Moldflow在塑料注塑成型中的应用.docx
《Moldflow在塑料注塑成型中的应用.docx》由会员分享,可在线阅读,更多相关《Moldflow在塑料注塑成型中的应用.docx(12页珍藏版)》请在冰豆网上搜索。
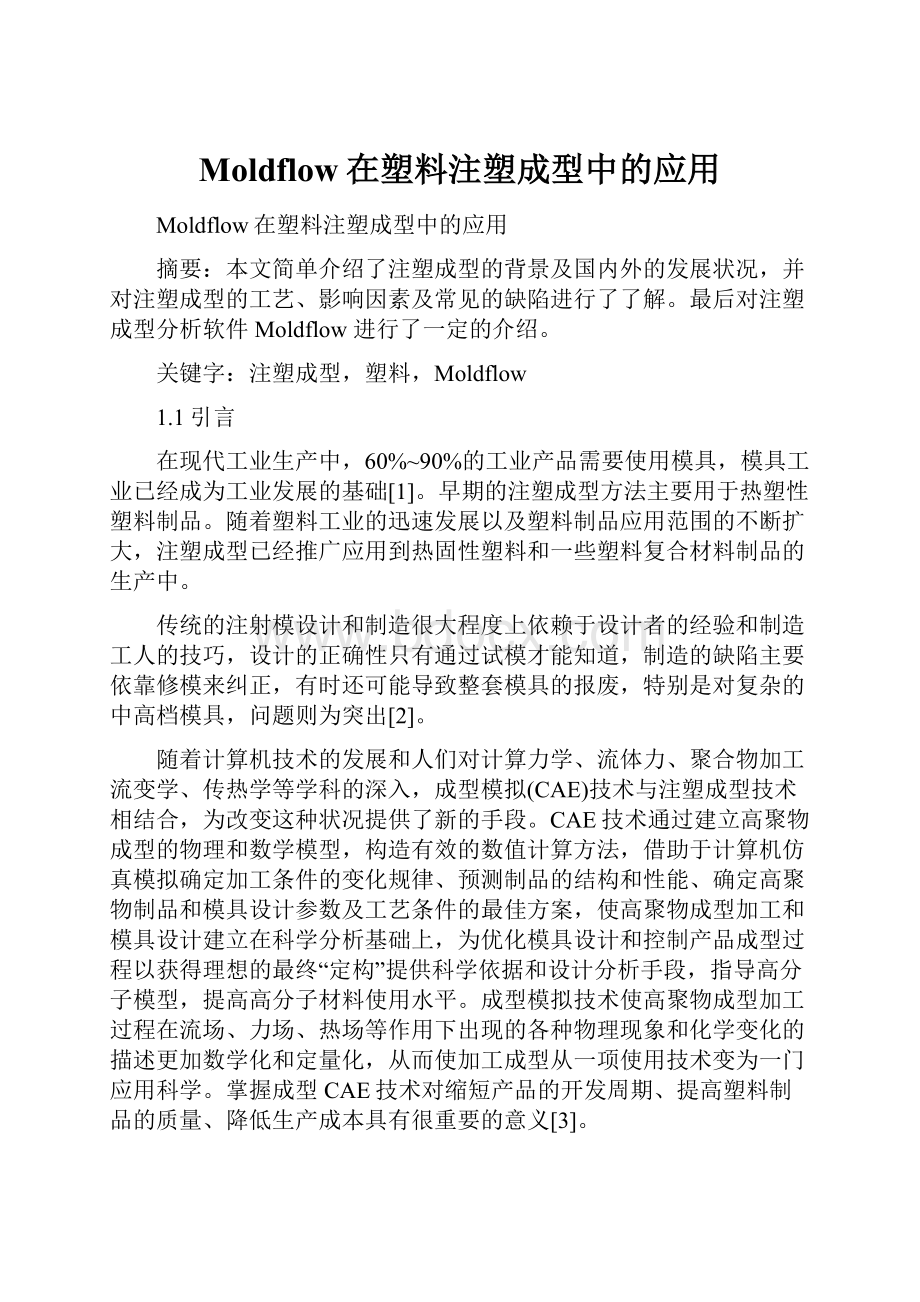
Moldflow在塑料注塑成型中的应用
Moldflow在塑料注塑成型中的应用
摘要:
本文简单介绍了注塑成型的背景及国内外的发展状况,并对注塑成型的工艺、影响因素及常见的缺陷进行了了解。
最后对注塑成型分析软件Moldflow进行了一定的介绍。
关键字:
注塑成型,塑料,Moldflow
1.1引言
在现代工业生产中,60%~90%的工业产品需要使用模具,模具工业已经成为工业发展的基础[1]。
早期的注塑成型方法主要用于热塑性塑料制品。
随着塑料工业的迅速发展以及塑料制品应用范围的不断扩大,注塑成型已经推广应用到热固性塑料和一些塑料复合材料制品的生产中。
传统的注射模设计和制造很大程度上依赖于设计者的经验和制造工人的技巧,设计的正确性只有通过试模才能知道,制造的缺陷主要依靠修模来纠正,有时还可能导致整套模具的报废,特别是对复杂的中高档模具,问题则为突出[2]。
随着计算机技术的发展和人们对计算力学、流体力、聚合物加工流变学、传热学等学科的深入,成型模拟(CAE)技术与注塑成型技术相结合,为改变这种状况提供了新的手段。
CAE技术通过建立高聚物成型的物理和数学模型,构造有效的数值计算方法,借助于计算机仿真模拟确定加工条件的变化规律、预测制品的结构和性能、确定高聚物制品和模具设计参数及工艺条件的最佳方案,使高聚物成型加工和模具设计建立在科学分析基础上,为优化模具设计和控制产品成型过程以获得理想的最终“定构”提供科学依据和设计分析手段,指导高分子模型,提高高分子材料使用水平。
成型模拟技术使高聚物成型加工过程在流场、力场、热场等作用下出现的各种物理现象和化学变化的描述更加数学化和定量化,从而使加工成型从一项使用技术变为一门应用科学。
掌握成型CAE技术对缩短产品的开发周期、提高塑料制品的质量、降低生产成本具有很重要的意义[3]。
注塑成型是一种主要的塑料制品成型方法,能够一次成型复杂外形的塑件,同时所生产的塑件尺寸精度高,是一种高效率,能大批量生产的加工方法。
长期以来,我国的注塑模具在设计过程中主要依赖设计员的直觉和经验,而产品结构、模具设计以及成型工艺参数的合理性都无法预知,因此一套模具生产出来的产品是否满足客户的需求,往往是在不断的试模与修模中进行改善的,这加大了模具的设计制造周期,延长了交付日期,同时也加大了模具制造成本,这在激烈的市场经济竞争中使得企业出于一个被动的位置,加大了企业的生存风险[3,4]。
CAE技术能让模具设计人员通过CAE软件对注塑成型过程进行模拟分析,使得设计人员能更加直观的了解注塑成型过程中塑料在熔融状态下型腔内的流动情况以及冷却固化的情况,同时获得相关参数以便于设计人员发现设计中的问题修改图纸,同时优化注塑成型工艺参数,从而使得设计人员摆脱经验化、提高工厂生产效率、降低生产成本和提高塑件质量等目的。
