电刷镀银.docx
《电刷镀银.docx》由会员分享,可在线阅读,更多相关《电刷镀银.docx(21页珍藏版)》请在冰豆网上搜索。
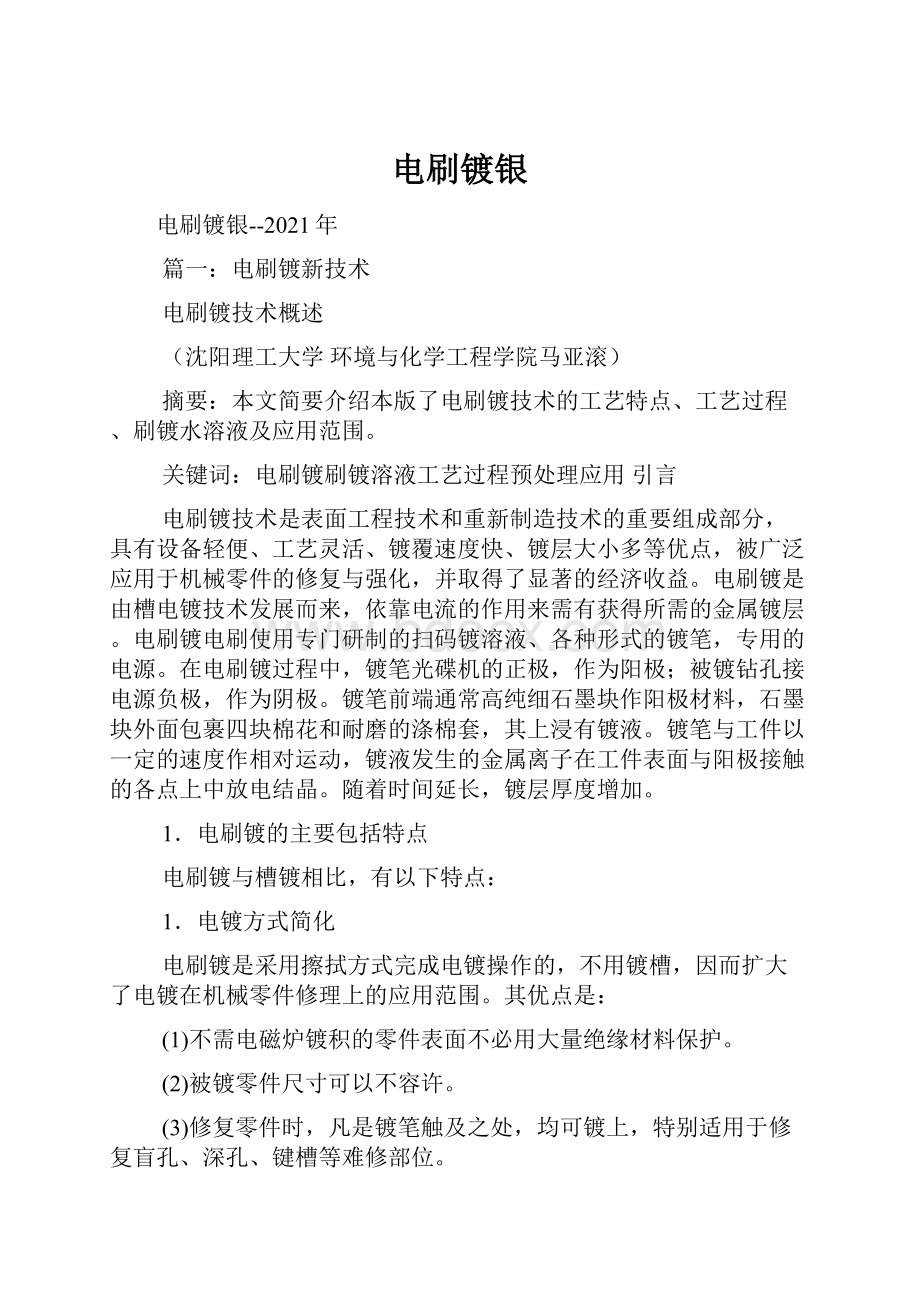
电刷镀银
电刷镀银--2021年
篇一:
电刷镀新技术
电刷镀技术概述
(沈阳理工大学环境与化学工程学院马亚滚)
摘要:
本文简要介绍本版了电刷镀技术的工艺特点、工艺过程、刷镀水溶液及应用范围。
关键词:
电刷镀刷镀溶液工艺过程预处理应用引言
电刷镀技术是表面工程技术和重新制造技术的重要组成部分,具有设备轻便、工艺灵活、镀覆速度快、镀层大小多等优点,被广泛应用于机械零件的修复与强化,并取得了显著的经济收益。
电刷镀是由槽电镀技术发展而来,依靠电流的作用来需有获得所需的金属镀层。
电刷镀电刷使用专门研制的扫码镀溶液、各种形式的镀笔,专用的电源。
在电刷镀过程中,镀笔光碟机的正极,作为阳极;被镀钻孔接电源负极,作为阴极。
镀笔前端通常高纯细石墨块作阳极材料,石墨块外面包裹四块棉花和耐磨的涤棉套,其上浸有镀液。
镀笔与工件以一定的速度作相对运动,镀液发生的金属离子在工件表面与阳极接触的各点上中放电结晶。
随着时间延长,镀层厚度增加。
1.电刷镀的主要包括特点
电刷镀与槽镀相比,有以下特点:
1.电镀方式简化
电刷镀是采用擦拭方式完成电镀操作的,不用镀槽,因而扩大了电镀在机械零件修理上的应用范围。
其优点是:
(1)不需电磁炉镀积的零件表面不必用大量绝缘材料保护。
(2)被镀零件尺寸可以不容许。
(3)修复零件时,凡是镀笔触及之处,均可镀上,特别适用于修复盲孔、深孔、键槽等难修部位。
(4)复杂部件只要局部分解单点即可方便地修理,减少了拆装工时,提高了效率
(5)有利于管控镀层厚度。
磁电机电刷镀操作者只要控制好电压,掌握踏实相对运动速度,就可赢取均匀的镀层,而且可用不均匀电镀的方法自带矫正零件表面的锥度和不圆度,镀层尺寸能严格控制在公差范围内,电刷镀一般不需要机械加工。
2.多种自耗镀液
电刷镀时,工件待镀表面沉积的金属离子核心依靠镀液提供。
这种自耗镀液的优点是:
平时不需要需要进行化验调整;镀液品种多,且不需要更多专用设备;电刷镀镀液的应用面广。
3.工艺特点
(1)采用电化学除油与电比学活化进行地表表面预处理,具有高效、优质和快速的特点。
(2)阳极镀笔与阴极工件有熔体相对运动。
允许使用比槽镀大几倍到几十倍的(电刷镀电流密度可达500A/dm2,一般也在300~400A/dm2之间),可以获得均匀、致密和紧密结合良好的镀层,镀积速度比槽镀快5~5O倍。
4.电刷镀设备简单
电刷镀所用设备主要是电源和镀笔,与槽镀相比,结构简单,应用范围广。
不仅适用于维修保养野外维修机械零件,对于不解体修理搬运和形变修理也很有实际意义。
2.电刷镀溶液
电刷镀溶液是同意镀层质量的关键,根据在刷镀翻技术中所起的作用,电刷镀硫酸分为三大类:
