MRP采购管理案例doc 33页.docx
《MRP采购管理案例doc 33页.docx》由会员分享,可在线阅读,更多相关《MRP采购管理案例doc 33页.docx(20页珍藏版)》请在冰豆网上搜索。
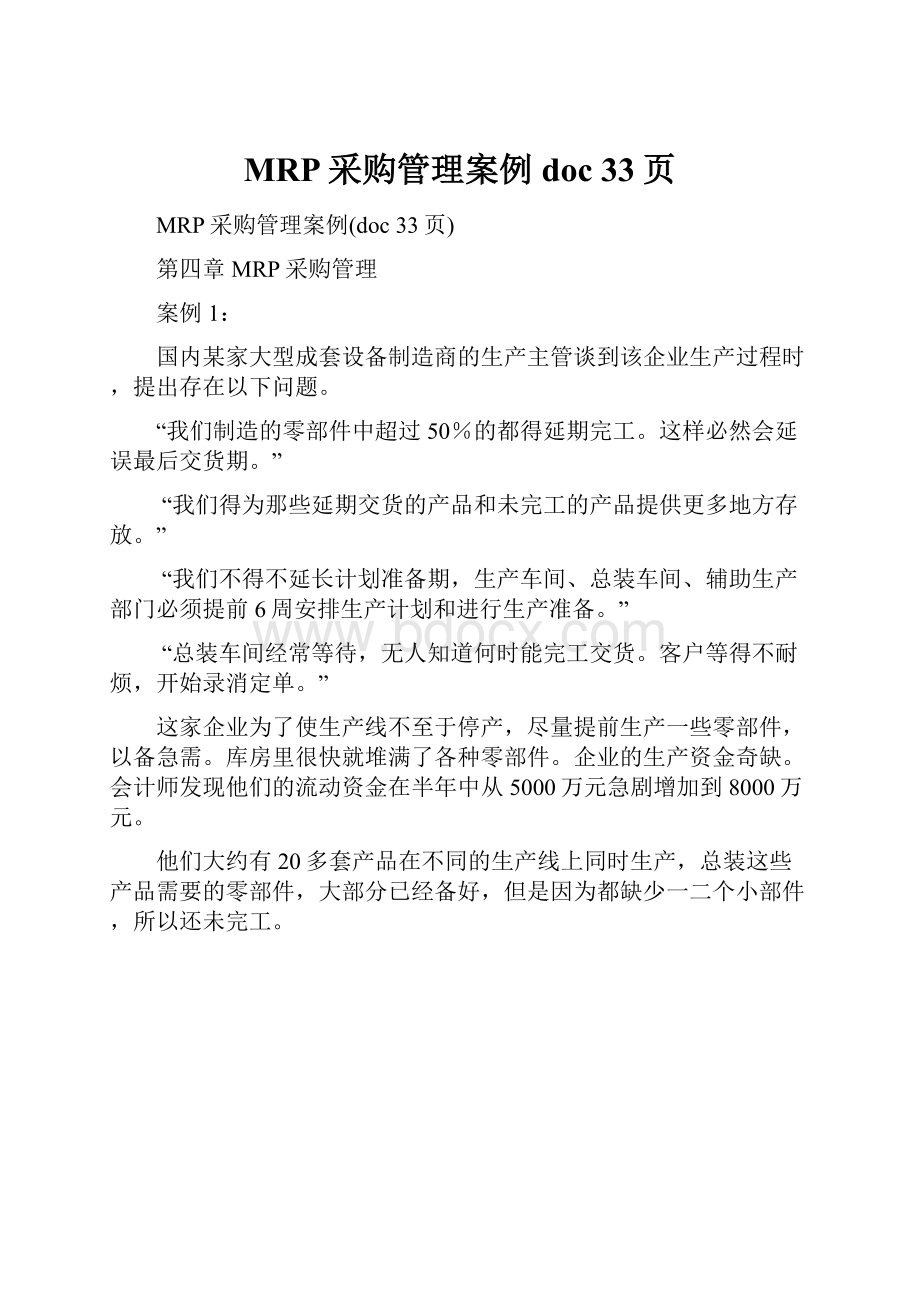
MRP采购管理案例doc33页
MRP采购管理案例(doc33页)
第四章MRP采购管理
案例1:
国内某家大型成套设备制造商的生产主管谈到该企业生产过程时,提出存在以下问题。
“我们制造的零部件中超过50%的都得延期完工。
这样必然会延误最后交货期。
”
“我们得为那些延期交货的产品和未完工的产品提供更多地方存放。
”
“我们不得不延长计划准备期,生产车间、总装车间、辅助生产部门必须提前6周安排生产计划和进行生产准备。
”
“总装车间经常等待,无人知道何时能完工交货。
客户等得不耐烦,开始录消定单。
”
这家企业为了使生产线不至于停产,尽量提前生产一些零部件,以备急需。
库房里很快就堆满了各种零部件。
企业的生产资金奇缺。
会计师发现他们的流动资金在半年中从5000万元急剧增加到8000万元。
他们大约有20多套产品在不同的生产线上同时生产,总装这些产品需要的零部件,大部分已经备好,但是因为都缺少一二个小部件,所以还未完工。
1.
