模型A数控工艺与编程设计.docx
《模型A数控工艺与编程设计.docx》由会员分享,可在线阅读,更多相关《模型A数控工艺与编程设计.docx(18页珍藏版)》请在冰豆网上搜索。
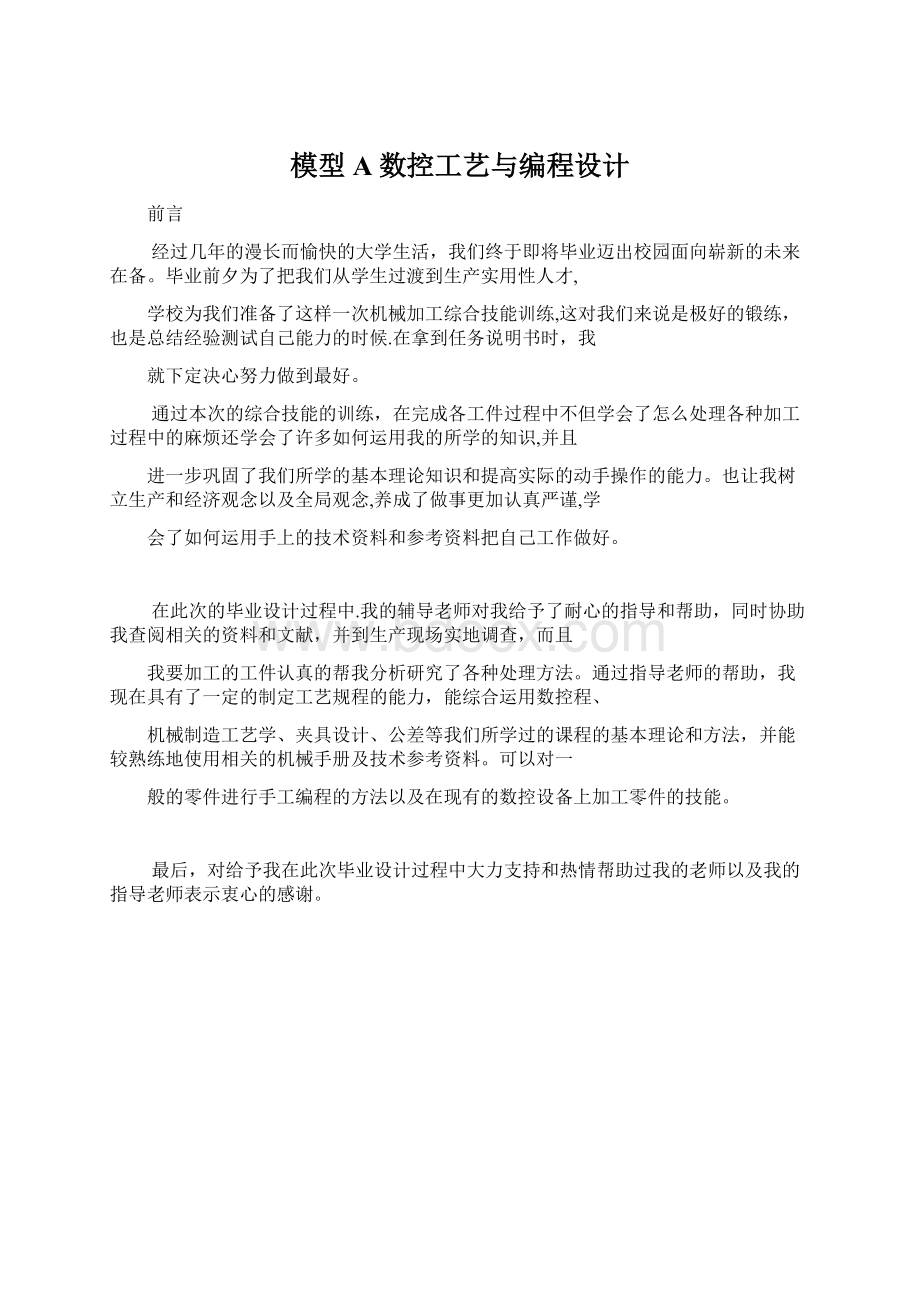
模型A数控工艺与编程设计
前言
经过几年的漫长而愉快的大学生活,我们终于即将毕业迈出校园面向崭新的未来在备。
毕业前夕为了把我们从学生过渡到生产实用性人才,
学校为我们准备了这样一次机械加工综合技能训练,这对我们来说是极好的锻练,也是总结经验测试自己能力的时候.在拿到任务说明书时,我
就下定决心努力做到最好。
通过本次的综合技能的训练,在完成各工件过程中不但学会了怎么处理各种加工过程中的麻烦还学会了许多如何运用我的所学的知识,并且
进一步巩固了我们所学的基本理论知识和提高实际的动手操作的能力。
也让我树立生产和经济观念以及全局观念,养成了做事更加认真严谨,学
会了如何运用手上的技术资料和参考资料把自己工作做好。
在此次的毕业设计过程中.我的辅导老师对我给予了耐心的指导和帮助,同时协助我查阅相关的资料和文献,并到生产现场实地调查,而且
我要加工的工件认真的帮我分析研究了各种处理方法。
通过指导老师的帮助,我现在具有了一定的制定工艺规程的能力,能综合运用数控程、
机械制造工艺学、夹具设计、公差等我们所学过的课程的基本理论和方法,并能较熟练地使用相关的机械手册及技术参考资料。
可以对一
般的零件进行手工编程的方法以及在现有的数控设备上加工零件的技能。
最后,对给予我在此次毕业设计过程中大力支持和热情帮助过我的老师以及我的指导老师表示衷心的感谢。
目录
第一章零件的工艺性分析
一.零件的结构工艺性分析
二.零件的技术要求
三.零件的材料
第二章零件工艺规程的设计
一.确定零件的生产类型和生产纲领
二.确定零件毛坯的制造形式
三.制定工艺路线的理论原则及制定工作路线
四.基准的选择
五.工序路线的制定
六.确定零件的工序尺寸和加工余量
第三章数控机床的工艺装备及夹具、刀具的选择
一.机床的选择
二.夹具的选择
三.刀具的选择
四.工序尺寸及机械加工余量的校核
五.确定切削用量及基本时间Tj等
第四章数控加工程序编制方法的选择
一.数控加工程序的编制
二.数控加工程序的内容
结束语
参考文献
第一章零件的分析
一.零件的结构工艺性分析
在初步了解零件的功能用途后,有必要对零件进行结构工艺分析,找出技术关键,以便在拟定工作规程时采用适当的工作措施加以保证。
1.零件的结构分析
总的来说我的零件由3部分组成,小端由1个M16螺纹和1个宽3的深度1的退刀槽构成,中间是1个R23的圆球有6个R30宽度为R5的圆形凹槽在圆球上分布,另一端则是需要铣床铣出1个心形。
2.零件的工艺性分析
