车身焊装夹具设计知识.docx
《车身焊装夹具设计知识.docx》由会员分享,可在线阅读,更多相关《车身焊装夹具设计知识.docx(20页珍藏版)》请在冰豆网上搜索。
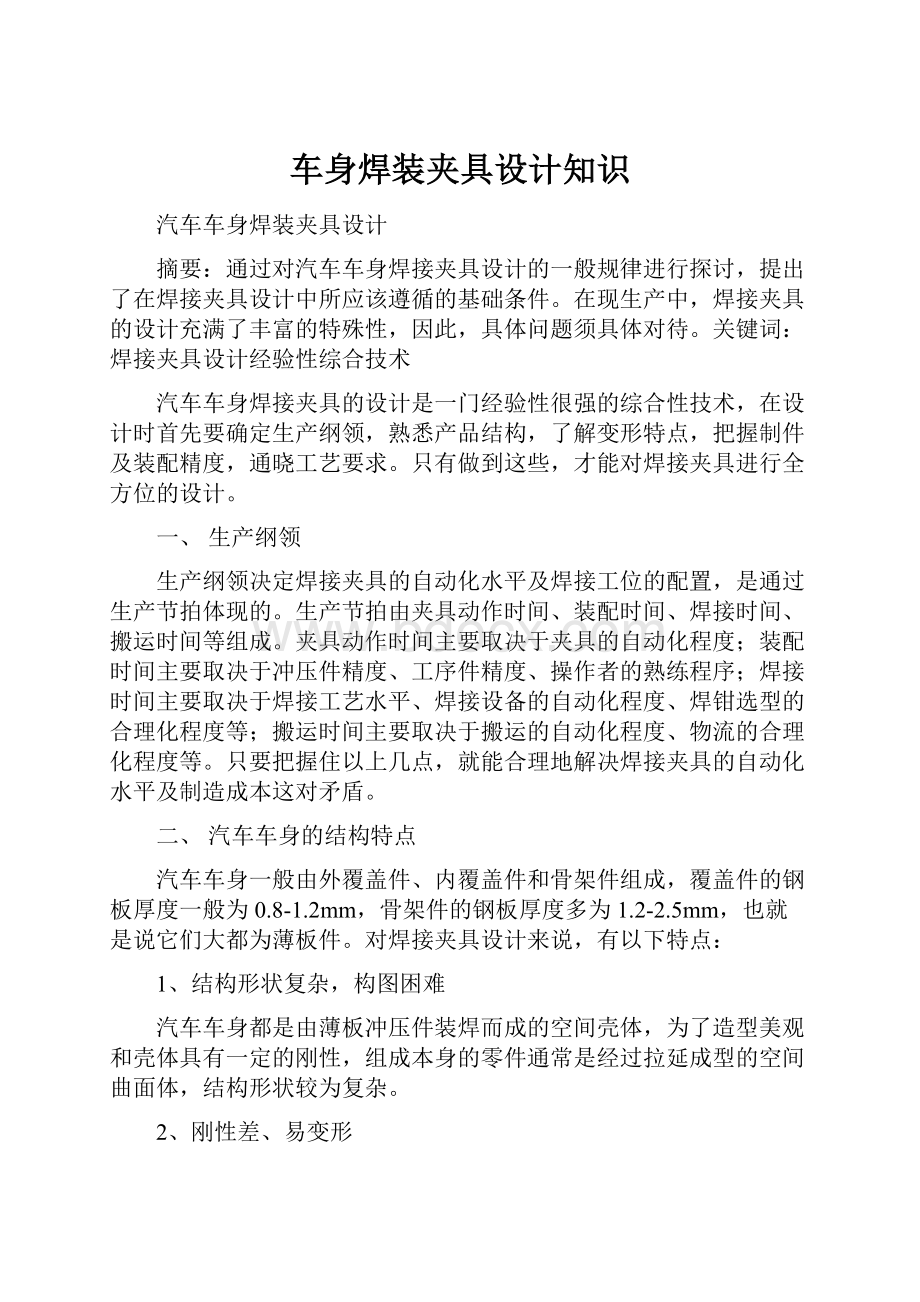
车身焊装夹具设计知识
汽车车身焊装夹具设计
摘要:
通过对汽车车身焊接夹具设计的一般规律进行探讨,提出了在焊接夹具设计中所应该遵循的基础条件。
在现生产中,焊接夹具的设计充满了丰富的特殊性,因此,具体问题须具体对待。
关键词:
焊接夹具设计经验性综合技术
汽车车身焊接夹具的设计是一门经验性很强的综合性技术,在设计时首先要确定生产纲领,熟悉产品结构,了解变形特点,把握制件及装配精度,通晓工艺要求。
只有做到这些,才能对焊接夹具进行全方位的设计。
一、生产纲领
生产纲领决定焊接夹具的自动化水平及焊接工位的配置,是通过生产节拍体现的。
生产节拍由夹具动作时间、装配时间、焊接时间、搬运时间等组成。
夹具动作时间主要取决于夹具的自动化程度;装配时间主要取决于冲压件精度、工序件精度、操作者的熟练程序;焊接时间主要取决于焊接工艺水平、焊接设备的自动化程度、焊钳选型的合理化程度等;搬运时间主要取决于搬运的自动化程度、物流的合理化程度等。
只要把握住以上几点,就能合理地解决焊接夹具的自动化水平及制造成本这对矛盾。
二、汽车车身的结构特点
汽车车身一般由外覆盖件、内覆盖件和骨架件组成,覆盖件的钢板厚度一般为0.8-1.2mm,骨架件的钢板厚度多为1.2-2.5mm,也就是说它们大都为薄板件。
对焊接夹具设计来说,有以下特点:
1、结构形状复杂,构图困难
汽车车身都是由薄板冲压件装焊而成的空间壳体,为了造型美观和壳体具有一定的刚性,组成本身的零件通常是经过拉延成型的空间曲面体,结构形状较为复杂。
2、刚性差、易变形
经过成型的薄板冲压件有一定的刚性,但和机械加工件相比,刚性要差得多,而且单个的大型冲压件容易变形,只有焊接成车身壳体后,才具有较强的刚性。
3、以空间三维坐标标注尺寸
汽车车身产品图以空间三维坐标来标注尺寸。
为了表示覆盖件在汽车上的位置和便于标注尺寸,汽车车身一般每隔200mm或400mm划一坐标网线。
三个坐标的基准是:
前后方向(Y向)———以汽车前轮中心为0,往前为负值,往后为正值;上下方向(Z向)———以纵梁上平面为0,往上为正值,往下为负值;左右方向(X向)———以汽车对称中心为0,左右为正负。
三、装配精度
装配精度包括两方面内容:
外观精度与骨架精度,外观精度指车门装配后的间隙面差,骨架精度指三维坐标值。
货车车向的装配精度一般控制在2mm内,轿车控制在1mm内。
焊接夹具的设计既要保证工序件之间的焊装要求,又要保证总体的焊接精度,通过调整工序件之间的匹配状态来满足整体的装配要求。
四、6点定则在车身焊装夹具上的应用
