底盖翻边挤切落料复合模设计说明书999.docx
《底盖翻边挤切落料复合模设计说明书999.docx》由会员分享,可在线阅读,更多相关《底盖翻边挤切落料复合模设计说明书999.docx(31页珍藏版)》请在冰豆网上搜索。
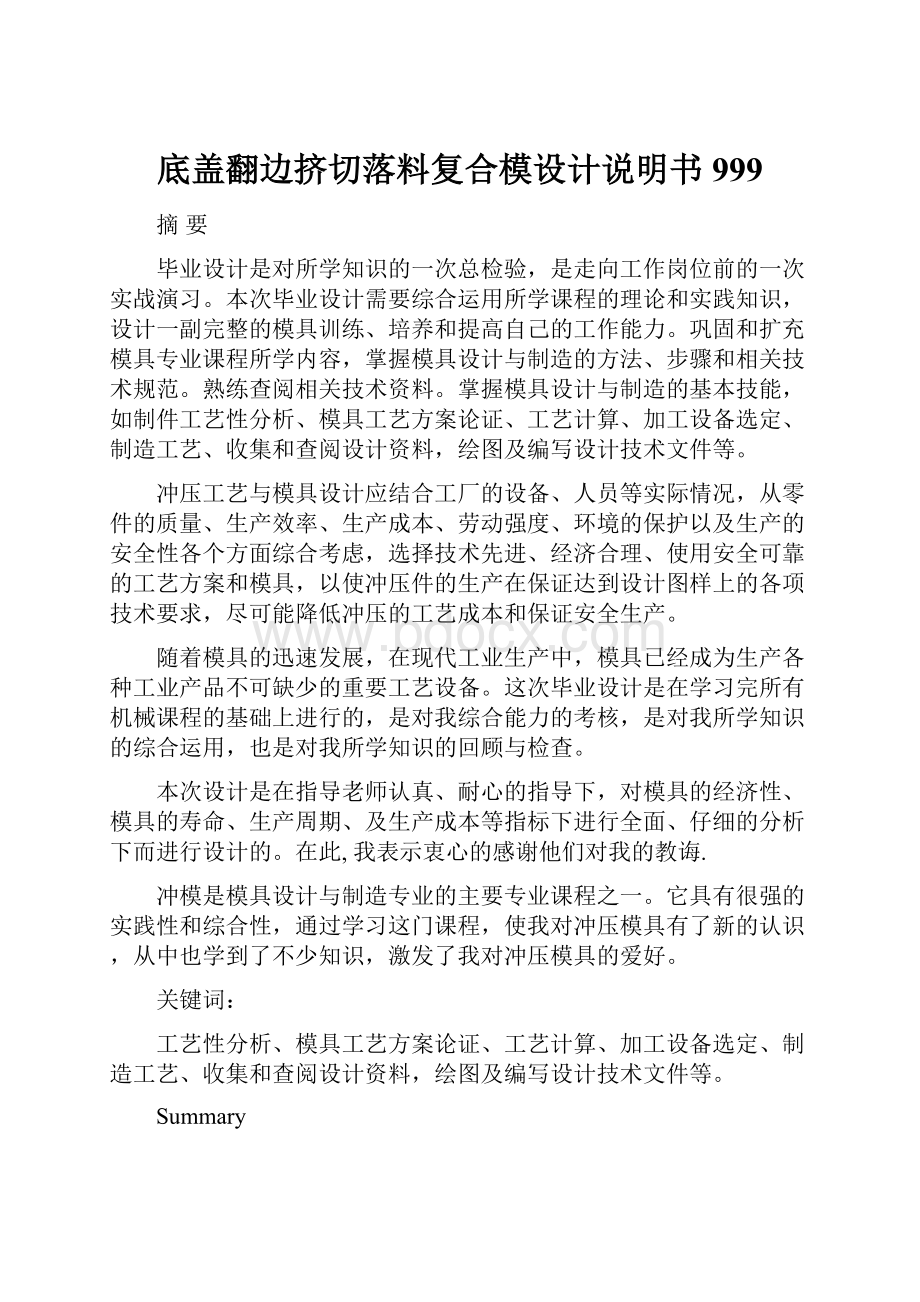
底盖翻边挤切落料复合模设计说明书999
摘要
毕业设计是对所学知识的一次总检验,是走向工作岗位前的一次实战演习。
本次毕业设计需要综合运用所学课程的理论和实践知识,设计一副完整的模具训练、培养和提高自己的工作能力。
巩固和扩充模具专业课程所学内容,掌握模具设计与制造的方法、步骤和相关技术规范。
熟练查阅相关技术资料。
掌握模具设计与制造的基本技能,如制件工艺性分析、模具工艺方案论证、工艺计算、加工设备选定、制造工艺、收集和查阅设计资料,绘图及编写设计技术文件等。
冲压工艺与模具设计应结合工厂的设备、人员等实际情况,从零件的质量、生产效率、生产成本、劳动强度、环境的保护以及生产的安全性各个方面综合考虑,选择技术先进、经济合理、使用安全可靠的工艺方案和模具,以使冲压件的生产在保证达到设计图样上的各项技术要求,尽可能降低冲压的工艺成本和保证安全生产。
随着模具的迅速发展,在现代工业生产中,模具已经成为生产各种工业产品不可缺少的重要工艺设备。
这次毕业设计是在学习完所有机械课程的基础上进行的,是对我综合能力的考核,是对我所学知识的综合运用,也是对我所学知识的回顾与检查。
本次设计是在指导老师认真、耐心的指导下,对模具的经济性、模具的寿命、生产周期、及生产成本等指标下进行全面、仔细的分析下而进行设计的。
在此,我表示衷心的感谢他们对我的教诲.
冲模是模具设计与制造专业的主要专业课程之一。
它具有很强的实践性和综合性,通过学习这门课程,使我对冲压模具有了新的认识,从中也学到了不少知识,激发了我对冲压模具的爱好。
关键词:
工艺性分析、模具工艺方案论证、工艺计算、加工设备选定、制造工艺、收集和查阅设计资料,绘图及编写设计技术文件等。
Summary
Withtheskillofmoldgraduallytoscientificdevelopment,graduallydevelopedfromthepreviousmanuallyusingsoftwareotherhigh-techwaystoassistthedesigniscomplete.Dieisoneofthem.
Graduationisaprofessionalmoldafterteachingthetheoryofpracticalteaching.Theknowledgeofthelump-sumtest,gotoworkbeforeapracticalexercise.Itspurposeistheintegrateduseofthecourseofstudytheoreticalandpracticalknowledgetodesignacompletemoldtrain,developandimprovetheirabilitytowork.Consolidateandexpandmoldprofessionalcoursestolearncontent,mastermolddesignandmanufacturingmethods,proceduresandrelevanttechnicalspecifications.Skilledconsulttherelevanttechnicalinformation.Mastermolddesignandmanufactureofbasicskills,suchaspartsmanufacturabilityanalysis,moldtechnologydemonstrationprogram,processcalculation,processingequipmentselection,manufacturingprocesses,andaccesstodesigndatacollection,preparationofdesigndrawingsandtechnicaldocuments.