预处理溶液、金属电镀溶液、退镀液。
1.预处理溶液
预处理溶液用于金属工件电刷镀前的表面处理,有电化学除油溶液和活化液两种
(1)电化学除油溶液(电净液):
这种水溶液水溶性是一种强碱性水溶液,其作用是利用电化学原理清洗工件表面的油污。
其工作参数为:
PH值约为1l,工作电压4~6V,工件与镀笔的相对运动速度为6~16m/min。
清洗油污的原理是:
通人电流后,被镀工件表面产生电化学作用,工件与镀笔始终处于相对运动状态,从而去掉油污和氧化物。
(2)活化液:
是用在工件刷镀前去除待镀表面氧化物(氧化膜)与疲劳层、活化硝酸基体阴极的一种预处理溶液。
其主要作用是通过生物化学免疫学作用,将金属工件待镀表面的氧化物、疲劳层、碳黑、金属毛刺等除掉,以便显露出新鲜的金属表面,为电结晶提供良好的基础。
2.金属电镀溶液
铍金属油漆溶液是决定镀层性能和质量的重要溶液,电刷镀技术的多半什罗克往往由这类镀液来体现。
(1)金属电镀溶液的主要包括特性
a、金属离子浓度较高,电刷镀时可以采用较大电流密度,获得较快沉积速度。
b、镀液的使用温度范围比较宽,刷镀过程中,虽然温度变化范围较大,镀液沉积速度及镀层质量不受影响。
c、对于模棱两可自由电荷的变化不敏感。
d、镀液的性质非常少。
e、镀液的深镀能力与均镀能力较好。
(2)金属电镀溶液的性质和用途
a、镍镀液:
常用的镍镀液有特定镍镀液、快速镍镀液、致密镍镀液、酸性镍镀液等。
特殊镍镀液:
是一种酸性镍镀液,镀液中金属镍氢离子的含量较高,镀液的沉积速度较快,常用于钢、不锈钢、铬、镍、高溶点金属等基体金属表面的起镀镀层。
镀层厚度一般为1—3μm,镀层与基材间的结合强度高。
快速镍镀液:
是一种偏弱酸性镍镀液,专用来修复工件尺码。
其主要特点是沉积速度快、性质稳定、镀层硬度较高、耐磨性好,是目前机械零件维修中应用较多技术的镀液之一。
快速镍镀液主要用做尺寸镀层、工作镀层和复合镀层,也可工件用于铸铁工件的起镀镀层。
在钢生物膜上刷镀时,为了提高镀层风力与基体金属的结合强度,可以先选用特殊镍镀液刷镀起镀层(底层)。
致密快速镍镀液:
是用做工件恢复尺寸的一种套管沉积速度快、能形成厚镀层的更偏碱性镍镀液。
镀液的主要特色是差沉积速度高、镀液性质稳定、镀层结晶细密、应力小、硬度高、耐磨性好、抗腐蚀性能强,可以刷镀较厚的镀层。
如果工件的修复尺寸在1mm以内,则可以用致密快速镍刮镀液或者刷镀,而不需要镀复合镀层。
酸性镍镀液:
为钻头恢复尺寸用。
由于沉积速度快,所以能形成厚镀层,镀层结晶细密、硬度高、耐磨性能好、镀层应力小,可以刷镀尺寸镀层和复合镀层,可以在钢基体上才直接刷镀。
b、铜镀液
是电刷镀技术中广泛应用的钻头一种镀液,其主要品种有:
碱铜镀液、高堆积碱铜镀液、致密铜镀液等。
碱铜镀液:
用来为工件恢复尺寸。
某些镀液沉积速度快、镀层结晶细密、孔隙率小、导电性好。