2.
3.序时间出发,把工序时间中最少的松弛时间、最早交货时间等参数,输入计算机中进行车间作业模拟,以观察哪一种方案最好。
4.60年代,许多企业曾尝试采用“车间作业管理系统”以期提高车间能力的利用率,解决“车间并没有完成应该完成的任务”、“车间设备工时利用率不高”、“车间作业负荷不均衡”、“车间能力不够”等问题。
5.车间作业负荷平衡及优化系统。
在一段时间内,许多企业自己尝试开发实施一种旨在更好地利用车间能力负荷的应用系统。
这种系统通过修改计划日期以保证均衡生产。
6.物料统管:
即把物料采购、生产控制、库存控制和其他物料管理功能集中起来,形成—个统—管理的组织形式,作为上面所分析问题的解决方案。
后来的实践证明,这些方案都无法达到预期的目标。
原因在于这些方案的设计者没有真正认识到:
出现问题的根源在于这些企业的计划问题。
绝大多数用来解决生产控制问题的方法,都没有考虑到真正的问题是计划问题。
1.采用优先级法则来控制生产活动的人们竞没有想到。
在模拟中使用的交货时间到底是否有效?
如果交货时间并不真正反映需求日期,这种模拟还有什么意义。
2.—些企业采用“生产作业管理系统”,是因“车间并没有完成应该完成的任务”、“车间设备工时利用率不高”、“车间作业负荷不均衡”、“车间能力不够”等表向现象误导了人们;实际上,这些问题并非是车间工作人员的问题,而是因为计划安排无效,他们根本不知道什么是应该完成的任务。
3.采用“车间作业负荷平衡及优化系统”的人们在实践中发现,该系统所依据的是不准确的计划日期。
4.物料统管的方案是必要的。
这种解决方案使采购人员、生产控制人员、库存控制人员一起工作,而不是相互扯皮,有利于解决物流过程的衔接问题。
但是如果没有有效的生产计划作保证,这种方案只是治标而不治本。
无效计划的影响:
美国人发现无效的计划安排是使得美国的制造企业竞争力下降的原因。
无效的计划安排常常表现为加班生产赶进度。
经常性的加班使得工人的工作效率下降,影响设备的正常维修和保养造成设备故障率增加。
如果计划安排是无效的,那么采购人员就常常是在一种紧张的气氛中工作。
由于采购紧缺物料是被动被迫的,必须马上完成任务,这样会使工作人员忽视经济效果评价、价格判断、签订供货协议以及与工程设计人员合作使产品符合企业控制标准等工作。
当计划不能有效运行时,采购和退货方面的交通运输费与定货费也会增加。
计划失效的原因:
为什么企业会出现计划无效的问题?
不断变化的环境使计划的编制极为复杂和困难。
所有在企业中编制过计划的人们都可能体会到,编制企业生产作业计划最困难的问题是复杂多变的环境!
