金工实习4章压力加工.docx
《金工实习4章压力加工.docx》由会员分享,可在线阅读,更多相关《金工实习4章压力加工.docx(25页珍藏版)》请在冰豆网上搜索。
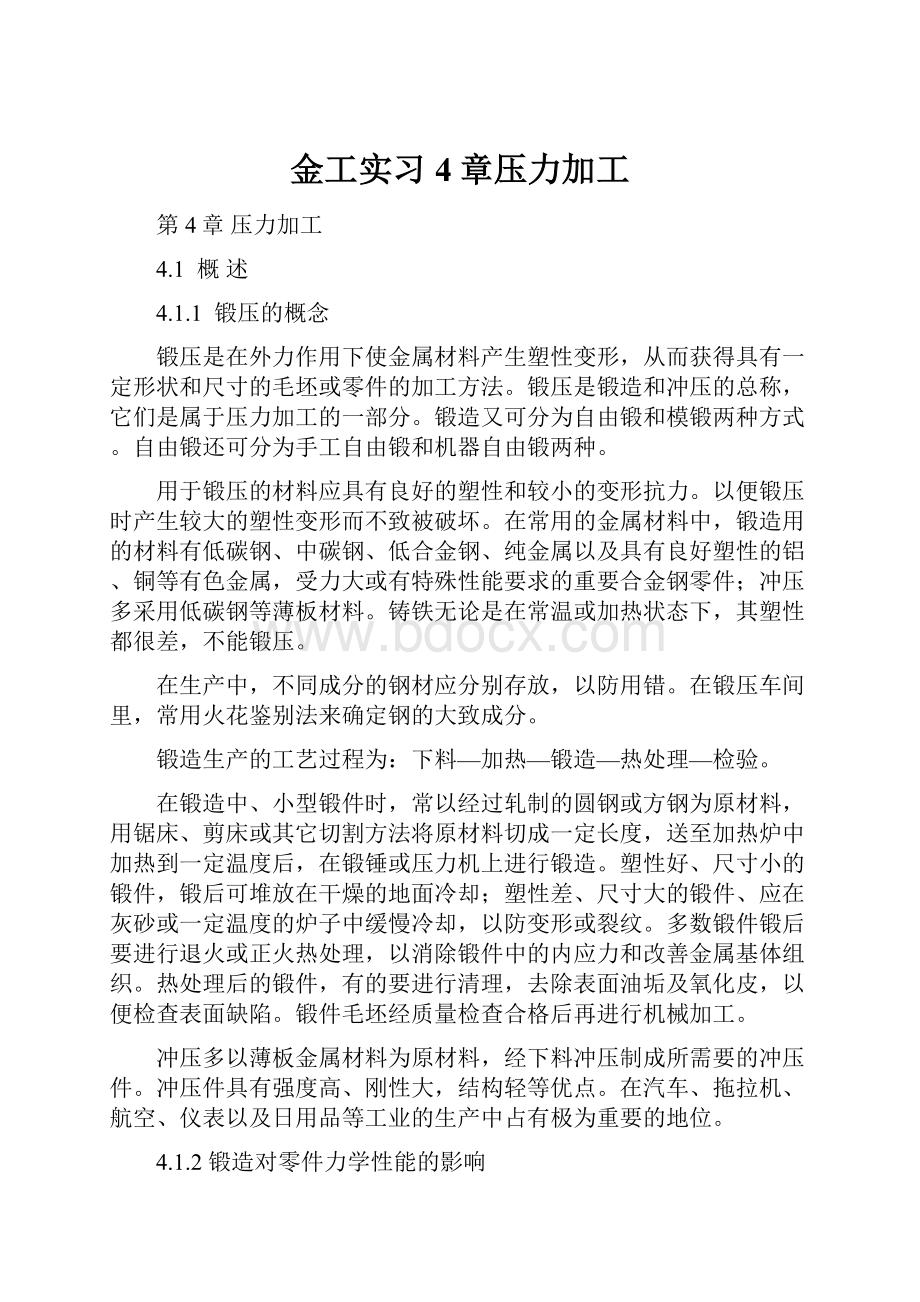
金工实习4章压力加工
第4章压力加工
4.1 概 述
4.1.1 锻压的概念
锻压是在外力作用下使金属材料产生塑性变形,从而获得具有一定形状和尺寸的毛坯或零件的加工方法。
锻压是锻造和冲压的总称,它们是属于压力加工的一部分。
锻造又可分为自由锻和模锻两种方式。
自由锻还可分为手工自由锻和机器自由锻两种。
用于锻压的材料应具有良好的塑性和较小的变形抗力。
以便锻压时产生较大的塑性变形而不致被破坏。
在常用的金属材料中,锻造用的材料有低碳钢、中碳钢、低合金钢、纯金属以及具有良好塑性的铝、铜等有色金属,受力大或有特殊性能要求的重要合金钢零件;冲压多采用低碳钢等薄板材料。
铸铁无论是在常温或加热状态下,其塑性都很差,不能锻压。
在生产中,不同成分的钢材应分别存放,以防用错。
在锻压车间里,常用火花鉴别法来确定钢的大致成分。
锻造生产的工艺过程为:
下料—加热—锻造—热处理—检验。
在锻造中、小型锻件时,常以经过轧制的圆钢或方钢为原材料,用锯床、剪床或其它切割方法将原材料切成一定长度,送至加热炉中加热到一定温度后,在锻锤或压力机上进行锻造。
塑性好、尺寸小的锻件,锻后可堆放在干燥的地面冷却;塑性差、尺寸大的锻件、应在灰砂或一定温度的炉子中缓慢冷却,以防变形或裂纹。
多数锻件锻后要进行退火或正火热处理,以消除锻件中的内应力和改善金属基体组织。
热处理后的锻件,有的要进行清理,去除表面油垢及氧化皮,以便检查表面缺陷。
锻件毛坯经质量检查合格后再进行机械加工。
冲压多以薄板金属材料为原材料,经下料冲压制成所需要的冲压件。
冲压件具有强度高、刚性大,结构轻等优点。
在汽车、拖拉机、航空、仪表以及日用品等工业的生产中占有极为重要的地位。
4.1.2锻造对零件力学性能的影响
经过锻造加工后的金属材料,其内部原有的缺陷(如裂纹,疏松等)在锻造力的作用下可被压合,且形成细小晶粒。
因此锻件组织致密、力学性能(尤其是抗拉强度和冲击韧度)比同类材料的铸件大大提高。
机器上一些重要零件(特别是承受重载和冲击载荷)的毛坯,通常用锻造方法生产。
使零件工作时的正应力与流线的方向一致,切应力的方向与流线方向垂直,如图4-1所示。
用圆棒料直接以车削方法制造螺栓时,头部和杆部的纤维不能连贯而被切断,头部承受切应力时与金属流线方向一致,故质量不高。
而采用锻造中的局部镦粗法制造螺栓时,其纤维未被切断,具有较好的纤维方向,故质量较高。
有些零件,为保证纤维方向和受力方向一致,应采用保持纤维方问连续性的变形工艺,使锻造流线的分布与零件外形轮廓相符合而不被切断,如吊钩采用锻造弯曲工序、钻头采用扭转工序等。
