回转窑耐火材料的选用及施工注意事项.docx
《回转窑耐火材料的选用及施工注意事项.docx》由会员分享,可在线阅读,更多相关《回转窑耐火材料的选用及施工注意事项.docx(14页珍藏版)》请在冰豆网上搜索。
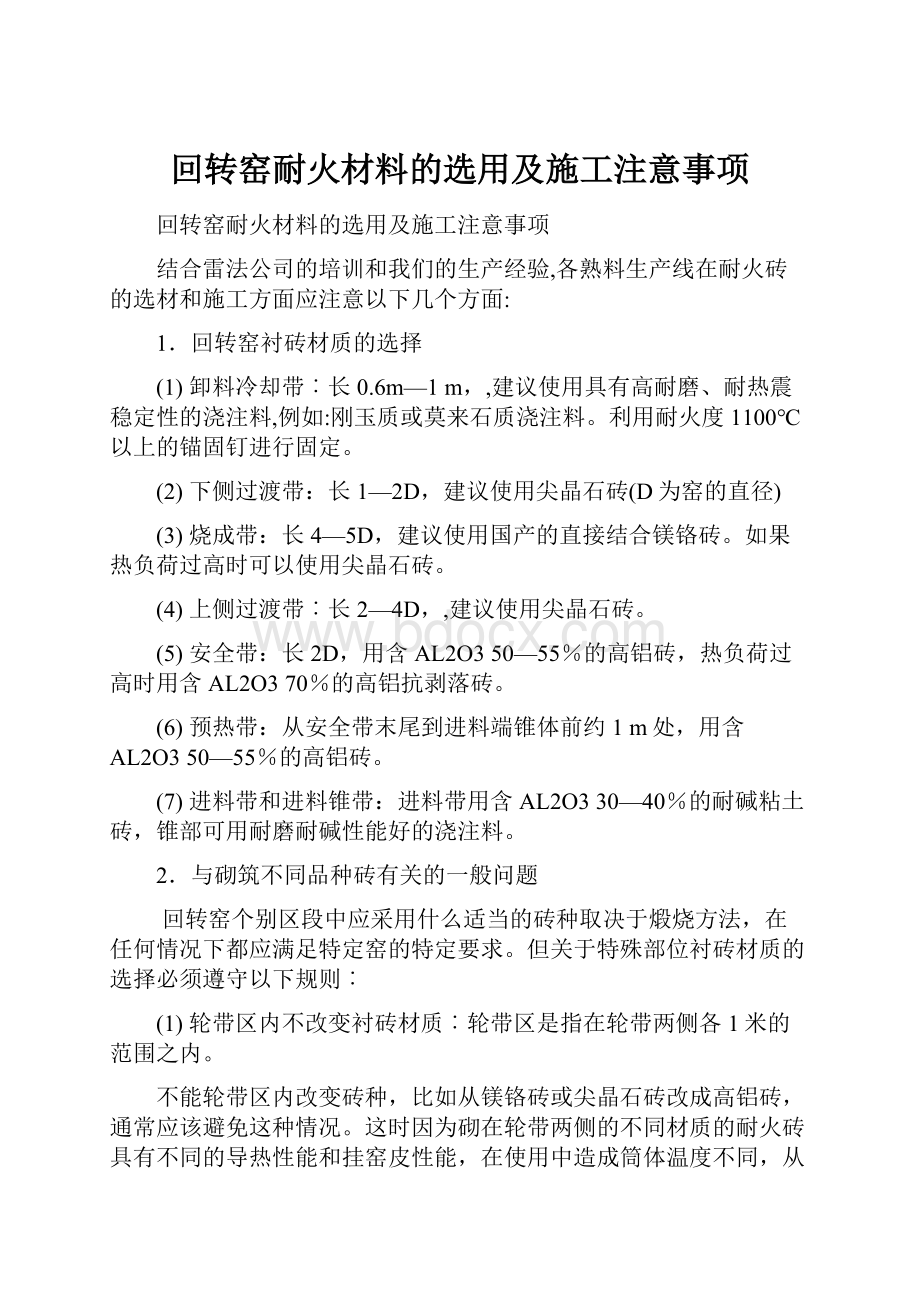
回转窑耐火材料的选用及施工注意事项
回转窑耐火材料的选用及施工注意事项
结合雷法公司的培训和我们的生产经验,各熟料生产线在耐火砖的选材和施工方面应注意以下几个方面:
1.回转窑衬砖材质的选择
(1)卸料冷却带︰长0.6m—1m,,建议使用具有高耐磨、耐热震稳定性的浇注料,例如:
刚玉质或莫来石质浇注料。
利用耐火度1100℃以上的锚固钉进行固定。
(2)下侧过渡带:
长1—2D,建议使用尖晶石砖(D为窑的直径)
(3)烧成带:
长4—5D,建议使用国产的直接结合镁铬砖。
如果热负荷过高时可以使用尖晶石砖。
(4)上侧过渡带︰长2—4D,,建议使用尖晶石砖。
(5)安全带:
长2D,用含AL2O350—55%的高铝砖,热负荷过高时用含AL2O370%的高铝抗剥落砖。
(6)预热带:
从安全带末尾到进料端锥体前约1m处,用含AL2O350—55%的高铝砖。
(7)进料带和进料锥带:
进料带用含AL2O330—40%的耐碱粘土砖,锥部可用耐磨耐碱性能好的浇注料。
2.与砌筑不同品种砖有关的一般问题
回转窑个别区段中应采用什么适当的砖种取决于煅烧方法,在任何情况下都应满足特定窑的特定要求。
但关于特殊部位衬砖材质的选择必须遵守以下规则︰
(1)轮带区内不改变衬砖材质︰轮带区是指在轮带两侧各1米的范围之内。
