冷硬树脂砂无箱造型工艺实践.docx
《冷硬树脂砂无箱造型工艺实践.docx》由会员分享,可在线阅读,更多相关《冷硬树脂砂无箱造型工艺实践.docx(33页珍藏版)》请在冰豆网上搜索。
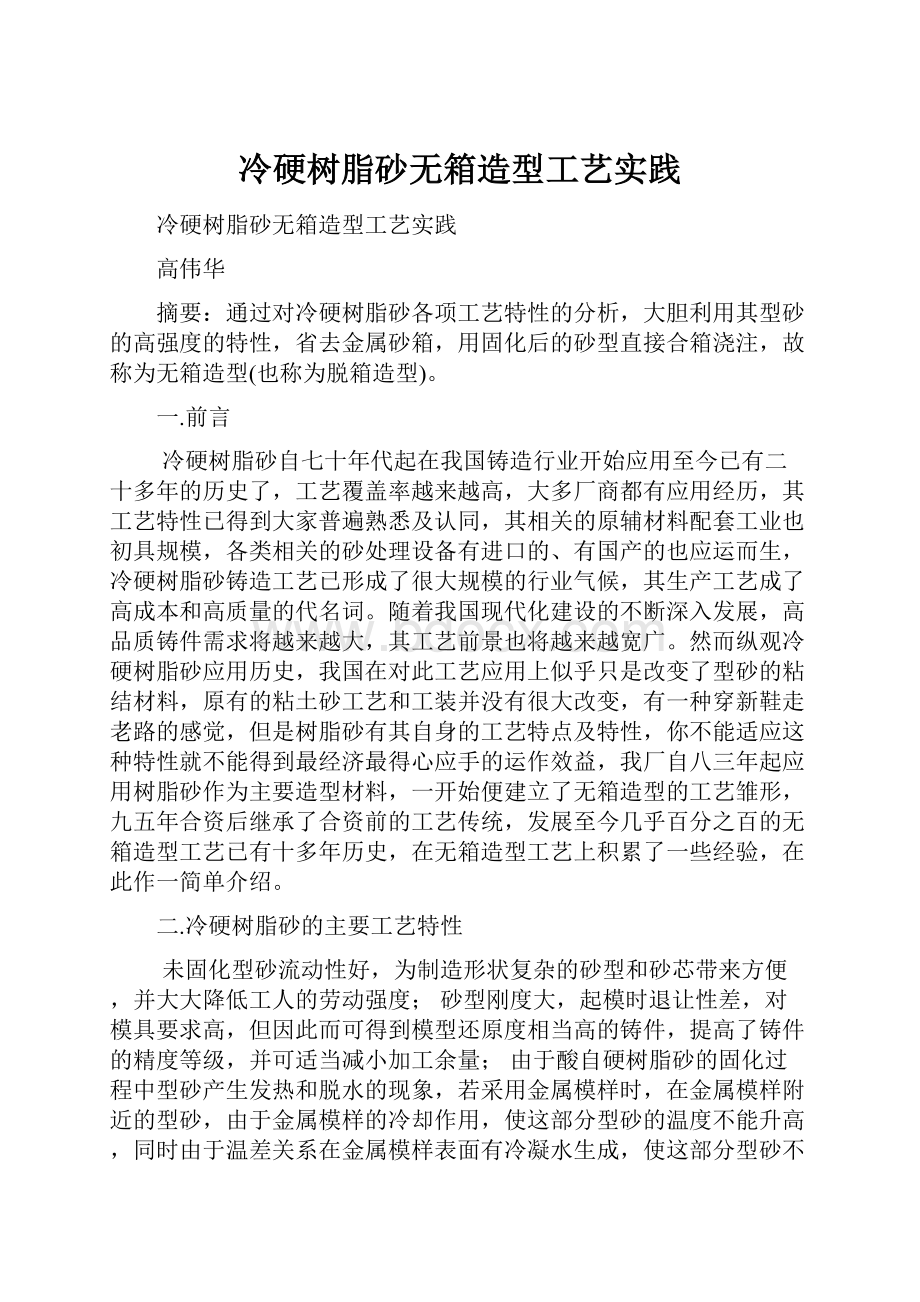
冷硬树脂砂无箱造型工艺实践
冷硬树脂砂无箱造型工艺实践
高伟华
摘要:
通过对冷硬树脂砂各项工艺特性的分析,大胆利用其型砂的高强度的特性,省去金属砂箱,用固化后的砂型直接合箱浇注,故称为无箱造型(也称为脱箱造型)。
一.前言
冷硬树脂砂自七十年代起在我国铸造行业开始应用至今已有二十多年的历史了,工艺覆盖率越来越高,大多厂商都有应用经历,其工艺特性已得到大家普遍熟悉及认同,其相关的原辅材料配套工业也初具规模,各类相关的砂处理设备有进口的、有国产的也应运而生,冷硬树脂砂铸造工艺已形成了很大规模的行业气候,其生产工艺成了高成本和高质量的代名词。
随着我国现代化建设的不断深入发展,高品质铸件需求将越来越大,其工艺前景也将越来越宽广。
然而纵观冷硬树脂砂应用历史,我国在对此工艺应用上似乎只是改变了型砂的粘结材料,原有的粘土砂工艺和工装并没有很大改变,有一种穿新鞋走老路的感觉,但是树脂砂有其自身的工艺特点及特性,你不能适应这种特性就不能得到最经济最得心应手的运作效益,我厂自八三年起应用树脂砂作为主要造型材料,一开始便建立了无箱造型的工艺雏形,九五年合资后继承了合资前的工艺传统,发展至今几乎百分之百的无箱造型工艺已有十多年历史,在无箱造型工艺上积累了一些经验,在此作一简单介绍。
二.冷硬树脂砂的主要工艺特性
未固化型砂流动性好,为制造形状复杂的砂型和砂芯带来方便,并大大降低工人的劳动强度; 砂型刚度大,起模时退让性差,对模具要求高,但因此而可得到模型还原度相当高的铸件,提高了铸件的精度等级,并可适当减小加工余量; 由于酸自硬树脂砂的固化过程中型砂产生发热和脱水的现象,若采用金属模样时,在金属模样附近的型砂,由于金属模样的冷却作用,使这部分型砂的温度不能升高,同时由于温差关系在金属模样表面有冷凝水生成,使这部分型砂不能有效地脱水,降低了砂型的表面强度;当采用木模样的时候,由于木模样的低导热性故不会阻碍型砂的升温,即不形成显著降低砂型表面的强度的条件,但由于升温和湿气的因素会使模型发生膨胀,故更进一步地增加了模型的起模难度; 固化后的型砂有很高的终强度,通常在普通高速搅笼式混砂机日常工况下1%的树脂加入量就可达到1Mpa左右的抗拉强度和1.5Mpa左右的抗弯强度,日常生产的正常搬动,不会引起砂型和砂芯断裂,普通形状和断面的坭芯可不用或少用芯骨; 虽然有很好的溃散性,但是当采用标准砂箱使吃砂量较大时,砂箱周围的型砂不能有效溃散,仍旧保持常温强度,给清砂带来很大的困难,手工清砂不容易,机械清砂就如同拆设备; 冷硬树脂砂造型方式属于流态砂造型,整个造型过程中没有很大强度的紧实过程,因而整体砂密度低于粘土砂等必须经过紧实工序的其它砂种,所以透气性较好; 型砂含水量较低,吸湿倾向也不大,允许存放一定的时间而不影响使用; 型砂成本较高。
