数控镗铣床购买技术协议.docx
《数控镗铣床购买技术协议.docx》由会员分享,可在线阅读,更多相关《数控镗铣床购买技术协议.docx(24页珍藏版)》请在冰豆网上搜索。
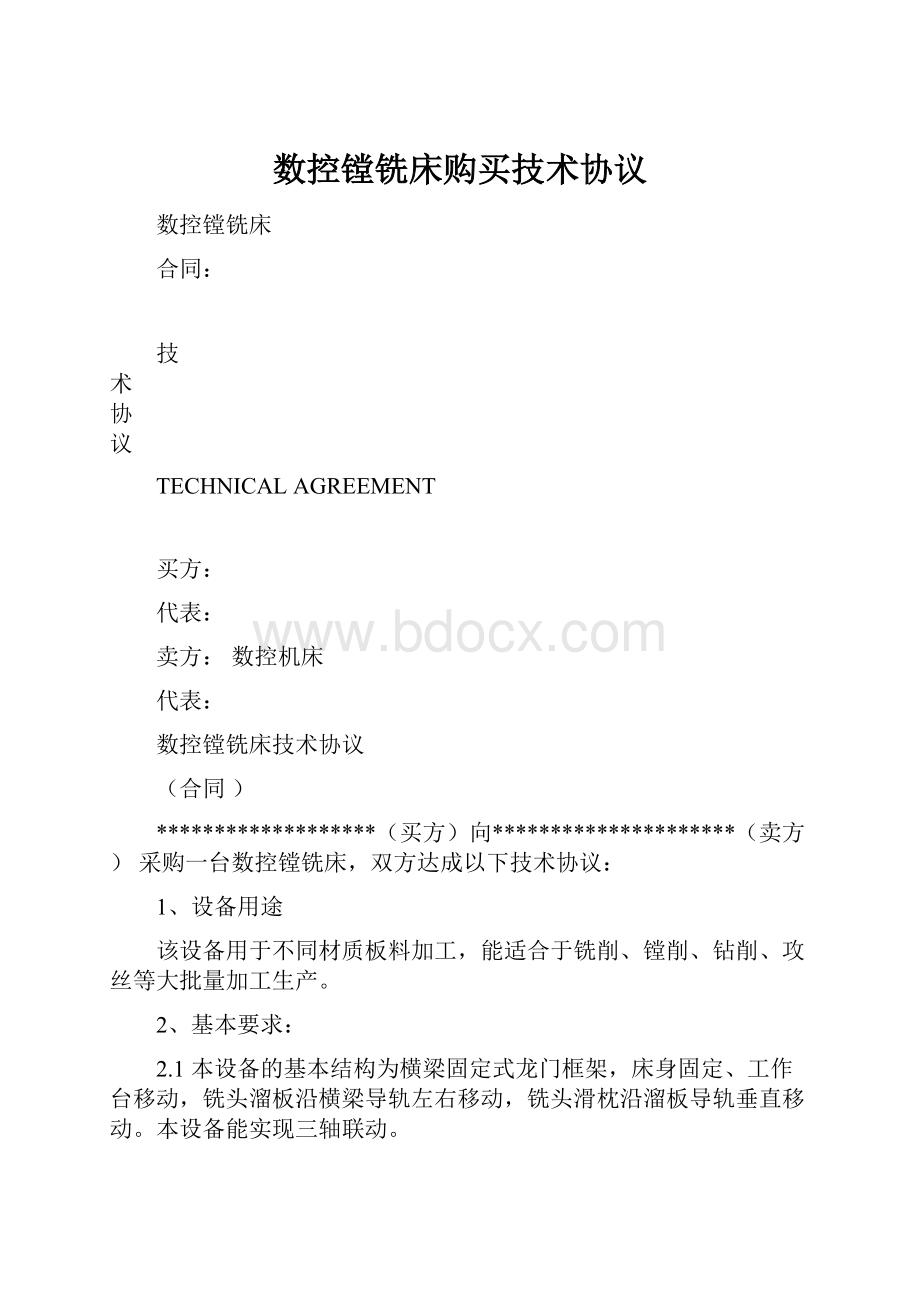
数控镗铣床购买技术协议
数控镗铣床
合同:
技
术
协
议
TECHNICALAGREEMENT
买方:
代表:
卖方:
数控机床
代表:
数控镗铣床技术协议
(合同)
*******************(买方)向*********************(卖方)采购一台数控镗铣床,双方达成以下技术协议:
1、设备用途
该设备用于不同材质板料加工,能适合于铣削、镗削、钻削、攻丝等大批量加工生产。
2、基本要求:
2.1本设备的基本结构为横梁固定式龙门框架,床身固定、工作台移动,铣头溜板沿横梁导轨左右移动,铣头滑枕沿溜板导轨垂直移动。
本设备能实现三轴联动。
2.2本设备由床身、工作台、立柱、横梁、溜板、液压系统、润滑系统、冷却系统、自动排屑系统、气动系统、数控系统、电控柜、操作台等组成(在无附件头小车的情况下,附件头安放位置不能与Y轴加工区干涉)。
2.3本设备必须是全新设备(包括所有零部件、元器件和附件),适合于铣削、镗削、钻削、攻丝等大批量加工生产。
2.4本设备加工精度必须满足工艺设计图纸要求,具有铣削、镗削、钻削、攻丝等功能,可加工各种类型复杂二坐标曲面。
2.5本设备结构设计合理,必须有足够的强度、刚度以及良好的稳定性,并且其构件应具有良好的耐磨性和较小的热变形。
本设备所有大的焊接件、铸件应当进行适当的热处理确保设备的精度稳定可靠;本设备在环境温度-5~45℃,相对湿度≤90%条件下,要求能正常连续工作22小时,且精度稳定。
2.6本设备零部件应选用优质材料制造,所选用的机械、液压、电气、电子元件是优质的、成熟的、可靠的系列产品。
2.7本设备应有可靠的安全保护、报警、保险措施,以防止误操作或意外事故致使机器受损或人身伤亡。
2.8本设备的零件和仪表及全部图纸资料的度量单位全部采用国际单位(SI)标准;所有仪表、零部件的设计、制造及所用材料应符合ISO和IEC标准或其他同等标准。
2.9本设备必须技术先进、成熟、可靠的且能满足用户产品加工工艺要求,在中国市场上有使用状况良好的同类产品操作直观简便,易于维护和维修。
3、主要参数:
1
工作台面积(宽×长)
2000×4000mm
2
工作台最大承重
15000kg
3
工作台T型槽数(纵向均布)
9个
4
工作台T型槽宽
36mm
5
工作台T型槽间距
200mm
6
立柱间距
≥2600mm
7
主轴端面至工作台面距离
