剪切模型在武钢1580热轧机的运用.docx
《剪切模型在武钢1580热轧机的运用.docx》由会员分享,可在线阅读,更多相关《剪切模型在武钢1580热轧机的运用.docx(10页珍藏版)》请在冰豆网上搜索。
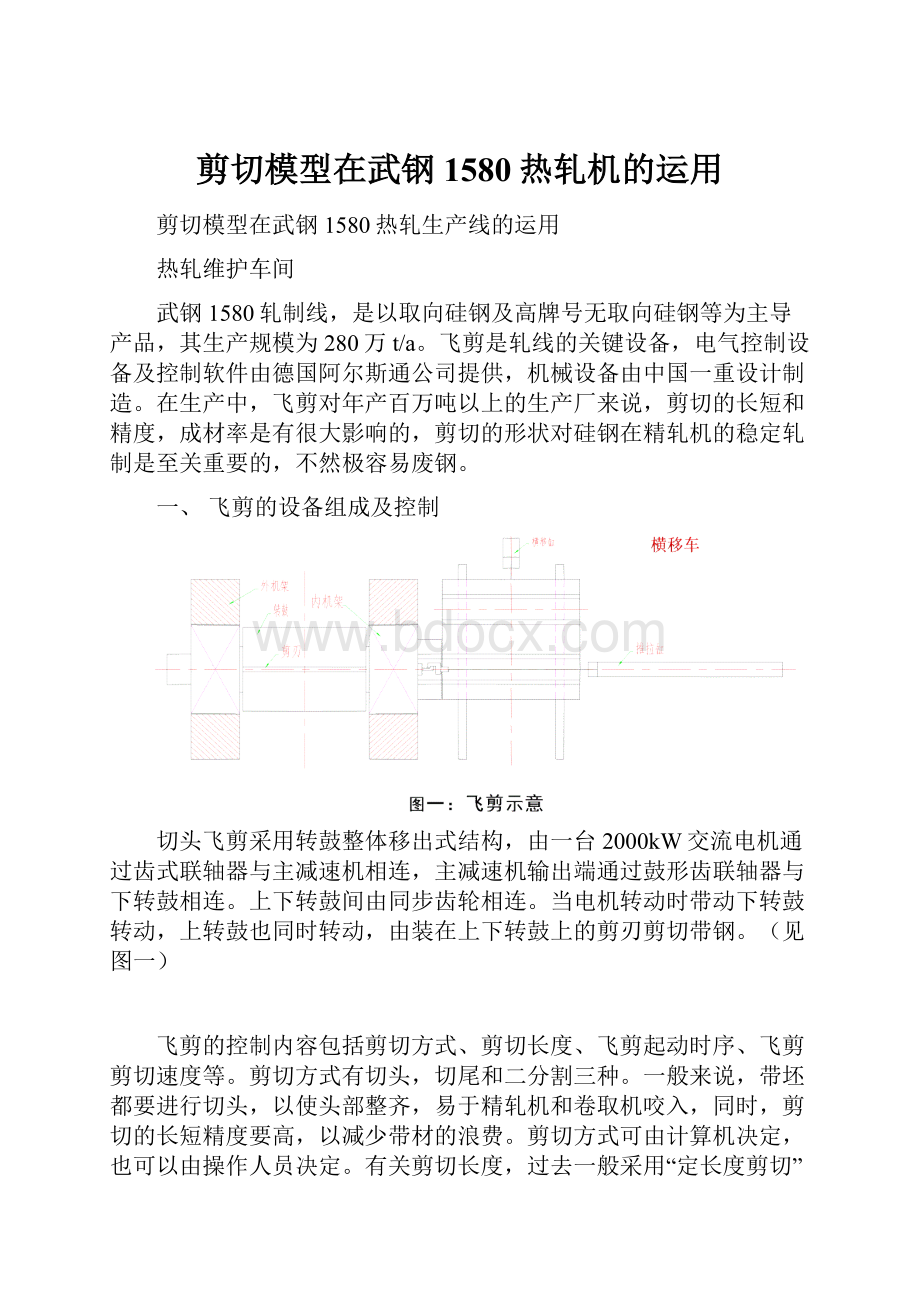
剪切模型在武钢1580热轧机的运用
剪切模型在武钢1580热轧生产线的运用
热轧维护车间
武钢1580轧制线,是以取向硅钢及高牌号无取向硅钢等为主导产品,其生产规模为280万t/a。
飞剪是轧线的关键设备,电气控制设备及控制软件由德国阿尔斯通公司提供,机械设备由中国一重设计制造。
在生产中,飞剪对年产百万吨以上的生产厂来说,剪切的长短和精度,成材率是有很大影响的,剪切的形状对硅钢在精轧机的稳定轧制是至关重要的,不然极容易废钢。
一、飞剪的设备组成及控制
切头飞剪采用转鼓整体移出式结构,由一台2000kW交流电机通过齿式联轴器与主减速机相连,主减速机输出端通过鼓形齿联轴器与下转鼓相连。
上下转鼓间由同步齿轮相连。
当电机转动时带动下转鼓转动,上转鼓也同时转动,由装在上下转鼓上的剪刃剪切带钢。
(见图一)
飞剪的控制内容包括剪切方式、剪切长度、飞剪起动时序、飞剪剪切速度等。
剪切方式有切头,切尾和二分割三种。
一般来说,带坯都要进行切头,以使头部整齐,易于精轧机和卷取机咬入,同时,剪切的长短精度要高,以减少带材的浪费。
剪切方式可由计算机决定,也可以由操作人员决定。
有关剪切长度,过去一般采用“定长度剪切”,并由操作人员设定切头、切尾的长度。
近年来发展为根据带坯的不同头部形状进行“最佳长度剪切”,以提高成材率。
切头时,飞剪的速度要高于带坯的高度,切尾时飞剪的速度要低于带坯的速度。
起动飞剪剪切的控制时序为:
当带坯使E辊道上指定HMDON时,测带钢的速度,控制带钢的速度已降到与飞剪的速度相适应,经过一定的延迟时间后,起动飞剪切头。
切尾时飞剪的起动则依靠热金属检测器的检失信号(HMDOFF)
工艺控制精度及要求见下表
1
切头飞剪剪刃停位精度
±3°以内
2
切头飞剪剪切长度精度
±5mm(最佳化剪切)
±30mm(无最佳化剪切)
3
飞剪剪刃一次上机剪切次数
10000次
4
最大剪切能力
60×1430mm(1-2.5m/s)
≥900℃碳素钢、低合金钢
二、剪切参数计算
假设:
飞剪半径(带剪刃)
SHR_RADIUS
基本不变
重叠量
OVER_LAPPING
基本不变
剪切启动时角度
ALPHA_START
常量
板坯厚度
MAT_THICK
变量
剪切长度
CUT_LENGTH
变量
剪切速度(1+超前量%)
CUT_LEAD
变量
切头角校正
COR_CUT_ANG
常量
抛钢角校正
COR_EXIT_ANG
常量
我们可以得出:
1.飞剪剪刃旋转周长:
CIRCUMF=2*Π*SHR_RADIUS
2.COS(剪切角alpha):
用邻角边/半径
理论上讲:
邻角边=轧制线-板坯厚度。
板坯中心线与上转鼓中点距离=飞剪半径-1/2(剪刃重叠量),再减去一半的带钢厚度即为邻角边长。
COS_CUT_a=[SHR_RADIUS-0.5(MAT_THICK+OVER_LAPPING)]/SHR_RADIUS