按树脂加入量为1%,固化剂加入量为树脂的40%计,根据97年底的市场价格树脂为11900元/吨,固化剂为3080元/吨,每吨型砂在树脂和固化剂上的费用即达131.32元,按泵用铸件4.5的砂铁比,每吨铸件在树脂和固化剂上的费用即达590.94元。
从以上叙述可以看出,冷硬树脂砂是一种优秀的造型、制芯工艺,它优化了多项型砂参数,是制造高精度铸件的优选材料,但是由于它的高成本和延时硬化特性限制了它的应用范围,它可能永远不会取代粘土砂单件大批量简单铸件机械造型,因为虽然它们同样具有较高的铸造精度,但是由于延时硬化不能即时起模,提高不了产品的产量,也不具有铸造成本的优势。
然而它却是多品种小批量复杂铸件生产单位提高铸造产品等级的上选工艺,因为我们可以不增加工装甚至减少工装投入替代粘土砂等砂种,获得高等级铸件。
比如我们车间,有700多个产品零件需要常年生产,每月都有数十种零件需要生产,而每种零件的生产数量一般都不会超过10个,一般每个零件的分型面一到二个(二到三箱),最多5个(6箱),有相当多的零件需要阶梯分型或水平垂直混合分型,若要采用专用砂箱起码要有几百甚至上千种不同规格的砂箱,要是采用标准砂箱吃砂量实在太大,无箱造型给我们解决这些问题带来了最经济的方法。
三.冷硬树脂砂无箱造型的工艺方法
1.无型造型工艺的特定工艺装备及要求
(1).模型必须配备型板及砂框,一般模型应固定于型板上,浇注系统及冒口系统按工艺要求做出,型板上做定位销,砂框按型箱情况可做成固定斗形或活络直方形;
(2).在外模型箱造型时在型砂内安放钢筋作为型箱骨架,大于1200mm的型箱应以焊接钢管架作为骨架,同时伸出型箱部分的钢管可作为起吊翻型的吊搭子。
可以手工合型的型箱应在砂框上做出透空以形成搭手,型箱尺寸小于1200mm但必须机械起吊的型箱必须在箱角安放起吊环;
(3).型箱底面应放置带孔平板以保证型箱平整和为夹紧杆提供夹紧点,也可利用过去粘土砂造型用的带横档的砂箱作为底平板;
(4).用方钢管做各分段规格的夹紧杆。
一般一个型箱使用二个夹紧杆。
2.无箱造型的特定工艺参数
(1).侧面最小吃砂量50mm,底面最小吃砂量30mm;
(2).型箱最大尺寸1600mm×1600mm;
(3).一爿型箱最小厚度50mm,同时侧面长度与厚度(高度)之比最大不能超过8。
3.无箱造型工艺造型工部工艺流程(图略)。
4.无箱造型的工艺优点
(1).可随意根据铸件尺寸的大小确定型箱的尺寸及形状,克服了由于采用标准砂箱而产生的不必要的吃砂量,降低了砂铁比;
(2).节约了大量用来制造砂箱的金属材料;
(3).节约了大量堆放砂箱而占用的辅助场地;
(4).由于免去了砂箱,省去了制造专用砂箱的时间使新产品投产周期大大缩短;
(5).由于没有砂箱使型箱变原来的半封闭式为全开放式,进一步增强了型箱的透气性,基本上杜绝了侵入性气孔缺陷的发生;
(6).由于树脂砂高度的溃散性,浇注后铸件即完全与型砂分离,但型砂与砂箱不能分离,省去了砂箱便省去了落砂工序,因此砂处理设备变得简单,同时也使车间内噪音和粉尘污染大大减小;
(7).降低了型箱重量和合箱的劳动强度。
