汽车悬架弹簧钢.docx
《汽车悬架弹簧钢.docx》由会员分享,可在线阅读,更多相关《汽车悬架弹簧钢.docx(26页珍藏版)》请在冰豆网上搜索。
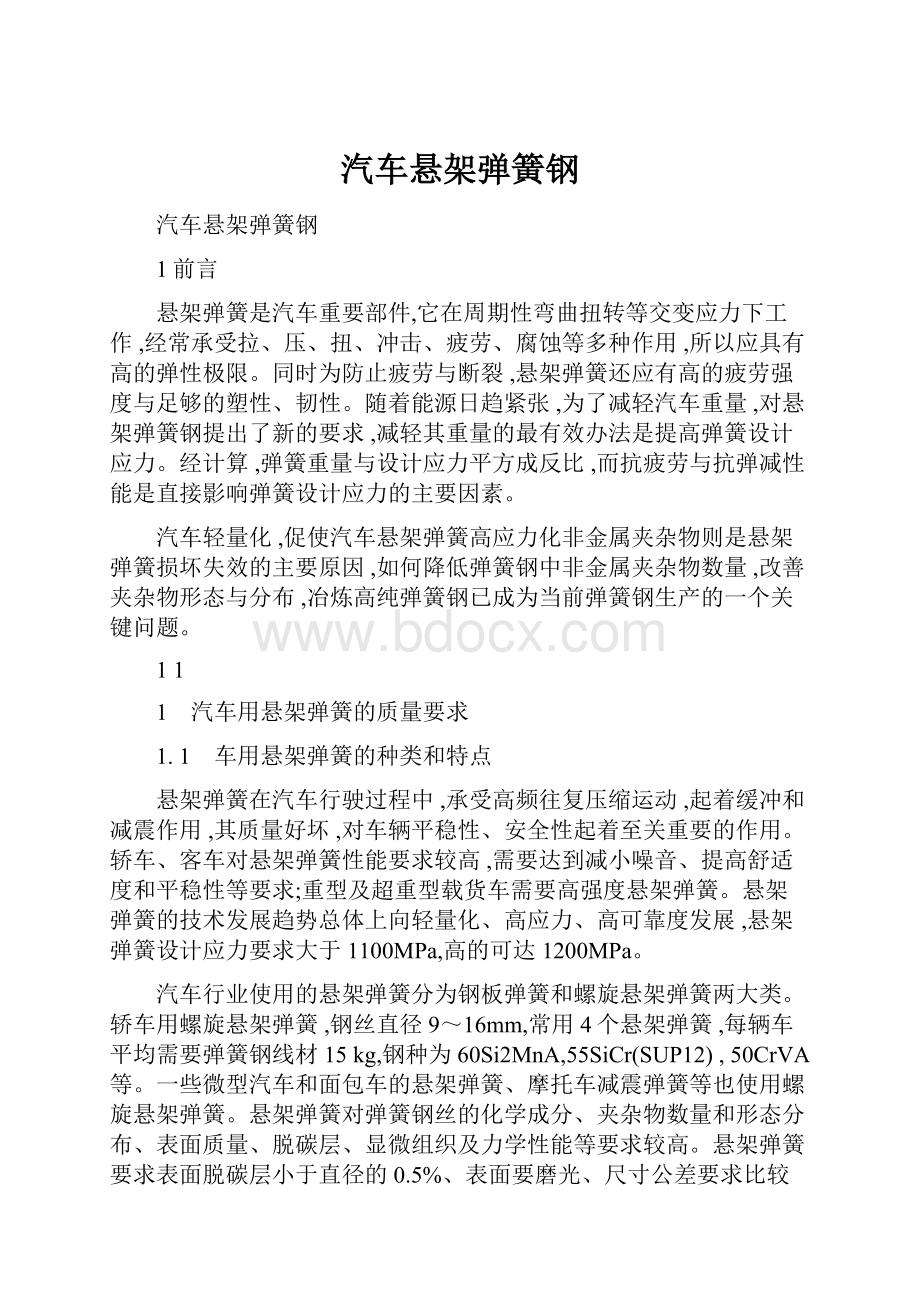
汽车悬架弹簧钢
汽车悬架弹簧钢
1前言
悬架弹簧是汽车重要部件,它在周期性弯曲扭转等交变应力下工作,经常承受拉、压、扭、冲击、疲劳、腐蚀等多种作用,所以应具有高的弹性极限。
同时为防止疲劳与断裂,悬架弹簧还应有高的疲劳强度与足够的塑性、韧性。
随着能源日趋紧张,为了减轻汽车重量,对悬架弹簧钢提出了新的要求,减轻其重量的最有效办法是提高弹簧设计应力。
经计算,弹簧重量与设计应力平方成反比,而抗疲劳与抗弹减性能是直接影响弹簧设计应力的主要因素。
汽车轻量化,促使汽车悬架弹簧高应力化非金属夹杂物则是悬架弹簧损坏失效的主要原因,如何降低弹簧钢中非金属夹杂物数量,改善夹杂物形态与分布,冶炼高纯弹簧钢已成为当前弹簧钢生产的一个关键问题。
11
1 汽车用悬架弹簧的质量要求
1.1 车用悬架弹簧的种类和特点
悬架弹簧在汽车行驶过程中,承受高频往复压缩运动,起着缓冲和减震作用,其质量好坏,对车辆平稳性、安全性起着至关重要的作用。
轿车、客车对悬架弹簧性能要求较高,需要达到减小噪音、提高舒适度和平稳性等要求;重型及超重型载货车需要高强度悬架弹簧。
悬架弹簧的技术发展趋势总体上向轻量化、高应力、高可靠度发展,悬架弹簧设计应力要求大于1100MPa,高的可达1200MPa。
汽车行业使用的悬架弹簧分为钢板弹簧和螺旋悬架弹簧两大类。
轿车用螺旋悬架弹簧,钢丝直径9~16mm,常用4个悬架弹簧,每辆车平均需要弹簧钢线材15kg,钢种为60Si2MnA,55SiCr(SUP12),50CrVA等。
一些微型汽车和面包车的悬架弹簧、摩托车减震弹簧等也使用螺旋悬架弹簧。
悬架弹簧对弹簧钢丝的化学成分、夹杂物数量和形态分布、表面质量、脱碳层、显微组织及力学性能等要求较高。
悬架弹簧要求表面脱碳层小于直径的0.5%、表面要磨光、尺寸公差要求比较严格、应无缺陷交货。
采用通常热加工方式难以达到用户要求,因此,轿车悬架用弹簧逐渐由热成形改为冷成形,经拉拔、热处理后制成卷簧。
悬架弹簧钢丝发展方向是降低碳含量、减少脱碳,提高塑性成形性和抗弹性衰减等性能。
车用悬架弹簧应用较多的是Si-Cr系弹簧钢。
这类钢的抗回火稳定性好,松弛抗力高,疲劳寿命较理想,但在一些微型车上,悬架弹簧也常用60Si2MnA或50CrVA钢。
扭杆弹簧结构简单,有利于车辆整体布置,在一些轿车和轻型车上应用,也有在重型军用车上应用的。
在传统Si-Mn弹簧钢的基础上通过降低C含量并添加Ni,Cr,Mo和V等合金元素,已开发出高强度和韧性的弹簧用钢。
在传统的Cr-V系弹簧钢中添加Nb可提高钢的抗延迟断裂性能,使钢的抗拉强度达到1800MPa。