100~800mm
8
主轴锥孔
ISONO.50
9
进给速度
X、Y轴
覆盖1~15000mm/min
Z轴
覆盖1~12000mm/min
10
快速移动
X、Y轴
15000mm/min
Z轴
12000mm/min
11
X轴行程
≥4200mm
12
Y轴行程
≥3200mm
13
Z轴行程
≥700mm
14
X轴电机功率
≥12.1Kw
15
Y轴电机功率
≥12.1Kw
16
Z轴电机功率
≥8.7Kw
17
主轴功率(连续/S6-60%)
≥30/37Kw
18
主轴转速
覆盖10~4000r/min
19
主轴扭矩
≥1570N.m
20
滑枕横截面尺寸
≥450×450mm
21
机床的位置检测精度检验标准:
VDI/DGQ3441
22
定位精度
X轴:
0.03mm/全长
Y轴:
0.02mm/全长
Z轴:
0.015mm/全长
23
重复定位精度
X、Y、Z轴:
0.01mm
24
数控系统
FANUC0iMC
25
系统最小分辩率:
0.001mm,0.001°
4、机床结构要求:
4.1机械部分的要求
4.1.1本设备的床身、立柱、横梁、工作台采用优质铸铁件并经过时效处理消除应力,具有良好的刚度,且精度稳定,经久耐用。
4.1.2工作台采用进口重载滚柱直线导轨,必须有良好的承载性能和动态性能,X轴驱动采用交流伺服电机通过减速箱(德国ALPHA公司的高精密大扭矩的伺服进给专用行星减速机)带动滚珠丝杆旋转,实现X轴直线运动。
Y轴导轨副采用直线滚动(滚柱)导轨,Z轴导轨为滑动导轨,即铸铁---贴塑摩擦副,有良好的吸震性,耐磨且保证切削的稳定性。
4.1.3Y轴驱动采用交流伺服电机通过同步带降速后带动滚珠丝杆旋转,实现溜板横向运动,Y轴必须有良好的减震性能,确保切削的稳定性。
4.1.4Z轴驱动采用交流伺服电机通过减速箱带动滚珠丝杆旋转,实现滑枕铣头垂直运动,Z轴必须有良好的减震性能,确保切削的稳定性。
4.1.5本设备的三轴反馈全部采用HEIDENHAIN精密光栅尺,实现全闭环位置反馈。
三轴均采用接近开关方式回零。
当全闭环光栅尺发生故障时能迅速通过改变参数的方式变为半闭环,机床在半闭环状态下继续工作。
分辨率为0.001mm。
4.1.6本设备的床身导轨和横梁导轨采用不锈钢伸缩式防护罩防护,并采用迷宫式防尘。
4.1.7滚珠丝杠、轴承、夹紧器、滚动导轨块等关键部件必须进口著名品牌。
4.1.8本设备所有运动的零部件必须有完善的集中润滑系统,可实现定时、定量全自动和手动润滑,并可进行检测与报警。
4.1.9液压系统的主要零部件(如液压泵、电磁阀、减压阀、压力继电器等)必须使用日本油研产品,液压系统必须有自动循环冷却装置,液压系统必须设计油面液位报警、油温报警、回流堵塞报警、最低工作压力报警等安全监控装置。
