配合件的数控加工工艺分析与仿真.docx
《配合件的数控加工工艺分析与仿真.docx》由会员分享,可在线阅读,更多相关《配合件的数控加工工艺分析与仿真.docx(34页珍藏版)》请在冰豆网上搜索。
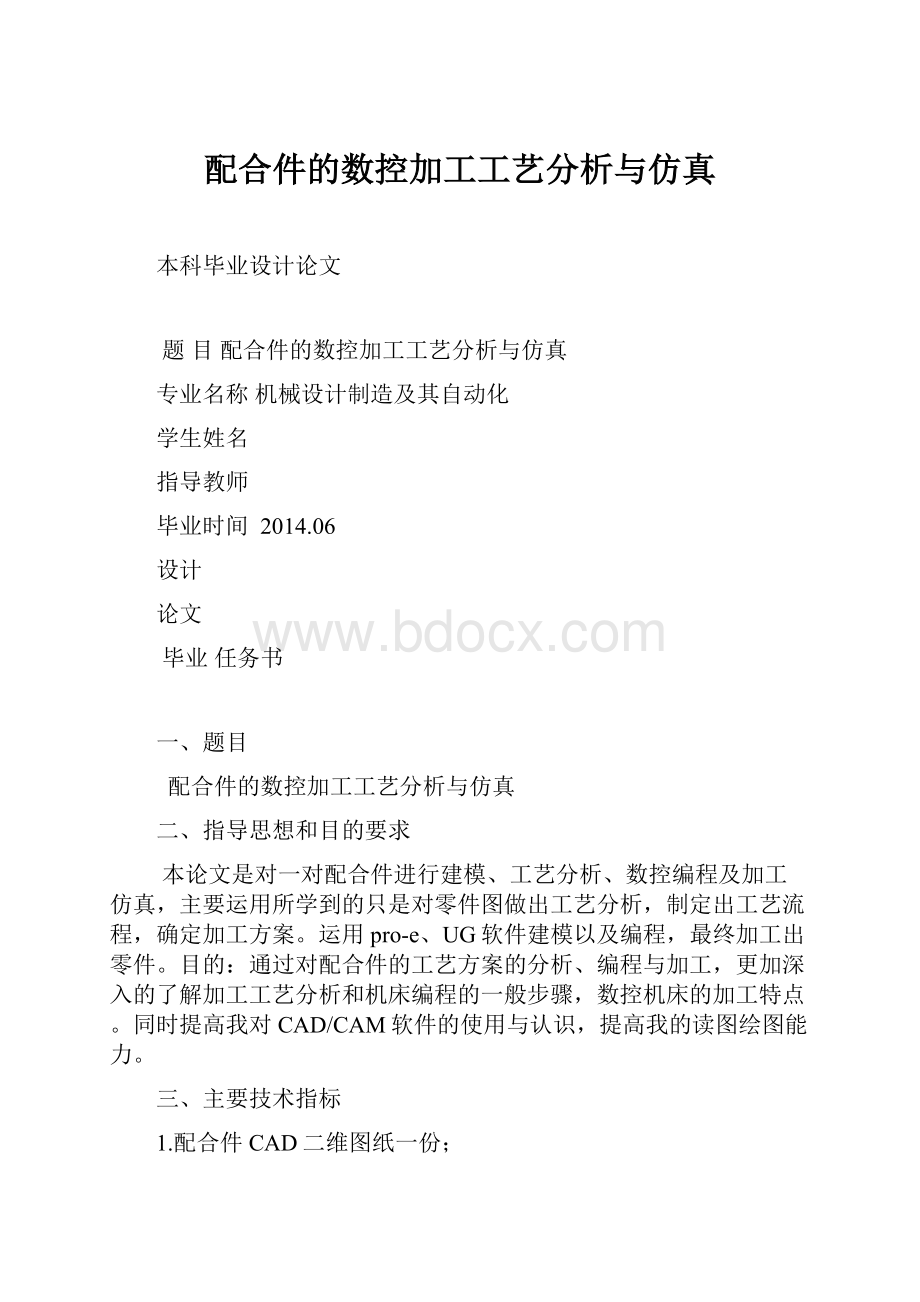
配合件的数控加工工艺分析与仿真
本科毕业设计论文
题目配合件的数控加工工艺分析与仿真
专业名称机械设计制造及其自动化
学生姓名
指导教师
毕业时间2014.06
设计
论文
毕业任务书
一、题目
配合件的数控加工工艺分析与仿真
二、指导思想和目的要求
本论文是对一对配合件进行建模、工艺分析、数控编程及加工仿真,主要运用所学到的只是对零件图做出工艺分析,制定出工艺流程,确定加工方案。
运用pro-e、UG软件建模以及编程,最终加工出零件。
目的:
通过对配合件的工艺方案的分析、编程与加工,更加深入的了解加工工艺分析和机床编程的一般步骤,数控机床的加工特点。
同时提高我对CAD/CAM软件的使用与认识,提高我的读图绘图能力。
三、主要技术指标
1.配合件CAD二维图纸一份;
2.pro-E建造三维模型;
3.UG软件出程序;
4.制作出工艺卡片;
5.撰写一份毕业论文。
四、进度和要求
第一阶段:
熟悉课题,收集借阅有关资料、粗拟开题报告;(第1-2周)
第二阶段:
对要加工的零件进行工艺分析;(第3-6周)
第三阶段:
数控加工工艺的确定;(第7-10周)
第四阶段:
对零件进行实体建模;(第10-11周)
第五阶段:
对零件进行UG编程及加工仿真;(第11-12周)
第六阶段:
完成论文。
(第12-15周)
第七阶段:
答辩准备(第16周)
五、主要参考书及参考资料
[1]方沂.《数控机床编程与操作》,国防工业出版社,1999年版
[2]王爱玲等.《现代数控原理及控制系统》,国防工业出版社,2002年版
[3]王爱玲等.《现代数控机床实用操作技术》,国防工业出版社,2005年版
[4]周济,周艳红.《数控加工技术》,国防工业出版社,2003.9
[5]谬效果.《数控技术》,湖北科学技术出版社,2003.7
[6]黄道业.《数控铣床(加工中心)编程、操作及实训》,合肥工业大学出版社,2005.8
[7]郑盛新.《数控机床与编程加工习题集》,合肥工业大学出版社,2005.8
[8]陈德生.《机械制造工艺学[M].》,杭州:
浙江大学出版社,2007.1
[9]赵家齐.《机械制造工艺学课程设计指导书[M].》,北京:
机械工业出版社,2000.
[10]古文生.数控机床及应用[M].北京:
电子工业出版社,2002.
[11]庞为.机匣制造技术[M].北京:
科学出版社,2002.
[12]邓文英,郭晓鹏.金属工艺学[M].北京:
高等教育出版社,2008.
[13]杜君文,邓广敏.数控技术[M].天津:
天津大学出版社,2002.
[14]余英良.《数控机床加工技术》,高等教育出版社,2007.5.1
[15]余英良.《数控加工编程及操作》,高等教育出版社,2005年1月第一版
[16]李开林.《UGNX4三维造型》,电子工业出版社,2009年1月第三次印刷
[17]周晓萍.《机械识图与CAD》,安徽教育出版社,2007年9月第一版
[18]朱宝林.《公差配合与技术测量》,华中科技大学出版社,2005年3月第一版
学生田晓指导教师李郁系主任魏生民
摘要
数控技术,是采用数字控制的方法对某一工作过程实现自动控制的技术。
它所控制的通常是位置、角度、速度等机械量和与机械能量流向有关的开关量。
数控的产生依赖于数据载体和二进制形式数据运算的出现。
而数控铣床是在普通铣床上集成了数字控制系统,可以在程序代码的控制下较精确地进行铣削加工的机床。
本文为配合零件的编程与加工,通过数控铣床的加工,针对具体的零件,进行了工艺方案的分析,加工方案的确定,刀具和切削用量的选择,确定加工顺序和加工路线,数控加工程序编制。
本文主要从三维模型的建造、加工工艺分析和机床编程的一般步骤着手,提高我对CAD/CAM软件的使用与认识、提高我的读图绘图能力。
最后通过自动编程与加工,希望能在过程中发现更好的编程方法和加工方法,提高效率,而且运用于实际工作中能够更深入的了解数控机床的加工特点。
关键词:
数控铣床,配合零件,三维模型,加工工艺,自动编程
ABSTRACT
Numericalcontroltechnology,isthemethodthatUSESdigitalcontrolofoneoftheworkingprocessofautomaticcontroltechnology.Itisusuallycontrolledbytheposition,Angle,speedandothermechanicalquantityandamountrelatedtothemechanicalenergyflowswitch.Numericalcontroldependsonthedatacarrierandthebinaryformdataoperation.AndCNCmillingmachineisinthecommonmillingmachineuseddigitalcontrolsystem,canbeunderthecontroloftheprogramcodeaccuratelyformillingmachine.