因此加大对注塑成型的研究尤为重要[5]。
传统的注射模设计和制造很大程度上依赖于设计者的经验和制造工人的技巧,设计的正确性只有通过试模才能知道,制造的缺陷主要依靠修模来纠正,有时还可能导致整套模具的报废,特别是对复杂的中高档模具,问题则为突出[2]。
随着计算机技术的发展和人们对计算力学、流体力、聚合物加工流变学、传热学等学科的深入,成型模拟(CAE)技术与注塑成型技术相结合,为改变这种状况提供了新的手段。
CAE技术通过建立高聚物成型的物理和数学模型,构造有效的数值计算方法,借助于计算机仿真模拟确定加工条件的变化规律、预测制品的结构和性能、确定高聚物制品和模具设计参数及工艺条件的最佳方案,使高聚物成型加工和模具设计建立在科学分析基础上,为优化模具设计和控制产品成型过程以获得理想的最终“定构”提供科学依据和设计分析手段,指导高分子模型,提高高分子材料使用水平。
成型模拟技术使高聚物成型加工过程在流场、力场、热场等作用下出现的各种物理现象和化学变化的描述更加数学化和定量化,从而使加工成型从一项使用技术变为一门应用科学。
掌握成型CAE技术对缩短产品的开发周期、提高塑料制品的质量、降低生产成本具有很重要的意义[3]。
1.2国内外研究概况
从上世纪五十年代起,国外大批学者对塑料熔体流动及冷却进行了一系列的理论研究,建立了塑料熔体的黏弹性模型,结合质量守恒、动量守恒、能量守恒及本构关系等数学模型,推导出了塑料熔体的流动控制方程及边界条件,在此基础上先后建立了流动的一维、二维及三维模型[5]。
上世纪六十年代到九十年代,通过合理的简化及假设,CAE分析程序从纯粹的流动与冷却分析程序发展到流动、冷却、保压、翘曲、纤维分子及应力分析的高集成化分析程序,市场上也涌现出了一批诸如Moldflow、Polyflow、Tmconcept、Z-Mold塑料成型模拟软件[6]。
1.2.1流道系统的优化
林旭东等在聚合物幂率基础上,对压力降进行控制调节,利用解析法得到优化后的流道尺寸[7]。
M.Zhai等建立充填平衡的判断准则,同时以充模完成后浇口最小压力评价充填平均,并以此对浇口位置进行优化研究[8-10]。
王攀等利用MoldflowInsight软件对针阀式热流道热嘴闭合顺序对纤维取向的影响进行研究[11]。
H.S.Kim使用CAE软件对成型过程中多种类型浇口对熔体流动路径的影响进行研究,考察是否会导致短射等缺陷[12]。
张伟建立以压力有效利用率为指标的优化目标,得出一种计算流道截面的方法[13]。
I.Pandelidis等以浇口位置优化为研究对象,采用爬山算法和模拟退火算法结合的算法,得到最佳浇口位置,达到降低翘曲变形的目标[14]。
林旭东等推导了优化流道截面尺寸的设计公式,并利用CAE系统进行优化设计[15]。
申长雨等为实现平衡冲模,采用优化浇口位置的方法达到目的[16]。
余晓容等利用有限元软件对塑件注塑注塑进行模拟,并对浇口大小、截面形状、流道排布及分流道尺寸进行优化[17-18]。