(1).从零件图可以看出主要表面是由一个球体和6个分布在球体周围的球形槽是右车车削和铣削来完成的,其中6个球形槽是由分度头来完成的,它们是以轴线为基准加工的。
(2)这个工件只有1个位置精度就是小端相对于轴心线的垂直度是0.04。
3.零件的设计基准
通过对零件图的分析可以看出零件基准为轴心线。
二.零件的技术要求
1.表面精度
螺纹表面粗糙度要求为Ra1.6,其余表面粗糙度Ra3.2。
2.位置精度
本零件只有1个位置精度是垂直度。
3调制处理
通常将淬火+高温回火成为调质处理。
调质处理的目的是使零件获得强度、硬度、塑性和韧性都较好的综合机械性能。
4.发蓝
将钢铁工件放入某些氧化性溶液中,使其表面形成0.6到0.8µm致密而牢固的Fe
O
薄膜的工艺方法为发蓝,又叫氧化处理。
发蓝能提高工件表面的抗腐蚀能力,有利于清除工件的残余应力,减少变形。
还能使边面光泽、美观,发蓝可用化学法和电解法。
化学法又可分为碱性法和非碱性法。
碱性法应用最多。
5.零件检验类别为二类检验。
三.零件的材料(40Cr)
1.性能特点
40Cr的性能特点是具有良好的综合力学性能和合适的淬透性。
2.成分特点
名称
C
Mn
Si
Cr
40Cr
0.37—0.45
0.17—0.37
0.5—0.8
0.8—1.1
3.热处理特点
40Cr属于低淬透性合金调质刚,它的热处理特点是油淬临界淬透直径为20—40mm,调质后强度比碳钢高,一般δb=800—1000Mpa,δs=600—800Mpa,αk=60—90j/cm²。
其合金元素总量小于2.5%。
常用作中等截面,要求机械性能比碳钢高的调质件。
第二章零件工艺规程的设计
一.确定零件的生产类型和生产纲领
确定生产类型主要依据是零件的生产纲领。
生产纲领是企业在计划期限内应当生产的产品产量和进度计划,即年产量。
包括合品率和废品率在内的一年产量。
零件的生产纲领的计算式如下:
N=Qn(1+α%)(1+β%)
N——零件的生产纲领(件/年)
Q——产品的年产量(台/年)
N——每台产品中该零件的数量(件/台)
α——零件的备品率
β——零件的废品率
生产类型的具体划分,可根据生产纲领和产品及零件的特征或工作地每月担负的工序数来确定。
按设计要求零件的生产类型为中批生产。
二.确定零件毛坯的制造形式
在制定零件机械加工工艺规程前一定要确定毛坯。
包括选择毛坯类型及制造方法,确定毛坯精度。
零件机械加工的工序数量,材料消耗的劳动量,在很大程度上与毛坯有关。
例如:
毛坯的形状和尺寸越接近成品零件,即毛坯的精度越高。
则零件的机械加工劳动量越少,材料消耗也少。
机械加工的生产率也可提高,成本则可降低,但毛坯的制造费用提高了。
因此,确定毛坯要从机械加工和毛坯制造两个方面综合考虑。
毛坯的类型有铸、锻、压制、冲压、焊接、型材和板材等。
确定毛坯还要考虑如下因素:
1、零件的材料及力学性能。
2、零件的形状和尺寸。
3、生产类型。