特别是产品结构比较复杂的离散制造企业,其生产计划必须在企业内安排生产数以千百计的项目或从企业外采购数以千计的不同种类的零部件、原材料或最终产品等。
他们编制计划的依据主要有两个:
一是市场预测,二是客户定货合同。
在许多企业,生产计划的编制是从市场预测开始的。
他们—般根据本企业过去的统计数字,再考虑一些现在变动的因素,最后通过臆想的系数来调整,得出其市场预测的结果。
问题是这些市场预测是很难准确的,实际执行的结果又会与原来预期的结果产生越来越大的偏差。
例如某项作业被遗漏了、被提前了或推后了。
客户需要提前交货等。
人们常常会在生产现场看到某些紧急下达的作业指令,其他计划中的作业必须让位于这些紧急作业。
原定计划会被打乱。
进而导致更多的紧急作业。
另外有很多企业是依据客户合同编制生产作业计划的。
因此他们不会遇到预测不准的问题,只需要根据销售部门已经落实的客户定货合同展开生产作业计划即可。
但实际上这样编制出来的生产计划在执行过程中,仍然会有问题。
例如,客户修改了产品规格,要求提前交货,已经发出的采购定单不能按期交货,供应商要改变规格等问题,都会使原定计划失效。
为了解决无效计划问题,美国制造业采用了MRP作为解决问题的方案。
第一节
生产企业采购
一、生产企业人工采购计划系统
企业生产系统是一个复杂系统。
一个产品由多个零部件构成,每个零部件又有多个零部件、多道加工工序,不同的零部件和工序又构成了不同的生产车间。
一个完整的产品,有成千上万个零部件。
这些不同的生产车间、不同的生产工序生产出来的零部件又要按一定的时间进度、一定的比例关系统一装配成—个一个完整的产品。
装配生产线一运转起来,各个零部件只要有一个到不了位,产品就装配不成。
因此从产品到零部件、再到原材料,从总装车间到各个分装车间、再到各个仓库,整个企业的生产需要有一个庞大、精确的计划,包括生产计划和采购计划,才能把不同空间、不同时间的零部件有条不紊地进行生产和装配,按时按量地组织到总装配线上来,最后装配成合格的产品。
装配所需要的零部件以及生产过程中所需要的零部件不一定都是自己生产的,有相当一部分要从外面企业采购进来。
由于品种多而杂,靠人工制订采购计划,一是工作量大,需要许多人参与做计划;即使这样,也常常是顾此失被,常常是采购了这个产品,忘了那一个。
而且由于计划人员多、相互之间协调难度大,有的产品重复采购,有的产品没人采购。
造成有的产品严重库存积压、有的产品却缺货,一方面花费了很高的库存成本,一方面又影响了装配线的正常运转。
某大型电讯企业在一段时间内就出现了这种情况。
为了支持庞大的生产系统的正常生产,企业建立了一个庞大的高层立体仓库,有许多的货位。
又建立了一个庞大的采购计划小组,制订采购计划,并且实施采购。
采购进来的各种各样的电子器件和配件,存放在各个货位中。
但是运行起来之后,发现有的货位堆得满满的,有的产品在需要装配的时候,却找不着存货,严重影响了正常的生产。
于是这个企业下决心改变这种混乱局面、改变它的人工采购计划系统。
他们引进、采用MRP系统,用计算机制订采购计划。
由于计算机处理速度快、计划精细、不出差错,所作出的采购计划交给采购人员去实施,企业终于迅速扭转了以前用人工采购计划系统出现的被动局面。
二、生产企业MRP采购计划系统
MRP本来是生产企业用来制订物料需求计划、进行生产管理的一个应用软件。
它不但可以制订出企业的物料投产计划,还可以用来制订外购件的采购计划,非常适合于在加工、制造、装配企业中使用,配合使用计算机,MRP可以迅速制订出比较详细复杂的生产计划和采购计划。