朱伟等对流道尺寸理论计算和人机交互设计时的参数优化设置的公式进行推导,并得出了节省设计时间的经验公式[19]。
B.H.Kim等利用CAE软件中流动模块进行分析,对流道和浇口进行优化以达到平衡充模的目的[20]。
1.2.2成型工艺参数的优化
Huang和Tai将CAE技术与正交实验设计法相结合,选择模具温度、熔体温度、保压时间及保压压力等作为变量因子,研究工艺参数对制件翘曲变形的影响,并得到最优优的工艺参数[21]。
刘春太等运用田口法对塑件的熔接线等进行优化[22]。
曾喜生通过建立正交实验表就,利用Moldflow软件进行实验模拟,考察各工艺参数对塑件表面Z向的平面度的影响情况,采用方差分析对实验结果进行分析,得到最优成型工艺参数[23]。
曹雄刚等利用正交实验法,使用Moldflow软件开展工艺参数对翘曲变形影响的研究,采用极差分析和方差分析的方法对实验结果进行分析,确定工艺参数对翘曲变形的影响,得到翘曲变形量最小的工艺参数[24]。
严志云等对Moldflow进行二次开发,提升软件对工艺优化的能力,并举例进行说明二次开发后的Moldflow在实际中运用[25]。
杨亚男以手机M2832为例,利用Moldflow软件对其进行翘曲分析,并利用正交实验法优化参数,减少了翘曲变形,对薄壁复杂塑件的设计与生产有指导意义[26]。
T.C.Chang采用田口法,确定对塑料收缩的影响程度较大的工艺参数,并得到了最佳注塑成型工艺参数,达到了减少塑件收缩的目的[27]。
童尧研究了数值模拟与优化设计在多质量目标工艺参数优化方面的的应用,利用正交实验法及Moldflow对参数分组模拟,得到结果并以灰色关联度作为评价因子,得到最优解[28]。
H.Ye等对塑件的变形程度采用应变张量的方式进行描述,并使用退火法进行优化,得到变形最小时的最优工艺参数[29]。
张昉昀等采用Moldflow软件结合DOE法,考虑多工艺参数的影响,对工艺参数进行优化[30]。
BehroozFarshi等采用Moldflow,从塑料熔体温度、各阶段保压压力、模温、速度/压力切换点、冷却液入口温度、保压时间六个方面降低塑件体积收缩和翘曲变形量[31]。
申长雨等对充模进行有限元模拟,采用数值分析方法,为优化工艺参数打下了基础[32].
2.1注塑成型概述
注塑成型是一种高分子材料的成型方法,其加工过程为:
利用注塑机的螺杆或柱塞运动时所产生的压力,将处于熔融状态的塑料以一定压力和速率填充到模具的密闭腔体内,在熔体冷却固化后,取得塑件[1]。
注塑成型在整个塑料加工业中具有极为重要的作用,注塑成型所生产的制品占总塑料制品总产量的三分之一左右。
2.1.1注塑成型的机构和系统
注塑成型在加工依靠注塑机和模具两个主体部分来完成。
注塑机内主要包括电控系统、注射系统和锁模系统;注塑模具结构则涵盖模具型芯型腔、浇道流道、导向定位系统、脱模顶出机构、温控系统和侧向分型抽芯机构;另外还有一些辅助设备,比如料筒。
模温机、温控箱等。
