汽车开发设计流程及各阶段工作内容.docx
《汽车开发设计流程及各阶段工作内容.docx》由会员分享,可在线阅读,更多相关《汽车开发设计流程及各阶段工作内容.docx(9页珍藏版)》请在冰豆网上搜索。
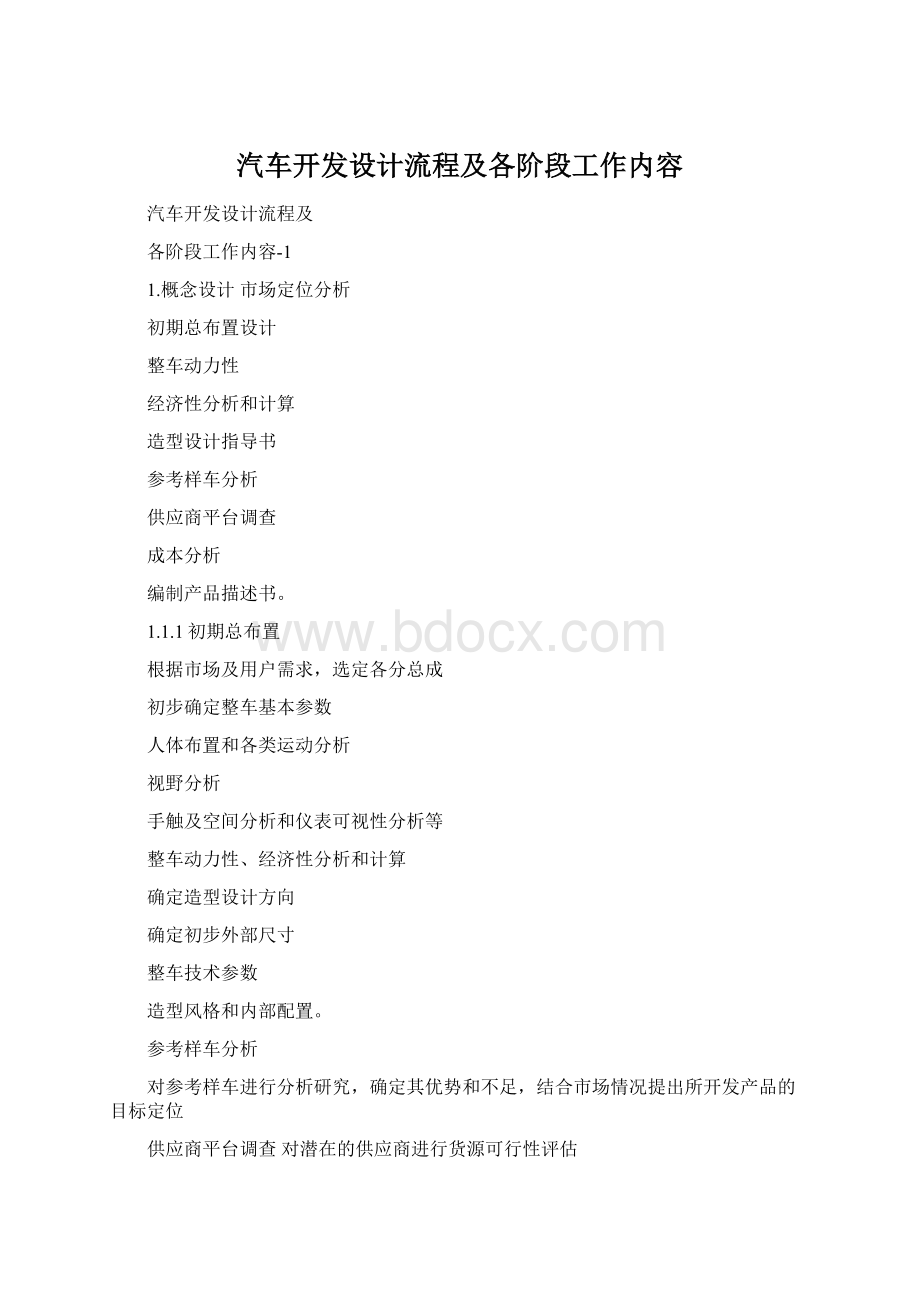
汽车开发设计流程及各阶段工作内容
汽车开发设计流程及
各阶段工作内容-1
1.概念设计市场定位分析
初期总布置设计
整车动力性
经济性分析和计算
造型设计指导书
参考样车分析
供应商平台调查
成本分析
编制产品描述书。
1.1.1初期总布置
根据市场及用户需求,选定各分总成
初步确定整车基本参数
人体布置和各类运动分析
视野分析
手触及空间分析和仪表可视性分析等
整车动力性、经济性分析和计算
确定造型设计方向
确定初步外部尺寸
整车技术参数
造型风格和内部配置。
参考样车分析
对参考样车进行分析研究,确定其优势和不足,结合市场情况提出所开发产品的目标定位
供应商平台调查对潜在的供应商进行货源可行性评估
评价他们在满足质量、供货能力及开发水平的前提下提供总成和部件的能力
识别价格及质量具有相对竞争力的供应商,以满足产品定位的要求。
在供应商和制造者之间建立信息沟通
成本分析
确定各系统和整车的目标成本。
编制产品描述书
描述书作为产品开发的依据文件,将所要开发的产品项目的背景、目标、车型规划、总成选择、装备、进度等进行详细描述。
1.2团队
一支有着丰富汽车理论知识和设计经验的优秀团队,熟知中国汽车配套资源及现有车型。
以敏锐的眼光洞察中国的汽车市场,能很好的把握中国汽车发展的潮流。
1.3市场定位
从消费者调查、市场调研、竞争对手分析及,企业制造能力分析来确定产品的市场定位。
2.汽车造型
分析造型设计任务书
收集和整理相关资料并进行样车准备
工程与造型的契合
确定设计理念,提出设计方案
阶段评审
初步草图设计方向性评审
细化效果图草图设计设计评审
效果图设计
效果图评审
效果图修改及提交
根据客户的意见修改效果图
效果图批准
进入零部件造型的细节设计阶段
团队要求:
具有锐意创新的精神,透过设计的表面来理解设计本身所代表的设计师对生活形态和消费心理的了解,赋予设计更多的实际意义。
高雅的艺术品味、丰富的设计经验、全面的汽车相关专业知识以及衍生的材料学、流体力学、热能学、人体工程学、社会学、环保学等众多方面知识。
对消费者及成本的了解以及极富魅力的创意思维使他们不断推陈出新,创造出更符合国际趋势和品牌定位的作品。