提高弹簧疲劳强度的有效途径是对弹簧进行喷丸和氮化处理。
1.2 车用悬架弹簧对线材的质量要求
轿车悬架弹簧用线材对钢的纯净度、尺寸精度、表面质量有严格的要求。
实践证明,线材的直径精度对减少拉丝模磨损、降低能耗、减少断丝、保证拉拔稳定进行具有重要意义。
悬架弹簧用线材的直径公差控制在±0.2mm,椭圆度不大于直径公差的60%。
线材表面的裂纹、折叠、划伤等缺陷严重影响钢丝的质量,降低悬架弹簧的疲劳寿命。
线材表面应光滑,不得有裂纹、折叠、结疤、耳子等。
局部的凸块、凹坑、麻面等缺陷尺寸不得大于0.10mm。
线材力学性能要好,并且波动小。
线材通条抗拉强度波动≤40MPa,断面收缩率波动≤15%,索氏体体积分数≥85%,游离态铁素体对疲劳寿命有较大影响,体积分数应控制在1.5%以内,晶粒度为8级以上,不得有马氏体。
夹杂物作为疲劳裂纹源会引发疲劳裂纹的扩展,最终导致弹簧断裂,它所造成的弹簧失效已成为弹簧破损最主要的原因之一。
特别是在高压应力条件下使用的弹簧,疲劳极限与硬度之间不再是线性关系,当材料硬度HV值超过400以后,显微夹杂物将成为疲劳裂纹源,使材料的疲劳极限下降,而汽车悬架弹簧通常在HV值为430~535时使用,要求不得有大于15μm的脆性夹杂物。
表面脱碳会引起表面硬度降低,易在加工中形成表面疲劳裂纹源,对悬架弹簧的疲劳寿命有重要影响。
要求线材表面总脱碳层不大于线材公称直径的1%,避免全脱碳。
碳含量的波动,会引起力学性能波动:
碳含量与抗拉强度正相关,与断面收缩率负相关,减少碳含量可减少脱碳,提高成形性和抗弹减性。
碳质量分数的波动范围应小于0.03%。
硅元素具有高的固溶强化作用,对提高抗弹减性有利,硅含量过高易形成硅酸盐夹杂并产生脱碳倾向。
锰可以加强弹簧的强度和淬透性,但也增加了钢的过热敏感性和回火脆性。
如高品质55SiCr中,硅的质量分数一般在1.33%~1.45%,锰的质量分数为0.67%~0.69%。
硫和磷含量要严格控制,高质量悬架弹簧产品要求硫和磷的质量分数分别小于0.01%和0.015%,氧的质量分数≤15×10,氮的质量分数≤35×10。
1.3 车用悬架弹簧的生产工艺
悬架弹簧的制造方式有两种:
热卷成簧和冷卷成簧。
热卷成簧工艺:
弹簧直条(冷拉退火钢丝/热轧退火剥皮抛光料)→热卷簧→油淬火、回火→磨削、喷丸→热强压→整型→负荷分类→包装。
冷卷成簧工艺:
油淬火回火钢丝→冷卷簧→去应力→磨削、喷丸→热强压→整型→负荷分类→包装[1]。
2 国外超纯弹簧钢冶炼新工艺
60Si2MnA是高级优质弹簧钢,其纯净度、夹杂物形态及分布、表面质量对弹簧抗弹减性、疲劳强度有重要影响,俄罗斯奥斯尼斯克等冶金厂掌握了从直接还原铁冶炼60Si2MnA新工艺,日本大同特钢厂二次冶金技术的应用,为大批量生产低成本、高质量弹簧钢提供了可能。
