汽车中地板后横梁中段加强件冲压模的毕业设计.docx
《汽车中地板后横梁中段加强件冲压模的毕业设计.docx》由会员分享,可在线阅读,更多相关《汽车中地板后横梁中段加强件冲压模的毕业设计.docx(49页珍藏版)》请在冰豆网上搜索。
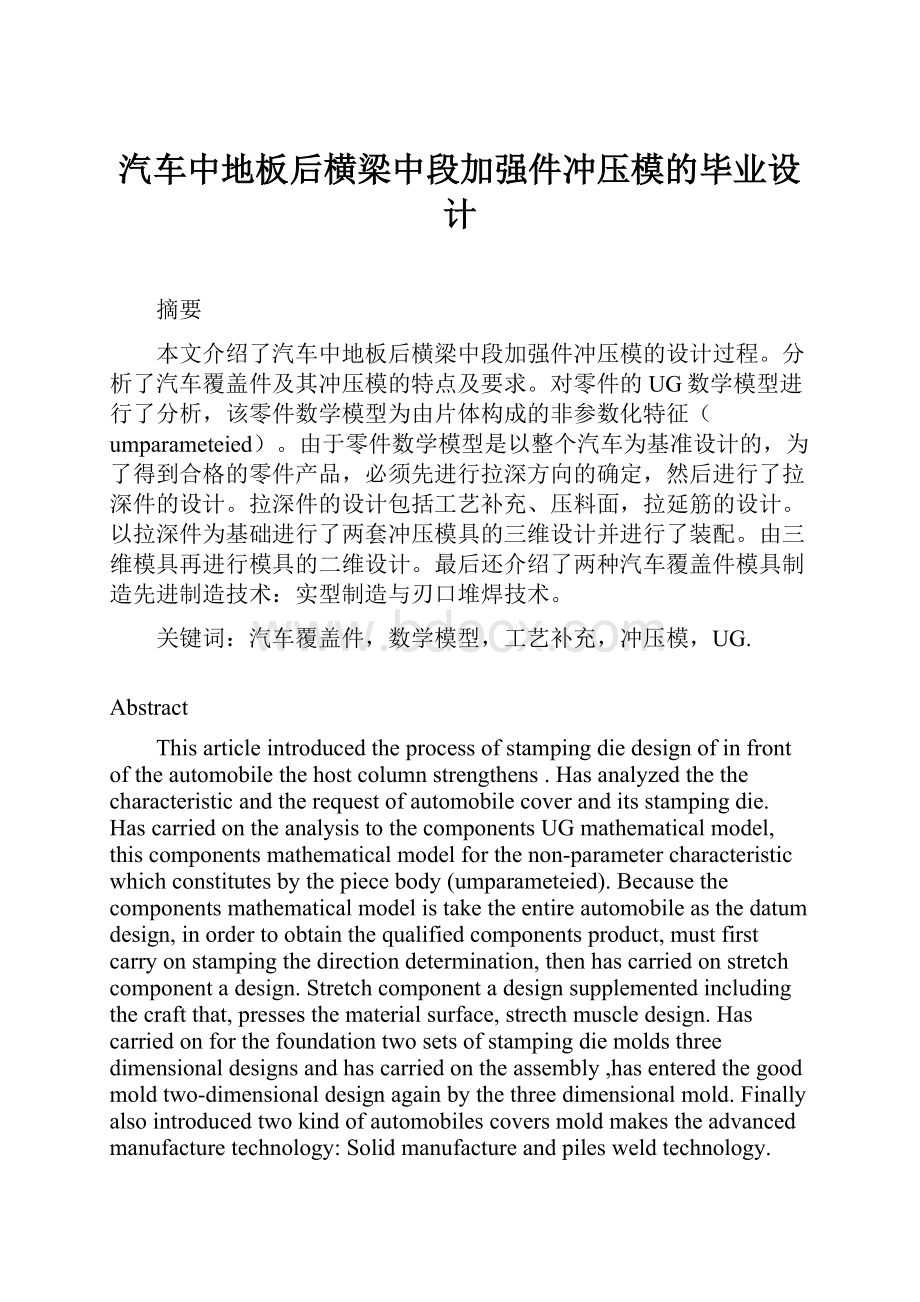
汽车中地板后横梁中段加强件冲压模的毕业设计
摘要
本文介绍了汽车中地板后横梁中段加强件冲压模的设计过程。
分析了汽车覆盖件及其冲压模的特点及要求。
对零件的UG数学模型进行了分析,该零件数学模型为由片体构成的非参数化特征(umparameteied)。
由于零件数学模型是以整个汽车为基准设计的,为了得到合格的零件产品,必须先进行拉深方向的确定,然后进行了拉深件的设计。
拉深件的设计包括工艺补充、压料面,拉延筋的设计。
以拉深件为基础进行了两套冲压模具的三维设计并进行了装配。
由三维模具再进行模具的二维设计。
最后还介绍了两种汽车覆盖件模具制造先进制造技术:
实型制造与刃口堆焊技术。
关键词:
汽车覆盖件,数学模型,工艺补充,冲压模,UG.
