11工业管道安装工艺守则.docx
《11工业管道安装工艺守则.docx》由会员分享,可在线阅读,更多相关《11工业管道安装工艺守则.docx(18页珍藏版)》请在冰豆网上搜索。
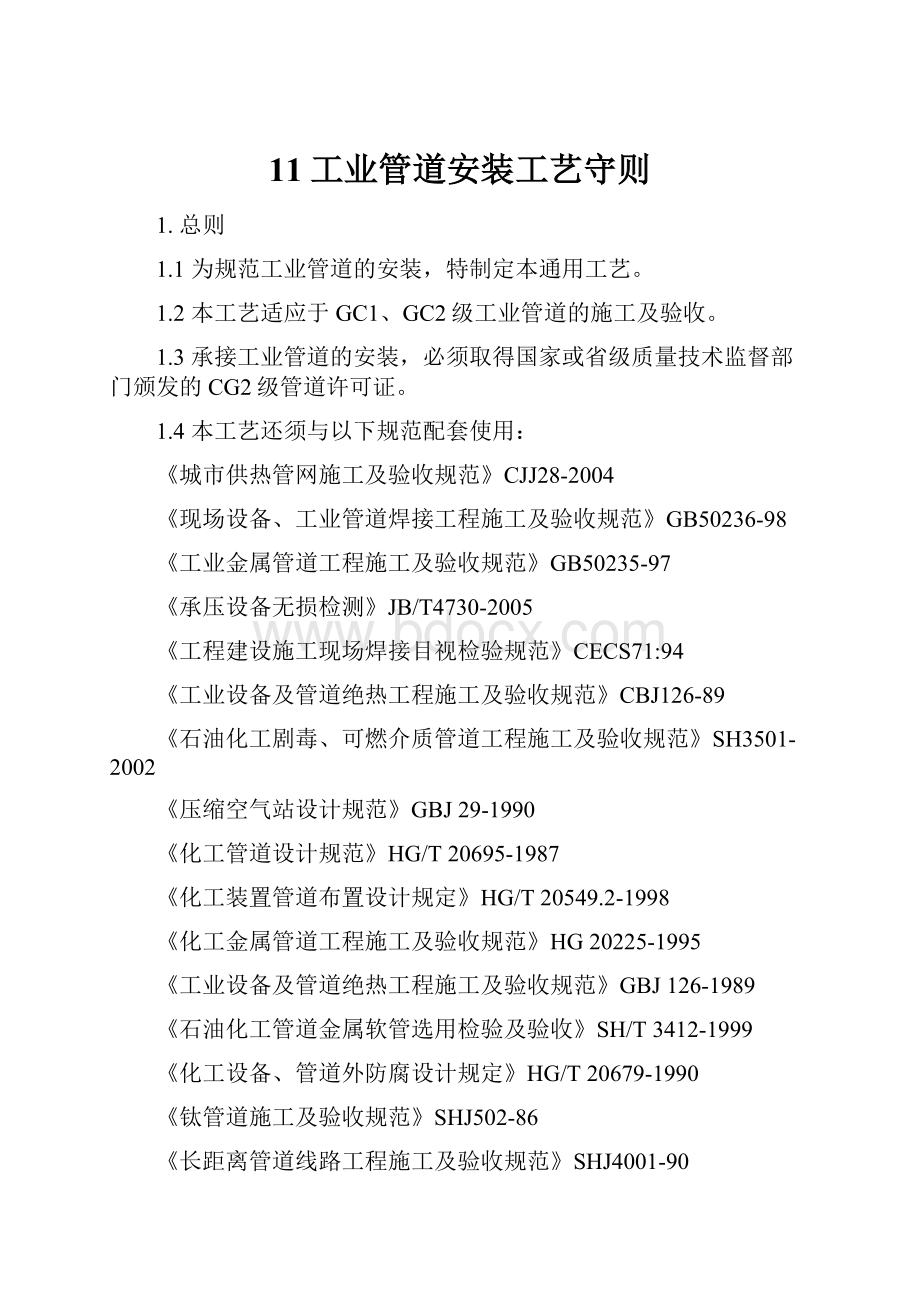
11工业管道安装工艺守则
1.总则
1.1为规范工业管道的安装,特制定本通用工艺。
1.2本工艺适应于GC1、GC2级工业管道的施工及验收。
1.3承接工业管道的安装,必须取得国家或省级质量技术监督部门颁发的CG2级管道许可证。
1.4本工艺还须与以下规范配套使用:
《城市供热管网施工及验收规范》CJJ28-2004
《现场设备、工业管道焊接工程施工及验收规范》GB50236-98
《工业金属管道工程施工及验收规范》GB50235-97
《承压设备无损检测》JB/T4730-2005
《工程建设施工现场焊接目视检验规范》CECS71:
94
《工业设备及管道绝热工程施工及验收规范》CBJ126-89
《石油化工剧毒、可燃介质管道工程施工及验收规范》SH3501-2002
《压缩空气站设计规范》GBJ29-1990
《化工管道设计规范》HG/T20695-1987
《化工装置管道布置设计规定》HG/T20549.2-1998
《化工金属管道工程施工及验收规范》HG20225-1995
《工业设备及管道绝热工程施工及验收规范》GBJ126-1989
《石油化工管道金属软管选用检验及验收》SH/T3412-1999
《化工设备、管道外防腐设计规定》HG/T20679-1990
《钛管道施工及验收规范》SHJ502-86
《长距离管道线路工程施工及验收规范》SHJ4001-90
《长输管道站内工艺管线工程施工及验收规范》SYJ4002-90
《压力钢管制造安装及验收规范》DL5017-93
《电力建设施工及验收技术规范》(管道篇)DL5031-94
《给水排水管道工程施工及验收规范》GB50268-97
3.管道工艺流程
3.工业管道安装通用工艺
3.1施工准备
3.1.1技术资料的准备
A、收集业主提供的工程设计文件资料,厂家的设备图、说明书、厂家标准、国家现行的施工验收规范。
B、组织专业技术人员、施工员对上述资料进行学习,使大家熟悉工程项目的技术要求、质量标准。
C、收集我司有关技术资料,以便对此进行借鉴。
3.1.2项目负责人组织有关专业人员对管道工程的施工图纸、技术文件进行综合会审。
会审前,应由各专业人员对图纸、文件预见先熟悉和自审,发现问题及时记录。
自审完毕后,集中进行会审。
会审的内容一般应包括:
A、图纸、资料是否齐全,设计深度能否满足要求。
B、流程图、平、立、剖面图与空视图(单管图)是否一致;管网的来龙去脉是否已基本清楚。
C、管道与设备、管线与管线间的接口的标高、坐标、方位的接口规格(直径、压力等级)是否相符,与厂房、构架有无碰撞。
D、所拟定的施工标准、规范等是否满足图纸、资料的技术要求。
E、有无漏项。
3.1.3管道施工前,除工艺流程简单的管道外,施工现场应请顾客牵头,会同设计人员对参与工程施工的有关人员进行设计交底,其内容包括:
A、工艺流程有关设备
B、施工现场的平面布置
C、管道工程的特点、特殊要求、施工标准及验收规范。
