压力管道焊接工艺流程正式版.docx
《压力管道焊接工艺流程正式版.docx》由会员分享,可在线阅读,更多相关《压力管道焊接工艺流程正式版.docx(8页珍藏版)》请在冰豆网上搜索。
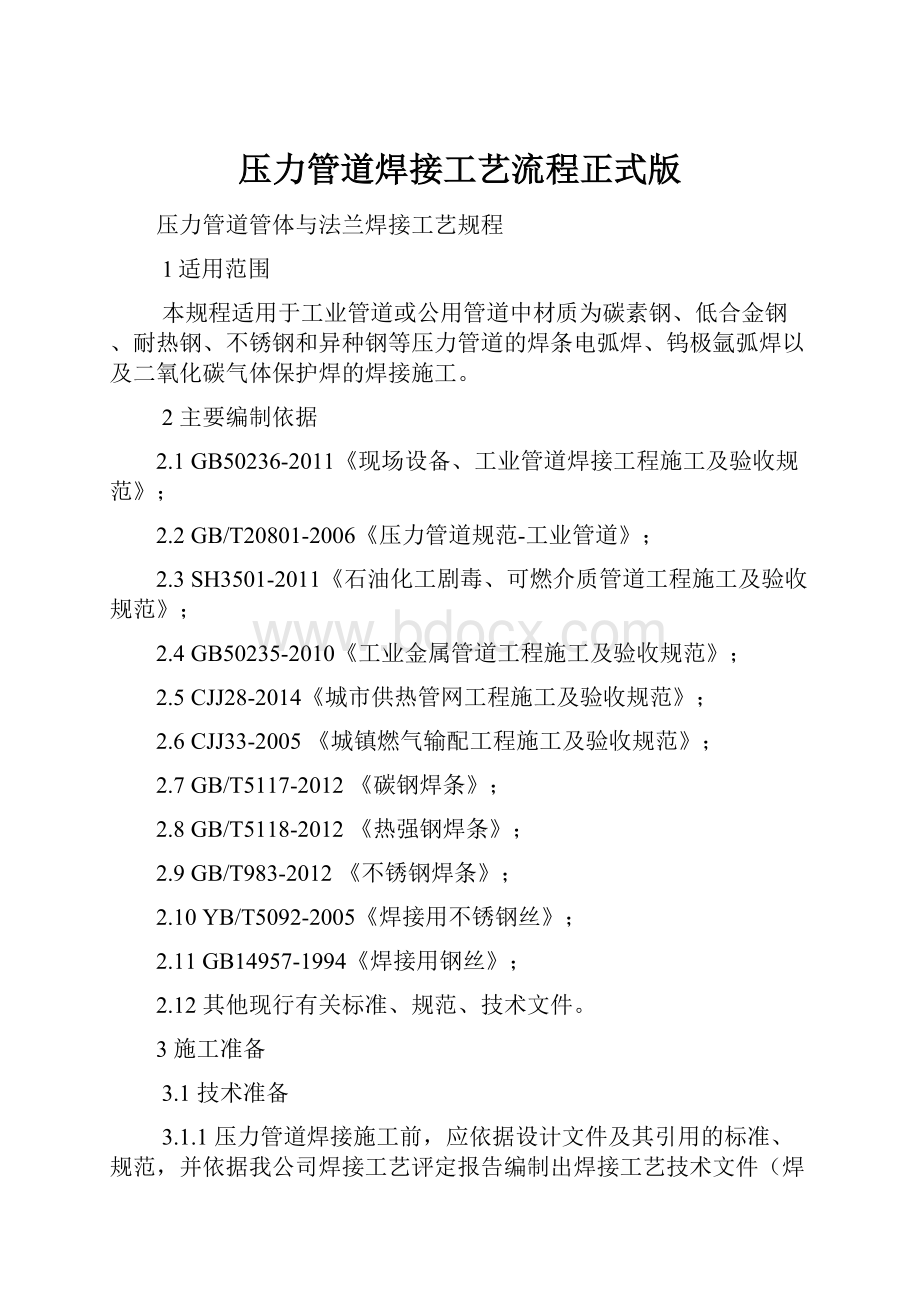
压力管道焊接工艺流程正式版
压力管道管体与法兰焊接工艺规程
1适用范围
本规程适用于工业管道或公用管道中材质为碳素钢、低合金钢、耐热钢、不锈钢和异种钢等压力管道的焊条电弧焊、钨极氩弧焊以及二氧化碳气体保护焊的焊接施工。
2主要编制依据
2.1GB50236-2011《现场设备、工业管道焊接工程施工及验收规范》;
2.2GB/T20801-2006《压力管道规范-工业管道》;
2.3SH3501-2011《石油化工剧毒、可燃介质管道工程施工及验收规范》;
2.4GB50235-2010《工业金属管道工程施工及验收规范》;
2.5CJJ28-2014《城市供热管网工程施工及验收规范》;
2.6CJJ33-2005《城镇燃气输配工程施工及验收规范》;
2.7GB/T5117-2012《碳钢焊条》;
2.8GB/T5118-2012《热强钢焊条》;
2.9GB/T983-2012《不锈钢焊条》;
2.10YB/T5092-2005《焊接用不锈钢丝》;
2.11GB14957-1994《焊接用钢丝》;
2.12其他现行有关标准、规范、技术文件。
3施工准备
3.1技术准备
3.1.1压力管道焊接施工前,应依据设计文件及其引用的标准、规范,并依据我公司焊接工艺评定报告编制出焊接工艺技术文件(焊接工艺卡或作业指导书)。
如果属本公司首次焊接的钢种,则首先要制定焊接工艺评定指导书,然后对该种材料进行工艺评定试验,合格后做出焊接工艺评定报告。
3.1.2编制的焊接工艺技术文件(焊接工艺卡或作业指导书)必须针对工程实际,详细写明管道的设计材质、选用的焊接方法、焊接材料、接头型式、具体的焊接施工工艺、焊缝的质量要求、检验要求及焊后热处理工艺(有要求时)等。
3.1.3压力管道施焊前,根据焊接作业指导书应对焊工及相关人员进行技术交底,并做好技术交底记录。
3.2对材料的要求
3.2.1被焊管件必须具有质量证明书,且其质量符合国家现行标准(或部颁标准)的要求;进口材料应符合该国家标准或合同规定的技术条件。
3.2.2焊接材料(焊条、焊丝、钨棒、氩气、二氧化碳气、氧气、乙炔气等)的质量必须符合国家标准(或行业标准),且具有质量证明书。
其中钨棒宜采用铈钨棒;氩气纯度不应低于99.95%;二氧化碳气纯度不低于99.5%;含水量不超过0.005%。
3.3焊接设备
3.3.1焊接机具设备主要包括:
交流焊机、直流焊机、氩弧焊机、二氧化碳气体保护焊机、内磨机及电动磨光机等。
3.3.2用于压力管道焊接的各类焊机必须装有电流表、电压表,并按要求定期进行检定,焊接规范参数调节应灵活。
3.4焊接人员
3.4.1压力管道焊工应具备按《特种设备焊接操作人员考核细则》考试合格的焊工合格证,且其合格项目与施焊项目相适应,并在规定的有效期内。
3.5施焊环境
a)手工电弧焊:
8m/s;
b)氩弧焊、二氧化碳气体保护焊:
2m/s。
3.5.2焊接电弧1m范围内相对湿度不得大于90%XXX。
