吹塑成型模具.docx
《吹塑成型模具.docx》由会员分享,可在线阅读,更多相关《吹塑成型模具.docx(12页珍藏版)》请在冰豆网上搜索。
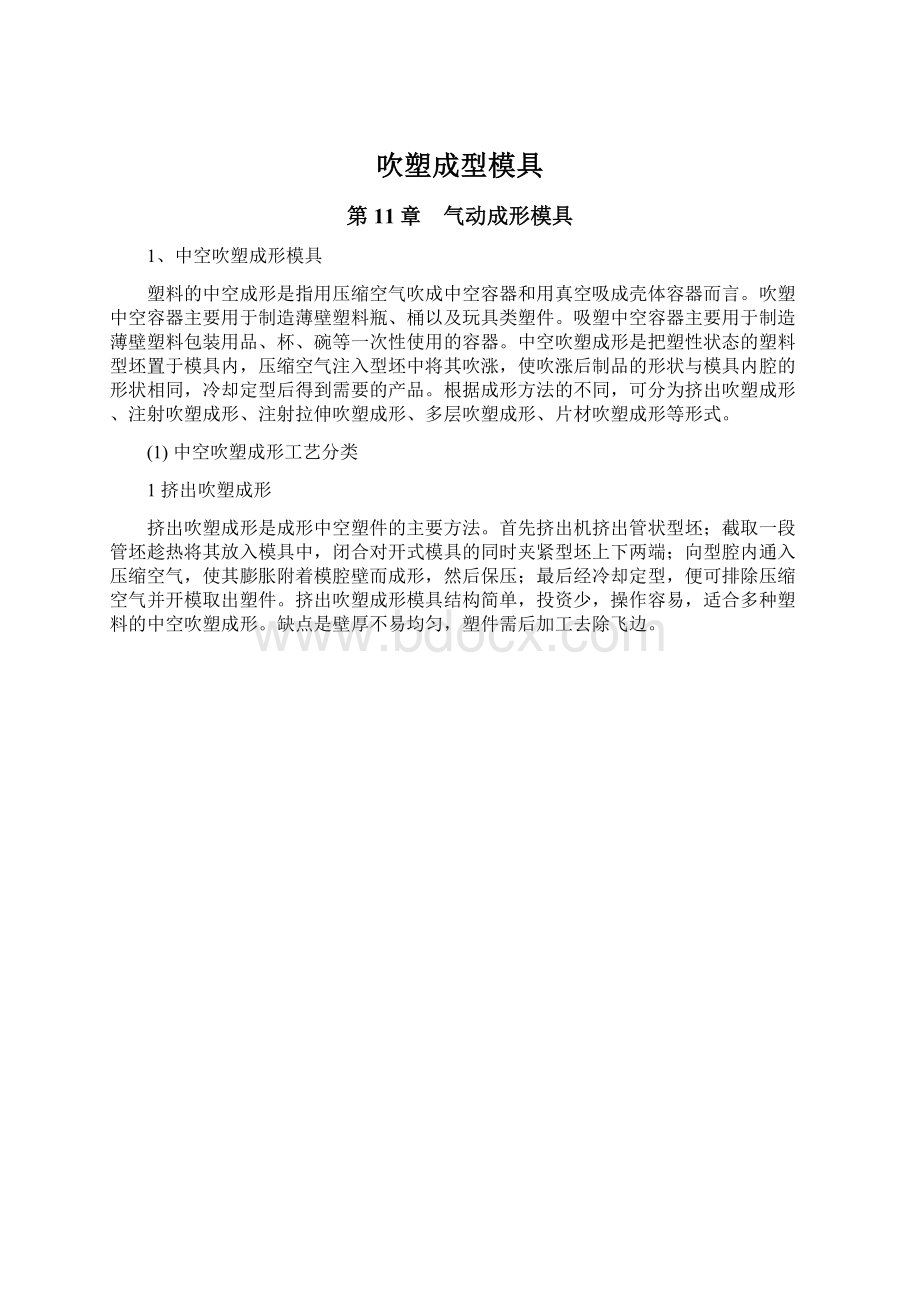
吹塑成型模具
第11章 气动成形模具
1、中空吹塑成形模具
塑料的中空成形是指用压缩空气吹成中空容器和用真空吸成壳体容器而言。
吹塑中空容器主要用于制造薄壁塑料瓶、桶以及玩具类塑件。
吸塑中空容器主要用于制造薄壁塑料包装用品、杯、碗等一次性使用的容器。
中空吹塑成形是把塑性状态的塑料型坯置于模具内,压缩空气注入型坯中将其吹涨,使吹涨后制品的形状与模具内腔的形状相同,冷却定型后得到需要的产品。
根据成形方法的不同,可分为挤出吹塑成形、注射吹塑成形、注射拉伸吹塑成形、多层吹塑成形、片材吹塑成形等形式。
(1)中空吹塑成形工艺分类
1挤出吹塑成形
挤出吹塑成形是成形中空塑件的主要方法。
首先挤出机挤出管状型坯;截取一段管坯趁热将其放入模具中,闭合对开式模具的同时夹紧型坯上下两端;向型腔内通入压缩空气,使其膨胀附着模腔壁而成形,然后保压;最后经冷却定型,便可排除压缩空气并开模取出塑件。
挤出吹塑成形模具结构简单,投资少,操作容易,适合多种塑料的中空吹塑成形。
缺点是壁厚不易均匀,塑件需后加工去除飞边。
图11-1挤出吹塑成型
1-挤出机头;2-吹塑模;3-管状型坯;4-压缩空气管;5-塑件
2注射吹塑成形
注射吹塑成形是用注射机在注射模中制成型坯,然后把热型坯移入中空吹塑模具中进行中空吹塑。
首先注射机在注射模中注入熔融塑料制成型坯;型芯与型坯一起移入吹塑模内,型芯为空心并且壁上带有孔;从芯棒的管道内通入压缩空气,使型坯吹涨并贴于模具的型腔壁上;保压、冷却定型后放出压缩空气,并且开模取出塑件。
经过注射吹塑成形的塑件壁厚均匀,无飞边,不需后加工,由干注射型坯有底,因此底部没有拼和缝,强度高,生产效率高,但是设备与模具的价格昂贵,多用于小型塑件的大批量生产。
图11-2注射吹塑成型
1-注塑机喷嘴;2-注塑型坯;3-空心凸模;4-加热器;5-吹塑模;6-塑件
3注射拉伸吹塑成形
图11-3注射拉伸吹塑成型
1-注塑机喷嘴;2-注塑模;3-拉伸芯棒(吹管);4-吹塑膜具;5-塑件
注射拉伸吹塑成形与注射吹塑成形比较,增加了延伸这一工序。
首先注射一空心的有底的型坯;型坯移到拉伸和吹塑工位,进行拉伸;吹塑成形、保压;冷却后开模取出塑件。
还有另外一种注射拉伸吹塑成形的方法,即冷坯成形法,型坯的注射和塑件的拉伸吹塑成形分别在不同设备上进行,型坯注射完以后,再移到吹塑机上吹塑,此时型坯已散发一些热量,需要进行二次加热,以确保型坯的拉伸吹塑成形温度,这种方法的主要特点是设备结构相对较简单。
4多层次吹塑成形
多层吹塑是指不同种类的塑料,经特定的挤出机头挤出一个坯壁分层而又黏结在一起的型坯,再经吹塑制得多层中空塑件的成形方法。