3.1.4综合会审中提出的问题应尽量在会上予以解决,否则应作好记录交由有关部门限期解决。
会审的结果应作详细记录,并形成纪要,落实解决问题的人员和时间。
3.1.5进行焊接工艺评定工作。
3.1.6进行施工机具与人员的准备工作。
3.2施工前的检查
A、现场的检查:
包括对现场的主要构筑物、所有预埋件的坐司法位置、水平标高等作测量和检查,并作记录,发现问题及时要求有关部门解决。
B、设备检查:
对所有已安装及到货的设备的管口进行检查,包括管口方位、标高、法兰材质、法兰压力等级等。
发现问题及时向设计部门反映,以便及时解决。
3.3材料的检查验收
3.3.1压力管道元件应有制造厂的产品质量证明书,其质量不得低于国家有关标准的规定。
3.3.2压力管道元件的材质、规格、型号、质量应符合设计文件的规定,并按国家现行有关标准进行外观检验,符合要求后才能使用。
3.3.3压力管道所采用的管材应符合下列标准:
GB/T14976-2000不锈钢无缝钢管;
GB3087-99中低压锅炉用无缝钢管;
GB/T8163-1999输送流体用无缝钢管;
GB/T8163-1999结构用无缝钢管;
SY/T5037-2000低压流体输送管道用螺旋缝埋弧焊钢管
SY5297-1991石油天然气输送管道用直缝电阻焊钢管
GB/T9711.1-1997石油天然气工业输送钢管交货技术条件第1部分:
A级钢管
GB/T9711.2-1999石油天然气工业输送钢管交货技术条件第2部分:
B级钢管
GB6479-2000高压化肥设备用无缝钢管
GB/T13793-1992电焊钢管
GB/T9948-1988石油裂化用钢管;
GB/T1527-1997铜管;
GB/T1528-1997黄铜管;
GB5310-1995锅炉用高压无缝钢管;
GB6497-2000化肥用高压无缝钢管
3.3.4压力管道所采用的管件材质应符合下列标准:
GB12459-99钢制对焊无缝管件;
GB/T13401-92钢板制对焊管件;
GB/T14383-93锻钢制承插管件;
GB/T14626-93锻钢制螺纹管件
SY0510-1998钢制对焊管件
SY/T5257-1991钢制弯管
GB/T12777-1999金属波纹管膨胀节通用技术条件
GB/T14525-1993波纹金属软管通用技术条件
SH3064-1994石油化工钢制通用阀门选用检验及验收
GB/T17116.1-1997管道支吊架第1部分:
技术规范
GB/T17116.2-1997管道支吊架第2部分:
管道连接部件
GB/T17116.3-1997管道支吊架第3部分:
中间连接件和建筑结构连接件
HG/T21578-1994管道减振器
JB/T8132-1995弹簧减振器
3.3.5合金钢管道组成件应采用光谱分析或其他方法对材质进行复查。
合金钢阀门的内件材质应进行抽查。
3.3.6阀门在安装前应逐个进行壳体压力试验和密材试验,壳体压力为公称压力的1.5倍,试验时间不少于5min,以壳体填料无渗漏为合格,密封试验宜以公称压力进行,以阀瓣密封面不漏为合格。
3.3.7安全阀应按设计条件规定的开启压力进行调试,每个安全阀的启闭试验不少于3次。
3.3.8带有蒸汽夹套的阀门,夹套部分应以1.5倍的蒸汽工作压力进行压力试验。