液压系统采用空气冷却系统,以保证机床的正常运动及降低温升。
4.1.10工作台两边都必须安装链式排屑装置,且安装位置合理,不影响操作,排屑装置要能够方便排屑。
4.1.11机床周围配备可移动式防护罩,既保证工件装夹、校正、加工方便,又防止铁屑飞出。
4.1.12本设备要有自动冷却和防止冷却液飞溅装置,要有冷却液回收循环使用装置。
4.1.13主轴可无级调速,两档机械变速,通过液压自动换挡,提高主轴的转速围。
变速箱要用循环油进行润滑和冷却,避免主轴热变形。
主轴要有自动拉刀装置。
根据加工要求,配备直角铣头壹件。
主轴头要使用液压缸平衡装置平衡。
主轴可自动定向,且定向位置准确可靠。
4.1.14主轴端部径向跳动不大于0.003mm,轴向跳动不大于0.003mm。
4.1.15主轴安装自动松夹刀机构,便于换刀。
4.1.16机床噪音小于80dB。
4.1.17设备配备直角铣头(直角头两个方向有自动补偿功能)
许用功率20KW
转速围10-1500r/min
主轴锥度ISONO.50
4.1.18横梁上有防护栏,立柱上有扶梯,便于机床维修,安全可靠。
4.1.19液压和气动
液压系统应符合JB/T10051等的有关液压标准,气动装置应符合GB/T6576等的有关气动标准。
本机床的液压系统主要由液压油箱、液压泵组及液压阀、液压附件等组成。
高压泵组主要提供刀具夹紧、松开,及滑枕和平衡缸用。
本机床的压缩空气主要用于X、Y、Z向光栅尺吹气、刀具刀柄的清洁吹气。
用户提供0.4-0.6MPa压力的1100L/min的压缩干空气。
4.1.20冷却系统
冷却系统是为工件的外冷而安排的。
冷却系统由水箱、泵、电机、过滤器、及向主轴头提供外冷所必须的管线、阀、及相关的硬件组成。
水箱是一个单独的水箱,放置在机床床座的一端。
电机及泵的组合固定在水箱的上部,从水箱向外抽水。
主轴头的冷或外冷通过高、低压水泵来选择。
这种选择可以通过手动或程序自动的方式来完成。
此外,水箱上还设有水位开关2FS,当水位过低时,数控系统报警,提醒操作人员及时加入冷却液。
此外,机床还配有一个潜水排污泵。
当放置水箱的水坑,水的高度超出规定要求时,潜水泵自动工作,将水抽入水箱。
4.1.21本设备有RENISHAW机械式自动对刀装置TS27R,能够实现自动对刀及自动刀具补偿功能。
4.1.21用刀柄装在主轴上的光电式寻边装置,实现工件的正确装夹。
4.2电器部分的要求
4.2.1FANUC0iMC数控系统标准功能
标准的机床配置FANUC0iMC数控系统
配置10.4”彩色液晶显示器.
