最新塑料模具课程设计说明书.docx
《最新塑料模具课程设计说明书.docx》由会员分享,可在线阅读,更多相关《最新塑料模具课程设计说明书.docx(29页珍藏版)》请在冰豆网上搜索。
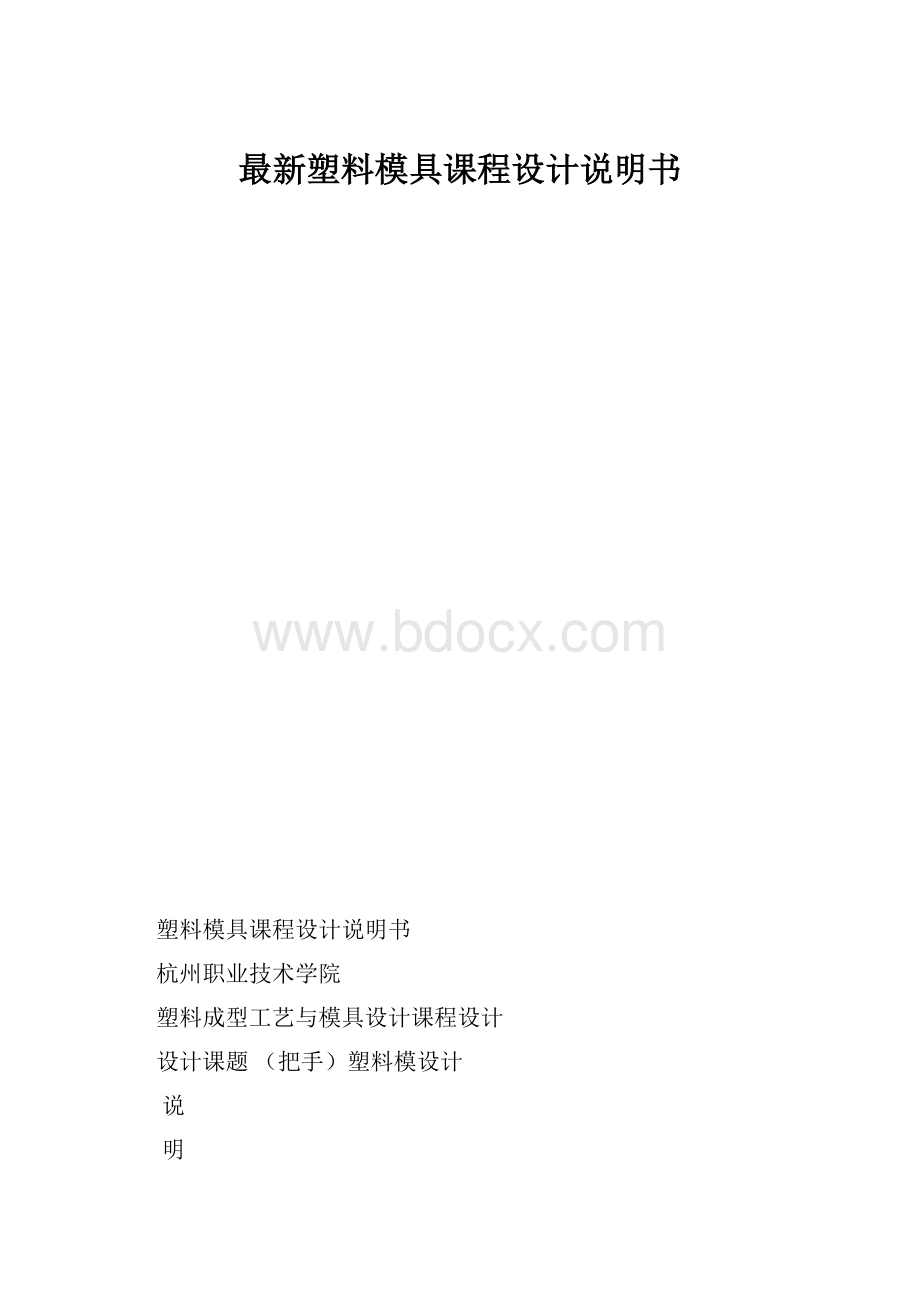
最新塑料模具课程设计说明书
塑料模具课程设计说明书
杭州职业技术学院
塑料成型工艺与模具设计课程设计
设计课题(把手)塑料模设计
说
明
书
班级:
模具1221班
学生:
王国林
学号:
17号
指导教师:
郭伟刚
2013年12月11日
材料:
ABS
二维图
三维图
大批生产,精度MT5。
要求:
一模多腔,侧浇口结构设计
一.塑件成型工艺分析
1.1材料..................................................................................................
