电炉锌粉操作规程.docx
《电炉锌粉操作规程.docx》由会员分享,可在线阅读,更多相关《电炉锌粉操作规程.docx(28页珍藏版)》请在冰豆网上搜索。
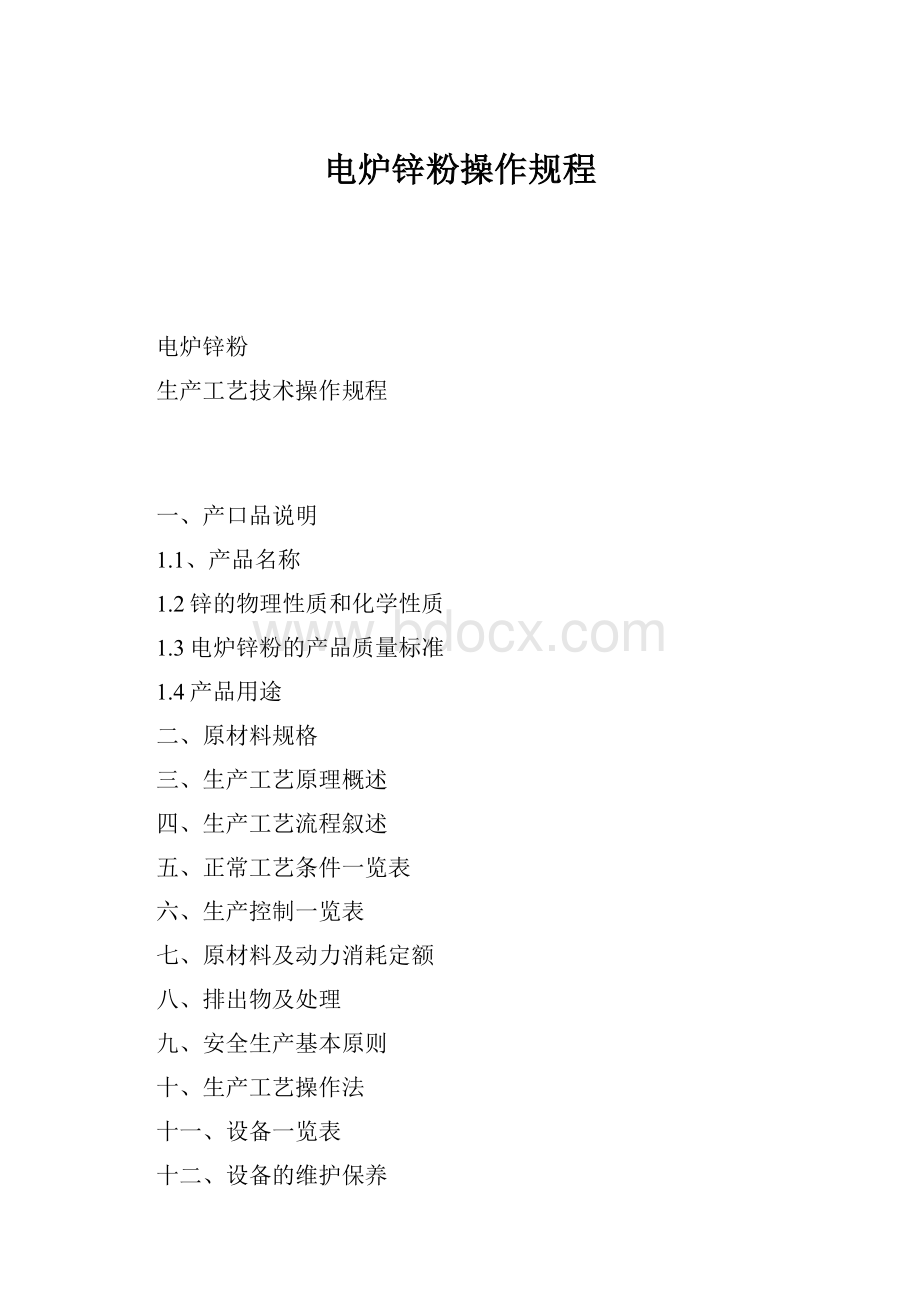
电炉锌粉操作规程
电炉锌粉
生产工艺技术操作规程
一、产口品说明
1.1、产品名称
1.2锌的物理性质和化学性质
1.3电炉锌粉的产品质量标准
1.4产品用途
二、原材料规格
三、生产工艺原理概述
四、生产工艺流程叙述
五、正常工艺条件一览表
六、生产控制一览表
七、原材料及动力消耗定额
八、排出物及处理
九、安全生产基本原则
十、生产工艺操作法
十一、设备一览表
十二、设备的维护保养
十三、常见故障及处理
十四、分析规程(略)
1、产品说明
1、1产品名称:
锌粉(Zincdust)
分子式:
Zn分子量:
65.38
1.2锌的物理性质和化学性质
1.2.1锌的物理性质
锌外观为银灰色;锌粉无味;熔点419.5℃;沸点906℃;密度:
常温固态时为7.14克/厘米3;锌不溶于水。
锌结晶为六面体,汽化热:
102.1千焦/摩尔。
1.2.2锌的化学性质:
锌在常温下和干燥的空气中稳定,但在红的热的温度时,锌易被氧化生成氧化锌。
在潮湿的空气中易氧化,生成碳酸锌薄膜,保护内部的锌不再被氧化和侵蚀。
二氧化碳及水蒸汽均使锌蒸汽氧化,使火法炼锌受到一定影响。
锌在熔融时能与铁形成化合物。
纯锌不溶于任何浓度的硫酸和盐酸中。
但商品锌含少量杂质就极易被硫酸和盐酸溶解,同时放出氢气:
Zn+H2SO4=ZnSO4+H2↑
Zn+2HCl=ZnCl2+H2↑
商品锌还可以溶于碱中,但在碱中溶解速度要比酸中慢。
锌在电化次序中处于比较活泼的位置,能从很多金属溶液中置换出多种重金属。
在1273K(10000C)时,锌能在空气中燃烧,生成氧化锌。
2Zn+O21273K2ZnO
锌能与许多金属组成各种合金。
1.3电炉锌粉的产品质量标准
桂Q/LYB5—83
指标名称
一级锌粉
二级锌粉
有效锌含量%≥
86
82
硫含量%≤
0.54
1.0
细度(80目筛)
全部通过
全部通过
1.4产品用途
金属锌有着广泛用途,在国民经济中占有重要地位。
锌粉主要用于:
镀锌工业、制造合金和锌的化合物。
氧化锌在橡胶工业中用作添加剂,在化学工业中用作白色颜料。
锌还用于制造富锌底漆、富锌涂料、磷化锌、保险粉、染料等。
在冶金工业中,利用锌从氰化溶液中置换金,在粗铅精炼时用于提取贵金属;在湿法炼锌生产过程中净化溶液,除去铜、镉等杂质;在炼镉过程中用锌粉净化溶液,并且置换镉等。
2、原料规格
2.1含锌物料:
锌熟砂、锌白炉渣、铸型锌渣等。
要求含金属锌达80%,水份小于0.4%。
2.2焦碳:
粒度10—40mm,含固定碳80%以上,含水份小于0.4%,灰份<18%,挥发份<2%。
2.3石灰:
含有效成份CaO≥90%,粒度小于50mm。
3、生产工艺原理概述