5.无箱造型的不足之处
(1).对混砂质量相对较高,混砂不均匀的型砂易形成裂纹及断裂,使型箱报废;
(2).不适用于大型铸件,尤其是壁厚或高度参数很大的铸件。
四.结论
我厂的生产实践证明,无箱造型的工艺方法是产品多品种小批量的铸造单位树脂砂铸造生产最上选的工艺方法。
至今,我们已经用无箱造型的工艺方法应用于铸钢和铸铜等各类铸造合金(ZG230-450,ZG270-500,ZG1Cr13,ZG2Cr13,ZG1Cr18Ni9Ti,ZCuZn16Si4,ZCuSn10Zn2等),最大型箱尺寸1600mm,最大铸件实体尺寸1200mm,最大金属压头(连冒口浇注高度)1500mm,最大浇注重量1000Kg,干型无箱率为百分之百。
生产实践证明,无箱造型能有效降低砂铁比,平均砂铁比从过去有箱造型的4.5降至目前的4.1左右,节约型砂成本近10%;省去了大量每年需要添置及更新砂箱的费用;极大地提高场地利用率,在不扩大厂房的条件下,腾出了原来用于堆放砂箱的场地,用以扩大生产,在十五年的生产中产量翻了三倍,取得了很大的综合效益。
铝铸件常见缺陷及分析
一 氧化夹渣
缺陷特征:
氧化夹渣多分布在铸件的上表面,在铸型不通气的转角部位。
断口多呈灰白色或黄色,经x光透视或在机械加工时发现,也可在碱洗、酸洗或阳极化时发现
产生原因:
1.炉料不清洁,回炉料使用量过多
2.浇注系统设计不良
3.合金液中的熔渣未清除干净
4.浇注操作不当,带入夹渣
5.精炼变质处理后静置时间不够
防止方法:
1.炉料应经过吹砂,回炉料的使用量适当降低
2.改进浇注系统设计,提高其挡渣能力
3.采用适当的熔剂去渣
4.浇注时应当平稳并应注意挡渣
5.精炼后浇注前合金液应静置一定时间
二 气孔 气泡
缺陷特征:
三铸件壁内气孔一般呈圆形或椭圆形,具有光滑的表面,一般是发亮的氧化皮,有时呈油黄色。
表面气孔、气泡可通过喷砂发现,内部气孔 气泡可通过X光透视或机械加工发现气孔 气泡在X光底片上呈黑色
产生原因:
1.浇注合金不平稳,卷入气体
2.型(芯)砂中混入有机杂质(如煤屑、草根 马粪等)
3.铸型和砂芯通气不良
4.冷铁表面有缩孔
5.浇注系统设计不良
防止方法 :
1.正确掌握浇注速度,避免卷入气体。
2.型(芯)砂中不得混入有机杂质以减少造型材料的发气量
3.改善(芯)砂的排气能力
4.正确选用及处理冷铁
5.改进浇注系统设计
三 缩松
缺陷特征:
铝铸件缩松一般产生在内浇道附近飞冒口根部厚大部位、壁的厚薄转接处和具有大平面的薄壁处。
在铸态时断口为灰色,浅黄色经热处理后为灰白浅黄或灰黑色在x光底片上呈云雾状严重的呈丝状缩松可通过X光、荧光低倍 断口等检查方法发现
产生原因:
1.冒口补缩作用差
2.炉料含气量太多
3.内浇道附近过热
4.砂型水分过多,砂芯未烘干
5.合金晶粒粗大
6.铸件在铸型中的位置不当
7.浇注温度过高,浇注速度太快
防止方法:
1.从冒口补浇金属液,改进冒口设计
2.炉料应清洁无腐蚀
3.铸件缩松处设置冒口,安放冷铁或冷铁与冒口联用
4.控制型砂水分,和砂芯干燥
5.采取细化品粒的措施
