安全事故案例讲解.docx
《安全事故案例讲解.docx》由会员分享,可在线阅读,更多相关《安全事故案例讲解.docx(54页珍藏版)》请在冰豆网上搜索。
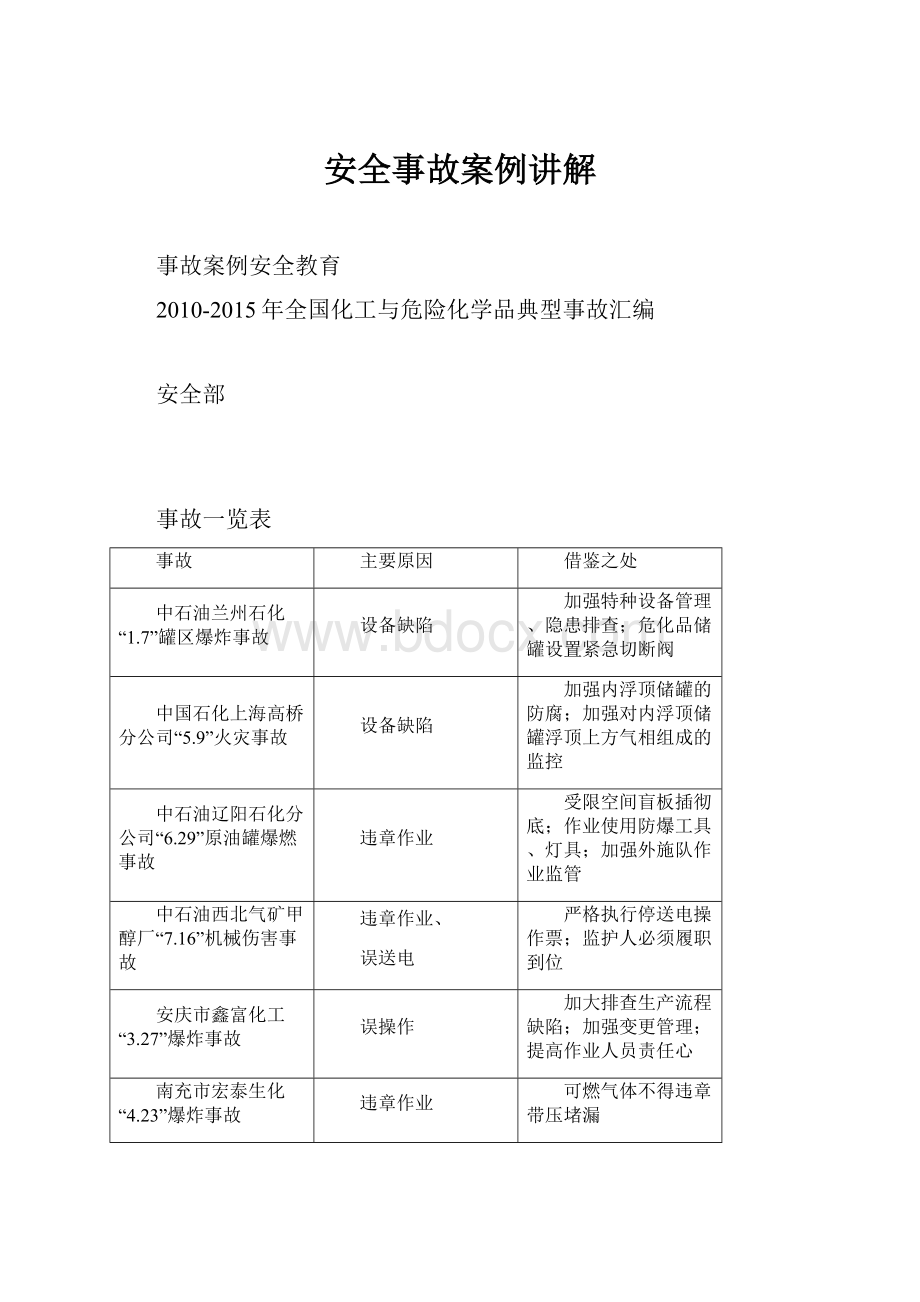
安全事故案例讲解
事故案例安全教育
2010-2015年全国化工与危险化学品典型事故汇编
安全部
事故一览表
事故
主要原因
借鉴之处
中石油兰州石化“1.7”罐区爆炸事故
设备缺陷
加强特种设备管理、隐患排查;危化品储罐设置紧急切断阀
中国石化上海高桥分公司“5.9”火灾事故
设备缺陷
加强内浮顶储罐的防腐;加强对内浮顶储罐浮顶上方气相组成的监控
中石油辽阳石化分公司“6.29”原油罐爆燃事故
违章作业
受限空间盲板插彻底;作业使用防爆工具、灯具;加强外施队作业监管
中石油西北气矿甲醇厂“7.16”机械伤害事故
违章作业、
误送电
严格执行停送电操作票;监护人必须履职到位
安庆市鑫富化工“3.27”爆炸事故
误操作
加大排查生产流程缺陷;加强变更管理;提高作业人员责任心
南充市宏泰生化“4.23”爆炸事故
违章作业
可燃气体不得违章带压堵漏
中海油惠州炼油分公司“7.11”火灾事故
设备带病运行
避免设备带病运行;带病运行时要明确巡检要求;完善设备仪表监控
中石油大连石化公司“8.29”储罐火灾事故
违章作业、
静电
按要求控制浮顶罐液位;控制物料流速
江西乐平市江维高科“9.13”爆炸事故
违章作业
防爆区域使用防爆工具;设备法兰螺栓必须上齐
常山绝缘材料公司“10.16”爆炸火灾事故
工艺缺陷、
电机不防爆
提高工艺自动化控制程度;防爆区域使用防爆电机
一:
中石油兰州石化“1.7”罐区爆炸事故
关键词:
设备缺陷
一、事故简介
2010年1月7日17时24分,兰州石化公司316#罐区发生火灾、爆炸事故,事故共造成6人死亡、1人重伤、5人轻伤,未造成次生事故和环境污染。
二、事故经过
2010年1月7日早班,合成橡厂316#罐区碳四、丁二烯罐区当班班组外送R202球罐裂解碳四物料,同时接收烯烃装置送来的裂解碳四物料。
7日中班按照本厂调度安排,于15时30分停止外送R202球罐裂解碳四物料,继续接收烯烃装置送来的裂解碳四物料。
17:
15合成橡胶厂316#罐区操作工王某按照当班班长孙某指令,到碳四、丁二烯罐区巡检并检查丁二烯卸车工艺流程,走到罐区平台时,发现R202罐底部出料管线第一道阀门下弯头处有碳四喷出,罐区防火堤内弥漫一层白雾,浓度很大,呼吸困难,便立刻跑回控制室,向班长孙某进行了汇报。
17:
19班长孙某电话向本厂调度室报告,316#罐区R202罐体底部管线泄漏,请求立即派遣消防车到现场监护。
并安排王某立即到第4#货位疏散等待卸料的丁二烯槽车。
石油化工厂丙烯腈装置焚烧炉当班人员向本厂调度室报告,316#罐区北侧铁路附近有大片白雾,接着又报告白雾迅速扩大。
17:
21合成橡胶厂316#罐区班长孙某再次向本厂调度室报告,泄漏十分严重,现场一片白雾,要求停止向R202球罐送料。
17:
24:
32大量泄漏的碳四物料迅速汽化扩散,蔓延至罐区东北侧石油化工厂丙烯腈装置焚烧炉区域,与焚烧炉明火引燃,外围火焰迅速回燃至316#罐区。
达到爆炸极限的混合气体在316#罐区发生空间爆炸。
17:
28根据石化总调度指令,烯烃装置紧急停止间316#罐区R202球罐输送碳四物料。
三、事故原因
(1)直接原因
设备缺陷。
由于316#罐区R202球罐出料管弯头母材焊缝热影响区存在组织缺陷,致使该弯头局部脆性开裂,导致碳四物料大量泄漏,泄漏汽化后的碳四物料蔓延至罐区东北侧丙烯腈装置焚烧炉,遇焚烧炉明火引燃爆炸。
(2)间接原因
①特种设备安全监督管理不到位
I、未按规程规定对事故管线进行定期检验
没有按照国家质监总局2003年6月试行的《在用工业管道定期检验规程》规定,对在用工业管道进行全面定期检验,致使R202球罐出料管线母材存在的组织缺陷未被发现和整改。
II、未按规定落实事故管线更换计划
2007年3月,经检验发现R203,R206,R207球罐底部进出物料管线腐蚀严重、壁厚减薄,定为4级,企业下达了R201,R202,R203,R204球罐底部进出物料管线更换计划。
实际仅更换了R201球罐底部进出物料管线,R202,R203,R204球罐底部进出物料管线一直未更换。
②设备管理人员没有认真履行设备管理职责
设备管理部门和有关管理人员,没有按照规定要求对碳四车间R202等球罐进出物料管线进行全面检测检验,在R202球罐管线更换计划下达后,又没有履行监督落实职责,致使事故隐患长期存在并最终导致事故发生。
③安全应急处置设施不完善
316#罐区自1986年建成投运以来,未按《石油化工企业设计防火规范》(GB50160-2008)规定,对储罐进出物料管道设置自动联锁切断装置,致使事故状态下无法紧急切断泄漏源、导致致泄漏扩大并引发事故。
四、点火源分析
技术组通过仔细分析事故发生全过程的视频资料、电话录音、事故当事人的笔录、事故现场勘察情况和316#-R202球罐1#出口管线失效分析结论,反复核查事故证据,查找事故区域碳四泄漏点和事故点火源。
1、事故区域内的设备及管道勘察
316#-R202球罐:
支柱部分防火层脱落,支柱、拉杆等受热变形,球罐保温层脱落,梯子、平台和喷淋管线等附件脱落,部分接管断裂。
球罐向316#-8202方向倾斜,球罐本体无显著变形,罐体未开裂。
316#-R201A放水槽:
罐体基本完好,无过火痕迹,保温层脱落,罐体向北位移0.3m,连接管道变形、断裂,支腿受热变形。
316#-R203球罐:
支柱隔热层完全脱落,支柱受热变形,罐体坍塌,球罐保温层脱落,梯子、平台和喷淋管线等附件脱落。
罐顶部有一长度约3m,宽度大于1m的横向韧性裂口,裂口在母材上扩展。
支柱受热,严重变形。
罐底部及其接管严重受热变形、有严重氧化痕迹。
个别接管部分表面无氧化痕迹或氧化较轻,出料口接管弯头开裂。
316#-R203球罐:
罐体基木完好,支柱基本完好,球罐保温层脱落,梯子、平台和喷淋管线等附件脱落,面向316#-R202一侧有明显的黑色过火痕迹。
316#-R204球罐:
球罐支柱基本完好,球罐保温层脱落,梯子、平台和喷淋管线等附件脱落。
面向316#-R202一侧有明显的黑色过火痕迹,下部球壳板出现一处韧性裂口,长度约1800mm最大宽度550mm。
进口接管弯头部位一处韧性裂口(80×40mm)。
底部管线受热严重、断裂,表面严重氧化。
316#-R205球罐:
支柱基本完好,球罐保温层脱落,梯子、平台和喷淋竹线等附件脱落,罐体面向316#-R202一侧和底部有明显的黑色过火痕迹,但受热明显较316#-R201和316#-R204要轻,且上部球壳板出现一处韧性裂日,底部部分管线断裂。
316#-R207球罐:
罐体面向316#-R202一侧有明显的过火痕迹。
上述事故现象表明:
(1)泄漏在事故区域的碳四遇“火”燃烧后,火焰最后集中在316#-R202球罐进行燃烧:
(2)燃烧产生强大的辐射热使316#-R201,R202,R204,R205球罐存在不同程度的过火:
(3)与316#--R202相邻的316#-R201,R204,R205球罐由于受到辐射热的加热分别表现为:
316#-R201球罐3根支柱(面向316#-8202侧)受热强度降低,由于不堪重负,3根支柱失稳。
造成该球罐向316#-R202侧倾斜;
316#--R202、R204、R205球罐本体由于在极短的时间内受到高温加热,球罐气相空间的球壳板温度升高,强度降低;同时由于3个球罐内储存的物料随着温度升高,蒸气压力急剧升高【物料温度为38℃时:
1,2丁二烯饱和蒸汽压力为0.27459MPa,160℃时:
1,2丁二烯饱和蒸汽压力为3.7844MPa,(2002.5化学工业出版社《化学化工物性数据手册》P232)】,也就是说,受热后的球壳内物料的温度由38℃提高到160℃时,内压力被剧烈提高到了设计压力的2.37倍。
160℃时的压力还不足以使其爆裂,但从裂口钢板的颜色可以确定其当时的温度超过了600℃。
因此,在如此环境下3个球罐都在其气相空间破裂。
316#-R202,R204,R205球罐开裂后,加剧了316#罐区的燃烧状况,使邻近的其他设备如:
拔头油罐F1/C,F1/D,西侧丙烯、丙烷罐区中的F2/A(丙烯罐),F3/A(丙烷罐),常压罐区的F6(抽余油罐)、F7(加氢汽油罐)、F8/A(甲苯罐)、F5(重碳罐)、F10(裂解油罐)和316#罐区的部分管线造成相应的破坏。
(4)316#-R202底部接管中球罐物料出口接管与球罐的物料进口接管的宏观形貌表明:
该球罐物料出口接管(1号)为第一泄漏点的结论除与班长孙景林、合成橡胶厂值班调度电话录音吻合外,还有如下分析。
出料口接管(1号):
管子外表面残留有绿色油漆,外表面无高温氧化痕迹。
表明该管子表温度一直处于较低状态,说明该管子在火灾中,持续有物料从管内流出,降低了管子的表向温度。
出料口接管(2号):
管子外表面呈褐色,氧化皮厚重,呈严翼纂化态,表明管子在火灾没有介质泄漏,处于高温状态。
进料口接管(3号):
管子外表面呈铁锈色,阀门上残留有绿油漆。
表明管子在火灾处于高温状态,但温度较2号管低,有介质在管道中通过对管子表面起到了降温的作用。
(5)316#-R202球罐1#出口管线失效分析结沦:
弯头和粉线化学成分符合GB9948-88中20钢要求;除1#管线母材、弯头焊缝外,其余部分S含量不符合GB9948-2006中20钢的要求;
管线材料力学性能中抗拉强度符合GB9948-2006和GB9948-88中20钢要求,但延伸率部分低于GB9948-2006/88中20钢标准值。
冲击韧性随温度降低明显下降,冲击韧性较低:
1#弯头和直管金相组织晶粒较粗大,含有少量的魏氏组织,焊缝热影响区有魏氏组织存在;在塑性变形较大区域,珠光体明显分解,渗碳体分布于晶粒晶界;