电炉法制造锌粉,是利用三相电弧炉内,通过电弧将电能转变为热能,同时焦碳燃烧亦产生热量,产生高温(10000C以上)的条件下,将含锌物料中的锌,在焦碳造成的还原气氛下锌被还原出来,生成锌蒸汽(升华),并将锌蒸汽导入冷却系统中经冷凝捕集而获得固体粉未状的金属锌粉。
3.1含锌物料中的锌,一般以氧化锌(ZnO)、硫酸锌(ZnSO4)、铁酸锌(ZnO.Fe2O3)等形式出现,但主要是以氧化锌形式出现,当然,铸型锌渣中,亦会有大量的金属态锌。
两阶段理论认为:
在高温条件下,金属氧化物离解析出氧:
ZnO=Zn+1O2
氧与碳反应生成二氧化碳:
C+O2=CO2
在碳过量而氧不足的情况下,二氧化碳与碳反应生成一氧化碳:
CO2+C=CO
综述上面的反应为:
ZnO+CO=Zn+CO2
由于一氧化碳气体能很好地与固体金属氧化物接触,故反应比较快。
当然,固体金属氧化物也可以与固体碳起反应:
ZnO+C=Zn+CO+237507.6kJ
2ZnO+C=2Zn+CO2
但由这种还原过程的进行只发生在固体碳与氧化物接触的表面上,很难向金属氧化物内部扩散,反应进行得很慢。
故主要靠CO还原锌。
沸点低于或相近于锌的沸点的其他金属亦会被还原出来,成为杂质,影响锌粉的质量。
还原锌过程需要大量的热,所以要消耗大量的电能。
3.2混合炉料中焦碳的作用:
焦碳用作含锌原料的还原剂以及作炉料的导电体和传热体,焦碳的类型、数量及粒度对电炉操作及效率有很大影响,并且在一定功率和操作电流下,影响着三相电极的位置。
焦碳粒度的大小,直接影响到炉内反应的接触面的大小。
焦碳的粒度过大,则反应接触面减小,反应不易完全,并可能造成剩余焦碳在炉内积存,增加了炉料的导电能力,致使电极位置上移,炉气温度和粉尘量显著增加,恶化电极操作。
相反,焦碳的粒度减小,则焦碳的表面积增加,有利于反应趋于完全,亦能得到较高的电流,降低了电极的消耗,又便于炉内过剩的焦碳从出渣口排出,减轻焦碳在电炉内的积存现象,有利于稳定操作。
但是,焦碳的粒度过小,虽然能给生产带来好处,但却降低了焦碳破碎设备的生产能力,增加焦碳的细粉量极容易吸入冷凝器中,造成产品质量降低,杂质含量增高。
我厂对焦碳粒度要求控制在10—40mm之间。
焦碳的用量对电炉中的反应有很大影响,焦碳用量大,更多地造成还原气氛,有利于含锌物料中的氧化锌还原出来,但焦碳过多将增加炉料的导电能力,恶化电极操作,造成电极位置升高,出渣困难。
而焦碳量不足,则不利于氧化锌的还原,也势必造成从石墨电极中夺取碳而增加电极的消耗量,同时也造成从炉底炉壁的衬里碳砖中夺取碳而使炉体烧穿,影响电炉的寿命。
一般焦碳用量应稍大于理论计算用量。
3.3混合炉料中石灰的作用:
炉料中氧化钙能加快还原反应的进行,生成熔点低、流动性好的炉渣便于从出渣口排出,使电炉能够连续运转。
炉渣的熔点决定于炉渣中(MgO+CaO)/(SiO2+Fe2O3)的重量百分比值(称为碱度比)。
碱度过大,易形成泡沫渣,同进炉渣的副反应就增多,增加电耗,对电炉的碳素砖侵蚀也大。
加入石灰,能改善渣型,减少泡沫渣的生成,有利于出渣,实际采用的碱度比为1.1—1.2来生产较适宜。
过多的氧化钙会与过量焦碳起反应生成乙炔:
CaO+3C=CaC2+CO↑
