热处理讲课.docx
《热处理讲课.docx》由会员分享,可在线阅读,更多相关《热处理讲课.docx(56页珍藏版)》请在冰豆网上搜索。
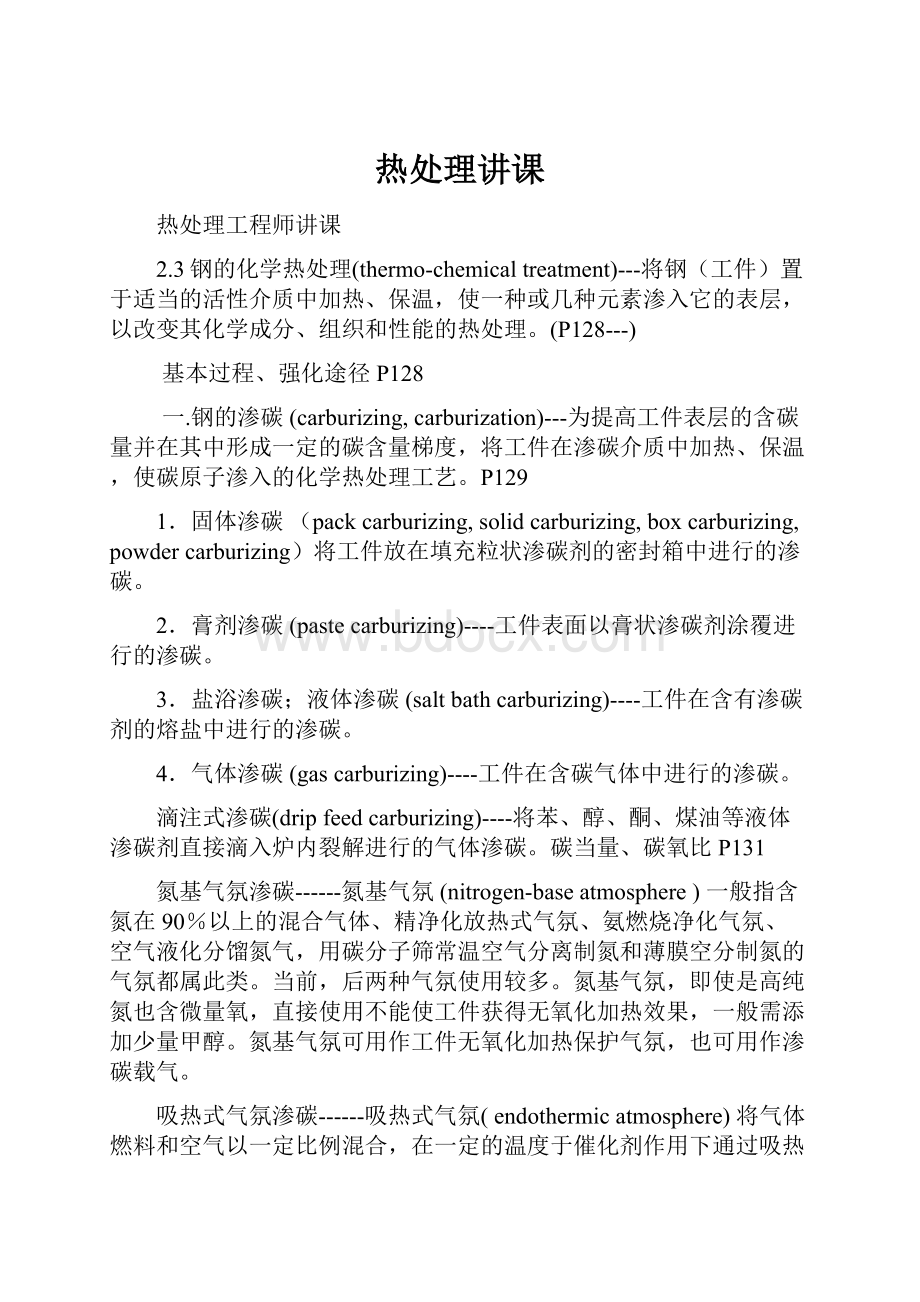
热处理讲课
热处理工程师讲课
2.3钢的化学热处理(thermo-chemicaltreatment)---将钢(工件)置于适当的活性介质中加热、保温,使一种或几种元素渗入它的表层,以改变其化学成分、组织和性能的热处理。
(P128---)
基本过程、强化途径P128
一.钢的渗碳(carburizing,carburization)---为提高工件表层的含碳量并在其中形成一定的碳含量梯度,将工件在渗碳介质中加热、保温,使碳原子渗入的化学热处理工艺。
P129
1.固体渗碳(packcarburizing,solidcarburizing,boxcarburizing,powdercarburizing)将工件放在填充粒状渗碳剂的密封箱中进行的渗碳。
2.膏剂渗碳(pastecarburizing)----工件表面以膏状渗碳剂涂覆进行的渗碳。
3.盐浴渗碳;液体渗碳(saltbathcarburizing)----工件在含有渗碳剂的熔盐中进行的渗碳。
4.气体渗碳(gascarburizing)----工件在含碳气体中进行的渗碳。
滴注式渗碳(dripfeedcarburizing)----将苯、醇、酮、煤油等液体渗碳剂直接滴入炉内裂解进行的气体渗碳。
碳当量、碳氧比P131
氮基气氛渗碳------氮基气氛(nitrogen-baseatmosphere)一般指含氮在90%以上的混合气体、精净化放热式气氛、氨燃烧净化气氛、空气液化分馏氮气,用碳分子筛常温空气分离制氮和薄膜空分制氮的气氛都属此类。
当前,后两种气氛使用较多。
氮基气氛,即使是高纯氮也含微量氧,直接使用不能使工件获得无氧化加热效果,一般需添加少量甲醇。
氮基气氛可用作工件无氧化加热保护气氛,也可用作渗碳载气。
吸热式气氛渗碳------吸热式气氛(endothermicatmosphere)将气体燃料和空气以一定比例混合,在一定的温度于催化剂作用下通过吸热反应裂解生成的气氛。
可燃,易爆,具有还原性。
一般用作工件的无脱碳加热介质或渗碳时的载气。
5.离子渗碳(plasmacarburizing,ioncarburizing,glowdischargecarburizing)在低于1×105Pa(通常是10~10-1Pa)渗碳气氛中,利用工件(阴件)和阳极之间产生的辉光放电进行的渗碳。