受热影响区中魏氏组织的影响,材料冲击韧性降低;
裂纹源位于焊缝热影响区附近一平断口区域;材料低温脆性是造成开裂的直接原因。
介质的泄漏对开裂口的冲刷以及温度和塌压等原因,导致开裂部位继续撕裂,引起局部塑性变形减薄。
2、事故点火源的确定
技术组对事故区域内所有可能导致事故发生的点火源进行了认真的排查,确定丙烯腈装置污水焚烧炉(位于事故区域东北方向距316#-R202约105m,角度北偏东25.37°,当时处于工作状态,有明火)为事故点火源。
与2010年1月7日17时24分32秒视频资料提供的事实相符。
3、事故结论
316#-R202碳四球罐1#出料口弯头焊缝热影响区组织缺陷使弯头局部脆性开裂,导致易燃易爆的碳四物料泄漏并扩散至整个事故区域,遇丙烯腈装置污水焚烧炉的明火着火爆炸是造成此次事故的直接原因。
五、反思与建议
(一)加强特种设备安全管理工作,完善特种设备安全管理制度,按照《在用工业管道定期检验规程》要求,定期组织开展在用工业压力管道在线检验和全面检验,切实落实检修工作,及时发现和消除事故隐患,确保安全运行。
(二)加大设备改造力度,提高本质安全水平。
对存在安全隐患的设各设施进行彻底整改,对不能满足安全生产条件的压力容器和压力管道要坚决淘汰更新,特别对液态烃、液氯,液氨及剧毒化学品等重点储罐,按照《石油化工企业设计防火规范》(GB50160-2008)的要求,设置紧急切断阀,装备安全联锁装置,完善泄漏检测报警系统,全面提升危险化学品储罐区等重大危险源安全监控水平。
(三)加强企业应急管理工作,提高全员应急处置能力。
完善事故应急救援预案,采取多种形式强化教育培训,定期开展事故应急预案演练,提高全员对事故的分析判断和应急处理能力。
同时储备必要的应急器材和物资,确保在突发事故中,做到及时有效、科学果断处置。
二:
中国石化上海高桥分公司“5.9”火灾事故
关键词:
设备缺陷、浮顶罐
一、事故简介
2010年5月9日11时20分左右,上海高桥分公司炼油事业部储运2号罐区石脑油储罐发生火灾事故,事故造成1613#罐罐顶掀开,1615#罐罐顶局部开裂,此次事故没有造成人员伤亡,经济损失为625535元。
二、事故经过
5月9日0:
45,按照调度安排,1613#罐(重整原料罐,罐容5000立方米,内浮顶结构,直径21米,高度16.5米,储存介质为石脑油)开始收蒸馏三装置生产的石脑油。
10:
00左右,在继续收蒸馏三装置生产的石脑油的同时,开始自1615#罐向1613#罐转罐,此时1613#罐液位为5.09m在继续收蒸馏三装置生产的石脑油的同时,开始自1615#罐向1613#罐转罐,此时1613#罐液位为5.09m。
11时20分,1613#罐液位为5.62m,存储石脑油1345吨。
11时30分左右,1613#罐发生闪爆,罐顶撕开,并起火燃烧。
现场操作人员立即停泵,启动各个储罐冷却水喷淋,并进行转油、关阀等应急处理。
作业人员发现1615#缺冷却喷淋管线损坏,在火灾初期无法对1615#罐进行冷却保护。
企业消防队接警后迅速调派15台消防车赶赴现场灭火,并通知蒸馏、重整等有关装置降量生产。
上海市先后调动50多台消防车赶赴火灾现场。
14时左右火势得到控制,14时37分明火被扑灭。
