模具moldflow设计.docx
《模具moldflow设计.docx》由会员分享,可在线阅读,更多相关《模具moldflow设计.docx(28页珍藏版)》请在冰豆网上搜索。
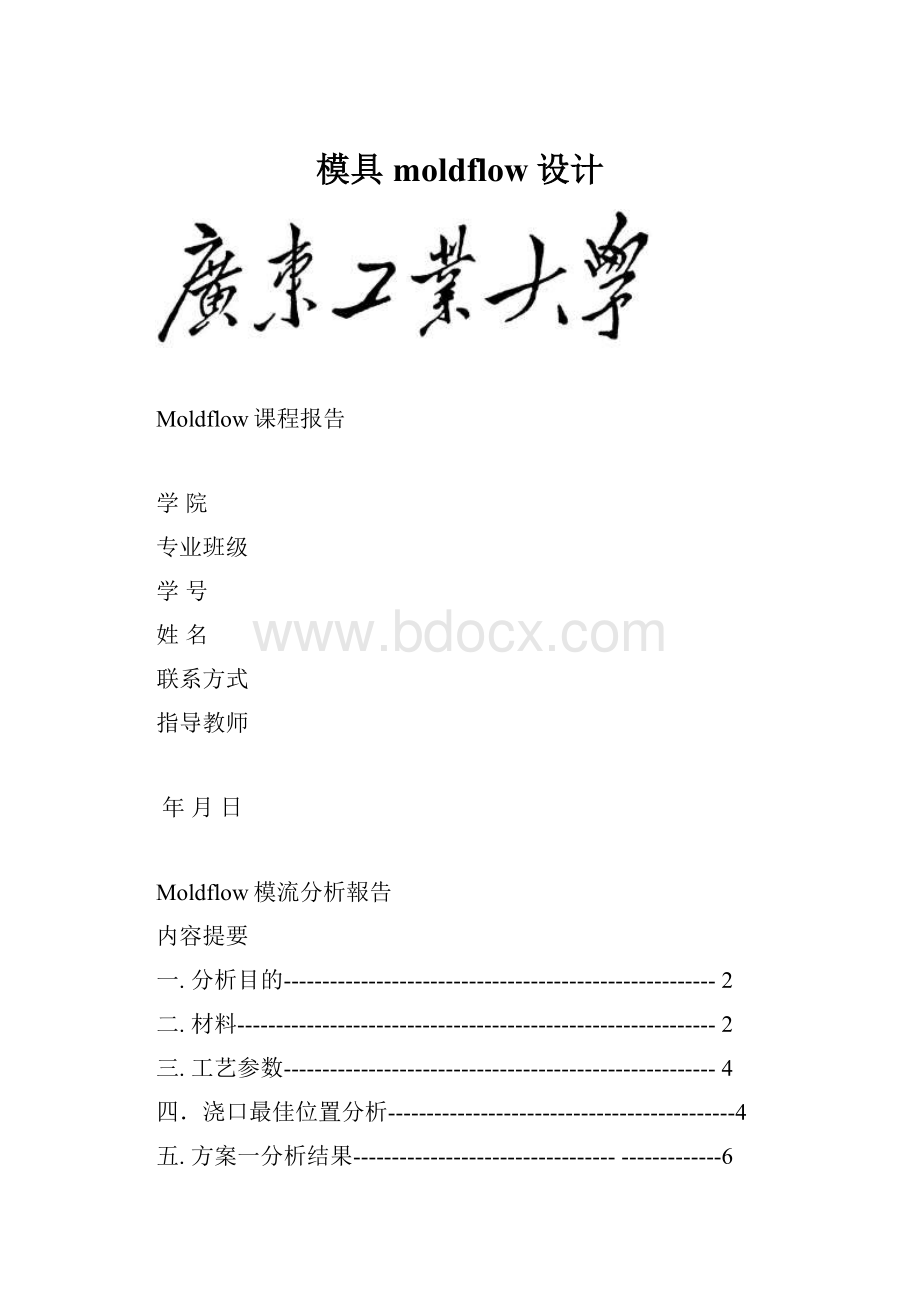
模具moldflow设计
Moldflow课程报告
学院
专业班级
学号
姓名
联系方式
指导教师
年月日
Moldflow模流分析報告
内容提要
一.分析目的--------------------------------------------------------2
二.材料--------------------------------------------------------------2
三.工艺参数--------------------------------------------------------4
四.浇口最佳位置分析---------------------------------------------4
五.方案一分析结果-----------------------------------------------6
六.方案二分析结果-----------------------------------------------16
六.总结-------------------------------------------------------------26
八.讨论-------------------------------------------------------------27
一.分析目的:
在本报告中,我们用Moldflow软件对电脑面板的各种不同的流道系统进行了分析,并做了总结。
在本次分析中,由于零件的设计已经固定,我们不能修改零件的形状,因此我们只能修改浇口的位置和流道的尺寸。
这在一定程度上限制了产品质量问题特别是熔接痕和翘曲变形方面的解决。
我们仅仅修改了浇口的类型、大小和工艺参数。
我们采用MPI的流动、保压、冷却和变形分析模块来检查塑件的质量并得到优化的流道设计。
塑件使用的材料是CHIMEIABS‘POLYLACPA707’,但在本次分析中,由于我们在Mold-flow材料库中不能找到精确的收缩数据,我们修改并建立了个人材料库。
二.材料属性
三.工艺参数
四.浇口最佳位置分析:
塑件初始模型在CAD系统中以STL格式给出。
我们用MOLDFLOW的中型面生成器生成了中型面,并修补了由于转换过程中损坏的一些面。
最佳浇口位置:
五.方案
5.01浇注系统初始设计使用两个侧浇口。
详细的尺寸、冷却水管排布如图所示.其中
5.02结果:
填充型式
填充总用时1.572s
5.03结果:
温度分布(料流前峰)
大部分温度分布在允许范围之内。
(限制:
+/-20degC)
5.04史曲线结果:
压力&锁模力力
最大注射压力约为32.78MPa而锁模力达到33.7吨.这意味着当我们使用大于40吨的注塑机时,塑件很容易填满和控
5.05结果:
体积剪切速率
体积剪切速率必须低于允许值,特别是在浇口区域。
(许用值:
500001/sec)
如果超过这个限制,材料很容易发生降解。
对于这个方案,体积剪切速率不是一个问题,。
5.06结果:
困气位置
左图显示塑件上困气的位置。
大部分困气出现在筋和边的末端,因此除了顶部,其它区域不易发生烧焦和短射现象。
为了防止困气和得到更好的熔接痕,我们必须减小顶面末端的厚度。
5.07结果:
熔接痕位置
左图显示了熔接痕的位置。
有多条熔接痕比较明显。
要移动和消除熔接痕,我们必须修改塑件的壁厚和浇口的位置。
5.08结果:
缩痕深度
5.09结果:
冷却水管冷却效果
这个结果显示了模具的冷却效果。
所设置的冷却工艺参数也较为合适。
.
