导热油使用规范.docx
《导热油使用规范.docx》由会员分享,可在线阅读,更多相关《导热油使用规范.docx(18页珍藏版)》请在冰豆网上搜索。
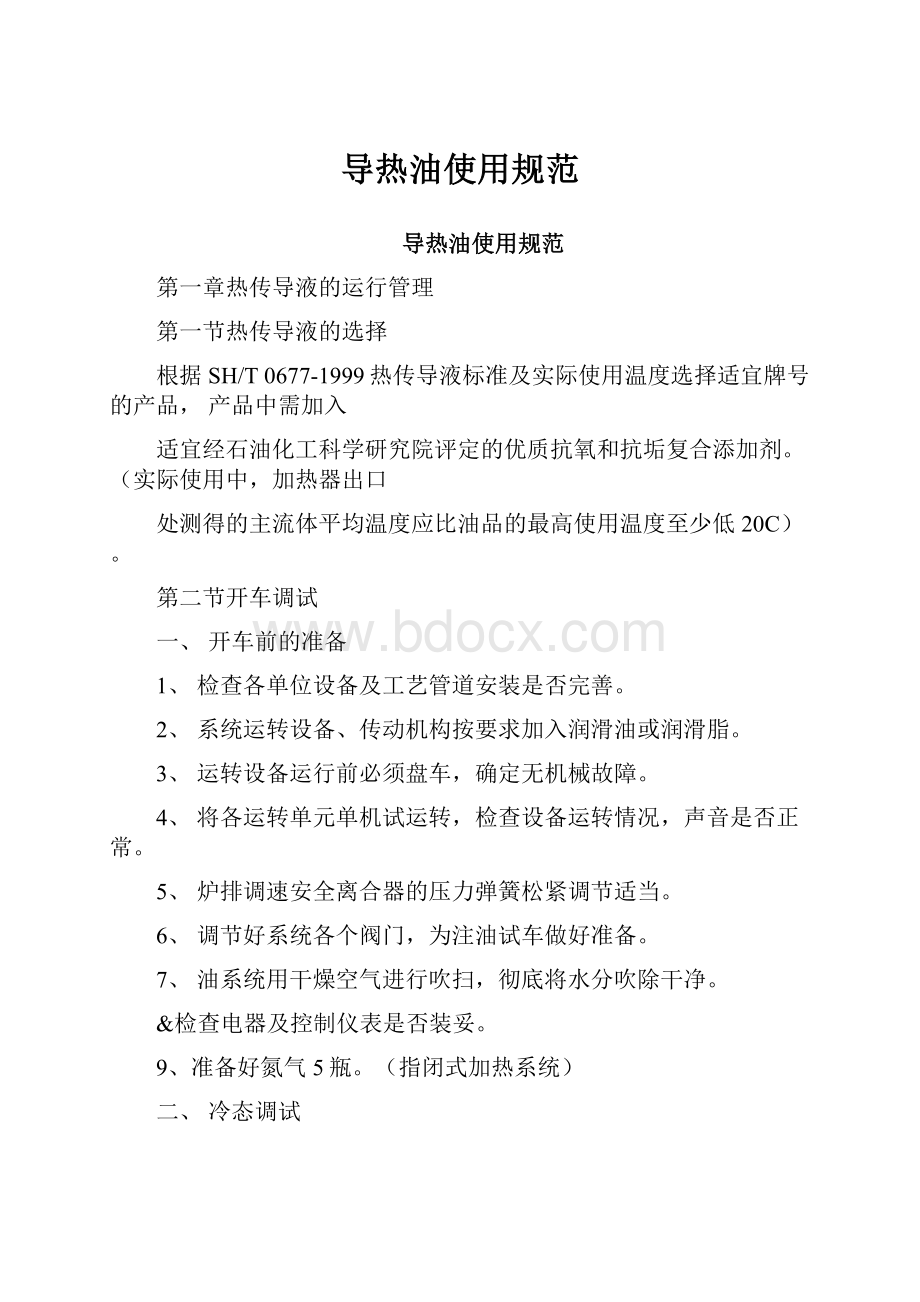
导热油使用规范
导热油使用规范
第一章热传导液的运行管理
第一节热传导液的选择
根据SH/T0677-1999热传导液标准及实际使用温度选择适宜牌号的产品,产品中需加入
适宜经石油化工科学研究院评定的优质抗氧和抗垢复合添加剂。
(实际使用中,加热器出口
处测得的主流体平均温度应比油品的最高使用温度至少低20C)。
第二节开车调试
一、开车前的准备
1、检查各单位设备及工艺管道安装是否完善。
2、系统运转设备、传动机构按要求加入润滑油或润滑脂。
3、运转设备运行前必须盘车,确定无机械故障。
4、将各运转单元单机试运转,检查设备运转情况,声音是否正常。
5、炉排调速安全离合器的压力弹簧松紧调节适当。
6、调节好系统各个阀门,为注油试车做好准备。
7、油系统用干燥空气进行吹扫,彻底将水分吹除干净。
&检查电器及控制仪表是否装妥。
9、准备好氮气5瓶。
(指闭式加热系统)
二、冷态调试
1、开启注油泵向高位槽注油,直至高位槽低液位不报警,关闭注油泵,启动热油循环
泵开始冷油循环,打开高位槽放空阀,经常开启管道放空阀,不断排出空气,及时补充高位
槽内热传导液,保持低液位。
2、冷油循环时间不少于4小时,观察油循环泵进出口压力及系统压力表、温度表等仪
表显示是否正常,直至压差波动转向平稳,检查系统内无泄漏和阻塞现象,清理过滤器2-3
次。
三、热态调试
1、点火:
用不带铁钉等金属的木柴,均匀铺在炉排上引燃,并控制燃烧量,使油循环
泵保持不抽空,油升温速率控制在10C/h左右。
2、上煤:
用手工向炉内均匀铺撒干煤,逐步过渡用煤斗上煤,从观火门观察炉内燃烧情况。
确保炉火燃烧平稳、均匀,无断火现象。
3、烘炉:
按升温曲线要求进行,油温控制在100C以下,注视循环油泵进出口压差波
动情况,如出现循环油泵吸空,可停运2-3分钟,再重新启动,观察炉膛烘干情况。
以上三点指燃煤锅炉(新炉),燃油锅炉可参照第3点〈烘炉〉,要严格控制进油量与时渐进按升温曲线控制热油温度。
4、脱水排气:
按升温曲线进行,油温控制在120C—150C,在此期间重点除去油中水
分和低挥发成分,随着温度升高至200C以上时,系统法兰连接处可进行热紧固,热油泵吸
空可停运0.5-1分钟,再重新启动。
低位槽、高位槽放空阀全部开启,直至压差由波动转向平稳,排气明显减少。
5、升温:
升温速率控制在10C/h左右,使油温度逐步升至260C左右,并全面检查各控制仪表的正常显示。
6、加氮封:
油温升至260C-270C时,热传导液在此阶段脱轻组分,热传导液高温使用,在此时加氮封,关闭放空阀,从加氮口向低位槽和高位槽充入氮气,调整氮气减压阀门,