.1 从直接还原铁冶炼超弹簧钢
1原料
奥斯尼斯克厂主要运用占金属炉料40%-100%的优质炉料——金属球团矿(由俄罗斯库尔斯克独一无二的地磁异常矿石直接还原)。
炉料由自动输送系统加入150t电弧炉中熔炼。
2.1.2 冶炼工艺
在熔炼中按配方准确控制添加合金元素(硅硅锰合金),认真制定脱氧工艺,将硅与铝直接加入炉中,在吹氩及真空冶炼时,监查铝的加入量,在连铸中采用保护套管与浸入式水口,设计、制造了专用气(氩)系统。
浇钢包采用高氧化铝耐火材
料,采用防止二次氧化的保护浇铸技术。
在浇钢包中添加固态造渣混合物脱硫。
2.2 二次冶金技术
2.2.1 降低夹杂物含量精炼技术
DH、RH真空脱气是常用精炼方法,在RH基础上,日本钢公司的RH-SCS法,见图1、2,大同特钢研制的ULO(超低氧)钢处理工艺可达极限含量。
大同特殊钢厂按图3所示生产工艺研究了纯洁度对悬架弹簧钢60Si2MnA所需性能影响,并得出如下结论:
(1)证实了氧含量低于15×10-6的超低氧(ULO)钢是实现悬架弹簧钢200kgf高应力值的一种有效手段。
(2)用超低氧加超低氮化钛工艺生产的ULO+ULTiN钢的疲劳极限和真空电弧重熔钢相同。
大同特殊钢厂ULO超低氧处理简介如下:
在超高功率碱性电弧炉中熔化钢水,吹氧后钢水加入Fe-Si进行脱氧处理并得到高碱度还原渣,然后将钢水倒入钢包,并将RH循环脱气设备插入钢液,汲取钢水进入真空室。
利用大容量喷射泵,保持真空度<13.3Pa(0.1mmHg),并将小流量氩气引入钢水,钢水发泡进入真空室,钢水中碳脱氧反应快速进行,从而钢水脱氧,当碳氧反应达到平衡时,加入铝脱氧剂,以促进脱氧产物上浮分离与去除,保持脱氧状态的稳定,继续进行脱氧操作,最后调整加铝量。
RH循环脱气后,氧含量下降到15×10-6以下,为保持氧含量不大于15×10-6,应在钢水浇注及凝固时保持钢水免遭污染,并促进去除脱氧产物。
采用脱气法生产超纯弹簧钢主要目的在于严格限制钢中氧含量,降低钢中夹杂物的尺寸与数量。
2.2.2 控制弹簧钢夹杂物形态及分布的纯洁钢精炼技术
此精炼技术是在ASEA-SKF或VAD精炼炉中通过合成渣控制弹簧钢中夹杂物组分、形状及分布。
日本神户制钢超纯化处理工艺如下:
用电弧使钢水保持适当温度,同时采用电磁搅拌去除夹杂物,控制夹杂物。
另外为了消除混入铝产生的不良影响,控制钢水加热及搅拌时钢包顶部渣子组分。
调整渣子碱度将钢中氧含量,控制在最适宜值,可使铝生成的夹杂物由高熔点的Al2O3、CaO·Al2O3、MgO-Al2O3转变成低熔点的CaO·Al2O3-SiO2·MgO的复杂夹杂物。
随着大量塑性夹杂物增加,Al2O3等脆性夹杂物大幅度减少。
通过调整渣子,控制夹杂物的工艺不但改善了弹簧钢的疲劳寿命及可靠性,而且提高了弹簧钢的抗弹减性及耐热性。
