热处理工法.docx
《热处理工法.docx》由会员分享,可在线阅读,更多相关《热处理工法.docx(15页珍藏版)》请在冰豆网上搜索。
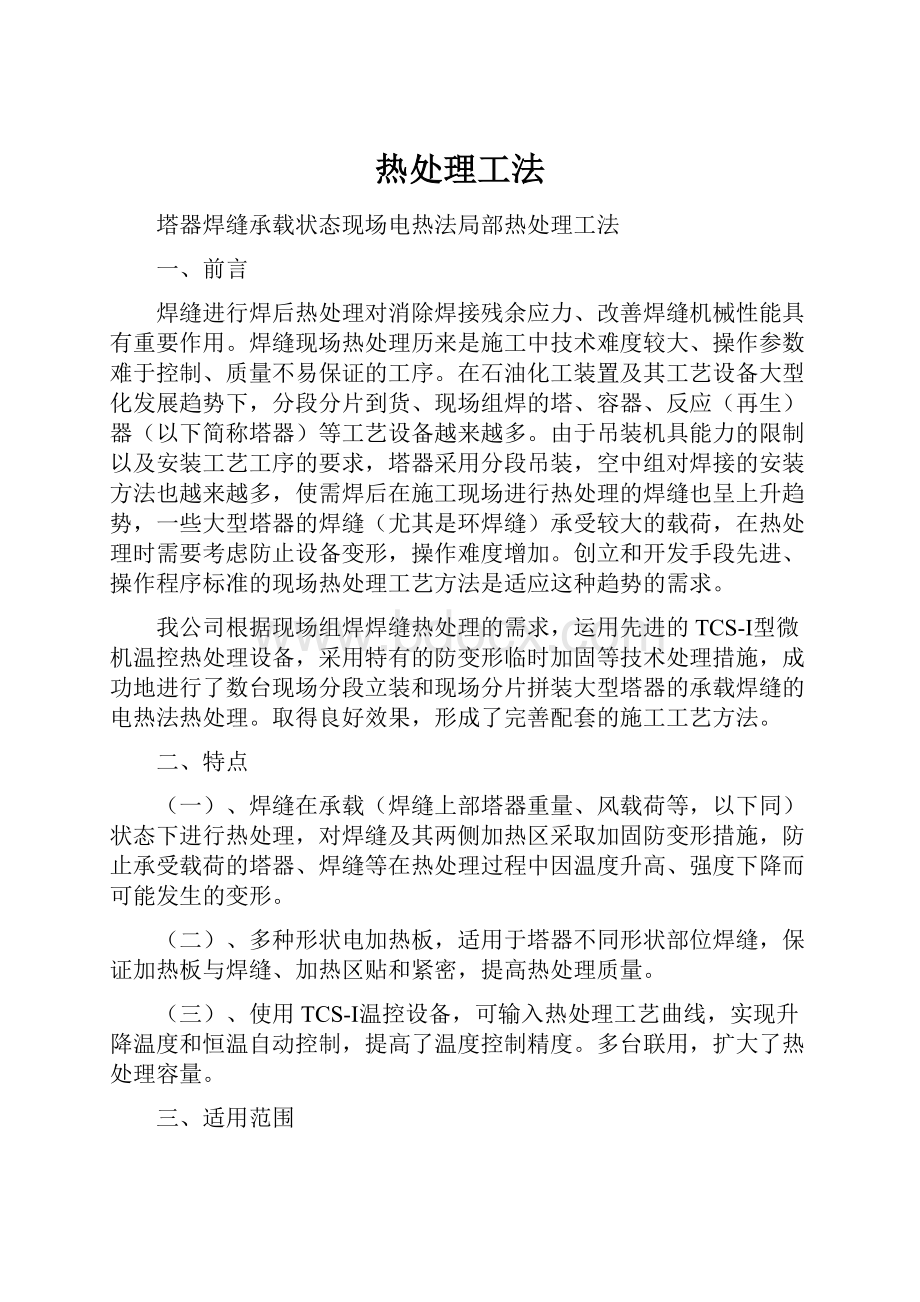
热处理工法
塔器焊缝承载状态现场电热法局部热处理工法
一、前言
焊缝进行焊后热处理对消除焊接残余应力、改善焊缝机械性能具有重要作用。
焊缝现场热处理历来是施工中技术难度较大、操作参数难于控制、质量不易保证的工序。
在石油化工装置及其工艺设备大型化发展趋势下,分段分片到货、现场组焊的塔、容器、反应(再生)器(以下简称塔器)等工艺设备越来越多。
由于吊装机具能力的限制以及安装工艺工序的要求,塔器采用分段吊装,空中组对焊接的安装方法也越来越多,使需焊后在施工现场进行热处理的焊缝也呈上升趋势,一些大型塔器的焊缝(尤其是环焊缝)承受较大的载荷,在热处理时需要考虑防止设备变形,操作难度增加。
创立和开发手段先进、操作程序标准的现场热处理工艺方法是适应这种趋势的需求。
我公司根据现场组焊焊缝热处理的需求,运用先进的TCS-Ⅰ型微机温控热处理设备,采用特有的防变形临时加固等技术处理措施,成功地进行了数台现场分段立装和现场分片拼装大型塔器的承载焊缝的电热法热处理。
取得良好效果,形成了完善配套的施工工艺方法。
二、特点
(一)、焊缝在承载(焊缝上部塔器重量、风载荷等,以下同)状态下进行热处理,对焊缝及其两侧加热区采取加固防变形措施,防止承受载荷的塔器、焊缝等在热处理过程中因温度升高、强度下降而可能发生的变形。
(二)、多种形状电加热板,适用于塔器不同形状部位焊缝,保证加热板与焊缝、加热区贴和紧密,提高热处理质量。
(三)、使用TCS-Ⅰ温控设备,可输入热处理工艺曲线,实现升降温度和恒温自动控制,提高了温度控制精度。
多台联用,扩大了热处理容量。
三、适用范围
该工法适用于分段分片到货现场组焊的塔器的焊缝现场热处理,对于采用分段立装焊接方法的位于高空的在承载状态下的环焊缝的热处理尤为适用。
四、工艺原理
(一)、加固
焊缝在承载状态下进行热处理过程中,焊缝及其两侧加热区筒体的许用应力随温度升高而降低,强度亦有所下降。
所以需要在热处理焊缝两侧的适当部位采取加固措施,由加固结构来支撑由焊缝所承受的上部塔器结构的载荷,防止在承受外载荷作用的条件下,焊缝及其加热区由于强度降低,在热处理过程中可能发生的变形。
1、加固形式
(1)、承重加固
蝶簧承重加固方式:
在焊缝两侧适当部位的筒体上焊接支承座,利用蝶簧箱作为弹簧支撑。
在热处理前对蝶簧进行预压缩,压缩值综合考虑塔体和焊缝达到热处理最高温度时的计算热伸长值与蝶簧额定承重值时的预压缩值确定,使蝶簧在塔器受热膨胀、蝶簧伸长后仍具有需要的承重能力,以满足在塔体热膨胀后加固支撑的承重需要。
其结构形式见图1。
蝶簧承重加固方式是一种无拘束承重方式,仅适用于塔器高度或安装标高低,自身稳固性强,风载影响小的场合,或与其它加固形式混合使用。