1.2塑件的结构工艺性..........................................................................
2.分型面位置的分析和确定
2.1分型面的选择原则.........................................................................
2.2分型面选择方案.............................................................................
3.塑件型腔数量及排列方式的确定
3.1数量.................................................................................................
3.2排列方式.........................................................................................
四.注射机的选择和有关工艺参数的校核
4.1所需注射量的计算..........................................................................
4.2塑件和流道凝料在分型面上的投影面积及所需锁模具、力的计算
4.3注射机型号的选定..........................................................................
4.4有关工艺参数的校核......................................................................
五.浇注系统的形式选择和截面尺寸的计算
5.1主流道的设计...................................................................................
5.2冷料穴的设计...................................................................................
5.3分流道的设计...................................................................................
5.4浇口设计............................................................................................
5.5浇注系统的平衡................................................................................
6.成型零件的设计及力学计算
6.1成型零件的结构设计........................................................................
6.2成型零件工作尺寸计算....................................................................
6.3成型零件的强度及支撑板厚度计算................................................
7.模架的确定和标准件的选用..................................................
8.导向机构的设计......................................................................
9.脱模机构的设计......................................................................
10.温度调节系统的设计..............................................................
11.模具总体结构......................................................................
参考文献
一,塑料成型工艺性分析
1.1材料:
ABS(丙烯酯--丁二烯--苯乙烯共聚物)
英文名:
AcrylonitrileButadieneStyrene
ABS的性能分析:
ABS是一种高强度改性PS(聚苯乙烯),由丙烯酯,丁二烯和苯乙烯三种组元以一定比例共聚而成。
比重:
1.05克/立方厘米
燃烧鉴别方法:
连续燃烧、蓝底黄火焰、黑烟、浅金盏草味
溶剂实验:
环已酮可软化,芳香溶剂无作用
干燥条件:
80-90℃2小时
成型收缩率:
0.4-0.7%
模具温度:
25-70℃(模具温度将影响塑件光洁度,温度较低则导致光洁度较低)
融化温度:
210-280℃(建议温度:
245℃)
成型温度:
200-240℃
注射速度:
中高速度
注射压力:
500-1000bar
特点:
1、综合性能较好,冲击强度较高,化学稳定性,电性能良好.
2、与372有机玻璃的熔接性良好,制成双色塑件,且可表面镀铬,喷漆处理.
3、有高抗冲、高耐热、阻燃、增强、透明等级别。
4、流动性比HIPS差一点,比PMMA、PC等好,柔韧性好。
5、用途:
适于制作一般机械零件,减磨耐磨零件,传动零件和电讯零件.
6、同PVC(聚氯乙烯)一样在屈折处会出现白化现象。
成型特性:
1.无定形料,流动性中等,吸湿大,必须充分干燥,表面要求光泽的塑件须长时间预热干燥80-90度,3小时.
2.宜取高料温,高模温,但料温过高易分解(分解温度为>270度).对精度较高的塑件,模温宜取50-60度,对高光泽.耐热塑件,模温宜取60-80度.