Stampingprocessanddiedesignshouldbecombinedwithfactoryequipment,personnel,theactualsituation,fromthepartofthequality,productivity,productioncosts,laborintensity,environmentalprotectionandproductionsafetyaspectsintoaccount,choosetechnologicallyadvanced,economicalandreasonable,theuseofsafeandreliabletechnologysolutionsandmoldtomakestampingpartsproductiontomeetthedesigntoensurethetechnicalrequirementsonthedrawing,stampingprocesstominimizecostsandensuresafetyinproduction.
Withtherapiddevelopmentofmoldinmodernindustrialproduction,moldproductionofvariousindustrialproductshasbecomeanimportantandindispensableprocessequipment.Thegraduationprojectiscompletedinthestudyofallmechanicalcoursesbasedon,isthecomprehensivecapacityassessmentforme,formetheintegrateduseoftheknowledge,butalsoonmyknowledgeofthereviewandinspection.
Thisdesignistheinstructorcarefullyandpatientlyundertheguidanceoftheeconomyofthemold,themoldlife,theproductioncycle,andlowerproductioncostsandotherindicatorstoconductacomprehensive,detailedanalysiscarriedoutunderthedesign.Here,Iexpressmyheartfeltthanksthemfortheirteachings.
Diemolddesignandmanufacturingexpertiseisthemainoneofprofessionalcourses.Ithasastrongpracticalandintegrated,throughthiscourse,mademeanewunderstandingofstampingdies,fromwhichwelearnedalotofknowledge,inspiredmetostampinghobby.
