EMI防护.docx
《EMI防护.docx》由会员分享,可在线阅读,更多相关《EMI防护.docx(22页珍藏版)》请在冰豆网上搜索。
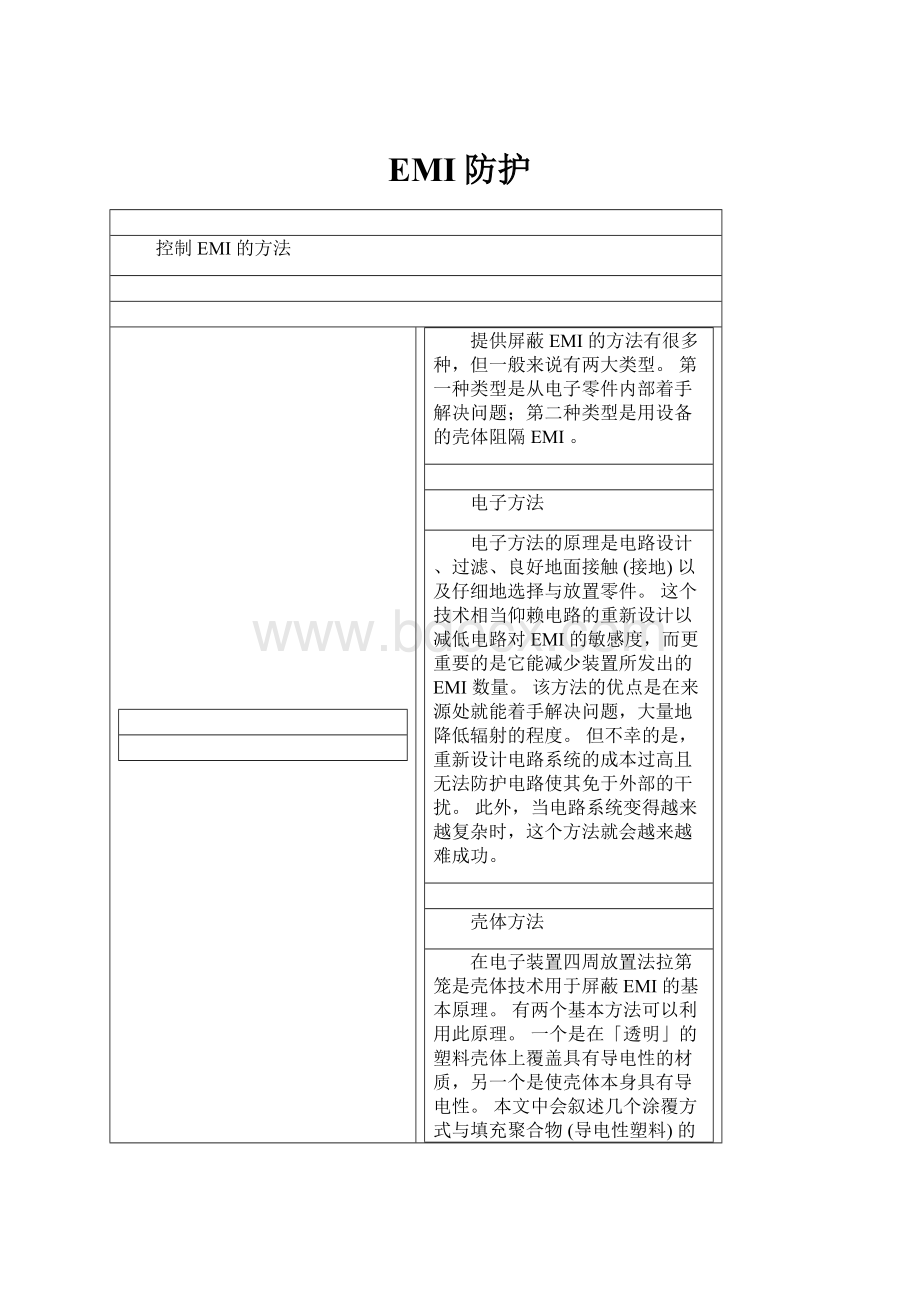
EMI防护
控制EMI的方法
提供屏蔽EMI的方法有很多种,但一般来说有两大类型。
第一种类型是从电子零件内部着手解决问题;第二种类型是用设备的壳体阻隔EMI。
电子方法
电子方法的原理是电路设计、过滤、良好地面接触(接地)以及仔细地选择与放置零件。
这个技术相当仰赖电路的重新设计以减低电路对EMI的敏感度,而更重要的是它能减少装置所发出的EMI数量。
该方法的优点是在来源处就能着手解决问题,大量地降低辐射的程度。
但不幸的是,重新设计电路系统的成本过高且无法防护电路使其免于外部的干扰。
此外,当电路系统变得越来越复杂时,这个方法就会越来越难成功。
壳体方法
在电子装置四周放置法拉第笼是壳体技术用于屏蔽EMI的基本原理。
有两个基本方法可以利用此原理。
一个是在「透明」的塑料壳体上覆盖具有导电性的材质,另一个是使壳体本身具有导电性。
本文中会叙述几个涂覆方式与填充聚合物(导电性塑料)的使用。
第三种选择是透过共同注射塑模来结合这两种方式。
在叙述各种涂层、导电性与共同注射塑模屏蔽技术前,必须先介绍另一种观念。
绝大多数用于屏蔽的壳体方法都是应用在整个装置的外部机壳。
然而,您也可应用该方法使其成为内部屏蔽机制。
在这种情况下,会使用微型导电箱(通常是金属)来隔离所有最容易感应的电子组件。
而结果就是在完工装置中创造出一个微型的法拉第笼。
对作为屏蔽技术的微型导电箱而言,其最主要的缺点就是无法保护装置的其它部分不受外部来源的EMI影响。
覆盖金属
金属提供其与生俱来的绝佳屏蔽特性,幷且因使用简单、无机能性零件而具备有成本效益。
塑料提供统合特色与杰出美学等增强的设计灵活性。
但是塑料需要二次加工或是导电纤维来达成屏蔽特性。
因此解决这个屏蔽问题的方法之一就是为塑料壳体装上金属外衣。
由于子母箱技术是材料的非机能性应用,所以可能不合乎经济效益。
使用塑料所获得的容易组装优点将会因为金属外衣的使用而折损。
因为金属衬里必须依附在塑料壳体上,这会造成组装过程的复杂化与延长时间。
涂层方式
塑料零件上的涂层方式是目前最普遍及最多样化的屏蔽技术。
基本上,这些方式全都牵涉到在完工的塑料壳体上覆盖上一层导电材质,这是为了在设备周围产生法拉第笼以形成EMI屏蔽效果。
与塑料壳体最常合用的涂层技术已完整建立。
大部分涂层最早都是发展用于金属上以作为装饰性或保护性涂层。
接下来的这些技术会在下面叙述:
导电涂漆
无电镀膜
电镀
真空金属喷敷技术
施加金属箔
电弧喷锌
导电涂漆。
导电涂漆目前被广泛地用为EMI屏蔽。