真空渗碳(partialpressurecarburizing,vacuumcarburizing,lowpressurecarburizing)在低于1×105Pa(通常是10~10-1Pa)的条件下于渗碳气氛中进行的渗碳。
6渗碳名词解释
渗碳层(carburizedcase,carburizedzone)渗碳工件含碳量高于原材料的表层。
碳含量的分布(carbonprofile)在沿渗碳工件与表面垂直方向上碳在渗层中的分布。
渗碳层深度(carburizedcasedepth,carburizeddepth)由渗碳工件表面向内至碳含量为规定值处(一般为0.4%C)的垂直距离。
渗碳淬火有效硬化层深度(carburizingandhardeningeffectivecasedepth)由渗碳淬火后的工件表面测定到规定硬度(550HV)处的垂直距离,以CHD表示。
测定硬度时所用的试验力为9.807N。
碳活度(carbonactivity)与渗碳有关的碳活度通常是指碳在奥氏体中的活度。
它与奥氏体中碳的浓度成正比,比值称为活度系数。
这个活度系数又是温度、奥氏体中溶入的合金元素品种及各自的浓度以及碳的浓度的函数。
其物理意义时碳在奥氏体中的有效浓度。
碳可用率(carbonavailability)在气氛碳势从1%降至0.9%时,1立方米(标准状态下)气体可传递到工件表面的碳量(以g/m3表示)。
碳传递系数(carbonmasstransfercoefficient,carbontransfercoefficient,carbontranstervalue)单位时间(s)内气氛传递到工件表面单位面积的碳量(碳通量)与气氛碳势和工件表面含碳量(碳钢)之间的差值之比。
工艺学P418(β)
7.渗碳工艺:
温度、时间、碳势工艺学P428
8.碳势控制:
工艺学410、415
9.渗碳后热处理-------工件渗碳后进行合理的热处理(见表)来获得高的力学性能和应用性能。
相应的渗碳层显微组织为细粒状弥散均匀分布碳化物+隐针状马氏体,心部显微组织不出现块状铁素体。
工艺学P436
表渗碳后的热处理方式
热处理方式
淬火回火方式
适用情况
渗碳后随炉冷或出炉预冷直接淬火方式
1)冷至(760~850)℃直接淬火+(160~200)℃低温回
火2~3h
20CrMnTi、20MnVB、25MnTiBRe
等本质细晶粒钢
2)预冷后在(120~160)℃热油中分级停留一段时间,空冷+(180~200)℃低温回火2~3h
形状复杂,厚薄相差大的小零件适用
3)直接淬火后进行(-60~-80)℃,1~2h冷处理+(180~200)℃低温回火2~3h