因此许多大型的企业,都把使用MRP作为自己坚定不移的目标。
切实按照其制订的计划去执行,既可以保证产品在装配时不发生缺货、保障企业生产的正常进行,而且保证采购的产品库存量不高也不低、刚好可以满足生产计划规定的需要,不会造成库存积压,也不会造成缺货。
并且使得库存管理井井有条,节省保管费用,节省计划人员。
第二节MRP基本介绍
一、传统订货点方法的缺点与mrp的提出
二、MRP的思想原理
MRP应用的目的之一是进行库存的控制和管理。
按需求的类型可以将库存问题分成两种,独立性需求和相关性需求。
独立性需求是指将要被消费者消费或使用的制成品的库存,如自行车生产企业的自行车的库存。
制成品需求的波动受市场条件的影响,而不受其他库存品的影响。
这类库存问题往往建立在对外部需求预测的基础上,通过一些库存模型的分析,制定相应的库存政策来对库存进行管理,如什么时候订货、订多少。
如何对库存品进行分类等等。
相关性需求库存是指将被用来制造最终产品的材料或零部件的库存。
自行车生产企业为了生产自行车还要保持很多种原材料或零部件的库存。
如车把、车梁、车轮、车轴、车条等。
这些物料的需求彼此之间具有一定的相互关系。
例如一辆自行车需要有两个车轮,如果生产1000辆自行车,就需要1000x2=2000个车轮。
这些物料的需求不需要预测,只有通过相互之间的关系来进行计算。
在这里白行车称为父项,车轮称为子项(或组件)。
20世纪60年代计算机应用的普及和推广,....资料搜索网人们可能应用计算机制定生产计划,美国生产管理和计算机应用专家首先提出了物料需求计划(MaterialRequirementPlanning),IBM
公司则首先在计算机上实现了MRP处理。
MRP基本的思想原理是,由主生产进度计划(MPS)和主产品的层次结构逐层逐个地求出主产品所有零部件的出产时间、出产数量。
把这个计划叫做物料需求计划。
其中,如果零部件靠企业内部生产,需要根据各自的生产时间长短来提前安排投产时间,形成零部件投产计划;如果零部件需要从企业外部采购,则要根据各自的订货提前期来确定提前发出各自订货的时间、采购的数量,形成采购计划。
确实按照这些投产计划进行生产和按照采购计划进行采购,就可以实现所有零部件的出产计划,从而不仅能够保证产品的交货期.而且还能够降低原材料的库存,减少流动资金的占用。
第三节
MRP系统
在计算机应用之前,人工得用6—13个星期计算物料需要量,因此也只能按季度订货。
这样的话,MRP方法也不见得比订货点方法优越。
然而,应用计算机之后,情况就不同了,计算物料需求量的时间被缩短至1—2天,订贷周期短,订货时间快,可以由每季订贷改为每月了。
因此,MRP系统就成为实现MRP的手段。
MRP系统是一个信息处理系统,作为一个信息系统,应该有输入,处理,有输出。
比如一个中国移动通信网站中的话费查询功能,需要输入手机号码和密码,然后登陆系统,用户选择话费查询业务,然后系统输出这个月的话费详单!
那么这个系统包括了用户信息的输入和功能选择的输入,然后系统进行一系列操作,作后向用户输出需要的信息。
系统的业务流程如下。
一个信息系统的框架基本如此,那么一个MRP系统也应该有它的输入、输出以及处理过程。
本节将向大家简单介绍一下MRP系统的输入、输出和处理过程。
一、MRP的输入
物料需求计划的依据是:
1.MPS主生产计划
2.BOM物料清单
3.库存信息
他们的关系如下:
处理的问题
需用的信息
1.生产什么?
生产多少?
1.现实可行的MPS
2.需要用到什么?
2.准确的BOM
3.已有什么?
3.准确的库存信息
4.还缺什么?
何时需要?
