金属半固态加工技术历史现状与今后方向.docx
《金属半固态加工技术历史现状与今后方向.docx》由会员分享,可在线阅读,更多相关《金属半固态加工技术历史现状与今后方向.docx(13页珍藏版)》请在冰豆网上搜索。
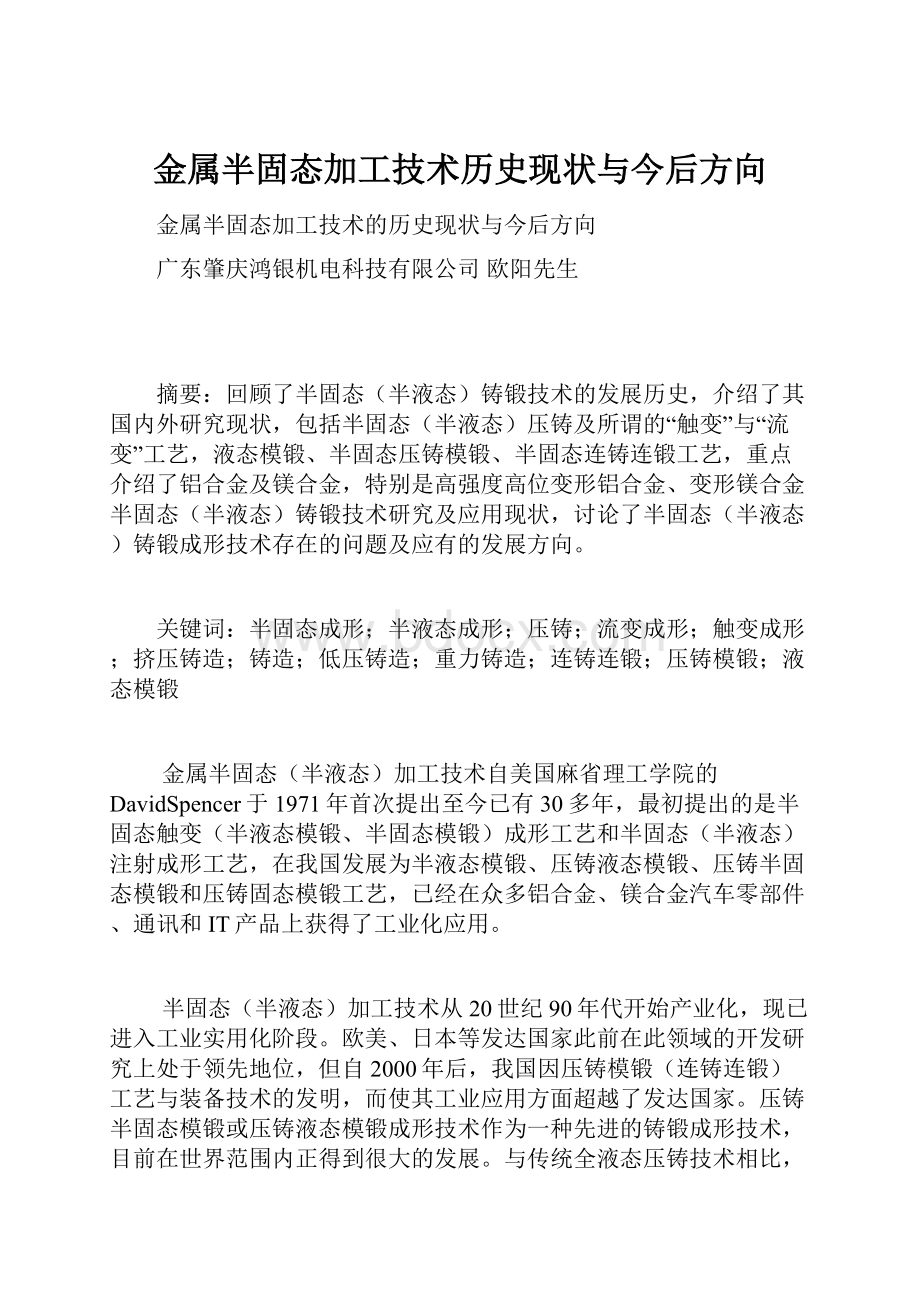
金属半固态加工技术历史现状与今后方向
金属半固态加工技术的历史现状与今后方向
广东肇庆鸿银机电科技有限公司欧阳先生
摘要:
回顾了半固态(半液态)铸锻技术的发展历史,介绍了其国内外研究现状,包括半固态(半液态)压铸及所谓的“触变”与“流变”工艺,液态模锻、半固态压铸模锻、半固态连铸连锻工艺,重点介绍了铝合金及镁合金,特别是高强度高位变形铝合金、变形镁合金半固态(半液态)铸锻技术研究及应用现状,讨论了半固态(半液态)铸锻成形技术存在的问题及应有的发展方向。
关键词:
半固态成形;半液态成形;压铸;流变成形;触变成形;挤压铸造;铸造;低压铸造;重力铸造;连铸连锻;压铸模锻;液态模锻
金属半固态(半液态)加工技术自美国麻省理工学院的DavidSpencer于1971年首次提出至今已有30多年,最初提出的是半固态触变(半液态模锻、半固态模锻)成形工艺和半固态(半液态)注射成形工艺,在我国发展为半液态模锻、压铸液态模锻、压铸半固态模锻和压铸固态模锻工艺,已经在众多铝合金、镁合金汽车零部件、通讯和IT产品上获得了工业化应用。
半固态(半液态)加工技术从20世纪90年代开始产业化,现已进入工业实用化阶段。
欧美、日本等发达国家此前在此领域的开发研究上处于领先地位,但自2000年后,我国因压铸模锻(连铸连锻)工艺与装备技术的发明,而使其工业应用方面超越了发达国家。
压铸半固态模锻或压铸液态模锻成形技术作为一种先进的铸锻成形技术,目前在世界范围内正得到很大的发展。
与传统全液态压铸技术相比,该技术在适应铝合金、镁合金的范围,在提高铸锻件强度、抗冲击韧性,改善铸锻件内外质量,实现变形合金的表面阳极氧化,提高毛坯表面光洁度,在消除铸锻件表时针孔,扩展压铸工艺的适应范围,降低纯锻压工艺的成本,提高生产率,及延长模具寿命等方面具有无可比拟的优越性。
1半固态(半液态)金属铸锻成形方法及特点
目前,应用在工业上的半固态(半液态)金属成形方法,传统的有半固态(半液态)压铸、半固态间接挤压、半固态直接挤压(半固态触变)、半固态(半液态)模锻、半固态注射成形、半固态铸造充型+锻造(半固态连铸连锻、半固态压铸模锻),最新的工艺就是压铸液态模锻、压铸半固态(半液态)模锻与压铸固态模锻等。
与普通的加工方法相比,金属半固态加工技术具有许多优点:
可以实现较低的充型速度、实现平稳、无湍流、无喷溅充型;充型温度相对低,凝固收缩相对小;对于半固态锻造(半固态触变锻压)来说,铸锻件的尺寸精度高。
如半固态锻压铝合金毛坯,热收缩率约千分之三,只有压铸工艺的一半,是真正的无切削、少余量精密成形工艺。