不能轮带区内改变砖种,比如从镁铬砖或尖晶石砖改成高铝砖,通常应该避免这种情况。
这时因为砌在轮带两侧的不同材质的耐火砖具有不同的导热性能和挂窑皮性能,在使用中造成筒体温度不同,从而形成不同的轮带间隙,轮带便不能在整个表面上最佳的运行,加大了砖衬所受的机械应力,就相应地导致这个部位耐火砖的过早损坏。
(2)在烧成带不能采用几种不同品种的镁质砖;小区段的镁铬砖砌在高铝砖和尖晶石砖之间的过渡带内,由于他们的荷重软化温度不同,镁铬砖便暴露在高的机械负荷之下,通常的结果是耐火砖的过早损坏。
3.镶砌砖缝的预留
耐火材料的热膨胀系数不同,镁质砖的热膨胀性大,必须在环缝预留砖缝补偿,干法砌筑砖体必须粘贴2mm纸板,湿法则采用胶泥进行调整;在窑的轴向和径向上高铝砖和轻质砖的膨胀只比整个窑体的膨胀性稍大些,所以他们在窑内不需要任何增加接缝。
施工中窑内各带中的膨胀接缝需按以下规定进行预留︰
(1)卸料带:
选用浇铸料,在轴向设膨胀缝,每隔1.5m设一道3mm膨胀缝.
(2)下侧过渡带:
本带基本上选用尖晶石砖,每环砖要设2mm膨胀缝,约相当于砖长的1%.轴向缝中不需要额外的膨胀缝.
(3)烧成带:
用直接结合镁铬砖、尖晶石砖,每环砖2mm膨胀接缝,相当于砖长的1%,轴向缝中不需要额外的膨胀缝.
(4)上侧过渡带:
建议用尖晶石砖,每环砖2mm膨胀接缝相当于砖长的1%,轴向缝中不需要额外的膨胀缝.
(5)安全带:
总是采用高铝砖或富铝砖,不需要另设膨胀缝.
(6)进料带:
采用轻质砖或粘土砖,不设膨胀缝.
(7)砖圈锁缝:
窑内各个砖圈的正确锁缝极为重要,请注意以下几点:
〈1〉只能用原状砖来锁砖圈,不得再加工砖.