生成的CaC2(乙炔)存在于炉内,既使出渣困难,又可能在出渣时,乙炔随着灼热的炉渣一起冲击,遇水后而引起空气爆炸。
4、生产工序及工艺流程叙述
4.1工艺流程图见附图1。
4.2工艺流程叙述
供料工序按照厂部下达的配料比,将各种原料——锌焙砂、熔铸渣等含锌物料、焦碳、石灰等经计量后,用小车送入烘干炉。
原料在600℃温度下(注意:
焦炭不能着火),除去物料中多余的水分,使出烘干炉的物料含水量应小于0.4%。
经烘干的原料经混合均匀后,用电动葫芦吊至料架上,由螺旋给料机定时定量将原料加入电炉内。
原料在电炉内经三相电弧打弧燃烧产生12000C高温下,含锌物料中的ZnO被CO和C所还原,生成锌蒸气。
由于电炉内所产生的高温炉气,体积膨胀,压力大于后部冷却系统的气压,使系统形成正压,所以系统不用引风机亦能使炉气顺利地进入后部的冷却系统。
电炉出来的高温含锌炉气,进入冷却器、第一惯性除尘器、第二惯性出尘器。
由于冷凝降温及重力的作用,电炉气中的锌粉被捕集下来,用小车装粉送至筛分机,经80目筛子筛分后,筛下物经计量装入铁桶而成为成品,筛余物则返回电炉作二次冶炼回收。
最后电炉气经布袋除尘器,收集细微的锌粉,使炉气达标后而排入大气中。
4.2.1供料工序
4.2.1A目的要求
本工序的主要任务是提供给电炉生产所需要的一定配比、一定水份含量的合格炉料。
4.2.1B供料工序工艺流程
按照厂部下达的配比要求,将各种锌物料、焦碳、石灰等原料,经小车计量后,加入烘干炉内。
烘干炉的热源由煤燃烧室提供。
各种原料在炉内6000C高温烘焙(注意:
焦碳不能着火)下,水份被蒸发出来,要求物料最终含水量不大于0.4%。
烘干后的物料按配比混合均匀后,装入料桶,用电动葫芦吊至料架上的下料桶,送入螺旋给料机,定时定量向电炉供料。
4.2.1C配料经要求
基准:
1000kg锌为基准,配料比为:
Zn:
C:
CaO=1000:
205:
92
4.2.2炉面工序
4.2.2A目的要求
本工序主要任务是把合格炉料和电能输入电炉内,通过电能变热能,俣炉料中的含锌物质(ZnO)与焦碳、一氧化碳起反应还原出锌,产生含锌蒸气的高温电炉气。
4.2.2B炉面工艺流程
炉面工序所需的合格炉料由螺旋给料机定时定量供给,所需的热量由三相石墨电极把三相交流电能通过打弧而变为热能。
炉料在助溶剂石灰的存在及12000C高温下,焦碳、一氧化碳还原ZnO,生成高温的含锌蒸气的电炉气。
在压力差的作用下,电炉气出电炉而进入炉气冷却收尘系统。
4.2.3炉前工序
4.2.3A目的要求
定期排出电炉内的炉渣,以保证电炉生产连续进行。
4.2.3B工艺流程
当炉内渣位超过出渣口20—25cm时,应该把炉内渣排出,以保证电炉能连续进行生产。
出渣前一班下料分4—5次投完,并保证提前二小时下完料;出渣后的第一班下料应分5—6次投完,待下一班生产时按正常生产分7次投完。
出渣前要清理排渣槽并检查水泵。
出渣时,应切断电源,用钢钎打穿出渣口,让炉渣流出。
炉渣流完后,用耐火泥堵上出渣口。
4.2.4冷却收尘工序
4.2.4A目的要求
冷却电炉炉气,收集电炉锌粉,筛分包装成品电炉锌粉。