Abstract
Thisarticleintroducedtheprocessofstampingdiedesignofinfrontoftheautomobilethehostcolumnstrengthens.Hasanalyzedthethecharacteristicandtherequestofautomobilecoveranditsstampingdie.HascarriedontheanalysistothecomponentsUGmathematicalmodel,thiscomponentsmathematicalmodelforthenon-parametercharacteristicwhichconstitutesbythepiecebody(umparameteied).Becausethecomponentsmathematicalmodelistaketheentireautomobileasthedatumdesign,inordertoobtainthequalifiedcomponentsproduct,mustfirstcarryonstampingthedirectiondetermination,thenhascarriedonstretchcomponentadesign.Stretchcomponentadesignsupplementedincludingthecraftthat,pressesthematerialsurface,strecthmuscledesign.Hascarriedonforthefoundationtwosetsofstampingdiemoldsthreedimensionaldesignsandhascarriedontheassembly,hasenteredthegoodmoldtwo-dimensionaldesignagainbythethreedimensionalmold.Finallyalsointroducedtwokindofautomobilescoversmoldmakestheadvancedmanufacturetechnology:
Solidmanufactureandpilesweldtechnology.
Keyword:
Theautomobilecover,themathematicalmodel,thecraftsupplemented,stampingdie,UG.
前言
随着我国改革开放的不断深入,人民生活水平的提高,和我国加入WTO,我国的汽车的销售和生产得到了很大的提高。
国内汽车制造业近年来得到迅速的发展,汽车产量已名列前十名,模具工业是汽车产品开发和大批量生产的重要部分,一辆客车或轿车的约有80%的零部件是用模具加工制造的,而覆盖件的模具又以其大型、复杂、精密等特点而成为模具举足轻重的部分。
目前,我国汽车模具工业还不能适应整车开发和换型要求,其中一个原因是汽车模具设计与制造水平较低,制造装备落后,为使汽车模具工业尽快满足汽车生产发展的需要,使我国汽车工业以实力跻身于国际竞争大潮中,并取得巩固和发展。
除了靠国家有关汽车模具产业和汽车产业的方针政策外,也需要汽车模具产业成员的共同努力,在汽车模具生产技术方面赶上世界先进水平。
在未来的汽车覆盖件模具的发展趋有以下几点:
一、数学模型
从汽车车身设计开始,建立全车的数学模型,用以代替实体模型。
数学模型是覆盖件模具实现CAD/CAM技术的基础。
在新的一体化的汽车车身设计和制造过程中,从产品设计、工程图纸的绘制,结构分析、到冲模设计,模具型面的数控加工都围绕表达车身形状和特性的数学模型,展开,今后,无论是汽车覆盖件图纸,还是模具型面的加工程序,都由定型车身数学模型自动生成。
在覆盖件设计分析阶段,显示在计算机屏幕上的数学模型可以很方便地进行缩小,放大,平移,旋转,消除隐线,图形修改,工艺补充设计,照光着色和透视感处理从而可以有效的帮助人们观察和分析各种技术问题。
随着技术的发展,数学模型的用途也将更加广泛。
因此,在现有的基础上,不断更观念,开发应用软件,开发应用软件,扩大应用范围量项十分重要的工作。
二、CAE技术
覆盖件冲模的CAE技术是新兴的一种判断零件成型工艺能力的技术。
利用Autoform/dynaform等成型分析软件可以预先分析零件的成型机率,可以提高模具设计的可靠性,节省模具设计的时间和成本.