〈2〉如果用几块砖来锁缝时,锁缝砖不得相互连用.
〈3〉在锁缝带内要保证砖的水平缝与窑轴的平行.
〈4〉锁缝金属板的厚度不大于2mm.
〈5〉每条缝只能用一块锁砖钢板,同一块砖两侧不能都使用钢板.
〈6〉如果用几块钢板来锁砖,应把它们均匀地分布在整个锁砖区内.
4.砌筑施工方法
目前我们常用的砌筑施工方法有支撑法和移动平台拱架法两种
(1)直径4米的窑型可以采用顶杠支撑法进行砌筑,也可以采用移动平台拱架法进行砌筑.
(2)直径4.8米的窑型必须采用移动平台拱架法进行砌筑.
新型干法窑常见工艺故障原因分析及应对措施
一、窑内形成厚结皮或后结圈
(一)现象:
1.窑尾负压升高.当窑皮长厚或形成后结圈时,窑内通风断面减小,风速高,阻力大,致使窑尾负压升高.
2.窑内通风不畅,窑前返正压,窑前煤加不进去.由于火焰后部结圈,通风断面缩小,影响窑内通风,窑前成正压状态,因窑内通风不畅不能满足正常用煤量所需要的氧气,迫使窑前减煤(不减煤,就会造成煤粉不完全燃烧,温度更低).
3.回转窑电流高.当窑皮长厚或后结圈时,一方面窑本体加重;另一方面,圈后的物料填充率增大以上两个原因导致回转窑的电流升高.
4.窑尾温度降低.因火焰伸不进去,煤加不进去,势必导致尾温降低.
5.出窑熟料减少.因有一部分物料粘附在窑皮上,一部分滞留在圈后,与正常生产的入窑生料量和出窑熟料量不成正比..
(二)原因:
1.生料的液相成分高.熟料矿物中要有一定的液相成分,如Al2O3、Fe2O3、硫、碱、以及一些微量元素.当液相量过高时,一方面共熔点温度降低,液相早出现;另一方面液相量大,液相粘度增大(尤其是Al2O3高时),就会使窑皮加厚加长,若不及时处理就会形成后结圈.
2.煤质差,煤灰分高.煤质差,一方面煤粉燃烧速度慢,火焰长.导致窑皮长;另一方面,煤灰分高,有害的液相成分高,造成物料的粘结,窑皮加厚.
3.煤粉不完全燃烧.窑前的煤粉必须完全燃烧,若出现不完全燃烧现象,窑内就会出现还原气氛,还原气氛会使三价铁还原二价铁,液相粘度增大,窑皮加厚.
4.喷煤管的火焰长而不集中.火焰长,窑皮就长.窑皮过长就为结圈奠定了基础;一旦生料成分发生变化或操作不当,就会形成后结圈.
(三)应对措施:
一旦如前述异常现象出现时,我们就可以判断有形成长厚窑皮或后结圈的可能,有针对性的采取相应的措施,就会转危为安.具体措施如下:
1、调整生料成分.根据化验室提供的生、熟料全分析结果,若液相成分或有害成分高,应通知化验室及时调整生料指标,尤其是要提高硅酸率的指标.
2、若煤质差,可根据情况采取以下两个措施:
A、更换质量好的煤;B、调整三通道喷煤管的火焰.加大内风的比例,加强风煤混合,使煤粉快速燃烧,缩短火焰.
3、保证煤粉完全燃烧.当形成长厚窑皮或后结圈时,窑内通风不良.此时,应减料,加大排风,保证煤粉完全燃烧所需要的空气.若煤粉不完全燃烧,会加剧结圈,其结果是,导致停窑,人工处理结圈.
4、冷热交替处理.当已确认窑内形成结圈时,可采用冷热交替法进行处理,具体做法是:
先将火点后移(喷煤管向窑内推进,加大排风,在保证煤粉完全燃烧的情况下尽量加大煤量),减少入窑生料量,连续烧3—4小时.然后将火点前移,连续烧3—4小时.此种办法交替进行.此种方法采用了热胀冷缩的原理,若结圈不很严重时,可使结圈自动垮掉.