跟其它的屏蔽方法比较起来,它们使用简便且设备与原料成本较低。
这些系统是提供EMI屏蔽的简单方法,因为它们使用一般的喷漆设备。
由于这些系统灵活性很强,大多数壳体材质可以根据选用的填充剂与涂层厚度,而在喷涂后达到不同的衰减程度。
根据基材(塑料壳体)的兼容性来选择粘合剂。
导电涂漆是由悬浮在树脂载体(粘合剂)系统中的导电填充剂颗粒与颜料所构成。
导电颗粒可以是镍、铜、银或是石墨。
树脂(粘合剂)可以是聚胺基甲酸酯、聚丙烯酸酯、聚乙烯酯或是任何非导电涂漆所使用树脂化合物的合幷物。
今日使用最广泛的粘合剂是聚丙烯酸酯。
这些漆料是利用空气喷雾器与无空气喷涂设备施加到零件上。
导电涂漆系统一般都是含有大量固体且使用熔剂为基材的系统,所以使用前必须用稀释剂稀释。
厚度25微米到75微米(0.001英吋到0.003英吋)的干膜就能在大部分用途中提供合格的屏蔽效率。
喷漆主要是一种可视操作,幷且依靠溶剂来化学腐蚀一些塑料以增进涂层对基材的粘合力。
在塑料零件上施加过多的涂漆时,就会发生应力裂痕与折痕。
各个漆层间的厚涂层如果没有干透,就会产生「皱肤效应」,涂漆的上层会变硬而使溶剂陷在基材/涂漆接口。
这种陷入会在涂漆干燥期间导致溶剂凸出。
而太薄的涂层则在固化时更容易剥落。
剥落的涂漆碎片会损害电子组件。
这些问题可以藉由使用建议的涂层厚度、谨慎地制模与使用低应力塑料零件来减少。
镍基漆系统是目前最普遍的方法,它在宽广的频率范围之内提供合理的信号衰减。
它们有良好的抗氧化性以及厚度在50微米到70微米(0.002英吋到0.003英吋)之间的干膜就可以得到30dB到60dB的衰减程度。
然而镍系统所获得总导电性明显的不如银涂漆方法。
铜也显示出高抵抗力与导电性。
在薄膜厚度方面,铜底产品比镍底产品更有效。
可是,铜很容易在空气中氧化幷产生不导电的氧化层。
这个不导电层会减少铜的电气性能与减弱系统的屏蔽效能。
少数导电涂漆制造商似乎已能藉由减低这种氧化作用而发展出非氧化等级铜基漆以克服问题。
银拥有非常高的导电性,是达到高屏蔽标准所绝对必要的,但是它的成本也限制了它的应用。
银基漆层能够提供65+dB的衰减程度。
一般来说,银基漆比镍基漆贵5到20倍。
最便宜的漆层方法是石墨基的。
因为它可获得的衰减程度比起其它材质低很多,所以石墨最适合用于静电放电的保护。
供货商正努力发展水性涂漆系统,以排除溶剂系统中的挥发性有机化合物(VOC)。
目前,水性系统还不是一个广泛利用或者具成本效益的方法。
这些方法常有缺乏粘合力与水解安定性的缺点。
然而,供货商对这些方法在未来能变的有效与具备竞争力抱以乐观的态度。
无电镀膜
无电镀膜是以化学的方式在绝缘体(类似塑料,能容易地让电磁波穿透的材质)上形成连续的金属膜。
将塑料零件浸入一系列调配好的水槽,在不导电的工程数脂上化学沉积出金属。