曲轴广泛采用的“全纤维曲轴锻造法”,如图4-2b所示。
可以显著提高其力学性能,延长使用寿命。
图4-1螺栓的纤维组织比较
a)车削方法b)镦粗法
图4-2曲轴纤维分布示意图
a)纤维被切断b)纤维完整分布
4.2 金属的加热与锻件的冷却
加热的目的是提高金属的塑性和降低变形抗力,即提高金属的锻造性能。
除少数具有良好塑性的金属可在常温下锻造成形外,大多数金属在常温下的锻造性能较差,造成锻造困难或不能锻造。
但将这些金属加热到一定温度后,可以大大提高了塑性,并只需要施加较小的锻打力,便可使其发生较大的塑性变形,这就是热锻。
加热是锻造工艺过程中的一个重要环节,它直接影响锻件的质量。
加热温度如果过高,会使锻件产生加热缺焰,甚至造成废品。
因此,为了保证金属在变形时具有良好的塑性,又不致产生加热缺陷,锻造必须在合理的温度范围内进行。
各种金属材料锻造时允许的最高加热温度称为该材料的始锻温度;终止锻造的温度称为该材料的终锻温度。
一、锻造加热设备
锻造加热炉按热源的不同,分为火焰加热炉和电加热炉两大类。
图4-3明火炉结构示意图
1-排烟筒2-坯料3-炉膛4-炉蓖5-风门5-风管
1、 火焰加热炉
采用烟煤、焦炭、重油、煤气等作为燃料。
当燃料燃烧时,产生含有大量热能的高温火焰将金属加热。
现介绍几种火焰加热炉。
(1)明火炉:
将金属坯料置于以煤为燃料的火焰中加热的炉子,称为明火炉,又称为手锻炉。
其结构如图4-3所示。
由炉膛、炉罩、烟筒、风门和风管等组成。
其结构简单,操作方便,但生产率低,热效率不高,加热温度不均匀和速度慢。
在小件生产和维修工作中应用较多。
锻工实习常使用这种炉子。
因此,常用来加热手工自由锻及小型空气锤自由锻的坯料,也可用于杆形坯料的局部加热。
(2)油炉和煤气炉:
这两种炉分别以重油和煤气为燃料,结构基本相同,仅喷嘴结构不同。
油炉和煤气炉的结构形式很多,有室式炉、开隙式炉、推杆式连续炉和转底炉等。
如图4-5所示,为室式重油加热炉示意图,由炉膛、喷嘴、炉门和烟道组成。
其燃烧室和加热室合为一体,即炉膛。
坯料码放在炉底板上。
喷嘴布置在炉膛两侧,燃油和压缩空气分别进入喷嘴。
压缩空气由喷嘴喷出时,将燃油带出并喷成雾状,与空气均匀混合并燃烧以加热坯料。
用调节喷油量及压缩空气的方法来控制炉温的变化。
这种加热炉用于自由锻,尤其是大型坯料和钢锭的加热,它的炉体结构比反射炉简单、紧凑,热效率高。
近年来,为提高锻件表面质量,通过控制燃烧炉气的性质,实现坯料的少或无氧化加热。
如图4-6所示,为我国精锻生产中采用的一室二区敞焰少无氧化加热炉示意图。
图4-5室式重油炉示意图
图4-6一室二区敞焰少无氧化加热炉示意图
2、 电加热炉