3.剪切角(弧度):
CT_a_ger=arcCOS(COS_CUT_a)
4.抛钢角(弧度):
剪切角加偏移量2(以转鼓中心线为起点,逆时针旋转)
CL_a=CT_a_ger+COR_EXIT_ANG
5.切头角(弧度):
2Π减去剪切角,加上偏移量1(以转鼓中心线为起点,逆时针旋转)
CT_a=2Π-CT_a_ger+COR_CUT_ANG
6.抛钢位置(与2Π的比值):
BETA_EXIT=CL_a/2Π
7.切头位置(与2Π的比值):
ALPHA_CUT=CT_a/2Π
8.剪切点与转鼓中心线距离,即剪切对角边长:
用三角函数即可
DELTA_S=-SIN(CT_a)*SHR_RADIUS
9.剪切速度(与板坯速度的比值):
如下图二,由三角函数易得出:
剪刃旋转方向的线速度=板坯速度/COS(CT_a)
图二、剪刃线速度矢量示意图
RU_FACTOR=(1+LEAD%)/COS(CT_a)
10.剪切过程剪刃旋转弧长:
RU_DIST_SHR=(ALPHA_CUT-ALPHA_START)*CIRCUMF
11.带钢行走距离(剪切过程中):
理论上讲:
剪刃线速度从0加到RU_FACTOR斜坡不变,即在此过程中剪刃的平均速度为RU_FACTOR/2。
在剪切过程中:
MAT_LENGTH/SHR_LENGTH=MAT_SPD/SHR_SPD=
1/(RU_FACTOR/2)=2/RU_FACTOR.因此在剪切过程中,带钢行走距离MAT_LENGTH=2*RU_DIST_SHR/RU_FACTOR。
RU_MATLENGTH=2*RU_DIST_SHR/RU_FACTOR
12.飞剪启动时带钢距离:
MAT_DIST_START=CUT_LENGTH-RU_MATLENGTH-DELTA_S
三、HMD与飞剪动作指令
HMD_E501/502
↑
切头
SHR_WAIT→SHR_START
HMD_E403/404或者HMD_E501/502
↓
切尾
SHR_WAIT→SHR_START
HMD_E501/502和HMD_2048
↑
切头
SHR_START→SHR_HEAD_CUT
HMD_E501/502和HMD_2048
↓
切尾
SHR_START→SHR_TAIL_CUT
四、飞剪区域板坯跟踪
飞剪区域以飞剪转鼓中垂线和轧制线交点为基准“0”,沿轧制线精轧方向为正方向,粗轧方向为负方向。
例如:
HMD_2048位置坐标为(-7.78m,0)。
4.1切头时板坯位置跟踪
由于切头开始由HMD_2048给出指令,所以起始位置为HMD_2048,再对板坯速度积分,注意:
切头加上延迟距离=延迟时间(0.003s)*板坯即时速度
HEAD_POS=-HMD_2048_DIST+HMD_DELAY*MAT_SPD+∫MAT_SPD…….(公式1)
=-7.78+0.003*MAT_SPD+∫MAT_SPD
4.2切尾时板坯位置跟踪
当以上公式1的计算值大于8m时,夹送辊速度积分器把以上HEAD_POS的数据记录下来HEAD_POS_MEMORY,并开始独立对夹送辊速度进行积分。