保持氮封压力为0.08(±).01)Mpa,升温过程中要有专人负责观察和调节氮封压力,压力过高从低位槽放空阀泄压,氮封系统安全阀开启压力定为0.1Mpa,如氮气调节阀失灵,压
力突然升高,除手工放空外,安全阀自动开启泄压。
(低位槽也可安装一块带电接点自动报
警的压力表)。
7、升温:
按升温曲线进行,升温速率控制在10-20C/h以内升至额定工作温度(高于使用温度20C)后,恒温4小时,使各项指标满足生产要求,并对生产系统设备、控制仪表
全面检查,发现问题及时处理。
高位槽保持高液位正常生产。
四、突然停电,冷油置换
当循环油泵因停电不能运转时,炉内盘管中的热传导液温会急剧升温而超过热传导液最高允许温度致使热传导液加速劣化结焦,迅速打开冷油置换阀门,高位槽的冷油经过炉内置
换到低位槽内,同时进行湿煤压火或蒸汽压火,此过程应在5分钟内完成。
五、停炉
1、紧急停炉:
热油循环泵必须继续运行,此时停止送煤和鼓风,炉排快速将红煤送出,若停电用湿煤压火或蒸汽压火。
2、计划停炉:
热油循环泵必须继续运行,停止送煤和鼓风,炉排继续运转,烧尽余煤
送出后停引风,待油温低于80C时停止循环油泵。
六、热传导液升温曲线图
恒温段段
250温
升
200
脱气脱水段
150
段
100温
升
50
12345678910111213141516
第三节注意事项
一、热传导液的注意事项
1、按用热工艺要求,正确选用适宜牌号的热传导液,并严格遵守化工部《载热体加热
安全技术规程》中的各项规定,正确使用热传导液。
2、在使用过程中应认真检查,严防水、酸、碱及低沸点物漏入使用系统,并加装过滤装置,防止机械杂物进入,确保油品纯度。
3、节能热传导液适用于燃煤、燃油加热炉作载热体,电加热反应等供热设备使用时,应具有高位槽和低位槽及其它安全组件和温控仪表等配套设施,确保安全运行。
4、凡旧导热设备更换新热传导液时,必须清除系统内壁杂物,以免影响热传导液的传
热效率和使用寿命。
5、高温热传导液经使用半年后,应进行一次油品分析。
若长期使用后,发现传热效果
差、或发现异常情况,根据油品分析决定(残炭不大于1.5%,酸值不大于0.5mgKOH/g,
闪点变化率不大于20%,粘度变化率不大于15%)。
若其中一项不合格时应考虑添加部分新油或全部换油。
6、运行中严禁超温使用,确保热传导液的正常使用寿命。
二、开车注意事项
1、压差不稳定时,不得投入使用。
2、停炉时热油降至80C以下,热油循环泵方可停止使用。
3、高温状态下,要确保系统油循环良好。
4、正常工作时,高位槽应保持高液位,低位槽处于低液位。
5、应按规定向各种运转设备注入润滑油。
6、热油温度不得超过热传导液允许工作温度。
&紧急停炉不得用水浇炉膛。
9、保证出渣机密封性良好。
10、升温必须按升温曲线进行。
11、密切注意系统的氮封压力变化,超压泄压时,要保持系统内正压,并及时补充高位槽,低位槽氮圭寸压力到规定的数字。
第四节劣化与防止措施
一热传导液的劣化
热传导液的劣化主要是热传导液加热后逐渐分解及聚合反应,使热传导液原结构发生改