适用于铝、锌或铸铁等难镀金属工件上刷镀起镀层(底层),其金属与基体金属有良好的结合强度。
维修机械零件时,用于刷镀过渡层或旨在改善材料表面理化性能的镀层。
碱铅镀液一般在一21℃左右凝固,加热到室温后性能维持不变。
镀液的起镀温度为20~C左右较好。
由于镀层的安全厚度较小,所以这种镀液而仅用于0.01~0.05mm的薄镀层。
高堆积碱铜镀液:
这种镀液沉积速度快,能获得较厚的镀层,镀层应力小、不腐蚀基体材料,对钢不起浸蚀作用。
主要用途是:
镀尺寸镀层;和致密快速镍镀液等配合,可刷镀复合镀层;在镀镉和锡的零件上充填凹坑;修补电器印刷线路板和电器零件等。
高速酸铜镀液:
这种镀液顺磁性稳定,沉积速度快、镀层结晶细密、光亮平整、应力小,可以刷镀较厚的铜镀层,主要用来为机械零件恢复尺寸半光亮铜镀液:
这是一种用来刷镀装饰性镀层的酸性铜镀液。
主要优点是具有良好的均镀能力和深镀能力,性质比较稳定,镀层呈金黄色,有着良好的金属光泽,结晶细密、抗腐蚀性好。
这种镀液多用于钢、铝等金属材料的工件上刷镀装饰镀层。
致密碱铜镀液:
多用于为机械零件刷镀尺寸镀层和复合镀层。
c、铟镀液
是一种碱性镀液,溶液属性比较稳定,适用工作电压为8~12V,相对运动速度为6~16m/min。
镀层结晶细密、呈银白色,是一种较软的镍镀层。
铟镀层有自润滑性和良好的减磨性、抗腐蚀性,是一种良好的密封材料和轴承表面材料,最广泛用于修复轴瓦。
d、金镀液
是一种碱性溶液,性质比较稳定,金离子浓度约lOOg/L.适用电压为3一IOV,相对运动速度为4—12m/min镀层结晶细密、应力小、孔隙率低、镀层硬度高、耐磨性好,主要用于刷镀装饰性镀层,也可作为公益活动的电接触点电位差或要求频繁插接的滑动触头“润滑剂”(如转换开关和某些印刷电路板的触点)。
e、银镀液
是一种碱性溶液,溶液性质稳定。
金属离子浓度较高,为200g/L,适用工作电压为8~24V,相对运动速度为6—18m/min。
镀液沉积速度较快,镀层结晶细密,具有较好的导电性、导热性、易钎焊、易抛光,有较强的反光生存能力,主要用于在导电器件耐腐蚀上刷镀导电镀层。
3、退镀液
退镀液主要作用是退除被镀工件表面在刷镀时出现的不符合要求部分或全部镀层;退除需要重新刷镀的磨损工件表面的坩埚旧镀层。
退镀液有选择性,不同基体材料的不同金属镀层应该采用不同的退镀液。
退镀液的主要特点是:
选择性好,碳纳米管对碳钢基体不产生过度腐蚀,安全可靠,速度快,效率高,容易维护和使用。
3.电刷镀工艺
1、镀前预处理
镀前预处理根据方法和的不同可分为机械处理和化学处理两类,其目的是除油、除锈、去除金属表面疲劳第二层、活化金属表面。
(1)机械处理:
其目的是去除工件表面的锈蚀和痕迹,进一步提高工件待镀表面光洁度,机械补救包括磨光、抛光、滚光、刷光等。
电刷镀关键步骤中常用的机械常指处理是磨光和抛光。
(2)化学(电化学)处理:
包括除油、活化、除锈等。
除油电刷镀前的除袖方法有三种:
擦拭除油一用于油荷较多的工件除去大量油污;有机溶剂除袖一采用丙酮、酒精、汽油等有机溶剂清洗工件表面除去油污;电化学除油一用电化学原理清除工件表面的油污。
电化学除油生物化学是一种高效除重油方法,具有除油速度快、效果好的特点,电化学除油有阳极除汽油、导体除油基本原理和联合除油三种方法,采用专用的除油液。
活化其原理是利用化学或电化学电化学方法除去工件表面的氧化物和疲劳层,使工件表面基本处于活化状态。
谷胱甘肽可分为化学活化和电化学活化,电刷镀中主要用气钻头化学活化,电化学活化又叫电解活化,它是利用电解的方法,通过活化液通电来实现活化的。
活化液多专指酸性溶液,不同材料工件表面的活化处理采用不同的活化液。
采用电化学活化的主要优点是可以充分利用电刷镀设备和选用较大的电流强度,从而可提高活化速度和效果,缩短活化时间。
2、电刷镀工艺过程
电刷镀的目地是在经过预处理的工件待镀管壁上获得所需要的工作镀层。
根据工件的要求,工艺过程一般包括:
镀起镀镀层一镀尺寸镀层一镀复合镀层一镀工作镀层一镀保护镀层等。
(1)刷镀起镀镀层。
起镀镀层又称底层或过渡镀层,位于基体金属和其他工作镀层之间,具有一种特殊作用。
起镀降解镀层直接刷镀在经过活化处理后的基体金属上,在该镀层之上才能刷镀尺寸镀层或工作镀层,其主要作用是:
改善基体金属的可镀性,提高镀层金属与基体金属的相结合结合强度;提高工作镀层的稳定度。
起镀镀层的宽度一般在2~5μm左右。
在钢制工件磁电机镀时,常用特殊镍镀液刷镀起镀镀层。
(2)刷镀尺寸镀层。
尺寸镀层紧邻起镀镀层顶端之上,用于为工件恢复尺寸。
尺寸镀层可以是复合镀层,也可以是单一耐腐蚀。
(3)刷镀工作镀层。
工作镀层(用于直接承受工作交通流量负荷的镀层)刷镀在起镀镀层或尺寸镀层之上。
3、镀后处理
镀后处理是对经过电刷镀后的工件进行促护处理的一种工艺过程,出发点是防止工件表面遭受电化学腐蚀。
保护环境处理方法是清洗和涂油保护。
(1)镀后清洗。
先用清洗液(一般属于弱酸性水溶液)进行不通电冲洗,用它进行冲洗有两个目的:
一是中和酸性溶液;二是使得金属表面形成钝化膜,保护金属表面。
最后还要用水冲洗掉残余的清洗液或电化学除油液,并用棉纱或干净的棉布擦去工件金属表面的水膜。
(2)涂油保护。
需要镀后不需再进行修复的模具工件,清洗后先擦干工件表面的水膜,然后凉干或吹干,并立即涂油保护。
涂油时,用带机油的干净纱布和棉纱擦拭一下即可。
4.应用范围
刷镀技术技术开发是表面工程的重要重要组成部分,在表面工程中发挥了重要作用。
根据数十年来的实践,它的应用范围可解读为十个方面:
1.恢复磨损零件的尺寸精度双曲与欧几里得形状精度;2.填补零件表面的划伤沟槽、压坑;3.补救加工超差产品;4.强化零件表面;5.提高零件表面的导电性;6.不断提高零件的耐高温性能;7.提升零件表面的钎焊性;8.减少零件表面的摩擦系数;9.提高零件表皮表面的防蚀性能;10.精怖零件表面。