Keywords:
Processanalysis,moldtechnologydemonstrationprogram,processcalculation,processingequipmentselection,manufacturingprocesses,andaccesstodesigndatacollection,preparationofdesigndrawingsandtechnicaldocuments.
1引言
1.1模具行业的发展现状及市场前景
现代模具工业有“不衰亡工业”之称。
世界模具市场总体上供不应求,市场需求量维持在700亿至850亿美元,同时,我国的模具产业也迎来了新一轮的发展机遇。
近几年,我国模具产业总产值保持15%的年增长率(据不完全统计,2005年国内模具进口总值达到700多亿,同时,有近250个亿的出口),到2007年模具产值预计为700亿元,模具及模具标准件出口将从现在的每年9000多万美元增长到2006年的2亿美元左右。
单就汽车产业而言,一个型号的汽车所需模具达几千副,价值上亿元,而当汽车更换车型时约有80%的模具需要更换。
2005年我国汽车产销量均突破550万辆,预计2007年产销量各突破700万辆,轿车产量将达到300万辆。
另外,电子和通讯产品对模具的需求也非常大,在发达国家往往占到模具市场总量的20%之多。
目前,中国17000多个模具生产厂点,从业人数约50多万。
1999年中国模具工业总产值已达245亿元人民币。
工业总产值中企业自产自用的约占三分之二,作为商品销售的约占三分之一。
在模具工业的总产值中,冲压模具约占50%,塑料模具约占33%,压铸模具约占6%,其它各类模具约占11%。
模具的发展是体现一个国家现代化水平高低的一个重要标志,就我国而言,经过了这几十年曲折的发展,模具行业也初具规模,从当初只能靠进口到现在部分进口已经跨了一大步,但还有一些精密的冲模自己还不能生产只能通过进口来满足生产需要。
随着各种加工工艺和多种设计软件的应用使的模具的应用和设计更为方便。
随着信息产业的不断发展,模具的设计和制造也越来越趋近于国际化。
现在模具的计算机辅助设计和制造(CAD/CAM)技术的研究和应用。
大大提搞了模具设计和制造的效率。
减短了生产周期。
采用模具CAD/CAM技术,还可提高模具质量,大大减少设计和制造人员的重复劳动,使设计者有可能把精力用在创新和开发上。
尤其是pro/E和UG等软件的应用更进一步推动了模具产业的发展。
。
数控技术的发展使模具工作零件的加工趋进于自动化。
电火花和线切割技术的广泛应用也对模具行业起到了飞越发展。
模具的标准化程度在国内外现在也比较明显。
特别是对一些通用件的使用应用的越来越多。
其大大的提高了它们的互换性。
加强了各个地区的合作。
对整个模具的行业水平的提高也起到了重要的作用。
冲压工艺是塑性加工的基本加工方法之一。
它主要用于加工板料零件,所以有时也叫板料冲压。
冲压不仅可以加工金属板料,而且也可以加工非金属板料。
冲压加工时,板料在模具的作用下,于其内部产生使之变形的内力。
当内力的作用达到一定程度时,板料毛坯或毛坯的某个部位便会产生与内力的作用性质相对应的变形,从而获得一定的形状、尺寸和性能的零件。
冲压生产靠模具与设备完成加工过程,所以它的生产率高,而且由于操作简便,也便于实现机械化和自动化。
利用模具加工,可以获得其它加工方法所不能或难以制造的、形状复杂的零件。
冲压产品的尺寸精度是由模具保证的,所以质量稳定,一般不需要再经过机械加工便可以使用。
冲压加工一般不需要加热毛坯,也不像切削加工那样大量的切削材料,所以它不但节能,而且节约材料。
冲压产品的表面质量较好,使用的原材料是冶金工厂大量生产的轧制板料或带料,在冲压过程中材料表面不受破坏。
因此,冲压工艺是一种产品质量好而且成本低的加工工艺。