设计部门承担整车造型、总体布置及整车集成,内容涵盖了从美学表面的质感、动感、内外饰的创意、计算机辅助曲面设计到产品外型的最终数据发布。
高级技工的丰富经验成为专家系统,我们不再是中国汽车行业中的“设计迁就于生产”,而是通过高超的技术去完善汽车设计,突破本土“工与艺”不能完美结合的瓶颈
3.三维造型
三维造型室以评审通过的效果图为依据构建及渲染三维数字模型。
充分利用三维造型软件以及虚拟现实和视景仿真技术,实现全数字化的造型设计流程,以及与工程部门的无缝连接。
旨在模拟控制产品各个角度的造型状态,多维评价、推敲造型方案,向工程结构设计部门提供第一轮造型信息,供结构工程部门分析造型实施的可行性。
同时,渲染出的动画效果供市场部门进行前期市
场分析。
4.油泥模型制作
胶带图绘制
评审
油泥模型骨架准备
油泥模型制作
油泥模型评审
油泥模型改制
结构和工艺性评审
油泥模型完善
油泥模型批准
油泥模型喷漆
油泥模型展示
油泥模型按要求销毁或存档
5.数字表面化
三维扫描:
采用先进的ATOSII设备进行三维扫描。
ClassA建模:
获取点云数据后,根据客户要求,可提供快速表面重建或ClassA表面。
模型铣制:
相对传统的人工粗刮油泥技术,在保证满足工程要求的同时,极大的提高了工作效
率。
模型验证:
在模型数据化或生成A级表面后,使用五轴数控铣床,根据数学模型的数据,在专用的树脂材料模型上,再现数学模型的表面。
达到验证表面数据准确性,确保数学模型与原始模型数据的一致性。
6.样车制作
概念车制造
工程验证样车
零部件试制加工
车辆设计性改装
整车使用说明书验证
螺钉车试装
主模型制造
展示用模型
展览样车
数字成型加工
各种模型制作
6.2概念样车
制作概念样车,其目的在于验证产品概念,是概念设计的实物结果。
概念样车也包含在产品开发早期用以验证结构和功能的可行性,同时为后续工作提供必要的信息输入。
区别于量产车,概念样车通常在没有充分的实物零件及工程信息的条件下,由手工制作完成,制作过程中会使用大量的“模型”零件。
6.3工程样车
用以进行整车和系统工程设计验证、耐久性和碰撞验证,采用硬工装和软工装制造的钣金件装配的样车。
制作工程样车的目的在于:
1)验证工程设计;2)验证工艺可行性;3)验证供应商的开发结果;4)系统开发与验证;5)设计改进;6)风险评估;7)可靠性验证。
制造工程样车要求所使用的每一零件必须达到图纸的尺寸和性能要求。
专用于白车身验证的分析手段。
白车身数模协调完成后,其理论尺寸与形状几乎没有误差,然而实际冲压零件不可避免地存在各种各样的误差,如何将这些存在误差的零件焊装成车身?