半固态锻压成形的凝固时间比压铸工艺短一半以上,比低压铸造、重力铸造缩短2/3以上,生产率显著提高;半固态锻压可以生产比纯锻压更复杂的毛坯,毛坯表面更光滑(可达到镜面),缺陷更少,成本更低;铸锻件内部组织致密,晶粒极细,能完全消除压铸工艺会产生的内部气孔、缩孔缩松,因其锻压激冷的工艺特征,而基本不会产生偏析缺陷;毛坯的力学性能显著提高,通过提高锻压比压,就能达到锻压件的内在水平。
除了纯粹的半固态充型的自然冷却工艺,模具的寿命有所提高,对于半固态锻压成形,则既产生激冷,又在短时间释放结晶潜热,是加大了对模具的热冲击的,加上锻压比压一般比传统压铸的充型比压高,并是一个持续的物理做功过程,对模具的要求更高。
除了需要按锻压模具的技术要求处理外,与普通压铸模相比,在同等情况下,寿命有所下降。
材料的力学性能:
应用半固态锻压加工工艺,与液态模锻工艺一样,都可制备“金属—非金属”的复合材料,即将熔融状的金属材料压进非金属材料的间隙中,其瞬间激冷工艺特性,有效解决高位合金(高溶质元素含量的高强度合金)的偏析;走出半固态浆料制备成形的误区,直接通过相关参数的控制,利用压铸半固态锻压成形工艺,可以生产出结构外形极复杂的锻态毛坯,就能实现连续的工业化自动化生产。
半固态铸锻技术通常分为两种:
第一种将浆料(此时的桨料是否“半固态”,没有任何意义)预先制成一定大小的锭块,需要时再重新加热到半固态温度,然后送入压室进行半固态的充型压铸,这种工艺称为流变压铸,准确的名称叫“半固态充型压铸工艺”,它与普通压铸工艺一样,充型后是自然冷却,就只能生产出铸件毛坯,并不能消除与普通压铸件同样存在的缩孔缩松缺陷;第二种是将液态或半固态熔体,经压射装置充型到模具型腔里,或再经一个时间冷却,在半固态下锻压(所谓“触变”),生产出锻压毛坯,可划入半固态的触变成形,正确的名称叫“压铸半固态模锻工艺”。
由此应建立两个基本思想观点:
一是不能认为说到“半固态加工”,就能消除缩孔缩松缺陷,关键是看最后的工步,是否存在一个锻压补缩的工艺过程,否则还是与传统铸造工艺一样,出现基本相同的缺陷;二是“半固态”不能仅看充型时坯件的状态,因为就算是半液态充型,但仍有铸态(液态)的成份,仍存在“液—固相”的相变收缩。
关键还是最后的工步,有无补缩(或强制补缩作用的锻压)工步。
与科学研究不同,在工业上,到底毛坯是应在半固态补缩,还是液态就补缩,甚至在固态时补缩,也不特别强求,关键是哪个细分工艺更恰当。
2金属半固态铸锻成形
2.1金属半固态触变铸锻成形
半固态金属触变铸锻成形工艺主要包括三个工艺流程:
液态或半固态金属的熔化或制备、金属熔体的充型、半固态(半液态)下触变(锻压)成形。
半固态锻压(所谓“触变”),才是半固态金属铸锻成形技术的关键,是否半固态制坯、半固态充型并非决定性因素。
最初提出的半固态加工工艺,老是将注意力集中于半固态桨料的制备,而忽视了无论是何种工艺,生产出的毛坯,是铸态的还是锻态的这个根本标准。