主要特性
标准坐标管理性能
▪控制轴数:
X,Y,Z轴
▪联动轴数:
X,Y,Z轴
▪自动加减速
▪间隙补偿
▪轴误差补偿
▪速度进给控制
▪快速加工模式---增强加减速降低非切削时间的快速移动
▪切削进给锁定
▪AICC控制
▪----优化联动速度和精度
▪----速度进给前馈
▪----线性加减速
操作者特性
▪256MB数据卡
▪以太网卡
▪存储程序:
400
▪零件程序存储:
256KB
▪PCMCIA程序卡接口
▪RS232C接口
▪DNC数据传输
▪背景编辑
▪扩展的零件程序编辑
▪1)转换---X地址能被转换到Y地址
▪2)程序拷贝
▪3)程序移动
▪4)程序合并
▪5)序列号自动嵌入
▪序列号搜索
▪单程序段执行
▪空运转
▪M,S,T功能锁定
▪程序保护
▪轴和刀具较验
▪单键控制功能
▪----紧邻刀安装按扭
▪----卸刀按钮
▪绝对,相对和机床坐标系显示
▪增强刀具寿命管理
▪公英制转换
▪轴单步手轮控制
▪主轴速度修调50-120%
▪进给修调0-120%
▪快速移动修调0-100%
▪记事本
▪程序开始
▪运转时间和零件计数显示
▪快速攻丝
维护和诊断支持功能
▪帮助功能
▪报警和操作信息显示
▪自诊断功能
▪控制和编码器报警
▪诊断功能:
▪PMC梯形图显示
▪轴和主轴功率显示(负载显示)
▪PMC信号状态和跟踪功能
▪报警历史纪录
▪操作历史纪录显示
▪维修显示
G代码
下述G代码被支持
▪G00
▪定位(快速移动)
▪G01
▪直线插补(切削进给)
▪G02
▪圆弧插补/螺旋线插补(顺时针)
▪G03
▪圆弧插补/螺旋线插补(逆时针)
▪G04
▪暂停
▪G07.1
▪圆柱插补
▪G09
▪准确停
▪G10
▪数据设定
▪G11
▪数据设定模式取消
▪G17
▪XY平面选择
▪G18
▪ZX平面选择
▪G19
▪YZ平面选择
▪G20
▪英寸输入
▪G21
▪毫米输入
▪G27
▪参考点返回检测
▪G28
▪返回参考点
▪G29
▪从参考点返回
▪G30
▪第二参考点返回
▪G31
▪跳跃功能
▪G40
▪刀具补偿取消
▪G41
▪刀具左偏补偿
▪G42
▪刀具右偏补偿
▪G43
▪刀长正补偿
▪G44
▪刀长负补偿
▪G49
▪刀长补偿取消
▪G50
▪比例取消
▪G51
▪比例
▪G52
▪坐标系统设定
▪G50.1
▪程序镜像取消
▪G51.1
▪程序镜像
▪G53
▪机床坐标系统命令
▪G54
▪工件坐标系1选择
▪G55
▪工件坐标系2选择
▪G56
▪工件坐标系3选择
▪G57
▪工件坐标系4选择
▪G58
▪工件坐标系5选择
▪G59
▪工件坐标系6选择
▪G61
▪精确停模式
▪G62
▪自动拐角修调
▪G63
▪攻丝模式
▪G64
▪切削模式
▪G65
▪宏程序访问
▪G66
▪宏程序方式访问
▪G67
▪宏程序访问方式取消
▪G68
▪坐标系旋转
▪G69
▪坐标系旋转取消
▪G73
▪钻削循环
▪G74
▪反攻循环
▪G76
▪微镗
▪G80
▪固定循环取消
▪G82
▪钻削循环.反镗
▪G83
▪钻削循环
▪G84
▪攻丝循环
▪G85
▪镗孔循环
▪G86
▪镗孔循环
▪G87
▪背镗循环
▪G88
▪镗孔循环
▪G89
▪镗孔循环
▪G90
▪绝对命令
▪G91
▪增量命令
▪G92
▪绝对零点编程
▪G92.1
▪工件坐标系设定
▪G94
▪每分钟进给
▪G95
▪每转进给
▪G98
▪在固定循环中返回初始点