生产实践证明:
有害不变形Al2O3夹杂物含量明显降低,且剩余夹杂物组分是低熔点完全可变形的表面层与中心夹杂物CaO-SiO2-Al2O3,尺寸明显缩小,夹杂物总量下降,由于纯洁度改善从而提高了疲劳强度。
2新工艺特点
2.1使用直接还原铁,降低钢中有害元素含量
随着废钢多次循环使用及涂镀层钢铁制品的增加,废钢中有害杂质不断增加,特别是Sn、As、Cu、Pb等元素氧化性能比铁低,在冶炼时几乎100%进入钢水中,钢水凝固时,有害元素多数在表面富集,富集系数达几十倍、甚至上百倍,形成低熔点区,极易形成热脆,大大恶化了弹簧钢的塑性及抗弹减性。
使用优质还原铁作炉料,能生产高纯度钢,据介绍,使用100%直接还原铁与使用废钢相比,钢的屈服强度低15%左右,应变时效大大降低,钢中残余元素及夹杂物含量、形状都能控制在较好水平。
2.2使用气(氩)幕系统,降低钢中含氮量
氮对钢材机械性能影响较大,过高氮含量会导致低倍疏松,形成气泡。
电炉钢中氮含量为(50~70)×10-6,远高于转炉钢水平,这是由于电弧离子化作用,使钢水吸收了氮,而在电弧周围采用气幕系统就能降低钢水对氮的吸收。
同时,在使用直接还原铁时,还原铁中氧化铁与碳在氧化期的不间断沸腾形成泡沫渣,既能减少电弧对炉衬侵蚀,又能在熔池中逸出CO气泡,以带走钢中氮,降低氮含量<120×10-6。
2.3 二次精炼技术的运用与完善
过去,弹簧钢主要在电炉或平炉中冶炼,为不断提高弹簧钢质量,降低生产成本,国外冶金企业从主要采用电炉加电渣重熔或真空重熔逐步发展到如今的二次精炼工艺,这就为大批量生产低成本、低夹杂物优质弹簧钢提供了可能。
2脱氧工艺
分析汽车悬挂簧和阀门弹簧等的失效原因发现,引起疲劳破坏的主要因素为非金属夹杂物,尤其是Al2O3和TiN夹杂物对弹簧疲劳寿命的危害最大。
为生产高质量的弹簧钢,以往通常采用电炉-电渣重熔或真空电弧重熔等特种冶炼方法。
随着炉外精炼技术的发展,采用炉外精炼工艺可显著减少钢中的夹杂物,如日本采用RH真空脱气实现超低氧钢(ULO)或超纯钢(UCS)的生产。
在国内,目前人们主要考虑的是降低钢中气体含量和对夹杂物进行变性处理。
为防止弹簧钢连铸过程中因钢中残余铝含量较高导致水口结瘤现象,一般小方坯连铸均采用非铝脱氧剂及低铝硅铁,并通过控制精炼渣组成优化最终夹杂物的组成及分布,借此提高钢液的洁净度。
而大方坯连铸时由于水口直径较大,通常采用铝脱氧。
弹簧钢冶炼过程钢中气体含量的变化和造成连铸水口结瘤的原因,认为在LF或LF-VD流程中,降低钢液气体含量的第一步是降低钢液初始氧含量,在此基础上采用铝和硅预脱氧剂将钢中的溶解氧转化成Al2O3和SiO2夹杂物,再采用碱土或稀土合金进行深度脱氧或夹杂物变性、优化吹氩搅拌工艺和装置及采用埋弧渣精炼技术,使钢中的Al2O3夹杂物形成复合的大颗粒液态夹杂物上浮排除(采用钡合金可形成最低熔点为1120℃的低熔点复合夹杂物)。