三、CAD技术
覆盖件冲模的CAD技术是以产品的数学模型作为依据进行的。
它除了使用具有较大的数据处理能力大的计算机或工作站,还需要各种功能的软件进行支援。
冲模CAD要根据各种工艺进行具体的冲模设计。
由于覆盖件的形状特别复杂,要实现CAD还是比较困难的,因此我们今后的任务就是要不断扩大CAD的比例。
四、CAM技术
目前,CAM技术应用较广泛。
普遍的方法是根据主模型进行数学扫描,然后CAM加工,或者应用数控仿型铣床进行加工,CAM和CAD相结合,将设计中的开关信息与加工中的加工信息相结合,应用加工软件如mastercam/powmill等软件,由计算机进行编程,并控制数控机床选用刀具,最佳切削量和实现刀具轨迹,这样可保证模具的高精度,达到一次加工合格不需要反复研修。
五、CAT技术
计算机辅助测量(CAT)使用三坐标测量机,可以彻底改变现有的测量手段,使模具制造处于可靠的监控状态。
六、研修技术
现在的研配压力机,上工作台可以翻转95º~180º,下工作台可移出机床外,研修模具非常方便,研修后复位精度可达到0.02mm
七、FMC技术
实型铸造技术(FMC)能够提供高质量的模具毛坯,铸造余量8~12mm,数控加工时粗铣和精铣各一次,就可以达到规定要求。
实型铸造的模型是用泡沫状的较软的聚苯乙烯塑料制成,型采用高速数控机床加工,能够保证均匀的余量。
八、模具使用优质材料及应用先进的表面处理技术
在整个模具价格构成中,材料所占比重大,一般在20%~30%之间,因此选用优质钢材和应用的表面处理技术来提高模具的寿命就显得十分必要。
对于模具钢来说,要采用电渣重熔工艺,努力提高钢的纯净度、等向性、致密度和均匀性及研制更高性能或有特殊性能的模具钢。
如采用粉末冶金工艺制作的粉末高速钢等。
粉末高速钢解决了原来高速钢冶炼过程中产生的一次碳化物粗大和偏析,从而影响材质的问题。
其碳化物微细,组织均匀,没有材料方向性,因此它具有韧性高、磨削工艺性好、耐磨性高、长年使用尺寸稳定等特点,是一种很有发展前途的钢材。
特别对形状复杂的冲件及高速冲压的模具,其优越性更加突出。
这种钢材还适用于注射成型漆加玻璃纤维或金属粉末的增强塑料的模具,如型腔、形芯、浇口等主要部件。
另外,模具钢品种规格多样化、产品精料化、制品化,尽量缩短供货时间亦是重要方向。
模具热处理和表面处理是能否充分发挥模具钢材性能的关键环节。
模具热处理的发展方向是采用真空热处理。
模具表面处理除完善普及常用表面处理方法,即扩渗如:
渗碳、渗氮、渗硼、渗铬、渗钒外,应发展设备昴贵、工艺先进的气相沉积(TiN、TiC等)、等离子喷涂等技术。
九、模具CIMS管理
随着现代科学技术的发展,计算机的应用技术已走向集成化,制造来也向集成化发展,模具的CIMS管理包括信息管理、技术管理、物流和经营管理的许多系统。
它包括从市场分析、经营决策、产品设计、经过制造各个环节,最后到销售服务、包括原材料的、生产和库存管理、财务资源管理等全部运转活动,在一种全局集成规指导下,一步一步实现计算机化,以实现更短的设计生产周期,改善企业经营管理,适应市场的迅速变化,获得更大的经济效益。
第一章零件的分析与方案的论证
一汽车覆盖件的特点和要求
本毕业设计的是昌河汽车中地板后横梁中段加强件,是汽车覆盖件的一部份。
汽车汽车覆盖件是指汽车车身或驾驶室、覆盖发动机和底盘的薄金属制成的异形体表面和内部零件,轿车的车前板和车身、载重车的车前板和驾驶室等都是由覆盖件和一般冲压构成的。
覆盖件组装后构成了车身或驾驶室的全部外部和内部事关大局,它既是外观装饰性零件,又是封闭薄壳状的受力零件。