▪G99
▪在固定循环中返回参考点
M代码
下述M代码被系统支持
▪
▪
▪M00
▪程序停
▪M01
▪选择程序停
▪M02
▪程序结束
▪M03
▪主轴顺时针启动
▪M04
▪主轴逆时针启动
▪M05
▪主轴停
▪M06
▪换刀
▪M08
▪冷却开
▪M09
▪冷却关
▪M10
▪第四轴卡紧
▪M11
▪第四轴松开
▪M13
▪主轴顺时针启动,冷却开
▪M14
▪主轴逆时针启动,冷却开
▪M19
▪主轴定向停
▪M28
▪刀具探测头被启用
▪M30
▪结束程序,返回参考点
▪M33
▪带冷主轴顺时针启动
▪M34
▪带冷主轴逆时针启动
▪M38
▪通过主轴冷启动
▪M46
▪进给修调使能关(100%)
▪M47
▪进给修调使能
▪M48
▪主轴转速修调使能关(100%)
▪M49
▪主轴转速修调使能
▪M70
▪额外M代码
▪M71
▪额外M代码
▪M98
▪子程序访问
▪M99
▪子程序结束
▪M198
▪从外部调用子程序
4.2.2各伺服驱动轴要采用日本FANUC0iMC全数字交流伺服驱动电机。
4.2.3本设备具有完善的诊断功能(监视、显示、报警、功能检查、故障检测、紧急自动停车、隔离故障),每个报警应包括报警号、报警容及报警点。
4.2.4本设备电控柜要有电柜空调,电控柜采用密封技术确保灰尘不能进入,电缆采用日本FANUC系列产品。
外部控制电缆须采用国著名品牌。
4.2.5本设备具有二维图形显示功能。
4.2.6本设备PLC输入输出板带灯显示。
4.2.7标准电气设备
机床有集成控制,高可靠性的电控柜。
机床电器柜和操作台采用施耐德产品,全密封,全空调。
电气控制元件采用施耐德产品,检测元件采用TURKE产品,数控柜上配有一个220V交流三孔电源插座,有断电、漏电保护功能,主电源配置隔离变压器、滤波器等保护装置。
所有的电机、控制元气件和它们的安装符合金属切削机床的电气标准。
在主电源进入电源控制板时,安装一个电路断路器型断开开关。
4.3安装环境
标准的机床配置120KVA
电源:
三相交流电、380V(±10%)、单相220V(±10%)、50HZ、
空气压力:
0.4-0.6Mpa。
4.4标准要求
设备应符合中华人民全标准及环保标准。
设备按以下标准制造和验收并提供该标准的复印件。
JB/6086-1992《数控龙门镗铣床精度》
JB/T6600-93《数控龙门镗铣床技术条件》
GB/T9061-1988《金属切削机床通用技术条件》
GB5226.1-1996《机床电气设备通用技术条件》
GB15670-1995《金属切削机床安全防护通用技术条件》
JB/T10051-1999《金属切削机床液压系统通用技术条件》
附件1供货围
1
主机:
UB-20/40(配FANUC0iMC控制系统)
包括:
30/37kW;0~4,000rpm主轴;
10.4英寸彩色液晶屏显示器;
1
制造厂培训、预验收及试切削
1
用户工厂安装、调试、验收及培训
1
周围半罩防护
1
自动排屑器及容屑小车
1
三轴HEIDENHAIN光栅尺全闭环系统
1
一个进口的附件头(90°直角头),半自动交换(自动定位,人工拧螺栓拉紧)
1
电器柜空调系统
1
工作区域照明装置
1
分离式冷却系统
1
手持冷却液喷枪
1
手持冷清洁气枪
1
分离式液压单元
1
润滑系统
1
主轴端部清洁装置
1
光栅清洁吹气
1
手持脉冲发生器
1
RENISHAW机械式自动对刀装置TS27R
1