事实上,几十年来,就是因循于半固态的制坯及“二次加热”,走入了半固态加工的死胡同,才使早前的半固态加工工艺裹足不前,一直停留在实验室阶段,生产成本极高,工艺过程也极难控制,根本不具有工艺经济性与工业经济性。
所谓“在工业上批量供应半固态铝、镁合金坯料”,都是无从谈起的废话。
“压铸半固态加工”工艺的提出,使人们清楚地看到,我们无须具体或能从“宏观”上,看得到“半固态”的东西,而是要细心去品味,这个工艺过程,是否存在“半固态锻压”,能不能生产出没有“液—固”相的相变缩孔缩松缺陷的毛坯来。
故,无论从成本的降低还是从工艺控制的难度,半固态加工,都应舍弃或不应侧重半固态的充型,这样就能将最初最难控制与成本最高的“二次加热”工步省掉。
省了这个工步,半固态锻压加工的工业化生产优势,才能展现出来。
压铸+半固态触变(锻压)成形工艺,其“半固态”的液固相组份百分比,可简单通过液相充型后“始锻延时的时间”来控制,它的实质,也就是“始锻温度”的控制。
始锻温度的高低,是影响毛坯最后微观组织的一个因素,但这个因素,并不能看得过大过重。
影响毛坯金相的最大最关键因素,还是“锻压比压”,简单来说,就是锻压力的大小。
对于高位合金,还有激冷的快慢所导致的偏析现象。
半固态金属触变(锻压)成形,设备性能、响应速度的快慢与精度,决定可生产毛坯材料牌号(合金成份高低)的范围,也影响毛坯件的内在与外观质量。
早期在研究半固态金属触变成形,一般都是在固态金属锻造成形的液压机(油压机)上进行,这种工艺,其实可叫做“半液态模锻”。
由于对半固态加工认识上的误区,世界上许多公司早期对全液态金属压铸机进行了一定的设计和改造,以为生产出了“半固态触变”加工设备,包括了瑞士Buhler公司于1993年生产出的所谓“铝合金半固态压铸”的SC压铸机。
这台设备,本质上还是一台压铸机,只不过采用电磁搅拌连续铸造出的坯料,在感应加热至半固态,然后送入压铸机的压室,由压射冲头将半固态的坯料挤进模具型腔内成形。
而意大利Idra、Italpress.英国Servotest,日本ToshibaMa—chine,美国PrinceMachine、EPCO、HPM等公司生产“半固态加工”,都如上述的基本相同,走不出这个误区。
相反,中国的同行并没有走这条弯路。
他们最早是在“液态模锻工艺”的基础上发展出“半液态模锻(半固态模锻)”,在提出“压铸液态模锻”工艺与装备的情况下,很自然就引伸出“压铸半固态模锻”或“压铸半固态触变模锻”的工艺来。
“压铸半固态模锻(触变)成形工艺”的显著优点,是与压铸工艺一样,实现全自动工业大批量生产。
因为这种工艺,并不存在别外的“半固态制坯与二次加热”,也不注重或要求半固态的充型,这就使材料的熔化工步,其设备与普通压铸的完全一样,它的半固态加工,是靠对熔体进入模具型腔后的“延时”与“始锻温度”的工艺参数控制实现。
所以,“压铸半固态触变锻压成形”,仅从外观上,是看不出“半固态”的,而只能从整个工艺过程的参数,从最终毛坯的内在质量,才能有所分别。
