最新大型机床床身铸造工艺研究汇编.docx
《最新大型机床床身铸造工艺研究汇编.docx》由会员分享,可在线阅读,更多相关《最新大型机床床身铸造工艺研究汇编.docx(7页珍藏版)》请在冰豆网上搜索。
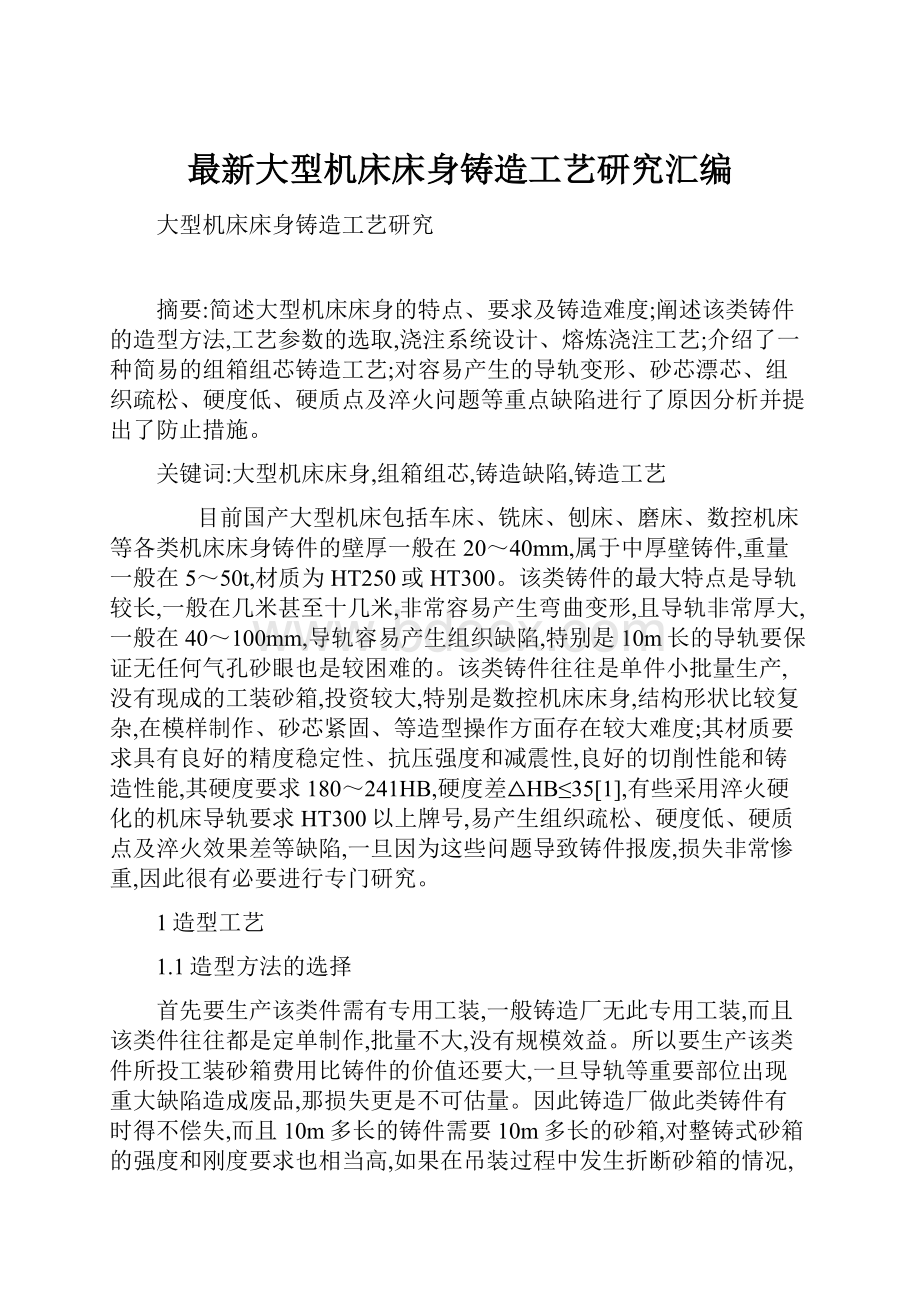
最新大型机床床身铸造工艺研究汇编
大型机床床身铸造工艺研究
摘要:
简述大型机床床身的特点、要求及铸造难度;阐述该类铸件的造型方法,工艺参数的选取,浇注系统设计、熔炼浇注工艺;介绍了一种简易的组箱组芯铸造工艺;对容易产生的导轨变形、砂芯漂芯、组织疏松、硬度低、硬质点及淬火问题等重点缺陷进行了原因分析并提出了防止措施。
关键词:
大型机床床身,组箱组芯,铸造缺陷,铸造工艺
目前国产大型机床包括车床、铣床、刨床、磨床、数控机床等各类机床床身铸件的壁厚一般在20~40mm,属于中厚壁铸件,重量一般在5~50t,材质为HT250或HT300。
该类铸件的最大特点是导轨较长,一般在几米甚至十几米,非常容易产生弯曲变形,且导轨非常厚大,一般在40~100mm,导轨容易产生组织缺陷,特别是10m长的导轨要保证无任何气孔砂眼也是较困难的。
该类铸件往往是单件小批量生产,没有现成的工装砂箱,投资较大,特别是数控机床床身,结构形状比较复杂,在模样制作、砂芯紧固、等造型操作方面存在较大难度;其材质要求具有良好的精度稳定性、抗压强度和减震性,良好的切削性能和铸造性能,其硬度要求180~241HB,硬度差△HB≤35[1],有些采用淬火硬化的机床导轨要求HT300以上牌号,易产生组织疏松、硬度低、硬质点及淬火效果差等缺陷,一旦因为这些问题导致铸件报废,损失非常惨重,因此很有必要进行专门研究。
1造型工艺
1.1造型方法的选择
首先要生产该类件需有专用工装,一般铸造厂无此专用工装,而且该类件往往都是定单制作,批量不大,没有规模效益。
所以要生产该类件所投工装砂箱费用比铸件的价值还要大,一旦导轨等重要部位出现重大缺陷造成废品,那损失更是不可估量。
因此铸造厂做此类铸件有时得不偿失,而且10m多长的铸件需要10m多长的砂箱,对整铸式砂箱的强度和刚度要求也相当高,如果在吊装过程中发生折断砂箱的情况,造成人员伤亡,那更是雪上加霜。
因此如何生产此类铸件,非常值得探讨。
