板金件和塑料件设计的工艺准则.docx
《板金件和塑料件设计的工艺准则.docx》由会员分享,可在线阅读,更多相关《板金件和塑料件设计的工艺准则.docx(32页珍藏版)》请在冰豆网上搜索。
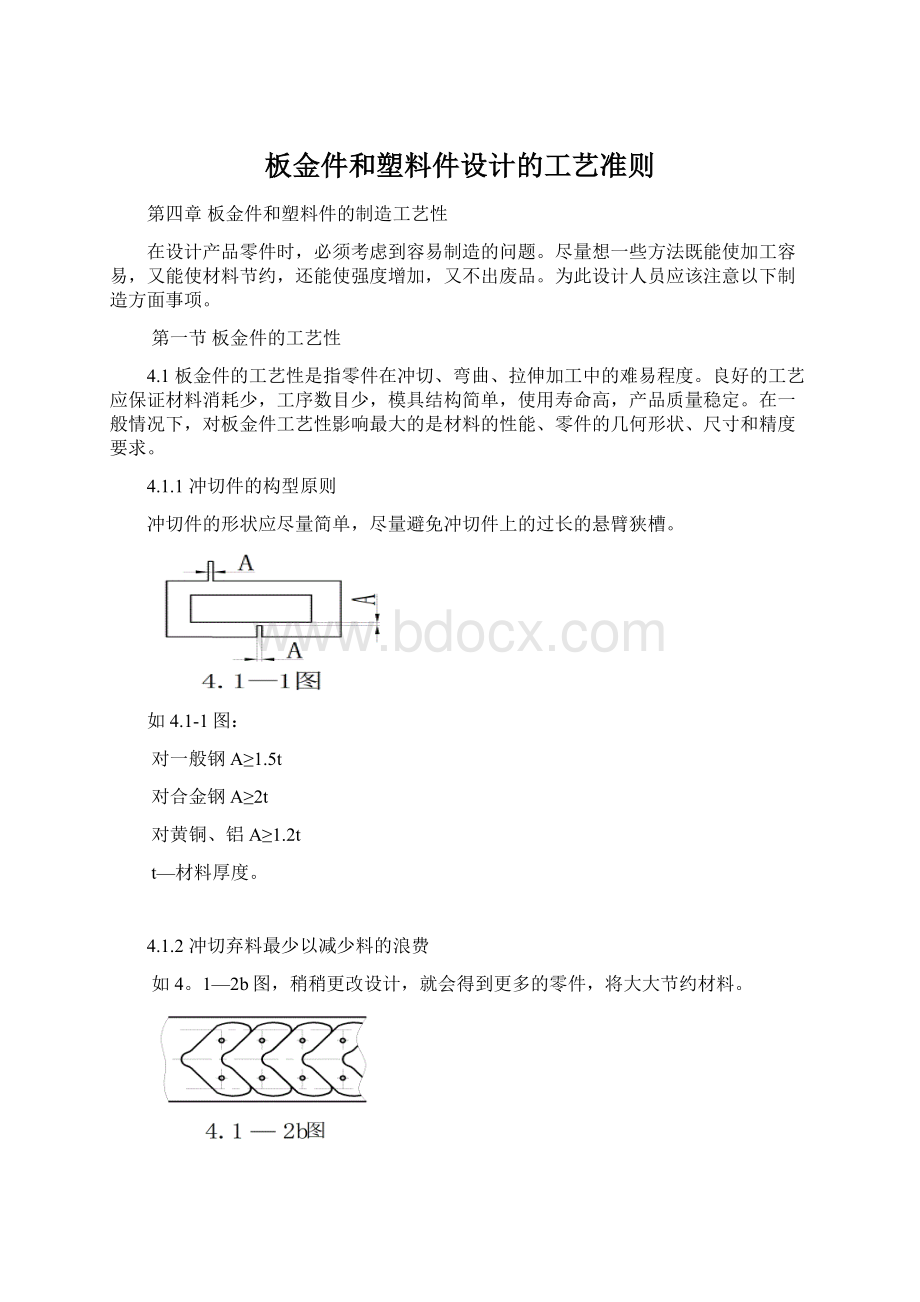
板金件和塑料件设计的工艺准则
第四章板金件和塑料件的制造工艺性
在设计产品零件时,必须考虑到容易制造的问题。
尽量想一些方法既能使加工容易,又能使材料节约,还能使强度增加,又不出废品。
为此设计人员应该注意以下制造方面事项。
第一节板金件的工艺性
4.1板金件的工艺性是指零件在冲切、弯曲、拉伸加工中的难易程度。
良好的工艺应保证材料消耗少,工序数目少,模具结构简单,使用寿命高,产品质量稳定。
在一般情况下,对板金件工艺性影响最大的是材料的性能、零件的几何形状、尺寸和精度要求。
4.1.1冲切件的构型原则
冲切件的形状应尽量简单,尽量避免冲切件上的过长的悬臂狭槽。
如4.1-1图:
对一般钢A≥1.5t
对合金钢A≥2t
对黄铜、铝A≥1.2t
t—材料厚度。
4.1.2冲切弃料最少以减少料的浪费
如4。
1—2b图,稍稍更改设计,就会得到更多的零件,将大大节约材料。
4.1.3冲孔件的构型原则
最小边距和孔间距。
零件上冲孔设计应考虑留有合适的孔边距和孔间距以免冲裂。
最小孔边距和孔间距见4.1—1表。
4.1.3-1最小冲孔直径或方孔的最小边长
冲孔时,应受到冲头强度的限制,冲孔的尺寸不能太小,否则容易损坏冲头。
最小冲孔直径及最小边长见4.1—2表。
4.1—2表
t—材料厚度
4.1.3-2冲切缺口原则
冲切缺口应尽量避免尖角,如4.1—3a图所示。
尖角形式容易减短模具使用寿命,且尖角处容易产生裂纹。
应改为如4.1—3b图所示。
R≥0.5t
(t─材料厚度)
4.1—3a图4.1—3b图
4.1.4弯曲件的结构原则
4.1.4-1板件最小弯曲半径
板件弯曲时,若弯曲处的圆角过小,则外表面容易产生裂纹。
若弯曲圆角过大,因受到回弹的影响,弯曲件的精度不易保证。
为此规定最小弯曲半径。
见4.1-3表。
4.1—3表
材料
最小弯曲半径(R)
冷轧板、电镀锌板、镀锌板
R≥2t
黄铜板
R≥1t
铝合金板
R≥1.2t
4.1.4-2弯曲的直边高度不宜过小,否则不易成形足够的弯矩,很难得到形状准确的零件。
其值h≥R+2t方可。
见4.1—5图。
4.1─5图4.1─6图
4.1.4-3弯曲边冲孔时,孔边到弯曲半径R中心的距离L不得过小,以免弯曲成型后会使孔变形。
其值L≥2t方可。
见4.1—6图。
4.1.4-4当a<R时,弯曲后,b面靠a处仍然有一段残余圆弧,为了避免残余圆弧,必须使a≥R。
4.1—7图
4.1.4-5在U形弯曲件上,两弯曲边最好等长,以免弯曲时产生向一边移位。
如不允许,可设一工艺定位孔。
如图4.1—8图。
4.1—8图
4.1.4-6防止侧面(梯形)弯曲时产生裂纹或畸形。
应设计预留切槽,或将根部改为阶梯形。
槽宽K≥2t,槽深L≥t+R+K/2。
4.1—9图
4.1.4-7防止圆角在弯曲时受压产生挤料后起皱,应设计预留切口。
如室外机侧板(上端、下端)圆角处切口形式。
上端下端
B与盖板厚度(t)相等
4.1—10a图4.1—10b图
4.1.4-8防止弯曲后,直角的两侧平面产生褶皱,应设计预留切口。
褶皱
4.1—11图