6点定则指限制6个方向运动的自由度,在设计车身焊装夹具时,常有两种误解,一是认为6点定位则对薄板焊装夹具不适用;二是看到薄板焊装夹具上有超定位现象,产生这种误解的原因是把限制6个方向运动的自由度理解为限制6个方向的自由度,焊接夹具设计的宗旨是限制6个方向运动的自由度,这种限制不仅依靠夹具的定位夹紧装置,而且依靠制件之间的相互制约关系。
只有正确认识了薄板冲压件焊装生产的特点,同时又正确理解了6点定则,才能正确应用这个原则。
从定位原则看,支承对薄板来说是必不可少的,可消除由于工件受夹紧力作用而引起的变形。
超定位使接触点不稳定,产生装配位置上的干涉,但在调整夹具时只要认真修磨支承面,其超定位引起的不良后果是可以控制在允许范围内的。
80年代,车身焊接使用的大量夹具其型式是从冲压模具的定位面截切而来,即在车身冲压零件的型腔上定位,它被称为“定位块”,其特点是定位面积大,据统计投影面积在50×100以上。
定位块是加工件,其余支撑部分为铸铁件,定位块在装配调整后再配作定位销。
在外观上它有两种式样:
大面积的定位块,小面积的气动或手动压头;大面积的定位块,大面积的气动或手动压头。
前者造成定位块加工复杂,产生车身零件压紧力不够,后者干涉焊钳的点焊操作及装件困难。
在生产中使用的夹具,其精度必须保证产品总成的要求;其选择定位面的数量也是比较保守的,宁多勿少。
另外,每个定位块的装配全部是用四个螺钉在沉孔中固定在焊接支承底板上,因焊渣飞溅的填充,造成返修更换的困难。
因此这种整体为铸件的“定位块”式夹具是耗能耗材的,其设计、制造周期和成本都比较高。
随着工装制造水平与检测手段的提高,车身焊接夹具的定位转化为定位板定位,板的厚度在16、19、25几档中选用。
整个夹具本体改为焊接合件,在制造、装配上都缩短了周期,相对降低了成本。
定位板与角支座、角支座与底板各定位销孔均采用镗孔,孔间距偏差为,L±0.02。
这种在加工上采用此方式,在调试中若车身产品尺寸略有变化(如冲压件常有的尺寸误差),机加中保证的尺寸精度就浪费掉了。
要想使车身几何精度在夹具上一次装调成功,冲压件就不能有较大的尺寸偏差,而且定位点的数量也比较多。
用直角块可调定位方式与上相同,只是定位板、压头用直角块加垫片过渡。
它的优点是定位板、压头用损后修复、装调比较方便;也比较容易形成标准化设计、制造(除定位块、压头上压块外,其余零件均可制成标准件)。
但设计人员要解决镗出的定位销孔与垫片的关系,不能让定位板无公差加工。
也延长了装配周期,从定位型面到检测销孔等尺寸链增多,累计误差上升。
如平头车身左/右侧围夹具,仅直角块就有900个左右。
可想装配调整工作量之大,它同样是以提高加工精度为代价换来的。
夹具从整体外形看0有章法、但不美观。
采用三个圆柱销定位各零、部件,它把以上两种定位法加工精度从,L±0.02降到,L±0.05,就使夹具在生产使用中加工、装配上使车身装焊精度得到了保证。
但在设计、装配中,要考虑定位部件的使用状况,否则精度就会随磕碰等不良因素走失掉。
五、车身分块和定位基准的选择