3.4管道加工
3.4.1管道的下料切割按下列方法进行:
A、镀锌钢管用机械方法切割,普通碳素钢、普通低合金钢管一般用机械方法切割,也可用手工气割或半自动火焰进行切割,但应将割口及附近的氧化物打磨干净。
B、不锈钢管禁止使用錾断法切割,只可用机械法或等离子法切割。
有色金属管道采用机械方法切割。
3.4.2管道的弯制DN≤20mm采用氧气-乙炔气火焰烤制弯曲或手动变管机弯曲;20mm≤DN≤100mm小口径管道,宜采用手动液压弯管机进行。
大口径管道、高压管道、合金钢管管道的弯制应委托专业管道弯制公司。
3.4.3高压管道上与法兰联结的螺纹或焊接坡口,应使用机床加工。
螺纹的切削应以管道内圆定心。
坡口的切削,可以以外圆定心。
对端口处(坡口钝边)内圆的偏差会导致组焊时的内壁错边量超过标准,应以不大于45度的锥角向管内削斜成锥面。
3.4.4有色金属管加热制作弯管时,其温度范围应符合下列要求:
管道材质
加热温度范围(℃)
铜
500~600
铜合金
600~700
铝11~17
150~260
铝合金LF2、LF3
200~310
钛合金
<350
铅合金
100~130
3.4.5奥氏体不锈钢管制作弯管时可不进行热处理,当设计文件瓢进行热处理时应按设计文件进行。
3.4.6弯管质量应符合下列规定要求:
1)不得有裂纹、过烧、分层等缺陷;
2)管子弯曲内侧表面波浪度:
小于060管△<2mm,大于076管△<4mm。
3)测量弯管任一截面上的最大外径与最小外径差应小于制作弯管闪管子公称外径的4%。
4)弯管的平面度允许偏差△应符合下列要求:
长度L
<500
500~1000
>1000~1500
>1500
平面度△
≤3mm
≤4mm
≤6mm
≤10mm
3.5管道预制
管道预制可大大提高工作效率,并可缩短现场施工时间保证产品质量,因此,在精确测量和合理安排的基础上,就尽可能加大管道工作量的预制深度,减少现场安装的工作量。
3.5.1管道预制应拥有必要的加工设备如行车、机床、焊机(包括自动焊机)、各类切割设备、坡口机、套丝机、各类工装工具等,不锈钢与碳钢管道的预制场地应加以隔离。
3.5.2管道的预制工作应按设计单位提供的管道系统单线图进行。
管道应遵守下列程序和规定:
A、管道组成件应按单线图规定的数量、规格、材质选配,并按单线图标明管系号和按预制的顺序标明各组成件的顺序号。
B、为了保证工程质量和便于安装,应合理选定自由管段和封闭管段。
C、自由管段应按单线图规定的长度加工,封闭管段应留有适当的裕度,按现场安装实测后的长度加工;其加工尺寸偏差应符合下表:
项目
允许偏差
自由管段
封闭管段
长度
±10
±1.5
法兰面与管子中心垂直度
DN<100
0.5
0.5
100≤DN≤300
1.0
1.0
DN>300
2.0
2.0
法兰各螺栓孔对称水平度
±1.6
±1.6
D、预制管段应具有足够的刚性,必要时,可进行加固,以保证存放,运输过程中不变形。
E、预制完毕的管段运抵现场,经现场安装人员检查,确认合格后,方可交付安装。
3.6卷管制作
3.6.1加工前应检查板材的外观质量,不应有裂纹、皱皮、分层等缺陷。
3.6.2在卷管制作加工过程中,应防止板材表面机械损伤,对于有严重伤痕的部位必须进行修磨,使其圆滑过渡,且修磨处的壁厚不小于设计壁厚。