3、如需解决夹水纹,需提高材料的流动性,采取高料温、高模温,或者改变入水位等方法。
4、如成形耐热级或阻燃级材料,生产3-7天后模具表面会残存塑料分解物,导致模具表面发亮,需对模具及时进行清理,同时模具表面需增加排气位置。
1.2塑件的结构工艺性
1.2.1塑件的尺寸精度分析
该零件的尺寸精度无特殊要求,所有尺寸均为自由尺寸,按要求IT7精度查询公差。
1.2.2塑件表面质量分析
对该零件表面没有特殊要求,一般情况下,外表面要求光洁,表面粗糙度Ra可取0.8um,没有特殊要求的塑件内部表面粗糙度Ra可取3.2um。
1.2.3塑件的工艺分析
1)该塑件为ABS的空心球柄,外形为光滑的球面,外表光滑,无注射缺陷,无翘曲变形,外观质量要求较高,尺寸精度要求相对较低。
因此在模具设计和制造时要有精密的定位措施和良好的加工工艺,以保证空心球各尺寸吻合和形状的逼真。
2)无侧凹侧孔侧槽,结构简单,易于用模具成型。
由于中间管较长故设计脱模机构时需采用特殊脱模机构。
3)脱模斜度:
该塑件厚度约为2mm,由于该塑料的收缩率较小,形状比较简单,高度较大,孔隙较深,又由查表的其型腔脱模斜度20°—45°,型芯脱模斜度为25°—45°。
1.2.4塑件的生产批量
该塑件的生产类型为大批量生产,因此在模具设计中要提高塑件的生产率,倾向于多型腔,高寿命,自动脱模模具,以便降低生产成本。
1.3注射工艺参数
表1-2[1]
注射成型机类型
螺杆式
转速(r/min)
30~60
料筒温度(℃)
中段180~200
喷嘴温度(℃)
150~180
模具温度(℃)
30~60
喷嘴形式
直通式
注射压力(MPa)
70~100
保压力(MPa)
40~50
注射时间(s)
0~5
保压时间(s)
15~60
成型周期(s)
40~140
冷却时间(s)
15~60
第2章分型面位置的分析和确定
2.1分型面的选择原则
①分型面的选择应便于塑件脱模和简化模具结构,选择分型面应尽量使塑件开模时留在动模;
②分型面应尽可能选择在不影响外观的部位,并使其产生的溢料边易于消除和修整;
③分型面的选择应保证塑件尺寸精度;
④分型面选择应有利于排气;
⑤分型面选择应便于模具零件的加工;
⑥分型面选择应考虑注射机的规格。
2.2分型面选择方案
根据上述选择原则和该塑件的形状,选择分型面方案如下,如图1-1所示:
图2-1
分型面与开模方向平行,置于最大截面处,塑件包紧在动模型芯上。
利用推出机构易于推出,开模行程合理,模具结构简单,制造方便,塑件成型精度高,能够满足要求。
经分析可知,该模具结构简单,塑件成型精度可靠。
第3章塑件型腔数量及排列方式的确定
3.1数量
分型面确定以后,就需要考虑是采用单型腔模还是多型腔模。
一般来说,大中型塑件和塑件精度要求较高的小型塑件优先采用一模一腔的结构。
但对于精度要求不高的小型塑件(没有配合精度要求),形状简单,又是大批量生产时,若采用多型腔模可使生产率大为提高且降低成本。
结合塑件的批量、质量要求、塑料的品种形状尺寸、塑件的生产成本及所选用的技术要求和规范,本套模具选择一模四腔。
3.2排列方式
多型腔模具设计的重要问题之一就是浇注系统的布置方式。
由于型腔布置方式与浇注系统布置密切相关,因而型腔的排布在多型腔模具设计中应加以考虑:
(1)型腔的布置应使每个型腔都通过浇注系统从总压力中均等的分得所需要的足够的压力;
(2)型腔与主流道之间的距离应尽可能的短,同时采用平衡的流道和合理的尺寸以及均匀分布的冷却系统等。
综上所述,采用的布置如图3-1所示:
图3-1
第4章注射机的选择和有关工艺参数的校核
4.1所需注射量的计算
(1)塑件质量和体积的计算
