机械机床毕业设计94L22柴油机机体顶面精铣床设计.docx
《机械机床毕业设计94L22柴油机机体顶面精铣床设计.docx》由会员分享,可在线阅读,更多相关《机械机床毕业设计94L22柴油机机体顶面精铣床设计.docx(20页珍藏版)》请在冰豆网上搜索。
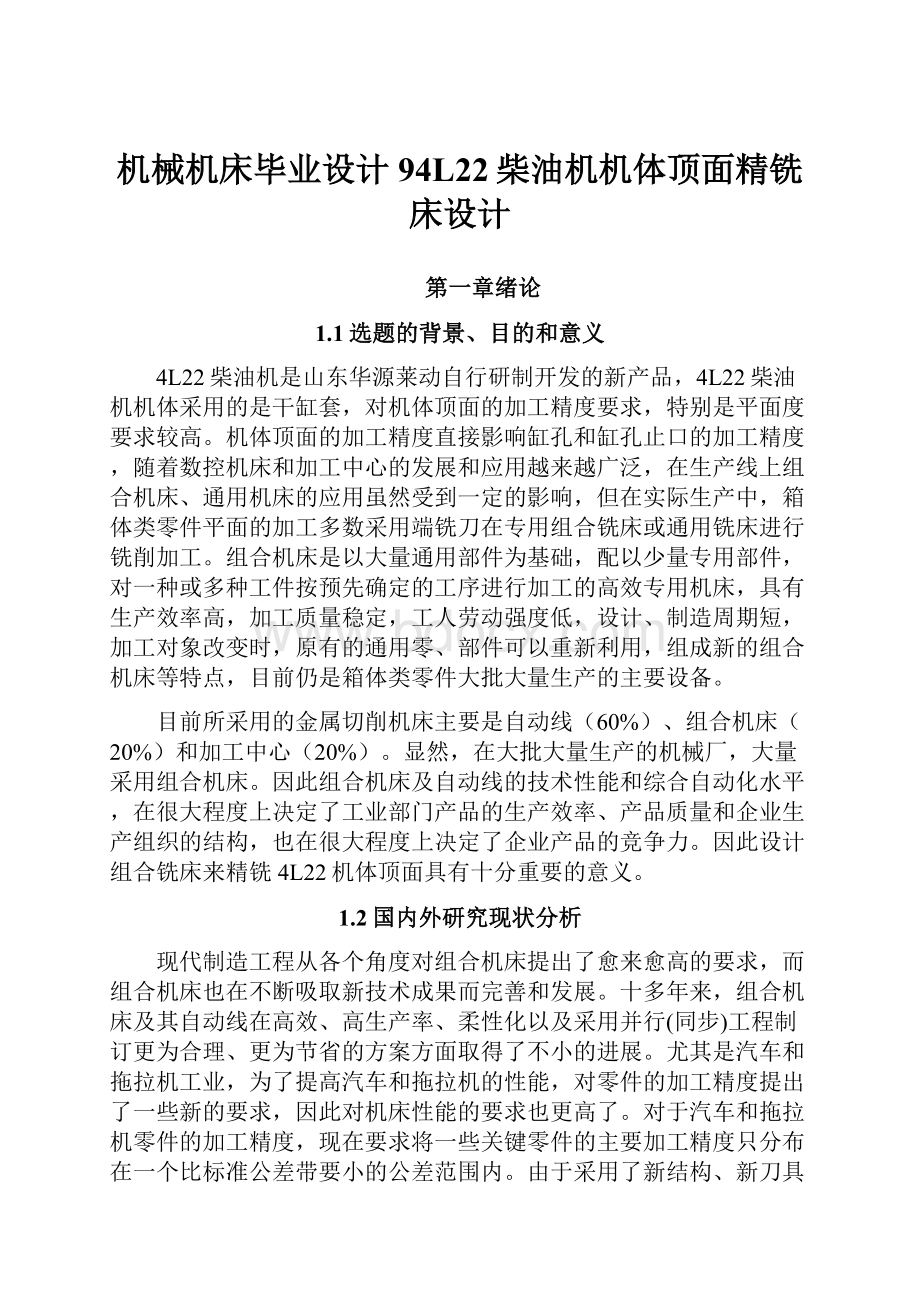
机械机床毕业设计94L22柴油机机体顶面精铣床设计
第一章绪论
1.1选题的背景、目的和意义
4L22柴油机是山东华源莱动自行研制开发的新产品,4L22柴油机机体采用的是干缸套,对机体顶面的加工精度要求,特别是平面度要求较高。
机体顶面的加工精度直接影响缸孔和缸孔止口的加工精度,随着数控机床和加工中心的发展和应用越来越广泛,在生产线上组合机床、通用机床的应用虽然受到一定的影响,但在实际生产中,箱体类零件平面的加工多数采用端铣刀在专用组合铣床或通用铣床进行铣削加工。
组合机床是以大量通用部件为基础,配以少量专用部件,对一种或多种工件按预先确定的工序进行加工的高效专用机床,具有生产效率高,加工质量稳定,工人劳动强度低,设计、制造周期短,加工对象改变时,原有的通用零、部件可以重新利用,组成新的组合机床等特点,目前仍是箱体类零件大批大量生产的主要设备。
目前所采用的金属切削机床主要是自动线(60%)、组合机床(20%)和加工中心(20%)。
显然,在大批大量生产的机械厂,大量采用组合机床。
因此组合机床及自动线的技术性能和综合自动化水平,在很大程度上决定了工业部门产品的生产效率、产品质量和企业生产组织的结构,也在很大程度上决定了企业产品的竞争力。
因此设计组合铣床来精铣4L22机体顶面具有十分重要的意义。
1.2国内外研究现状分析
现代制造工程从各个角度对组合机床提出了愈来愈高的要求,而组合机床也在不断吸取新技术成果而完善和发展。
十多年来,组合机床及其自动线在高效、高生产率、柔性化以及采用并行(同步)工程制订更为合理、更为节省的方案方面取得了不小的进展。
尤其是汽车和拖拉机工业,为了提高汽车和拖拉机的性能,对零件的加工精度提出了一些新的要求,因此对机床性能的要求也更高了。
对于汽车和拖拉机零件的加工精度,现在要求将一些关键零件的主要加工精度只分布在一个比标准公差带要小的公差范围内。
由于采用了新结构、新刀具、新工艺方法、刀具自动补偿系统、专用刀具的复合工艺。
直接利用软件进行误差补偿等办法,组合机床加工精度正在不断提高。
现阶段在组合机床上加工大平面的平面度已达到lm长上0.02-0.04mm.粗糙度达到Ra0.4-0.8um;孔经精度达到H5-H6;孔的圆度和圆柱度达到0.0015-0.055;定位销孔的中心距精度达到
0.013mm;一般孔位精度达到
0.02-
0.025mm;单向镗孔的同轴度达0.005-0.01mm;双向镗孔的同轴度达到015-0.02mm;一些特种加工工艺的精度,如止口精度可达到0.015-0.02mm.缸盖阀座及导管孔的同轴度达到0.0075-0.01mm。
[1]为适应高效加工的需要,现代组合机床自动线和自动加工系统的生产节拍愈来愈短,自动线的节拍,主要是通过缩短基本时间和辅助时间来实现的。
缩短基本时间的主要途径是采用新的刀具材料和新颖刀具,以提高切削速度和进给速度来缩短基本时间。