用它生产的产品一般还具有重量轻且刚性好的特点。
冲压加工在汽车、拖拉机、电机、电器、仪器、仪表、各种民用轻工产品以及航空、航天和兵工等的生产方面占据十分重要的地位。
现代各种先进工业化国家的冲压生产都是十分发达的。
在我国的现代化建设进程中,冲压生产占有重要的地位。
由于冲压工艺具有生产效率高、质量稳定、成本低以及可加工复杂形状工件等一系列优点,在机械、汽车、轻工、国防、电机电器、家用电器,以及日常生活用品等行业应用非常广泛,占有十分重要的地位。
随着工业产品的不断发展和生产技术水平的不断提高,冲压模具作为个部门的重要基础工艺装备将起到越来越大的作用。
可以说,模具技术水平已成为衡量一个国家制造业水平的重要指标。
当今,随着科学技术的发展,冲压工艺技术也在不断革新和发展,这些革新和发展主要表现在以下几个方面:
(1)工艺分析计算方法的现代化
(2)模具设计及制造技术的现代化
(3)冲压生产的机械化和自动化
(4)新的成型工艺以及技术的出现
(5)不断改进板料的性能,以提高其成型能力和使用效果。
1.2课题来源和研究意义
本设计题目由实习单位提供,经系指导老师审核通过的。
本设计题目涉及的主要内容是对冲压模的设计,研究目的是在厂原有的基础上,对模具进行改进设计,提高产品质量与效益。
在二十世纪中期甚至更早,国外就已经出现很多对模具及模具工业的高度评价与精辟的比喻。
例如:
“模具是美国工业的基石”(美国);“模具是促进社会繁荣富强的原动力”(日本);“模具工业是金属加工的帝王”(德国);“模具是黄金”(东欧)等。
在二十世纪未,中国人才开始认识到其极端重要性,作出了科学的评价:
“模具工业是现代工业之母”(中国)。
21世纪的制造业,正从以机器为特征的传统技术时代,向着以信息为特征的技术时代迈进,即用信息技术改造和提升传统产业。
经济全球化和世界市场一体化加速发展,不断加剧了制造商之间的竞争,提出了快速反应市场的要求,与之相适应,制造业对柔性自动化技术及装备的要求更加迫切而强烈。
同时,微电子技术和信息通信技术的快速发展,为柔性自动化提供了重要的技术支撑,工业装备的数控化、自动化、柔性化呈现蓬勃发展的态势。
现今,全世界模具工业年总产值约为650亿美元,其中亚洲地区占到全世界一半的总产值。
而在亚洲,最高属于日本,年产值达200亿美元上下。
美国的年产值为50亿美元。
中国也在后来居上,现在已经达到70亿美元。
然而,产值并不等同于技术质量。
虽然我国冲压模具无论在数量上,还是在质量、技术和能力等方面都已有了很大发展,但与发展经济需求和世界先进水平相比,差距仍很大。
一些大型、精度、复杂、长寿命的高档模具每年仍大量进口,特别是中高档轿车的覆盖件模具,目前仍主要依靠进口。
而技术含量低的模具已供过于求,市场利润空间狭小。
近五年来,平均每年进口模具约为11.2亿美元,2003年就进口了近13.7亿的模具,这还未包括随设备和生产线作为附件带进来的模具。
这表示中国大陆模具业的发展潜力仍然很巨大。
这就是这次研究的意义。
我国模具CAD/CAM技术的发展已有20多年历史。
由原华中工学院和武汉733厂于1984年共同完成的精冲模CAD/CAM系统是我国第一个自行开发的模具CAD/CAM系统。
华中工学院和北京模具厂等在1986年共同完成的冷冲模CAD/CAM系统是我国自行开发的第一个冲压模CAD/CAM系统。
上海交通大学开发的冷冲模CAD/CAM系统也于同年完成。
21世纪开始,CAD/CAM技术逐渐普及,现在具有一定生产能力的冲压模具企业基本都有了CAD/CAM技术,其中部分骨干重点企业还具备各CAE能力。
模具CAD/CAM技术能显著缩短模具设计与制造周期,降低生产成本,提高产品质量,已成为人们的共识。
在“八五”、九五“期间,已有一大批模具企业推广普及了计算机绘图技术,数控加工的使用率也越来越高,并陆续引进了相当数量CAD/CAM系统。