发展多层吹塑的主要目的是解决单独使用一种塑料不能满足使用要求的问题。
例如单独使用聚乙烯,但它的气密性较差,所以其容器不能盛装带有香味的食品,而聚氯乙烯的气密性优于聚乙烯,可采用外层为聚氯乙烯、内层为聚乙烯的容器,气密性好且无毒。
5片材吹塑成形
片材吹塑成形如图9.4所示。
将压延或挤出成形的片材再加热,使之软化,放入型腔,合模在片材之间通人压缩空气而成形出中空塑件。
图9.4a为合模前的状态,图9.4b为合模后的状态。
图11-4片状吹塑中空成型
(2)吹塑塑件设计
中空成形时,需要确定的是塑件的吹胀比、延伸比、螺纹、塑件上的圃角、支承面及外表面等。
1吹胀比
吹胀比是指塑件最大直径与型坯直径之比。
实践表明,吹胀比越大,塑料瓶的横向强度越高,但只能在一定的范围内。
型坯断面形状一般要做成与塑件的外形轮廓大体一致,如吹塑圆形截面的瓶子型腔截面应是管形;若吹塑方桶或矩形桶,则型坯断面应制成方管状或矩形管状;其目的是使型坯各部位塑料的吹胀情况趋于一致。
2延伸比
在注射拉伸吹塑中,塑件的长度与型坯的长度之比。
延伸比确定后,型坯的长度就能确定。
实验证明,延伸比越大的塑件,即相同型坯长度而生产出壁厚越薄的塑件,其纵向的强度越高。
也就是延伸比和吹胀比越大,得到的塑件强度越高。
在实际生产中,必须保证塑件的实用刚度和实用壁厚。
3螺纹
吹塑成形的螺纹通常采用梯形或半圆形的截面,而不采用细牙或粗牙螺纹,这是因为后者难以成形。
为了便于塑件上飞边的处理,在不影响使用的前提下,螺纹可制成断续状的.即在分型面附近的一段塑件上不带螺纹。
4圆角
吹塑成形甥件的角隅处不允许设计成尖角,如其侧壁与底部的交接部分一般设计成圆角,因为尖角难于成形。
对于一般容器的圆角,在不影响使用的前提下,圆角以大为好,圆角大壁厚则均匀,对于有造型要求的产品,圆角可以减小。
5塑件支撑面
在设计塑料容器时,不可以整个平面作为塑件支承面.应尽量减小底部的支承面,特别要减少结合缝作为支承面,因为切口的存在将影响塑件放置平稳。
6塑件的外表面
吹塑塑件大部分都要求外表面的艺术质量。
如雕刻图案、文字和容积刻度等。
有的要做成镜面等。
这就要求对模具的表面进行艺术加工。
其加工方式如下:
a)用喷砂做成缄面;
b)用镀铬抛光做成镜面;
c)用电铸方法铸成模腔壳体然后嵌入模体;
d)用钢材热处理后的碳化物组织形状,通过酸腐蚀做成类似皮革纹;
e)用涂覆感光材料后经过感光显影腐蚀等过程做成花纹。
成形聚氯乙烯塑件的模具型腔表面,最好采用喷砂处理过的粗糙表面,因为粗糙的表面在吹塑成形过程中可以存储一部分空气,可避免塑件在脱模时产生吸真空现象。
有利于塑件脱模,并且粗糙的型腔表面并不妨碍塑件的外观,表面粗糙程度类似于磨砂玻璃。
7塑件收缩率
通常容器类的塑料制品对精度要求不高.成形收缩率对塑件尺寸影响不大,但对有刻度的定容量的瓶子和螺纹制品,收缩率有相当的影响。
(3)吹塑模具设计
1上吹口式
2下吹口式