MAT_DIST=HEAD_POS_MEMORY+∫MAT_SPD……………………………………(公式2)
由于切尾指令由HMD_2048下降沿给出,所以切尾位置就是“带钢头部”位置加上HMD_2048_DIST。
切尾减去HMD时间延迟。
HEAD_POS=MAT_DIST+HMD_2048_DIST-MAT_SPD*HMD_DELAY…………………………………………..….(公式3)
五、剪切角偏移量计算
5.1切头时剪刃角度偏移量(弧度)
由于剪刃本身有厚度,安装时上下也不是绝对靠近转鼓中垂线,所以切头时存在一个负的偏差量。
偏差量由实际测量出。
COR_CUT_ANG=arcTAN(-OFFSET/RADIUS)
5.2切尾时剪刃角度偏移量(弧度)
COR_EXIT_ANG=arcTAN[GRIND_RADIUS2-(0.5*MAT_WIDTH)2+OFFSET-GRIND_DADIUS]/RADIUS
六、自动模式下的剪切计算
图三、剪切流程示意图
飞剪在剪切过程中基本上由以上8个基本动作构成(如图三),除去我们不用的7-chopping,2-speed_up_man_cut和用于校正飞剪角度的8-calibration_turn,6-triangle可视为3-cut的剪刃速度部分。
下面着重分析0-idle,1-speed_up_auto,3-cut,4-positioning四个步骤(见下表)。
板坯跟踪实际位置>MAT_DIST_START(见1.12)
0-idle→1-speed_up_auto
S1
剪刃实际位置>ALPHA_CUT(见1.7)
1-speed_up_auto→3-cut
S3
抛钢时剪刃实际角度>BETA_EXIT(见1.6)
3-cut→4-positioning
S4
板坯跟踪实际位置>MAT_DIST_START(见1.12)
4-positioning→1-speed_up
S1
由于飞剪各个流程的控制实际上是对主电机速度的控制,即飞剪变频器的速度基准值Wn。
飞剪在各个不同的流程计算时,会将特定的速度给定计算激活,下面进行速度给定值的计算分析。
注意:
以下计算大部分采用比例计算的方式即:
实际值/参考值,无实际意义只能说明其与飞剪基准速度Wn的增加,减少,正比和反比关系。
给出的基准速度Wn也是比例值。
飞剪电机的最大速度为600转/min,剪刃最大线速度为2.618m/s。
即以下计算值如果超出“1”,则“1”位速度给定值。
6.1S1-speed_up过程速度给定值计算:
设:
MAT_RUN=(MAT_DIST-REF_DIST_TO_START)/RUN_UP_LENGTH
我们可以看出:
当带头超过给定起始位置时MAT_DIST>DIST_TO_START,MAT_RUN开始大于0,并随着带钢靠近飞剪不断递增。
即:
MAT_RUN与带头位置成正比关系。
Wn=MAT_SPD*RU_FACTOR*MAT_RUN+∫[MAT_RUN2-(ALPHA_ACT-
REF_SHTAR_POSITION)*CIRCUMF/REF_DIST_SHR]
我们可以看出:
1.带钢速度、带头位置与飞剪速度成正比例关系,并随着带钢靠近飞剪不断递增。