用刀柄装在主轴上的光电式寻边装置
附件2:
技术文件
1检测记录或报告,均要有辛辛那提的质检人员签字。
提供设备质量标准和检验方法。
2供设备的有效合格证书以及设备所配备的测量仪器、仪表合格证。
3合同签订后2个月卖方应提供设备安装所必须的技术文件一份。
具体容包括设备安装基础图、动力线路布置图以及与此相关的电子文档等。
4主要零部件、元器件的检验由卖方进行并出具合格证。
5提供进口件清单及相关的进口件进关证明(尤其是辛辛那提原装进口主轴进关证明)。
6出示本设备的强度计算报告,提供设备的全套安装、调试、使用、维修所必须的技术资料各三套。
包括以下容:
·设备及主要维修部分构件的装配图,功率扭矩—转速图,刀柄图等
·维修机械零件图,液压、润滑系统的原理图和技术文件以及维修技术手册
·设备电气原理图、接线图(包括主要元件的型号、参数)
·伺服驱动装置电气原理图及维修保养技术手册
·数控系统的程编手册/操作手册
·PLC编程、维修资料及PLC程序清单
·数控系统中PLC编程软件(光盘)。
·提供PLC程序、PLC参数、PLC符号表、PLC程序说明书、MMC及NC参数的电子档一份备份。
·数控系统资料(英文、中文或中英文)全套。
·设备机械、电器、液压元件等备件手册。
·提供自制易损件零件图。
·系统软件及系统连接手册
·设备参数手册说明。
·设备故障诊断手册。
·电气控制手册。
·驱动(含主轴和坐标)维修手册
·系统参数手册
·驱动(含主轴和坐标)参数手册
·接口手册及传输软件
·PLC编程手册及PLC梯形图
·报警信息文本、接口文本及传输软件
·机床系统参数光盘
·提供上述备份光盘资料一套
这其中一套应在合同签订后4个月提供。
文件必须字迹清楚,容完整,使用参考必须尽可能全面,用户部应有权无偿复制上述文件。
附件3:
监造、安装调试、验收及培训:
1监造:
制造厂家在机床开始生产之后,须将生产计划发送至买方,买方根据需要可派2~3名技术人员到生产厂家生产现场进行设备制造过程监造,监造期间由卖方免费提供当地食宿和交通。
按应标时的要求,出示部分辛辛那提的设计图纸,及在该设备中图纸的更改处要有辛辛那提设计者签名。
2预验收前培训要求:
制造厂家在机床所有部件生产完毕进入装配之前邀请买方派5~6名技术、专业维修人员到生产厂家生产现场参加设备的机械,电器系统的安装调试的学习(免培训费用,同时提供免费市交通及工作午餐)。
对设备的关键尺寸,装配精度,液压系统设计及原理,整机的操作和维修等制作详细的培训计划,为用户以后的使用,维护保养提供技术保障,培训时间为三周以上,培训合格后,制造商发给相应人员培训合格证书。
同时用户有义务对卖方的技术。
制造厂家应在培训前15天做出详细的培训计划,培训容至少包括如下几方面:
⑴设备设计思路;
⑵设备的结构及工作原理;
⑶设备的使用和操作;
⑷设备的机械和电气维修;
⑸设备的保养;
⑹安全生产注意事项;
⑺设备的常见故障及处理方法;
⑻FANUC0iMC控制系统;
⑼数控编程;
⑽PLC编程等。
3预验收:
预验收在机床制造厂家进行,调试完毕,进行预验收。
预验收包括以下容:
按国际标准或制造厂标准对机床各项精度进行检测(检测几何精度、定位精度、动态精度、确认机床功能);
标准试件加工;
满负荷实验;
卖方提供预验收的所有数据资料。
预验收试切中刀具、材料及检测工具由卖方提供。
预验收达到相应要求,并满足合同相关条款后,由用户和卖方共同签署预验收报告,机床才能发运。