3.6.3卷管的同一筒节上的绷焊缝不宜大于两道,两纵向焊缝间距不宜小于20mm。
3.6.4卷管组对时,两纵向焊缝间距应大于100mm,支管外壁距焊缝不应小于50mm。
3.6.5卷管的周长念头及圆度偏差应符合下表规定:
(mm)
公称直径
<800
800~1200
1300~1600
1700~2400
2600~3000
>3000
周长偏差
±5
±7
±9
±11
±13
±15
圆度偏差
<4
4
6
8
9
10
3.6.6卷管时采用校园样板跟踪检查,圆弧样板的弧长应为管子的1/4~1/6.样板与管内壁不贴合间隙应符合下列规定:
1)对接焊缝处不得大于壁厚的10%加2mm,且不大于3mm。
2)离管端200mm的对接焊缝处不得大于2mm,其他部位不得大于1mm。
3.6.7卷管端面与中心线的垂直偏差不得大于管子外径的1%,且不大于3mm,平直度偏差不得大于1mm/M。
3.6.8焊缝不能双面成型的卷管,当公称直径大于或等于600mm时,宜在管内进行封底焊。
3.7管道焊接
A、焊接施工前,技术人员应按单线图对焊缝进行编号,包括焊工号、焊口号等,并加以记录。
B、管道热处理按“压力管道热处理一般规定”执行。
C、管道理,包括焊接工艺、焊工、焊接材料,现场焊接等按本指导书“压力管道焊接通用规程”执行。
D、高压管道组成件的环缝焊的坡口,应使用机械方法加工,尽量避免使用加热方法,如采用加热方法如等离子或火焰成形的坡口,必须除去坡口附近的氧化物,并将凹凸不平处打磨平整。
对于碎硬倾向较大的管材,应将其热影响区磨去。
对于簿壁管的坡口(┙<159,δ<6mm),也可以用砂轮机直接打磨成形。
E、管道焊接,为保证工程质量,原则上均采用氩电联焊的焊接方法,如管径DN≤80mm,可采用全氩焊。
F、焊接不锈钢及低合金钢的根部焊道时,焊缝背面应采取充氩保护。
G、坡口定位焊应采用与正式焊接相同的焊接工艺。
H、除工艺或检验要求需分次焊成外,每条焊缝应一次连续焊完,否则就采取后热保温措施,并在再次施焊前,对焊道加以预热。
I、对焊口的焊前预热和焊后热处理,应严格遵循焊接工艺文件的规定温度、升(降)温速率、保温时间等参数执行。
J、管道环缝热处理前应将两端的开口封闭,以免“穿堂风”穿过,但要注意单侧开孔以通大气。
有阀门者,阀瓣应开启。
壁厚≤20mm者,宜用指形加热器(镍铬电阻丝)加热,壁厚大于30mm者,宜用电感应法加热。
K、施工过程中,应在每道完成的焊缝附近将焊口编号笔作标记,包括焊口号、焊工号等,并加以记录。
3.8管道脱脂
管道脱脂按本指导书“管道酸洗、脱脂一般规定”执行。
3.9管道安装
3.9.1管道的安装顺序在同一作业面上其先后通常按下列秩序进行:
A、先地下管后地上管;
B、先大管后小管;
C、先高压管后低压管;
D、先合金钢管后碳素钢管;
E、先高等级管后低等级管;
F、先夹套管后一般管。
3.9.2法兰联结应保持与管道轴心,确保密封面完好且螺栓能自由出入,所用和螺栓应同规格、足数量及同向安装。
3.9.3使用一次性密封垫片者,不得反复使用,对于参与试压及冲洗面需先安装的管道组成件,其密封片应采用临时的垫片暂代,待试压和冲洗完毕后,再装以正式垫片。