变。
生成的低分子或高分子物质逐渐增多,从而改变热传导液的特性。
劣化原因主要是高温,
空气中的氧及生产过程中化学物质的混入等。
劣化分为热劣化、氧化劣化和混入异物的劣化三种。
1•热劣化:
热传导液长期处于高温环境则原子间、分子间的链键断裂,化合物发生分解,
分解物主要有气体,低分子物及自由基分子。
此自由基分子和其他分子发生聚合,生成聚合
物的活跃集团。
所发生的聚合反应为连锁性,即使在一定温度下,随着时间的延长,所生成
的聚合物的分子量和生成量都有增加倾向。
粘度等指标发生缓慢的变化。
2.氧化劣化:
高温热传导液和空气中的氧接触后,会氧化生成有机酸,有机酸可进一步
促进热传导液的聚合反应,并不限于高温,温度100c前后也会发生,随温度的升高其反应
速度加快。
其结果可导致粘度增加,而且所生成的有机酸遇水后对设备带来一定腐蚀作用。
3•混入异物劣化:
所混入的物质有可能成为催化剂,催化热传导液的分解、聚合反应;
可直接和热传导液发生反应,生成分解物及聚合物;所混入的物质即使不溶于热传导液,也
可在热传导液中进行自身的分解和聚合反应,因此,热传导液还未发生劣化,由于混入物的
自身反应,改变热传导液的特性而影响热传导液正常运行;有高位槽、系统配管等处脱落的
铁锈混入后,也可促进热传导液的分解、聚合反应。
二防止劣化的有关措施
1.热劣化的对策:
对热传导液发生热劣化影响最大的因素为其加热炉加热面的管壁温度。
控制温度在热传导液允许使用温度范围内是防止热劣化的必要措施,并加入适宜经石油化工科学研究院评定的优质抗垢添加剂。
2.氧化劣化的防止措施:
防止氧化劣化的原则应尽量避免高温热传导液和空气接触,并
加入适宜经石油化工科学研究院评定的优质抗氧添加剂。
3•异物混入的防止对策:
异物,主要指那些能改变载热体的物性,使之发生分解,聚合
反应的物质,要防止异物的混入,首先要明了不能混入的原因,再针对采取有效的防止对策。
以下对异物混入的原因作一简介:
1在生产过程中,由于热交换器的内部蛇管或套管发生破损而引起被加热物(反应原料、
蒸馏源液等)的混入。
2空气、水等的混入。
热传导液填充前加热设备及配管的干燥或洗净不充分,运行开始
后法兰盘的结合不良,热传导液贮槽、油桶等管理不善造成水份的混入。
3铁锈的混入。
系统和设备安装完毕后内部清洗工作不充分而残留的焊渣、泥等引起;
另外,管理不佳的贮槽或密封不充分的高位槽也会产生锈。
4热传导液严重劣化而产生的重质化物。
三、热传导液在使用中的检验
热传导液在建议的温度范围内可长期使用。
为了使热传导液性能长期保持优良,应该对
热传导液进行检测,检测能帮助人们了解热油系统运行情况。
热传导液在高温下长期使用,
其品质会缓慢发生劣化,因此对于在最高使用温度下连续运转的系统最少每年取样分析一
次,当出现问题是,热传导液的分析结果,可帮助您找出原因以及需要采取的应急措施。
热传导液检测分析需要2升样品,样品需有代表性,能反映系统热传导液的运行情况。