Thisarticleforprogrammingandmachiningoftheparts,throughtheprocessingofCNCmillingmachine,forspecificpartsoftheprocessofanalysis,theschemeofmachiningtoolandcuttingparameterselection,determinetheprocessingorderandprocessingroute,thencmachiningprogramming.Thisarticlemainlyfromtheconstructionofthe3dmodel,processingtechnologyanalysisandthegeneralstepsofmachinetoolprogramming,improvemyunderstandingoftheuseofCAD/CAMsoftwareandfiguredrawing,improvemyreadingability.Finally,automaticprogrammingandprocessing,thehopecanfindbetterwaysofprogrammingandprocessingintheprocessmethod,improveefficiency,andappliedtorealworkcanfurtherunderstandthemachiningcharacteristicofncmachinetools.
KEYWORDS:
CNCmillingmachine,cooperatewithparts,3dmodel,processingtechnology,automaticprogramming
目录
第一章绪论5
1.1数控技术发展及现状5
1.1.1数控技术的发展5
1.1.2数控技术在国内的现状5
1.2本课题研究的目的及意义6
1.3课题的主要内容7
第二章零件的工艺分析8
2.1零件图工艺分析8
2.1.1零件图分析8
2.1.2零件毛坯选择9
2.2零件定位基准选择9
2.2.1精、粗基准选择9
2.2.2基准的确定10
2.3零件加工工艺规程分析11
2.3.1配合件01工件工艺规程分析11
2.3.2配合件02工件工艺规程分析12
第三章运用pro-E建造三维模型13
3.1pro-E简单介绍13
3.2创建零件模型14
3.2.1配合件01工件建模14
3.2.2配合件02工件建模20
第四章配合件的编程及加工仿真24
4.1UG编程的简单介绍24
4.2以配合件02工件为例进行UG编程25
4.2.1对02工件进行模型分析25
4.2.2加工坐标系、几何体设定25
4.2.3创建加工刀具26
4.2.4加工程序顺序管理26
4.2.5对02工件加工编程27
4.3刀路仿真及加工代码输出30
4.3.1刀路仿真及加工代码的输出30
4.3.2配合件02工件输出部分加工代码32
第五章配合件工艺表、程序单38
5.1配合件01工件工艺表、程序单38
5.2配合件02工件工艺表、程序单40
第五章全文总结42
致谢43
参考文献44
毕业设计小结45
附录46
第一章绪论
1.1数控技术发展及现状
1.1.1数控技术的发展
数控加工技术先后经历了电子管(1952年)、晶体管(1959年)、小规模集成电路(1965年)、大规模集成电路及小型计算机(1970年)和微处理机或微型计算机(1974年)等第五代数控系统。
前三代属于采用专用控制计算机的硬接线(硬件)数控装置,一般简称NC装置。
第四代数控系统出现了采用小型计算机代替专用硬件控制计算机,这种称之为计算机数控系统(computerizednumericalcontrol)也就是CNC。
自1979年开始以微处理机为核心的数控装置(microcomuperizednumericalcontrol)也就是MNC,得到迅速发展。
我国数控系统研究起步于1958年,60、70年代研制了晶体管数控系统和集成电路数控系统,在这一段时间里,由于国外技术封锁和我国的基本条件限制,数控系统发展较慢。
到70年代开始,数控技术在车、铣、钻、磨、齿轮加工、电加工等领域全面展开,数控加一工一中心研制成功。