图11-上吹口模具结构图11-下吹塑模具结构
1-口部镶块;2-底部镶块;3、6-余料槽;1、6-余料槽;2-底部镶块;3-螺钉;
4-导柱;5-冷水管道4-冷水管;5-导柱;7-瓶颈(吹口)镶块
模具设计要点:
a)模口
模口在瓶颈板上.是吹管的人口,也是塑件的瓶口,吹塑后对瓶口尺寸进行校正和切除余料。
口部内径校正是由装在吹管外面的校正芯棒,通过模口的截断部分,同时进行校正和截断的。
b)夹坯口
夹坯口也称切口。
挤出吹塑过程中,模具在闭合的同时需将型口将余料切除,因此在模具相应部位要设置夹坯口。
切口部分的制造是关键部位,切口接合面的表面粗糙度值要尽可能地减小,热处理后要经过磨削和研磨加工,在大量生产中应镀硬铬抛光。
c)余料槽
型坯在刃口的切断作用下,会有多余的塑料被切除,它们将容纳在余料槽内。
余料槽通常设在切口的两侧,其大小应依型坯夹持后余料的宽度和厚度来确定,以模具能严密闭合为准。
d)排气孔(槽)
模具闭合后,型腔呈封闭状态,应考虑在型坯吹胀时,模具内原有空气的排出问题。
排气不良会使塑件表面出现斑纹、麻坑和成形不完全等缺陷。
为此,吹塑模还要考虑设置一定数量的排气孔(槽)。
一般开设在模具的分型面上和模具的“死角部位”(如在多面角部位或圆瓶的肩部)。
e)冷却
吹塑模具的温度一般控制在20-50度,冷却要求均匀。
f)锁模力
锁模力的大小应使两个半模闭合严密,应大于胀模力。
2、真空成形模具
(1)真空成形工艺分类
1凹模真空成形
首先将塑料板材置于模具上方将其四周固定.并进行加热软化,然后在模具下方抽真空,抽出板材与模具之间空隙中的空气,使软化的板材紧密地贴台在模具,当塑件冷却后,冉从模具下方充入空气,取出塑件。
用凹模成形法成形的塑件外表面尺寸精度较高,一般用于成形深度不大的塑件。
如果塑件深度很大时,特别是小型塑件,其底部转角处会明显变薄。
多型腔的凹模真空成形比相同个数的凸模真空成形节省原料,因为凹模模腔间距可以较近,用同样面积的塑料板,可以加工出更多的塑件。
图11-凹模真空成型
2凸模真空成形
有些要求底部厚度不减薄的吸塑件,可以用凸模真空成形,被夹紧的塑料板在加热器下加热软化,当加热后的片材首先接触凸模时,即被冷却而失去减薄能力。
当材料继续向下移动,一直到完全与凸模接触;抽真空开始,边缘及四周都由减薄而成形。
凸模真空成形多用于有凸起形状的薄壁塑件,成形塑件的内表面尺寸精度较高。
图11-凸模真空成型
3凹、凸模先后抽真空成形
凹凸模先后抽真空成形首先把塑料板紧固在凹模上加热,软化后将加热器移开,然后通过凸模吹人压缩空气,而凹模抽真空使塑料板鼓起,最后凸模向下插入鼓起的塑料板中并且从中抽真空,同时凹模通人压缩空气,使塑料板贴附在凸模的外表面而成形。
该成形方法,由于将软化了的塑料板吹鼓,使板材延伸后再成形,故壁厚比较均匀,可用成形深型腔塑件。
图11-凹凸模先后抽真空成型
4吹泡抽真空成形