4设备到货后,制造厂家须在买方通知的日期派有经验的机械、电气、操作人员到用户工厂负责整台设备的安装、调试。
确保设备进入正常工作状态以及买方工程技术人员、设备操作人员和维修人员掌握设备操作、维护,使之达到独立操作、维修水平。
5用户工厂进行培训:
用户工厂培训分为三部分,第一部分是专门针对操作人员、工艺技术人员的培训,培训容为设备操作、维护及保养,培训从设备调试阶段开始,培训时间不少于一周,培训合格后,培训合格后由制造商发给相应人员培训合格证书;第二部分为针对设备维修人员的培训,培训人员主要为参加过预验收阶段的培训人员,培训容除包括设备安装调试外,还需针对设备安装及在预验收培训阶段不够完善的部分进行再次针对性培训,培训时间不少于三天;第三部分是现场培训,对操作者、工程技术人员及维修人员进行现场操作及维护培训,使之达到独立操作、维修水平,确保设备进入正常工作状态。
在培训前,制造商应编制一个详细的培训方案。
6在设备安装、调试完成后,在用户车间现场对设备按双方认可的验收文件(验收技术文件附在合同中)进行最终验收,容包括:
设备精度检查(按制造厂商的《出厂验收报告》,对设备进行定位精度检测、重复定位精度检测,检测由制造厂商负责,用户现场监督。
使用激光干涉仪进行检测);
设备功能检查;
NAS试件切削(卖方提供试切刀具、材料);
强力切削(参数和刀具由机床厂家提供);
产品加工(工件尺寸和工艺要求由用户提供,满足用户工艺要求)。
如达不到要求,须延长调试时间。
如加试后,仍达不到要求则买方有权退货。
终验收合格后,卖方和用户签署最终验收合格报告。
XK2120×40数控铣终验收单
1、设备精度检查(按制造厂商的《出厂验收报告》,对设备进行定位精度检测、重复定位精度检测,检测由制造厂商负责,用户现场监督。
使用激光干涉仪进行检测)结论:
2、设备功能检查(按技术协议检查)结论:
3、强力切削(参数和刀具由机床厂家提供)
结论:
4、产品加工(工件尺寸和工艺要求由用户提供,满足用户工艺要求)
结论:
5、NAS试件切削(卖方提供试切刀具、材料)
检验项目
简图
检验方法
检验
工具
精度mm
允差
实测
中心孔
a)圆柱度
试件:
JB/T8771.7-A320
材料:
LY12
刀具:
ф50
2齿套式立铣刀
切削参数:
转速4000RPM,
进給635mm/min,切深0.25mm
三坐标测量机
圆度仪
0.015
b)孔中心轴线与基面A的垂直度
φ0.015
正四边形
c)侧面的直线度
0.015
d)相邻面与基面B的垂直度
0.02
e)相邻面与基面B的平行度
0.02
菱形
f)侧面的直线度
0.015
g)侧面对基面B的倾斜度
0.02
圆
h)圆度
0.02
i)外圆和圆孔C的同心度
φ0.025
斜面
j)面的直线度
0.015
k)3゜角斜面对B面的倾斜度
0.02
镗孔
n)孔相对于孔C的位置度
φ0.05
s)孔与外孔D的同心度
φ0.02
结论
附件4:
质量保证及售后服务:
1该设备在正常情况下质保期为12个月,数控系统的质保期为24个月,主轴的质保期为3年,从最终验收签字之日起计算。
质保期如有零件损坏(除用户使用不当),自更换该零件起,再对该零件重新计算质保期。
在保质期,卖方无偿提供设备维护和更换零部件,接到用户通知后,一星期必须保证设备恢复正常运行。
2质保期售后服务由卖方免费负责。
卖方自接到服务通知(传真或信函)始8小时给买方作出响应;对用户不