一般厂家采用地坑造型,但对于紧张的造型面积,地坑造型不是很合适,而采用简易的组箱组芯法较好地解决了这一问题,它可以有效利用车间面积。
1.2组箱组芯法简介
该工艺区别于传统的组箱组芯法(劈模造型)。
传统的劈模造型是将模样根据各个面的形状分成几部分,然后将这几部分固定在模板上,再用专用砂箱舂箱,舂完箱再将各面砂箱组起来,用螺栓紧固好,空腔用砂芯组合。
而新型组箱组芯法不用外模样,不用模板,直接将分段砂箱组合起来,在组合好后的砂箱内用砂芯直接组出铸件结构形状。
采用组箱组芯法制作专用工装,铸件结构形状全部用砂芯组合,重点要解决好砂箱组合起来的刚度问题,所以必须用螺栓连接,这是该件能够投产的前提条件。
对于分成若干段的总共长达十几米的砂
箱,重点保证砂箱的强度和刚度的连续性,要求混砂速度快,舂砂也要跟上出砂的节奏,否则易出现砂型隔层裂纹等缺陷。
1.3该工艺的优缺点
该工艺把砂箱做成不同规格(1m、1.5m、2m、3m等)不同数量的几段,然后拼凑起各种长度和宽度不同的砂箱框,各段砂箱间用螺栓联结,满足不同长度和宽度的铸件需求,通用性强,一套工装可满足几种铸件的生产,工装费用大大降低,适用范围广,且操作方便,对砂箱的尺寸精度要求低。
该工艺将长达十几米的砂箱分成几段,减小每块砂箱的重量和尺寸大小,降低在行车吊装过程的危险性,可成功地避免这方面的安全事故,因为曾经发生几米长的砂箱在吊装过程中折断而发生危险的事情。
表1是组箱组芯法与传统方法的比较。
该方法缺点是要求操作人员的素质较高,操作过程尺寸精度的控制很大程度上依赖于操作人员的把握。
表1.组箱组芯法与传统方法的比较
造型方法
传统方法
组箱组芯
模样芯盒
外模芯盒都做
只做芯盒
模板
需做模板
不需模板
砂箱
专用性强
通用互换性强
经济性
工装费用高
降低工装费用
安全性
不安全
安全性好
①函数的取值范围是全体实数;操作性
较复杂
94.23—4.29加与减
(二)4P49-56操作简便
125.14—5.20加与减(三)4P68-74适用性
使用专一
3、通过教科书里了解更多的有关数学的知识,体会数学是人类在长期生活和劳动中逐渐形成的方法、理论,是人类文明的结晶,体会数学与人类历史的发展是息息相关。
使用范围广
精度
③tanA不表示“tan”乘以“A”;要求高(需要加工)
低(不需加工)
切线的性质定理:
圆的切线垂直于过切点的半径.