3.5.4焊接时允许的最低环境温度如下:
碳素钢:
-20℃;低合金钢:
-10℃;中高合金钢:
0℃。
4焊接工艺
4.1压力管道焊接施工流程图(见图1)
打压试验
图1焊接施工流程图
4.2焊前准备及接头组对
法兰与管子的装配连接:
法兰与管子的装配质量不但影响管道连接处的强度和严密度,而且还影响整条管线的倾心度。
因而,在向管子上装配法兰,必须符合下列基本要求。
?
⑴、法兰中心应与管子的中心同在一条直线上。
?
⑵、法兰密封面应与管子中心垂直。
?
⑶、管子上法兰盘螺孔的位置应与相配合的设备或管件上法兰螺孔位置对应一致,同一根管子两端的法兰盘的螺孔位置应对应一致。
?
法兰与管体的焊接采用承插焊?
承插焊的优点:
没有打破口的问题,没有对口错边的问题,可将焊接位置调整为平焊。
采用CO?
气体保护焊进行焊接。
?
4.3正式焊接
4.3.1焊接引弧应在坡口内进行,严禁在管子(件)表面引燃电弧、试验电流或焊接临时支撑物。
4.3.2在焊接中应确保起弧及收弧的质量,收弧应将弧坑填满,多层焊的层间接头应相互错开。
4.4.3除焊接工艺有特殊要求外,每条焊缝应一次连续焊完,如因故被迫中断,应采取缓冷措施,再焊时应仔细检查确认无裂纹后,方可按焊接工艺继续施焊。
有预热要求的管材应按预热要求重新预热后施焊。
4.3.5焊接时焊接工艺参数均按表5、表6选择。
表5二氧化碳气体保护焊工艺参数
焊接方法
焊条直径(mm)
允许电流(A)
最佳电流(A)
二氧化碳气体保护焊
Φ0.8
60~160
60~100
二氧化碳气体保护焊
Φ1.0
70~240
70~120
二氧化碳气体保护焊
Φ1.2
90~260
90~175
二氧化碳气体保护焊
Φ1.6
110~290
110~200
二氧化碳气体保护焊
Φ2.0
120~350
120~250
表6钨极氩弧焊工艺参数
焊接方法
焊丝直径(mm)
焊接电流(A)
电弧电压(V)
气体流量(L/min)
钨极氩弧焊
Φ2~2.5
80~100
12
8~10
4.3.6根据设计及焊接工艺评定需焊前预热的管子(件),焊前应按要求进行局部预热。
具体程序按照《压力管道安装通用热处理工艺规程》中的有关条款执行。
4.3.7当采用氩弧焊打底时,应及时进行打底焊缝的检查,合格后尽快进行盖面焊接,以防止产生裂纹。
4.3.8有淬火倾向的管材施焊过程中,层间温度应不低于规定的预热温度的下限。
4.3.9中、高合金钢(含铬量≥3%或合金总含量>5%)的管子(件)焊接时,为防止根层氧化或过烧,内壁应充氩气或混合气体保护。
4.3.10厚壁大直径管的焊接应采用多层多道焊进行逐层焊接,其中氩弧焊打底的焊层厚度不小于3mm,各层经自检合格后方可焊接次层,直至完成。
4.3.11为减少焊接变形和应力,直径大于194mm的管子(件)宜采用二人对称施焊。
4.3.12对需做检验的隐蔽焊缝,应经检验合格后,方可进行其他工序。
4.3.13低温钢、奥氏体不锈钢、耐热耐蚀高合金钢以及奥氏体与非奥氏体异种钢接头焊接时应符合下列规定:
(a)应在焊接作业指导书规定的范围内,在保证焊透和熔合良好的条件下,采用小电流、短电弧、快焊速和多层多道焊工艺,并应控制层间温度。
(b)对抗腐蚀性能要求高的双面焊缝,与腐蚀介质接触的焊层应最后施焊。