14时47分,罐内发生复燃,因罐体严重变形,消防泡沫很难打到罐内,彻底扑灭罐内余火难度较大。
18时40分左右,现场指挥部在确定安全前提下,组织消防人员沿油罐扶梯爬到罐上部,将消防泡沫直接打到罐内。
19时10分余火完全扑火。
三、事故原因
1、直接原因
1613#油罐铝制浮盘腐蚀穿孔,导致石脑油大量挥发,油气在浮盘与罐顶之间积聚;罐壁腐蚀产物硫化亚铁发生自燃,引起浮盘与罐顶之间的油气与空气混合物发生爆炸。
2、间接原因
设备防腐和监督检查不到位,2003年至今只做过一次内壁防腐,石脑油罐罐壁和铝制浮盘两重腐蚀。
四、事故原因分析
(一)可燃物分析
(1)石脑油燃爆性质
①闪点
5月12日检测结果表明,石脑油闪点小于-10℃,根据《石油化工设计防火规范》第3.0.2条,属于甲B类火灾爆炸物质。
②爆炸极限
石脑油爆炸极限在1.3-6%,爆炸下限较低。
(2)浮盘与罐顶之间形成油气空间的几种原因
①油罐付油过程中随着液面的下降,浮盘顶部形成了一定的负压,粘附在油罐内壁上的油品汽化挥发。
②当油面降至浮盘支撑高度以下时,在浮盘下形成了一个浓度较高的油气空间,油气通过浮盘上的检尺孔、通气孔等扩散至浮盘上方,充满了整个油罐空间。
(3)浮盘密封圈不严或浮盘腐蚀情况
1613#油罐内浮顶铝皮表面不均匀分布着一些白点,除去上面白色的氧化物,某些白点下面已经穿孔,直径在1-3mm之间。
靠近罐壁位置的浮盘铝皮白点较多,中间较少。
内浮顶约20%部位有此情祝。
(4)分析
上述检测情况说明,部分石脑油罐的浮盘存在不同程度的泄漏,1654#罐浮盘与罐顶之间的油气浓度已达到1.0%以上(石脑油的爆炸下限为1.5%)
发生爆炸的1613#罐浮盘的腐蚀穿孔现象严重,导致油气挥发,在浮盘与罐顶之间形成油气和空气的爆炸性混合气体。
(二)点火源分析
经过现场勘查、资料搜集和人员问询,事故调查组对导致石脑油罐1613#爆炸的三种可能性进行了逐项分析:
(a)外部火源情况
(b)静电火源的情况
(c)硫化亚铁自燃产生点火源的情况
(1)外部火源的情况
①罐区内作业情况
从5月7日开始,安徽美祥实业有限公司在1612#罐内部安装浮盘。
5月9日上午8:
30储运2号罐区员工李文勇(监火人)到车间办理好用火作业许可证。
8:
50,安徽美祥实业有限公司员工开始作业,电源由北面马路上配电柜接出,作业是在罐体内部进行,罐内3人作业,1人使用手枪钻钻孔,另外2人配合,铺铝制盖板,并将浮盘各部件装配起来,在罐外有车间及安徽美祥实业有限公司2人监火。
10点45分,安徽美祥实业有限公司作业人员停止作业,前往厂外吃午饭。
在离开现场前,切断了电源。
在此期间,罐区区长宋某和安全员苏建忠均来过现场(上述情况是根据事故笔录整理)
进入受限空间(进罐)作业许可证期限:
5月8日8:
30至5月10日16:
00;动火作业许可证期限:
5月9日8:
00至5月9日16:
00。
②临时电源线的接线情况
临时电源线接自北侧蜡油罐区处的配电箱,出罐区后跨过马路,进入石脑油罐区,最后从1612#罐人孔进入储罐,供手枪钻用电。
③1613#罐与1612#罐的连接情况
经现场勘查,1613#罐与1612#罐的消防泡沫线、冷却水线均独立设置,没有相互联通,不会由于1612#罐内使用电钻作业,产生电火花、发生火焰在管道中传播,导致1613#罐爆炸的情况。