汽车覆盖的制造是汽车车身制造的关键环节。
同一般冲压件相比,覆盖件具有材料薄、形状复杂、结构尺寸大和表面质量要求高等特点,覆盖件的工艺设计、冲模结构设计和冲模制造工艺都具有特殊性,因此在,在实践中常把覆盖件从一般冲压件中分离开来,作为一种特殊类别加以研究和分析。
覆盖件的特点如下:
1表面质量
覆盖件表面上任何微小的缺陷都会在涂漆后引起光线的漫反射而损坏外形的美观,因此覆盖件的表面不允许波纹、皱折、擦伤、边缘拉痕和其它破旧表面美感的缺陷。
覆盖件上的装饰棱线和筋线和筋条要求清晰、平滑、左右对称和过渡均匀,覆盖件之间的棱线衔接应吻合流畅,不允许参差不齐。
总之覆盖件不仅要满足结构上的功能要求,更要满足表面装饰的美观要求。
2尺寸形状
覆盖件的形状多为空间立体曲面,其形状很能难在覆盖件图上完事准确地表达出来,因此覆盖件的尺寸形状常常借助主模型来描述。
主模型是覆盖件的主要制造依据,覆盖件科上标注出来的尺寸形状,其中包括立体曲面形状、各种孔的位置尺寸,形状过渡尺寸,都应和主模型一致,图面上无法村标注尺寸,要依赖主模型量取,从这个意义上讲,主模型是覆盖件的必要补充。
3刚性
覆盖件拉深成型时,由于其塑性变形的不均性,往往会使某些部位刚性较差,刚性差的覆盖件受振动后会产生空洞声,用这样的零件装车,汽车在高速行驶时就会发生振动,造成覆盖件的早期破坏,因此覆盖件刚性要求不可忽略。
4工艺性
覆盖件的结构形状和尺寸决定该件的工艺性。
覆盖件的工艺性关键是拉深工艺性,覆盖件一般都采用一次成形法,为了创造一个良好的拉深的条件,通常将翻边展开,窗口补满,再加添上工艺补充,构成一个拉伸件。
二冲压件的工艺分析
本次毕业设计的零件为昌河汽车中地板后横梁中段加强件。
零件上面有十一不同大小的螺钉孔,精度要求不是很高,孔距位置要求不高。
整个零件没有外形尺寸要求,精度要求不是很高。
这个零件的形状相对来说不是很复杂,拉深深度不是很深,覆盖件成型可能性的分析是一项艰苦细致的工作,由于覆盖件的形状一分复杂,其成型可能性很难用计算的方法来准确的判断出来。
因此判断覆盖件是否成型,最好的办法还是参考以前加工的覆盖件,用类比的方法进行判断,经过多次工厂的调研,这个零件是可以通过冲压成形的。
此零件的材料ST13,为冷轧钢,又称特殊镇静钢,即非时效钢板,屈服点Ós≤240N.mm2,抗拉强度Ób为270~370N·mm2,伸出长率≥34%。
冷轧铝镇静钢板具有一定的强度和很好的塑性,是目前汽车上最大量的冷轧钢板,由于钢中加入了铝,固定了钢中的氮,钢板冲压成形后,零件表面产生滑移线,称为非时效钢材[9]。
零件图如下:
三设计方案
1方案的提出
工艺方案是在保证冲压件的质量下,实现生产的高效和降低成本上通过上面的分析,根据这个零件的生产批量为年产20万件,属于大批量生产。
生产处于长期稳定状态,形状改变可能性小,工艺方案要为流水线生产保证提供保证,每一道工序都要使用冲模,拉延,修边,冲孔等工序同时安装在一条冲压线上。
初步得出以下的方案:
A方案:
先把整个零件数学模型展开,进行零件的外形尺寸计算,先下料和垂直冲孔后拉延成形,共两套模具;
B方案:
先对整个零件数学模型进行工艺补充,后进行拉延成形,然后修边,最后冲孔,共三套模具;
C方案:
先对整个零件数学模型进行工艺补充,后进行拉延成形,先修一边冲孔,后冲孔和修另一边,共两套模具;
D方案:
先对整个零件数学模型进行工艺补充,后进行拉延成形,最后同时修边和冲孔,共两套模具。
2方案的论证与选择