注塑成型便是依靠这些系统或者机构进行的[3]。
2.1.2塑料特性
塑料是一种高分子有机物。
在选用塑件时须考虑塑件外观、工件工况条件及成本等因素。
塑料材料确定后,其缩水率也就确定下来。
在模具设计过程中,对塑料的物化特性及塑件结构等诸多因素需要进行考虑分析。
成型工艺参数的确定则需要考虑塑料的物性、品质要求及模具浇注系统等因素。
塑料材料主要特性如下[3]:
(1)结晶性
塑料的结晶性用于确定模具结构、编制工艺参数等方面。
不同的结晶度决定不同的塑件性能。
塑料结晶不一致也会导致制品的翘曲变形。
(2)流动性
塑料熔体处于一定工艺参数下的填充型腔的能力,称为塑料的流动性。
影响塑料流动性的因素包括:
塑料的物化特性,模温,注射压力,注射速率以及模具成型腔体结构。
(3)收缩性
收缩性是指塑件脱模冷却后发生与原设计尺寸相比的收缩变化的性能。
塑件收缩性的主要影响因素包括:
塑料的物化特性,模具成型腔体结构,塑件结构特性以及成型条件。
(4)吸湿性
吸湿性是指塑料在空气中对水分亲疏的倾向。
必须在成型前的准备工作中采取相应合理的方法对塑料进行干燥。
(5)热敏性
热敏性是指塑料对热比较敏感,在高温受热时间较长或者由于进料口处尺寸过小导致剪切作用大时,材料容易发生变色、分解或烧焦等倾向。
2.1.3注塑成型过程
注塑成型过程分为预处理、注塑和后处理等几个阶段[2,3]
(1)预处理。
在此步中,应对塑料进行重量、吸水性和收缩性检测,成型前应对塑料进行干燥;清洗料筒;预热金属嵌件及模具。
(2)注塑。
经充分加热、塑化的塑料,在液压缸推力推动柱塞或螺杆的作用下,由料筒前端经过注塑机喷嘴注入浇注系统,进入型腔成型的过程。
(3)后处理。
塑件脱模后,为改善和提高塑件的性能及尺寸稳定性,通常需要进行适当的后处理,一般采用退火和调湿处理。
2.1.4注塑成型工艺影响因素
注塑成型工艺的制定是为了保证注塑成型过程的顺利进行以及得到成本控制的最优结果。
其中温度、压力和时间是最为重要的工艺参数[3]。
(1)温度的影响
在注塑成型过程中,温度包括了成型步骤中的各种温度参数,其中最为重要的是料温和模温。
料筒温度关系到塑料塑化的质量,其选择温度的原则为保证顺利注射而不发生降解。
另外提高料温度可以提高熔体的流动性,能有效降低流动阻力提高充填效率。
模温通常是由冷却系统控制的,它决定了冷却速度。
模温越低,冷却越快但熔体的黏度增大、注塑过程中喷嘴所产生的压力在型腔中损失过高,严重时可能导致短射。
而模温越高,熔体流动性越好,充模压力越小制品质量提高,而冷却时间过长,生存率下降,收缩率变大。
(2)压力的影响
背压、注射压力和型腔压力为注塑过程中的三种主要压力。
背压增大了熔体的内压,剪切效果得到加强了,因此也引发熔体温度上升。
较大的背压使螺杆回退速度减慢,塑料加热时间变长,可以改善塑件质量。
然而过高的背压会导致熔体输送能力下降,塑化量减少,增加功率消耗,严重时因为剪切发热过高而导致熔体降解。
注射压力应在注塑机应许范围之内,同时考虑塑件需要的注射压力。