对于该设计,用户提供了塑件样图,据此进行三维建模,对其分析得:
塑件体积V1≈17.55cm3
塑件质量m1=ρV1≈1.05×17.55=18.43g
(2)浇注系统凝料体积的估算
可按塑件体积的0.6倍计算,由于该模具采用一模四腔,所以浇注系统凝料体积为V2=4V1×0.6=4×17.55×0.6=42.12cm3
(3)该模具一次注射所需塑料
体积V0=4V1+V2≈4×17.55+42.12=112.32cm3
质量m0=ρV0≈1.05×112.32=117.94g
4.2塑件和流道凝料在分型面上的投影面积及所需锁模力的计算
流道凝料(包括浇口)在分型面上的投影面积为A2,在模具设计前是个未知数,根据多型腔模的设计分析,A2是每个塑件在分型面上的投影面积A1的0.2~0.5倍。
因此可用0.35A1来进行计算,所以:
A=nA1+A2=nA1+0.35nA2=1.35nA1
A1=πR2/4=3.14×20×20/4=314mm2
A=1.35×4×314=1695.6mm2
则Fm=A×P型=1695.6×25=42390N=42.39KN
4.3注射机型号的选定
由上述数据查阅参考文献[1]附录6及参考文献[3]选注射机型号为XS-ZY-250,基本参数如表4-1所示:
表4-1
螺杆直径
50mm
额定注射量
250mm3
额定注射压力
130MPa
锁模力
1800KN
最大成型面积
550cm2
最大开模行程
500mm
顶出行程
100mm
最大模具厚度
350mm
最小模具厚度
200mm
螺杆转速
25-89r/min
定位孔直径
Ø125+0.006
推出孔径
Ø40
两侧孔距
280mm
喷嘴球半径
SR18mm
孔直径
Ø4
4.4有关工艺参数的校核
(1)按注射机的最大注射量校核型腔数量
公式4-2[3]
式中K—注射机最大注射量的利用系数,一般取0.8;
Vn—注射机允许的最大注射量cm3;
V2—浇注系统所需塑件的体积cm3;
V1—单个塑件的体积cm3。
左边=4,右边=
,满足要求。
(2)注射量的校核
根据生产经验,注射机的最大注射量是其允许最大注射量的80%,由参考文献[3]式4-4有:
nV1+V2≤80%Vn
式中Vn—注射机允许的最大注射量cm3;
V2—浇注系统所需塑件的体积cm3;
V1—单个塑件的体积cm3。
左边=112.32cm3,右边=80%×250=200cm3,满足要求。
(3)塑件在分型面上的投影面积与锁模力的校核
计算投影面积与锁模力远小于所选注射机的投影面积和锁模力,满足要求。
(4)注射压力的校核
所选注射机额定注射压力为130MPa,该塑件的注射压力为70-100MPa,由于选用的是螺杆式注射机,其注射压力的传递比柱塞式要好,同时HDPE流动性好,因此注射压力选用80MPa,注射应满足:
Pmax≥k’P0
式中max—注射机额定注射压力;
P0—注射成型时所用的注射压力;
k’—安全系数,常取k’=1.25~1.4。
左边=130MPa,右边=1.25×80~1.4×80=100~112MPa,满足要求。
(5)模具厚度的校核
模具厚度指模板闭合后达到规定锁模力时,动模板与定模板之间的距离。
厚度H应满足:
Hmin≤H≤Hmax
对于所选注射机,式中Hmin=200mm,Hmax=350mm,
厚度为H=40+20+25+25+114+20mm=243mm,满足要求。
(6)开模行程的校核
XS-ZY-250式注射机为全液压式注射机,注射机最大开模行程与模具厚度有关,必须满足:
Sk-Hm≥S
式中Sk—注射机的最大开模行程;
Hm—模具闭合高度;
S—开模距离。
对于单分型面,S=H1+H2+(5~10)=64+62+8mm=134mm,