如何将零件的累计误差合理地分配到一些不重要的位置?
如何将有误差的零件与其他非白车身零件协调装配?
这些则要求设计部门必须通过实物进行分析,并提供合理的解决方案。
螺钉车身的装配分析完全在精确测量及数模的指导下进行,其解决方案仅依赖于工程技术人员的实际经验。
特别值得注意的是,测量本身也会带来误差,只有消除所有这些影响,才可制造出完美的产品。
6.5展示样车
样车制造部门,有着多年的制作及参加国际车展样车的经验,样车制作水平为国内一流。
6.6试验支持
对样车的整车道路试验提供全面的试验支持。
包括试验报告分析、样车维护,发现样车在部件配合、外观质量、功能、尺寸方面的缺陷及装配性、维修性、整车重量等方面的问题,确定需要进行设计改进的方面。
白车身工程设计
7.1白车身正向工程设计
按照市场及用户新车型开发的需求,完成车身结构设计;按照市场及用户年度换型的需求,完成产
品的更新换代。
7.2白车身逆向工程设计
按照用户需求,完成整车或零部件的逆向建模。
7.3白车身工艺分析
731冲压成型工艺分析
借助先进的冲压成型分析软件,在车辆零件具体设计阶段就考虑它的冲压成型性,可以及时发现问题,指导设计修改,避免在模具制造后反复修改模具,这样可大大地降低设计成本,缩短开发周期
732装焊工艺分析及优化制造团队与设计团队必须在产品开发的早期达成共识,工程设计应充分吸收制造工厂的意见,在设计阶段对装焊定位、夹紧分析及优化,能有效的降低产品的制造风险,节省时间并降低成本。
733车身密封降噪结构设计
在车身被动降噪的过程中借助先进声场和声强的检测仪器,完成主噪音源的定位分析。
有效地消减主噪音传播,从而降低驾驶室的噪音。
734车身运动件的几何运动学分析
在设计初期借助三维软件对运动机构进行运动仿真分析,可有效检查运动中的死点和干涉,保证运动机构布置合理。
735车身附件设计
不仅具备自主开发能力,而且可以与供应商紧密合作,联合开发符合技术要求的车身附件产品。
内饰工程设计
8.1内饰工程设计
仪表板布置及其结构设计
座椅/安全带布置
硬内饰结构设计
顶棚、地毯以及隔热垫和阻尼垫的结构设计
汽车空调
内饰工程部门可按客户要求进行新内饰的匹配设计、结构设计和现有内饰的改进设计。
8.2内饰改型设计
采用逆向设计理念,将内饰零件和周边钣金零件复原成3D模型。
以3D模型为参考,在不改变与
周边零件配合的前提下,按客户要求进行设计改进。
在满足整车总布置和造型设计要求的前提下,充分利用车内空间,并保证内饰结构的功能性。
外饰工程设计
前后保险杠
顶置行李架
装饰彩条
外置备胎
前格栅
标牌及特种标志和灯具
针对客户的不同要求和概念设计的规划,依据客户的生产纲领,对客户的各种车型外部件进行工
程设计。
提供从造型到工程设计的系统服务和根据客户提供的外饰件进行逆向工程设计
底盘工程设计
底盘总布置
运动部件的运动分析
制动系统的匹配及零部件选型和设计
悬挂系统匹配及零部件选型和设计
转向系统匹配及零部件选型和设计
车轮和轮胎设计的匹配和选型
系统和总成设计计算书
底盘工程主要负责车架设计、悬架系统设计、制动系统设计、转向系统设计
悬架系统设计
兼顾舒适性、行驶平顺性、操纵稳定性等设计出具有领先水平的独立悬架和非独立悬架,解决现