过低会导致型腔压力不足而导致短射;过高则塑件过保压,难以脱模,严重时会导致溢料、制品变形以及系统过载。
(3)时间的影响
注射完成所用时间称为注射周期。
在整个周期中,对塑件质量有着决定性影响的是注射速度和冷却时间参数。
随着注射速度的增大,熔体流速增大,有利于充模,各部分的熔接痕强度也有所加强。
但是过快的注射速度使得熔体从层流状态变为湍流状态,不利于充模。
模具的冷却时间对于调节模具温度,保证注塑成型连续稳定进行有着关键作用。
在Moldflow依靠调节以上等成型参数来进行注塑工艺参数的优化。
由于以上参数的关联性,在确定一套合适的成型工艺参数时往往需要考虑诸多影响因素,而这些因素又不是一成不变的,因此确定出最为合适的工艺参数需要花费较多的精力和成本来完成,而制定最佳成型工艺参数也成为了注塑成型中的一个重要环节。
2.2注塑成型中常见缺陷
在注塑成型中常见缺陷及其产生原因、解决办法如下[3,4]:
(1)熔接痕
塑料熔体在型腔内流动时分为多条流动熔体并最终相会,相会时其交会界面不能熔合,从而产生熔合痕。
(2)短射
短射是指成型周期结束后塑料未能完全充满型腔的缺陷,又称为欠注或者填充不足。
(3)翘曲变形
翘曲变形是指塑件偏离了模腔的形状,与设计的塑件不一致的现象。
(4)气穴
气穴是指熔料在填充的过程中,若干股熔料的前沿汇集而形成的空穴,或者由于模腔内的气体无法完全排出导致填充末端无法完全填充而形成的气泡。
(5)裂纹
裂纹是指在塑件的表面出现的开裂形成的裂缝。
(6)脱模困难
粘模是指成型后的塑件在脱模的过程中出现的难以脱模的现象。
2.3注塑成型CAE理论基础
塑料为高分子材料,其性能对温度和变形速率依赖性很强,其同时兼有粘性液体与弹性固体的性质,而被定义为黏弹体。
塑料在熔融状态一般被认为是非牛顿流体,其流动过程视为非等温、非稳态[26]。
因此注塑成型的CAE技术是在塑胶熔体的粘性流体力学的基本方程的基础上,建立塑胶熔体在模具型腔内流动和传热的物理模型,进行合理的假设和简化,结合特定的边界条件,借助有限元法、有限差分法以及边界元法等数值方法,在PC机上进行计算分析,得出各参数的变化分布情况的一种分析技术。
注塑成型的CAE模拟技术的优势在于能高效率的在计算机上对注塑过程中各环节进行模拟分析,得出温度和压力等参数分布变化的可视化结果,大大节约了计算时间,结果清晰明了,有助与预测塑件质量、注塑缺陷及周期长短,为产品的研发和制造提供了理论基础。
2.4注塑成型分析软件Moldflow简介
随着塑料零件在大多数的行业中的应用不断扩大,以及在成本控制并缩短制造周期承受的压力不断加大,企业对仿真工具的需求日益迫切。
AutodeskMoldflow仿真软件包含注塑成型仿真工具,能够帮助用户对塑料零件、注塑模具和注塑成型流程进行验证和优化[29]。
运用Moldflow进行分析,在设计阶段就可以预测可能出现的缺陷并找出产生的原因,也可以分析得出最佳的成型工艺,提高一次试模的成功率,达到利用Moldflow来减少对高成本物理样机的需求,避免潜在的制造缺陷,更快地向市场推出更加优质产品的目的[20]。