四、热传导液检测结果的分析
1、粘度:
粘度变化一般表明系统内的热传导液受到污染,热裂解和氧化降解程度。
当
变化率大于15%时,应当
引起重视。
2、闪点:
闪点变化表明系统内有低沸物生成,当变化率大于20%时,应当引起重视。
3、酸值:
酸值变化表明系统内热传导液被污染或被氧化,当酸值达到0.5mgKOH/g时,应引起重视。
4、残炭:
残炭增大一般表明来自脏物、腐蚀物、严重氧化或严重热烈解所造成,当达到
1.5%时,应引起重视。
检测结果出来后,如各项指标均未超出变化范围,说明热传导液运行良好;如果一项
或多项超出范围,应当考虑采取措施,部分或全部更换热传导液,使热传导液恢复良好状态。
三、热传导液的安全使用
热传导液虽有较高的沸点、闪点,但仍是可燃液体,因此在使用时应注意安全,使用不当时可能造成失火,失火的原因是泄漏引起的,泄漏失火主要有四种类型:
1、保温区失火:
是热传导液系统最常见的失火类型。
在法兰或仪表连接处发生热传导
液漏,并渗入保温区,最后在空气存在条件下,循环液体和管道热量将热传导液加热,并逐
渐氧化液体,使保温区被引燃而造成失火。
2、管道泄漏、爆裂引起失火:
由于管道泄漏或爆裂使热传导液流入热气火焰区而造成失火。
2、闪点引起失火:
导致闪点失火的因素是在高于最低闪点温度时,同时存在热传导液、空气和火源。
3、工艺原料引起的失火:
主要是热传导液漏到正在加热的系统中,而其工艺原料是易氧化
和具有氧化性的物质而造成失火。
除以上四种失火外,还应更加注意在气相系统中使用时,如造成大量热传导液蒸汽泄漏,可形成气溶胶雾,它在空气中遇明火可引起爆炸燃烧。
综上所述,要防止热传导液失火,就要做好热油系统的设计、维修、保养,以预防热传导液泄漏。
第二章热传导液炉的安装及使用
第一节热传导液炉的基本知识
一、热传导液炉的特性
热传导液炉具有结构合理,技术先进,占地面极小,外形体积小,外形美观,管理简便,
热效率高具有显著的节能效果和经济效益。
炉型有立式、卧式。
机械化燃烧,运行安全可靠,
燃尽度高,操作简便,可减轻机炉人员的劳动强度,并能在较低的运行压力下获得较高的工
作温度,而且热稳定性好。
温度调节精确可靠,配有完整的运行控制和安全监测装置。
二、热传导液炉的组成
热传导液炉系统由:
燃烧系统、循环系统、电器控制系统三大部分组成。
燃烧系统包括:
燃烧室、鼓风机、引风机、烟囱、除尘器、炉排调速装置、上煤机、出渣机。
循环系统包括:
热油炉体、高位槽、循环泵、注油泵、过滤器、油气分离器、烟气余热回收器(用户根据需求选择,热水、热风、蒸气回收装置)。
电器系统包括:
电控柜及电热阻、电接点远传压力计、具有下列功能
1.热油炉进出口温度,烟气出口温度显示
2.热油炉超温度报警(声、光)并与鼓、引风机联锁
3.热油炉进出口差压报警(声、光)
4.高位槽低液位报警(声、光)
5.鼓风、引风与热油泵联锁
6.炉排传动与出渣机联锁
三、燃烧方式
燃烧方式可分为:
1•往复炉排:
可连续运行、煤层在炉排往复推动下,上下翻滚,煤质要求低、燃尽率高,排尘量少、维修方便等特点。
2•链条炉排:
可连续运行、炉排可间断冷却、炉排寿命长、故障率低、运行可靠、炉排速度调节范围广等特点。
3•手烧炉排:
手烧炉排比较简单,但燃烧周期性不协调,劳动量增大,大量可燃物燃烧不尽,要求操作时要勤、快、匀;勤,加煤量不多;快,加煤层要薄;匀,撒均匀好着火。
炉膛设计有二次通风,使可燃物充分燃烧,减少碳氧化合物的分解。
加煤后因为空气供给不足,需向炉内二次补充空气,但不可连续供给,其风量大小根据当地煤种定,以不冒黑烟为准。
四、进煤出渣方式
1•进煤方式-机械斗式上煤机
2•出渣方式-人工出渣、刮板式出渣机
第二节安装及调试
一、有机热载体炉使用安装必须由质量监督局批准登记,并持有质量监督局颁发的《锅炉安装许可证》的单位施工。
二、锅炉房的要求
锅炉房应按照《热水锅炉安全监督规程》中对锅炉房的规定,进行设计和布置。
并应符合国家防火设计规范。
三、设计布置要求
1•设备布置应便于操作,通行和检修。
2•高位槽底部至少比炉顶高1.5m,并不得布置在炉子正上方,高位槽容积不小于系
统膨胀量的1•3倍。
3•低位槽应设在系统最低处,须与热油炉用隔墙隔开,低位槽容积不小于总油量的1
2倍。
4•电控柜应设置在无热辐射处,并应面对操作人员,易于观察及维护。
5•其它设备可根据具体情况,参考《工艺流程图》进行布置。
四、设备安装要求
1.基础施工,可按随炉设备基础图,根据当地土壤条件及需求自行确定基础标高、深度、
标号。
2•设备就位后,浇灌地脚螺栓,进行找正找平,然后紧固地脚螺栓。
3•燃热油炉,炉体与底座联接处应布10-20mm石棉绳,紧固联接螺栓达到密封要求。
4•炉体与炉座联接后,必须用耐火砖砌筑,并用耐火浇注料与炉管密封,高过炉管1
2圈。
五、管路布置要求:
管道直径须根据本单位管路长度及泵的扬程和用热情况进行合理确定。
1•管道必须采用无缝钢管(GB/T8163),连接采用焊接或法兰连接阀门管件必须大于等
于1.6MPa级,并不得采用铸铁及有色金属,管道管件安装前必须清除杂物杂质。
2•油气分离器与高位槽连接的膨胀管,管径不得小于《有机热载体炉安全技术监察规程》
规定值,管子弯曲角度不宜小于120度,其管道严禁装设阀门并不得保温。
3.高位槽溢流管直径不宜小于膨胀管。
4•低位槽的排气管直径应比膨胀管规定值大一档次,排气管上不宜装阀门,应加防雨弯
头,
低位槽排气管应接到安全地点。
5•在系统最高处和最低处,应设置排气阀和排泄阀。
6•低位槽与循环系统连接,必须装设二个阀门。
7•管道安装应有2%o-3%。
的坡度。
&管架设置要合理,管道应采取热补偿措施。
9•管道连接处密封材料应采用金属缠绕石墨垫片或膨胀复合石墨垫片。
第三节开车前的准备
一、系统吹扫与压力实验
1.系统吹扫
系统安装完毕,应先用压缩空气分段进行吹扫,清除内部的焊渣和异物。
2•压力实验