(2)静电火源的情况
①进入1613#罐内的石脑油的线速度计算
10:
00-11:
25分,1613#罐收油量计算为142.361吨
石脑油密度:
0.71吨/m3
则,进1613#罐的石脑油的体积流量为:
Vs=(142.361/0.71)/(85*60)=0.0393m3/s
Vs=uA
1613#罐进口管道截面积:
A=3.14*(d0/2)2=3.14*0.12=0.0314m2
u=Vs/A=0.0393/0.0314=1.25m/s
根据((中石化集团公司安全管理制度》—易燃、可燃液体防静电安全规定第四条,“甲、乙类易燃、可燃液体进入贮罐和槽车时,初流速度不应大于1m/s。
当入口管浸没200mm后可逐步提高流速,但最高不应超过6m/s。
甲、乙类易燃、可燃液体含游离水、有机杂质以及两种以上油品混送时的初流速度亦不应超过lm/s。
”
进入罐内石脑油的最大线速度为1.25m/s,低于《中石化集团公司安全管理制度》规定的6m/s。
②进口扩散管的位置
根据1613#罐设备结构图,进口扩散管在储罐底部,事故发生时液面高度5.6m,进口扩散管插入液面以下,不存在喷溅进油的情况。
③储罐接地情况
储罐每年要做2次防雷接地检测,2010年4月按照规定对1613#油罐进行了第一次防雷接地检测,检测结果为合格。
初步分析结论:
进入罐内石脑油的线速度为1.25m/s,低于6m/s,并且进口扩散管插入液面以下,静电接地良好,因此,由于静电积聚产生电火花的可能性很小。
(3)储罐浮盘上部硫化亚铁自然产生点火源的情况
①石脑油腐蚀情况
Ⅰ、罐壁腐蚀情况
该罐1998年建成,2008年曾对1613#罐进行罐壁测厚,测厚精况列表如下:
原设计罐壁壁厚与2008年罐壁厚的比较
1
2
3
4
5
6
7
8
9
原设计罐壁厚
11
11
11
10
9
7
6
6
6
2008年罐壁厚
12.1
12.3
11.7
9.6
8.5
6.9
5.6
5.6
5.6
减薄量
-
-
-
0.4
0.5
0.1
0.4
0.4
0.4
上述情况说明,1613#罐罐壁上部腐蚀较为严重,这是由于罐壁上部与空气接触时间较长,腐蚀较为严重。
Ⅱ、原油及石脑油硫含量分析
5月9日,3#蒸馏加工的原油硫含量为1.7-1.8%。
5月12日,对1613#石脑油罐内油品进行了硫含量分析,检测结果为0.0436%(436ppm),硫含量偏高。
由于石脑油中硫含量较高,对罐壁造成严重腐蚀。
Ⅲ、石脑油罐内腐蚀产物分析
5月11日,抽净1613#罐油水之后,打开1613#罐底人孔,发现1613#罐浮盘已沉到罐底,观察到1613#罐内浮盘上有大量腐蚀产物,厚度在1cm以上。
5月12日,在1615#罐内石脑油倒空之后,打开1615#罐底人孔,发现浮盘己落至底部,浮盘支撑完好,经测量,罐底腐蚀产物厚度20cm左右(含水)。
事故调查组分别对1613#罐罐底人孔盖、浮盘边缘部位、1615#罐罐底腐蚀产物进行了取样,采用元素分析对三个样品的硫、铁含量进行了分析,结果如下:
样品中硫、铁含量分析结果
序号
样品名称
检测结果,wt%
备注
硫含量
铁含量
1
1613#罐底人孔1#
25.04
26.60
采用电感藕合等
离子体发射光谱分析,
ISO11885-2007