车身焊接总成一般由底板、前围、后围、侧围和顶盖几大部分组成,不同的车型分块方式不同,在选择定位基准时,一般应做到:
1、保证门洞的装配尺寸
当总成焊接无侧围分块时,门洞必须作为主要的定位基准,在分装夹具中,凡与前后立柱有关的分总成装焊都必须直接用前后立柱定位,而且从分装到总装定位基准应统一;当总成焊接有侧围分块时,则门洞应在侧围焊接夹具上形成,总装焊时以门洞及工艺孔定位,且从分装到总装定位基准也应统一。
2、保证前后悬置孔的位置准确度
车身底板上的悬置孔一般冲压在底板加强梁上,装焊时要保证悬置孔的相对位置,以便使车身顺利地下落到车架上。
3、保证前后风窗口的装配尺寸
前后风窗口一般由外覆盖件和内覆盖件组成,有的是在前后围总成上形成,在分装夹具上要注意解决其定位,有的在总装夹具上形成,一般在专门的窗口定位装置对窗口精确定位,以保证风窗玻璃的装配。
六、车身焊接夹具的结构及定位夹紧特点
1、车身焊装夹具的结构特点
车身焊装夹具体积庞大,结构复杂,为了便于制造、装配、检测和维修,必须对夹具结构进行分解,否则,无法进行测量。
车身总装夹具有3个装配基准:
底板、左侧围和右侧围,在它们的平面上都加工有基准槽和坐标线,定位夹紧组合单元按各自的基准槽进行装配、检测,最后将3大部分组合起来,成为一套完整的夹具。
2、车身焊装夹具的定位特点
车身焊装夹具大都以冲压件的曲面外型、在曲面上经过整形的平台、拉延和压弯成型的台阶,经过修边的窗口和外部边缘、装配用孔和工艺孔定位,这就在很大程度上决定了它的定位元件形状比较特殊,很少能用标准元件。
焊接夹具上要分别对各被焊工件进行定位,并使其不互相干涉,在设计定位元件时要充分利用工件装配的相互依赖关系作为自然的定位支承。
有的工件焊接成封闭体,无法设置定位支承,可要求产品设计时预冲平台、翻边作为定位控制点,总之,对于要求不严格的装配,尽量不使用焊接夹具。
车身焊装夹具上,板状定位较多,定位板一般用A3、A5号钢板,厚度为12-20mm。
定位块间距既要保证定位精度,又要保证焊钳伸入的方便性。
定位件按坐标标注尺寸,不注公差。
3、车身焊装夹具的夹紧特点
车身冲压件装配后,多使用电阻焊接,工件不受扭转力矩,当工件的重力与点焊时加压方向一致,焊接压力足以克服工件的弹性变形,并仍能保持准确的装配位置与定位基准贴合,此时可以省去夹紧机构。
焊接通常在两个工件间进行,夹紧点一般都比较多,电阻焊是一种高效焊接工艺,为减少装卸工人的辅助时间,夹紧应采用高效快速装置和多点联动机构。
对于薄板冲压件,夹紧力作用点应作用在支承点上,只有对刚性很好的工作才允许作用在几个支承点所组成的平面内,以免夹紧力使工件弯曲或脱离定位基准。
夹紧力主要用于保持工件装配的相对位置,克服工件的弹性变形,使其与定位支承或导电电极贴合,对于1.2mm厚度以下的钢板,贴合间隙不大于0.8mm,每个夹紧点的夹紧力一般在300-750N.范围内;对于1.5-2.5mm之间的冲压件,贴合间隙不大于1.5mm每个夹紧点的夹紧力在500-3000N.范围内。