4、具体生产条件。
5、充分考虑利用新工艺、新技术和新材料的可能性。
我所加工的模型件A的材料是钢材,并且大部分表面为回转加工表面,各台阶直径尺寸相差不多,因此选择棒料为毛坯。
三.制定工艺路线的理论原则及制定工艺路线
1.制定工艺路线的理论原则
(1).零件图及技术要求
零件图及其技术条件,是制造零件的主要依据,在零件图上应包括:
结构技术条件,材料在制订工艺路线时首先应对零件的构造要求进行详细的工艺分析,以便掌握加工要求和保证质量。
(2).零件的毛坯图
毛坯图是根据零件图设计的。
对于一些强度要求不高的零件可选用型材作毛坯,用型材的规格尺寸制造零件所需的长度,对此综合训练的零件总强度有一定的要求,且属于中批生产,所以选用的毛坯应经过热处理等工序。
(3).生产类型
生产类型是指企业(或车间、工段、班组、工作地)生产专业化程度的分类,一般分为三种基本类型:
单件生产、成批生产、大量生产。
模型件A为中批生产。
(4).生产条件
主要应从现有的机床设备出发来制定工艺路线。
使现有的设备充分利用,并且为了更好的保证质量,提高劳动生产率,降低生产成本,制定工艺过程时也要注意新技术的引用及现有的实际设备情况等综合考虑。
总的来说,在制定工艺路线时,应使零件上各尺寸精度,位置精度,表面粗糙度和各项技术指标均能得到保证,同时也要尽量提高生产率,降低生产成本,从而获得最好的经济效果。
]2.加工阶段的划分
模型件A的加工阶段可划分为粗加工—精加工,它是通过程序来保证的。
划分加工阶段的目的是保证各主要表面达到设计图的质量要求,并提高尺寸精度,降低表面粗糙度。
(1).保证加工质量
工件粗加工时,切削金属较多,产生较大的切削力和切削热,同时需要有较大的夹紧力,且内应通过粗加工还能重新分布,造成工件生产较大的变形。
划分阶段后,粗加工造成的加工误差可通过精加工得到纠正,从而提高了零件的加工精度,降低了表面粗糙度,保证了零件的加工质量。
(2).合理地使用设备提高产品生产率
在加工时选用数控机床,可以把工件的粗加工与精加工在一道工序内完成,这样就避免了工件的二次装夹,提高了工件的形状与位置精度。
(3).便于安排热处理
把热处理安排在精加工之前,可保证热处理引起的局部变形在精加工中得以纠正。
把粗精加工分开后,毛坯的缺陷在粗加工后即可及早发现并及时决定修补或报废,以免对报废零件继续进行精加工,而浪费工时和其他制造费用。
3.工序的集中与分散问题的分析
在制订工艺路线时,当选定各表面加工方法和确定了阶段划分后,就可以将同阶段中的各加工表面组合成若干工序,组合时可采用集中与分散的原则。
工序集中是指工件的加工集中在少数几道工序内完成,即每道工序的加工内容较多。
工序分散是将工件的加工分散在较多工序内进行,即每道工序的内容较少,最少时即每道工序仅一个简单工步。
工序集中与工序分散是拟定工艺路线时确定工序数的两种原则。