缩短辅助时间主要是缩短包括工件输送、加工模块快速引进以及加工模块由快进转换为工件后至刀具切入工件所花的时间。
为缩短这部分空行程时间,普遍采用提高工件或随行夹具的输送速度和加工模块的快速移动速度。
滑台的工作循环时间必须相应缩短。
国外有些厂家中等规格滑台的工作循环时间已缩短到5s。
其中快速行速度已达15m/min,而最大工作进给速度由通常的0.7m/min提高到1.2-1.5m/min,切入有的已可缩短到0.25mm。
要提高快进和工作行程速度,需要有高的转换精度,用伺服驱动滑台便能满足要求。
现代组合机床和自动线作为机电一体化产品,它是控制、驱动、测量、监控、刀具、和机械组件等技术的综合反映。
近些年来,这些技术有长足进步,同时作为组合机床主要用户的汽车和内燃机等行业也有很大的变化,其产品市场寿命不断缩短,品种日益增多且质量不断提高。
这些因素有力的推动和激励了组合机床和自动线技术的不断发展。
在工业发达国家的组合机床行业中组合机床设计已普遍采用CAD工作站,在设计室几乎很难见到传统的绘图板。
CAD除应用于绘图工作外,并在构件的刚度分析(有限元法)、组合机床及自动线设计方案比较和选择,以及方案报价等方面均已得到广泛应用,从而显著得提高了设计质量和缩短了设计周期。
为缩短产品开发周期、降低制造费用和提高产品质量世界上许多机械厂都在积极推行精益生产方式其主要内容之一是并行工程,既要求产品开发部门、生产规划部门和组合机床制造厂之间进行紧密合作。
组合机床厂则需要装备制造部门早期介入用户产品的规划和设计,在产品设计部门考虑其结构和功能时,能协同考虑产品的加工和装配工艺从而加速产品开发、降低制造费用和提高产品质量的目的,从而取得较好的经济效益。
[2]
现代,组合机床自动线技术取得了很大的进步,自动线在加工精度、生产效率、利用率、柔性化和综合自动化等方面的巨大进步,标志着组合机床自动线技术发展达到的高水平。
自动线的技术发展,刀具、控制和其它相关技术的进步以及用户需求的变化起着重要的推动作用,其中,特别是CNC控制技术对组合机床自动线结构的变革及其柔性化起着决定性作用。
第二章方案选择与论证
2.1确定方案
4L22柴油机机机体顶面的铣削加工可采用如下方案:
方案1、选用通用的立式升降台铣床、设计专用夹具精铣4L22柴油机机机体顶面;
方案2、设计组合铣床和专用夹具精铣4L22柴油机机机体顶面;
方案3、选用镗铣加工中心、设计专用夹具精铣4L22柴油机机机体顶面。
2.2方案分析和选择
方案1,选用通用的立式升降台铣床,工艺范围广、通用性强,但它的生产率低、工人劳动强度大,同时它的刚度、强度不高,所以加工精度低;
方案2,设计组合铣床,组合铣床是已经系列化、标准化的通用部件和少量专用部件组成的一种高效专用机床。
它的生产率比通用机床高几倍至几十倍,它的加工精度稳定,自动化程度高,工人劳动强度低,同时因为结构模块化、组合化可按工件或工序要求,用大量通用部件或少量专用部件灵活组成各种类型的组合机床及自动线,配置灵活,机床易于改装,产品或工艺变化时通用部件可重复利用。
在大批大量生产中,设计组合铣床精铣4L22柴油机机机体顶面是理想的方案。
方案3,选用镗铣加工中心,具有适应产品更换能力强、加工精度高等优点,但它的造价昂贵、机床生产率有时不如组合铣床。