4.MRP的计算结果
MRP的输入有三个文件:
(一)主生产进度计划MPS(MasterProductionSchedule)
主生产进度计划一般是主产品的一个产出时间进度表。
主产品是企业生产的用以满足市场需要的最终产品,一般是整机或具有独立使用价值的零件、部件、配件等。
不要把主生产计划和销售预测相混淆,后者反映的是一种需求。
主产品一般是独立需求产品,靠市场的订货合同、订货单或市场预测来确定其未来一段时间(一般是一年)的总需求量,包括需求数量、需求时间等。
这些资料再根据企业生产能力状况经过综合调配平衡,把它们具体分配到各个时间单位中去。
这就是主产品出产进度计划。
这个主产品出产进度计划是MRP系统最主要的输入信息,也是MRP系统运行的主要依据。
MPS的对象
最终产品。
主生产计划的计划对象是生产规划的产品系列具体化后的产品,通称最终项目(enditem)。
主生产计划中的最终项目可以是产品、主要组件、虚拟物料单中的组件,甚至可以是产品结构中最高层次上的单个零件。
MPS的对象的确定应遵循满足最少项目数的原则。
例如,电脑制造公司可用零配件来简化MPS的排产。
市场需求的电脑型号,可由若干种不同的零部件组合而成,可选择的零配件包括:
6种CPU、4种主板、3种硬盘、3种软驱、2种光驱、3种内存、4种显示器、3种显卡、2种声卡、2种Modem、5种机箱电源。
基于这些不同的选择,可装配出的电脑种类有6×4×3…=103680种,但主要的零配件总共只有6+4+3+…=35种,零配件的总数比最终产品的总数少得多。
显然,将MPS定在比最终产品(电脑)这一层次低的某一级(零配件)比较合理。
经过对装配过程的分析,确定只对这些配件进行MPS的编制,而对最后生成的103680种可选产品,将根据客户的订单来制订最终装配计划。
主产品出产进度计划来自企业的年度生产计划。
年度生产计划覆盖的时间长度一般是一年,在MRP中用52周来表示。
但是主产品的出产进度计划可以不一定是一年,要根据具体的主产品的出产时间来定。
但是有一个基本原则,即主产品出产进度计划所覆盖的时间长度要不少于其组成零部件中最长的生产周期。
否则,这样的主产品出产进度计划不能进行MRP系统的运行,因此是无效的。
产品A的出产进度表
时期(周)
1
2
3
4
5
6
7
8
产量(件/周)
25
15
20
60
15
(二)主产品结构文件BOM(BillofMaterials)
主产品结构文件不简单地是一个物料清单,它还提供了主产品的结构层次、所有各层零部件的品种数量和装配关系。
一般用一个自上而下的结构树表示。
每一层都对应一定的级别,最上层是0级,即主产品级,0级的下一层是1级,对应主产品的一级零部件,这样一级一级往下分解,……一直分解到最末一级n级,一般是最初级的原材料或者外购零配件。
每一层各个方框都标有三个参数:
1.组成零部件名;
2.组成零部件的数量。
指构成相连上层单位产品所需要的本零部件的数量。
3.相应的提前期。
所谓提前期,包括生产提前期和订货提前期。
所谓生产提前期,是指从发出投产任务单到产品生产出来所花的时间;而订货提前期是指从发出订货到所订货物采购回来入库所花的时间。
提前期的时间单位要和系统的时间单位一致,也以“周”为单位。
有了这个提前期,就可以由零部件的需要时间而推算出投产时间或采购时间。
例:
见教材 p140
(三)库存文件
库存文件也叫库存状态文件。
它包含有各个品种在系统运行前的期初库存量的静态资料,但它主要提供并记录MRP运行过程中实际库存量的动态变化过程。
由于库存量的变化是与系统的需求量、到货量、订货量等各种资料变化相联系的,所以库存文件实际上提供和记录各种物料的各种参数随时间的变化。
这些参数有:
l.库存量
库存量是指每周库存物资的数量,包括现有库存量和未来各周的计划库存量两种。
在开始运行MRP以前,仓库中可能还有库存量,叫做现有库存量,也叫本期期初库存量。
MRP运行是在期初库存量的基础上进行的,所以各个品种的期初库存量作为系统运行的重要参数必须要输入到系统之中。
由于在一周中,随着到货和物资供应的进行,库存量是变化的,所以周初库存量和周末库存量是不同的。