6.改进铸件在铸型中的位置降低浇注温度和浇注速度
四 裂纹
缺陷特征 :
1.铸造裂纹。
沿晶界发展,常伴有偏析,是一种在较高温度下形成的裂纹在体积收缩较大的合金和形状较复杂的铸件容易出现
2.热处理裂纹:
由于热处理过烧或过热引起,常呈穿晶裂纹。
常在产生应力和热膨张系数较大的合金冷却过剧。
或存在其他冶金缺陷时产生
产生原因:
1.铸件结构设计不合理,有尖角,壁的厚薄变化过于悬殊
2.砂型(芯)退让性不良
3.铸型局部过热
4.浇注温度过高
5.自铸型中取出铸件过早
6.热处理过热或过烧,冷却速度过激
防止方法:
1.改进铸件结构设计,避免尖角,壁厚力求均匀,圆滑过渡
2.采取增大砂型(芯)退让性的措施
3.保证铸件各部分同时凝固或顺序凝固,改进浇注系统设计
4.适当降低浇注温度
5.控制铸型冷却出型时间。
6.铸件变形时采用热校正法。
7.正确控制热处理温度,降低淬火冷却速度。
呋喃树脂砂工艺
1—1自硬呋喃树脂砂的概念
自硬呋喃树脂砂的命名来源于英语的FuranNo-Bakeprocess,它表示以呋喃树脂为粘结剂,并加入催化剂混制出型砂,不需烘烤或通硬化气体,即可在常温下使砂型自行固化的造型方法。
通常被简称为“冷硬树脂砂”,甚至“树脂砂”。
以下介绍两个基本概念。
一、呋喃树脂的概念
由碳原子和其它元素原子(如O、S、N等)共同组成的环叫做杂环、组成杂环的非碳原子叫杂原子。
含有杂环的有机化合物叫做杂环化合物。
所谓“呋喃”,是含有一个氧原子的五员杂环有机化合物,它是表示一族化合物的基本结构总称。
在呋喃系中不带取代基的杂环作为母体,叫做“呋喃”,它的衍生物则根据母体来命名。
呋喃本身在互业上并无什么用途,但它的衍生物——糠醛和糠醇,却是互业上的重要原料,它们是最重要的呋喃衍生物,糠醛学名叫α——呋喃甲醛,糠醇学名叫呋喃甲醇。
它们的分子结构如下:
含有糠醇的树脂称为呋喃树脂。
作为铸造粘结剂用的呋喃树脂一般是用糠醇(FA)与尿素、甲醛或苯酚等缩合而成的,如尿醛呋喃树脂(UF/FA)、酚醛呋喃树脂(PF/FA)、酚脲醛呋喃树脂(UPF-FA)和甲醛——糠醇树脂(F/FA)等。
二、呋喃树脂的硬化机理
根据呋喃树脂的组成不同,分别可以通过加热、通入硬化气体或添加酸催化剂等方法使其固化。
酸催化(即“自硬”)的呋喃树脂一般糠醇含量都超过50%。
其硬化机构很复杂,现在还未完全弄清楚,但基本的树脂化反应包括了糠醇的第一醇基和呋喃环的第五位氢之间的脱水缩合,此外呋喃环的断裂生成乙酰丙酸,第一醇基间脱水生成醚和醛等等的反应。
图1-1为呋喃树脂粘结剂的成分和代表性的呋喃自硬树脂结构的一例。
•初期阶段
1—2
自硬呋喃树脂砂的优缺点
一、自硬呋喃树脂砂具有以下优点:
1.铸件表面光洁、棱角清晰、尺寸精度高。
这是由于树脂砂造型可以排除许多使型(芯)变形的因素。
如:
(1)型砂流动性好,不需捣固机紧实,减少了模样(芯盒)的伤损和变形;