镀镍铜(合幷的两层薄膜)是最常使用的方法,也可利用此技术来沉积金和锡。
1微米到2微米(0.00004英吋到0.00008英吋)厚的金属铜层就能达到65dB到120dB的衰减程度。
较厚的膜虽然可以提高衰减程度,但通常不需要。
此薄薄的金属层也能在配接零件间提供绝佳的电导通性。
无电镀膜与传统电镀的差别在于它不需要外部的电源来激活与控制电镀过程。
相反的,用一系列化学步骤可以让不导电基材形成一个可接受的初步附着金属层。
此初始金属层接着会扮演着催化剂的角色让过程能持续自动催化(自动地)。
用为EMI屏蔽无电镀膜过程中,包含了腐蚀、活化与电镀(图13)。
一般都是利用铬酸与硫酸水溶液来腐蚀(粗糙化)塑料零件的表面以制作镀膜表面。
腐蚀阶段是确保金属涂层是否附着在塑料基材的关键性一环。
根据使用的塑料树脂,在腐蚀前必须先以溶剂软化塑料的外表,让铬酸腐蚀能够进行。
然后将钯锡胶体(化合物)附着到已经腐蚀的表面。
接着将锡溶解掉,基材上就会生成富含钯的表面。
钯扮演催化剂的角色,促成铜镀到已催化的表面上。
此连续的铜层基本上是纯铜幷且是屏蔽的主层。
然后镍以类似的方式沉淀在铜的上方,提供防蚀的外涂层。
外层的镍对整个屏蔽效能幷无太大的贡献,但是它能防耗损、磨损与屏蔽铜层避免氧化。
无电镀膜技术
图13
在每个电解槽之间,基材应进行一连串的冲洗,以移除附着在零件上的任何额外化学物质。
冲洗对于预防镀膜生产线上其它电解槽受污染而言是相当重要。
电解挂物架应该设计成倾斜状以将溶剂从凹处与孔中排出。
针对每一个不同的零件,挂物架应个别制作以避免空气与溶剂混入。
因为无电镀膜是一种浸入的过程,所以不论任何大小或复杂性的组件都可以得到均匀的膜层。
此方式不需仰仗技工的专门技能就能提供精准的覆盖。
无电镀膜屏蔽也在配接零件间提供低阻抗(抗力),能够在没有衬垫的情况下维持绝佳的电连贯性。
在机械性质上,无电镀膜能提供金属对塑料基材的绝佳附着性、优良抗磨损性,以及在腐蚀性与温暖/湿气环境中提供耐久性。
无电镀膜化学作用与制造模制零件的塑料树脂种类有高度关连性。
加入到基材树脂基质中的不同添加剂(例如阻燃剂),可能需要修改化学作用过程以及操作条件以达到最理想的粘合力。
无电镀膜是很多聚合物材质可以使用的方法。
高量填充(例如,玻璃纤维与矿物)与「泡沫」的零件,对电镀而言是一项额外的挑战,但它们都以商业上大量生产的方式制造。
最近发展了一种类似无电镀膜的程序,能够以化学的方式一次就把金属附到塑料上。
此种新的过程能提供良好的附着幷降低塑料零件必要的腐蚀量。
这种化学结合是(没有任何的腐蚀之下)存在于基材与金属涂层间的粘合作用,反之机械性结合是由腐蚀所提供的「物理互锁作用」。
这个程序目前只适用于一种树脂;在它成为广泛利用的化学程序前,在这个领域中还需要更多的开发工作。