3.9.4管道安装时,应检查法兰密封面及密封垫片,不得有影响密封性能的划痕、斑点等缺陷。
当大管径垫片需要拼接时,应采用斜口搭接或迷宫式拼接,不得平口对接。
3.9.5软钢、铜、铝等金属垫片,当出厂前未进行退火处理时,安装前应进行退火处理。
3.9.6工作温度低于200度的管道,其螺纹接头密封材料宜选用聚四氟乙烯带,拧紧螺纹时,不得将密封材料挤入管内。
3.9.7高温或低温管道螺栓的冷态、热态紧固应符合设计及规范的规定。
3.9.8当管道安装工作有间断时,应及时封闭敞开的管口。
3.9.9有预拉伸(压缩)的管道,预拉伸(压缩)前应符合下列规定:
A、区域内固定支架间所有焊缝(预拉口除外)已焊接完毕,需热处理的焊缝已作热处理,并经检验合格。
B、预拉伸区域支、吊架已安装完毕,管子与固定支架已固定。
预拉口附近的支吊架已预留足够的调整裕量,支吊架弹簧已按设计值压缩,并临时固定。
3.9.10管道上取源部件的开孔和焊接应在管道安装前进行。
3.9.11管道膨胀指示器应按设计文件规定装设,管道吹洗前应将指针调至零位。
蠕胀测点和监察管段的安装位置及要求应符合设计及规范规定。
3.9.12当管道安装遇到下列情况之一时,螺栓、螺母应涂以二硫化钼油脂、石墨油或石墨粉:
A、不锈钢、合金钢螺栓和螺母。
B、管道设计高于100度或低于0度。
C、露天装置。
3.9.13有静电接地要求的管道,应严格近霜求设置接地耳和地板,以确保接地电阻符合要求,管道接头外当两侧的电阻大于0.03Ω时,要有导线跨接,并复核跨接后的电阻。
对钛管和不锈钢管道,导线跨接或接地引线不得与钛管道及不锈钢管道直接连接,应采用企事业管或不锈钢管过渡。
用作接地的材料或零件,安装前不得涂漆。
导电接触面必须除锈并紧密连接。
3.9.14管架的安装
A、严格近珠位置、形式、数量设计管道的全部管架;
B、锚固型管架应在管道预拉伸(压缩)前紧固,导得型管或滑支架其相对移动面应平滑,不得有卡涩现象,滑移方向和定位提前量正确;
C、弹簧支架的弹簧活动部份应锁住,待管道试压、防腐、保温完毕后方可解锁,并按设计负荷值整定弹簧的负荷;
D、不容许与管架的碳钢部件直接接触的管道组成件(如其材质为不锈钢或部分有色金属),应在它们的接触部位之间,垫以隔离物,此隔离物应既能长期耐受管道组成件的外壁温度和工作负荷,亦不会对管道造成二次污染。
3.9.15阀门安装应符合下列要求:
A、阀门安装前,应检查填料及压盖螺栓,应留有调节裕量。
B、阀门安装前应复核产品合格证和试验记录,并根据设计文件核对其型号。
C、阀门安装位置应尽量布置在集中区内及便于操作检修,阀门安装高度宜在1.2m上下。
D、平行布置管道上的阀门、手轮间净距不应小于100mm,为减少管道间距,可把阀门错开布置。
E、阀门应尽量靠近干管或设备安装,这样在系统水压试验时试验较多的管道,检修时也可拆下(或隔开)设备而不影响管道系统。
F、当阀门与管道以焊接方式连接时阀门不得关闭,焊缝底层宜用氩弧焊接。
G、安装铸铁、硅铁阀门时,不得强力连接,受力应均匀。
H、安装安全阀门,应符合下列规定:
*安全阀应垂直安装
*安全阀在管道投运前应进行送检调校,符合要求后再进行安装
*安全阀最终调校宜在系统上进行,其开启回座压力应符合设计文件规定。