二、窑尾缩口结皮及烟室斜坡积料
(一)现象:
1、分解炉压升高.不管是窑尾缩口结皮还是烟室斜坡积料,均使通风断面缩小,阻力增大,致使分解炉负压升高.
2、窑尾出现正压.因缩口结皮或斜坡积料影响通风,使窑内形成正压.
3、窑前火焰发憋,煤量加不进去.由于窑尾阻力大,窑内通风不畅,致使火焰发憋.通风不畅,供煤粉燃烧的空气不足,迫使减少煤量.
(二)原因:
1、生料中挥发性成分高(如硫、碱、氯离子等).当硫、碱、氯成分高时,就会在窑预热分解系统形成碱循环、硫循环、氯循环(当温度高时成气态,当温度低时成固态).在窑尾缩口或烟室富集并粘结生料形成结皮.
2、窑尾温度高.C3A、C4AF形成液相的温度为1100—1200℃,当窑尾温度超过1100℃时,将有大量的液相出现,导致缩口结皮、斜坡积料.这就是为什么窑尾温度控制在1050℃左右的道理.
3、煤质差.低质煤不易燃烧,容易产生还原气氛和二次燃烧,导致粘结结皮.
(三)应对措施:
1、选择挥发性成份低的原料.如生料中,R2O∠1%,Clˉ∠0.02%,S∠2%,硫碱比∠1
2、控制好窑尾温度.窑尾温度最佳控制温度为1050℃,严禁超过1100℃.
3、选用较好发热量的燃料.一般要求:
热值不低于5500Kcal∕Kg,灰份不超过30%.
三、预热器堵塞
(一)现象:
A、预热器锥部负压降低或出现零负压。
预热器的堵塞一般是从下料管或预热器的锥部开始的,不管是物理堵塞还是化学堵塞,均会使锥部负压管阻力增大,负压值降低;当负压管完全堵塞时,阻力无穷大,负压值为零。
B、锁风阀不闪动。
正常情况下,预热器的锁风阀在料流的冲击下有规律的闪动。
当出现不闪动时,说明下料管内料流停止,预热器堵塞。
C、下一级预热器(或分解炉)温度升高。
如四级预热器发生堵塞,就会造成分解炉内因断料而温度快速升高。
五级堵塞,窑尾温度升高。
(二)原因
预热器的堵塞分为物理堵塞和化学堵塞。
1、物理堵塞
A、预热器内部的耐火材料垮落,将下料口堵死。
B、预热器内筒因氧化磨损或安装不牢而坠落,将下料口堵死。
C、锁风阀因轴窜或轴抱死不能活动而积料。
D、检修预热器时因下料管内杂物未清理干净而积料。
2、化学堵塞
A、温度过高。
温度高,液相出现早,物料发粘,形成结皮堵塞。
如分解炉内煤粉不完全燃烧,部分煤粉跑到五级预热器内燃烧,就会出现温度倒挂现象(五级温度高于分解炉温度),分解炉煤粉不完全燃烧是造成五级预热器化学堵塞的主要原因。
B、原、燃料中挥发性成分过高。
当挥发性成分高时,就会在预热分解系统造成碱循环、硫循环、氯循环,在预热器锥部富集粘结生料粉造成结皮堵塞。
四、篦冷机堆“雪人”
所谓篦冷机堆“雪人”,是指篦冷机高温段的出窑熟料粘结在一起,并不断堆积,形成象“雪人”状的高温熟料堆。
若不及时发现处理,将会导致停窑,人工进篦冷机处理。
(一)现象
1、高温充气篦板的高压风机压力升高。
2、熟料冷却效果差,风温降低,过剩风温升高。
3、大窑落料点的料层增厚。
(二)原因
1、熟料液相成分高。
如熟料中的C3A、C4AF液相矿物含量高时,一方面,熟料结粒粗,篦层上的熟料层布风不匀(大窑落料点熟料颗粒细,阻力大,透风少;边壁熟料颗粒大,阻力小,透风多),大窑落料点的熟料因透风少,不能快速冷却而粘结成堆;另一方面,液相矿物含量高时,熟料颗粒表面发粘,颗粒之间相互粘结。
2、窑前温度高。
回转窑窑前要有一定的冷却带,烧成的熟料经过冷却带得到适当的冷却,使熟料颗粒表面温度降低至1300℃以下.若窑前温度过高,出窑熟料颗粒表面温度降不下来,落到篦冷机的熟料就会粘结.