5.10结果:
型腔冷却效果
这个结果显示了型腔的冷却效果。
红圈区域内温度较高,而上下的温差也较大。
这是导致热弯曲的主要原因。
因此我们必须修改冷却水管或模具的结构。
5.11结果:
9.4秒时的凝固率
5.12结果:
模具收缩
5.13结果:
deflection
X-deflection
左图显示了X方向的变形分布.
可以通过使用较高的保压压力来减少这一收缩量。
结果:
Y-deflection
左图显示了Y方向的变形分布。
红色区域表明制件顶部向内缩进0.5888mm.
其余区域变形较为均匀,所以我们仅需考虑顶部区域的翘曲
Z-deflection
红色所指区域向上翘约0.85mm.
其他区域所指表明制件向下缩进1mm
总体变形:
5.14结果:
回路热去除效率
六.方案二
6.02结果:
填充型式
填充总用时1.827s
6.03结果:
温度分布(料流前峰)
大部分温度分布在允许范围之内。
(限制:
+/-20degC)
6.04史曲线结果:
压力&锁模力力
最大注射压力约为32.78MPa而锁模力达到13.5吨.这意味着当我们使用大于20吨的注塑机时,塑件很容易填满和控
6.05结果:
体积剪切速率
体积剪切速率必须低于允许值,特别是在浇口区域。
(许用值:
500001/sec)
如果超过这个限制,材料很容易发生降解。
对于这个方案,体积剪切速率不是一个问题,。
6.06结果:
困气位置
左图显示塑件上困气的位置。
大部分困气出现在筋和边的末端,因此除了顶部,其它区域不易发生烧焦和短射现象。
为了防止困气和得到更好的熔接痕,我们必须减小顶面末端的厚度。
6.07结果:
熔接痕位置
左图显示了熔接痕的位置。
有多条熔接痕比较明显。
要移动和消除熔接痕,我们必须修改塑件的壁厚和浇口的位置。
6.08结果:
缩痕深度
6.09结果:
冷却水管冷却效果
这个结果显示了模具的冷却效果。
所设置的冷却工艺参数也较为合适。
.
6.10结果:
型腔冷却效果
这个结果显示了型腔的冷却效果。
红圈区域内温度较高,而上下的温差也较大。
这是导致热弯曲的主要原因。
因此我们必须修改冷却水管或模具的结构。
6.11结果:
18.43秒时的凝固率
6.13结果:
deflection
X-deflection
左图显示了X方向的变形分布.
可以通过使用较高的保压压力来减少这一收缩量。
结果:
Y-deflection
左图显示了Y方向的变形分布。
红色区域表明制件顶部向外缩进0.02mm.
其余区域变形较为均匀,所以我们仅需考虑顶部区域的翘曲
Z-deflection
红色所指区域向上翘约0.85mm.
其他区域所指表明制件向下缩进1mm
总体变形:
6.14结果:
回路热去除效率
六.分析
2.锁模力比较
锁模力方案一方案二
33.7T13.5T
生产周期方案一方案二
35秒50秒
1.不推荐使用热流道。
原因是模具成本上升,填充依然不均匀。
5.变形量在设计精度范围内。
6.通过修改浇注系统和冷却系统,可缩短生产周期(50-35)=15秒。
1.本报告显示了各方案之间的区别
2.在方案中制件顶部极容易发生困气。
通过控制注塑速率和改变壁厚变化,避免了困气
3.通常制件厚度方向80%凝固,流道60%凝固,我们可以开模。
所以在方案一中25秒时,而方案二在35秒可以开模,这样我们可以节省注塑周期40%.
4.在方案一,熔接痕比较明显,我们应修改制件厚度变化。
5.方案的翘曲形状和翘曲量很相似。
如果超过了公差要求,我们必须修改厚度或在制件的侧壁增加加强筋。
6.在二方案中制件顶部极容易发生困气。
我们通过控制注塑速率和改变壁厚变化,避免了困气
7.如果使用两方案中的浇口尺寸,不容易发生塑料降解。
温度降低并分布均匀
七.结论:
采用方案二:
原因如下:
所用设备吨位小,熔接痕小但周期长
采用方案一:
周期短,但设备吨位大,熔接痕多