如上的述,在这个工艺流程中,进入到模具型腔中的熔体,其半固态的组份并不是太重要,其“触变”的锻压比压,能实现的金相破碎度,以及激冷响应时间的快慢,其所影响的偏析,才是最后最关键的东西。
因此,“压铸半固态触变锻压成形”装备的外围设备,如抓取成形件机器人、喷涂料机构、冷却系统、浇注系统等,这些辅助设备都与压铸生产并无二致。
2.2“半固态金属流变压铸成形”及其真实工艺表达
所谓“半固态金属的流变压铸”是最早进行研究的半固态金属成形工艺。
早期未知这种“半固态金属的流变压铸”,只是形式上名义上的“半固态加工”,不但其通过强烈机械搅拌获得的半固态合金浆料,工业的过程控制十分不便,制备的成本也很高,关键的问题是,其以普通压铸机,用其压室将“半固态”的坯料压进型腔,也只生产出比普通压铸工艺好不了多少的坯件,缩孔缩松缺陷依然。
故这种“半固态金属的流变压铸”,根本是走错了方向,绝不可能发展出“成熟的技术”。
只有压铸充型半固态触变(锻压)工艺,才获得完满的成功与工业化大规模应用。
所以说,工业上不存在所谓的“半固态金属的流变压铸”,只应存在“普通压铸充型+半固态触变锻压”的工艺。
2.3外国几种涉及“半固态”加工技术的点评
要指出的是,日本公司设计制造的与注塑机原理相类似的“射铸成形流变铸造机”,其能实现的“流变成形”,也与之前用普通压铸机,在压室中将半固态坯料压进型腔,只是实现与“中心压铸”一样的工艺结果,只不过是加大了进水口的截面积的“大水口”缓慢充型压铸状态罢了。
有所区别的是其投料,是将铝粉、镁粉加人高温螺旋混合机.一边加热一边旋转剪切推进,使铝合金、镁合金在“半固态”状态,象注塑机一样射入模具型腔成形,成本高到不可以接受。
而1996年日本UBE公司申请的一项所谓“非机械或非电磁搅拌的低过热度倾斜板浇注式的流变铸造技术”专利,也称为NewRheoc-sting,简称NRC,不过是一项“半固态合金的制备”思路,重踏制备半固态合金的覆辙,工艺复杂麻烦,成本极高,根本没有工业经济性。
(该技术的思路是:
降低浇注合金的过热度,将合金液浇注到一个倾斜板上,合金熔体流入收集坩埚,再经过适当的冷却凝固,这时的半固态合金熔体中的初生固相就呈球状,均匀分布在低熔点的残余液相中,最后对收集坩埚中的合金浆料进行温度调整,以获得尽可能均匀的温度场或固相分数,就可以将收集坩埚中的半固态合金浆料送人压铸机的射室、挤压铸造机的射室或锻造机的锻模中。
)
在2001年.美国麻省理工学院(MIT)的YurkoJA等人提出了一种新的“流变铸造”技术,它同样的是一种半固态合金的制备方法,再在压铸机进行“半固态压射”,其结果同样可想而知。
3半固态铸锻技术的现状
金属半固态铸锻成形技术的研究与开发已经有30多年的历史。
该技术走过了对半固态浆料(坯料)的制备、加工与充型特性研究的原始阶段,这包括了对“半固态成形毛坯”,究竟是铸态的还是锻态的定性分辩的认识过程,厘清了“流变”与“触变”概念的含糊误区;也就是认清了,不管是“流变”还是“触变”,只有充型时的半固态,该工艺断不能生产出锻态的毛坯,它还只能是一种铸态的毛坯,仍然避免不了传统铸造(包括压铸)工艺所生产、所出现的缺陷,都不是“半固态加工”该能实现的目标的本意。