图1承重加固示意图
支撑管承重加固方式:
在焊缝两侧适当部位的筒体上焊接支承座,支承座中间设支撑管,支撑管两端与上下支承座焊接,以其来承受焊缝上部的塔器重量等载荷,防止变形。
其结构形式见图2。
支撑管承重加固方式为常用方式,可适用于塔器高度及安装标高高、自身有一定稳定性、风载影响较小的场合。
图2支撑管承重加固示意图
(2)、承重抗弯加固
对于受风载影响较大的塔器热处理时,需要在
(1)承重加固的基础上增加抗弯加固。
并使承重加固与抗弯加固配合使用,交叉布置,前者承重,后者可承受风载等形成的弯矩作用,防止弯曲变形。
抗弯加固的形式为:
支承座与支撑管承重加固方式相同,支座间用内外钢管套筒式焊接连接,(套入深度不小于全长1/3至1/2),在内、外套筒的径向分别开圆孔和长圆孔(上下方向),采用销轴限位。
本加固方式具有抗风载的作用。
热处理升、降温过程中,微松销轴螺栓,使内管随筒体膨胀上升(或下降);恒温(达到最高温度)时,把紧销轴螺栓。
由于内外钢管套筒的配合及销轴限位,可抵抗风载弯矩。
其结构形式见图3。
该加固形式与承重加固形式混合使用,适用于圆筒形立式塔器受风载影响的承载环焊缝热处理。
图3抗弯加固示意图
2、加固点数量及加固件强度
(1)、加固点数量的确定
加固点沿塔器周长均布。
其数量n由下式确定
n≥G/P
式中:
G——加固承载重量
P——每个加固点的承载重量
说明:
1.对于蝶簧承重加固,P为所选蝶簧设计承重重量;
2.对于支撑管承重加固和抗弯加固,根据承载重量,通过强度、稳定性计算,选择加固数量和支座、支撑管尺寸。
(2)、加固件强度校核:
加固件强度校核内容应包括:
1)、护板与塔器焊缝强度校核;
2)、护板与支承座间焊缝强度校核;
3)、支撑管强度与稳定性校核;
4)、风载荷下承重抗弯强度校核。
加固件强度校核应明确下列几点:
1)、强度校核时,假设重力及风力的作用完全由加固件承担;
2)、各加固件受力均匀一致;
3)、加固件各焊缝焊肉厚度按板厚计,焊缝系数取0.7;
4)、热处理时,采取措施以保证支承座处温度低于350℃;
5)、加固结构校核时,按350℃时钢材的许用应力[σ]进行;
6)、风载荷按7级风计。
(二)、加热、温控
按现场一次热处理工作量(或热处理焊缝总长度)计算电加热板的数量,来确定TCS-1型热处理设备的台数和连接方式,确定“路、点”布置方式。
一次热处理量大者,采用2台或多台联用。
按工艺要求向温控设备输入热处理工艺曲线,热处理运行后,由温控设备按输入工艺曲线自动跟踪、控温。
若超出设定的温度报警值范围,发出报警信号,可由人工进行调节。
五、工艺流程及操作要点
(一)、工艺流程
(二)、操作要点
1、加固
(1)、加固件预处理
对于进行整体热处理的塔器,按计算位置在设备热处理前,按加固设计位置安装、焊接护板(参见图1~3),并随设备同炉热处理。
(2)、加固件的选择及组焊
