就是这Mastercam9.0是全英文的操作界面,尽管老师耐心的讲解过一次,可是还是有很多东西没有记住,在接下来的实践中,虽然花了很多时间来熟悉这个软件,不过还是很大的收获,在上机中,慢慢的向老师和同学提问,也解决了很多的问题,培养了同学间的合作能力和交流能力。
虽然花费了很长的时间,最后还是把槽轮的数控加工模拟给做出来了,其中学到了很多的知识,比如刀具的选择和刀具参数的设定等等…
第三次上级实践中,学习快速原型制造的实践过程,学会了使用Rpprogram软件进行实践的数据采集,对原型零件制作的大小和方向的设置,对零件进行分层处理,对零件的轮廓进行编辑,修复轮廓线,最后进行支撑设计,其中包括基础支撑和辅助支撑的设计以及参数的设定。
数据准备完成以后,加载模型,最后输出成型加工文件,得到模拟的加工过程。
第四次的上机实践中,学习了原型零件的上机制造过程,其中我们观察了紫外线快速成型机的工作过程,由于我们的实验材料放置的时间太长了,导致材料无法感光凝固,不过我们还是了解的紫外光快速成型机的工作原理,设备的组成,介绍了实验材料是液态光敏专用树脂,了解的如何进行快速成型。
总之,随着实践的结束,我也更加认识动手能力的重要性,凡事都要行动;也认识到我们应该培养发现问题,分析问题,解决问题的能力;更为重要的是意识到了团队合作的重要性,在学习过程中遇到不懂之处就应该虚心向别人请教,共同探讨,共同解决,这才是作为一个学生应具有的学习的品质。
更要感谢老师们耐心,细心的教导,我们才可以学到如此多的知识。
参考文献
[1]《数控综合实践指导书》,陶桂宝、刘英、张毅,编写,2005;
[2]《机械制造技术基础》,袁绩乾主编,机械工业出版社,2002;
[3]《数控加工技术》,蒋和生主编。