4.1.4-9防止弯曲后,产生回弹的切口形式。
a≥1.5t
(t—材料厚度)
4.1—12图
4.1.4-10防止冲孔后,弯曲产生裂纹的切口形式。
裂纹切口
4.1—13图
4.1.4-11防止弯曲时,一边向内产生收缩。
可设计工艺定位孔,或两边同时折弯,还可用增加幅宽的办法来解决收缩问题。
工艺孔
两边折弯
增加幅宽
4.1—14图
4.1.4-12弯成直角的搭接形式。
B
AA—A
B
A
B—B
4.1—15图4.1—16图
4.1.4-13凸部的弯曲
若象a图那样弯曲线和阶梯线一致,有时会在根部开裂变形。
所以使弯曲线让开阶梯线如图b,或设计切口如c、d那样。
r≥2t
n=r
abcd
m≥2tk≥1.5tL≥t+R+k/2
4.1—17图
4.1.4-14防止弯曲时,弯曲面上的孔受力后会变形,孔边距(至底根部)其值A≥4方可。
鼓起
4.1—18图
4.1.5拉深件的构形原则
a.拉深件的形状应尽量简单、对称。
b.拉深件各部分尺寸比例要恰当,尽量避免设计宽凸缘和深度大的拉深件。
(D凸>3d,h≥2d)因为这类零件要较多的拉深次数。
c.拉深件的圆角半径要合适,圆角半径尽量取大些,以利于成型和减少拉深次数。
4.1.5-1拉深件的圆角半径。
4.1—4表
4.1.5-2拉深件或弯曲件冲孔的合适位置。
4.1—19图
4.1.5-3防止拉深时产生扭曲变形,A、B宽度应相等(对称)即A=B。
扭曲
A≠BA=B
4.1—20图
4.1.6穿破件的构型原则
当搭接在一道工序中用冲切法制成90°的弯边时,选材要注意材质不宜太硬,否则易在直角弯折处破裂。
应在弯边位置设计工艺切口,防止折角处破裂。
R≥2t
A
A
A≥3A-B≥0.5L≥t+R+K/2K≥2tA—A旋转
2:
1
4.1—21a图4.1—21b图
4.1—21c图
4.1.7提高零件强度的合理构型
4.1.7-1对较长的板金件为了提高其强度,应该设计加固筋。
筋的形状、尺寸及适宜间距见4.1—5表。
4.1—5表
4.1.7-2在弯曲件的弯角处再作弯折,能起到筋条的加强作用。
角部处加强筋的形状、尺寸及筋间距见4.1—6表。
4.1—6表
L
R1
R2
R3
H
B
筋间距
12
6
9
5
3
16
60
15
7
12
6
4
20
70
(B—参考值)
4.1—22图
4.1.8板金件常用自攻螺钉底孔、翻边孔直径及翻边高度。
见4.1—7表。
4.1—7表
4.1.9钻普通螺纹底孔的钻头直径。
见4.1—8表。
4.1—8表
4.1.10钻英制螺纹底孔的钻头直径。
见4.1—9表。
4.1—9表
4.1.11板金件的尺寸公差
公差是影响产品质量和价格的重要因素之一。
在制造零件的时候,经验告诉我们,无论投入多少成本和时间,完全按图纸上标注的尺寸准确地加工出来几乎是不可能的。
产品设计无论从性能上还是经济上都要满足用户的需要。
从企业本身来说,也必须保持正常的利润。
为此公差必须由产品的性能和经济两方面来决定。
所以设计要充分掌握公差的原则。
4.1.11-1冲切件的尺寸公差。
见4.1—10表及4.1—23图、4.2—24图。
4.1—10表
基本尺寸
圆孔Φ(H12)
长度L(JS12)
下偏差
上偏差
极限偏差
≤3
0
+0.10
±0.05
>3~6
+0.12
±0.06
>6~10
+0.15
±0.075
>10~18
+0.18
±0.09
>18~30
+0.21