对分段立装焊接、位于高空的承载状态的环焊缝,根据待热处理焊缝所处环境(焊缝所在塔器部位、焊缝形状和承载情况)按4.1选择加固形式、加固位置及加固点数量。
在现场进行组对焊接。
其它处理:
大直径塔器、卧置热处理塔器环焊缝还需在焊缝两侧筒体内部加“米”字型支撑加固;
异形结构,如塔器大型斜插管连接焊缝热处理,作防斜插结构下沉引起筒体变形的刚性加固。
2、电加热板固定
(1)、电加热板的主要形式
常用电加热板有矩形形状的履带式、扇形和扇形中间可折式加热板,以及异形加热板等多种形式。
(2)、电加热板的选择
圆筒形塔器环焊缝及各种直线形纵焊缝:
选用矩形形状的履带式电加热板。
塔器锥体(过渡段或锥形封头)环焊缝:
选用扇形加热板;对于连接锥体与圆柱体的环焊缝选用扇形中间可折加热板。
其它异形焊缝如斜插管连接焊缝等,选用扇形加热板或特制其它异形加热板。
(3)、电加热板固定方法
立式圆筒形塔器环焊缝采用的履带式矩形加热板,用扁钢制作的L型挂钩固定,挂钩焊在塔器壁(或固定板)上,电热板逐块插入挂钩内,外部用铁丝绑扎,铁丝上作若干热膨胀补偿扣圈。
不能采用挂钩固定的其它情况,用保温钉绑扎铁丝固定。
3、安装热电偶
热电偶采用点焊于塔器壁内侧的带槽螺母、螺栓压紧固定。
热电偶测温点以隔3块电加热板布置一点为宜,测点最大间距为1800mm。
4、保温
用硅酸铝镁保温被或其它保温材料进行内外保温。
保温厚度100~150mm,保温宽度不小于500mm。
保温层采用在器壁(或加热板L型挂钩表面)焊接钉头绑扎铁丝固定。
铁丝绑扎以保温层贴紧加热板及塔器壁不松动,且压紧度以铁丝不陷入保温层为度。
5、设定并输入热处理工艺曲线
(1)、焊后热处理规范
塔器常用材料压力容器用碳素钢(如20R、16MnR),焊后热处理温度为600℃±20℃。
恒温最短时间(厚度δ≤50mm情况)δ/25小时,且不少于1/4小时,一般可为1.5~2小时。
(2)、输入并储存热处理工艺曲线
用TCS-I型温控设备人机对话操作程序输入工艺曲线并储存。
6、回路联接
(1)、热处理回路如图4所示
图4热处理回路
(2)、联接要求
用低压动力电缆将变压器与控制柜总电源端相连;
用接长导线将加热板与控制柜加热电源端子相连;
用补偿导线将热电偶与控制柜测温输入端子相连;
TCS-I设备多台联用时,根据设备台数选择动力变压器容量。
联接完毕,每组加热板均需试升温,确保热电偶与加热板一一对应。
7、热处理
进入TCS-I温控设备运行状态,控制程序自动按热处理工艺曲线升温、恒温及降温,并自动记录热处理温度。
运行中若出现意外值或报警,可暂停运行,实施补救措施。
检查加热回路、热电偶测温回路、保温、电加热板贴合等有无意外情况,排除故障后恢复运行。
8、硬度测定
根据规范要求确定测定点数量和测点位置。
测点硬度值满足设计要求(一般HB≤200)为合格;若超标不合格,必须重新热处理。
9、拆除防变形加固件
热处理完毕后拆除防变形加固件。