4.2.4B工艺流程
出电炉的高温含锌炉气,依次进入冷却器,——人字管——第一惯性收尘器——第二惯性收尘器,通过热交换和重力的作用,从而捕集炉气中的锌粉。
定期取出各器中锌粉,待冷却至400C以下,通过80目筛分机筛分,筛下物为电炉锌粉,装入桶内;筛余物返回电炉二次冶炼回收。
4.2.5尾气工序
4.2.5A目的要求
利用布袋收尘器收集细微的锌粉,过滤后炉气(主要含CO)经烟囱排入大气中。
4.2.5B工艺流程
由第二惯性收尘器来的电炉气,沿夹带有少量的细微锌粉,必须再经过布袋除尘器进一步捕集,然后废气才从烟囱排入大气中。
4.2.6冷却水工序
电炉法生产锌粉工艺中所用的水作为电炉炉壁冷却水套、冷凝器水管中的冷却水,没有其它杂质渗入,不成为污水,故不需要加以处理,有条件的话也可采用循环使用,减少用水量。
5、正常工艺条件一览表
工序
指标名称
温度0C
压力pa
电流A
电压V
备注
供
料
配料比
1000:
205:
92
烘干温度
6000C
干物料含水量
0.4%
炉
面
一次电压
10000V
一次电流
34.64A
二次电压
90—110V
二次电流
3149—3849A
炉内温度
12000C
炉壁水箱水温
<900C
炉顶温度
10000C
炉气出口温度
12000C
电极升降行程
45—100Cm
出
渣
放渣时渣位
高于出渣口20—25cm
两次出渣间隔时间
1-2天
冷
却
收
尘
冷凝器水温度
进水200C
第一惯性收尘器水温
进水200C
第二惯性收尘器水温
进水200C
筛分细度
过80目筛
尾
气
布袋进口温度
1200C
布袋出口温度
1200C
废加成份含量
CO
6、生产控制一览表
工序
控制项目
控制频次
控制指标
分析方法
控制者
供
料
配料比
每班一次
原料Zn≥67%
C>80%
CaO>90%
配料工
烘干物料量
配料工
烘干温度
配料工
烘干物料含水量
低于0.4%
配料工
螺旋机下料量
配料工
炉
面
二次电压
90-110V
电炉工
二次电流
3194A-3849A
电炉工
电极升降行程
45-100Cm
电炉工
炉内温度
1200℃
电炉工
炉顶温度
1000℃
电炉工
炉气出口温度
1200℃
电炉工
炉壁水箱水温
<90℃
电炉工
炉
前
出渣渣位
超过渣口20-25Cm
探渣
炉前工
出渣间隔时间
1-2天一次
炉前工
炉渣含锌量
冷
却
收
尘
冷凝器水温
进水20℃
冷凝器出粉
每小时一次
一惯器水温
进水20℃
一惯器出粉
每四小时一次
二惯器水温
进水20℃
二惯器出粉
每四小时一次
电炉锌粉质量
每班一次
Zn≥88%
化验
化验员
尾
气
尾气布袋收尘
每班一次
取料工
进布袋炉气温度
120℃
取料工
7、原材料及动力消耗定额
序号
名称
单位
规格
耗实物(1吨100%产品计算)
备注
1
含锌物
T
Zn≥80%
1.03
2
焦碳
T
C≥80%
0.22
3
烟煤
T
0.14
4
电极
T
0.027
5
石灰
T
CaO≥90%
0.12
6
电
KWh
交流
4500
7
水
T
自备深井泵循环用水
8
粉袋