其工业化应用,则走出了侧重所谓的“半固态”桨料或坯料的制备与“二次加热”误区,最后的落脚点放在了最终的成形毛坯,必须是“锻压件”的内部质量上。
对半固态铸锻加工认识与转变的关键有两个方面:
一是不再纠缠于是否宏观“可见到”“半固态”,也就是说不再将“半固态”加工,理解为熔体充型前、充型时的制桨或制坯的半固态状态;二是不再将半固态理解为“铸造充型时的半固态”,而理解为“锻造时的半固态”。
也就是说,将半固态加工,归入锻造的工艺范畴。
在这两个基本认识下,区分定义清析了“半固态加工”最初而特有提出的,其实是模糊不清的所谓“流变”与“触变”工艺。
这就是,所谓“半固态流变
工艺”,是半固态铸造,归入铸造的范畴;所谓“半固态触变”,是半固态锻压,归入锻造的范畴。
而只有后者,才是半固态加工所追求的东西。
半固态加工,它后来实质上否定了单纯的“半固态充型压铸”工艺在工业上应用意义,因为这种工艺也只是能生产出铸态的毛坯,其比熔融状态充型的传统压铸工艺,优势很不明显,工艺难度与成本却高得多。
认识到“半固态充型”,其所谓的“利用其高表观粘度降低自身的雷诺数实现实体平稳充型”,以“减少甚至消除气孔”,不过是一种表象,是不能避免“液—固相”的相变缩孔缩松缺陷的。
因为缩孔缩松缺陷,内部是真空的,是由相变收缩产生的,利用半固态的平缓的、低温的充型过程,根本不能解决这个问题,从而失去了意义。
3.1铝合金半固态铸锻技术的应用
目前半固态金属加工应用最成功和最广泛的是在铝合金,包括了变形铝合金(锻铝、硬铝与超硬铝)的生产。
其原因不仅是因为铝合金的熔点较低和使用范围广泛,而且铝合金,特别是变形铝合金,有更宽的液固共存区(即半固态区间或“粥样状态区间”)的合金体系,更适宜半固态加工与“半液态模锻”加工。
更宽的半固态区间,可以使用更低的“电液响应精度”设备,具体生产工艺参数的摸索更容易,生产的难度更低。
最早用于半固态加工的为亚共晶铸造铝合金(ZL203、A356,A357)。
这些合金在发达国家及我国,早在上世纪的八十年代开始,已采用半固态成形(半液态模锻工艺)实现工业化生产。
我国“半液态模锻工艺”用得最早最好的,是位于广东肇庆的广东仪表厂,它们用该工艺,特别以ZL203铝合金,几十年来大规模生产出对气密性要求甚严的气动传感器(仪表)的核心部件。
肇庆市广厦自动控制元件厂及后来的肇庆鸿银机电科技有限公司,在2005年前,也生产出半固态区间较窄的ZL102、ZL107铝合金毛坯。
此后,利用其发明的压铸模锻机,又开发了用6061、5052等高强度变形铝合金和过共晶成分的A390、ZL117、ZL109超高硅铝合金的半液态、半固态加工结构复杂的锻压件,如跑车的锻压活塞、电动自行车的锻压轮毂、高铁电缆悬挂件、LED散热板、摩托车连杆、空调压缩机斜盘等。