因此规定这里记录的库存量都是周末库存量。
它在数值上表示为:
库存量=本周周初库存量+本周到货量-本周需求量
=上周周末库存量+本周计划到货量-本周需求量
库存量是满足各周需求量的物资资源。
在有些情况下,为了防止意外情况造成的延误,还对某些关键物资设立了安全库存量,以减少因紧急情况而造成的缺货。
在考虑安全库存的情况下,库存量中还应包含安全库存量。
2.计划到货量。
计划到货量是指在本期MRP计划之前已经购近在途、或者生产在产、预计要在本次MRP计划期的某个时间到达的货物数量。
它们会在给定时间点实际到货入库,而且可以用来满足本次MRP计划期内的生产和装配要求。
它们也可以是临时订货、计划外到货或者物资调剂等得到的货物。
但不包括根据这次MRP运行结果产生的生产任务单生产出来的产品或根据采购订货单采购回来的外购品。
这些产品由下面的“计划接受订货”来记录。
3.总需要量
总需要量是指主产品及其零部件在每一周的需要量。
其中主产品的总需要量与主生产进度计划一致,而主产品的零部件的总需要量根据主产品出产进度计划和主产品的结构文件推算而得出。
总需要量中,除了以上生产装配需要用品以外,还可以包括一些维护用品,如润滑油、油漆等,既可以是相关需求,也可以是独立需求。
合起来记录在总需要量中。
表6—3给出了一个库存文件的例子。
见教材p142。
以上三个文件就是MRP的主要输入文件。
除此之外,为运行MRP还需要有一些基础性的输入,包括物料编码,提前期,安全库存等。
二、MRP的输出
MRP的输出包括了主产品及其零部件在各周的净需求量、计划订货接受和计划订货发出三个文件。
(一)净需求量
净需求量,是指系统需要外界在给定的时间提供的给定物料的数量。
这是物资资源配置最需要回答的主要问题,即到底生产系统需要什么物资、需要多少、什么时候需要。
净需求量文件很好地回答了这些问题。
不是所有零部件每一周都有净需求的,只有发生缺货的周,即计划库存量小于0才可能发生净需求量。
净需求量的计算方法是:
1.当本周计划库存量大于0时,因为不缺货,所以净需求量为0;
2.当本周计划库存量小于0时,又分成两种情况:
(1)当本周计划库存量小于0、而上周的计划库存量大于等于0时本周净需求量就等于本周的缺货量,即本周计划库存量的绝对值;
(2)当本周计划库存量小于0、而上周的计划库存量也小于0时,则本周净需求量就等于本周的缺货量与上周的缺货量之差。
即本周计划库存量与上周计划库存量之差的绝对值。
所以,MRP在实际运行中,不是所有的负库存量都有净需求量的。
求净需求量可以这样简单地确定:
在现有库存量一栏中第一个出现的负库存量的周,其净需求量就等于其负库存量的绝对值;在其后连续出现的负库存量各周中,各周的净需求量等丁其本周的负库存量与前一周的负库存量之差的绝对值。
(二)计划接受订货量
它是指为满足净需要量的需求,应该计划从外界接受订货的数量和时间。
它告诉人们,为了保证某种物资在某个时间的净需求量得到满足,提供的供应物资最迟应当在什么时候到达、到达多少。
这个参数的用处,除了用于记录满足净需求量的数量和时间之外,还为后面的参数“计划发出订货”服务,是“计划发出订货”的参照点(两者数量完全相同,时间上相差一个提前期)。
计划接受订货的时间和数量与净需要量完全相同。
计划接受订货量=净需要量
(三)计划发出订货量
它是指发出采购订货单进行采购、或发出生产任务单进行生产的数量和时间。
其中发出订货的数量,等于“计划接受订货”的数量,也等于同周的“净需求量”的数量;计划发出订货的时间是考虑生产或订货提前期,为了保证“计划接受订货”或者“净需要量”在需要的时刻及时得到供应,而提前一个提前期得到的一个时间。
即:
计划发出订货时间=计划接受订货时间-生产(或采购)提前期
=净需求量时间—生产(或采购)提前期
因为MRP输出的参数是直接由MRP输入的库存文件参数计算出来的,所以为直观起见,总是把MRP输出与MRP库存文件连在一起,边计算边输出结果。
例如表6—3就列出了A产品的MRP运行结果。
其运行过程如下:
首先根据MRP输入的库存文件计算出A产品各周的库存量。
本周库存量=上周库存量+本周计划到货订货—本周总需求