个
20
9
粉桶
个
20
10
合格率
%
100
11
回收率
%
93
8、排出物及处理
8.1废气
电炉生产的炉气,经过冷凝器、第一惯性出尘器、第二惯性出尘器收集锌粉,最后排出烟气经布袋捕尘后排入天空。
8.2废渣
由于采用锌焙砂和熔铸渣作原料,废渣量较少,渣的主要成份是煤渣,可作填路或制砖用。
8.3废水
本生产过程所用水为炉壁冷却水套的冷却水,无杂质渗入,故不需要加以处理,并采用循环用水,减少用水量。
9、安全生产基本原则
9.1工作时必须穿戴劳动保护用品,操作电器设备必须穿戴好绝缘防护用品。
9.2楼梯要有扶手,平台要有栏杆。
9.3对所有钢结构的平台、楼梯、屋架要定期检查是否牢固可靠,定期作防腐处理。
9.4所有电器设备都必须可靠接地。
9.5备料行车和电动葫芦在吊物料时,吊物下面严禁站人。
9.6电炉在下料时,应先将炉顶送料系统进行检查,是否有障碍物,如果有,要打通后方能下料。
在打下料包时,要注意冲火,以免伤人。
严禁伸头从下料口往炉内看。
9.7出粉前应先将烟管、人字管清理好,在出粉过程中不准调整电流。
9.8更换和加接电极时,要停电操作,炉顶要放好防塌木板。
9.9不加料,不出渣,不加电极时,电炉顶和渣口严禁站人。
9.10放渣前首先开冲渣水,渣槽内保持干燥,畅通无阻碍物,附近严禁存放易燃物品。
在打开渣口时,扶钢钎的人和打锤人不得在同一方向,扶钎人要戴手套,而打锤人不得戴厚手套打锤。
当渣放出时,渣槽附近及水池边严禁站人,防止渣爆伤人。
9.11炉壁水套及冷却水管必须保持长流水,且水温不得超过90℃。
9.12打炉喉时,拉开冷却器时要迅速、安全,注意冲火和放炮。
9.13冷却器防爆孔破裂时,应立即拉出冷却器,重新换上纸片封好,严禁在未拉开冷却器进行作业。
如果耙粉杆折断,应把安全闸板闸好后,方能更换耙杆。
9.14锌粉仓库和筛粉房严禁烟火,锌粉温度超过40℃和正在燃烧的粉不能筛。
9.15装卸和筛粉时,必须戴防尘口罩,工作完毕要进行洗漱。
9.16严禁变压器超负荷使用,如变压器声音异常,应立即通知电工检查,待处理好后方能使用。
9.17转动设备进行修理时,必须先停车,再拉下电门开关,切断电源,并在电门开关上挂“有人修理,严禁合闸”的警告牌,然后才能进行修理。
9.18颚式破碎机用皮带传动设备上的皮带轮必须有防护罩。
9.19筛粉房电器开关上必须有防尘罩。
9.20遇到炉子严重漏水、漏渣、失火、放炮等,危及操作人员人身安全时,应立即切断电源,向厂级领导报告。
9.21耙粉不能耙得过满,发现粉箱内着火后应立即用锌砂盖好、封严,不得用水淋,但可以用干粉灭火器灭火。
9.22接班时,带班人要认真听取交班人的安全情况介绍和认真检查设备运行情况,发现有不安全的因素要及时提出,并请有关人员处理好后方能使用。
10、生产工艺操作法
10.1生产操作法
10.1.1供料工序操作法
10.1.1A备料:
清除物料中的铁件、泥块等杂物,不合规格的物料按要求进行过筛和破碎处理,按配料单把各种物料认真过磅,然后用吊车吊至烘干炉顶,放入烘干炉内,进行焙烘。
每班烘一炉,炉内温度在600℃左右,不准开炉门鼓风。