3、篦冷机高温端的高压风机风量少.高温端的熟料必须快速冷却.快速冷却的条件是必须有足够的冷却风量.若冷却风量不足,熟料不能得到快速冷却,就会相互粘结.
4、篦冷机一端篦床的篦速过低.篦冷机的篦速要与出窑熟料量成正比关系,其控制原则是保证适当的料层和一定的风压.当出窑熟料量大,一端篦速低时,高温端的料层加厚,料层阻力大,冷却风量少,熟料不能得到快速冷却,高温熟料就会相互粘结.
(三)应对措施
1、控制熟料的液相矿物的含量.对于预分解窑来说,由于碳酸盐的分解大部分(90%以上)在窑外进行,回转窑的烧成能力增强,其液相矿物含量可以适当提高.目前,预分解窑一般采用“两高一中”(高硅酸率、高铝氧率、中饱和比),采用高硅酸率的目的,一方面可提高硅酸盐矿物的含量,提高熟料的强度;另一方面,降低液相矿物,使熟料颗粒细小均齐,有利于熟料的快速冷却.
2、控制火焰的形状和温度.熟料的烧成要有合理的火焰的形状和温度,若火焰短粗,就会形成短焰急烧,此时的火焰、窑皮、出窑熟料温度都高.解决的措施是:
加大排风,拉长火焰,适当增加三通道煤管的外风.
3、适当加大篦冷机高温端的冷却风量.一般情况下,篦冷机的操作应尽量开大高温端的高压风机,以使出窑高温熟料快速冷却,既可避免篦冷机堆“雪人”的发生,又可提高熟料强度和易磨性,还可提高二次风温度.
4、控制合理的篦床篦速.所谓合理的篦速是指篦床的运行速度要与出窑的熟料量、熟料的温度、熟料的结粒情况相匹配.当出窑的熟料量增多,熟料的结粒不均齐,这时,应适当加快一段篦床的篦速,其他篦床的篦速也要相应加快,反之,应适当减慢篦速.
预分解窑塌料问题的分析及解决措施
塌料是预分解窑生产中经常遇到的一种不正常现象,其表现特征是在极短的时间内,有一段料失控下落,从分解炉底部卸出,下落物料经窑尾进入窑内,使窑内未分解生料增多,窑头烧结困难,熟料质量差,塌料严重时,生料可直冲窑头,造成窑头返火,甚至从窑头罩或冷却机冲出高温红料.此外,由于塌料引起风、煤、料不平衡,热工制度破坏,影响正常生产的进行.
造成系统塌料主要有三个方面的原因,预分解系统结构问题、生产操作控制问题和喂煤系统的问题,据此文本从以上三个方面来讨论预分解窑系统塌料的原因及防治措施.