*安全阀调校后,在工作压力运行状态下不得有漏泄
*安全阀经最终调校合格后,应做铅封,并填写有关调试记录
3.9.16补充器安装应符合下列要求:
A、安装门形补偿器,应按设计文件规定进行预拉仲或压缩,允许偏差为±10mm。
补充器水平安装时,平行臂应与管线坡度相同,两垂直臂应平行。
铅垂安装时,应调协排气及疏水装置。
B、安装填料式补偿器时,补偿器应与管道保持同心,不得歪邪。
导向支座应保持运行时自由伸缩,不得偏离中心。
并应按设计文件规定的安装长度及温度变化,留有收缩量。
插管应安装在介质流入端。
补偿器填料石棉绳应涂石墨粉,并应逐圈装入,逐圈压紧,各圈接口应有相互错开。
C、安装波纹膨胀节时应按设计文件的规定进行预拉伸,波纹膨胀节应与管道同轴,不得倾斜。
内有焊缝的端,在水平管道上应迎介质流向安装,在铅垂管道上应置于上部。
安装波纹膨胀节时应有临时约束装置。
3.9.17管道安装的允许偏差应符合下表规定:
项目
允许偏差(mm)
坐标及标高
室外
架空
25
地沟
15
埋地
60
室内
架空
15
地沟
15
水平管道垂直度
DN≤100
2L‰最大50
Dn>100
3L‰最大80
立管铅垂度
5L‰最大30
成排管段间距
15
交叉管的外壁或绝热层间距
20
3.10管道的检验和试验
3.10.1管道的无损探伤应按本指导书“压力管道无损检测一般规定”执行。
3.10.2管道试压
A、管道试压前,应按照设计方提供的流程图,划定试压系统,确定试验压力,每一系统应在相关流程图中标出相关管线,并附上相关管线的单线图;
B、压力试验一般以液体作为试验介质。
当管道试验压力≤0.6Mpa时也可采用气体为试验介质,但应采取有效的安全措施。
脆性材料严禁使用气体进行压力试验;
C、试验前应准备好所有必需的试压工具和设备如电动(手动)试压泵,各种临时肓板、垫片等;
D、压力试验前应具备以下条件:
*试验范围内的管道安装工程除涂漆绝热外,已按设计图纸全部完成,安装质量符合有关规定:
*焊缝及其他等部位尚未涂漆绝热;
*管道上的膨胀节设置了临时约束装置;
*试验用的压力表已经校验,符合要求;
*止回阀的阀芯已拆下,并已妥善保管;
*有经批准的管道试压方案,并已进行技术交底。
E、液压试验应使用洁净水,当对奥氏体裁不锈钢管道或连有奥氏体不锈钢管或设备的管道进行试验时,水中氯离子含量不得超过25ppm。
当采用可燃液体介质进行试验时,其闪点不得低于52摄氏度。
F、注水时应注意注水顺序,及时开闭排空阀门,使整个试压系统内的空气排尽;
G、整个系统充满试验介质,空气已经排尽时,方可一开始升压,升压过程应缓慢进行;
H、试验过程发现漏泄或异常情况时,应立即停止升压,并缓慢降至常压再行处理,严禁带压处理。
I、试验合格后,应缓慢将压力卸至常压,卸压过程中应注意按顺序打开放空阀和导淋阀,以防止管道内形成负压,并将余液排尽,必要时进行吹干。
J、在试验压力10min内及降至工作压力30min内压力无下降,检查焊缝及接口连接处无任何水珠和水雾,系统无变形,则水压试验为合格。
K、水压试验压力:
按《工业金属管道工程施工及验收规范》的规定如下:
管道级别
设计压力P(Mpa)
试验压力(Mpa)
直空管
0.2
中低压
地上管道