我国在二十世纪八十年代初期通过引进、消化、吸收国外的先进技术,从美国、德国等国家引进了一些新技术,又在“七五”、“八五”、“九五”期间对伺服驱动技术进行重大科技项目攻关,取得了重大成果。
代表我国当前数控机床水平的中华1型、航天1型数控系统已能够向国内各机床制造厂配套自身的数控系统所需的伺服系统,还应用于一些老设备的技术改造。
1.1.2数控技术在国内的现状
目前,我国的机床工业正从生产大国逐渐变为机床强国,主要体现在数控机床产品的技术水平和质量不断发展和提高。
其中,特别是数控系统和数控机床的可靠性不断提高,由于科学技术人员的不懈努力,新的数控产品也不断涌现。
具体体现在以下三点:
1)现已能生产小型仪表机床、重型机床,各种精密的、高度自动化的、高效率的机床。
2)目前生产的数控系统(以数控机床为主)大部分都是以PC机作为控制核心,使得我国生产的数控系统在硬件、软件方面都有不同程度的提升,增强了市场竞争力。
3)目前已能生产100多种数控机床,并研制出六轴五联动的数控系统,可以应用于更加复杂的曲面加工。
国产的数控机床精度已经提高到0.001mm,系统的可靠性也大大提高,这些都源于我国生产的数控系统均采用模块化设计,并且运用超大规模集成电路,保证了系统的整体可靠性。
1.2本课题研究的目的及意义
制造业是国民经济的命脉,机械制造业又是制造业中的支柱与核心。
在现代社会生产领域中,计算机辅助设计、计算机辅助制造、计算机辅助管理以及将它们有机地集成起来的计算机集成制造(CIM)已经成为现代企业科技进步和实现现代化的标志。
用计算机辅助制造工程技术对我国传统产业进行改造,是我国制造业走向世界、走向现代化的必由之路。
在国际竞争日益激烈的今天,作为计算机辅助制造工程技术基础的数控加工技术在机械制造业中的地位显得愈来愈重要。
现在很多工业发达国家的数控化率可达30%以上,数控机床已成为机械制造业的主要设备。
我国从1958年开始研制和使用数控机床,至今在数控机床的品种、数量和质量等方面得到了长足的发展。
特别是在改革开放以来,我国数控机床的总拥有量有了显著的增加。
数控加工技术的应用和普通机床的数控化改造已成为传统机械制造企业提高竞争力、摆脱困境的有效途径。
数控机床是根据加工程序对工件进行自动加工的先进设备,工件的加工质量主要由机床的加工精度、工艺和加工程序的质量决定,基本上排除了机床操作人员手工操作技能的影响,但对操作者的综合素质提出了较高的要求。
数控机床要按照数控加工程序自动进行零件的加工,必须由机床操作人员具体实施。
可以说,数控加工工艺方案是通过机床操作人员在数控机床上实现的,数控加工现场经验的积累又是提高数控加工工艺和数控加工程序质量的基础。
因此,数控机床的操作是企业生产过程中一个重要的环节,数控机床操作人员的素质和水平将直接影响企业的生产效率、产品质量以及生产成本,高素质的数控机床操作人员是保证数控加工工艺得以正确和顺利实施的重要条件之一。
从以上可以看出,本课题研究的目的在于设计比较经济的工艺规程,出出合理的G代码程序,实现理论与实践的相结合,提高自己的素质和水平能够更加充分的利用数控机床加工。
1.3课题的主要内容
分析课题——配合件,编制出简单合理的加工程序以及制定出合理有效的工艺规程,充分利用数控加工的优势。
在编程、加工仿真过程中主要有一下问题:
1)分析图样容易出现编程繁琐的问题;
2)对于薄壁零件的加工处理;
3)进行仿真时,加工执行时间长。
设计的主要内容:
1)对零件图进行工艺分析;
2)分析工艺规程;
3)制定出工艺规程;
4)造出三维模型;
5)UG编程出G代码;
6)制作出工艺表、程序单。
第二章零件的工艺分析
2.1零件图工艺分析
2.1.1零件图分析
图2-101工件图
图2-102工件图
零件的尺寸公差在0.02—0.1mm之间,表面粗糙度Ra6.3um,其余达到Ra3.2um。
而且01工件有厚度为2mm薄壁,区域面积较大相对难加工,加工时容易产生变形处理不好可能会导致其壁厚难以保证。
零件形状如图2-1、2-2工件图所示,有轮廓加工、凸面、凸曲面、凹面、凹曲面加工及打孔等。
由于典型零件需要配合零件且有薄壁,形状虽然不是很复杂,但是工序复杂,表面质量和精度要求高,所以从精度要求上考虑,定位和工序安排比较关键。