同时对残余的夹杂物进行变性处理,最终得到以塑性夹杂物为主,且夹杂物细小、均匀、弥散分布的洁净弹簧钢[5]。
2.1不同脱氧条件下弹簧钢非金属夹杂物尺寸分布
众所周知,对弹簧材料产生有害影响的非金属夹杂物是那些在材料热轧状态下不变形的大颗粒脆性夹杂物,弹簧材料的强度越高,非金属夹杂物对其疲劳性能的影响就越敏感。
因此对高质量弹簧钢必须严格控制大颗粒非金属夹杂物的尺寸和数量。
弹簧钢中的非金属夹杂物主要由各类脱氧产物组成,如刚玉、石英、硅酸盐、铝酸盐等;其次是非脱氧产物,如硫化物、氮化物以及外来夹杂。
一般而言,具有良好热轧变形能力的硫化锰和钙铝硅酸盐对弹簧材料的疲劳性能不会产生危害,钢中的氮化钛颗粒尺寸通常很小,故其对材料疲劳性能的危害程度也较氧化物夹杂小。
作为构成弹簧钢大颗粒夹杂主体的脱氧产物,有可能通过控制脱氧工艺条件来控制脱氧产物在弹簧钢中的尺寸分布,以改善弹簧材料的疲劳性能。
薛正良[3]等人研究了工业生产中采用的3种脱氧和精炼工艺来分析弹簧钢非金属夹杂物尺寸分布:
工艺1:
80t超高功率电弧炉(EAF—EBT),用普通硅铁合金化,LF用CaO-CaF2系合成渣精炼,用连铸法浇铸成150mm×150mm小方坯。
工艺2:
80t超高功率电弧炉(EAF—EBT),用专用硅铁合金化,LF用CaO-SiO2-CaF2系合成渣精炼,用连铸法浇铸成150mm×150mm小方坯。
工艺3:
初炼炉为出钢18t的电弧炉,用专用硅铁合金化,LF用CaO2-Al2O3-SiO2系合成渣精炼,经VD处理后浇铸成400kg钢锭。
采用工艺1时弹簧钢60Si2MnA的T[O]和Als分布见图1,按工艺2生产时弹簧钢60Si2MnA的T[O]和Als分布见图2。
当不用铝终脱氧时,钢中的酸溶铝含量决定于硅铁中的铝含量,当硅铁含铝1.0%时,合金化时由硅铁带入钢液的铝达到0.025%,因此合金化后钢中的Als通常可达到0.01%~0.02%。
根据Al—O反应的化学平衡关系可知,钢中溶解氧将Als升高而下降,但从图1和图2可以看出弹簧钢中T[O]含量并不决定于钢中Als的含量水平,而是决定于LF精炼的吹氩制度。
上述结果表明,采用连铸法较采用模铸法能大幅度减少大型夹杂物的尺寸和数量。
当采用连铸工艺时,用工艺2生产的弹簧钢的夹杂物尺寸分布明显优于用工艺1生产的弹簧钢的夹杂物尺寸分布。
4 讨论
弹簧钢中的氧化物夹杂主要来自合金化和终脱氧时析出的一次脱氧产物和钢液冷却与凝固过程中析出的二次脱氧产物,当采用工艺1脱氧合金化时,一次脱氧产物量占总脱氧产物量的90%以上,因此钢液的脱氧过程实质上就是脱氧产物从钢中排除的过程。