电加热炉有电阻加热炉、接触电加热炉和感应加热炉等,如图4-7所示。
电阻炉是利用电流通过布置在炉膛围壁上的电热元件产生的电阻热为热源,通过辐射和对流将坯料加热的。
炉子通常作成箱形,分为中温箱式电阻炉如图4-8所示和高温箱式电阻炉,如图4-9所示。
前者的发热体为电阻丝,如图4-8所示。
最高工作温度950℃,一般用来加热有色金属及其合金的小型锻件;后者的发热体为硅碳棒,最高工作温度为1350℃,可用来加热高温合金的小型锻件。
电阻加热炉操作方便,可精确控制炉温,无污染,但耗电量大,成本较高,在小批量生产或科研实验中广泛采用。
图4-7电加热的方式
(a)电阻加热(b)接触电加热(c)感应加热
图4-8箱式电阻炉示意图
1-炉门;2-电阻体;3-热电偶;4-工件
图4-9红外箱式炉示意图
1-踏杆2-炉门3-炉膛4-温度传感器
5-硅碳棒冷端6-硅碳棒热端7-耐火砖8-反射层
二、锻造温度范围
坯料开始锻造的温度(始锻温度)和终止锻造的温度(终锻温度)之间的温度间隔,称为锻造温度范围见表4-1。
在保证不出现加热缺陷的前提下,始锻温度应取得高一些,以便有较充足的时间锻造成形,减少加热次数。
在保证坯料还有足够塑性的前提下,终锻温度应选得低一些,以便获得内部组织细密、力学性能较好的锻件,同时也可延长锻造时间,减少加热次数。
但终锻温度过低会使金属难以继续变形,易出现锻裂现象和损伤锻造设备。
1、锻造温度的控制方法
(1)温度计法通过加热炉上的热电偶温度计,显示炉内温度,可知道锻件的温度;也可以使用光学高温计观测锻件温度。
表4-1常用钢材的锻造温度范围
材料种类
始锻温度表(℃)
终锻温度(℃)
材料种类
始锻温度(℃)
终锻温度(℃)
碳素结构钢
合金结构钢
碳素工具钢
合金工具钢
铝 合 金
1200-1250
1150-1200
1050-1150
1050-1150
450-500
800
800-850
750-800
800-850
350-380
高速工具钢
耐热钢
弹簧钢
轴承钢
铜 合 金
1100-1150
1100-1150
1100-1150
1080
800-900
900
800-850
800-850
800
650-700
(2)目测法实习中或单件小批生产的条件下可根据坯料的颜色和明亮度不同来判别温度,即用火色鉴别法见表4-2。
表4-2碳钢温度与火色的关系
火色
黄白
淡黄
黄
淡红
樱红
暗红
赤褐
温度(℃)
1300
1200
1100
900
800
700
600
三、碳钢常见的加热缺陷
由于加热不当,碳钢在加热时可出现多种缺陷,碳钢常见的加热缺陷见表4-3。
表4-3碳钢常见的加热缺陷
名称
实质
危害
防止(减少)措施
氧化
坯料表面铁元素氧化
烧损材料;降低锻件精度和表面质量;减少模具寿命