一、预分解系统结构问题及其改进
(一)合理风速的问题
我们认为预分解系统各部分风速不能太低,对于发生塌料的预分解系统,应验算其
不同产量时的各部风速,若局部风速太低,则可根据情况对其进行处理,或改造设备,或增加局部内衬厚度以缩小通风面积,使其达到生产要求.预分解窑生产时,燃烧空气分别从三次风管和窑通过.为了保证窑,炉燃料的正常燃烧,又保证窑头良好的火焰形状和分解炉内较好的携带物料,入窑二次风和入炉三次风必须按合适比例分配,并使各部分风速达到合理取值,特别是分解炉喷腾口和炉内气体要达到一定的流速,才能有效携带物料,避免分解炉塌料.生产中主要是通过调节三次风管阀门或窑尾缩口规格不合适或调节范围过小,生产中不能按操作要求调节,就会使两股风不匹配,影响窑炉正常煅烧,也影响分解炉内气体带料能力,若喂料量不当时,很容易引起分解炉内物料塌落.为避免分解炉塌料,我们建议合理风速值可见下表(单位:
m/s)
旋风筒
连接风管
喷腾型分解炉
DD分解炉
分解炉下缩口
4-6
15-20
5.5-7
8-10
>35.0
(二)各级旋风筒散料装置结构和安装位置问题
理论上讲,撒料板的作用一是消除物料下冲动能并抛散物料;二是深入风管内阻挡气流,使撒料板下面的上升气流受阻挡后,挤向撒料板周围绕行,形成一股流速较高的绕行气流,有利于冲散和托升物料.撒料装置的形式、大小、倾角的度数和撒料板深入风管的长度,撒料板距旋风筒进口距离等几个参数是影响撒料效果的关键因素.若撒料板设计太小或合适,则不能有效分散成股物料,当风管风速稍低时,就有可能托不住下冲成股料,使物料直接掉入下级旋风筒,此过程物料积聚,料量增大,又有较大的下冲力从分解炉卸入窑内,成为塌料.
对因撒料装置结构或安装位置不当导致的系统塌料,一般可增加撒料板长度,对于撒料板安装位置的调整,因受现场限制比较困难.可以通过适当加长下级旋风筒内筒来解决.
(三)旋风筒下料管及其翻板阀的问题
旋风筒下料管和翻板阀如果出现问题也会导致塌料.首先考虑下料管,设计直径过小或下料管因结皮造成管径缩小会造成阻塞,,但料管中的填充率也不能太低,应使下料管配上合适的翻版阀能起好的锁风作用.翻板阀的阀板开口过大,阀体位置不当,阀板翻动不灵活或烧坏等,其锁风效果就很差.旋风筒间就会产生内漏风现象,使旋风筒分离效率下降,一部分物料随气流进入上一级旋风筒,一部分在旋风筒内形成循环积聚,积到一定量时,成股卸出旋风筒到下面各级旋风筒和风管内不能很好分散,导致系统塌料.另外,内漏风使窑和分解炉高温气体直接进入上级旋风筒,使其易结皮堵塞也会产生塌料.其次下料管的布置,若拐弯过多或角度太小,则生产中容易结皮、下料不畅、不稳,产生脉动,成股下料,也会产生料短路而引起塌料.
从解决塌料问题出发,我们要考虑旋风筒下料管的走向布置、空间角度、管径及锁风阀等因素.各管段空间角度尽可能大于55度,锁风阀一定要严密锁风,翻动灵活.配重不要太轻,尽量不设在下料管的小角度段上.这样,尽可能减少系统内漏风,也是解决塌料的一个重要途径.
二、生产操作控制问题及其改进
烧成系统生产操作不正确,也会引起窑系统的塌料,常见的问题有:
(一)长时间低产量运行
在窑系统点火升温挂窑皮阶段.窑系统要低产量运行,在某些特殊情况下(如烧成系统附机有小故障;煤料临时供应不上;熟料库满等.)也习惯低产量运行,此时系统用煤、加料量均较正常情况低,系统用风量也必须降低,使旋风筒及连接风管各处的风速降低,塌料情况较易发生.为了避免上述情况的发生可适当加大系统过剩空气系数,尽管生产不经济合理,但尚可维持生产.因此预分解窑的生产操作要尽量避免低产量运行,在点火升温或窑况不好时,操作人员应对系统进行全面分析,作出正确判断,尽快跨过低产量阶段,达到正常生产.