⑴全系统吹扫完毕后,将管线联接,进行复查确认无误后,进行压力实验,实验前后用
压缩空气升至工作压力,
保持压力进行检查,合格后进行压力实验。
⑵压力实验采用热传导液进行液压实验,实验压力先升至1.5倍工作压力,保压20分钟,
然后降压至工作压力
进行检查,检查期间压力保持不变。
⑶试压时,高位槽、低位槽不进行试压,需用盲板封住。
⑷系统打压实验确认无漏后,撤除盲板,与系统管道接通,保证系统管道畅通。
⑸关闭高位槽、低位槽放净阀,系统最低处排泄阀及注油管入口阀,打开系统所有阀门,
用注油泵向系统注油,
注意系统最高处排气阀,无气时及时关闭。
二、管道保温
输送热传导液的管道外皮不加保温,在280OC时每平方米散热约14600-21000kJ。
管道保
温厚度可参照下表选择:
使200C250C300C350C
岩棉
径
38-76mm
50mm
60mm
70mm
80mm
89-219mm
70mm
80mm
80mm
80mm
第三章热传导液工段的安全操作
一、操作程序
1.操作前准备
⑴操作人员必须经质量技术监督局培训考核发证。
⑵制定出各项必要的规章制度,健全原始记录报表。
⑶检查管道仪表电器,电器接地是否完好。
⑷检查所有传动部分润滑情况是否良好,变速箱轴承箱油位应正常。
⑸检查炉排片是否完整无损,煤层闸板是否灵活,清除炉膛各部位杂物。
⑹用手转动传动设备,检查有无卡住现象及异常声响。
⑺有条件时,电机单独运转2小时。
⑻运转设备(包括炉排、上煤、出渣、鼓引风机)空载运行2-4小时。
2•烘炉,无论新炉、改装炉、大修炉、长期停用热油炉,如不烘炉,则因炉墙拱中含有
水分,如点火升温过快,水分迅速蒸发膨胀,致使炉墙炉拱,开裂或倒塌。
燃煤炉一般须烘
3-4天,大型炉或冬天等特殊情况适当延长烘炉时间。
⑴启动热油泵,冷循环4-8小时后方可点火烘炉。
⑵前三天必须采用木柴作燃料,火焰应在炉膛中央勿靠近炉墙,第一天升温不得超过50
度,以后每天升温不得超过40度,注意热传导液温度不得超过100度。
⑶链条炉在烘炉期间应定时转动,以防烧坏。
⑷烘炉后期,可将煤闸板调到40-60mm,开启炉排将煤送进炉膛,适当多添木柴,开鼓、引风来调节烟气及热油温度。
⑸控制鼓、引风来调节烟气及热传导液温度。
3•热传导液脱水及脱除轻组分物
⑴当热传导液温度升高到120OC—150OC即进入脱水阶段,油温升到200OC有少量轻组
分物排出,此阶段采用缓慢升温或恒温控制脱水量及脱除轻组分量。
⑵脱水掌握宜慢,可观察热油泵入口压力指针,摆动即说明有气存在,也可观察高位槽排气量来进行控制。
⑶燃煤热油炉控制升温同烘炉阶段。
⑷热传导液脱完水后应缓慢升温,脱掉热传导液中的轻组份挥发物后,即可升至工艺温度进行正常操作。
⑸当油温升至工艺温度,要全面检查整个系统有无泄露现象膨胀情况,然后进行管道保
温。
注:
脱水时间控制应根据实际情况延长或缩短以脱掉水分和轻组份为准。
二、操作注意事项
1.注意控制煤的粒度,不得超过40mm;煤中不得有金属石块等杂物。