在高温区减少加热时间;采用控制炉气成分的少无氧化加热或电加热等。
采用少装、勤装的操作方法。
在钢材表面涂保护层
脱碳
坯料表层被烧损使含碳量减少
降低锻件表面硬度、变脆,严重时锻件边角处会产生裂纹
过热
加热温度过高,停留时间长造成晶粒粗大
锻件力学性能降低,须再经过锻造或热处理才能改善
过热的坯料通过多次锻打或锻后正火处理消除
过烧
加热温度接近材料熔化温度,造成晶粒界面杂质氧化
坯料一锻即碎,只得报废
正确地控制加热温度和保温的时间
裂纹
坯料内外温差太大,组织变化不匀造成材料内应力过大
坯料产生内部裂纹,并进一步扩展,导致报废
某些高碳或大型坯料,开始加热时应缓慢升温
4.2.2 锻件的冷却
热态锻件的冷却是保证锻件质量的重要环节。
通常,锻件中的碳及合金元素含量越多,锻件体积越大,形状越复杂,冷却速度越要缓慢,否则会造成表面过硬不易切削加工、变形甚至开裂等缺陷。
常用的冷却方法有三种,见表4-4。
表4-4锻件常用的冷却方式
方式
特点
适用场合
空冷
锻后置空气中散放,冷速快,晶粒细化
低碳、低合金钢小件或锻后不直接切削加工件
坑冷(堆冷)
锻后置干沙坑内或箱内堆在一起,冷速稍慢
一般锻件,锻后可直接进行切削加工
炉冷
锻后置原加热炉中,随炉冷却,冷速极慢
含碳或含合金成分较高的中、大型锻件,锻后可进行切削加工
4.2.3 锻件的热处理
在机械加工前,锻件要进行热处理,目的是均匀组织,细化晶粒,减少锻造残余应力,调整硬度,改善机械加工性能,为最终热处理做准备。
常用的热处理方法有正火、退火、球化退火等。
要根据锻件材料的种类和化学成分来选择。
4.3自由锻的设备及工具
使用机器设备,使坯料在设备上、下两砧之间各个方向不受限制而自由变形,以获得锻件的方法称机器自由锻。
常用的机器自由锻设备有空气锤、蒸气-空气锤和水压机,其中空气锤使用灵活,操作方便,是生产小型锻件最常用的自由锻设备。
空气锤的规格是用落下部分的质量来表示,一般为50~1000kg。
一、空气锤
空气锤是由锤身(单柱式)、双缸(压缩缸和工作缸)、传动机构、操纵机构、落下部分和锤砧等几个部分组成,如图4-10a所示。
空气锤是将电能转化为压缩空气的压力能来产生打击力的。
空气锤的传动是由电动机经过一级带轮减速,通过曲轴连杆机构,使活塞在压缩缸内作往复运动产生压缩空气,进入工作缸使锤杆作上下运动以完成各项工作。
空气锤的工作原理如图4-10b所示。
图4-10空气锤
a)外形图b)工作原理
1-工作缸2-旋阀3-压缩缸4-手柄5-锤身6-减速机构7-电动机8-脚踏杆9-砧座10-砧垫
11-下砧块12-上砧块13-锤杆14-工作活塞15-压缩活塞16-连杆17-上旋阀18-下旋阀
空气锤操作过程是:
首先,接通电源,启动空气锤后通过手柄或脚踏杆,操纵上下旋阀,可使空气锤实现空转、锤头悬空、连续打击、压锤和单次打击五种动作,以适应各种加工需要。