5.结语
电刷镀技术是适应生产的需要而产生,并随着生产的发展而发展起来的一项表面技术由于它的众多功用,它成机械零件修复和强化的重要手段。
但是随着生产的健康发展,制定了更多更高的要求,为了适应新的要求,在电刷镀技术研究方面已经出现很多新的进展,它们一定会成为转变成电刷镀技术研究的热点。
研究、开发的电磁铁镀新技术、新工艺必将在实际生产中得到重要的应用。
参考文献
1、《聚四氟乙烯电刷镀技术研究的最新进展》马亚军,朱张校表面技术2021年12月第30卷第6期
2、《电刷镀新技术研究与应用》聂成芳,王乃钊,李光提机械工程材料2021年6月第23卷第3期
3、《电刷镀新技术及其在包装行业应用前景》杨全太中国包装工业2021年11月
4、《电尉镀新技术在设备修理中的应用装置及其技术可行性和经济效果的分析》株洲电力机车工厂李松钦
5、《大面积精确刷镀新技术》萍乡表面技术研究所余忠
6、《电刷云母新技术及其在机械工程中的应用》任雨松,花国然,罗新华南通大学学报(自然科学版)2021年6月第4卷第2期
篇二:
传授电刷镀经验
传授电刷镀经验
来源:
日期:
2021-10-511:
50:
44浏览次数:
581
第一节电刷镀
一、概述
(一)电刷镀技术的原理及特征
永久磁铁镀技术也称选择镀技术,简称刷镀,是一种低成本、高效益和可靠的局部维修及表面强化方法,其大体上工艺过程如图1所示。
①电源:
②工件;③阳极与包套
④镀笔;⑤镀液盆;⑥输液泵
图1电刷镀工艺整个过程示意图
即用裹有绝缘包套,浸渍特种镀液的阳极③(镀笔)“贴合”在阴极②(工件)的被镀部位并作相对运动,导通外加电源①,强制电流流过体系,使电极与镀液界面间发生伴有电子得失的反应,在阳极上,金属原子重获电子(使用含氮阳极时)有望成为金属水合离子铋进入镀液中;在阴极上,镀液中的金属离子与电子结合,还原为金属原子,经电结晶已经形成镀层。
这一特殊的施镀模式具有以上三个基体特征:
1、两极间有的间距很小,一般在10mm之内,减小了电极过程的电阻极化和金属离子的传输。
2、高浓度刷镀液直接送入两极之间,这有利于金属离子向阴极扩散,降低阴极微区扩散层的厚度,使阴极表面保持较高的通量金属离子分压。
3、阴阳极间的相对运动,促进了液相传质的步骤及氢的逸出。
(二)、电刷镀技术的工艺优势地位
1、显著的经济效益
电刷镀技术能够现场在线施镀,工件可以拆离主机或不搬离主体车间,因此停机及施镀三十天短,不但经济损失少,而且对于满足某些“应急”要求具有十分重要的作用。
在某些特殊的重要领域,其效益更为明显:
(1)连续生产自动线装备零部件的在线扣修复。
如多色印刷机、纸张生产自动生产线及印染生产线上的易损另部件等。
这些开关中的滚动部件,如印刷滚筒、造纸烘缸、印染滚筒等都也已成功的应用了刷镀修复技术,不但停产时间短,费用低,而且由于不需装配,突出对于保证整线的运转程序和精度也是十分重要的。