2.1.2零件毛坯选择
两配合件01、02从图上可以看出大轮廓为Φ125mm大圆,切掉两端两平端距离为110mm。
01工件厚24,02工件厚30。
考虑到现有机床工作台面是一个平面所以装夹方式是用压板压,所以先下料219*114*26mm和219*114*34mm各留2mm余量。
下料长219mm是留有两端压压板45mm余量。
材料:
铝料。
2.2零件定位基准选择
在制定零件的加工工艺流程时,基准选择的好坏不仅影响零件的加工位置精度,而且对零件个表面的加工顺序也有很大的影响。
基准有粗、精基准之分。
选择定位基准时要从保证工件的精度要求出发,所以定位基准的选择顺序应从精基准到粗基准。
2.2.1精、粗基准选择
精基准原则:
1)基准重合原则:
应尽量选用被加工表面的设计基准作为精基准;
2)基准统一原则:
应尽可能选择同一组精基准加工工件上尽可能多的加工表面,以保证各加工表面之间的相对位置关系;
3)互为基准原则:
当工件上两个加工表面之间的位置精度要求比较高时,可以采用两个加工表面互为基准反复加工的方法;
4)自为基准原则:
一些表面的精加工工序,要求加工余量小而均匀,常以加工表面自身为精基准。
粗基准:
最初工序中,只能选择以未加工的毛坯面作为定位基准,称为粗基准。
精基准:
用已加工过的表面为定位基准,称为精基准。
粗基准原则:
1)如果必须首先保证工件上加工表面与不加工表面之间的位置要求,则应以不加工表面为粗基准;
2)如果工件必须首先保证某重要表面的加工余量均匀,则应选择该表面为粗基准;
3)零件上有较多加工面时,为使各加工表面都得到足够的加工余量,应选择毛坯上加工余量最小的表面为粗基准;
4)选择粗基准的表面,应尽可能平整和光洁、不能有飞边、尧口、冒口及其它缺陷,以便定位准确、可靠;
5)粗基准应避免重复使用,在同一尺寸方向通常只允许使用一次,否则会造成较大的定位误差。
2.2.2基准的确定
根据以上基准选择原则,结合实际零件以及按照基准面先主后次、先近后远、先里后外、先粗加工后精加工、先面后孔的原则依次划分工序加工原则。
在对毛坯219*114*26mm和219*114*34mm料粗开时:
1)先铣大面以一面为粗基准,多次翻面加工铣厚度24mm和30mm到位;
2)以一侧面为拉直粗基准铣另一侧面见光,再倒压板以铣光侧面为精基准铣另一侧面,铣宽度110mm到位;
3)以同样的方法铣长度215mm到位。
2.3零件加工工艺规程分析
2.3.1配合件01工件工艺规程分析
图2-3图2-4
配合件01工件如图图2-3带有凹槽周边有薄壁,如图图2-4是凸出曲面和中间部分下凹曲面。
如果以图2-4作为A面先加工,翻面以其为基准面加工作为B面的图2-3就不好装夹,因为图2-4面不是一个平面。
所以选择图2-3面为A面,做完A面以其为基准面翻面加工作为B面的图2-4面。
但是图2-3面做A面存在问题是有薄壁如果翻面做基准面很有可能损坏其薄壁,可是又不能把图2-4作为A面,只能将图2-3作为A面。
所以,最终解决办法是以图2-3作为A面,图2-4作为B面。
先将毛料铣到215*110*24mm到位,然后以B面做基准加工A面,A面加工完后用水泥填充凹槽及凹槽以外,将A面填平,防止薄壁变形或损坏,再以A面作为基准加工B面。
根据实际情况结合理论知识将加工基准坐标设在工件中心位置是合理的,沿着长边215mm作为X方向,短边110mm作为Y方向。
A面加工,定好坐标后先做整体开粗铣出形状,再铣下凹曲面,完了对薄壁处做精修,清根、倒尖角。
粗开时侧壁可以多留点余量,对薄壁加工时可多次反复加工,编程选择层优先,吃刀量给少点,防止变形。
最后铣Φ20mm两个窝,窝深10mm;再将两Φ10mm的孔,初孔做到Φ8mm,作为工艺孔。
翻面进行B面加工,以两Φ8mm的孔拉直找正,定坐标,开粗铣形,再铣下凹曲面跟凸出曲面,清根、倒尖角;做两Φ10mm的孔到位。
最后再走两个切断程序去除压板余量。
2.3.2配合件02工件工艺规程分析
图2-5图2-6
配合件02工件如图图2-5中间部分凸台比周围高,如图图2-6中间是凹槽,凹槽里有一凸出曲面但是却低于周围部分,而且图2-6壁还是挺厚的。
所以,可以选择图2-6这面作为A面,图2-5这面作为B面加工。