1、空转(空行程)
当上、下阀操纵手柄在垂直位置,同时中阀操纵手柄在“空程”位置时;压缩缸上、下腔直接与大气连通,压力变成一致,由于没有压缩空气进入工作缸,因此锤头不进行工作。
2、锤头悬空
当上、下阀操纵手柄在垂直位置,将中阀操纵手柄由“空程”位置转至“工作”位置时,工作缸和压缩缸的上腔与大气相通。
此时,压缩活塞上行,被压缩的空气进入大气;压缩活塞下行,被压缩的空气由空气室冲开止回阀进入工作缸的下腔,使锤头上升,置于悬空位置。
3、连续打击(轻打或重打)
中阀操纵手柄在“工作”位置时,驱动上、下阀操纵手柄(或脚踏杆)向逆时针方向旋转使压缩缸上、下腔与工作缸上、下腔互相连通。
当压缩活塞向下或向上运动时,压缩缸下腔或上腔的压缩空气相应地进入工作缸的下腔或上腔,将锤头提升或落下。
如此循环,锤头产生连续打击。
打击能量的大小取决于上、下阀旋转角度的大小,旋转角度越大,打击能量越大。
4、压锤(压紧锻件)
当中阀操纵手柄在“工作”位置时,将上、下阀操纵手柄由垂直位置向顺时针方向旋转45°,此时工作缸的下腔及压缩缸的上腔和大气相连通。
当压缩活塞下行时,压缩缸下腔的压缩空气由下阀进入空气室,并冲开止回阀经侧旁气道进入工作缸的上腔,使锤头压紧锻件。
5、单次打击
单次打击是通过变换操纵手柄的操作位置实现的。
单次打击开始前,锤处于锤头悬空位置(即中阀操纵手柄处于“工作”位置),然后将上、下阀的操纵手柄由垂直位置迅速地向逆时针方向旋转到某一位置再迅速地转到原来的垂直位置(或相应地改变脚踏杆的位置)这时便得到单次打击。
打击能量的大小随旋转角度而变化,转到45°时单次打击能量最大。
如果将手柄或脚踏杆停留在倾斜位置(旋转角度≤45°),则锤头作连续打击。
故单次打击实际上只是连续打击的一种特殊情况。
二、蒸汽-空气锤
蒸汽-空气锤也是靠锤的冲击力锻打工件,如图4-11所示。
蒸汽-空气锤自身不带动力装置,另需蒸汽锅炉向其提供具有一定压力的蒸汽,或空气压缩机向其提供压缩空气。
其锻造能力明显大于空气锤,一般为500~5000kg(0.5-5t),常用于中型锻件的锻造。
图4-11双柱拱式蒸汽-空气锤
1-上气道2-进气道3-节气阀4-滑阀5-排气管6-下气道7-下砧
8-砧垫9-砧座10-坯料11-上砧12-锤头13-锤杆14-活塞15-工作缸
三、水压机
图4-12水压机
1、2-管道3-回程柱塞4-回程缸5-回程横梁6-拉杆7-密封圈8-上砧
9-下砧10-下横梁11-立柱12-活动横粱13-上横梁14-工作柱寒15-工作缸
大型锻件需要在液压机上锻造,水压机是最常用的一种,如图4-12所示。
水压机不依靠冲击力,而靠静压力使坯料变形,工作平稳,因此工作时震动小。