(c)低温钢焊接完毕,宜对焊缝进行表面焊道退火处理。
(d)奥氏体不锈钢焊缝及其附近表面应进行酸洗、钝化处理。
4.3.14管道冷拉口所使用的工卡具,应待焊接及热处理工作结束后方可拆除。
5质量检查及评定
5.1焊缝质量检查
5.1.1焊缝应进行外观自检和专检,自检率为100%,专检率根据设计要求执行。
外观检查质量应符合设计要求,当设计无规定时,应符合以下要求:
(a)焊缝外观成型良好,与母材圆滑过渡,其宽度以每边盖过坡口边缘2mm为宜。
(b)焊缝表面不允许有裂纹、未熔合、气孔、夹渣、飞溅等存在。
(c)设计温度低于-29℃的管道、不锈钢和淬硬倾向较大的合金钢管道焊缝表面,不得有咬边现象。
其他材质管道咬边深度不大于0.5mm,连续咬边长度不大于100mm,且焊缝两侧咬边总长不大于该焊缝全长的10%。
(d)焊缝表面不得低于管道表面。
焊缝余高≤1+0.2焊缝坡口宽度,且不大于3mm。
(e)焊接接头错边不应大于壁厚的10%XXX,且不大于2mm。
(a)压力管道焊缝无损检测方法:
抽检率、合格等级和执行的标准应按设计要求执行。
(b)按百分比抽检的焊接接头,应由质量检查员根据焊工和现场的情况指定检测位置。
(c)同管线的焊接接头抽样检验,若有不合格时,应按该焊工的不合格数加倍检验,若仍不合格,则应全部检验。
(d)不合格的焊缝同一部位的返修次数,非合金钢管道不得超过3次,其余钢种管道不得超过2次。
经返修后的焊缝按原要求复检合格。
(e)其他要求按本公司《无损检测通用作业指导书》的规定执行。
5.1.3合金焊缝光谱分析按设计规定执行。
5.1.4焊后热处理质量检验根据设计规定进行,当焊缝的硬度值超过规定的范围时,应按班次作加倍复检,并查明原因,对不合格焊缝重新进行热处理及硬度测试。
6安全技术措施
6.1所有带电设备必须有良好的接地,焊工及热处理工在启动带电设备时,必须首先检查设备接地是否良好。
6.2非电工严禁拆装一次线,焊接及热处理设备的接线、检查、维修必须在切断电源后进行。
6.3焊接设备裸露部分、转动部分及冷却部分均应设保护罩,焊工所用导线必须是绝缘良好的橡皮线,在连接电焊钳一端的接头至少有5米绝缘软导线。
6.4焊工在闭合和断开电源开关时,应戴干燥手套,通电后不准触摸导电部分。
6.5焊工离开工作场所时,必须随即切断电源,检查施焊场地确无火种后离去。
6.6禁止焊接带有压力的管道;禁止在存有易燃易爆物品的车间、室及其周围5米的地方进行焊接与切割。
6.7高空焊接与热处理时,应戴安全帽、安全带并携带工具袋,所使用的工具一律放在工具袋内,并放置在可靠的地点。
在焊接与热处理场所上部临时吊装物体时,焊工及热处理工应自动避开。
6.8高空作业使用的脚手架一定要用软铁丝扎牢固,焊工及热处理工使用前要认真检查,禁止登在梯子的最高层进行各种操作。
6.9打药皮时,要防止药皮伤害眼睛,两人对称焊时,应互防弧光打眼。
6.10热处理部位应设明显的警示和隔离措施。
加热电缆及热电偶信号电缆应尽可能悬挂设置,防止意外损伤。
6.11其他安全技术要求按本公司《安全生产管理制度》的规定执行。
7质量记录
7.1工程竣工后,按设计或合同规定及时向业主移交焊接质量记录。
压力管道管体与法兰焊接工艺规程
辽宁汾西华益实业有限责任公司
2016年1月