(二)系统结皮积料的影响
窑系统在运行一段时间后,某些部位必然要产生结皮或积料,窑尾烟室和分解炉缩口就是非常关键的部位,窑尾烟室斜坡有积料,回转窑内通风减小,缩口处的喷腾风速就会降低,产生塌料;缩口结皮虽风速有所提高,但通过风量大大减少会造成分解炉内风速降低,带料能力降低,物料积聚到一定程度,产生塌料;预热器连接管道存在积料,则直接影响到整个系统的通风,造成料、风、煤不匹配,也会产生塌料,针对这一类问题,操作和巡检人员要密切配合,及时处理.对于不方便处理的结皮积料,要制定出改造措施,尽快整改.
三、窑系统喂煤波动的影响
喂煤系统的运转效果,直接影响到系统的运转质量.煤风搭配不合理,送煤管道设计存在问题,将会使煤粉输送过程中产生脉冲,喷入窑炉的煤粉瞬间发生较大波动,风速随之变化,形成较频繁的塌料.可以通过检查喂煤设备,理顺送煤管道予以解决.
水泥磨系统中控操作与异常情况判断
一些水泥粉磨系统带辊压机、V型选粉机的挤压-打散联合粉磨系统,本文从中控角度探讨一下该系统的操作.
一、工艺流程
(一)料路
配好的原料经过水泥配料皮带,进入料饼提升机经V型选粉机,粗料进入称重仓,称重仓的料经过辊压机的挤压又回到了料饼提升机,从而完成了一次物料循环,如此反复(习惯称之为:
辊压机的物料循环)
经过V型选粉机分离出的细粉,由细粉分离收集下来,经过斜槽将物料喂入水泥磨,物料经过研磨,由出磨提升机提升起来,经过斜槽,进入O-Sepa选粉机分离出的细粉-成品,进入高浓度收尘器,水泥成品由高浓度收尘器收集下来,经过斜槽、水泥入库提升机,提升起来进入水泥库.
(二)风(含尘气流)路
空气从V型选粉机进口补风阀进入V型选粉机内,含尘气流由其出口进入细粉分离器,再由细粉分离器出口进入循环风机,从循环风机出来的风分以下几路:
1、含尘气流经过循环风阀又回到了V型选粉机进口(称之为:
循环风);
2、含尘气流经过风阀进入放风袋收尘器,经过滤后的气流由放风风机排入大气(称之为:
放风),收集下来的料回到磨头;
3、含尘气流经过短路风阀进入V型选粉机侧部(称之为:
短路风);
4、在不“放风”的情况下,含尘气流经过风阀进入O-Sepa选粉机的二次风进口;
水泥磨内的废气经过出磨风管风阀,由O-Sepa选粉机的一次风进口进入其内部,然后进入高浓度袋收尘器,经过滤后的气流由主排风机排入大气.
二、几个主要调风阀的作用
这套工艺系统的特点之一是:
入磨物料的多少,主要是循环风量的多少来控制的;一般循环风量增大,喂料量增大;否则喂料量则减少.下面将几个调风阀或者变频器的作用例举如下:
1、循环风阀:
在其它风阀开度不变的情况下,循环风阀开度增大,循环风量增大;反之,循环风阀开度减小,循环风量减小;
2、短路风阀:
在其它风阀开度不变的情况下,短路风阀开度增大,循环风量减小;反之,短路风阀开度减小,循环风量增大;
3、放风风机:
在其它风阀开度不变的情况下,风机速度增加,循环风量减小;反之,风机风速减小循环风量增大;
三、V型选粉机的工作原理
含有料饼的物料,由顶部喂入,经过格板(V型选粉机内部由“V”字形格板构成)的过程中,在重力、风力的作用下,料饼被碰撞、打散,从而在设备的截面上形成“料幕”;“风”从进口到出口的过程中随着“V”字形格板而走了一条“V”字形路线,“风”在穿越“料幕”后,将细粉带走,大部分粗粉在“风”突然转向时,失去速度而落下,从卸料口排出.
四、中控操作应熟练掌握的知识(水泥磨系统)
(一)、主机设备的额定功率、额定电流
记住他们的目的是:
在中控操作的过程中,避免设备过负荷而“烧坏”电机,在发挥设备最大能力时,有自己的“心里底线”.