不需要笨重的砧座;锻件变形速度低,变形均匀,易将锻件锻透,使整个截面呈细晶粒组织,从而改善和提高了锻件的力学性能,容易获得大的工作行程并能在行程的任何位置进行锻压,劳动条件较好。
但由于水压机主体庞大,并需配备供水和操纵系统,故造价较高。
水压机的压力大,规格为500~12500t,能锻造1~300t的大型重型坯料。
4.3.2自由锻工具
一、机器自由锻的工具
根据工具的功能可分为以下几类,如图4-13所示:
1.夹持工具:
如圆钳、方钳,槽钳、抱钳、尖咀钳、专用型钳等。
2.切割工具:
剁刀、剁垫、刻棍等。
3.变形工具:
如压铁、摔子、压肩摔子、冲子、垫环(漏盘)等。
4.测量工具:
如钢直尺、内外卡钳等。
5.吊运工具:
如吊钳、叉子等。
图4-13机锻工具
钳手刻棍压铁剁刀冲子垫环
剁垫摔子压肩摔子
二、手工自由锻工具
利用简单的手工工具,使坯料产生变形而获得的锻件方法,称手工自由锻,如图4-14所示。
1、手工锻造工具分类如下:
(1)支持工具:
如羊角砧等;
(2)锻打工具:
如各种大锤和手锤;
(3)成型工具:
如各种型锤、冲子、漏盘等;
(4)夹持工具:
各种形状的钳子;
(5)切割工具:
各种錾子及切刀;
(6)测量工具:
钢直尺、内外卡钳等。
图4-14手锻工具
a)羊角钻b)锻锤c)衬垫工具d)手钳e)测量工具
2、手工自由锻的操作
(1)锻击姿势手工自由锻时,操作者站离铁砧约半步,右脚在左脚后半步,上身稍向前倾,眼睛注视锻件的锻击点。
左手握住钳杆的中部,右手握住手锤柄的端部,指示大锤的锤击。
锻击过程,必须将锻件平稳地放置在铁砧上,并且按锻击变形需要,不断将锻件翻转或移动。
(2)锻击方法手工自由锻时,持锤锻击的方法可有:
手挥法主要靠手腕的运动来挥锤锻击,锻击力较小,用于指挥大锤的打击点和打击轻重。
肘挥法手腕与肘部同时作用、同时用力,锤击力度较大。
臂挥法手腕、肘和臂部一起运动,作用力较大,可使锻件产生较大的变形量,但费力甚大。
三、锻造过程严格注意做到“六不打”:
①低于终锻温度不打;
②锻件放置不平不打;
③冲子不垂直不打;
④剁刀、冲子、铁砧等工具上有油污不打;
⑤镦粗时工件弯曲不打;
⑥工具、料头易飞出的方向有人时不打。
4.4自由锻工艺
4.4.1自由锻的工艺特点
一.应用设备和工具有很大的通用性,且工具简单,所以只能锻造形状简单的锻件,操作强度大,生产效率低。
二.自由锻可以锻出质量从不到1kg到200~300t的锻件。
对大型锻件,自由锻是唯一的加工方法,因此自由锻在重型机械制造中有特别重要的意义。
三.自由锻依靠操作者控制其形状和尺寸,锻件精度低,表面质量差,金属消耗也较多。
所以,自由锻主要用于品种多,产量不大的单件小批量生产,也可用于模锻前的制坯工序。
4.4.2自由锻的基本工序
无论是手工自由锻、锤上自由锻以及水压机上自由锻,其工艺过程都是由一些锻造工序所组成。