4L22柴油机机机体的生产纲领是大批生产类型,顶面的加工精度要求高。
通过上面的分析,为满足生产纲领,同时在满足加工精度的要求上尽量降低生产成本,决定采用方案2设计组合铣床来精铣4L22柴油机机体顶面。
第三章4L22柴油机机体顶面精铣床外观图设计
对4L22柴油机机体进行工艺分析:
根据工件工序卡片和4L22柴油机机体图纸,机体顶面进行精加工前,机体的两端面、两侧面已加工完毕长度为430
0.15mm,宽度为254mm;机体底面和底面两个定位销孔已加工完毕,半精铣顶面保持的高度为314.2
0.10mm,精铣顶面之后机体高度为313.2
0.10mm,加工余量为1mm。
背吃刀量
=1mm,机体顶面的宽度为155mm。
根据零件的结构、形状和尺寸特点及加工要求,4L22柴油机机体顶面精铣床外观图采用立式布局形式,该布局形式有利于简化夹具的的定位、夹紧机构,夹紧也比较省力。
考虑到该机床是大批大量生产,设计组合铣床来加工机体顶面。
铣削头、滑台分别是实现主运动和进给运动的,为缩短设计制造周期,同时为提高铣床适用产品更新换代的能力,决定采用标准的通用部件。
立柱、侧底座为组合铣床的基础部件,为了降低生产成本,在满足加工要求的条件上,决定参照标准立柱、侧底座部件自行设计。
3.1选取铣刀
根据4L22机体加工部位的形状和加工精度的要求,选用硬质合金弹性夹固细齿可转位面铣刀,材料为YG6。
该刀具依靠微调装置来解决端跳精度,所以能够确保机体顶面的加工质量。
查《机械工艺师手册》[3],硬质合金铣刀参数的选取:
铣刀直径d=(1.1-1.6)
,铣刀直径应采用公比为1.25的标准系列即d=50、63、80、100、125、160、200、250…mm.根据4L22机体顶面宽度
=155mm,选取铣刀直径
200mm,Z=16。
3.2选取动力部件
3.2.1计算铣削力
查《机械工程手册》[4]表46.4-8组合机床用硬质合金端铣刀的铣削用量,工件材料为灰铸铁HT250时:
精加工
=0.05-0.2mm/z,切削速度为
=80-130m/min。
选取
=0.15mm/z,切削速度
=120m/min;
确定主轴转速:
取200r/min,
所以实际切削速度为:
=
查《机械工程手册》[4]表46.4-9硬质合金端铣刀的铣削功率公式:
铣削深度(mm)。
每齿进给量(mm/z)。
铣削宽度(mm)。
铣刀齿数
铣刀转速(r/min)。
查表46.4-10硬质合金铣刀铣削功率的修整系数:
,
所以
根据
得圆周铣削力:
查《机械工程手册》[4]表46.4-14
当采用对称铣时:
取0.4,得进给力:
3.2.2选取主运动部件—铣削头
铣削头是实现主运动的,一般有皮带传动装置和齿轮传动装置的铣削头。
由于铣削是断续切削,而且在一定铣削宽度上同时铣削的刀齿数是变化的,因而会引起振动,因此在铣削头的结构上必须使主轴和主轴箱体具有足够的刚性,并要适当提高传动系统的传动平稳性。
考虑到上述原因决定采用齿轮传动装置的铣削头。
根据主轴转速、刀盘直径。
查《大连专用机床厂》[5]通用部件样本选取型号为1TX40的铣削头,传动装置型号为1NGb40(齿轮传动装置),功率为7.5kw。
验证功率:
=0.75-0.85,为保证选取的电动机功率能够满足所需的切削功率,选取最小值,取