可采用气割方法进行,但应避免切割到母材。
切割后用砂轮磨平,并进行PT检查。
整体热处理塔器的预焊护板不切除。
六、机具设备及材料
主要机具设备及材料表 表一
序号
名称
型号及规格
数量
备注
1
微机温控柜
TCS-Ⅰ360KW
2台
2
履带式电加热板
380×620mm
10KW
72块
3
蝶簧箱
CZD90—19C
8个
4
电焊机
ZX5—400
1台
加固焊接及点焊保温钉、螺母等
5
磨光机
¢125mm
2台
6
热电偶
K型铠装式
24支
7
硬度仪
1台
8
K型补偿导线
KC2×1.0mm2
600m
9
接长导线(阻燃)
50mm224m长
144根
10
低压动力电缆
VV223×185+1×95mm2
200m
11
硅酸铝镁保温被
1000×500×60mm
50m2
12
扁铁
40×3mm
135m
制作L型加热板固定挂钩
13
螺栓/母
M10×20mm
24套
螺母开槽
14
铁丝
20#
150Kg
15
钉头
L=170mm
975个
16
钢板
δ18mm
27m2
垫板、支承座
17
无缝钢管20#
¢159×10mm
20m
支撑管、外管
18
无缝钢管20#
¢133×8mm
6m
内管
19
销轴
¢20
16个
注:
本表为热处理焊缝长度为45m所需数量
七、劳动组织
劳动力需求表 表二
序号
工种名称
人数
分工与职责
1
铆工
3
加固、固定电热板及保温棉
2
电焊工
2
加固焊接、固定电热板及热电偶
3
电工
3
连接电源、供电维护
4
仪表工
3
连接测温、加热回路、操作温控柜
5
架子工
6
防风放雨棚的架设
6
调度
1
综合协调热处理工作
7
技术人员
2
负责热处理技术工作
8
安全员
1
管理、检查热处理现场的安全
9
司机
1
值班
10
化验员
1
硬度测定
八、安全措施
(一)、对参加热处理工作的人员进行专门训练和安全教育。
(二)、热处理应尽量选择在风力较小天气的时间进行。
(三)、作业前进行全面检查,加固支撑牢固,电气设备工况良好。
(四)、热处理现场划定安全区,设置警戒线,非工作人员严禁入内。
(五)、脚手架绑设牢固,设置安全护栏或安全网,高空作业挂好安全带。
(六)、作业现场严格管理易燃物品,预防火灾。
并配置足够的消防器材和照明设备。
(七)、维护好现场用电设备,保护好电缆线,以防漏电。
(八)、配备值班车和值班电话,专职安全员巡回检查,及时发现隐患并处理事故。
九、质量要求
(一)、执行标准
执行以下标准,并应探讨使用其最新版本的可能性:
GB150—98《钢制压力容器》
JB/T4709—92《钢制压力容器焊接规程》
GBJ236—82《现场设备、工业管道焊接工程施工及验收规范》
(二)、主要质量指标
升温速度V1:
50℃/h≤V1≤5000/δ℃/h,
且V1≤200℃/h。
降温速度V2:
50℃/h≤V2≤6500/δ℃/h,