通过该连铸连锻、压铸模锻的专利工艺与装备,生产出一大批与压铸件一样结构复杂的半固态锻压件,将变形铝合金、锻铝合金、硬铝与超硬铝合金的半固态成形加工,一步提升到工业化大批量生产应用的高度。
对于过共晶易偏析铝合金,特别是超硬铝(LC、7075),可通过传统的搅拌方式,减轻熔体晶粒长大的趋势,细化初晶硅相及其它合金元素晶核,达到初步均匀分布在熔体中,通过模具内浇流道与充型工艺参数的优化设置,特别是对最终的“半固态相份锻压”几大关键参数控制,选择合适的始锻温度,以生产出激冷超细金相的锻压毛坯,从而显著提高合金的强度、延伸、冲击韧性和耐磨性。
半固态铸锻成形技术,能生产出高强度铝合金(LC超硬铝合金,强度最高达600MPa)的锻压毛坯,足以替代黄铜(Hpa59-1、H62)、锌等贵价有色金属,也能有效替代强度只在400Mpa的铸铁(灰口铸铁与球墨铸铁)零件。
自2008年起,该工艺生产的高强度铝合金件,已应用于生产电动车轮毂及后车桥上。
而对于普通压铸铝、铸造铝的半固态锻压加工,也是能提高抗拉强度约20%,提高延伸率约1-2倍,提高抗冲出韧性约50%,并能显著细化晶体。
3.2镁合金半固态铸锻技术的应用
从材料学的角度看,现时公布的国标牌号镁合金,具体更宽的半固态区间,更适宜用半固态(半液态)模锻加工,包括应用连铸连锻、压铸模锻工艺的生产。
因为这些牌号的镁合金,其实都是变形镁合金,包括了标注为“铸造镁合金”的合金,都更适宜用压力(锻压与挤压)成形工艺生产。
在这里,或可消除一个认识误区,同时也加深对铝合金的半固态加工及铝合金的其它铸锻成形工艺的认识。
在镁合金或铝合金中加硅,会提高合金的流动性,有利于在低充型压力下的铸造充型。
但在合金中加硅,将导致两大严重后果:
一是缩小合金的半固态区间。
硅元素加得越多,半固态区间越窄,越不利于半固态工艺及连铸连锻、压铸模锻工艺的应用。
当年用液压机进行液态模锻生产时,同一种毛坯结构,用ZL203材料,比较容易生产出合格毛坯,但改有ZL102、ZL107时,就困难得多了;二是显然降低合金的强度与延伸率,使合金变脆。
硅在镁或铝的溶解度只有2%以下,利用铸锻工艺的激冷等有利因素,最边际的含硅量在5%左右,超过这个含量,合金综合机械性能直线下降。
这就是A356、ZL101等铝合金的含硅量定在这个水平的依据。
当硅含量提高一倍到10%时,铝合金的抗拉强度就降低一半,只到180-230MPa的水平,其延伸率则显著降低约70-80%,到只有2%以下,其抗冲击韧性基本失去。
所以,高强度变形铝合金的含硅量总在2%以下,这些牌号包括应用最广泛的我国LD、LC、LF、LY牌号,和外国的6061、6063、2024、5052、7075牌号。
而现时的铸造镁合金牌号,含硅量都在2%以下,与变形铝合金的6061、6063、7075、2024、5052的含硅量一样低,都是不应宜压铸的。
因为压铸工艺是单向高速充型及自由缓慢冷却,完全没有补缩的可能。