钢包吹氩一方面利用气泡的浮选作用使夹杂物上浮分离,另一方面吹氩引起钢液环流使脱氧产物作跟随运动而不能有效去除。
因此,在这种情况下选择合理的吹氩制度十分重要。
当采用工艺2时,一次脱氧产物量仅占总脱氧产物量的50%左右,其余溶解在钢液中的氧将与碳在氩气泡壁上发生C—O反应而去除。
现代二次精炼工艺采用全程吹氩操作,因此,当采用工艺2和工艺3脱氧时吹氩过程对钢液溶解氧的去除起着十分重要的作用。
吹氩脱氧产生的气相脱氧产物不会污染钢液,因而采用工艺2和工艺3将大大减少残留于钢中的固相脱氧产物量。
采用工艺1脱氧和精炼时,钢中Als可达到0.01%~0.02%,成品材中T[O]分布在(10~30)×10-6。
从棒材中电解萃取出的夹杂物平均尺寸为26.16μm,尺寸大于40μm的夹杂物颗粒占14.14%,最大夹杂物颗粒尺寸达100~110μm。
采用工艺2脱氧和精炼时,钢Als分布在(10~18)×10-6,成品材中T[O]分布在(10~30)×10-6。
从棒材中电解萃取出的夹杂物平均尺寸为18.8m。
尺寸大于40μm的夹杂物颗粒占7.39%,最大夹杂物颗粒尺寸达60~70μm。
(4)采用模铸法浇铸时,浇钢过程的二次氧化和钢锭模内的卷渣造成成品材中存在大量大型夹杂。
从棒材中电解萃取出的夹杂物平均尺寸达44.6μm,40μm以上的夹杂物占48.11%。
2.2不同脱氧条件下弹簧钢氧化物夹杂的性质和形貌
薛正良[4]等人用光学显微镜和扫描电镜研究了工业生产条件下用不同脱氧工艺生产的60Si2MnA弹簧钢氧化物夹杂Al2O3、SiO2和铝硅酸盐的性质、形貌和控制。
工业生产中采用三种脱氧工艺,工艺1用硅铁合金化加喂铝线终脱氧,钢中AlSol.通常达到0.020%~0.030%;工艺2用硅铁合金化不用铝终脱氧,钢中AlSol.通常在0.008%~0.020%之间;工艺3用专用硅铁合金化,钢中AlSol<0.002%。
在前两种脱氧工艺下钢中T[O]与AlSol之间不存在相关关系,采用工艺3时钢中T[O]并不因AlSol低而升高。
钢中T[O]决定于精炼过程的吹氩制度。
采用工艺1和2脱氧时,钢中90%以上的溶解氧在一次脱氧时析出,这时脱氧产物的去除效率就决定了最终钢中的T[O]含量;采用工艺3脱氧时,一次脱氧量仅占总脱氧量的50%~60%,剩余溶解氧的绝大部分可通过精炼过程的吹氩来去除。
因此吹氩方式、吹氩强度和精炼时间的分配最终影响到钢中T[O]含量的高低。
2 不同脱氧工艺和脱氧阶段析出的夹杂物性质和形貌
2.2 铝终脱氧时析出的B类夹杂物
将经过铝终脱氧的弹簧钢热轧材金相试样用光学显微镜观察抛光面上的B类(Al2O3)夹杂形
貌,见图1。
图1a为已轧成串链状的B类夹杂物的典型形貌,它们是在钢液中聚集成簇后,在材料热轧时又被压碎,并沿轧制方向成串链状分布。
图1b、c为被MnS包裹的单个Al2O3颗粒的形貌。