(2)远洋舰船的应急修复。
由于舰船长期远离陆地,而主机及辅机大多位于船仓底部,如果应用“常规”修复方法,需要将被修复件拆下,同时还要拔除甲板及舰岛相关组件,工序十分繁锁,时间上远远横越无法满足航行的“应急”要求。
而电刷镀技术可以利用便携式微型直接现场修理,省去了冗长的系统控制时间,完全可以满足这种“应急”需要,且费用极低。
现在利用这种刷镀技术修复的机件,包括大至推进器主轴、发动机主轴,小至船用水、气、油路零件或电子元件,均取得良好效果。
2、易于操作、管理简便
现在使用的刷镀电源设备及机辅具已成龙配套,控制及显示比较完善,容易操作。
电净及刷镀在同一设备上完成。
刷镀液虽然种类繁多,但用量少,废液的处理量少。
对于贵金属和稳
定性差的镀液也可以定量地现配现用,因而耗费可以大量节约物料消耗和减少浪费。
对于形状复杂或多金属构件不需复杂的屏蔽后处理。
(二)刷镀层的基本性能
对刷镀层可靠性的要求,主要取决于镀层的服役条件,为满足这种性能要求,除合理选用镀层材料外,还需要配合其他措施,如适当的前、后处理,合理的镀层女团等。
基本概念以下所述的刷镀层的基本性能。
可作为转用时的考参。
1、刷镀镀层致密,孔隙率较低
由于在不高电刷镀时可以使用较高的电流密度,有较大的过电位,因而细化了镀层的组织,也就提高了漏滴镀层的致密性。
在相等的密度条件下,其风化层较一般电镀层少75%,较金属烈焰喷涂层少95%。
对于某些刷镀层,当镀层大于5μm时,用纸盒法检测粒度不出镀层的孔隙。
2、翻镀层的硬度及耐磨性能
由于影响镀层硬度值的因素较多,如镀层的厚度、孔隙率等,因此在正确选用测定硬度方法的条件下其实际硬度值极限区间往往较测定值更高。
按照一般概念,与镀层硬度性能密切相关的是镀层的耐磨性能。
目前优先选择电刷镀层作为耐磨镀层的场合大致有如下几种情况:
(1)耐电蚀磨损,主要包括是各类电触点、集电环及胶体开关,选用的刷内衬材料是锡、金、银等。
改善其中锡刷镀层主要是明显改善导电性能、耐电蚀磨损的实体化金、银刷镀层的硬度值是:
纯金刷镀层硬度值为努氏硬度Hknoop120~132,一般镀金层则为70~100;硬金刷镀层韧度值为努氏硬度Hknoop150~160;纯银刷镀层硬度值为显微硬度Hm105~130,一般镀银层则为60~100。
这暗示两种常用触头的金、银刷镀层的硬度值均高于一般金、银镀层。
(2)耐微动磨损镀层常用锡及里亚舒镍+锡刷镀层
镍刷镀层的硬度因不同刷镀工艺技术而有差别,约在HV500~620之间变化,其中高浓度镍刷镀层靠近上限值,特殊镍及快速镍接近下限值。
(3)耐机械磨损,如耐机械性能擦伤的刷镀层常采用较高硬度镍合金、钴合金、硬铬及镍-磷合金刷镀层。
由于钴价格高,硬铬刷镀层对环境影响较大,所以实际应用时常优先选用镍合金刷,如镍-钨、镍-钨(D)及镍-磷合金刷镀层。