(二)、设备运行时的空载电流
记住它们的目的是:
在中控操作的过程中,判断设备内物料的多少.例如:
记住水泥入库提升机的空载电流,可以避免带料停机等.
(三)、正常生产时,设备的运行电流
记住他们的目的是:
在中控操作的过程中,判断设备负荷的多少;设备是否正常;系统是否正常.例如:
就料饼提升机而言在辊压机正常状态下,如果配料给定台时产量比正常高,则料提升机的电流应该比正常的“运行电流”高,否则就应立即分析原因;如果在正常喂料时,“运行电流”总是比正常时偏高,则可能是液力偶合器漏油(这是带偶合器类提升机电机电流“跑高”的常见现象之一。
)例如:
如果磨机实耗功率比正常“运行电流”有降低的趋势(实耗功率曲线拐头向下),则磨机有“饱磨”的趋势,应当引起注意。
(四)、提高硅酸盐水泥早期强度的措施
1、适当提高水泥熟料C3S和C2A含量;
2、控制混合材的掺加量和质量;
3、提高水泥细度;
4、适当提高石膏的掺入量,特别是在熟料C3S和混合材的AL2O3含量较高时,水泥细度较细的情况下,有利于形成钙矾石;
5、在熟料C3A含量和矿渣AL2O3含量高的矿渣水泥中,加入适量的石灰石代替矿渣,也可提高其早期强度,这是由于碳酸钙与水化铝酸钙形成水化碳铝酸钙;
6、采用减水剂或早强剂;
(五)、理解水泥磨系统“放风”的目的
1、维持辊压机、V型选粉机系统的风量平衡,更容易使称重仓的料位保持平衡;
2、系统补进空气放出废气,能在进厂物料水分较高或者熟料温度较高时,最大限度的降低入磨物料的水份和温度,从而维持较高的台时产量;
五、水泥磨操作异常情况判断
要根据中控数据和部分现场的电视画面快速、准确的对异常情况做出判断,这要基于操作中控人员对系统的工艺原理、设备的工作原理、设备本身的“健康”状况、进场的物料水分、粒度、品位等必须有全面的了解.
下面将水泥磨系统设备的常见异常情况和处理方法尽可能的列出,在处理问题时,根据自己掌握的情况,找几种最有可能的原因,然后一一排除.
(一)料饼提升机“运行电流”波动范围异常
原因有可能是:
1、液力偶合器漏油或者油量灌的不到位;(原因:
液力偶合器内油量不到位,输出的机械能就会减少,提升机若要提升同样重量的物料,就得多做功,提升机电流就会升高.)
2、辊压机物料通过量过大,提升机负荷增大;
3、“传动链条”或“牵引链条”有“爬链”趋势(原因:
1、链条“销子外窜”或者链板脱落;2、安装不到位或设备在运行过程中链轮移位,这种原因造成的电流波动,往往具有周期性和突然性,有时候电流的波动幅度较正常不大,中控员对正常的“运行电流”波动范围非常清楚.)
4、牵引链条“掉道”或者斗子刮机壳;(原因:
设备运行过程中,牵引链条较长或者配重没起到作用,这种原因造成的电流波动幅度较正常大;现场异常响声较大.)
5、提升机底部有较多密实的物料,回程的牵引链条在下链轮拐点部位“掏取”物料时,摩擦力较大,电流波动幅度较正常大,有时斗子会严重变形.
6、在正常喂料过程中,提升机电流持续下降(原因是:
配料秤不下料或者配料库不下料,常常伴随着给定台时反馈小于给定值;有时某台秤的传动链条断开后,配料秤停止运转,但电机仍旧运转,这时你单从反馈上看不出异常,因为配料秤虽然不转了,但是物料始终压在配料秤上,所以反馈始终不变.)
需要注意的是:
水泥磨房内的提升机逆止器均为“棘轮式”的,在检修或安装时,检修人员不要忘记使“卡块”复位,否则提升机带料突然停机会造成“事故”.
(二)称重仓的料位变化因素:
1、其它条件不变,单纯台时给定增大,称重