在电解萃取的夹杂物群中,扫描电镜下发现的单个Al2O3颗粒形貌如图2,它们的线径达到60~80μm。
图1 铝终脱氧弹簧钢中典型的B类夹杂物
a2光学显微镜×300;b2扫描电镜×2000;c2扫描电镜×6000
图2 铝脱氧弹簧钢中电解萃取的Al2O3单个颗粒扫描电镜照片
a2×300;b2×200
2.3 专用硅铁合金化时析出一次脱氧产物SiO2
用专用硅铁合金化时钢中AlSol<0.0020%,此时钢中的一次脱氧产物为合金化时析出的SiO2夹杂。
由于弹簧钢60Si2MnA含硅1.8%~2.0%,故合金化时析出的SiO2量达到0.010%左右。
在热轧棒材磨制的金相试样上,光学显微镜下观察到的SiO2见图3。
图4为电解萃取的夹杂物群中在扫描电镜下发现的单个SiO2颗粒形貌,从能谱仪打出的成分看,它们几乎是纯粹的SiO2。
图3 硅铁合金化时析出的SiO2夹杂 ×800
图4 硅铁合金化时弹簧钢中SiO2夹杂颗粒,电解萃取,SEM:
a2×350;b2×350;c2×600;d2×500
2.4 普通硅铁合金化时析出的SiO2与铝反应生成的铝硅酸盐
硅铁中通常含有0.5%~2.0%的Al,若硅铁含铝1.0%,用硅铁合金化时由硅铁带入钢液的铝达到0.025%。
硅铁在钢液中溶解的同时参与脱氧反应析出SiO2,在精炼过程中,它们与钢液中的Al反应生成铝硅酸盐。
用普通硅铁合金化生产的弹簧钢热轧棒材的电解萃取夹杂物群中绝大部分是如图5所示的铝硅酸盐。
图5 铝硅酸盐夹杂的形貌,电解萃取,SEM:
a2×400;b2×1200;c2×500;d2×2000
2.5 普通硅铁合金化时析出的铝酸钙和铝硅酸钙
硅铁中除了含0.5%~2.0%Al外还含有1.0%~1.5%的钙,硅铁在钢中溶解时,Al和Ca参与脱氧有形成铝酸钙和铝硅酸钙的热力学和动力学条件。
图6为用普通硅铁合金化生产的弹簧钢热轧棒材中萃取出的铝酸钙和铝硅酸钙在扫描电镜下的形貌,其颗粒尺寸达20~40μm
图6 铝酸钙和铝硅酸钙的形貌,电解萃取,SEM:
a2×500;b2×1000
2.6 专用硅铁合金化时析出的二次脱氧产物
钢液用专用硅铁合金化时钢中AlSol很低,钢液中溶解的氧在钢液冷却和凝固过程中以CaO2-Al2O3-2SiO2硅酸盐夹杂析出。
这类夹杂物具有良好的塑性,在钢材热轧过程中随基体流变沿轧制方向延伸成长条状,在电解萃取的夹杂物群中,可以发现许多如图7所示的长条状硅酸盐夹杂。
金相试样上测定的夹杂物尺寸分布并不能代表钢材中夹杂物尺寸的分布,但金相试样上观察到的夹杂物形貌是它们在钢中的实际存在形貌。
图7 长条状硅酸盐夹杂物的形貌,电解萃取,SEM:
a2×300;b2×400;c2×400
3 结论
合金化时钢中主要析出SiO2,铁合金中的Al和Ca参与脱氧析出铝酸钙和铝硅酸钙。