因为高应力模制塑料零件很可能在暴露于无电镀膜的温暖溶液时,产生应力松弛(或扭曲),所以模制时应该特别考虑到这个问题。
当塑料零件发生应力松弛时,会将更多应力加到涂层/基材的结合上,这会危及粘合作用。
由于树脂的分子形状造成无法轻易地在应力区上镀膜。
制模者应该在模塑期间,藉由在适度的填充速度下维持高度熔化与模型温度,以提供充分的流动而预防应力区的产生。
制模者应尝试利用低模塑应力来生产零件。
在生产期间,内加及外加的离型化合物也会因为干扰树脂表面与化学加工步骤而导致粘合力的消失。
多数使用的离型化合物很难在无电镀膜过程之前去除。
当树脂表面须经过无电镀膜,应该避免使用外加的离型化合物。
普通的镀层是双面的(也就是所有的表面都会被镀到)。
此种遍布的涂层能够提供「双重屏蔽」幷在外层或内层之一被刮损时,能够保证可减少狭缝天线生成的可能。
要求严格外观的零件通常会再上涂料。
涂漆的另一种功能是「遮盖」,它是在涂漆程序中使用抗摩漆料来隐藏装饰性表面的一种方法。
该抗摩涂漆会阻碍特定区域上的电镀,因为抗摩涂漆的区域是不活化的。
另一个替代法是选择性的程序,利用可喷涂的基材涂层将电镀溶液引到需要屏蔽的区域而完成单面镀膜。
金属离子只会在喷涂涂层上沉积出来,让其它的表面能使用模塑颜色。
这个方式能够排除装置外部涂料的需求,虽然它能节省化学物品的使用,但是仍是一种花费甚巨的方式。
电镀
电镀因为花费的成本远高于无电镀膜,所以通常不作为形成EMI/RFI屏蔽的方法。
因为较厚的金属层是用来得到较高的反射性,因此电镀的主要目的是装饰,例如汽车栏架。
它对军事的TEMPEST需求、雷击保护、航空工业中的不导电材质以及需要电连接性的用途而言是很重要的。
因为这些成本问题,使得这个程序仅能用在小型零件上。
电镀基本上与无电极电镀的过程相同,只除了它是利用阳极与阴极之间的电压差异将金属沉淀在塑料上(以电解的方式)。
要电镀前,塑料材料应先变成有导电性。
电镀与无电镀膜的电镀前步骤都是透过初始的铜层(也可利用镍来代替铜)来达成的。
除了在无电镀膜中使用的化学机制之外,在电镀中会沉淀出额外的金属层(图14)。
电镀能沉积出无电镀膜技术所不能沉积的金属。
这些包含了铬、铑,锌、锡铅合金、银以及其它金属与它们的合金。
沉积的金属层有时候会因为电镀的电流分布而不均匀。
电镀技术
图14
真空金属喷敷技术
一般来说,有三种真空技术可以在真空室中让金属从蒸汽中凝结而在塑料零件上沉积出薄金属膜。
直流热蒸发、电子束涂覆与阴极喷洒等程序将依据在EMI屏蔽中广泛使用的顺序来讨论。
直流热蒸发
这是目前真空技术作为EMI屏蔽方式中最常使用的。
直流热蒸发跟其它真空程序的相似之处是它藉由升华将金属蒸发幷沉淀在塑料零件上成为薄膜。
升华是一种固体不经过液体阶段直接变成气体的现象。