夹紧器按照夹紧方向有平面、垂直、45度夹紧器;按照操作方式有螺栓夹紧、快速夹紧、手柄螺旋夹紧;还有手工、气动或液压。
其中带补偿的螺旋夹紧器最为常用。
这种夹紧器在悬臂中增加了弹性伸缩,抵消夹紧时的侧向分力,以补偿夹具本身的变形和插入过程中的间隙,保证夹紧力与受力面垂直。
夹紧头部一般由碳钢、不锈钢、尼龙材料制成,以适合不同的工件要求。
如果配备两点、三点夹紧桥,可以同时夹紧不同高度的两个位置的工件。
另外也可以按照夹紧的型面加工特殊的夹紧头。
七、焊接夹具的精度控制
焊接夹具精度标准由设计单位制定,其中规定了底板基准槽和坐线的形态和精度要求;定位销和其他定位支承件的尺寸和形位公差要求,承制单位按要求进行检测、判断并进行调整,合格后就固定定位销。
随着机床加工精度的提高,为了降低定位误差,提高加工精度,对夹具的制造精度要求更高。
高精度夹具的定位孔距精度高达0.01mm/±5um,夹具支承面的垂直度达到0.01mm/300mm,平行度高达0.01mm/500mm。
德国demmeler(戴美乐),公司制造的4m长、2m宽的孔系列组合焊接夹具平台,其等高误差为±0.03mm;精密平口钳的平行度和垂直度在5um以内;夹具重复安装的定位精度高达±5um;瑞士EROEA柔性夹具的重复定位精度高达2-5um。
机床夹具的精度已提高到微米级,世界知名的夹具制造公司都是精密机械制造企业。
诚然,为了适应不同行业的需求和经济性,夹具有不同的型号,以及不同档次的精度标准供选择。
八、模块、组合
夹具元件模块化是实现组合化的基础。
利用模块化设计的系列化、标准化夹具元件,快速组装成各种夹具,已成为夹具技术开发的基点。
省工、省时,节材、节能,体现在各种先进夹具系统的创新之中。
模块化设计为夹具的计算机辅助设计与组装打下基础,应用CAD;技术,可建立元件库、典型夹具库、标准和用户使用档案库,进行夹具优化设计,为用户三维实体组装夹具。
模拟仿真刀具的切削过程,既能为用户提供正确、合理的夹具与元件配套方案,又能积累使用经验,了解市场需求,不断地改进和完善夹具系统。
组合夹具分会与华中科技大学合作,正在着手创建夹具专业技术网站,为夹具行业提供信息交流、夹具产品咨询与开发的公共平台,争取实现夹具设计与服务的通用化、远程信息化和经营电子商务化。
九、通用、经济
夹具的通用性直接影响其经济性。
采用模块、组合式的夹具系统,一次性投资比较大,只有夹具系统的可重组性、可重构性及可扩展性功能强,应用范围广,通用性好,夹具利用率高,收回投资快,才能体现出经济性好。
德国demmeler(戴美乐),公司的孔系列组合焊接夹具,仅用品种、规格很少的配套元件,即能组装成多种多样的焊接夹具。
元件的功能强,使得夹具的通用性好,元件少而精,配套的费用低,经济实用。
专家们建议组合夹具行业加强产、学、研协作的力度,加快用高新技术改造和提升夹具技术水平的步伐,创建夹具专业技术网站,充分利用现代信息和网络技术,与时俱进地创新和发展夹具技术。