20Cr2Ni4、20CrNiMo、12SiMn2WV
大截面重负荷零件减少残留奥氏体
4)直接淬火后在>500℃温度多次回火,使残留奥氏体中析出特殊细小碳化物发生二次硬化,使在(350~370)℃工作时硬度达58HRC
高速大负荷高温下工作零件(>350℃高速齿轮),15Cr3NiWMo2V,1030℃渗碳淬火在530℃回火三次
5)冷至(780~810)℃直接淬火+(160~200)℃低温回火2~3h+(-60~-80)℃冷处理1~2h+(160~180)℃低温回火2~3h
大截面、重负荷高合金渗碳件,
如18Cr2Ni4W、20CrNiMoA等
渗碳后空冷或缓冷坑中冷至300℃空冷+重新一次淬火+低温回火方式
1)重新加热至(770~830)℃后淬火+(160~200)℃低温回火2~3h
不宜直接淬火零件或渗碳后需机加工零件
2)空冷后+(640~660)℃×(2~3)h回火2~3次(空冷)+(780~820)℃加热淬火+(180~200)℃回火2~3h
12CrNi3、20CrNiMo、18Cr2Ni4WA渗层中残留奥氏体减少,析出合金碳化物的大截面高负荷工件
3)空冷后+650℃高温回火+790℃加热淬火+(-120)℃冷处理+低温回火160℃+时效120℃
要求极精密高合金钢,高速柴油机喷油器壳体,18Cr2Ni4WA、20Cr2Ni4
4)渗碳后+感应加热淬火+低温回火
表面受高接触应力、磨损及抗弯、抗扭,但对心部要求不高的工件
5)渗碳后空冷+一次淬火加热后在心部Ms点以下和渗层Ms点以上等温分级淬火+低温回火
18Cr2Ni4WA马氏体分级淬火
渗碳空冷+二次淬火+低温回火方式
1)第一次加热至心部Ac3以上,碳钢(880~920)℃、合金钢(860~900)℃淬火细化心部组织;第二次加热至渗层Ac1以上(760~780)℃淬火+(160~200)℃低温回火1.5~2h
10、20、15Cr、20Cr钢,表面高硬度心部有高冲击韧度的零件;高强度高合金渗碳钢12CrNi3、12Cr2Ni4、20CrNi4、18Cr2Ni4WA等
2)渗碳后+(850~870)℃淬火+(640~670)℃高温回火+(780~830)℃二次淬火+(160~180)℃低温回火1.5~2h
大截面、高负荷高合金渗碳钢
18Cr2Ni4WA、20CrNiMo等
3)渗碳后直接淬火+(350~450)℃回火+快速加热至较低淬火温度淬油+(170~230)℃低温回火
使工件耐磨性、韧度和接触疲劳强度提高
10.渗碳缺陷P137
怎样进行气体渗碳操作?
操作注意事项是什么?
(问答5.8)
滴注式渗碳气氛为何出现失控?
如何防止?