±0.105
>30~50
+0.25
±0.125
>50~80
+0.30
±0.15
>80~120
+0.35
±0.175
>120~180
+0.40
±0.20
>180~250
+0.46
±0.23
>250~315
+0.52
±0.26
>315~400
+0.57
±0.285
>400~500
+0.63
±0.315
>500~630
+0.70
±0.35
>630~800
+0.80
±0.40
>800~1000
+0.90
±0.45
>1000~1250
+1.05
±0.525
>1250~1600
+1.25
±0.625
>1600~2000
+1.50
±0.75
4.1—23图4.1—24图
4.1.11-2弯曲件的边高h直线尺寸公差。
见4.1—11表及4.1—25图。
4.1—25图
4.1—11表
弯边高度h
≤10
>10~18
>18~30
>30~50
>50~120
>120~250
>250
极限偏差
材料厚度
≤1
±0.18
±0.215
±0.26
±0.31
±0.435
±0.57
±0.65
>1~2
±0.215
±0.26
±0.31
±0.435
±0.57
±0.65
±0.77
注:
弯曲边长L直线尺寸公差按4.1—10表规定。
4.1.11-3弯曲件的角度公差。
见4.1—12表及4.1—26图。
4.1—26图
4.1—12表
角短边的长度L
非配合角度偏差
Δa
最小角度差Δa
角短边的长度L
非配合角度偏差Δa
最小角度偏差Δa
>30~50
±2°
±45′
>260~360
±30′
±15′
>50~80
±1°30′
±30′
>360~500
±25′
±12′
>80~120
±1°
±25′
>500~630
±22′
±10′
>120~180
±50′
±20′
>630~800
±20′
±9′
>180~260
±40′
±18′
>800~1000
±20′
±8′
4.1.11-4拉深件的高度h尺寸公差。
见4.1—13表及4.1—27图。
4.1—27图
4.1—13表
拉深高度
h
材料厚度t
0.5
0.5~1
1~1.5
1.5~2
2~2.5
2.5~3
极限公差
3
±0.15
±0.18
±0.21
±0.25
±0.30
±0.33
3~6
±0.18
±0.21
±0.25
±0.30
±0.33
±0.36
6~10
±0.21
±0.25
±0.30
±0.33
±0.36
±0.40
10~18
±0.25
±0.30
±0.33
±0.36
±0.40
±0.45
18~30
±0.30
±0.33
±0.36
±0.40
±0.45
±0.51
30~50
±0.46
±0.50
±0.60
±0.70
±0.90
±1.10
50~80
±0.5
±0.60
±0.70
±0.90
±1.10
±1.30
80~120
±0.7
±0.80
±0.90
±1.10
±1.30
±1.50
注:
拉深边长L直线尺寸公差按4.1—10表规定。
4.1.11-5冲切件的断面粗糙度。
见4.1—14表。
4.1—14表
材料厚度t
≤1
>1~2
>2~4
粗糙度
4.1.11-6冲切件的毛刺允许高度。
见4.1—15表。
4.1—15表
材料厚度t
试模
批量生产
~0.35
≤0.015
≤0.05
0.5~1.