A方案先对整个零件的展开,这就要求对整个零件的计算得非常准确,要展开整个零件不但要有很强的数学知识,而且又要有很强的软件应用能力,由于这个数学模型为非参数片体(unparameteied)特征,不是钣金特征,因此不能用PRO/E或UG下的钣金的模块进行展开,以本人的计算机知识用计算机目前是不能展开。
只能用手工进行计算,本人曾经参考过《钣金工展开程序计算》(王杨平,治金工业出版社出版),因为这是这个复杂的数学模型,有很多的复杂曲面,这需要非常复杂与大量的工作,而且计算那十一个孔的位置也是很难确定的,因此这十一孔的位置是以它们在汽车的位置进行设计的。
还有一个孔在成形中离边的距离很小只有4mm,很可能在后来的拉延成形的时候尺寸得不到保证,甚至有可能拉裂,位置有可能不准确,这对后来的安装天线架可能装不上去,因此本方案特别是展开存在理论的可能性,但实际操作起来可能行不通,或许有待软件的开发吧,还有存在工艺的缺陷,在目前的情况下虽然这个方案只有两套模具,减少了模具的制造成本,减少了生产周期但这个方案还是不可取。
B方案先采用了工艺补充,首先对零件进行工艺补充,压料面的补充等,得出拉深件,进行工艺补充后,改变了原来的零件冲压方向,进行压料面的工艺补充能够很好保证材料成形的速度的一致性,采用了加强肋,有效的防止了起皱,这有利于冲压件的顺利成形,经过工艺补充的拉延成形的零件,零件的外形尺寸的精度得到了很好的保证。
但是先进行修边,后进行冲孔,增加了整个模具的设计与制造的复杂程度,因此B方案也不是最佳的方案
C方案与B方案比较都是先进行工艺补充成拉深件后,再进行修边和冲孔,所不同的只是C方案采用了复合连续模,先冲一边后冲孔和修另一边,这样降低了模具的复杂程度,孔的形状尺寸和位置尺寸等也得到了很好的保证,且只使用了两套模具,降低了模具制造成本。
因此C方案是最佳的方案,也是本次设计采用的方案。
D方案,D方案进行工艺补充后,拉延成形,后同时修边和冲孔,这虽然保证了孔的位置尺寸和外形尺寸,但增加了模具的复杂程度,增加了模具制造的费用和时间,,因此D方案不是最佳的方案,
第二章拉延模的设计
一覆盖件拉深工艺设计
在进行汽车覆盖件拉深工艺的设计的时候,为了保证覆盖件在冲压中能够顺利的成形,首先要进行拉深件的设计,即根据冲压零件的图设计出拉深件图。
拉深件图不仅要有好的工艺性,而且要为后边的修边等工序创造良好的条件,如为修边工序预冲工艺孔、工艺缺口等。
拉深件的设计包括选择合理的拉深流动方向,工艺补充和压料面的设计等工作,然后选择其它工艺参数和设备参数。
1拉深方向的选择
汽车覆盖件的产品是按照其在车身上的安装位置绘制的,故大多数情况下与冲压时放置的位置不一致,所以必须将产品图所示的位置进行改变,选择一个最合适的位置使之有利于冲压过程的顺利进行,这就是选择拉深方向的过程。
(1)冲压方向对拉深成形的影响
汽车覆盖件拉深成形时,所选择的拉深冲压方向(以下简称拉深方向),是否合理,将直接影响:
凸模能否进入凹模、毛坯的最大变形程度、是否能最大限度地减拉深件各部分的深度差、是否能使各部分毛坯之间的流动方向和流动速度差比较小、变形是否均匀、是否能充分发挥材料的塑性变形能力、是否有利于防止破裂和起皱等质量问题的产生等。
也就是说,只有选择了合理的拉深方向,才能使拉深成形过程顺利实现。
(2)选择拉深方向的原则
1)保证能将拉深件的全部空间形状(包括棱线、肋条和鼓包等)一次拉深出来,不应有凸模接触不到的“死区”,即要保证凸模能全部进入凹模。
2)有利于降低拉深的深度。
拉深度太深,会增加拉深成形的深度,容易产生破裂、起皱等质量问题;拉深深度太浅,则会使材料在成形过程中得不到较大的的塑性变形,覆盖件的刚度得不到加强。