(500问374)
二.钢的渗氮(氮化nitriding,nitrogencasehardening)---在一定温度下于一定介质中使氮原子渗入工件表层的化学热处理工艺。
P139
1.液体渗氮(盐浴渗氮liquidnitriding)在含渗氮剂的熔盐中进行的渗氮。
2.气体渗氮(gasnitriding)在可提供活性氮原子的气体中进行的渗氮。
可控渗氮抗蚀渗氮
一段渗氮(singlestagenitriding)在一定温度和一定氮势下进行的渗氮。
多段渗氮(multiplestagenitriding)在两个或两个以上的温度和多种氮势条件下分别进行渗氮。
3.离子渗氮(plasmanitriding,ionnitriding,glowdischargenitriding)在低于1×105Pa(通常是10-1~10-3Pa)的渗氮气氛中,利用工件(阴极)和阳极之间产生的辉光放电进行的渗氮。
4.渗氮名词解释
退氮(denitriding)为使渗氮件表层去处过多的氮而进行的工艺过程。
氮化物(nitride)氮与金属元素形成的化合物。
碳钢渗氮时常见的氮化物有-Fe4N,-Fe(2-3)N,-Fe2N等。
氨分解率(ammoniadissociationrate)气体渗氮时,通入炉中的氨分解为氢和活性氮原子的程度,一般以百分比值来表示。
在一定渗氮温度下,氨分解率取决于供氨量。
供氨愈多,分解率愈低,工件表面氮含量愈高。
供氨量固定时,温度愈高,分解率愈高。
氨分解率是渗氮的重要工艺参数。
氮势(nitrogenpotential)表征渗氮气氛在一定温度下向工件提供活性氮原子能力的参数,通常通过调整氨分解率进行监控,氨流量愈大,氨分解率愈低,气氛氮势愈高。
工艺学P471
渗氮层深度(nitridedcasedepth)渗氮层包括化合物层(白亮层)和扩散层,其深度从工件表面测至与基体组织有明显分界处或规定的界限硬度值处的垂直距离,以DN表示。
5.渗氮工艺:
温度、时间、氮势(氨分解率)工艺学489
6.一些常见的渗氮件缺陷及对策P144简述见表
表一些常见的渗氮件缺陷及对策
缺陷类型
产生原因
对策
工件表面
氧化色
冷却时供氨不足,管内出现负压,渗氮罐漏气,压力不正常,出炉温度过高。
干燥剂失效,氨中含水量过高,管道中存在积水。
适当增加氨流量,保证罐内正压,保证罐内压力正常。
工件炉冷至200ºC以下出炉。
表面腐蚀
氯化铵(或四氯化碳)加入量过多,挥发太快
除不锈钢和耐热钢外,尽量不加氯化铵,加入的氯化铵应与硅砂混合,以降低挥发速度。
渗氮层硬度低
温度过高;分段渗氮时第一段温度太高;氨分解率过高或中断供氨;炉子的炉盖等处密封不良而漏气;渗氮罐使用过久;工件表面油污未清除。
校验仪表,调整炉温;降低第一段温度;调整并稳定氨分解率;保证渗氮罐密封性能;新渗氮罐应经过预渗,长久使用的渗氮罐(包括夹具)均应进行退氮处理,以保证分解率正常;渗氮前严格进行除油、除锈处理。
渗氮件表面有亮点、软点、硬度(或渗层)不均匀
工件表面油污或氧化皮未清洗(理)干净;材料组织不均匀;装炉量太多或工件吊挂不当;炉温、炉气不均匀;离子渗氮(零件狭缝、小孔)屏蔽不当;零件上有锡、铜、锌、水玻璃等溅射到零件表面。
清洗去污,清除零件表面氧化皮;合理装炉;改进炉子设计,降低罐内温差,强化炉气循环;离子渗氮时,不允许零件屏蔽物上有非铁物质。
屏蔽狭缝小孔。
渗氮层脆性大
渗氮时工件表面脱碳,或者渗氮前(如38CrMoAlA)的调质处理时发生脱碳;氮势过高
提高渗氮罐密封性,降低氨中含水量,提高预先热处理质量;提高氨分解率,降低氮势;离子渗氮的可在冷却时,采用氢轰击退氮。
渗氮层网状或针状、脉状氮化物
渗氮温度过高,氮势过高,氨含水量大,原始组织粗大;表面脱碳层未加工掉;渗氮件表面粗糙,存在尖角、棱边;调质后的游离铁素体(体积分数)大于5%。