形成的膜厚范围大约从0.05微米到1.2微米(2微英吋到47微英吋)。
铝是最常使用的金属,但是也可以沉积银、铜、镍、铬、锡与它们的合金。
在过去,塑料的传统真空金属喷敷曾是一种装饰性的程序。
它提供装饰性的抛光,但是金属层与塑料基底幷无良好的粘合力。
为了提升较好的粘合力,在金属喷镀前会在塑料表面上加上底部涂层或是透明漆。
通常也要有外涂层已保护非常薄的金属层不至于磨损与受环境损害。
由于方法与程序的发展上已显著地改善塑料基材与金属的粘合力,所以真空金属喷敷作为屏蔽的方法在过去几年受欢迎程度有增加趋势。
一种粘合力提升技术是在金属化前使用直流的等离子体来进行「清洗」,以移除会损害金属与塑料直接「连结」的表面污染(一般的离型剂、加工助剂或技工的指纹)。
在真空室抽气后,会加入少数惰性气体(通常是氩)到真空室中。
在电极与真空室壁之间(以及所有其它的接地源)会加上电位差而造成在气体气氛中建立等离子场。
正电荷气体离子会被阴极高速吸引,透过连续不断的撞击作用而「清洗」塑料表面。
此「活化的」表面能够让塑料与金属涂层之间有较好的粘合力,而排除掉平常使用塑料时所需要的底部涂层。
透过在金属化之前使用直流电等离子体腐蚀塑料,如此在塑料基材与金属涂层间形成的粘合力非常强,足以通过UL746C超过100种树脂/金属涂层结合的粘合力测试。
传统的快速真空金属喷敷是将零件放入真空室中,而在真空室中装有悬挂着99+%纯铝条的钨丝。
此真空室先排气,也就是移除大部分能够与铝产生反应的气体。
低压也会降低铝的沸点。
如果必要的话,塑料零件可以接着用等离子体清洗过。
利用等离子体清洗过后,关掉惰性气体流,就是回复真空状态了。
让电流通过钨丝来发热幷将热传到铝,一直到铝沸腾变成蒸气。
铝蒸气颗粒有足够动能,能以高速移动幷让铝以化学及机械方式附着到零件上。
铝以致密的方式沉积在零件上而形成如同镜子的涂层。
相对于前面所述的传统金属薄膜沉积法而言,另一种直接热蒸发的技术已经发展到能够沉积出厚的纯铝膜。
其厚度范围从2.5微米到15微米(98微英吋到590微英吋)。
此厚膜程序利用的是以连续递增的方式将铝镀到灯丝上。
当灯丝上所有的铝都被使用后,更多的铝会自动地加到灯丝上,所以此程序才能在真空状态下不断进行。
利用此连续程序可得到更厚的铝。
增加的金属厚度会增强抗磨损力,结合上铝所形成的稳定氧化层将有助去除掉使用外涂层的需求。
利用厚膜程序,铝以圆柱状沉积出来而使涂层很像绒毛地毯。
在蒸发/沉积程序期间,会使用较低的真空(厚膜沉积时为5x10-5托到1x10-6托,传统薄膜沉积时为5x10-4托到1x10-5托)。
真空度较低则操作温度越低,这对铝沉积时的结晶生长有较好的控制。
低真空也能在金属喷镀之前移除更多塑料零件的挥发性污染物。
使用低真空的代价就是必须延长达成所需真空程度的时间。