基准坐标系的选择与01工件一样。
为了保险,在A面做基准面加工B面时也可以采用01工件的方法用水泥把凹槽填平。
A面加工,定好坐标后先做整体开粗铣出形状,再铣凸曲面及凹槽,清根、倒尖角;再将两Φ10mm的孔,初孔做到Φ8mm,作为工艺孔。
翻面进行B面加工,以两Φ8mm的孔拉直找正,定坐标,开粗铣形,再铣下凸台,清根、倒尖角;做两Φ10mm的孔到位。
最后再走两个切断程序去除压板余量。
第三章运用pro-E建造三维模型
3.1pro-E简单介绍
pro-E是Pro/Engineer的简称,更常用的简称是ProE或Pro/E,Pro/E是美国参数技术公司(ParametricTechnologyCorporation,简称PTC)的重要产品,在目前的三维造型软件领域中占有着重要地位。
pro-e作为当今世界机械CAD/CAE/CAM领域的新标准而得到业界的认可和推广,是现今主流的模具和产品设计三维CAD/CAM软件之一。
Pro/E第一个提出了参数化设计的概念,并且采用了单一数据库来解决特征的相关性问题。
另外,它采用模块化方式,用户可以根据自身的需要进行选择,而不必安装所有模块。
Pro/E的基于特征方式,能够将设计至生产全过程集成到一起,实现并行工程设计。
它不但可以应用于工作站,而且也可以应用到单机上。
Pro/E采用了模块方式,可以分别进行草图绘制、零件制作、装配设计、钣金设计、加工处理等,保证用户可以按照自己的需要进行选择使用。
1)参数化设计
相对于产品而言,可以把它看成几何模型,而无论多么复杂的几何模型,都可以分解成有限数量的构成特征,而每一种构成特征,都可以用有限的参数完全约束,这就是参数化的基本概念;
2)基于特征建模
Pro/E是基于特征的实体模型化系统,工程设计人员采用具有智能特性的基于特征的功能去生成模型,如系列化快餐托盘设计[1]腔、壳、倒角及圆角,您可以随意勾画草图,轻易改变模型。
这一功能特性给工程设计者提供了在设计上从未有过的简易和灵活,特别是在设计系列化产品上更是有得天独到的优势;
3)单一数据库
Pro/Engineer是建立在统一基层上的数据库上,不象一些传统的CAD/CAM系统建立在多个数据库上。
所谓单一数据库,就是工程中的资料全部来自一个库,使得每一个独立用户在为一件产品造型而工作,不管他是哪一个部门的。
换言之,在整个设计过程的任何一处发生改动,亦可以前后反应在整个设计过程的相关环节上。
例如,一旦工程详图有改变,NC(数控)工具路径也会自动更新;组装工程图如有任何变动,也完全同样反应在整个三维模型上。
这种独特的数据结构与工程设计的完整的结合,使得一件产品的设计结合起来。
这一优点,使得设计更优化,成品质量更高,产品能更好地推向市场,价格也更便宜。
大型捕鲸船装配设计;
4)直观装配管理
Pro/ENGINEER的基本结构能够使您利用一些直观的命令,例如“贴合”、“插入”、“对齐”等很容易的把零件装配起来,同时保持设计意图。
高级的功能支持大型复杂装配体的构造和管理,这些装配体中零件的数量不受限制;
5)易于使用
菜单以直观的方式联级出现,提供了逻辑选项和预先选取的最普通选项,同时还提供了简短的菜单描述和完整的在线帮助,这种形式使得容易学习和使用。
3.2创建零件模型
零件图
3.2.1配合件01工件建模
1.打开pro-E中新建一个窗口,文件名输入“01gongjian”,注意:
选择使用缺省‘mmns_part_solid’。
2.首先做出厚11mm图轮廓外形的拉伸实体,拉伸位置定义,选择FRONT面绘制轮廓外形,拉伸选择拉伸厚度11mm,确认拉伸,如图3-1、3-2、3-3所示。
图3-1草绘界面图3-2拉伸
图3-3拉伸实体
上图如图3-1草图那样放置是为了下一步两椭圆画起来方便。
3.拉伸位置定义,选择图3-3实体上表面作为草绘平面,绘制草图,拉伸选择厚度为6mm,确认拉伸,做出突出台如图3-4、3-5所示。
图3-4草绘界面图3-5拉伸凸台实体
4.拉伸位置定义,使用先前平面作为草图平面,绘制两端头草图,拉伸选择厚度
5.
4.3.2配合件02工件输出部分加工代码
精下凹槽凸曲面,由于程序太大这里截了部分程序
%
N0020G0G90G54Z100
N0030