主动与国外夹具厂商联系,争取合资与合作,引进技术,这是改造和发展我国组合夹具行业较为行之有效的途径。
结束语
汽车车身焊接夹具的设计与冲压件、工序件结构及精度关系极为密切,充满了丰富的特殊性,在设计时,除了考虑遵循一般的规律外,还必须具体问题具体对待。
1前言
近年来,客车市场的竞争日趋激烈,各客车生产厂家在大力开发新车型的同时,对整车的质量也越来越重视。
在车身外形质量的控制过程中,车身骨架的合拢夹具起着重要的作用。
目前,车身骨架总成大多利用通用合拢夹具进行定位及拼焊。
通用合拢夹具刚性强,定位点的精度由机械加工及安装调整保证,精度高,定位点三维可调,夹具体及夹具的动作大多由液压驱动完成,适应夹具长度及高度涵盖范围内所有车型的车身骨架总成的组焊。
此夹具投资较大、夹紧及松脱快捷,但更换车型时夹具的调整时间较长,较适应于多品种、中大批量的客车生产。
2通用合拢夹具结构、工艺过程及调整
2.1通用合拢夹具结构(图1)
合拢夹具由左右夹具体、夹具、体上的Z方向及X方向导轨、地板定位梁装置、各种定位夹紧总成、液压驱动系统、电气控制系统等组成。
左右夹具体上各布置有三条可上下调整的T型槽导轨,其上分别固定7-10个上、中、下定位夹紧总成、3个水平定位总成、1个纵向定位总成、2个顶盖导向总成、3~4个前围及后围夹紧总成及其固定导轨。
上定位夹紧总成可夹紧侧围窗立柱上部或侧围骨架上边梁和顶盖边梁,中定位夹紧总成可夹紧侧围窗下梁或仓上梁,下定位夹紧总成可夹紧侧围裙立柱。
上、中、下定位夹紧总成控制侧围骨架的弧度,水平定位总成可定位侧围骨架窗下梁或仓上梁、控制侧围骨架的Z方向尺寸,纵向定位总成一般定位前乘客门后立柱及驾驶员窗后立柱、控制侧围骨架X方向尺寸,前围夹紧总成可定位前围骨架并夹紧前围侧立柱和侧围前立柱,后围夹紧总成可定位后围骨架并夹紧后围侧立柱和侧围后立柱,左右夹具体合拢后控制车身骨架的宽度(Y方向尺寸)。
可升降的地板定位梁装置上布置有通长的T型槽导轨,其上固定相应的定位夹紧总成、控制地板骨架总成的X及Z方向尺寸。
2.2车身骨架合拢工艺
工作前,左右夹具体处于打开位置,水平定位总成处于降下状态,其余各定位夹紧总成处于打开状态。
首先将水平定位总成升起处于定位状态,将左右侧围骨架吊挂到水平定位总成上,用于纵向定位的侧围立柱应位于纵向定位总成开口范围内,在纵向定位总成动作完成侧围骨架的X方向定位后,中定位夹紧总成动作,之后上定位夹紧总成及下定位夹紧总成动作,完成侧围骨架的定位夹紧。
将地板定位梁升起,地板梁骨架吊运到地板定位梁装置上,各定位件位于定位夹紧总成作用范围内,地板梁纵向定位总成动作并完成地板梁骨架的X方向定位。
使左右夹具体合拢,完成地板梁骨架Y方向定位后分开少许,地板定位梁上的各总成动作并完成地板梁骨架的夹紧,之后将左右夹具体合拢到位。
分别将前后围骨架吊运到位,完成骨架的定位及夹紧。