每炉料翻料时要关上烟囱闸板,不准开鼓风机翻料。
每炉料至少要翻料四次,保证出炉料水份在0.4%以下,认真记录耗煤量。
10.1.1B拌料:
将出炉料冷却后按配料单在铁板上拌匀。
注意捡出大于进料规格的物料进行破碎,以免堵塞螺旋下料机。
10.1.1C进料:
把烘料匀筛后装入料桶,用行车吊到电炉架上,进行投料。
投全料时,按每小时一次,分6-7次投完;放渣前,分4-5次,提前两小时投完;放渣后,分5-6次投完。
正常投料时电流降至1600A,投完料后将电流回升到2500A。
一般不准超过2800A。
如果下料口堵塞,应立即停机分闸,进行人工通料口,畅通后方能继续投料。
10.1.2炉面工序操作法
各水管保持长流水,炉壁水套温度保持在90℃以下。
水温的高低用进水量调节;调节电流及电极的位置,维持三相电流平衡,以保证炉内的微正压,有利于出粉;如果水箱漏水,应停炉修理好后才能重新开炉生产。
10.1.3炉前工序操作法
10.1.3A渣位超过渣口20-25Cm时应放渣。
一般每隔1-2天放渣一次。
放渣前一班与放渣后当班应减少50%的料投入炉内,并保证在放渣前两小时下完料。
10.1.3B先提起电极离开渣面,断电后再进行出渣工作。
打渣口前,先检查冲渣水泵情况是否正常,以保证出渣安全。
渣槽内要保持干燥,渣沟要畅通无阻,附近严禁堆放易燃物品。
在打出渣口进,扶钎人与打锤人不得站在同一方向。
10.1.3C放完渣后用耐泥堵好渣口,可投料进行生产,电流逐步升温到放渣前的电流,以防因渣层薄而烧坏炉底,下一班再按正常电流生产。
10.1.3D如果需要清理炉喉,可在出渣后进行;在做好准备后,迅速安全松开人字管,拉开冷凝器。
清理时,要一步一步向外耙,不得推向炉内引起冲火。
清理完后再装好冷凝器、通电升温到正常生产电流时,进行正常生产。
10.1.4出粉工序操作法
10.1.4A冷凝器每小时出粉一次;第一惯性收尘器、第二惯性收尘器正常情况下,每四小时出粉一次,出粉前先用木锤依次震击烟囱、第二惯性收尘器、第一惯性收尘器、人字管、冷凝器,保证系统畅通。
10.1.4B出粉前,拉开出粉口闸板,用耙杆将粉耙入粉箱,耙满后,关牢闸板,并耙少量粉盖在闸板上,增加密封性。
打开粉箱门板,用拉钩钩出粉箱,再用脚慢慢将空箱推进室内,关上门板。
出粉时必须稳定电流,遇到粉中有火时可用锌砂盖封牢,出完粉及时通炉喉。
10.1.4C将取出的粉认真过磅,冷却到40℃以下,通过80目筛粉机筛粉,成品装包堆放好。
10.1.4尾气工序操作法
每班打布袋两次。
打布袋时,必须两个人在场,一人监护,一人操作,注意站在风口上方,防止CO中毒。
10.2电炉的开炉和停炉操作法
10.2.1开炉
10.2.1A正式开炉前,须全面检查炉体、导电系统,运输系统是否符合要求。
10.2.1B经检查无问题,才进行铺料。
铺旧炉渣4吨。
石灰300公斤和旧炉渣拌匀。
焦碳:
300公斤。
10.2.1C按照升温表烘炉
天数温度达到天数温度达到
1-2200-250℃8700-850℃
3250-500℃9850℃
4500℃保温10850℃