即Sk≥Hm+S=243+134=377,满足要求。
综上所述,注射机选择合理,能够满足使用要求。
第5章浇注系统的形式选择和截面尺寸的计算
所谓浇注系统是指注射模中从主流道的始端到型腔之间的熔体进料通道。
浇注系统可分为普通流道浇注系统和无流道浇注系统两类。
普通浇注系统由主流道、分流道、浇口、冷料穴四部分组成。
浇注系统的作用是使来自注射模喷嘴的塑料熔体平稳而顺利的充模、压实、保压。
5.1主流道的设计
主流道是浇注系统中从喷嘴与模具相接触部位开始,到分流道为止的塑料熔体的流动通道,属于从热的塑料熔体到相对较冷的模具中的过渡阶段,因此它的形状和尺寸非常重要。
主流道部分在成型过程中,其小端入口处与注射机喷嘴及一定温度和压力的塑料熔体冷热交换的反复接触,属于易损件,对材料的要求高,因而模具的主流道部分常设计成可拆卸更换的主流道衬套式—浇口套。
主流道部分尺寸如下:
(1)主流道小端直径d=注射机喷嘴直径+(0.5~1)
=4+0.5mm=4.5mm;
(2)主流道球面半径SR=注射机喷嘴球面半径+(1~2)
=18+1mm=19mm;
(3)球面配合高度h=3~5,取h=3mm;
(4)主流道锥角α=2°~6°,取α=4°;
(5)主流道长度L尽量≤60mm,取L=40-3mm=37mm;
(6)主流道大端直径D=d+2Ltg
=7.15mm,取D=
7.2mm。
主流道衬套及定位圈的固定形式如图5-1所示:
图5-1
5.2冷料穴的设计
冷料穴的作用是贮存两次注射间隔而产生的冷料及熔体流动前锋冷料,以防止熔体冷料进入型腔。
冷料穴一般设置在主流道的末端,当分流道较长时,在分流道的末端有时也设冷料穴。
同时冷料穴兼有分模时将主流道凝料从主流道衬套中拉出并滞留在动模一侧。
本设计采用推板脱模机构,采用代球形头的冷料穴,适用于弹性较好的ABS,结构如图5-2所示:
图5-2
5.3分流道的设计
(1)分流道的布置形式
分流道在分型面上的布置与前面所述型腔排列密切相关,有多种不同的形式,但应遵循两个方面的原则:
一是排列紧凑,缩小模板尺寸,二是流程尽量短,锁模力均匀。
该流道布置采用平衡式,其布置形式如图5-3所示即为最佳:
图5-3
(2)分流道的长度
长度应尽可能短,结合模具尺寸结构,取分流道长度L=20mm。
(3)分流道形状及尺寸
圆形分流道截面积虽然效率高,但其是以分型面为界分成两半进行加工才利于凝料脱出,因而其加工工艺性不佳,不予采用。
许多模具设计采用梯形截面,加工工艺性好,且塑料熔体的热量散失,流动阻力均不大,一般采用如下公式5-5,5-6[3]确定截面尺寸的大小,即:
式中B—梯形大底面的宽度,mm;
m—塑件质量,g;
L—分流道的长度,mm;
H—梯形高度,mm。
注:
上述公式的适用范围,塑件厚度在3mm以下,质量小于200g且B的计算结果在3.2~9.5mm才合理。
符合公式的应用范围,可以采用。
其截面形状尺寸如图5-4所示:
图5-4
(4)分流道表面粗糙度
分流道表面不要求太光洁,表面粗糙度常取Re=1.25~2.5um,这可增加对外层塑料熔体流动阻力,使外层塑料冷却塑料皮层固定形成绝热层,有利于保温。
(5)分流道与浇口连接形式
分流道与浇口采用斜向与圆弧连接,这样有利于塑料的流动与填充,防止塑料流动产生反压力,消耗动能。
5.4浇口设计
浇口是连接流道与型腔之间的一段细短通道,是浇注系统的关键部分,起着调节控制料流速度,补料时间及防止倒流等作用。
浇口的形状.尺寸.位置对塑件的质量产生很大的影响。
(1)类型及位置的确定
该模具是中小型塑件的多型腔模具。
有塑料顾问分析可知,选择在SR20与分型面交界处合理。