本周库存量都是指周末库存量,它可以为正数、负数和0。
然后MRP系统就计算和输出各周的净需要量。
只有那些库存量为负数的周才有净需要量。
净需要量的计算方法是:
第一次出现的负库存量(-10)的周(第二周)的净需要量就等于其负库存量的绝对值(10),紧接在后面的负库存量的周(第三周)的净需要量就等于本周的负库存量(—15)减去上一周的负库存量(—10)所得结果的绝对值(5)。
同样算出第五周净需求量为20,第四、六、七、八周的净需要量为0。
接着MRP系统就计算和输出计划接受订货量,它在数量和时间上都与净需要量相同,如表,第二周接受10.第三周接受5。
计划接受定货量满足净需求量,而计划到货量满足部分总需要量。
二者合起来,就完全满足了总需要量。
最后MRP系统就计算和输出计划发出订货量,它是把计划接受订货量(或净需要量)在时间上提前一个提前期(这里是l周)、订货数量不变而形成的.如表,第一周发出10个的订货单,第二周发出5个的订货单。
这就是MRP最后处理的结果。
它最后给出的是发出的一系列订货单和订货计划表。
三、MRP处理过程
MRP整个处理过程可以用图6—5所示的流程图表示。
整个过程可以分成以下几步:
(一)准备
在运行MRP之前,要做好以下几个方面的准备工作:
确定时间单位,确定计划期的长短。
一般计划期可以取1年,时间单位取为周,则计划期就是52周。
当然时间单位也可以取天,计划期可以取任意的天数。
在这里,取时间单位为周,计划期长度为M周。
1.确定物料编码,包括主产品和零部件的编码。
2.确认主产品出产进度计划MPS,它被表示成主产品各周的出产量。
3.确认主产品的结构文件BOM,它被表示成具有层级结构的树形图。
由主产品(0级)开始,逐层分解成零部件,直到最后分解到最低层(设为n级)——初级原材料或外购零配件为止。
每个组成零部件都要标明零部件名、单个上层零部件所包含本零部件的数量和本零部件的生产(或采购)提前期。
每一层都要标明层号(也叫层级码)。
除了主产品(一般为独立需求)及其零部件(一般为相关需求)外,还有些辅助生产用品、维护、维修用品等需要外购的用品,可以作为独立需求按实际需要量直接列入BOM的最低层,参与共同的物料需求计划。
4.谁备好主产品及其所有零部件的库存文件,特别是各自的期初库存量,计划到货量。
有些物资,尤其是长距离、难订货的物资还要考虑安全库存量、订货批量和订货点等。
(二)逐级处理
首先从层级码等于0的主产品开始,依次取各级层级码的各个零部件进行如下处理:
1.输入提前期L、期初库存量H0(有些物资还要输入订货点Qk、订货批量Qo、安全库存量Qs等)。
2.对于每一个时间单位t(周),输入或计算下列参数:
(1)输入或计算出产进度计划G(t);
(2)输入计划到货量S(t);
(3)计算库存量H(t):
H(t)=H(t-1)十S(t)-G(t);
(4)求出净需求量N(t):
当H(t)<0、而H(1-1)<0时,N(t)=|H(t)-H(t-1)|
当H(t)<0、而H(t-1)<0时,N(t)=|H(t)|
当H(t)>=0时,N(t)=0。
(5)计算计划接受订货量P(t):
P(t)=N(t);
(6)计算并输出计划发出订货量R(t—L):
R(t—L)=P(t)。
3.输出计划发出订货量R(t—L)。
这是每一个零部件发出的订货单,包括订货数量、订货时间,包括交各车间加工制造的生产任务单,也包括交采购部门采购的采购订货单:
它们按时间整理起来就是一个物料订货计划,也就是一个物料需求计划。
下面通过例子来说明。
见教材P146
第四节....资料搜索网
MRP采购实施
一、采购计划的确定
上一节讲的采购计划:
在上一节中,通过MRP系统的运行结果确定了所需物料的计划发出订货的订货量和订货时间。
这就是订货计划,也就是采购计划。
根据MRP的计算结果确定采购量和采购时间:
根据这个计划规定的时间发出订货,订货量取计划中规定的订货量,则经过一个采购提前期,采购回来的物资刚好可以赶上这一周的需要。
举例说明:
例如根据表6—7,经过MRP计算的结果,零件C在第一周,有一个计划发出订货量15件。
则根据这个计划实施采购,第一周就要出