=0.75,
所以能够满足铣削功率的要求。
3.2.3选取进给运动部件—机械滑台
组合机床动力滑台是实现进给运动的通用部件,选用合适的动力滑台关系到组合机床整机的性能和经济性,选用时往往根据主动力部件的大小(即切削力和进给力)选用,一般选用较主动力部件同规格或大一号规格,精加工机床选用精密滑台。
根据驱动方式不同可分为液压滑台、机械滑台和专用的机械铣削滑台。
由于本工序是精加工,加工余量不大,铣削力小,采用一般的液压滑台和机械滑台即可满足加工要求,所以从减少生产成本方面考虑决定不采用专用的铣削滑台。
液压滑台和机械滑台由于这两种滑台采用了不同的传动装置,因而在性能、使用及维修等方面都有自己的特点,而机械滑台较液压滑台具有进给量稳定,慢速无爬行、高速无振动,可降低加工工件的表面粗糙度值,具有较好的抗冲击能力,不会因冲击而损坏刀具的运行等优点。
此外考虑到生产成本等因素,决定采用机械滑台。
根据进给力
、加工零件的结构、形状和尺寸以及工作行程,查《大连专用机床厂》[5]通用部件样本选取型号为1HJ50M的机械滑台。
该滑台的最大行程为1000mm,台面宽500mm,台面长1000mm,最大进给力为
能够满足精铣4L22柴油机机体顶面加工要求。
3.2.4立柱尺寸确定
立柱是机床的支承部件,可以选择标准立柱,也可以自行设计非标准立柱。
标准立柱主要是与动力滑台配套使用的,它的成本比较高,由于铣削加工的功能比较单一,不需要配重和其它要求,因此决定设计非标准的立柱。
参考标准立柱1CL50的联系尺寸确定立柱的具体尺寸,见附件1:
4L22柴油机机体顶面精铣床外观图。
3.2.5中间底座尺寸确定
为了与选用的机械滑台配套使用,根据滑台的外观尺寸、工作行程,参考标准侧底座1CC50M的联系尺寸确定中间底座的具体尺寸,见附件1:
4L22柴油机机体顶面精铣床外观图。
3.2.6机床的工作循环
上料——工件夹紧——主轴启动——机械滑台快进——机械滑台工进——主轴停止——机械滑台快退——工件松开——下料。
第四章夹具设计
4.1确定夹具定位方案,设计定位装置
4.1.1定位方案的确定
工件在机床上加工时,为保证加工精度和提高劳动生产率,必须使工件在机床上相对刀具占用正确的位置,即定位。
该工序加工要求为机体顶底面高度为313.2
0.10mm及顶面对底面平行度要求,根据六点定位原理,满足该工序加工要求,需要限制绕X轴、绕Y轴、Z向三个自由度,如图4-1所示:
图4-1
本工序加工前底面和底面的定位销孔已加工完毕,因此可采用“一面二孔”组合定位,但考虑到“一面二孔”组合定位结构复杂,。
为了简化夹具结构,同时因为机体的两端面、两侧面已加工完毕所以决定采用三基面组合定位。
以机体底面为第一定位基准,限制工件三个自由度;以后侧面为第二定位基准,限制工件的两个自由度;左端面为第三定位基准,限制工件一个自由度,保证机体能够准确的定位。
4.1.2定位元件的设计
定位元件在夹具中的布置:
一方面要符合六点定位原理,另一方面为保证工件的定位稳定性,要使支承点之间的距离尽量取大。
这样可使工件的重力和切削力的作用点都落在支承点联线所组成的平面内。
在大多数情况下,工件的一个平面,在夹具中不是支撑在三个点上,而是支承在四个或更多一些的支承点上,这样可以提高“机床-夹具-刀具-工件”工艺系统的刚性,避免夹紧力和切削力超出支承点,引起工件的弹性变形,影响加工精度。