所谓工序是指在一个工作地点对一个工件所连续完成的那部分工艺过程。
根据变形的性质和程度不同,自由锻工序可分为:
基本工序,如镦粗、拔长、冲孔、扩孔、芯轴拔长、切割、弯曲、扭转、错移、锻接等,其中镦粗、拔长和冲孔三个工序应用得最多;辅助工序,如切肩、压痕等;精整工序,如平整、整形等三类。
一.镦粗
镦粗是使坯料的截面增大,高度减小的锻造工序。
镦粗有完全镦粗如图4-15所示和局部镦粗。
局部镦粗按其镦粗的位置不同又可分为端部镦粗和中间镦粗两种,如图4-16所示。
图4-16完全镦粗
镦粗主要用来锻造圆盘类(如齿轮坯)及法兰等锻件,在锻造空心锻件时,可作为冲孔前的预备工序。
镦粗的一般规则、操作方法及注意事项如下:
1.被镦粗坯料的高度与直径(或边长)之比应小于2.5~3,否则会镦弯,如图4-17a所示。
工件镦弯后应将其放平,轻轻锤击矫正,如图4-17b所示。
局部镦粗时,镦粗部分坯料的高度与直径之比也应小于2.5~3。
2.镦粗的始锻温度采用坯料允许的最高始锻温度,并应烧透。
坯料的加热要均匀,否则镦粗时工件变形不均匀,对某些材料还可能锻裂。
图2-17局部镦粗
a)漏盘上镦粗b)胎膜内镦粗c)中间镦粗
图4-17镦弯的产生和矫正
(a)镦弯的产生b)镦弯的矫正
3.镦粗的两端面要平整且与轴线垂直,否则可能会产生镦歪现象。
矫正镦歪的方法是将坯料斜立,轻打镦歪的斜角,然后放正,继续锻打,如图4-18所示。
如果锤头或砥铁的工作面因磨损而变得不平直时,则锻打时要不断将坯料旋转,以便获得均匀的变形而不致镦歪。
4.锤击应力量足够,否则就可能产生细腰形,如图4-19a所示。
若不及时纠正,继续锻打下去,则可能产生夹层,使工件报废,如图4-19b所示。
图4-18镦歪的产生和矫正图4-19细腰形及夹层的产生
a)细腰形b)夹层
二、拔长
拔长是使坯料长度增加,横截面减少的锻造工序,又称延伸或引伸,如图4-20所示。
拔长用于锻制长而截面小的工件,如轴类、杆类和长筒形零件。
图4-20拔长
a)拔长b)局部拔长c)心轴拔长
拔长的一般规则,操作方法及注意事项:
1.拔长过程中要将坯料不断地翻转,使其压下面都能均匀变形,并沿轴向送进操作。
翻转的方法有三种:
如图4-21(a)所示,为反复翻转拔长,是将坯料反复左右翻转90º,常用于塑性较高的材料;如图4-21(b)所示,为螺旋式翻转拔长,是将坯料沿一个作90º翻转,常用于塑性较低的材料;如图4-21(c)所示,为单面前后顺序拔长,是将坯料沿整个长度方向锻打一遍后,再翻转90º,尔后依次进行,常用于频繁翻转不方便的大锻件,但应注意工件的宽度和厚度之比不要超过2.5,否则再次翻转继续拔长时容易产生折叠。
图4-21拔长时锻件的翻转方法
a)反复翻转拔长b)螺旋式翻转拔长c)单面顺序拔长