5500℃11850-900℃
6500-600℃12900-1000℃
7600-700℃131050℃探渣
说明
a、升温时温度差波动在±20℃,超过温度不能降低。
b、升温到850℃时,装上冷凝器。
c、升温到1000℃,取出热电偶。
d、探测渣位到20Cm以上开始按配料单加料。
10.2.2停炉
10.2.2A停炉前四小时停止加料。
10.2.2B放出电炉渣,提起电极,切断电源。
10.2.2C取出冷凝器存粉,使炉体自然冷却或加水冷却。
10.3电极的安装
10.3.1更换新电极前,应先检查电极的螺纹是否完整洁净。
10.3.2将准备安装的电极用吊车吊到适当高度,对准两条电极螺纹口,使其缓慢靠拢,然后旋紧,再松动电极夹,用吊车将电极提到一定的高度时,再将电极夹旋紧。
10.4高压开关柜
结构和性能
高压开关柜:
由隔离开关、油开关、电流互感器、断电器、保护装置、操作机构、指示仪表和外壳组成。
设备额定电压为10KV,额定电流为40A,属于溶压设备。
用途:
用于电炉变压器供电、停电之用。
10.4.1合闸操作
10.4.1A合闸前须检查变压器、开关柜上是否有遗物,三相电极应提起,电表指示为零。
10.4.1B先合隔离开关:
用左手将隔离开关手柄上的机械锁拉开,用右手向上推开关手柄刻刀闸合到位,将机械锁拉入卡位,隔离开关合实。
10.4.1C将合闸手柄位出,顺时针压到合位,此时油开关合闸,变压器有电,高压柜上红灯亮,绿灯亮分闸合指示牌显示“合”,合闸完毕。
10.4.2分闸操作
10.4.2A先将电炉三相电极提起。
10.4.2B观察高压柜电流是否有电流,电流表无指示说明电极提起完毕。
10.4.2C右手握住分闸手柄向逆时针方向指至分位,此时柜上红灯亮,绿灯亮,机构分电显示“分”,变压器停电。
10.4.2D用左手拉开隔离开关的机械锁,用右手向下拉隔离开关的手柄,至隔离开关完全分开,手柄打至下方,机械锁将手柄锁上为止,至此高压分闸完毕。
10.4.2E挂上“有人操作,严禁合闸”的警告牌,方可进行操作。
10.4.3高压柜巡视内容
进入运行后,每班必须对设备进行巡检,其内容如下:
10.4.3A从窥视孔检查油开关、油标、油位,不得低于油标的1/3。
10.4.3B隔离开关的油开关上的瓷瓶是否有裂纹或爬电(有吱……响声)。
10.4.3C电流表指示是否灵活。
10.4.3D各部接头有否发热变色现象。
10.4.3E电度表是否转动。
10.4.4高压开关柜安全规范
10.4.4A进行合闸操作时,必须两人进行,严格遵守安全操作规程,穿戴好绝缘防护用品,技术较熟练的负责监护,技术较低的进行操作,操作人员重复指令一次,双方确认无误时,方可操作,操作完毕填好记录。
10.4.4B操作者必须站在绝缘木板上,并戴好绝缘手套,穿好绝缘鞋。
10.4.4C探视开关闸内部时,绝对不允许将开关闸的上下门打开,只能从窥视孔巡视。
10.4.4D电炉正常生产,无异常变化,严禁任何人乱动高压闸上一切揿扭。
10.4.4E非操作人员严禁靠近开关闸。
10.4.4F合闸时必须先合隔离开关,后合油开关,分闸时必须先分油开关,再