控制温度和氮势以及氨含水量;零件不允许有尖角,减少工件非平滑过渡;增加预先热处理后的加工余量,调质后应该是回火索氏体组织。
渗层太浅
温度(尤其是两段渗氮的第二段)偏低;保温时间短;氮势(氨分解率)不稳定;工件未进行调质预处理;新换渗氮罐或渗氮罐(或夹具)使用太久;装炉不当,气流循环不畅;离子渗氮真空度低。
适当提高温度。
校正仪表及热电偶;酌情延长时间;调整氮势(氨分解率);渗氮之前工件进行调质处理,以获得均匀致密的回火索氏体组织;新渗氮罐应预渗,长久使用的渗氮罐(或夹具)应进行退氮处理;合理装炉,调整工件之间的间隙;检查炉气漏气、供气情况。
渗氮件畸变
超差
1)机加工产生的应力较大,在渗氮加热时应力松弛;零件细长或形状复杂
2}渗氮层体积膨胀,渗层中含氮量高,渗氮层厚
3)工件自重的影响或装炉方式不当
4)气相氮势的影响
渗氮前预备热处理中,安排合理的去应力工序,对于尺寸精度要求比较高的零件要安排二次去应力处理。
第一次去应力预留1mm加工余量,第二次去应力预留0.15mm~0.3mm加工余量,也可视具体工件,经试验和生产经验而定。
去应力温度应高于渗氮温度而略低于调质处理的回火温度,保温时间一般以大于8小时为宜。
去应力处理后不允许进行校直(若校直必须重新进行去应力处理。
细长件去应力后最好使之处于垂直状态。
对于细长的轴类零件可加工“工艺孔”。
对单边开键槽的轴类零件,可在键槽对称的位置上开一个同样形状与尺寸的键槽,称为“工艺槽”。
选用合理的渗氮层深度,注意渗氮处理的升温操作,采用升温至略低于渗氮温度,保温适当时间后再缓升温至渗氮温度,使工件温度趋于均匀后再通氨气。
必要时改进渗氮炉结构,使气氛均匀。
必须合理装炉,装炉力求均匀;杆件吊挂平稳且与轴线平行,必要时设计专用夹具或吊具。
在渗氮温度和时间相同的情况下,气相氮势愈高,渗氮件畸变愈大,所以建议采用可控渗氮方法。
三.碳氮共渗、氮碳共渗
(一)碳氮共渗(carbonitriding)在奥氏体状态下同时将碳、氮渗入工件表层,并以渗碳为主的化学热处理工艺。
P144
1.液体碳氮共渗(cyaniding,liquidcyaniding)在一定温度下以含氰化物的熔盐为介质进行的碳氮共渗。
2.气体碳氮共渗(gascarbonitriding,drycyaniding)在含碳、氮的气体介质中进行的碳氮共渗。
常用的气体碳氮共渗介质
类别
介质组分(φ%)
说明
液体有机化合物+NH3
1)煤油+NH3(约占25~40)
2)甲醇+丙酮+NH3(约占25~30)
1)煤油+NH3应用最广泛
2)换气次数一般以2.5~5次为好
(大炉罐取小值,小炉罐取大值)
含氮有机化合物
1)丙酮+甲醇+尿素[(NH)2CO]
2)三乙醇胺+甲醇
3)三乙醇胺[(C2H4OH)3N]
4)甲醇+甲酰胺(HCONH2)
5)苯胺(C6H5NH2)
1)三乙醇胺在(200~300)℃形成沥青状物堵塞滴管,故在入炉处要加水冷却,但加甲醇可以防止堵塞
2)也可以用注射泵喷射入炉
3)为增加尿素流动性,可加热至(70~100)℃
气体渗碳剂+氨气
吸热式气氛(露点0℃~-5℃)+富化气(甲烷5%~10%或丙烷1%~3%或城市煤气10%)+氨气(1.5%~5%)
1)吸热式气氛的露点,根据碳势要求调整
2)煤气应去水脱硫
3)换气次数6~10次左右
(大炉罐取小值,小炉罐取大值)
3.离子碳氮共渗(glowdischargecarbonitriding,plasmacarbonitriding,ioncarbonitriding)在低于1×105Pa(通常是10~10-1Pa)的含碳、氮气体中,利用工件(阴极)和阳极之间的辉光放电进行的碳氮共渗。
4.碳氮共渗常见缺陷及防止P149
碳氮共渗常见缺陷有哪些?