2
1613#浮盘边缘2#
7.49
48.33
3
1615#罐底3#
9.12
23.76
从上表分析结果可以以着出,1613#罐底人孔处不与空气接触,硫化亚铁未被氧化,硫含量明显偏高,1613#罐浮盘边缘由于长期与空气接触并经历事故时的燃烧过程,硫含量较低。
对样品中的硫铁化合物组成进行X射线衍射分析,从谱图可以看出,样品中硫铁化合物的结构形式主要是Fe3S4,FeS2这进一步证明油罐中硫化物腐蚀后主要生成了硫铁化合物的不稳定价态,容易发生氧化放热反应。
(4)硫化亚铁自热自燃特性
①硫化亚铁形成机理
硫化亚铁是油品中活性硫与铁或铁的氧化物作用的直接产物,在油品加工储运过程中,非活性硫不断向S、H2S和硫醇(R-SH)等活性硫转变,这些活性硫在不同条件下与铁或铁的化合物发生反应,生成多种形态的硫铁化合物。
通常情况下铁的硫化物有二硫化铁、硫化亚铁和三硫化二铁。
硫化亚铁和三硫化二铁是生产设备储罐上氧化铁或铁与含硫物质(包括单质硫、硫化氢和有机硫化物等)长期发生腐蚀作用而生成的。
其主要反应方程式为:
常温下:
2Fe(OH)3+3H2S=Fe2S3+6H2O
温度较高的情况下:
2H2S+O2=2H2O+2S
Fe+S=FeS
Fe+H2S=FeS+H2
Fe2O3+4H2S=2FeS2+3H2O+H2
②硫化亚铁自燃反应机理
石油化工生产过程中,通常意义上说的硫化亚铁自燃导致的燃烧爆炸事故,准确的说应该是硫铁化合物,它是FeS,FeS2,Fe3S4等的统称,硫化亚铁(FeS)仅是其中的一种,它们的自热性能基本一致,研究人员都以FeS为研究对象,称呼也就以硫化亚铁代替了硫铁化合物。
硫化亚铁自燃反应方程式:
常温无水条件一下:
FeS2(s)+O2(g)=FeS(s)+S02(g)+222.4kJ/mol
FeS(s)+3/2O2(g)=FeO(s)+S02(g)+48.97kJ/mol
Fe2S3(s)+3/2O2(g)=Fe2O3(s)+3S(s)+586.04kJ/mol
(三)事故原因分析
(1)可燃物
1613#油罐内浮顶(铝制)腐蚀穿孔,导致石脑油大量挥发,在浮盘与罐顶之间积聚。
(2)助燃物
储罐在付油状态下,空气可通过罐顶呼吸阀、量油孔等处进入浮盘与罐顶之间的空间。
(3)点火源
由于罐壁长期经受腐蚀,腐蚀产物硫化亚铁(FeS2,Fe3S4)不断落在浮盘上,并逐步积聚(厚度1cm),逐渐在浮盘上形成厚厚的、呈多孔间隙状的堆积层,硫化亚铁与空气中的氧接触后,发生氧化反应放出热量,某处过厚的及具有较大比表面积的堆积层的散热速度不足以使其内部放热反应所产生的热量及时散发出来,热量逐渐在堆积层内积聚,内部温度升高,超过硫化亚铁的自燃点,发生自燃。
综上所述,此次事故的直接原因为:
由于硫化亚铁发生自燃,引起浮盘与罐顶之间的油气与空气混合气体发生爆炸。
五、反思与建议
(一)建议措施
1、严格控制进罐油品的硫含量,从源头上消除事故隐患。
加强工艺管理,以原油评价作为指导,制定优化加工方案,对原料的硫含量进行控制,控制硫腐蚀。
2、加强含硫油品内浮顶储罐的防腐,采用涂料保护、渗铝、化学镀、阴极保护等技术措施防止硫腐蚀。
3、加强油罐腐蚀监控,定期进行清罐检查,定期清理罐内形成的硫化亚铁,减少自燃的几率。
4、加强对内