吊运顶盖总成到相应位置,如上定位夹紧总成是夹紧侧围窗立柱的,可以使用弓形夹将顶盖边梁与侧围骨架上边梁夹紧;如上定位夹紧总成是夹紧侧围骨架上边梁和顶盖骨架边梁的,需先将上定位夹紧总成打开,顶盖总成到位后再夹紧。
此时车身骨架合拢完成,可实施点固及焊接作业。
车身骨架焊接完成后,左右夹具体上的各定位夹紧总成松开,水平定位总成下降,左右夹具体后撤到分开状态。
将地板定位梁上的各定位夹紧总成打开,用吊具将车身骨架总成吊出或地板定位梁下降将车身骨架总成放到输送设备(如辊床)上运至下一工位。
2.3通用合拢夹具的调整
更换车型时,要对合拢夹具进行相应的调整。
调整前应仔细分析图纸,确定各定位夹紧总成应处于的位置,计算出各定位夹紧总成需调整的方向及距离,并准备一套合格的车身骨架各分总成作为样件。
调整时,首先将左右夹具体上的T型槽导轨的高度位置调整到位并紧固,再将各总成紧固螺栓松开、移动到相应位置后预紧固,分别对夹具各部进行调整。
a高度的调整。
合拢夹具是以地板梁下平面为Z方向定位基准的,上下移动水平定位总成到相应位置紧固,测量的同时转动刹撑端部的螺栓将水平定位调整好。
b.侧围弧度的调整。
上、中、下定位夹紧总成决定侧围骨架的弧度,中定位夹紧总成的Y方向尺寸是固定的,转动上、下定位夹紧总成的丝杠将其Y方向尺寸调整到位。
将左右侧围骨架样件挂上,夹紧中定位夹紧总成。
c.车身骨架宽度的调整。
夹具体移动导轨的前端有可调的限位顶丝,合拢左右夹具体,测量的同时调整限位顶丝保证车身骨架的宽度尺寸,左右夹具体的调整量应基本相同。
d.纵向定位总成的调整。
左右夹具体合拢到位,测量两侧围上边梁的对角线,根据对角线尺寸差值情况调整纵向定位总成的位置,反复进行测量及调整,保证两对角线差值满足工艺要求,将纵向定位总成紧固。
测量时侧围骨架应处于夹紧状态,调整时则处于松开状态。
校正侧围骨架各定位夹紧总成的位置并紧固。
与上述调整相似,分别将地板梁骨架、前围骨架、后围骨架吊挂到相应位置,测量的同时调整各定位夹紧总成的位置,调整完成后紧固。
3通用合拢夹具改进
a.夹具体定位尺寸的快速调整及定位精度的提高。
按车身骨架最小宽度尺寸将夹具体定位尺寸调整好并紧固,根据各车型宽度尺寸的差值制作调整垫板,更换车型时插放相应的调整垫板来实现快速调整。
目前车身骨架宽度定位是平面定位方式,夹具体下部导轨的侧向间隙影响夹具体X方向的重复定位精度,可改为竖直V型槽与球头的定位方式消除此误差,提高定位精度。
b.夹具体上纵向导轨的快速调整。
纵向导轨质量大且为上下移动调整,更换车型调整时费时费力,可在纵向导轨与其下部的限位凸台间增加相应尺寸的限位垫板,实现快速调整。
c.定位夹紧总成的快速调整。
某种车型调整完成后,在各定位夹紧总成与其固定导轨间配钻定位孔,插上手动插销并做好车型标记,当重新制作此种车型的车身骨架时,只要将各定位夹紧总成移动到相应的位置,插上插销即可保证定位精度,可节省大量的反复测量调整时间,实现快速调整。