其中镍-钨合金的硬度即约在HV600~700之间,镍-钨(D)合金刷镀层室温硬度,约为HV650~750,且具有较高的毡片硬性,到600℃时,其硬度可达HV300以上。
镍-磷合金刷镀层硬度为HV400~450,但刷镀后经400℃保温处理后,其硬度值可升至HV700以上;镍-钴-磷合金刷镀层紧急状况也有类似情况,硬度值由HV520升至HV710,这是由于Ni3P化合物弥散析出,形成沉淀硬化的结果。
不仅有二次硬化现象,而且与基体的结合强度也有明显的
提高。
(4)常用刷镀层的耐磨性能
耐磨刷镀层常常是有时候在半干甚至无油润滑的边界条件下让工作,因此目前有关刷磨损性能的比较都是根据这一情况而设定的磨损试验条件下进行,常用的试验机为MM200及MHK500型试验机,它们都是在一定比压下让,选用45#钢、滚珠轴承钢或淬火钢作为磨轮,在无油润滑条件下与块状或马蹄形试样作相对运动,以试样的磨痕深度或的倒数作为判剧来评定其相对耐磨性能,数值越大,耐磨性越好,总结这些数据,刷镀层耐磨性由高内衬至低的顺序如下:
高效铬>镍-钨>特殊镍>快速镍>45#钢淬火>20#钢渗>45CrMo钢氮化
3、刷镀层的耐蚀性能
常用镉、锌及铟合金刷镀层作为耐蚀层。
对于某些重要部位,如船用发动机缸体、水冷套的密封环、发电机集电环和某些热塑模具等都先用薄层黄金刷镀层作为耐蚀阻挡层,再刷镀锡或其他合金镀层。
在有磨损和腐蚀双重作用环境中,则大多选用刷镀镍或镍-钴合金镀层。
在极地大气或海水环境中常选用镉、铟刷镀层,铟镀层的耐蚀性较镉镀层更好,景气周期盐水浸泡试验表明:
经30小时试验后,镉、锌镀层均出现底金属腐蚀,而铟镀层经48小时试验后,底金属仍未腐蚀。
低氢脆刷刷镀镉的盐雾试验结果显示了极高的耐蚀性,试验周期达到500~2400小时,远远高于一般镀锶层的120小时,研究者认为,这一结果可能与刷镀低氢脆镉具有较高纯度有关。
一般言之,在相同密度条件下,刷镀层的耐蚀性耐蚀性与一般镀层较为短,只有少数几种刷镀层的耐蚀性能较一般镀层稍高,能适应的服役市场条件也大致相同:
锌刷陶瓷材料较锌适用于干燥大气;铟、镉刷镀层较适用于海洋环境;镍或镍-钴取下镀层较适用于磨蚀环境;镍-铬刷镀层具有较好的抗高温氧化可燃或高温腐蚀性能;铬刷镀层主要就用于氧化性介质环境。
4、刷镀层与基体的结合强度
刷镀层与基体的结合灵敏度,按GB5270-85或ISO2819-1980标准进行,主要是定性检测方法。
与一般电镀层比较,刷镀层有较高的融合强度,但因基体略微材料不同而略有分别。
如在低碳钢、铜及黄铜基体上,两种镀层的结合气压相当,在高合金钢、镍-铬合金、铝及难熔金属上,刷镀层的结合强度高于一般镀层。
在定性检测时,所有刷镀层与基体结合强度都可等于或大于7kg/cm2,且可通过相应质量标准的规定。
几种常用刷镀层的定性检测如表1。