Moldflow是一家专业从事塑料CAE分析的跨国性公司,至今已有超过28年的历史,是全球最早专注于塑料模流模拟的软件公司,是塑料CAE(计算机辅助分析)领域中公司组织规模最大的厂商。
Moldflow已成为目前全世界最大的专业模流分析软件公司[31]。
Moldflow主要产品如下:
(1)AutodeskMoldflowAdviser:
用于产品开发早期验证产品的制造可行性。
(2)AutodeskMoldflowInsight:
在传统注塑的基础上,添加双色注塑、共注成型、注压成型。
热固性材料等分析模块。
(3)AutodeskMoldflowDesignLink:
数据链接工具。
通过它Moldflow各产品不仅可轻松读取IGES、STEP、StereoLithography(STL)等格式的3D模型,还可直接读取Parasolid(UG)、Pro/E、I-DEAS、CATIA、Solidworks等高端CAD软件的最新版本的3D模型。
(4)AutodeskMoldflowCADDoctor:
可以检查,修复,调整和简化实体模型。
2.4.1CAD互操作性和网格
CAD主流软件有UG、Pro/ENGINEER、SolidWorks和AutoCAD等,不同的软件采用不同的精度或者公差以及拓扑结构或算法,在模型数据交换或者采用中间格式的时候,不可避免造成数据丢失,产生间隙、重复面或面丢失等;另外在CAD设计中有些细微的特征是必须的,而这些特征在CAE分析过程中却会造成计算困难或者失败。
为了节省时间提高效率,用MoldflowCADDoctor软件对三维CAD导入的实体模型检查、纠正和简化,去除转换模型时产生的缺陷,为仿真做好准备[24]。
完成模型的修复之后,可根据仿真模拟的精度和求解时间来选择网格类型:
双层面网格(DualDomain)、中面网格(Midplane)、实体网格(Solid3D)。
2.4.2仿真与优化
Moldflow仿真技术主要体现在塑料流动仿真、浇注系统仿真、模具冷却仿真和收缩和翘曲仿真上,通过对整个注塑过程中充填、保压、冷却和翘曲的计算机模拟分析,对仿真结果进行可视化和评估,找出塑件及模具缺陷、确定最佳浇口位置、完成流道的优化设计以及建立最优的冷却系统[25]。
同时,可以通过Moldflow进行成型工艺窗口分析和DOE(DeignofExperiments)分析,找出工艺数据中各参数对注塑成型结果的影响,得到最优的成型工艺。
参考文献
[1]申开智.塑料成型模具[M].北京:
中国轻工业出版社,2007
[2]沈言锦.塑料工艺与模具设计[M].长沙:
湖南大学出版社,2007
[3]李志刚.中国模具设计大典[M].南昌:
江西科学技术出版社,2003
[4]周永泰.中国塑料模具发展概况及展望[[EB/OL],2010
[5]李德群.肖祥芷.模具CAD/CAE/CAM的发展概况及趋势[[J].模具工业,2005(7):
9-12.