2.俯角:
当从高处观测低处的目标时,视线与水平线所成的锐角称为俯角2工艺设计及过程控制
2、加强家校联系,共同教育。
2.1反变形量
如果一条直线具备下列三个条件中的任意两个,就可推出第三个.导轨面上留凸起的反变形量5~25mm不等,根据导轨长度确定:
床身长度<5m,每1m铸件留1~2mm反变形量;床身长度>5m,每1m铸件留反变形量1.5~2.5mm;地脚面也要随形做出反变形量;有些结构很不均匀的床身,可能还会出现侧弯曲,这样也当需要在导轨侧面甚至整个床身侧面都要留反变形量。
②d=r<===>直线L和⊙O相切.2.2加工余量
一般在反变形量基础上再留10~20mm加工余量,余量也不用太大,否则加工完后会出现硬度不够的现象。
2.3收缩率
一般长度方向取1.0%,宽度方向取0.8%,高度方向取0.5%。
考虑胀箱等因素,宽度方向可不留缩尺,甚至考虑将模样尺寸人为减小,以保证出件后铸件的净尺寸符合要求。
2.4工艺补正量
为防止加工后导轨因变形而变薄,导轨及地脚背面可留3~5mm工艺补正量。
2.5浇注系统设计
浇注位置当然是将导轨放在下面,一般从床身两端由导轨进入铁液;特别长的导轨可采用底返雨淋浇注系统,这种浇注系统可保证铁液流程不要太长,有效防止出现冷隔及导轨掉渣、气孔缺陷,使铁液杂质上浮。
浇注系统全部采用耐火瓷管,造型时预埋于砂型中。
根据床身长度、浇注重量、导轨及床身与立柱结合面位于下型的特点,选择两端座包浇注,且采用底返雨淋及由“平、V”导轨两端同时进入铁液,总体上两层阶梯浇注方式,这样内浇道多点分散注入,两部行车同时浇注,充分考虑铁液流程,避免产生冷隔、浇不足、气孔等缺陷。
导轨中间采用集渣包,分散引流等方式将冷铁液转移走,避免导轨中间出现气孔针孔等缺陷,从而达到保证导轨铸造无缺陷的目标实现。
浇注时间要尽量短,依据浇注重量,一般在3~5min内浇注完。
2.6冒口设计
多采用耳冒口形式,厚大部位用冷铁包敷;冒口放置位置避开厚大部位,防止形成接触热节。
2.7砂芯设计
在保证操作方便的情况下,尽量将各砂芯连在一起,以增大自重抵消铁液浮力。
另外要用紧固螺栓把砂芯固定在底箱上,紧固螺栓可以穿透一层甚至几层砂芯,另外导轨芯也要根据长度分成好几段。
2.8模板设计
较长的床身,模板可做成2~3段,段与段之间用燕尾销连接;若不用外模,纯粹用砂芯组合起来,那么形成外型的砂芯也要人为分成几段,以便制芯和下芯操作。
2.9冷却措施
对于比较厚大的导轨,可在导轨底面敷以冷铁激冷,冷铁材质最好采用石墨块,也可以采用铸铁冷铁,当然必须烘干水分,防止呛火,特别在冬季要注意避免温差太大,因此放置铸铁冷铁要慎用。
2.10尺寸精度控制
底箱首先要铺平,要用水平仪或拉线找平;导轨芯也要注意以水平线找正,其高度尺寸定位也要充考虑反变形量和加工余量。
2.11熔炼浇注工艺
采用高Si/C灰铸铁在CE=3.4%~3.8%条件下,适当增加废钢加入量,将Si/C从0.4~0.5提高到0.7~0.8,将铁液出炉温度提高到1450℃以上,抗拉强度可提高20~30MPa,铸件具有较小的变形倾向;但对于机床这类壁较厚的铸件,提高Si/C比会增加厚断面处的铁素体含量,反而会使硬度降低,此时加入Cr合金元素,提高机床厚断面处的珠光体含量,减少断
面硬度差,增加机床的精度稳定性。
另外,Mn量稍高于Si量的灰铸铁具有良好的性能:
收缩小,不易产生缩孔、缩松,切削性能好,是一种提高强度,弹性模量和耐磨性、减少铸件变形的良好材质。
[2]值得一提的是,机床导轨表面经常采用淬火热处理,淬火后的表面能获得马氏体+石墨的组织,珠光体基体淬火后表面硬度可达50HRC左右,因普通灰铸铁含Si高,淬透性差,添加少量Ni、Cr、Mo能改善其淬透性。
采用炉前孕育和浇注时瞬时孕育相结合的方法,一般浇注采用两包同时浇注。
要调整好铁液成分,保证铁液温度。
我厂采用的HT250、HT300的化学成分见表2。
表2HT250、HT300的化学成分(wt%)
牌号
C
Si
Mn
S
P
Cr
HT250
2.9~3.1
1.3~1.5
1.0~1.2
≤0.12
≤0.15
<0.3
HT300
2.9~3.2
1.2~1.6
0.9~1.2
<0.1
<0.12
<0.3
3重点缺陷防止
3.1变形问题
对于分导轨水平方向和床身侧面方向的变形问题,解决的措施:
一是上述已提到的做反变形量;二是根据铸件结构,在铸件抗弯薄弱的地方适当做拉筋。
3.2砂芯漂芯
最主要的是将导轨芯及上层砂芯用长螺栓紧固于下箱,若无法紧固,则应将各个独立的砂块用外力将它们联系起来,以抵消浮力的冲击。
3.3组织疏松硬度低
经常在床身导轨面加工后出现弥散分布的细孔,这就是组织疏松,这是由于其金相组织中片状石墨粗大,即组织异常造成的缺陷,表现出很低的硬度。
其形成原因主要是对应于铸件壁厚部位,碳当量过高,片状石墨粗大是根本原因;熔炼温度低,铁液过热度小,铁液中有未完全熔解的石墨片,易使片状石墨粗大;冲天炉熔炼过程中,铁液增碳过多。
其防止措施:
根据铸件壁厚,确定合理的碳当量,以获得细片状石墨和以珠光体为主的金相组织;铸件化学成分中添加适量的合金元素,如B、Mn等;提高铁液过热度,加强孕育处理,降低浇注温度,提高铸件厚壁部分的冷却速度,如放外冷铁等。
3.4硬质点及淬火效果差
主要是由于含Si量高,组织中含有未充分扩散的局部的硅富集区,富集区中的Si同铁液中的C形成硬度很高的非金属夹杂物SiC晶体[3]造成加工硬点;另外由于含Si量高,组织中有铁素体存在,使得淬火硬度和深度受到影响,因为铁素体组织的淬透性远比珠光体差。
因此,对于要求导轨表面淬火的机床床身,成份选取时应控制较低的含Si量,一般在1.2%~1.6%Si之间,对于原始组织中有铁素体存在需要表面淬火的灰铸铁件,则进行一次正火处理,能保证随后的淬火效果。
4应用效果
(1)采取以上工艺措施已成功为上海、威海、济南、沈阳等地生产数件机床床身,他们对我厂生产的铸件给予充分肯定和高度评价。
(2)该工艺成功应用于M7150×3m、M7150×5m、M7150×6.6m、M7150×8.6m,M7150×12.6m、M8463×6.6m、M8463×8.6m、M8040×6.6m、M8048×8.6m等几种大型磨床床身及桂林重达15t的工作台及本公司大型铸铁平台的生产,不仅操作安全方便,而且经济适用,效果很好,相比劈模造型而言,生产以上铸件可节约工装费用100余万元。
(3)应用组箱组芯法生产大型机床床身,具有经济适用,操作安全性高的优点,很适合铸造厂手工造型。
应用此工艺方法,从理论上讲,无论多长的铸件都能够生产,从而扩大了我厂的生产能力,拓宽了市场领域。
(4)充分考虑机床床身铸件本身的结构特点,正确选取各项工艺参数,合理调整铁液成分,保证铁液温度,做好各类缺陷的防止措施,就能够成功铸造大型机床床身。