因为真空金属喷敷程序一般会生产出相当致密的导电涂层,所以可以达到高度的衰减。
屏蔽程度的范围是从60dB到120dB。
可以利用手工遮盖或是将标志整合入零件挂架来完成选择性的涂层。
也可以将零件夹在夹具上来遮盖住无屏蔽区域。
这是一种精确的遮盖技术,且只有一次花费的操作法,因为该夹具能重复利用。
真空金属喷敷有一项独特的优点,就是它是在封闭的系统内进行。
因此只需处理极少的金属/化学物的废料。
因为环境的限制越来越严厉,使得这项优点变的越来越有意义。
但是,自从真空金属喷敷成为「视线」加工后,就限制了零件的复杂性。
通常会转动零件来帮助金属膜的完整覆盖。
限制此技术的另一个因素是真空室的大小。
目前已经发展出最大直径为六公尺的真空室,它克服了一些有关批量制法的操作问题。
举例来说,目前其主要的应用在于个人计算机的尺寸单位。
用于EMI屏蔽的真空金属化,通常不被认为是「标准化」程序,因为设备所花费的成本高且要求有专门经验。
其结果是限制了供货商的数量。
真空金属喷镀技术–直接热蒸发
图15
电子束涂覆
电子束涂覆(以及阴极喷溅)与直接热蒸发间的差异是金属蒸发的来源。
在直接热蒸发真空程序中,金属会从热的钨丝中蒸发。
电子束涂覆与阴极喷溅的相似之处是,它们都将电子束导入真空室中,以作为蒸发沉积在塑料基材上之金属的热能来源。
欲蒸发的金属是以小型铸块的形式出现,基本上是无特定形状的金属「块」。
金属放置在位于真空室底部的耐热坩埚中。
用真空室上方集中的电子束来撞击坩埚中的金属,幷将它加热直到它蒸发成金属蒸汽云。
金属以类似热蒸发的程序沉积到塑料基材。
电子束方法有最高的蒸发率幷且通常不需要如进行直接热蒸发真空程序时一样低的真空压力(10-3拖到10-7拖)。
跟直接热蒸发真空程序比较起来,此程序的主要缺点一般都是小真空室所造成的高成本。
尽管如此,一些在商业与军事上电子束涂覆应用中对于沉积金属的要求,电子束方法幷不是直接热蒸发能相比的。
这个技术在未来的几年间,可能因为电子束涂覆成本更能与直接热蒸发真空金属喷敷相比,以及其在特殊应用上有更宽广范围的金属选择,而明显地成长。
阴极喷溅
阴极喷溅是各种真空金属化程序中最复杂的一种。
虽然它能够提供有效的EMI防御,但是我们通常不会将阴极喷溅看做是一种电子附件的屏蔽方式,因为这关系到它的成本通常比那些加热方法高出三到四倍之多。
欲喷溅的金属(也就是蒸发)会附着在阴极上,称为「靶」。
欲涂覆的塑料零件是在阳极上,阳极是电极以及塑料零件遮盖物的支架。
撞击在靶上的电子束会使金属正离子以集中的束状喷出(与蒸汽云团相反)幷冷凝在塑料基材上而形成金属膜。
这项技术首先是发展用来沈积高熔点的金属,但实际上任何金属都可以利用此方式沉积。
此过程可以在沉积开始的同时,不使用或使用惰性气体,通常是氩。