(2)砂型(芯)固化后起模,减少了因起模前松动模样和起模时碰坏砂型(芯)引起的变形;(3)无需修型,减少了修型时引起的变形;(4)无需烘烤,减少了因烘烤造成的铸型(芯)变形;(5)铸型强度高、表面稳定性好,故芯头间隙小、分型负数小,减少了下芯、配模过程中铸型的破损和变形,保证了配模精度;(6)铸型(芯)硬度高,热稳定性好,可以有效地抵御浇注时的型壁退让、迁移现象,减少了铸型的热冲击变形(如胀砂等);(7)型砂的溃散性好,清理、打磨容易,从而减少了落砂清铲修整工序中对铸件形状精度的损害。
综上所述,由于在各个工序中都最大限度地排除了影响铸型、铸件变形和损坏的因素,所以树脂砂铸件的铸件表面质量、铸件几何尺寸精度方面比粘土烘模砂可以提高1—2级,达到CT7-9级精度和1-2mm/600mm的平直度,表面粗糙度更大有改观。
2.造型效率高,提高了生产率和场地利用率,缩短了生产周期。
这是由于
(1)、型砂流动性好,不需捣固机紧实,节省了大量的捣固工作量,使造型操作大为简化;
(2)铸型强度高,节约了起模后修型工作量;(3)型(芯)上醇基涂料点干后可省去烘干工序,节约了工时和场地;(4)旧砂回收后干法机械再生,使砂处理为封闭系统,便于机械化,可以节约大量旧砂处理,型砂混制、运输等辅助劳动;(5)型砂的溃散性好,落砂容易,修整工作量少、(6)节约了一些造型(芯)前的准备工作量。
如插芯固等。
根据一般统计,用自硬呋喃树脂砂代替粘土烘模砂后,生产效率可提高40—100%,单位造型面积产量可提高20—50%。
3.减轻劳动强度,大大改善了劳动条件和工作环境,尤其是减轻了噪音、矽尘等,减少了环境污染。
4.节约能源。
这表现在取消了烘窑和水力清砂,提高了铁水成品率,大大降低了压缩空气消耗,从而在节水、节电、节煤(焦)等方面效果显著。
5.树脂砂型(芯)强度高(含高温强度高)、成型性好、发气量较其它有机铸型低、热稳定性好、透气性好,可以大大减少铸件的粘砂、夹砂、砂眼、气孔、缩孔、裂纹等铸件缺陷,从而降低废品率,可以制造出用粘土砂难以做出的复杂件、关键件。
6.旧砂回收再生容易,可以达到90—95%的再生回收率。
在节约新砂、减少运输、防止废弃物公害等方面效果显著。
二、自硬呋喃铸型有一些缺点,应采取相应对策。
1.对原砂要求较高,如粒度、粒形、SI02含量、微粉含量、碱金属盐及粘土含量等都有较严格要求;
2.气温和湿度对硬化速度和固化后强度的影响较大;
3.与无机类粘结剂的铸型相比,树脂砂发气量较高,如措施不当,易产生气孔类缺陷;
4.由于硬化机理是脱水缩合型,故硬化反应需一定时间,模样的周转率较低,不易适应于大批量铸件的生产;
5.与粘土砂相比,成本仍较高;
6.对球铁件或低C不锈钢等铸件,表面因渗硫或渗碳可能造成球化不良或增碳,薄壁复杂铸钢件上易产生裂纹等缺陷;
7.浇注时有剌激性气味及一些有害气体发生,CO气发生量较大,需有良好的通风条件。
1—3自硬呋喃树脂砂的发展概况
呋喃树脂最早作为铸型用粘结剂是1958年在美国开始使用的,当时是作为热芯盒粘结剂使用的。
把它作为自硬性铸型进行研究是1963年-1971年在英国进行的。
这个期间从基础研究到生产大铸件都作了扎实的实用化研究。
其结果,报导了用少量粘结剂能获得很高的强度,铸型溃散性好,铸件尺寸精度高,生产效率提高等一系列优点。