所以在底面采用两块长条定位板来实现三点定位,如图4-2所示:
图4-2
该结构清屑容易,结构紧凑。
后侧面采用两块短定位板,限制工件的两个自由度。
左端面采用一块长条定位板,限制工件的一个自由度。
定位元件装入夹具体后,为使各支承面在一个水平面内,用于同一定位基面的定位板应再进行修磨,保证等高要求[6]。
4.1.3定位误差的分析和计算
对一批工件来说,刀具经调整后位置是不动的,即被加工表面的位置相对于定位基准是不变的,所以定位误差就是工序基准在加工尺寸方向上的最大变动量。
对工序尺寸L的进行定位误差计算和分析:
加工机体顶面时,尺寸L的工序基准和定位基准均是机体的底面,基准重合,所以基准不重合误差:
;
由于机体底面是已经加工过的表面,忽略平面度误差,所以基准位置误差
所以工序尺寸L定位误差:
通过上面分析,该定位方案能满足工序尺寸313.2
0.10mm的要求。
对平行度进行定位误差分析:
加工机体顶面时,平行度的工序基准和定位基准均是机体底面,基准重合,所以基准不重合误差:
由于机体底面是已经加工过的表面,忽略平面度误差,所以基准位置误差
所以顶面对底面的平行度的定位误差为:
通过上面分析计算,该定位方案不会因为定位产生定位误差,定位精度非常高,所以能满足尺寸L、平行度的加工要求。
4.2确定夹紧方案,设计夹紧装置
工件在夹具中的夹紧,将工件定位后的位置固定下来,保持工件在定位中获得的正确位置,使其在夹紧力、切削力等外力作用下,不发生移动和振动。
夹紧装置的设计和选用是否正确合理,将直接影响工件的加工质量和生产率,因此对夹紧装置提出以下要求:
确能保证工件定位后占据的正确位置,有助于定位,不应破坏定位;夹紧力的大小要适当、稳定,既要保证工件在整个加工过程中的位置稳定不变,振动小,又要使工件不产生过大的夹紧变形,夹紧力稳定可减少夹紧误差;夹紧装置的复杂程度与生产类型相适应;工艺性好,使用性好,其结构应尽量简单,便于制造和维修,尽可能使用标准夹具零部件,操作方便、安全、省力。
4.2.1夹紧力的确定
设计夹具的夹紧机构时,所需夹紧力的确定包括夹紧力的作用点、夹紧力的方向、夹紧力的大小三方面内容。
确定夹紧力方向:
确定夹紧力的方向时,应使夹紧力的方向有利于工件的准确定位,而不能破坏定位,一般要求主夹紧力应垂直于第一定位基准面,此外夹紧力的方向应方便装夹和有利于减小夹紧力。
该工序是以机体底面为第一定位基准,所以决定选择垂直于第一基准面往下的夹紧力。
确定夹紧力的作用点:
夹紧力的方向确定后,夹紧力的作用点的位置和数目的选择将直接影响到工件定位后的可靠性和夹紧后的变形。
夹紧力的作用点应与支承点“点对点”对应,或在支承点确定的区域内,以免破坏定位或造成较大的夹紧变形,同时应位于工件刚性高的方向和部位。
根据以上条件和机体的结构特点选择夹紧力的作用点位置位于两长条支承板的正上方压在机体的加强筋和凸台上等刚性高的部位。
为了减小夹紧变形,决定选取4个作用点,让夹紧力分散作用,如图4-3所示:
图4-3
计算夹紧力:
在加工过程中,工件受到切削力、离心力、惯性力及重力等的作用。
理论上,夹紧力的作用应与上述的力的作用平衡;而实际上,夹紧力的大小还与工艺系统的刚性、夹紧机构的传递效率等有关。