如美国EDS的UG,美国ParametricTechnology公司的Pro/Engineer,美国CV公司的CADSS,英国DELCAM公司的DOCT5,日本HZS公司的CRADE及space-E,以色列公司的Cimatron还引进了AutoCADCATIA等软件及法国Marta-Daravision公司用于汽车及覆盖件模具的Euclid-IS等专用软件。
国内汽车覆盖件模具生产企业普遍采用了CAD/CAM技术/DL图的设计和模具结构图的设计均已实现二维CAD,多数企业已经向三维过渡,总图生产逐步代替零件图生产。
在冲压成型CAE软件方面,除了引进的软件外,华中科技术大学、吉林大学、湖南大学等都已研发了较高水平的具有自主知识产权的软件,并已在实践中得到成功应用,产生了良好的效益。
快速原型(RP)传统的快速经济模具相结合,快速制造大型汽车覆盖件模具,解决了原来低熔点合金模具靠样件浇铸模具,模具精度低、制件精度低和制造难等问题,实现了以三维CAD模型作为制模依据的快速模具制造。
它标志着RPM应用于汽车身大型覆盖件试制模具已取得了成功。
1.3题目研究方法
本论文主要通过具体例子的方式对冲压模具的生产流程进行介绍、分析、研究。
通过对底盖模具设计的说明,详细地阐述了冲压模具生产的一般流程。
对零件加工工艺性分析、零件的加工方式、冲压模具的结构组成等进行介绍并对冲压模具生产中常常出现的缺陷进行分析研究。
步骤如下:
(1)零件成型方案确定;
(2)零件零件形状分析,根据模拟结果进一步提出工艺改良方案;
(3)使用CAD等软件对零件进行分析,设计模具装配图和零件图;
(4)完成冲压零件设计的文字说明。
1.4论文构成及研究内容
论文主要由绪论、零件的成型工艺分析、工艺方案制定、及设计计算、模具结构零部件的设计计算,模具缺陷分析等五大部分构成。
论文主要围绕该零件冲压成形工艺及模具设计展开,综合运用冲压成形工艺及模具设计理论以及AUTOCAD等辅助设计软件,完成设计计算,绘制模具的装配图和零件图。
2冲裁件的工艺性分析
冲压主要是按工艺分类,可分为分离工序和成形工序两大类。
分离工序也称冲裁,其目的是使冲压件沿一定轮廓线从板料上分离,同时保证分离断面的质量要求。
成形工序的目的是使板料在不破坯的条件下发生塑性变形,制成所需形状和尺寸的工件。
在实际生产中,常常是多种工序综合应用于一个工件。
冲裁、弯曲、剪切、拉深、胀形、旋压、矫正是几种主要的冲压工艺。
冲压用板料的表面和内在性能对冲压成品的质量影响很大,要求冲压材料厚度精确、均匀;表面光洁,无斑、无疤、无擦伤、无表面裂纹等;屈服强度均匀,无明显方向性;均匀延伸率高;屈强比低;加工硬化性低。
在实际生产中,常用与冲压过程近似的工艺性试验,如拉深性能试验、胀形性能试验等检验材料的冲压性能,以保证成品质量和高的合格率。
模具的精度和结构直接影响冲压件的成形和精度。
模具制造成本和寿命则是影响冲压件成本和质量的重要因素。
模具设计和制造需要较多的时间,这就延长了新冲压件的生产准备时间。
模座、模架、导向件的标准化和发展简易模具(供小批量生产)、复合模、多工位级进模(供大量生产),以及研制快速换模装置,可减少冲压生产准备工作量和缩短准备时间,能使适用于减少冲压生产准备工作量和缩短准备时间,能使适用于大批量生产的先进冲压技术合理地应用于小批量多品种生产。
冲压设备除了厚板用水压机成形外,一般都采用机械压力机。
以现代高速多工位机械压力机为中心,配置开卷、矫平、成品收集、输送等机械以及模具库和快速换模装置,并利用计算机程序控制,可组成高生产率的自动冲压生产线。
在每分钟生产数十、数百件冲压件的情况下,在短暂时间内完成送料、冲压、出件、排废料等工序,常常发生人身、设备和质量事故。
因此,冲压中的安全生产是一个非常重要的问题。
冲裁件的工艺性是指冲裁件在冲裁加工中的难易程度。