有车型悬架存在的问题。
在著名制动专家的亲自参与和指导下编制的制动性能分析计算程序,以变制动力为基础,使得计算条件更接近实际工况,可以在短时间内提出符合法规的制动力分配方案。
10.4转向系统设计
进行内外转向轮的转角关系分析、梯形运动分析、车轮跳动分析、车轮跳动转向分析、转向系统可靠性分析等。
电器工程设计
11.1整车电器安全性和使用性计算、校核及优化
11.2整车及分系统电器原理图设计
11.3CAN总线系统设计和开发
11.4系列电子控制模块的设计和开发(EBTC、ATS、ACE、APS、BLIS等)
11.5电器零部件设计和开发
11.6三维线束布置及二维线束图设计
11.7照明系统设计和开发
11.8防盗系统设计和开发
11.9车载信息集成系统设计和开发
11.10车载娱乐系统设计和开发
11.12展览样车电器系统设计、制造及安装调试
11.13电器零部件失效分析及解决方案
电器设计部为新开发车型进行电气系统匹配设计,对现有系统进行改进设计,设计涵盖轿车、货车、客车、越野车、多功能车乃至牵引车、电动车。
动力总成工程设计
12.1动力总成工程设计
12.1.2发动机舱数模12.1.3发动机舱验证模型
12.1.4动力总成悬置设计、计算
12.1.5发动机冷却、进排气、燃油系统设计
12.1.6发动机、离合器、变速器、分动器、驱动桥选型、匹配及与供应商联合设计
12.1.7传动系统部件设计
12.2发动机工程设计
选配性价比高的发动机,利用先进手段进行发动机附件优化配置,解决进气消声、排气消声、三
元催化器匹配等方面的问题。
模型技师具备精湛的技艺及相当的专业技术知识水准,可建立发动机实物模型,既可验证工程设
计的正确性,也可以启发工程师的设计概念,同时便于与客户及供应商沟通。
12.3传动系统工程设计
经过深入分析,选配性价比高的离合器、变速器、分动器、驱动桥;可与供应商联合设计开发满
足要求的各总成;通过前期NVH分析有效控制传动系统振动与可靠性。
CAE模拟与分析
13.1在汽车设计的各个阶段,借助计算机辅助工程(CAE)分析手段对工程设计进行虚拟验证和分析,从而大大减少了汽车研发的成本和周期。
在外国专家的指导下,根据国外著名整车厂CAE
分析规范,结合目前国内的实际条件,我们形成了一套完整的CAE分析规范和基础数据库。
13.2整车和零部件的结构动力学分析
13.2.1零部件的强度分析
考核各结构件是否满足强度的要求,并进行基于强度约束的结构优化。
分析零部件的结构刚度,并进行基于刚度约束的结构优化。
如分析白车身的弯曲刚度和扭转刚
度,按照行业标准进行车身刚度的评价。
1323整车模态分析
通过模态分析方法分析出结构在某一易受影响的频率范围内的各阶模态特性,预测结构在此频率范围内的实际振动响应
13.2.4响应分析
在带内饰的整车环境下,分析方向盘、座椅、地板和顶篷以及其他设计所关心的结构的振动情况。
13.3整车被动安全性分析
车辆被动安全性分析用于模拟汽车的正面碰撞、侧面碰撞、追尾碰撞、动态翻滚等事故情况,对车辆结构的耐撞性及其乘员约束系统的有效性进行分析,并对车辆的被动安全法规符合性给予评价,从而有效提高车辆设计的安全性,同时大幅减少实