<0.5
1.25P
埋地
管道
钢管
1.25P且不小于0.2Mpa
铸铁管
≤0.5
2P
>0.5
P+5
>2.5<10
1.5P
I、对于易燃、有毒介质的管道,在水压试验和吹洗合格后,还应作气密性试验。
气密性试验介质采用空气或惰性气体。
试验压力按《工业金属管道工程施工及验收规范》的规定,承受内压钢管及有色金属管的试验压力为设计压力的1.15倍,真空管道的试验压力为0.2Mpa。
当管道的设计压力大于0.6Mpa时,必须有规定或经建设单位同意方可用气体进行。
试验前必须用空气进行压力为0.2Mpa的预试验。
试验时应缓慢逐步升压,当压力升到试验压力的50%时,检查系统未发现异状或漏泄时,继续按试验压力的10%逐级升压,每次稳压3min,直到试验压力。
稳压10min,再将试验压力降至试验压力,用涂刷肥皂水或发泡剂检验方法进行全面检查。
3.11管道系统的吹扫与清洗
3.11.1吹扫与清洗工作应按生产工艺流程或系统进行。
吹扫和清洗工作应包括以下内容:
A、管道系统的人工清扫和冲洗;
B、管道系统的化学清洗和预膜处理;
C、蒸汽管道系统的蒸汽吹扫;
D、工艺管道系统的空气吹扫;
E、润滑、密封及控制油系统的油清洗。
3.11.2吹扫与清洗工作前应具备下列条件:
A、压力试验已经合格,工程质量已达到规范及设计文件规定的标准;
B、操作方案已经批准,且操作人员已经掌握;
C、工作的各种资源已齐备;
D、不允许吹洗的设备及管道与已吹洗系统隔离;
E、系统吹洗前,不应安装孔、法兰连接的调节阀、重要阀门、节流阀、安全阀、仪表等,对于已焊接的上述阀门和仪表,应采取流经旁路或卸下阀头及阀口加保护套等防范措施。
3.11.3管道系统的吹扫和清洗,应遵守下列规定:
A、吹扫的方法应根据对管道的使用要求,工作介质及管道内表面的脏污程序确定。
公称直径大于60mm的液体或气体管道宜用于手工清理。
直径小于600mm的液体管道宜用水冲洗,气体管道宜用空气吹扫。
蒸汽管道应以蒸汽吹扫,非热力管道不得以蒸汽吹扫,有特殊要求的管道,应按设计要求采用相应的吹洗方法。
B、吹洗的顺序应按主管、支管、疏排管依次进行,吹洗出的脏物不得进入合格的管道;
C、吹扫时应设置禁区,严防发生安全事故。
D、管道吹洗合格后,应及时对系统进行复位。
3.11.4管道吹扫和清洗后的检查标准依照现行的验收规范执行。
4.交工验收
4.1工业管道的安装按设计和规范要求全部完成后,应及时请顾客(监理)方对工程进行检查并确认,施工范围和内容符合合同规定;工程质量符合设计文件和规范的规定。
4.2工程验收的同时,需向顾客(监理)提供下列技术文件作为交工资料:
A、管道组成件和支承件的质量证明书和复验、补验报告;
B、阀门试验记录;
C、高压管文化人加工记录;
D、安全阀调试记录;
E、焊接记录;
F、射线探伤报告;
G、超声波探伤报告;
H、磁粉探伤报告;
I、渗透探伤报告;
J、热处理报告;
K、管道补偿装置安装记录;
I、隐蔽工程记录;
M、管道系统压力试验报告;
N、管道系统吹扫及清洗报告;
O、管道单线图(准确标明焊缝位置、焊缝编号、焊工代号、无损检测布片编号、热处理位置);
P、其它检验报告;
Q、竣工图
5.保运服务
在交工验收后,在合同约定的责任内进