如何防止?
(问答5.27)
(二)氮碳共渗(软氮化nitrocarburizing)工件表层同时渗入氮和碳,并以渗氮为主的化学热处理工艺。
在气体介质中进行的称气体氮碳共渗,在盐浴中进行的称液体氮碳共渗。
P150[液体氮碳共渗、固体氮碳共渗、气体(多种气氛)氮碳共渗、离子氮碳共渗]。
铁素体氮碳共渗:
工艺学P513(500-600℃)
奥氏体氮碳共渗:
工艺学P537(600-700℃)
氮碳共渗常见缺陷与对策
缺陷特征
产生原因
对策
渗层深度不够
1)温度低,保温时间短,介质浓度低或供气量少
2)渗件装炉重叠或与炉底、炉壁接触
按常规工艺,重新处理
渗层硬度不均匀
渗层厚度不均匀
1)渗件未清洗干净,装炉过多,进气、出气口位置不合理或堵塞,气氛温度不均匀
2)防渗层覆盖不均匀,或镀锡层淌流
1)渗件应清洗干净,合理装炉
2)改善气氛和温度均匀性
3)严格按工艺操作
渗层疏松
1)氨分解率低,渗剂加入量多
2)温度高、时间长
3)疏松的特征是表面附近出现空洞
1)调整工艺参数
2)留磨量大的渗件,可磨去疏
松层后使用
3)严重疏松报废
化合物层脆
氨气分解率低,氨气含水量过多
合理供气烘干或更换干燥剂
表面硬度低
1)温度过高,时间过长,造成表面疏松
2)时间短,氨气分解率偏低
3)渗剂供给不足
4)表面未清洗干净
1)去除表面污迹及锈斑
2)严格工艺纪律
表面呈蓝色或金黄色
1)炉膛密封性差,提罐冷却时供气不足
2)出炉温度过高,气氛含水量高
1)提罐冷却时适当加大供气量
2)烘干或更换干燥剂
工件表面颜色不均匀
1)工件表面有锈斑、氧化皮、严重油污
2)未清洗干净或局部有防渗剂覆盖
1)严格清洗工件,防渗涂覆部位要准确
2)不得沾污欲渗表面
3)镀锡层不得过厚
零件畸变量超差
1)处理前未消除应力
2)温度不均匀或温度过高
3)吊挂不合理
1)渗前去应力
2)炉温保持均匀
3)合理吊挂
4)对畸变要求严格件可用冷炉进料
硬氮化、软氮化的工艺特点有何不同?
(500问389)
四.其他化学热处理(渗其他非金属及渗金属类)
1.渗硼(boriding,boronizing)将硼渗入工件表层的化学热处理工艺,其中包括用粉末或颗粒状的渗硼介质进行的固体渗硼;|用熔融渗硼介质进行的液体渗硼;在电解的熔融渗硼介质中进行的电解渗硼;用气体渗硼介质进行的气体渗硼;在低于1×105Pa(通常是10-1~10-3Pa)的渗硼气体介质中,利用工件(阴极)和阳极之间产生的辉光放电进行的离子渗硼。
P153
2.渗硫(sulphurizing)将硫渗入工件表层的化学热处理工艺。
P154
3.渗金属(diffusionmetallizing,metalcementation)工件在含有被渗金属元素的渗剂中加热到适当温度并保温,使这些元素渗入表层的化学热处理工艺。
其中包括渗铝、渗锌、渗钛、渗钒、渗钨、渗锰、渗锑、渗铍和渗镍等。
渗铝P156、渗锌P158
2.4表面淬火(P163--)
一.感应加热淬火(感应淬火inductionhardening)利用感应电流通过工件所产生的热量,使工件表层、局部或整体加热并快速冷却的淬火。
1.原理、特点
感应加热主要基于电磁感应,表面效应和热传导这三项基本原理。
1).电磁感应
2)表面效应(集肤效应)
3)邻近效应
4)圆环效应
5)导磁体槽口效应
6)尖角效应
感应加热淬火的基本原理是什么?
交变电流具有哪些物理特性?