而且切削力在加工过程中是变化的,因此夹紧力的计算是个很复杂的问题,只能进行粗略的估算。
估算时,应找出对夹紧最不利的瞬时状态,估算此状态下所需要的夹紧力,并考虑主要因素在力系中的影响,略去次要因素在力系中的影响[7]。
对机体进行受力分析,如4-4图示:
图4-4
1、抵消进给力所需的夹紧力:
设实际夹紧力为F。
根据已知:
4L22机体的质量:
m=70kg
则G=mg=70
9.8=686N=
由受力分析得:
列平衡方程式:
(
+
)f=
查夹具设计2-13附表,当定位支承表面为光滑表面时,摩擦系数f=0.2
=
F=K
精加工时,安全系数:
K=1.5-2,取K=2,
则所需夹紧力为:
F=K
=2
=5540N
2、抵消主铣削力所需的夹紧力:
列平衡方程式:
[
]=1725
(
)
整理0.43
=715+686
(
)
由该式可看出当
=0.215时是对夹紧最不利的瞬时状态所需的夹紧力最大。
所以当
=0.215时
所以所需实际夹紧力为:
F=
=4010N
精加工时安全系数:
K=1.5-2,取K=2,
所以夹紧力为:
F=KF=8020N
同理,当
时,对夹紧最不利的瞬时状态为
=0.215,此时所需的夹紧力最大。
所以,所需总的夹紧力为:
W=8020+5540=13560N
单侧压板的夹紧力为:
=
=6780N
对压板进行受力分析,如图4-5所示:
图4-5
由受力平衡得:
6780
215=
185
所以
=8704N
4.2.2夹紧机构的设计:
楔铁夹紧机构是组合机床夹具常用的一种增力机构,由于其结构简单,工作可靠和调整方便,在组合机床夹具中得到广泛应用。
为保证工作可靠,减少所需液压缸的推力,
降低生产成本,决定采用楔铁夹紧机构,采用液压驱动方式。
考虑到本工序是精加工,所需的夹紧力不大,在结构尺寸上为与液压缸配套使用,查《组合机床及其调整与使用》[8]决定采用1T0232楔铁圆柱部分直径为60mm标准的楔铁夹紧机构。
该机构楔铁的楔角
=
,楔铁工作行程50mm,夹紧范围1-10mm,增力比(传递力放大倍数)为1.8。
4.2.3动力装置(液压油缸)的设计
为使夹具的结构紧凑,决定自行设计液压油缸。
根据经验,选液压油缸的直径为80mm,活塞杆的直径为40mm,大腔的工作面积为50
,小腔的工作面积37.7
。
活塞杆所需的推力:
Q=
=4835N
现在工厂所用的液压油液的压力一般为:
1.25-5Mpa[10],因为该工序是精加工,夹紧力不大所以决定取1.25Mpa
计算油缸的工作压力:
由公式
得
大于所需的活塞杆推力
,
所以能够满足加工的需要。
4.3对刀装置的设计
夹具安装在机床工作台上,需要确定刀具相对夹具定位元件的位置,因此需设计对刀装置。
对刀块可以自行设计,或选用标准对刀装置。
在大批大量生产中,为了简化夹具结构,常采用标准工件对刀或试切法对刀,第一件对刀后,后续工件就不在对刀,此时可以不设计对刀装置。
该设计采用的组合铣床是大批量生产类型,同时考虑到工件的结构尺寸决定采用标准工件进行对刀,对刀后,后续工件就不在对刀[9]。
4.4设计夹具底座:
夹具底座有焊接钢板的、铸铁的等[8],考虑到铸铁的抗压强度高、减震性能好、成本低等优点,同时在铸造夹具底座时可设置加强筋,增加夹具体的刚度和强度。