变形镁合金与变形铝合金的成形加工特性是极相似的,其相变体积收缩率高是一个方面,关键是合金的压力加工特性,包括了合金易偏析、晶粒易粗大,需要对晶粒进行压力破碎这种压力做功的内在要求,都是使之成为压铸工艺禁区的重要因素。
因此,现在牌号的镁合金,完全不该用所谓的“半固态流变充型压铸”,以及其它的压铸工艺生产。
只有更高充型速度的压铸机,并不是什么“镁合金压铸机”,也都是一种适用于相变收缩比较少,合硅量比较高的铝合金压铸件的生产。
也不要相信所谓的“镁合金半固态射铸充型”技术,它与注塑机成形的道理一样,它对于镁合金与铝合金的成形,都只是能生产出铸态的毛坯,不其缩孔缩松现象依然,基本不以消除,其热收缩裂纹现象或趋势是非常严重的,完全没有工业应用价值。
如前所述,目前能广为应用的半固态成形技术,只能归于以熔融状态,即以与压铸工艺一样的充型而不用搞无用的半固态桨料或制坯,通过对熔体进入到模具型腔内的半固态相份控制,通过半固态锻压,去表达半固态加工本质特性的工艺,这种半固态锻压,才是传统“触变成形”技术的核心思想与工业上应(可)表达的形式,才能取得预期的目标或效益。
一句话,不存在通过压铸机能实现真正的“半固态触变成形”任何可能。
可实现工业化生产镁合金的半固态成形,就只能是“普通铸造充型+半固态锻压(触变)”工艺。
镁合金的“普通铸造充型+半固态锻压(触变)”工艺,它需要装备有相关的功能才能得到表达。
它可以通过连铸连锻、压铸模锻,甚至包括最简单的液压机液态模锻工艺,在其锻压工步上去表达。
要完成这个工艺思路并不复杂,它不需要什么“半固态非枝晶化”的过程,不存在“锭料保温输送”,更不需对装备的压射系统作相应的改变,不需要“半固态制坯与半固态桨料”的制备与充型。
4半固态加工的应用与进一步的研发取向
无需对熔体的半固态制坯或半固态桨料的制备,没有了“二次加热”的工序,就走出了“半固态充型铸造”的方向误区。
这样,最初的半固态研究开发与工业化应用所必需的半固态制桨设备或制坯制备,及“二次加热”设备研发的拦路虎也就不存在。
不但“半固态压铸成形的压铸机”不存在,与“压铸模锻模具”不一致的“半固态充型模具”,也不存在。
没有半固态制坯所导致的生产制造成本的提高,“半固态加工”成本与普通压铸、压铸模锻工艺便基本相同,就具有工业化应用与进一步研究发展的基础。
由于半固态锻压与压铸模锻工艺所用装备是相同的,尽管每一种毛坯,其复杂程度与所需合金种类的不同,道理上其选择的“半固态相分”也不同,但通过压铸模锻机的PLC功能,我们还是可以随心所欲的进行所需工艺参数的调整。
最关键的,是对延时锻压参数设置,它所隐含的模具中的熔体,其瞬间的半固态组份的把握与控制,以及瞬间激冷减少偏析上。
在现实的生产中,它需要找出具体的毛坯与对应的模具,在“热平衡”生产时的最优工艺参数,确定与通过设备的电脑记录下来,以备下次生产时重新调出来。
半固态锻压加工工艺与压铸模锻的工艺与装备的进一步发展是共性的,都是要提高装备的精度,包括核心的“液—电”时滞性的响应精度,以能充分表达出工艺意愿;也包括使生产的毛坯,其尺寸精度得到同步的提高。