d.中定位夹紧总成结构的改进。
原定位夹紧总成(图2)结构复杂,上下支座(件1,4)为铸件,用连接板(件3)、16个螺栓及8个定位销连接,定位尺寸靠装配来保证。
驱动缸固定,带有活动连板(件6)。
总成质量较大,制造周期较长,成本较高。
改进后的定位夹紧总成(图3)结构简单,由立板(厚度为12mm或16mm)及筋板组成的焊接支座(件12)代替原来的组装件,定位尺寸由机械加工保证。
驱动缸铰接浮动,取消原活动连板。
总成质量较轻,制造周期短,成本较低。
其它各定位夹具总成也可采用类似的方法进行改进。
e.驱动方式的改进建议。
目前合拢夹具采用液压驱动,夹紧总成的夹紧力为2000N左右,由于驱动缸数量达到80-100个,各液压管路的连接点总数量较多(500~600个以上),易造成液压油的渗漏、污染操作环境,设备维护工作量较大。
可采用气动驱动系统,当驱动缸直径为63mm、压缩空气压力为0.4~0.6MPa时,采用附图三结构,夹紧力达到1300~1900N,满足使用要求,有利于保证良好的操作环境,降低设备维护难度及工作量,同时将降低合拢夹具的制造成本。
4结束语
随着对通用合拢夹具的不断改进和完善,将使合拢夹具的结构更加合理、精度提高,夹具的操作和调整更快捷,较适用于客车多品种、单件或小批量的生产方式。
使合拢夹具在保证及提高客车车身制作质量中起到更重要的作用。
焊接夹具气缸动作的程序化设计
气路设计在焊接结构中是经常遇到的问题。
为了操作的安全或出于工艺要求,对一些较复杂的夹具结构,常要求气动动作有一定的先后顺序。
要达到这个目的有三种方法:
1)不同的动作用不同的气阀控制。
这种设计要求工人操作时要记牢操作顺序,否则就易出现安全问题或损坏工件。
2)利用接近开关(如在气缸上固定磁性环)提供气缸到位情况的信号。
这种设计,因为加入了电磁元件,使得气路复杂化。
3)仅利用气阀本身通过气路设计来识别气缸到位状态。
这种设计对一些复杂的焊接结构可以实现程序化。
本文以我公司皮卡车后厢门焊接夹具为例,阐述气缸动作的程序化设计在焊接夹具中的应用。
一、工艺过程分析
皮卡车后厢门总成主要有以下零部件组焊而成:
后厢门本体、侧板总成、后厢门内部加强板、铰链板等。
以侧板与后厢门本体的组焊为例:
我公司采用了图1所示的焊接夹具结构。
根据产品结构,侧板必须采用定位销侧向定位。
为简化操作,定位销固定在侧板定位板上,这样为使焊后总成件顺利取出,限位板必须是活动的。
操作时,首先将后门本体放置在夹具上并可靠定位,在气缸作用下将限位板推到位,再将侧板以定位销定位安装在夹具上,保证与限位板贴合良好,然后用压头将工件夹紧后施焊。
焊接完成后,先将压头打开,然后再将限位板打开,退出定位销并使压头最大限度地后退,以便工件顺利向上取出。
图1 焊接夹具
三、主要设计内容
由上述工艺过程,可以确定后厢门焊接夹具设计的主要内容有:
1.根据后厢门的工艺过程确定焊接夹具的工艺方案,进而确定夹具结构。