因此,所选择的拉深方向,应使拉深件的尝试适中,既能充分发挥材料的塑性变形能力,又能使成形过程顺利完成。
深度差最小,以减小材料流动和变形分布的不均匀性。
深度差大,材料流动性差;深度差小,材料流动和变形减小,有利于成形,便于确定合理的拉深方向,使进料阻力均匀。
3)保证凸模与毛坯具有良好的初始接触状态,以减少毛坯与凸模的相对滑动,有利于毛坯的变形,并提高冲压件的表面质量。
①凸模与毛坯的接触面积应尽量大,保证较大的面接触,避免因点接触造成局部材料胀形太大而发生破裂。
②凸模的包容角尽可能的保持一致,即凸模的接触点处于冲模的中心附近,而不偏离一侧,这样有利于拉深过程中法兰上各部分材料较均匀地向凹模内流入。
③凸模表面与毛坯的接触点要多而分散,且尽可能均匀分布,发防止局部变形过大,毛坯与凸模表面产生相对滑动
④在拉深方向没有选择余地,而凸模与毛坯的接触状态又不理想的时候,应通过改变压料面来改善凸模与毛坯的接触状态。
通过改变压料面,使凸模与毛坯的接触点增加,接触面积增大,能保证零件的成形质量。
⑤有利于防止表面缺陷。
对一些表面件,为了保证其表面质量,在选择拉深方向的时候,对重要的部分要保证不产生拉深时出现的偏移、颤动线等表面缺陷。
在进行拉深件的设计时,要将确定的拉深冲压方向明确标注在拉深件图上及冲压工艺文件上,标注冲压方向时,首先要能使模具设计人员、现场施工员及操作工人等明确辨明冲压方向而不引起异议;其次要能够使模具设计人员在进行模具设计时方便地确定拉深模中的唯一位置。
当拉深冲压方向垂直于拉深件的某一平面时,应以此平面为基准进行标注。
综合考虑,得出以下的零件的冲压方向:
2工艺补充部分的设计
(1)工艺补充的作用与对拉深成形的影响
冲压方向确定之后,为适应拉深工艺的要求,对绝大多数汽车覆盖件要将其形状、轮廓或深度进行工艺补充,设计出拉深件才能进行冲压成形。
工艺补充部分有两大类:
一类是零件内部的工艺补充,即填补内部孔洞,如本零件的装天线架的两个孔,创造出适合于拉深成形的良好条件(即使是开工艺切口或工艺孔也是在内部工艺补充部分进行),这部分工艺补充不增加材料消耗,而且在冲孔后,这部分材料仍可利用;另一类工艺补充是在零件沿轮廓边缘展开(包括翻边的展开)的基础上添加上去的,它包括拉深部分的补充和压料面两部分,这种工艺补充是为了选择合理的冲压方向,创造良好的拉深成形条件而增加的,它增加材料的材料的损耗(如本零件的外面部分)。
工艺补充部分的设计是冲压工艺的重要内容。
工艺补充设计的合理与否,也是冲压设计先进与否的重要标志,它直接影响到拉深成形时工艺参数、毛坯的变形条件,变形量大小,变形分布,表面质量,破裂,起皱等质量问题的产生等。
(2)工艺补充的设计原则
1)内孔封闭补充的原则,对内部有孔的零件,首先要将孔洞部分进行封闭补充,使零件成为无内孔制作。
但若该部分属于内部的局部成形部分则要进行变形分析。
一般这部分成形属于胀形成形,若其胀形变形超过材料的极限变形,需要在工艺补充部分预冲孔或切口,以减小胀形变形量。
2)简化拉深件结构形状原则,拉深件的结构形状越复杂,拉深成形过程中的材料的流动和塑性变形就越难控制。
所以,零件外部的工艺补充要有利于使拉深件的结构、形状简单化,越接近于基本形状零件,冲压成形过程中的材料的流动和塑性变形就越容易控制。
3)对后工序有利原则,设计工艺补充时要考虑对后工序的影响。
要有利于修边等后工序中件的定位稳定、可靠,尽量能够进行垂直修边、垂直翻边,以便于采用结构简单的模具。