首先将片材加热,然后向密闭箱内送压缩空气。
热片材向外吹涨,再将凸模升起,与片材之间形成密闭状态;最后由凸模上的气孔抽真空,利用外面的大气压力使它成形。
图11-吹泡真空成型
5辅助凸模真空成形(柱塞下推真空成形)
图11-下向真空成型
辅助凸模真空成形分为下向真空成形和上向真空成形。
下向真空成形首先将固定于凹模的塑料板加热至软化状态;接着移开加热器,用辅助凸模将塑料板推下,这凹模里的空气被压缩,软化的塑料板由于辅助凸模的推力和型腔内封闭的空气移动而延伸;然后凹模抽真空成形。
(2)真空成形塑件设计
真空成形对于塑件的几何形状、尺寸精度、塑件的深度与宽度之比、圆角、脱模斜度、加强肋等都有具体要求。
1塑件的几何形状和尺寸要求
用真空成形方法成形塑件,成形后冷却收缩率较大,很难得到较高的尺寸精度。
一般凸模真空成形时,塑件内部尺寸精确;而凹模真空成形时,塑件外部尺寸精确。
2塑件的深度H与宽度(或直径)D之比
塑件的深度H与宽度(或直径)D之比称为引伸比,引伸比在很大程度上反映了塑件成形的难易程度。
引伸比越大,成形越难。
引伸比和塑件的均匀程度有关,引伸比过大会使最小壁厚处变得非常薄,这时应选用较厚的塑料来成形。
引伸比和塑料品种、成形方法有关。
3圆角
塑件设计时应使联接处圆滑过渡,圆角半径不小于型坯厚度。
4斜度
即工艺倾斜面,以便从模具中取出制品。
5加强肋
加强肋可减少型坯厚度,缩短加热时间,降低制品成本。
加强肋应沿制品外形或面的方向设计。
(3)真空成形模具设计
1抽气孔
抽气孔大小应适合成形塑件的需要,一般对于流动性好、厚度小的塑料板材,抽气孔要小,反之则大。
2型腔尺寸
该成形模具型腔尺寸计算方法与注射模型腔尺寸计算相同,应该考虑塑料收缩率和成形模具的精度。
3、压缩空气成形模具
(1)压缩空气成形工艺
塑件成形过程是将塑料板材置十加热板和凹模之间,固定加热板,塑料板材只被轻轻地压在模具刃口上,然后,在加热板抽出空气的同时,从位于型腔底部的空气口向型腔中送入空气,使被加工板材紧贴加热板;这样塑料板很快被软化,达到适合于成形的温度。
这时加强从加热板进出的空气,使塑料板材逐渐贴紧模具。
与此同时,型腔内的空气通过其底部的通气孔迅速排出,最后使塑料板紧贴模具。
待板材冷却后,停止从加热板喷出压缩空气,再使加热板下降,对塑件进行切边;在加热板回升的同时,从型腔底部进入空气使塑件脱模后,取出塑件。
图11-压缩空气成型工艺过程
压缩空气成形的方法与真空成形的原理相同,都是使加热软化的板材紧贴模具成形。
所不同的是对板材所施加的成形外力由压缩空气代替抽真空。
在真空成形时.很难达到对板材施加0.lMPa以上的成形压力。
而用压缩空气时,可对板材施加lMPa以上的成形压力。
由于成形压力很高,因而用压缩空气时可以获得充满模具形状的塑件及深腔的塑件。
(2)压缩空气成形模具设计
压缩空气成形用的模具结构,它与真空成形模具的不同点是增加了模具型刃,因此塑件