所谓冲裁工艺性好是指能用普通的冲裁方法,在模具寿命和生产率较高、成本较低的条件下得到质量合格的冲裁件。
因此,冲裁件的结构形状、尺寸大小、精度等级、材料及厚度等是否符合冲裁的工艺要求,对冲裁件质量、模具寿命和生产效率有很大的影响。
2.1冲裁件的形状
冲裁件如图1-1所示。
图1-1.零件及尺寸
产品采用1.5mm冷轧Q235-A钢板制成,生产批量大,零件形状较简单,上有四处翻边成形孔,翻边高度及孔距精度较高且须保证翻孔边缘料厚不小于1.4mm。
此材质抗拉强度470,抗剪强度380。
2.2冲裁件的尺寸精度
冲裁件的精度主要以其尺寸精度、冲裁断面粗糙度、毛刺高度三个方面的指标来衡量,根据零件图上的尺寸标注及公差,可以判断属于尺寸精度为IT12—IT14的经济级普通冲裁。
3制件冲压工艺方案的确定
冲裁工序可以分为单工序冲裁、复合工序冲裁和连续冲裁。
冲裁方式根据下列因素确定:
(1)根据生产批量来确定对于年产量需求100万件的该产品来说采用复合模或连续模较合适。
(2)根据冲裁件尺寸和精度等级来确定复合冲裁所得到的冲裁件尺寸精度等级高,而连续冲裁比复合冲裁的冲裁件尺寸精度等级低。
根据对冲裁件尺寸形状的适应性来确定产品的尺寸较小,考虑到单工序送料不方便和生产效率低,因此常采用复合冲裁或连续冲裁。
连续冲裁又可以加工形状复杂、宽度很小的异形冲裁件。
根据模具制造安装调整的难易和成本的高低来确定,对复杂形状的冲裁件来说,采用复合冲裁比采用连续冲裁较为适宜,因为模具制造安装调整较容易,且成本较低。
根据操作是否方便与安全来确定复合冲裁其出件或清除废料较困难,工作安全性较差,连续冲裁较安全。
该产品零件外形尺寸较小,四处翻边孔外壁距外形边缘直边距离不足2mm,翻孔时会引起边缘材料向孔部分转移,造成外形收缩畸形。
翻边孔孔径及高度均不大,根据圆孔翻边的最大翻边高度公式:
式中D翻孔中心层直径,Z)=5.2+t=6.7mm
r翻孔弯曲半径,r=1.5mm
查资料,得Q235-A材料最小翻边系数1=0.68代入数值,
凡零件要求高度F=5mm由于零件的特殊性,要保证翻孔边缘料厚大于1.4mm,采用较小翻边间隙的挤薄翻边不能达到零件高度,该零件难以一次翻孔成形。
该零件的传统加工工艺方案为:
先在剪切的平板坯料上拉延出四处浅圆角,然后冲切外形,再在四处浅圆角角底预冲孔,最终翻边成形,该种工艺稳妥、可靠,但针对底盖而言,存在明显不足。
首先,零件多次重复定位,要保证翻边孔孔距精度,必导致模具制造精度大大提高。
其次,翻边预冲孔,孔径计算公式仅适用于对翻边高度要求不高时近似计算。
实际变形中,其高度受变形程度、模具和板材性能等多种不确定因素影响,真实值须经翻孔验证、修正后才能确定,给技术、生产带来诸多不便。
再次,整个零件成形工艺流程长、占用设备多、费工费时,不利于大批量生产及企业效益的提高。
我们知道翻孔过程中,翻边材料主要切向拉伸变形,径向变形不大,变形材料遵循弯曲件中性层长度不变原则。
针对底盖结构特性,可作如下计算:
如图1-1所示,翻孔弯曲半径r=1.5mm,
翻孔直边高度(h=5-t-r=5-l.5-1.5=2mm)的翻孔成形需要的料长
底盖翻孔参与成形的长度
(d为翻孔内径)。
计算结果l'与l接近,这表明在料厚不变薄、边缘材料完全不流入的情况下,图1-1所示翻孔变形并不会造成缺料。
通过借助于四处翻边孔外形边缘材料的合理流动,必将改善翻孔的工作状况,减轻翻孔边缘材料由于承受较大的拉伸应力可能形成的料厚变薄,通过合理的模具结构设计来达到较高精度的翻边高度,解决边缘材料的收缩畸形。
根据上述分析,决定采用1副复合模一次性完成该件的加工。
4制件排样图的设计及材料利用率的计算
4.1制件排样图的设计
排样时需考虑如下原则:
提高材料利用率(不影响冲件使用性能前提下,还可适当改变冲件的形状)
合理排