为获得今天这样的发展奠定了基础。
在欧美,70—80年代是自硬呋喃砂取得飞跃发展的时期。
在日本将自硬呋喃砂用于生产一般铸件是从1973年开始的,约十年左右,全国多品种小批量的中、大铸件生产中有一大半过渡到用自硬呋喃铸型来生产。
这种发展趋势至今方兴未艾,尽管其他有机自硬铸型开发了更多种类,然而现在占首位的仍然是自硬呋喃树脂砂。
在我国,七十年代开始研究自硬树脂砂,但仅限于个别厂家和研究单位搞试验。
从八十年代初,尤其是1982年以后,随着改革开放政策的贯彻,我国与国外合作生产的工厂增多,不少合作生产的外国厂家都对铸件生产提出来用自硬树脂砂的要求,否则无法合作。
对国内来说,以出口产品为主,对铸件质量的要求也越来越高。
于是在这种社会生产发展的新形势下,在国外树脂砂热的推动下,迫使我国广大铸造工作者们认识到应用自硬树脂砂是造型工艺上的一场革命,是提高铸件和机械产品质量的重要途径,是振兴铸造行业改变后面貌的必由之路,是机械产品跃入国际市场的基本保证。
因此八十年代我国铸造生产战线上形成了“树脂砂热”。
由于自硬树脂砂最适合于多品种小批量的中大铸件生产,所以机床行业、水泵行业、阀门行业和造船、石化等行业在树脂砂推广应用中走在最前面。
迄今为止,据不完全统计,我国已引进树脂砂处理生产线不下五十家,国内有三大铸机厂(重庆、保定、漯河)已正式生产成套树脂砂设备。
另外,生产原辅助材料的厂家遍布各省,原辅助材料的质量进步很快,有些已接近或达到国外同类产品的水平。
事实表明用树脂砂工艺取代粘土烘模砂生产多种小批量中大铸件是今后国内铸造业界的发展方向之一。
第二章自硬呋喃树脂砂的原辅材料
组成自硬呋喃树脂砂的主要原材料有作为型砂骨料的原砂,作为粘结剂用的呋喃树脂,作为催化剂用的酸类固化剂和作为添加剂的硅烷偶联剂等,树脂砂造型中必须的辅助材料有涂料、脱模剂、粘合剂、浇口陶管、分型剂等。
原辅材料的好坏对树脂砂铸件质量的影响很大,本章对以上主要原辅材料作一简单介绍。
2—1原砂
一般仍选用天然石英砂。
对于部分高合金钢铸件或特殊需要的情况下,也有选用铬矿砂或锆砂等特殊骨料的。
这里我们主要讨论树脂砂对石英砂的要求。
一、矿物成分与化学成分
原砂的主要矿物成分是石英(即SiO2)、长石和云母,还有一些铁的氧化物和碳化物。
石英比重2.55,莫氏硬度七级,熔点1713℃,具有耐高温、耐磨损等优点。
若原砂中石英(SiO2)含量高,则原砂的耐火度和复用性都好。
长石是铝硅酸盐,常见的有钾长石(K2O、AI2O3、SiO2)钠长石(Na2O、AI2O3SiO2)和钙长石(2CaO、AI2O3、SiO2),长石比重2.54-2.76,莫氏硬度6-6.5级,熔点1100-1250℃,因其熔点低、硬度低、不耐磨、易粉碎,会降低树脂砂的复用性和耐火度。
云母是种含铝硅酸盐,有黑白云母之分,白云母的成分为(3AI2O3、6SiO2、H2O)。
云母的熔点为1145-1270℃,比重2.7-3.2。
硬度很低,极易破碎,它在砂中的含量多少对原砂的复用性很有影响。