惰性气体会防止金属离子与真空室中任何残留的氧气形成不想要的氧化物。
阴极喷溅是积体芯片与磁性硬盘材料制造时的标准屏蔽技术。
阴极喷溅和其它真空金属喷镀程序相比的主要优点是金属与基材间的增强粘合力。
因为蒸发的颗粒会使用高达十到一百倍于传统真空技术的能量撞击塑料零件,所以有增强的粘合力与涂层密度。
另外,它也能够将金属靶放置在相当接近塑料基材的地方。
此程序的缺点相似于直接热蒸发与电子束涂覆技术中的缺点。
在某些情况下,它仍需要使用基底涂覆与外层涂覆。
I阴极喷溅是需要高成本与高能量的技术。
此程序的高度电流放电以及电子束涂覆作用虽可强化粘合力,但是在某些情况下也会造成高热而使塑料基材变形。
这限制了能够沉积的金属厚度。
阴极喷溅与真空蒸发金属喷敷以及电子束涂覆比较下的一个缺点就是,单位金属沈积的成本过高。
施加金属箔
使用金属箔的EMI屏蔽只需使用压敏性、背部粘胶的金属箔。
这些金属箔通常是铝、铜、黄铜、或是锡的合金。
在必要的情况下金属箔能够直接压制上去,或者直接加到注射模塑的零件上。
这个方法需要稍微的准备工作幷且不需要特殊的设备,尽管如此,在应用中仍必须仔细操作以确保覆盖的完整。
金属箔有带状、薄片状与管状等形式,都能够提供良好的屏蔽效能。
举例来说,在其中一艘阿波罗号太空舱上,其鼻锥的部分就是使用黄铜箔来屏蔽EMI。
因为此过程幷不是一种能够经济地进行大量生产的方式,金属箔屏蔽主要是用于产品上或在EMI的故障检修时使用。
切割与放置金属箔是一件费时且费力的工作。
肋柱与轮毂的出现会使制作整个屏蔽变得非常困难,甚至会覆盖住这些特性,造成大量从箔的隙缝或缺口渗漏出危险的EMI。
然而,有时候习惯将金属箔胶带当作「补缀」,接合已经利用其它方法金属喷镀的零件上的接缝。
为了产生电连贯性,必须利用此金属箔胶带的导电表面造成电接触。
最有效的屏蔽金属箔胶带是同时具有导电性粘胶,或是在金属箔背压印深达粘胶层幷能与基材接触的装饰图形。
电弧喷锌
电弧喷锌很少用来屏蔽,主要是跟环境与粘合力有关。
金属线以特殊方法进入手提式喷枪中幷且使用电弧加以熔化。
一股压缩空气会将融化的金属雾化幷喷涂颗粒到壳体上。
图16说明此过程。
电弧喷锌技术
图16
锌是最常用的金属,但是铝与铜也可用于电弧喷涂。
其涂层厚度范围从70微米到120微米(0.003英吋到0.005英吋)。
锌涂层能够在宽广的频率范围中提供良好的导电性与屏蔽效能。
衰减程度可以从45dB到90dB。
底层涂漆(系涂层)一般都会与电弧喷锌技术合用来增加金属涂层对塑料基材的粘合力。
系涂层铺上好后,就可以在其上喷涂锌了。
在系涂层的使用尚未普遍之前,通常需要使用喷砂法来准备零件表面以达到所需的粘合力。
但是喷砂会产生问题,因为很难去判断哪一区已经处理过;未喷砂部分会产生不均匀的表面,这样一来会同时降低粘合力与屏蔽效能。