(问答4.1)2.技术要求P165
3.工艺参数P165
加热方式比功率频率
加热参数温度时间
冷却介质冷却方式冷却时间感应淬火的冷却方法及冷却介质应根据材质、工件形状和大小、采用的加热方式和淬硬层深度等因素综合考虑确定。
常用的冷却方法有喷冷、浸冷和自冷等;冷却介质有水、压缩空气、有机聚合物水溶液、油等。
形状简单的工件可采用喷水冷却。
低合金钢工件和形状复杂的碳钢工件可采用聚乙烯醇水溶液、聚烷撑乙二醇(PAG类如UconA、AQ251等)水溶液等进行喷射冷却。
形状复杂的合金钢工件可酌情采用油浸冷或适当浓度UconE等有机聚合物水溶液浸冷、喷射冷却。
回火.自热回火(自回火selftempering利用局部或表层淬硬工件内部的余热使淬硬部分回火)、炉中回火、感应回火。
P166
电参数调整
4.感应器设计P170
5.感应加热淬火中常见缺陷及预防措施P173
1)硬度不足
产生硬度不足的原因有两个:
加热不足或冷却不足。
(1)加热不足
比功率偏低、加热时间不足、感应器与工件表面间隙偏大,造成淬火温度偏低,组织中有较多未溶铁素体。
(2)冷却不足
加热结束后延时过长再冷却、喷液时间过短、喷射压力和喷射密度过低及淬火介质冷却速度低等均为造成冷却不足,组织中出现托氏体等非马氏体组织。
2)软点
喷水孔局部堵塞或分布过稀,导致工件局部区域冷却不足而出现软点。
3)软带
轴类零件连续加热淬火,有时会出现黑白相间螺旋型软带或沿工件与感应器的相对运动方向的某一区域出现直线黑带。
这些区域中存在未溶铁素体或托氏体组织。
原因如下:
(1)喷水角度偏小,加热区返水;
(2)工件旋转速度与工件或感应器移动速度不协调,工件旋转一圈感应器相对移动距离偏大;
(3)孔角度不一致,工件在感应器内偏心旋转。
(4)淬火裂纹
感应淬火裂纹的形成原因和预防措施如表所列。
表感应淬火裂纹的形成原因和预防措施
序号
淬火裂纹形成原因
控制措施
1
过热,如轴端裂纹、齿面弧形裂纹、齿顶延伸到齿面裂纹
降低比功率,减少加热时间,增大感应器与表面距离,同时加热时降低感应器高度
2
冷却过于激烈
采用冷速较缓慢的淬火介质,降低喷液供给量和喷液压力
3
钢材的碳质量分数较高,如ωC≥0.5%,开裂倾向急剧增加
精选碳量,使45钢中的碳控制在下限,采用冷速较缓慢的淬火介质
4
工件表面沟槽、油孔使感应电流集中
用铁屑堵塞
5
未及时回火
及时回火或采用
5)畸变
感应淬火多数表现为热应力型畸变。
为此应减少热量向工件内层中的传递。
为减少畸变,通常采用透入式加热,提高比功率,缩短加热时间;轴类零件采用旋转加热,齿轮内孔加防冷盖,减少内径缩小;薄壁齿轮淬火时对内孔喷水加速冷却以控制内径涨大。
6)硬化区分布不合理
淬硬区与非淬硬区的交接部位恰在工件的应力集中处,如花键轴的花键末端、齿轮的齿面与齿根的交接处、半轴法兰盘与轴的圆弧过渡区以及零件中的沟槽的交接面部位,由于这些地方存在残留拉应力峰,同时服役中又是结构上脆弱部位,容易产生断裂。
为此可采取一些措施,使硬化区离开应力集中的危险断面6mm~8mm或对截面过渡的圆角也实施淬火。
7)硬化层过厚
要求高硬度且经受冲击载荷易断裂的较小零件,如小模数齿轮,硬化层过厚是不利的。
为此选材上可用低淬透性钢或在工艺上采用较高的电源频率和比功率,适当减小感应器与工件的间隙,缩短加热时间,减少硬化层厚度。
8)表面灼伤
由于感应器与工件接触短路,使工件表面打弧留下烧伤痕迹和蚀坑。
注意工件内应力和预先处理状况(清除铁屑等)、淬火机床精度、感应器刚性以及与工件间的间隙。
二.火焰