总之,在选择原砂时,SiO2含量应尽量高一些,不纯物要少,当然还与金属的熔点和浇注温度,铸件壁厚等因素有关。
一般来说,铸钢用原砂SiO2含量应大于95%,铸铁应大于92%,有色金属可以低一些。
杂质允许含量还与旧砂是否再生回用以及下面谈到的耗酸量有关。
二、粒形和表面光滑度
对于粒形,要求园形或类园形,砂粒表面应光洁平整,没有孔洞或裂纹。
这样的砂粒表面积小,砂粒表面涂上一层薄膜所需的树脂量少些。
一般用角形系数表示砂粒形园整度,人造石英砂虽然SiO2含量高,但粒形为多角形甚至尖角形,角形系数太大,需经研磨处理,一般不采用。
天然砂中角形系数最小的要算风积砂,如内蒙通辽一带的大林标准砂,角形系数小于1.2,呈圆形。
为了改善粒形,对原砂最好进行擦磨处理。
目前我国唯一生产擦磨砂的是江西星子砂矿。
该矿对原砂经擦磨处理后,角形系数从1.47减少到1.35,与此同时,SiO2含量也从93%(水洗砂)提高到95%(45/75目)砂样抗拉强度也由12.2Kg/cm2增加到16.3Kg/Cm2。
原砂的粒形不仅影响树脂砂加入量,同时还影响到树脂砂的流动性及紧实程度,砂粒表面空洞裂纹不仅无效消耗树脂,而且砂粒易碎,影响复用性及粒度保持性。
三、粒度分布及微粉含量
粒形相同的原砂,以粒度较粗的总表面积小,树脂用量少,透气性好,耐火度高。
粗砂的缺点是抗机械粘砂能力低。
一般多选用30/50目、40/70目为宜,为提高综合性能,本厂采用30/70目的多筛号分布的砂。
微粉及含泥量严重恶化树脂砂性能。
由于微粉表面积很大,消耗树脂及固化剂影响透气性及强度,原砂中的泥份中碱土金属含量较高,据介绍细粉状比粒状耗酸值要大3—10倍。
一般要求原砂含泥量应小于0.3%。
四、含水量
树脂砂的硬化是放热反应,原砂含水量严重影响树脂的固化强度与固透性,实验证明,含水量由0.2%升高到0.4%,型砂的抗拉强度可从13.2kg/cm2降低到8.6kg/cm2,固化时间也从30分钟延长到70分钟。
国外一般要求原砂含水量小于0.1%,国内一般要求小于0.2%。
所以对树脂砂用原砂应进行干燥处理。
五、PH值与耗酸量
原砂的PH值对树脂砂的固化速度及终强度有一定的影响,由于树脂是在酸催化剂作用下脱水缩合固化的,故当原砂碱性较强时,需耗费额外的酸固化剂。
。
砂的PH值一般为6.5-7.2,若使用海砂时,PH值为9左右,耗酸量可达17以上,其中贝壳和CaCO3的耗酸量远远超过了其它物质,不易固化,需经过淡水冲洗或擦洗,擦磨处理。
前面也谈到,原砂中SiO2含量减少时,长石、云母和其它杂质会增加,长石和云母两种矿物中都含有碱金属化合物Na2O、K2O,钙长石和其它一些杂质中则含有CaO、MgO等,都是增加耗酸量的成分。
因为原砂中含有某些不溶于水的碱性物质,所以砂不采用简单的PH值实验,而采用耗酸量实验。
使用再生处理砂时,由于新砂加入量少,耗酸量的影响较轻,但对于全部采用新砂的树脂砂,耗酸量的影响则不可低估一般应控制在5以下。
综上所述,树脂砂对原砂的要求十分严格,国外特别重视树脂砂的原砂选用和处理。
如日本宁可从遥远的澳大利亚运