所以决定采用铸铁夹具底座,具体尺寸见附件3:
4L22柴油机机体顶面精铣床夹具图纸。
第五章结论
本文主要介绍了4L22柴油机机体顶面精铣床的设计。
研究的主要问题是4L22柴油机机体顶面精铣床外观图设计和夹具设计。
根据4L22柴油机机体的结构、形状和尺寸特点,4L22柴油机机体顶面精铣床外观图设计选用了通用部件:
铣削头、机械滑台等,配以专用的夹具和立柱、侧底座等基础部件,采用立式布局形式组成一组合铣床;夹具的设计,采用三基面组合定位,采用机动夹紧方式,使用液压斜楔夹紧装置完成工件夹紧。
该设计方案的具有设计制造周期短,生产率高,加工质量稳定,工人劳动强度低,产品更新时,组合铣床上的通用部件仍可重新利用组成新的组合机床等优点。
经过分析和精度验算表明该设计方案能够满足4L22柴油机机体生产纲领要求,能够保证4L22柴油机机体顶面的加工精度和表面质量要求。
本次设计的4L22柴油机机体顶面精铣床,并没有实现完全的自动化。
上料、下料需要人工完成,夹紧时,还需人工将压板送入送出,加重了工人的劳动强度,增加了辅助时间,使生产率的提高受到一定的影响,操作误差在一定程度上影响了产品的加工精度。
随着现代机械制造工业的发展,实现高生产率、高质量、高柔性是当前组合机床发展的一必然趋势。
建议在以后的设计中,能着重从减轻工人的劳动强度,提高生产率和提高加工质量方面考虑,可以选用数控滑台、数控铣削头等通用部件组成数控组合铣床,设计自动上下料装置,实现机床的完全自动化,进一步提高生产效率和加工精度。
参考文献
[1]金振华.组合机床与自动线.机械工业出版社,1990
[2]徐旭东.现代组合机床技术及其发展中国机械工程1995第五期
[3]徐灏.机械工艺师手册机械工业出版社,2000694~695
[4]机械工程手册、电机工程手册编辑委员会编.机械工程手册机械工业出版社,198246.342~46.346
[5]大连专用机床厂.通用部件样本
[6]东北重型机械学院、洛阳农业机械学院、长春汽车厂工人大学编.机床夹具设计手册上海科学技术出版社1974
[7]吴国梁.铣工实用技术手册江苏科学技术出版社2002.5258~369
[8]金振华.组合机床及其调整与使用机械工业出版社1984187~214
[9]大连组合机床研究所编.组合机床设计机械工业出版社1973.2108~114
[10]路甬祥.液压气动技术手册机械工业出版社2001.7
[11]于振汉.组合机床对提高大批量零部件加工质量及生产效率的作用19952~6
[12]李维荣.标准紧固件实用手册中国标准出版社1999.2
[13]上海市机械工程学会编.简明实用机械手册机械工业出版社1984.11190~210
[14]大连组合机床研究所编.组合机床设计参考图册机械工业出版社1975122~123
致谢
经过两个多月努力的工作,论文最终得以完稿;在此谨向曾给予过我关心和帮助的老师、同学表示衷心的感谢。
此次设计是对大学四年所学专业课的一个综合运用,通过这次设计使以前所学课程得到进一步复习和加深。
本文是在李爱芝老师的亲切关怀和精心指导下得以完成的。
在导师的帮助下,顺利完成了该课题的选题、设计、实施和完稿。
导师严谨求实的治学精神、精益求精的科研态度、渊博宽广的学识和高尚的道德情操都给我留下了深刻的印象,并