工序集中的特点是:
1.采用高效专用设备及工艺装备,生产率高。
2.工件装夹次数减少,易于保证表面间位置精度,还能减少工序间运输量,缩短生产周期。
3工序数目少,可减少机床数量、操作工人数和生产面积,还可简化生产计划和生产组织工作。
4.因采用结构复杂的专用设备及工艺装备,使投资大,调整和维修复杂,生产准备工作量大,转换新产品比较费时。
工序分散的特点是:
1.设备及工艺装备比较简单,调整和维修方便,工人容易掌握,生产准备工作量少,又易于平衡工序时间,易适应产品转换。
2.可采用最合理的切削用量,减少基本时间。
3.设备数量多,操作工人多,占用生产面积也大。
在制订工艺路线时,工序集中或分散主要取决于生产规模和零件的结构特点及技术要求。
批量小时为简化管理工作多将工序集中,大批量生产时可采用效率高的机床将工序集中。
也可以将工序分散后组织流水生产,对大型零件应适当分散。
这两种原则各有特点。
我所加工的模型件A,即遵循的是工序集中原则。
四.定位基准的选择
定位基准的选择对零件的加工尺寸和位置精度、零件各表面的加工顺序及夹具结构等都会产生举足轻重的影响,正确的选择定位基准是制订机械加工工艺规程和进行夹具设计的关键问题。
在选择定位基准时,是从保证工件精度要求出发的,因而分析定位基准选择的顺序就应从精基准到粗基准。
1.精基准的选择
(1).基准重合原则:
就是尽可能选用设计基准作为定位基准,这样可以避免定位基准与设计基准不重合而引起定位误差。
(2).基准统一原则:
位置精度要求较高的某些表面加工时尽可能选用同一定位基准,这样有利于保证各加工表面的位置精度。
(3).自为基准和互为基准原则。
(4).择精度较高,安装稳定可靠的表面作精基准,而且所选的基准应使夹具的结构简单,安装和加工工件方便。
2.粗基准的选择
(1).对于所有表面都要加工的零件,应选择余量和公差最小的表面做基准,以避免余量不足而造成废品。
(2).选取光洁平整的表面,并且面积足够大,装夹稳定的表面作为粗基准
(3).粗基准一般都只能用一次,尽量避免重复使用。
在实际工作中,定位基准的选择要符合上述所有的原则有时是不可能的,因此应根据具体情况进行分析,选出最有利的定位基准。
五.工序设计
1.工序路线
序号
工序名称
设备名称
0
下料
5
热处理
10
车基准面
数控车床
15
车大端
数控车床
20
去毛刺
25
铣球形槽
数控铣床
30
铣心形
数控铣床
35
去毛刺
40
清洗
45
最终检验
50
发蓝
55
60
2.设计计算
1.机械加工余量
机械加工余量就是保证零件规定的质量,在加工过程中从其表面上切除的金属层它对工艺过程有一定的影响,余量不足,不能保证零件的加工质量;余量过大,不但增加机械加工的劳动量,而且增加了材料刀具、能源的消耗,从而增加了成本,所以必须合理地安排加工余量。
通常确定机械加工余量的方法大致有三种