2、拔长时,坯料应沿砥铁的宽度方向送进,每次的送进量L应为砥铁宽度B的0.3~0.7倍,如图4-22a所示。
送进量太大,金属主要向宽度方向流动,反而降低延伸效率,如图4-22b所示。
送进量太小,又容易产生夹层,如图4-22c所示。
另外,每次压下量也不要太大,压下量应等于或小于送进量,否则也容易产生夹层。
3、由大直径的坯料拔长成小直径的锻件时,应把坯料先锻成正方形,在正方形的截面下拔长,到接近锻件的直径时,再倒棱,滚打成圆形,这样锻造效率高,质量好。
如图4-23所示。
图4-22拔长时的送进方向和进给量
a)送进量合适b)送进量太大、拔长率降低c)送进量太小、产生夹层
图4-23大直径坯料拔长时的变形过程
3.锻制台阶轴或带台阶的方形、矩形截面的锻件时,在拔长前应先压肩。
压肩后对一端进行局部拔长即可锻出台阶。
如图4-24所示。
图4-24压肩
a)方料压肩b)圆料压肩
5.锻件拔长后须进行修整,修整方形或矩形锻件时,应沿下砥铁的长度方向送进,如图4-25a所示,以增加工件与砥铁的接触长度。
拔长过程中若产生翘曲应及时翻转180°轻打校平。
圆形截面的锻件用型锤或摔子修整。
如图4-25b所示。
图4-25拨长后的修整
a)方形、矩形面的修整b)圆形截面的修整
6.采用专制的芯轴对孔进行拔长,主要用于孔深的工作,如图4-26所示。
图4-26芯轴拔长
三、冲孔
冲孔是用冲子在坯料冲出通孔或不通孔的锻造工序。
冲孔主要用于制造带孔工件,如齿轮坯、圆环、套筒等。
一般规定:
锤的落下部分重量在0.15~5t之间,最小冲孔直径相应为Φ30~Φ100mm;孔径小于100mm,而孔深大于300mm的孔可不冲出;孔径小于150mm,而孔深大于500mm的孔也不冲出;直径小于20mm的孔不冲出。
根据冲孔所用的冲子的形状不同,冲孔可分为实心冲子冲孔和空心冲子冲孔。
实心冲子冲孔又可分为单面冲孔和双面冲孔,如图4-27所示。
图4-27冲孔
a)双面冲孔b)单面冲孔c)空心冲子冲孔
1.单面冲孔:
对于较薄工件,即工件高度与冲孔孔径之比小于0.125时,可采用单面冲孔。
冲孔时,将工件放在漏盘上,冲子大头朝下,漏盘的孔径和冲子的直径应有一定的间隙,冲孔时应仔细校正,冲孔后稍加平整。
2.双面冲孔:
其操作过程为:
镦粗;试冲(找正中心冲孔痕);撒煤粉(煤粉受热后产生的气体膨胀力可将冲子顶出);冲孔,即冲孔到锻件厚度的2/3~3/4;翻转180°找正中心;冲除连皮;如图4-28所示。
修整内孔;修整外圆。
图4-28冲孔的步骤
(a)放正冲子,试冲;(b)冲浅坑,撒煤末
(c)冲至工件厚度的2/3深;(d)翻转工件在铁砧圆孔上冲透
3.空心冲子冲孔:
当冲孔直径超过400mm时,多采用空心冲子冲孔。
对于重要的锻件,将其有缺陷的