2.飞剪旋转过程中,剪刃位置与带头位置一起控制飞剪的加减速,剪刃旋转过快时减速,剪刃旋转速度旋转过慢时加速,并与带头位置相联系。
6.2S3_cut过程速度给定值计算:
由于cut整个时间比较短,大概在210ms左右。
一般来说:
在从S1切换到S3过程中,Wn基本保持S1完毕后的速度不变,直到S3完成。
6.3S4_positioning过程速度给定值计算:
定位过程主要分为2步进行,在IBA上可以明显看到定位过程中的基准速度的变换。
1.目标角度和实际角度差大于5.4度时:
假设:
alpha_minus=(Alpha_destination-Alpha_act)/1.2,1.2为可调参数。
Wn为alpha_minus的平方根。
由此我们可以看出当角度值越来越接近给定值时,给出的参考速度不断变小趋近于“0”。
2.目标角度和实际角度差大于5.4度时:
Wn=(Alpha_destination-Alpha_act)*4.944,4.944为可调参数。
七、关于优化剪切和激光测速的投入
7.1优化剪切的控制及设备
精确测量带钢宽度、速度、头和尾的形状,设定带钢的头尾的最佳剪切的长度;
优化剪切投入的基本设备:
●R2轧机后测宽仪1台
●R2轧机后测速仪1台
●飞剪前测速仪1台
飞剪前热金属探测器(线扫描)1台
利用安装在R2后的测宽仪和测速仪测量出带钢的宽度和速度,测速仪内部积分得出带钢的长度,并计算出需要剪切的头部和尾部的长度,通过网络传送给轧线控制系统。
当带钢到达飞剪前时热金属探测器探测到带钢的头部,飞剪前测速仪把速度信号送给轧线控制系统来实现带钢头部和尾部的最佳化剪切。
7.2关于优化剪切程序的启动
依次打开30Q1_CPU2_T00_5SHRSBINPUT如图四
图四、优化剪切程序段
从上面我们可以看出,如果要投入优化剪切只需要将shr.opmode.CropLengthFromKelkShape置为“1”。
但是要注意:
1.在刚开始投入时要注意比较从Kelk读过来的数据和我们现在使用的剪切长度。
例如:
切头时比较shr.kelk.HeadCutLength与70mm的差值,如果差值过大则需要调整kelk的数据。
2.在投入优化剪切以后我们可以看到以前的人工干预剪切已经无效,所以需要修改程序,在kelk的数据上加入偏差量即可。
将人工干扰参数与优化联系起来。
(优化剪切并不考虑飞剪本身的相关参数,由前面我们可知飞剪模型计算并不是绝对的实际值)。
6.3激光测速的投入
依次打开30Q1_CPU2_T01_2SHRFBINPUT如图五
图五、激光测速选择程序段
从上面我们可以看出激活激光测速需要:
1.在画面上选择激光测速,即:
shr.opmode.spdMeasWithLaser=1。
2.在程序中将penultimatestandactivefromrollschedule置“0”。
八、参考文献
[1]《MagneticalOpticalMedia》德国阿尔斯通公司
[2]《HPCI硬件和软件用户手册》德国阿尔斯通公司
[3]《1580热轧初步设计》中冶赛迪工程技术股份有限公司
[4]《电气设计任务书》中国一重
[5]《Functionaldescription》SMS
2010-8-20