2.设计满足夹具结构和工艺方案的气动原理图。
3.根据国产化冲压件调试出能生产合格产品的焊接夹具。
首先,根据产品结构,在气缸1推出时,气缸2必须处于缩入状态,否则侧板无法装入。
施焊完成后,在气缸1缩入时,气缸2也必须首先处于缩入状态,否则,就会将焊好的总成件拉坏。
由此可知,在设计气路图时必须保证:
1)夹紧工件时,气缸1先动,气缸2后动。
2)松开工件时,气缸2先动,气缸1后动。
也就是说,设计的气路图必须具有对气缸状态的识别功能。
在气缸状态不符合要求时,即在误操作的情况下,气动元件可以不理采外界输入的操作命令,而在执行操作命令时,气缸的动作必须按设计的程序进行,即气缸操作时实行程序化。
四、根据以上要求,设计了如图2所示的气动原理图,显然这个气路图达到了后厢门夹具的结构要求。
此气路图实现了对气缸状态的识别,也实现了气缸动作的程序化。
图2 气动原理图
前言
国内汽车行业近几年的快速增长,带动了国内汽车焊接夹具制造业的快速成长。
基本每个新车型投产,均需要投入相应的焊接夹具。
按目前市场情况看,从新车型开发到推进市场,要求周期短,进而对焊接夹具设计、制造、调试提出更高的要求。
汽车焊接夹具的功能是为了实现车身零件的正确装配,保证零件正确搭配和完成焊接。
工程上通常从装配精度、缩短制造周期和可调整性等方面来评价汽车焊接夹具设计的优劣。
定位是焊接夹具最基本的元素,也是设计过程主要考虑元素,定位设计规范化在很大程度上提高焊接夹具的性能,缩短周期,提高效益。
2“N-2-1”定位原理
一般的物体定位按照六点定位原则,即可确定正确位置。
对于车身柔性零件的定位,如果仅靠六点定位规则定位,将无法保证零件的正确位置和形状,因此,在汽车焊接夹具的设计中,经常有过定位的方式定位,即N大于3。
“N-2-1”定位原理更加适合汽车焊接夹具设计,防止薄板变形,在汽车焊接夹具上已广泛应用。
根据汽车零件的形状和考虑焊接夹具制造成本、焊接可操作性等考虑,夹具定位元件的数量N一般选取4-6。
3定位基准统一
基准统一是机械加工工艺设计的基本思想之一,焊接夹具设计定位基准统一要求保证两点,第一、保证焊接夹具设计基准与车身设计基准、冲压基准、检测基准的统一;第二、保证焊接夹具设计基准在分总成、总成、车身焊接总成的各总成之间保持前后统一。
基准统一保证了车身焊接精度,便于查找质量问题原因,提高管理水平。
4定位结构规范化
汽车焊接夹具基本结构,见图1,包括:
固定平台式底座;定位部件;紧固件连接;气动-杠杆复合夹紧;操作高度可调。
图1
4.1固定平台式底座
固定平台式底座有2种,一种是Q235平板式,见上图1的固定平台。
选用平板式的原则:
夹具固定平台面积在1200×500以下的,一般选用平板式。
另一种是焊接件式,见图2。
选用该结构的原则:
夹具固定平台面积在1200×500以上的,一般选用焊接件式。
焊接件由基板、槽钢、垫板焊接而成,结构规范化。
图2