[6]申长雨.陈静波.刘春太等.塑料模CAE技术发展概况[J].模具工业,2001.1,51-56
[7]林旭东,申开智.大型注塑模流道优化设计[J].塑料科技,1998(5):
28-33
[8]M.Zhai.Y.C.Lam,andC.K.Au.Automatedselectionofgatelocationforplasticinjectionmoldingprocessing.PolymerPlasticsTechnologyandEngineering,2005,44
(2):
229~242
[9]M.Zhai.Y.C.Lam,andC.K.Au.Algorithmsfortwogateoptimizationininjectionmolding.InternationalPolymerProcessing,2005,20
(1):
14~18
[10]M.Zhai.AndC.Shen.Anoptimizationschemebasedonflowresistancetolocateoptimumgateofcomplexpart.JournalofReinforcedPlasticsandComposites,2005,24(15):
1559~1566
[11]王攀,郑宝文.Moldflow在内外饰件上的应用[R].苏州:
苏州Moldflow大师赛,2010.4
[12]H.S.Kim,J.S.Son,Y.T.Im.Gatelocationdesignininjectionmoldingofanautomobilejunctionboxwithintegralhinges[J].JournalofMaterialsProcessingTechnology,2003,(140):
110–115
[13]张君.基于CAE技术的注塑模浇注系统优化设计[D].合肥:
合肥工业大学
[14]I.PandelidisandQ.Zhou.Optimizationofinjectionmoldingdesign.PartI:
Gatelocationoptimization.PolymerEngineeringandScience,1990,30(15):
873~882
[15]林旭东,王鹏驹.基于注塑CAE分析的流道优化设计[J].塑料工业1997(4):
72-75
[16]申长雨,余晓容,王利霞.塑料注塑成型浇口位置优化.化工学报,200455(3):
446~449
[17]余晓容,申长雨,陈静波等.多型腔注射模浇注系统优化设计.工程塑料应用,2004,32(4):
49~52
[18]余晓容,申长雨,王利霞,刘春太.注塑模流道优化设计[J].力学与实践,2003(25):
23-24
[19]朱伟,唐跃.一模多腔注塑模流道的优化设计[J].塑料,2005(34-5):
81-84
[20]B.H.KimandM.Ramesh.Automaticrunnerbalancingofinjectionmoldsusingflowsimulation.JournalofEngineeringforIndustry.1995,117:
508~515
[21]HuangMC,TaiCC.Theeffectivefactorsinthewarpageproblemofaninjection-moldedpartwithathinshellfeature[J].JournalofMaterialsProcessingTechnology,2001,110
(1):
1-9
[22]刘春太,申长雨.利用TAGUCHI方法优化纤维增强PA66注塑熔接线拉伸性能.复合材料学报,2004,21(5):
68~73
[23]曾喜生.基于Moldflow的注塑成型缺陷分析及成型周期优化[D].湘潭:
湘
潭大学
[24]曹雄刚,靳伍银,韩炎娜,畅越星.Taguchi实验设计在注射成型工艺参数优化中的应用[J].模具工业,2008,34(3):
1-5.
[25]严志云,丁玉梅,谢鹏程等.基于正交试验和MPI二次开发技术多目标优化注射工艺参数[J].塑料制造,2990(10):
76~79
[26]杨亚男.手机外壳注塑成型的数值模拟及翘曲变形控制[D].上海:
上海交通大学
[27]T.C.Chang,E.Faison.Shrinkagebehaviorandoptimizationofinjectionmoldedparts