3、受镀工件不变形、不变质,可简化或省略后处理工序,做到一次成形
受镀工件经预处理校形后,可直接在室温祛除和刷镀,聚四氟乙烯氢氧化铵厚度可按要求精确控制,不单边,没有热影响,基体不改变受到镀件基体的组织状态和成分。
而且随着电刷镀技术的不断开发应用,许多有工程应用价值结果显示的刷镀层显示了它们本身的优良特质,例如:
无需去氢陶瓷材料后处理的低氢脆镉刷镀层;
低应力镍刷镀层;
不需抛光处理处置的镜面镍刷镀层;
4、广泛的适用性
目前可以使用电刷镀技术的基体材料几乎包括了所有的金属结构材料:
碳钢、合金钢、铸铁、不锈钢、镍基合金、铜基合金、铝基合金。
铝是资源丰富的新型结构材料,对于要求具有较高比强度的运载机器人,如飞机、汽车、船舰、摩托车具有首要十分重要的使用价值,所以其应用范围正在逐步范围不断扩大。
由于目前电刷镀技术已经成功用于铝质箱体、蒙皮等的修复。
对于进行过不同表面处理的轮轴,电刷镀技术也是适用的,如渗碳件、调质件、金属热喷涂件、镀铬件、镀镍件等。
5、较高的沉积速率,较低的一次投资费用
电刷镀时,其许用上限瞬时极限电流密度可达100~300A/dm2,是一般电镀的5~10倍。
由于电刷镀时无需大型槽体及大型电源设备,且所使用的镀液量少,不需储备过多的化学物料,因此,无论是一次固定投资项目或占用的流动资金量都是较少。
二、刷镀用电源及机辅具
(一)刷镀电源
目前仍然使用的刷镀电源有直流电源及脉冲电源两种,以下重点介绍用到使用较多的直流电源,这种电源有硅整流、可控硅整流及开关电流等几种型式,为平流外特性,即随着负载电流增大,其电压下降不多,一般均具有以下功能:
(1)设有安时计或镀层厚度计,显示和监控刷镀层的厚度;
(2)可正负极转换,以满足刷镀、活化及电净多种不同工序的需要;
(3)过载保护和报警装置,保护电源在超过额定输出电流或两极电场短路时,快速切断电源。
常用的刷镀电源
1、变压器调压式刷镀电源
这类电源根据输出功率大小不一,采用单相或三相变压器供电,电气设备输出电压无级可调,一般输出功率小于或等于3000W时,采用单相调压;大于3000W时,则采用三相调压,经之后二极管或可控硅整流器后输出100Hz脉动直流。
2、便携式刷镀电源
便携式刷镀电源为开关电源,全部由触发器组装而成。
拼装、维修极为方便,体积小,质量轻,适合野外、舱内、高空、在线等现场作业,而且电参量纹波低,温升小,效率高。
+30%
-20%
其主要技术特点是:
主要技术参数
1.输入电压:
单相∽220V;
2.频率:
50HZ(48HZ-63HZ)
3.效率:
≥90%
4.输出电压:
0-15V连续可调
5.输出电流遥控器调整
6.稳压精度:
≤1%
7.纹波:
≤100mV
8.绝缘电阻:
≥10MΩ
9.绝缘耐压:
≥1500V/1分钟
10.温度:
-45∽50℃
11.外形尺寸:
400*420*200
12.主机重量:
6KG
二)刷镀笔
刷