类型选用常用的侧浇口,这类浇口加工容易,修整方便,并且可以根据塑件的形状特征灵活选择进料位置。
(2)浇口的结构尺寸经验数据
矩形侧浇口的大小由其厚度,宽度和长度决定公式6-5,6-6[1]
h=nt
b=
式中h—侧浇口厚度,mm;
B—侧浇口长度,mm;
T—塑件壁厚,mm;
n—与塑料品种有关的系数,查得n=0.6;
A—塑件外表面积,mm2。
代入数据得:
h=0.6×2.5mm=1.5mm;
b=1.5mm;
浇口长度取L=1.0mm。
5.5浇注系统的平衡
对于该模具,从主流道到各个型腔和分流道的长度相等,形状及截面尺寸相同,各个浇口也相同,浇注系统显然是平衡的。
第6章成型零件的设计及力学计算
本设计中成型零件就是球柄外壁的型腔和筋板处型芯及中间深孔处型芯。
6.1成型零件的结构设计
(1)型腔:
型腔采用整体式,用机械加工方法易于成型,结构简单,牢固不易变形。
塑件无拼接缝痕迹,适用于简单形状的塑件。
(2)型芯:
球内壁八个筋板的成型采用八个小型芯,考虑到制造安装准确方便,其底部采用圆形。
中间深孔由于长度较大,脱模时采用推管推出,需单独设置型芯。
这样八个小型芯的内孔即为深孔的型腔,计算考虑时需特别注意。
6.2成型零件工作尺寸计算
成型零部件工作尺寸计算有平均值法和公差带法两种。
本设计为便于计算采用平均值法。
塑件尺寸按一般精度取6级,除中心孔已注公差外,在计算之前,将各个尺寸按“入体“原则注上公差如下[1]”:
.
.
.
.
.
,
(1)
的型腔尺寸,对于中小型塑件,
,
式中Ls—塑件外形基本尺寸,为20mm;
Scp—塑件平均收缩率,(1.5~3.0)%,取Scp=2.25%;
Δ—塑件外形公差值,Δ=0.44;
得
(2)深孔型芯,型腔尺寸
对于中小型塑件:
式中Ls—塑件内形尺寸,
;
Scp—塑件平均收缩率,(1.5-3.0)%,取Scp=2.25%;
Δ—塑件外形公差值,Δ=0.2;
δz—制造公差,取δz=
。
型腔尺寸
含义同上,代入数据求得:
(3)八个小型芯底端球径型芯计算
,
代入数据得:
(4)型芯和型腔的长度计算
型腔深度
,
代入数据得:
型芯高度
=
(5)八个小型芯型腔尺寸的确定
6.3成型零件的强度及支撑板厚度计算
(1)型腔侧壁厚度
该型腔侧壁厚,因其直接为定模板,可按整体式圆形型腔,公式7-48[1]得:
式中p—型腔内压力,MPa,一般为20-50MPa;
R—型腔内半径,为20mm;
h—型腔深度,为20mm;
[σ]—型腔材料的许用压力,160MPa;
H—型腔外壁高度,35mm。
代入数据得:
考虑到导柱的长度和安装尺寸,预定的40mm显然满足上述尺寸,完全可以满足强度和刚度条件。
(2)型腔底板厚度
按强度条件计算,参考文献[1]式7-57得:
mm
所以对于球柄底部SR20型腔取厚度15mm,满足要求。
对于内孔Ø20型腔,考虑其位于8个小型芯的内部,垫板取大些以满足强度和刚度条件,取动模垫板为25mm。
第7章模架的确定和标准件的选用
以上计算内容确定以后,便可根据计算结果确定模架。
在生产中尽量选用标准模架,这样可大大缩短模具制造周期,提高企业经济效益。
由于该模具预直接采用定模板作型腔以节省材料,同时尺寸较小,但垫块厚度很厚,难以选择模架,故决定自制。
第8章导向机构的设计
导向机构主要用于保证动模和定模两大部分及其他零部件之间的准确对合。
导向机构主要有导柱导向和锥面定位两种形式,设计的基本要求是导向精确,定位准确,并且有足够的强度,刚度和耐磨性,多采用导柱导向机构。
(1)动定模合模导向机构
设计时将导柱置于动模,其导向部分尺寸由资料查得直径为16mm。
导柱与动模板的配合精度及导套与定模板的配合精度在装