精炼过程中,钢中Al与合金化时析出的SiO2反应生成铝硅酸盐。
当用铝终脱氧时,钢中析出Al2O3颗粒。
当用专用硅铁合金化时,钢中AlSol.控制在很低的水平,这时二次脱氧产物为具有良好变形能力的CaO-Al2O3-SiO2系硅酸盐,在钢材中它们的横向尺寸通常比一次脱氧产物小得多。
2.3合成渣处理对弹簧钢脱氧及夹杂物控制的影响
李正邦,薛正良[6]等人在实验室条件下研究了酸性和碱性合成渣处理弹簧钢时钢中酸溶铝、钙和氧含量的变化规律
通常的炼钢脱氧过程是先用Si2Mn预脱氧,然后加铝终脱氧,作为脱氧产物的硅酸锰和钢水中溶解的铝之间反应生成富含Al2O3的夹杂物。
在铝加入钢液的过程中,由于脱氧反应速度远大于铝在钢液中熔化和扩散的速度,故易产生局部
富铝而析出较大的夹杂物颗粒。
而用合成渣精炼脱氧时,钢液中不会产生局部富铝,因而析出的夹杂物成分均匀而细小。
以工业纯铁为原料,用中频感应炉熔炼的SUP7(成分%为:
0.60C、2.00Si、0.85Mn、0.0045S、0.011P、0.0067Alsol)浇铸成25kg钢锭。
钢锭锻成
Φ20mm钢棒,然后用氧化镁坩埚(Φ58mm×83mm)在碳管炉内进行二次精炼。
每次试验称取钢样800g,在指定温度恒温后加入预熔精炼渣40g,反应时间40min。
1823K时钢水经酸性渣处理后的酸溶铝变化与精炼渣组成的关系见图1和图2,
钢样原始酸溶铝含量为0.0067%。
实验结果表明应选择含应选择含Al2O3和MgO较低的酸性渣精炼钢液。
此外,从图3钢中全氧含量随精炼渣碱度的变化趋势来看,精炼渣碱度不宜低于1.0。
精炼反应的温度对渣钢反应也产生较大的影响,见图4。
碱性渣精炼钢液实验结果见图5,表明高碱度渣精炼时,渣中Al2O3和CaO不断被钢液中的Si还原,使钢中酸溶铝和全钙含量随反应时间延长不断增加。
图1 精炼渣碱度对钢中酸溶铝的影响
图2 精炼渣中Al2O3和MgO含量对钢中酸溶铝的影响
图3 精炼渣碱度对钢中全氧含量的影响
图4 反应温度对钢中酸溶铝的影响
图5 高碱度渣对钢中酸溶铝和全钙的影响
4 结论
(1)超低氧钢用铝终脱氧,并不能排除钢中存在危及材料疲劳性能的大颗粒夹杂物;若将钢中酸溶铝含量控制在较低或很低的范围,就可以避免可能析出的Al2O3对材料疲劳性能产生的危害。
(2)用酸性渣处理钢液时,渣的碱度、Al2O3和MgO含量对钢中酸溶铝的控制都存在较大的影响。
降低Al2O3含量一方面降低了渣中Al2O3的活度,另一方面可减少温度波动对钢液增铝的影响。
在实验室条件下碱性渣处理钢液使钢水有较大幅度的增铝和增钙。
3夹杂物
3.1 钢中脆性夹杂物相是弹簧疲劳破损最主要的原因之一[7]
夹杂物形态控制技术是现代洁净钢冶炼的主要内容之一,不同的钢种对夹杂物相的性质、成分、数量、粒度和分布有不同的要求