而系涂层能排除这种问题。
喷涂熔化的锌会对环境造成危害。
因此,技工们必须穿戴特殊的衣服与能够供给氧气的头盔。
此过程必须在特殊的喷水隔离室中进行以回收锌雾气。
由于这整个作业过程会产生高分贝的噪音,所以必须隔离。
电弧喷涂也会比导电涂料喷涂方法慢幷且需要比导电涂料厚将近两倍半的锌涂层,才能达到相同程度的屏蔽效能。
此外,此法的资金成本很高。
视线应用也是使用电弧喷锌的潜在问题来源。
导电塑料
导电塑料能是次要屏蔽加工与EMI屏蔽金属以及ESD应用之间的替换法。
虽然不是所有应用方面都能使用本法,但是随着设计知识的发展其用途也不断的扩张,产品的经济效益也变得更加吸引人了。
一般来说,在树脂基料中加入额外的导电纤维就可以制成导电塑料。
最常见的填充物为碳纤维、包镍石墨(NCG)纤维、不锈钢纤维与铝纤维与薄片。
树脂中的纤维量根据屏蔽所要求的程度不同而通常占总数的7%到20%之间。
导电纤维能够提供良好的EMI屏蔽性能。
对塑料而言,在完工的模块零件要保持导电纤维的最高效能时,应该维持住纤维的长度。
在树脂基质中的纤维越长,纤维的重叠或是电子网状系统就会越好。
此网状系统能提供穿透该树脂的连续性导电路径。
目前已经发展出来长纤维集中粒制造法。
长导电纤维集中粒与基底树脂粒进行干燥混合以形成所想要的导电纤维集中作用。
干燥混合物能去排除一种剪切步骤与维持纤维的长度一直到模塑,结果产生了较佳的电性能。
因为所产生的聚合物基质本身就有导电性,所以不需要间接的屏蔽操作来达到屏蔽的特性。
根据纤维填充的程度,已记录的衰减程度范围从20dB到60dB。
屏蔽的连贯性是在模塑过程中,透过均匀分配在塑料基质中的导电纤维来维持。
网状的纤维系统必须达到零件的表面以达成良好的表面导电性。
高表面导电率是很重要,它能避免配接的表面之间形成狭缝天线效应。
然而在塑料加工程序中,可能产生富含树脂的表面,这会形成绝缘层以及使表面电连续性丧失。
工业上所能接受的美观表面成品往往是填充聚化物所遭遇的问题。
填充物会降低成品的品质以及经常需要装饰涂料来遮盖表面的不完整。
选择导电塑料的选择方针定义如下。
额外的导电纤维会增加材质的成本。
因此,使用导电纤维作为大型、材质密集零件的屏蔽方式将失去成本竞争性。
然而,对较小型且更复杂的零件来说,使用导电塑料作为屏蔽方式会比使用间接屏蔽操作来的更为适合。
共同注射与两次注射模制法
对之前所有已经介绍过的屏蔽方式来说,我们习惯将用注射或泡沫模塑法来制造塑料附件。
共同注射膜塑法是一种同时使用两种不同的树脂来形成塑料附件的多组件模制程序。
其中一种树脂可以是导电塑料而形成屏蔽功能。
对共同注射膜塑而言,我们称外部的组件(或是包覆物)为外壳材质。
内部的材质则称为核心材质。
可注射导电塑料成