在进行工艺补充时,要考虑到模具压料面或拉深肋槽的修理时,不能影响到修边线;保证修模的凸模和凹模能有足够的强度;凸模和凹模的圆角的大小有利于毛坯的变形和塑性流动等。
在本零件的工艺零件的压料面的一部分就是覆盖件的法兰面。
拉深使用中,模具的压料面要进行调整,并且在使用一段时间之后要对已产生磨损的拉深肋和拉深肋槽进行打磨加工,为不使其影响到修边线,为不使其影响到修边线,一般修边线到拉深肋的距离为25mm,修边线到凸模圆角的距离应保证在使用中不致因凸模圆角的磨损而影响到修边线,一般取3~5mm,凸模圆角半径就根据拉深深度和形状来确定,一般3~10mm。
对拉深深度浅的和直线部分取下限,对于拉深深度深的和形状复杂部分取上限。
凹模圆角半径对拉深毛坯的流动和阻力影响极大,其大小必须合适,当凹模圆角半径也是工艺补充的组成部分时,rd取8~10mm;当凹模圆角部分本身就是覆盖件的组成部分时,首先要保证拉深成形工艺的要求,若因此而导致rd大于零件要求的圆角半径,则要在以后的工序中进行修整圆角。
综合考虑了上面的因素,得出了以下的工艺补充的示意图
3压料面的设计
(1)压料面的作用是对拉深件的影响
压料面是指凹模圆角以外的且在拉深开始时,凹模与压边圈压住毛坯的部分。
它是工艺补充的一个重要组成部分,对汽车覆盖件的成形起着重要的作用。
本零件的拉深件的压料面全部为工艺补充部分,有的拉深件的压料面则由零件的法兰部分和工艺补充部分共同组成。
在拉深开始前,压边圈将毛坯压紧在凹模压上,拉深后,凸模的作用力与压料面上的阻力共同形成毛坯的变形力,使毛坯产生塑性变形,实现拉深成形过程。
通过压料面的变化,可能使拉深件的深度均匀,毛坯流动阻力的分布满足拉深成形的需要。
压料面设计得是否合理,直接影响到压料毛坯向凹模内流动的方向与速度、毛坯变形的分布与大小,破裂起皱等问题的产生。
压料面设计不合理,还会在压边圈压料时就形成皱折、余料、松驰等。
(2)压料面的设计原则
设计压料面是要考虑两种情况,一种是压料面的一部分就是拉深件的法兰面,这种拉深件的压料面的形状已定,一般不改变其形状,即使显了改善拉深成形条件而作局修改,也是在后工序中进行整形校正。
另一种情况是压料面全部属于工艺补充部分(如本零件)。
后一种情况下,主要以保证良好的拉深成形工艺条件为主进行压料面的设计。
1)压料面形状尽量简单化,以水平平面为最好。
在保证良好的拉深条件下,为减少材料消耗,也可以设计成斜面,平滑曲面(如单曲面、锥面)或平面曲面组合等形状。
但是不要设计成平面大角度交叉,高度变化剧烈的形状,或在压料面上有凸起或凹坑。
因为这些形状的压面会造成材料的极不均匀分布,在拉深成形时产生起皱、堆积、破裂等现象。
2)水平压料面应用最多,其阻力变化相对容易控制,有利于调模时调整到最有利于拉深成形所需的最佳压料面阻力状态。
向内倾斜的压料面,对材料流动阻力较小,可在塑性变形较大的深拉深件的拉深时采用。
但为保证压边圈强度,一般控制压料面倾斜角a<40°~50°。
向外倾斜的压料面的流动阻力最大,对浅拉深时可增大毛坯的塑性变形。
但倾斜角太大,会使材料流动条件变差产生破裂。
3)压料面断面曲线长度要小于拉深件内部断面线的长度。
一般认为,汽车覆盖件的冲压成形时各断面上的伸长率达到3%~5%时,才有较好的形状冻结性。
最小伸长率不应小于2%。
因此,合理的压料面要保证拉深件各断面的伸长率达到3%以上。
如果压料面的断面曲线长度不小于拉深件内部断面曲线的长度,拉深件上就会出现余料、松弛、皱折等。
4)压料面应使成形深度小且各部分深度接近一致。
这种压