2.出渣机渣块不得太大及不得有杂物进入,以免损害出渣机,并注意保持出渣机水位高度。
3.以防冷空气进入炉内。
4.正常工作时,高位槽内热传导液应保持高液位。
5.正常工作时,保持系统油循环,不得关闭阀门和热油泵,造成热油循环量减少或中
断。
三、检查与保养
1.热油炉在运行中应建立严格的交接班制度,并认真填写运行记录,要有日检、周检、月检、年检制度和完整的记录,留档备查。
2.日检工作内容包括:
热油泵、上煤机、出渣机、鼓风机、引风机、炉排等运转是否正常,各种电控仪表指针
3.是否正确,系统管道有无渗漏,是否按时清灰等。
4.周检工作项目
⑴炉排片有无烧损,是否及时更换。
⑵热油循环系统是否缺油。
5.月检工作项目
⑴打开炉上体清灰口,进行清灰。
⑵校正各种电控仪表,保持准确度。
⑶高位槽缺油,高位槽加新油后要注意脱水。
⑷各传动部分加润滑油。
⑸炉膛有无烧损处,如有要及时修补。
5.年检工作项目
根据需要进行压力试验,压力为工作压力的1.5倍;升压后关闭阀门稳压,时间为20分
钟。
新热传导液半年化验一次,取样量为2L。
四、热油炉操作规章制度
为保证热油炉正常运行,必须有一套完整、简明、实用、易记切实可行又便于检查的
规章制度,主要有:
岗位责任制;安全操作制度和交接班制度,载入本说明书,供用户参考。
1.岗位责任制
⑴在工作岗位上操作人员应严守纪律,服从生产指挥,不做与岗位无关的事。
⑵按时检查设备情况,全面、正确填写运行记录。
⑶正确处理发生的异常情况,发现隐患及时向上级有关人员汇报。
⑷遵守操作规程,保证人身和设备安全。
⑸经常保持设备和场地整洁。
⑹配合进行设备修理后的验收工作。
2.安全操作制度
⑴密切监视高位槽液位、热油炉进出口温度、压力、压力差和燃烧情况,正确调整各种工艺用热参数。
⑵按规定做好日常工作,如清理炉排底积灰和盘管底灰口积灰。
⑶随时检查热油炉受压部件、热油泵、阀门、换热器等是否有泄露变形等异常现象。
⑷检查炉排、上煤、出渣、鼓风、引风运转是否正常,烟道有无积灰。
⑸随时掌握用热使用情况,及时调整热负荷,要严格执行热油炉运转各项制度。
各项记
录要存档以备月检,年检事故处理参考使用。
3.交接班制度
⑴交接上一班的现场记录
⑵交接上一班的特殊情况,如事故检修等。
⑶交接热油炉运转情况和缺陷问题。
⑷交接安全附件和附属设备的运转情况。
⑸交接各种阀门的开关位置和控制仪表运转情况。
⑹交接燃料的质量和存量。
⑺交接高位槽液位情况,高位槽不得缺油,加新油后注意脱水。
⑻交接所用的工具。
⑼交接清洁和保养情况。
⑽上下班班长和有关人员对热油炉和设备,共同进行一次巡回检查,认真交班与接班。
4.交班前应做的工作
⑴对设备进行全面检查。
⑵作好场地、设备、工具的清洁整理工作。
⑶若交接班前发生事故,应首先处理事故,再进行交班,交班人员应认真做好交班工作,如发生事故应主动了解情况,积极协助处理事故。
枯藤老树昏鸦,小桥流水人家,古道西风瘦马。
夕阳西下,断肠人在天涯