且V2≤260℃/h。
升温期间任意5000mm内温差不大于120℃。
保温期间最大温差不大于65℃。
(三)、质量保证措施
1、成立热处理领导小组,由项目技术负责人任组长,实行统一领导。
2、热处理前向热处理人员进行详细技术交底,交清质量要求,明确质量责任。
3、做好热处理期间天气预报预测,尽量选择好天气进行热处理。
热处理时做好挡风,防雨、雪措施。
4、加热板、保温层贴紧、严密。
5、热处理过程中实行全天候24小时监控。
6、热处理时统一指挥,协调行动,及时处理突发事故。
十、效益分析
(一)、采用TCS—I温控设备,提高了控温精度,减小温差,提高了热处理质量,热处理一次合格率达到100%。
(二)、开发塔器焊缝在承载状态下的局部热处理工艺,可实现大型塔器设备分段、分片出厂,现场立装组焊,对设备的拉运、吊装都有益,大大减少大型吊装、运输设备的使用台班,综合台班使用费降低20%以上。
(三)、采用电加热方法,比燃油、燃气加热效率高,并省去现场建筑退火炉等临时热处理设施,可降低热处理成本。
(四)、多台温控设备联合使用,提高了一次热处理容量即一次热处理焊缝长度。
并可同时处理一台塔器的不同高度的环焊缝及其它焊缝,减少处理次数,缩短工期。
(五)、减少空气污染,改善环境。
十一、应用实例
(一)、1998年5月,在大庆油田化工总厂180万吨/年ARGG(常压重油催化裂解)装置,脱吸塔(φ4000×54100×28mm、16MnR、三段)和稳定塔(φ4600×59250×28mm、16MnR、四段)2塔,分段立装组焊,共5道现场热处理环焊缝,其中焊缝最低标高21.48m;最高标高47.89m;受力最大的热处理焊缝最大承重近200吨。
采用支撑管承重加固,矩形履带加热板,运用一台TCS—I控温设备,分5次热处理,均做到一次成功。
其中升温阶段最大温差50℃,恒温时热处理温度最大误差10℃,最大温差18℃。
热处理后硬度测量值最高为HB196。
热处理工艺曲线如图5。
图5热处理工艺曲线
(二)、1998年8月,同上装置,再生器大过渡段,尺寸φ14300/φ10800×4973mm,壁厚48mm,材料20R,分片组焊成型(如图)后共3道环焊缝及所有纵焊缝累计208m焊缝现场热处理。
其中环焊缝B10最大承重79吨,采用蝶簧承重加固方式;环焊缝B9采用扇形加热板,环缝B8、B10采用扇形中间可折加热板,TCS—I型设备两台联用,分5次进行热处理,均做到一次成功。
其中升温阶段最大温差40℃,恒温阶段最大温差10℃。
图6再生器大过渡段组对成型外形图
(三)、1999年4月,同上装置,下部提升管Y型段(厚度δ=40mm,材质20R),焊缝长9m,最大承重14吨,再生器烧焦管底部斜插管接口(厚度δ=36、30mm,材质20R)焊缝总长88m,最大承重38吨,采用本工艺,斜管与主筒体刚性加固,扇形和异形加热板组合配置,TCS—I设备2台联用,分3次热处理,均一次成功。